
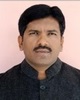
- Open Access
- Authors : Divya Kakara , Dr. Ramesh Malothu
- Paper ID : IJERTV10IS010008
- Volume & Issue : Volume 10, Issue 01 (January 2021)
- Published (First Online): 08-01-2021
- ISSN (Online) : 2278-0181
- Publisher Name : IJERT
- License:
This work is licensed under a Creative Commons Attribution 4.0 International License
Biodiesel Production from Chlorella Vulgaris by Media Optimisation and Transesterification
Production of Biodiesel from Chlorella Vulgaris
Divya Kakara1
Assistant Professor, School of Biotechnology Jawaharlal Nehru Technological University Kakinada, Kakinada, Andhra Pradesh, India- 533003
Dr. Ramesh Malothu1
Associate Professor, School of Biotechnology Jawaharlal Nehru Technological University Kakinada,
Kakinada, Andhra Pradesh, India- 533003
Abstract – Energy has become a crucial factor for humanity to continue the economic growth and maintain high standard of living especially after the inauguration of the industrial revolution in the late 18th and early 19th century. To battle up with the demand, fuel is being extracted from the land and sea. This usage of fossil fuels has filled the atmosphere with greenhouse gases causing global warming. We are at a point, where we must find other alternative fuels. Biofuel is one among the alternate fuels. This study paves the production and comparative study of biofuel using algae grown on different nutrient sources. The lipids of algae were extracted from non- edible chlorella vulgaris, Mustered algae using soxhlet and solvent extraction. The lipids are trans-esterified in-situ by adding catalysts (alcohol, acids, and base) and converting oil into FAMEs (Fatty Acid Methyl Esters) and glycerol which were later separated and purified by fractional distillation (hexane
/methanol) in order to obtain pure form of biodiesel.
Keywords: Biodiesel, chlorella vulgaris, Mustered algae, lipids, FAME, trans-esterification
-
INTRODUCTION
Vitality today is the most essential assets for humankind and its economic advancement, because of the vitality emergency which winds up one of the worldwide issues confronting the world. Real vitality assets originate from fills, because of their vitality content with critical sums. currently, convenient is a physically powerful trust of our existence on oil based commodities, for instance, oil, and vaporous oil, in view of the fact that supplementary 85% of the world's essentialness desires from non-sustainable power sources, whatever, in the mechanical creation section, nearby uses or in the transportation division. The issue likewise is that the populace development isn't secured by local unrefined petroleum generation and its subordinates. Also, the arrangement of petroleum derivatives requires a large number of years, thus the oil energizes are non-sustainable1.
Additionally, change of the unrefined petroleum costs prompts worldwide and international clashes particularly in the creating nations. Sustainable power source is considered as a standout amongst the most important assets in numerous
nations around the globe, which represents around 22% of the world's vitality consumption and can be changed over to erstwhile usable kinds of power similar to bio fuels. Liquid biodiesel have transformed into a sea green diesel engines2.
The annual production of the biodiesel is 7 billion liters globally 3 of which India is 0.2 billion liters. Biodiesel is normally eco friendly and non-noxious fuel1 Belay An., et al(1997), which can be delivered utilizing several vegetable oils (tasteful or non-consumable), mammal fats or unprecedented strain of microalgae. Microalgae have been viewed as of late as a shows potential biomass feedstock with extraordinary prospective for biodiesel creation in light of the fact that they recreate themselves each couple of time (2 or 18 days), yield oil outperforming 1x the yield of the most excellent oilseed crop, decrease radiations of critical ozone exhausting substance (0.2g of algal biomass requiring around of CO2) and can be procured to wastewater (1.5 m3 of wastewater is required to convey 800 g of dry green development).Also, microalgae as a fuel source does not battle with the sustenance crisis, since it isn't the crucial sustenance source. The oil productivity of many microalgae exceeds the best producing oil crops. Microalgae are photosynthetic microorganisms which convert sunlight, water and CO2 to sugars, from which macromolecules, such as lipids and triacylglycerols (TAGs) can be obtained. These TAGs are the promising and sustainable feedstock for biodiesel production.
