
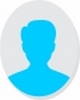
- Open Access
- Authors : Mahesh Kavimandan , Bassetti Chandrasheker
- Paper ID : IJERTV10IS010024
- Volume & Issue : Volume 10, Issue 01 (January 2021)
- Published (First Online): 08-01-2021
- ISSN (Online) : 2278-0181
- Publisher Name : IJERT
- License:
This work is licensed under a Creative Commons Attribution 4.0 International License
Design and Analysis of an Aristo Robot Arm under Varying Load Conditions
Mahesh Kavimandan
Cyient Ltd. (Hyderabad)
Bassetti Chandrasheker
Cyient Ltd. (Hyderabad)
Abstract A robot is an advanced device which is multifunctional and reprogrammable, designed to move parts, material, tools or any specialized devices through variable programmed motions to execute a range of tasks across various sectors. An Aristo robot is a six-axis articulated robot. Articulated robots are powered by a variety of means and can be used to lift small parts with great accuracy. They are used in various tasks to reduce human efforts such as painting, welding and assembly. The main aim of this paper is to make a model & analyze the six-axis robot arm for industrial applications. The robot is capable of lifting up to 2.5Kgs of payload. In this paper, static and fatigue analysis analyses will be done on the robot arm under varying load conditions. Static analysis will be done to analyze the stresses and displacements and fatigue analysis is done to analyze the life, damage. Modeling will be done in Pro/Engineer and analysis will be done in Solidworks.
KeywordsAristo Robot Arm
-
INTRODUCTION
A robotic arm is defined generally as a mechanical arm, usually programmable, with similar functions replicating to that of a human arm. The arm can be a complete mechanism or can be part of a more complex robot. The links of these manipulator are connected through joints, allowing either translational displacement or rotational motion. The links form a kinematic chain