The age of biodiesel using microalgae biomass as a possible feedstock has been portrayed2. The age of biodiesel from microalgae oil by transesterification process has already been evil presence started in the writing utilizing main traditional techniques, and the procedure ordinarily utilizes pre-extricated oil as crude material, which is typically conveyed by mechanical crushing took after by dissolvable extraction to isolate whatever is left of the oil, and a while later its change to FAAE and glycerol.
The transesterification reaction can be catalyzed by salt, acidic, or impetuses. The use of the dissolvable catalyzed
transesterification innovation would not be suitable for biodiesel age from microalgae oil; in light of the high FFA substance of microalgae lipids4. This is on account of the utilization of antacid catalysts with high FFA containing oils would bring about cleanser development and difficulties in the biodiesel separation5,6. The utilization of sulphuric corrosive, as response impetus, has been considered as small scale green growth lipid transesterication, because of its cold-heartedness to the FFA substance of this oil feedstock, as the trans-esterication and esterication responses of biodiesel proficient production are energized by methods for acidic catalysis, in any case, acidic trans-esterification process is obliged due to the water game plan in the midst of the esterification reaction, high alcohol to-oil extent (around 4:1), and sweeping entireties (5% to 15%) of stimuli may be required. Furthermore, the usage of proteins as a trans- esterification7 impetus is still under examination.
Under the conditions inspected, the best Distinction yields (97.2%) in perspective of the oil substance of the sunower seeds were procured at a molar extent of methanol to oil of 30:1, a Acid driving force centralization of 98% and a reaction time of 40 mins. The standard the sustenance crops are used as a piece of the fuel creation, unique liquid biofuels8. Mixotrophic cultivated algae often provide higher biomass production compared to the cultivation in autotrophic and heterotrophic9.
The lipid production from the mixotrophic Chlorella species are higher than the combination of lipids produced from photoautotrophic and heterotrophic culture10. However, the lipid production of Chlorella vulgaris under mixotrophic cultivation is lower than under heterotrophic cultivation due to the unsatisfactory lipid content (13.8%) of mixotrophic culture9,11.
These microalgae were cultivated in BG-11 medium and the oil was extracted to transesterification reaction. They also examined simultaneous extraction and trans-esterification using different solvents. Maximum biodiesel yield was obtained using hexane as a solvent. In addition, Chlorella Sp. had the highest growth rate and cell dry weight than the other two algae species12.
-
MATERIALS AND METHODS
-
Algae Cultivation:
Chlorella vulgaris was purchased from Culture Collection of Algae at JNTU Hyderabad Telangana, India. The cells were maintained in a medium containing three different medias viz. BG-11, N-8, M-8. The cells were grown in 250- ml Erlenmeyer flasks on an orbital shaker set at 150 rpm at room temperature. Optimization conditions for the growth are 18 hrs light using fluorescent lamps. The temperature was maintained a 370C and aeration was done at the rate of 136 cm3 min-1. The pH of the media is 7. Disinfected air was provided by a air motor apparatus (Hailee V-35). The alga was inoculated and the lipids are extracted by using different soxhlet and solvent extractions. Separation of biodiesel by using different solvents they are ethanol, hexane and
methanol, chloroform. The algae is incubated for 18 days and cell count is 1.25 x 108 cells/Ml.
-
Microalgae growth determination:
Chlorella vulgaris development was controlled through estimating the visual thickness (OD) utilizing OPTIZEN POP (UV/Vis spectrophotometer). For the assurance of a reasonable wavelength that can recognize C. vulgaris, UV absorbance was examined by the wavelengths run from 200 to 600 nm with distinction cell thickness. 480 nm was the pinnacle absorbance decided then the cell thickness was estimated by this wavelength. "The Phytoplankton.
-
Lipid Extraction:
Lipid extraction was done by utilizing Bligh and Dyer with few alterations. Chlorella vulgaris culture was secluded and algae growth test was utilized for lipid extraction. The lipid extraction was done using a mixture of 2.5 ml chloroform and
2.5 ml methanol (1:1). 1 ml of 0.85% NaCl was added to the mixture to make strides the execution of lipid extraction. The mixture was mixed well and centrifuged at 4000 rpm for 15 minutes. Methanol/ water (top layer) and chloroform (base layer) were observed. The chloroform layer was additionally purged with sodium sulphate anhydrous powder and gathered into the weighted measuring instrument. The natural solvents inside were evaporated under high sanitized nitrogen gas. The rest of the lipids were weighed. This assumes the level of lipids in the algal dry weight. Lipids efficiency (mg/L) was computed by the equation: Lipid content (%) x dry biomass (mg/L). We have done lipid extraction in 3 different methods by using salts, acids and solvents.
-
Acid treatment:
-
Addition of HCl: 1 ml of the cell suspension is mixed with 3.75 ml of chloroform/ methanol/ 12N HCl (2/4/0.1 v/v/v). After vigorous mixing, 1.25 ml of chloroform is incorporated with vortex for 30 sec and later by adding 1.25 ml of water with equivalent mixing. After 10 min of centrifugation at low speed, the lower chloroform layer is cleared and transferred to a glass tube for dissipation.
-
Addition of acetic acid: 1 ml of water incorporates 3.75 ml of a mixture of chloroform: methanol (1:2). Vortex for 10- 15 min and then add 1.25ml of chloroform into the mixture. Mixing was done for 1 min and to this; 1.25 ml of water is added and centrifuged at 4000rpm for a minute after complete mixing. Discard upper layer and collect the lower layer with Pasteur pipette. Acetic acid (0.5% v/v) is added to the extracted lower layer for the extraction of acidic phospholipids
-
-
Salt treatment:
-
Addition of NaCl: 1 ml of water incorporated with
3.75 ml of a mix chloroform: methanol in (1:2) ratio. Vortex for 10-15 min and then add 1.25ml of chloroform into the mixture. Mixing was done for 1 min and to this; 1.25 ml of water is added and centrifuged at 4000rpm for a minute after complete mixing. Discard upper layer and collect the lower layer with Pasteur pipette. The separated layer is treated with 1N NaCl to extract the lipids.
-
Addition of KCl: 1 ml water incorporated with 3.75 ml of a mix chloroform/methanol (1:2). Vortex for 10-15 min
and then add 1.25ml of chloroform into the mixture. Mixing was done for 1 min and to this; 1.25 ml of water is added and centrifuged at 4000rpm for a minute after complete mixing. Discard upper layer and collect the lower layer with Pasteur pipette. The separated extract was then treated with 1N KCl to extract the lipids.
-
-
Solvent Extraction:
1g sample of pre-dried and pulverised biomass (microalgae) sample is weighed accurately into a soxhlet glass sample tube. The sample tube was transferred to the extraction chamber in the soxhlet apparatus. A 50ml aliquot of the extraction solvent containing hexane:isopropanol (3:2) was transferred into the solvent cup and placed on the heating plates. The cooling water supply to the condensers was opened. The extractions were conducted for 3 h. On completion of the extraction process, the samples were left to cool for at least 15 min after which the solvent cups with the lipid extracts were removed. The lipids were extracted by solvent extraction.
-
-
Anthrones test for carbohydrates estimation:
Reagent : 5% phenol. Reagent : 96% sulphuric acid
To 1 ml algal extract solution, 2.5ml HCl is added. Sodium carbonate is added drop wise to neutralize the hydrochloric acid. The solution is finally makeup to 15ml. Centrifuge the algal solution at 10,000 rpm for 5min and collect the supernatant. Add 1ml of reagent 1 and incubate at a dark place for 5 min. Add 3ml of reagent and incubate in the water bath for 20min at 30°C. Take OD value at 490nm in 1 cm cuvette using Lab India UV-Vis-Spectrophotometer
-
Lowry's method for protein estimation:
Reagent : 48:1:1 of 2% sodium carbonate in 0.1 N NaoH: 1% sodium potassium tatarate:0.5% Cuso4.5H2O
Reagent : Take FC (Folin – ciocalteu) reagent and distilled H2O in 1:2 ratio
To 1ml of algae extract solution, add 2ml lysis buffer is added. Incubate for half an hour at 45°C and vortex for 1min. Add 250µl SDS and gently shake and centrifuge at 10,000rpm for 5min to collect the supernatant. Add 2ml of reagent and incubate for 20 min in dark place. Add 3ml of reagent and incubate for 20min in dark place. Take OD value at 660nm in 1cm cuvette using UV-Vis- Spectrophotometer and draw the concentration based on standard values.
-
Transesterification:
Trans-esterification is the path toward exchanging the normal social occasion R of an ester with the common get- together R of an alcohol. These reactions are often catalyzed by the development of a Acid or base impetus. The reaction can in like manner be refined with the help of synthetic compounds (biocatalysts) particularly lipases Strong acids catalyze the reaction by giving a proton to the carbonyl social event, therefore making it an all the more ground-breaking electrophile, however bases catalyze the reaction by removing a proton from the alcohol, subsequently making it more nucleophilic. Esters with greater alkoxy social occasions can be created utilizing methyl or ethyl esters in high flawlessness by warming the mix of ester, Acid/base,
and broad alcohol and vanishing the little alcohol to drive amicability.
-
Viscometer:
For estimation of consistency, the temperature of substrate being estimated must be precisely controlled since little temperatures may prompt change stamped changes of thickness.
The single-step technique was completed with 4.5 grams of dried green growth raced into the vessel, in which the impetus, methanol and were added to permit the extraction of lipid and the trans-esterification to happen all the while. To contrast its execution and the customary two-advance biodiesel creation, a chose condition was utilized for the two strategies, which was transesterified at 14% of impetus, 6:1 (v/w) proportion of liquor to biomass and the response time of 2 h. Two layers will be shaped. In the base layer glycerol's will be available and upper layer biodiesel. the biodiesel was sifted through by a No. 5 Whatmans paper and store it for advance GC examination.
-
-
RESULTS
-
Growth of algae:
Figure 1: Cultivation of mustered algae from initial day to 18th day
-
Biomass values:
Table 1: Biomass comparison between different medias for
chlorella vulgaris
Days
Biomass
Bg-11
N-8
Tap
Dy 0
0.30
0.26
0.25
Day 2
0.55
0.49
0.44
Day4
0.78
0.63
0.59
Day 6
0.96
0.88
0.71
Day 8
1.01
0.97
0.83
Day 10
1.25
1.12
0.91
Day 12
1.34
1.26
1.16
Day 14
1.49
1.35
1.28
Day 16
1.51
1.46
1.39
Day 18
1.60
1.53
1.55
Figure 2:Increase in algae growth rate- Chlorella Vulgaris
-
Mustered algae biomass:
Table 2: Mustered algae biomass in different media
Days
Biomass
Bg11
N-8
Tap
Day 0
0.63
0.51
0.64
Day 2
0.72
0.55
0.96
Day4
0.92
0.82
1.11
Day 6
1.03
0.92
1.23
Day 8
1.09
0.97
1.32
Day 10
1.21
0.99
1.48
Day 12
1.35
1.07
1.63
Day 14
1.55
1.25
1.75
Day 16
1.69
1.36
1.86
Day 18
1.75
1.45
1.93
Figure 3 Increase algae growth rate- Mustered Algae
-
Proteins and carbohydrates values:
Table 3: Proteins and Carbohydrate Concentrations in chlorella vulgaris
Day
Proteins
Carbohydrates
Bg11
N-8
Tap
Bg11
N-8
TAP
Day 0
0.29
0.31
0.30
1.72
1.80
1.76
Day 2
0.49
0.55
0.51
1.65
1.78
1.68
Day 4
0.64
0.78
0.69
1.52
1.68
1.59
Day 6
0.89
0.96
0 .93
1.40
1.49
1.45
Day 8
0.78
0.87
0.81
1.18
1.26
1.22
Day 10
0.67
0.70
0.69
0.89
0.96
0.91
Day 12
0.50
0.59
0.56
0.68
0.79
0.71
Day 14
0.40
0.42
0.45
0.57
0.65
0.63
Day 16
0.34
0.38
0.33
0.53
0.62
0.57
Day 18
0.32
0.35
0.36
0.51
0.60
0.59
Table 4: Proteins and Carbohydrate Concentrations in mustered algae
-
Aeration values:
Table 5: Aeration time for 5 medias for algae growth
s.no
Organism
aeration
media
growth rate
Lipid (%)
on
off
1
Chlorella Vulgaris
18
24
6
0
Bg-11
1.25
0.81
16%
14%
Mustered algae
18
24
6
0
Bg-11
1.55
0.89
19%
13%
2
Chlorella vulgaris
18
24
6
0
N8
1.01
0.61
12%
9%
Mustered algae
18
24
6
0
N8
1.23
0.67
15%
10%
3
Chlorella vulgaris
18
24
6
0
Tap
0.99
0.81
14%
13%
Mustered algae
18
24
6
0
Tap
0.41
0.16
4%
2%
-
Light period:
Table 6: Different light period for 5 medias for algae growth
S.
no
organism
light period
media
growth rate
Lipid (%)
light
dark
1
Chlorella Vulgaris
24
6
4
0
18
20
Bg-11
1.60
0.96
0.88
19%
14%
13%
Mustered algae
24
6
4
0
18
20
Bg-11
1.75
1.09
0.99
27%
15%
14%
2
Chlorella vulgaris
24
6
4
0
18
20
N8
1.53
0.92
0.81
18%
14%
13%
Mustered algae
24
6
4
0
18
20
N8
1.45
0.97
0.81
16%
14%
13%
3
Chlorella vulgaris
24
6
4
0
18
20
TAP
1.55
1.01
0.85
18%
15%
13%
Mustered algae
24
6
4
0
18
20
TAP
1.93
1.61
1.07
29%
19%
14%
-
Lipids extracted:
Table 7: Lipids percentages from Chlorella vulgaris
MEDIA
Bg-11
N-8
TAP
% of lipids
45%
28%
Day
Proteins
Carbohydrates
Bg11
N-8
Tap
Bg11
N-8
TAP
Day 0
0.44
0.35
0.44
0.39
0.33
0.33
Day 2
0.47
0.46
0.47
0.40
0.34
0.37
Day 4
0.51
0.48
0.51
0.43
0.41
0.38
Day 6
0.52
0.49
0.53
0.48
0.44
0.40
Day 8
0.54
0.50
0.54
0.50
0.46
0.41
Day 10
0.59
0.56
0.61
0.52
0.48
0.46
Day 12
0.62
0.60
0.62
0.39
0.33
0.33
Day 14
0.66
0.63
0.68
0.54
0.49
0.50
Day 16
0.67
0.64
0.69
0.59
0.51
0.52
Day 18
0.70
0.65
0.71
0.62
0.57
0.56
Figure 4: The production of Biodiesel from algae
-
Viscosity :
Table 8: Mustard algae biodiesel viscosity values at 60 rpm
Viscosity values
Bg-11
N-8
Tap
Viscosity (cP)
3.96
3.6
3.6
RPM
100
100
100
Temp ()
31
29.7
28.9
Torque
6.6
6.6
6.6
spindle
61
61
61
Table 9: Chlorella vulgaris algae biodiesel viscosity values at 100 rpm
Viscosity values
Bg-11
N-8
TAP
Viscosity (cP)
4.40
4.14
4.40
RPM
100
100
100
Temp (0C)
29.4
29.7
28.6
Torque
6.6
6.6
6.6
Spindle
61
61
61
-
DISCUSSION
The chlorella vulgaris has the capability to produce lipids (in vitro) from which the biodiesel can be produced that would replace the fossil fuels. The biodiesel produced from the algae acts as an alternative fuel. In this production process, the chlorella vulgaris and mustered (yellow) algae are cultured in three different medias viz. Bg 11, N8, TAP medium. The conditions essential for the growth of the algae in their respective medium are maintained which include light, temperature, nutrients, aeration, pH. After the incubation period, growth was observed as shown in figure 1. For all the medias, the growth biomass for chlorella vulgaris was ensured on every alternate day during the incubation period, which is tabulated in table 1. The biomass is calculated from the turbidity values by using lab-India UV VIS spectrophotometer UV 3000+. The algal biomass values have gradually increased which is shown in the histogram representation (Figure 2). Similarly, for all the medias, the growth biomass for mustered algae was checked on alternative days during the incubation period, as shown in table 2. The biomass is calculated from the turbidity values by using lab-India UV VIS spectrophotometer UV 3000+. The algal biomass values have gradually increased day by day which is shown in the histogram representation (figure 3). In comparision of the both chlorella vulgaris and mustered algae biomass values, it is observed that mustered algae have shown high values compared to the chlorella vulgaris.
The protein and carbohydrates values for the chlorella vulgaris and mustered algae were measured on alternative days during the incubation period as shown in table 3 and table 4 respectively. From these, it can be inferred that the carbohydrates and proteins (provided in the media) are utilized for the growth, maintenance of the algae and lipid. So, they first increased and later decreased in all three medias. In comparision of the protein and carbohydrates values among chlorella vulgaris and mustered algae, we can infer that mustered algae have high amounts of proteins and chlorella vulgaris have high amounts of carbohydrates.
The effect of aeration time on the growth rate and lipid production is observed for both chlorella vulgaris and mustered algae for different medias as shown in table 5. It can be inferred that both chlorella vulgaris and mustered algae have highest growth and lipid content for Bg11 media at 24hrs aeration which is recorded as 1.55 and 19% respectively.
The effect of light period on the growth rate and lipid production is observed for both chlorella vulgaris and mustered algae for different medias as shown in table 6. It can be inferred that chlorella vulgaris have highest growth and lipid content for Bg11 media at 24hrs light exposure which is recorded as 1.60 and 19%; whereas mustered algae have highest growth and lipid content for TAP media at 24hrs light exposure which is recorded as 1.93 and 29%.
The lipids were extracted from chlorella vulgaris and from mustered algae, by treating algae with the solvents like hexane and chloroform, followed by incubation at boiling temperatures. The estimation of the lipid percentage were tabulated in table 7 and graphically represented in the figure
-
From the tabulated values, it can be inferred that highest percentages of lipids were obtained from Bg11 media i.e. 45%.
The lipids extracted were treated with methanol in the presence of catalyst KOH to undergo the transesterification reaction. This mixture was left undisturbed for 2 hours in a separating funnel. Two layers were observed in which the top layer is biodiesel and bottom layer is glycerin. The upper layer is separated and filtered. The biodiesel yield was obtained as 10.3% at 25 – 320C.
For the obtained biodiesel, the viscosity of the biodiesel was measured for mustered algae and chlorella vulgaris at 100 rpm which are tabulated in table 8 and 9 respectively. From the tabulated values, it can be inferred that Bg11 medium showed highest viscosity values of 3.96cP and 4.40cP for mustered algae and chlorella vulgaris respectively.
-
-
CONCLUSION
Microalgae biodiesel is the only renewable biodiesel that has the potential to completely displace liquid transport fuels derived from petroleum. Existing demand for liquid transport fuels could be met sustainably with biodiesel from microalgae, but not with bioethanol from sugarcane. Algal biomass needed for production of large quantities of biodiesel could be grown in photo bioreactors, but a rigorous assessment of the economics of production is necessary to establish competitiveness with petroleum-derived fuels. Achieving the capacity t inexpensively produce biodiesel from microalgae is of strategic significance to an
environmentally sustainable society. Extensive efforts are already in progress to achieve commercial scale production of micro-algal oil, but for the moment.
The biodiesel yield in our study is 10.3%. The endeavor to compare different media for the biodiesel production was conquered. The inclusive study suggests that the BG11 media has extensive scope for the algae growth and development; high lipid content and production of biodiesel.
-
REFERNCES
-
-
Belay, A. M. H. A.. Mass culture of Spirulina outdoorsthe Earthrise Farms experience. Spirulina platensis, 1997, pp. 131-158.
-
Chisti, Y. Biodiesel from microalgae. Biotechnology advances, 2007, 25(3), 294-306.
-
https://www.iea.org/data-and-statistics/charts/annual-change-in- biofuel-production 2018-2020
-
Darzins, A., Pienkos, P., &Edye, L. Current status and potential for algal biofuels production. A report to IEA Bioenergy Task, 2010, 39(13), 403-412.
-
Hill, J., Nelson, E., Tilman, D., Polasky, S., & Tiffany, D. Environmental, economic, and energetic costs and benefits of biodiesel and ethanol biofuels. Proceedings of the National Academy of sciences, 2006, 103(30), 11206-11210.
-
Dinh, L. T., Guo, Y., & Mannan, M. S. Sustainability evaluation of biodiesel production using multicriteria decisionmaking. Environmental progress & sustainable energy, 2009, 28(1), 38-46.
-
Torzillo, G., Pushparaj, B., Bocci, F., Balloni, W., Materassi, R., &Florenzano, G. Production of Spirulina biomass in closed photobioreactors. Biomass, 1986, 11(1), 61-74.
-
Di Lucia, L. Too difficult to govern? An assessment of the governability of transport biofuels in the EU. Energy Policy, 2013, 63, 81-88.
-
Heredia-Arroyo, T., Wei, W., Ruan, R., & Hu, B.. Mixotrophic cultivation of Chlorella vulgaris and its potential application for the oil accumulation from non-sugar materials. Biomass and bioenergy, 2011, 35(5), 2245-2253.
-
Cheirsilp, B., & Torpee, S. Enhanced growth and lipid production of microalgae under mixotrophic culture condition: effect of light intensity, glucose concentration and fed-batch cultivation. Bioresource technology, 2012, 110, 510-516.
-
Shen, X. F., Qin, Q. W., Yan, S. K., Huang, J. L., Liu, K., & Zhou,
S. B. Biodiesel production from Chlorella vulgaris under nitrogen starvation in autotrophic, heterotrophic, and mixotrophic cultures. Journal of Applied Phycology, 2019, 31(3), 1589-1596.
-
Farzandi, R., Nayebzadeh, H., Hokmabadi, M., & Saghatoleslami,
N. Optimization of Biodiesel Production Conditions Using Chlorella vulgaris Microalgae Cultivated in Different Culture Medium: Statistical Analysis. Iranian (Iranica) Journal of Energy & Environment, 2020, 11(3), 212-220.
-
Jensen, S. K. (2008). Improved Bligh and Dyer extraction procedure. Lipid Technology, 20(12), 280-281.M. Y. Chisti, Biodiesel from microalgae, Biotechnology Advances, 2007, pp. 294-3.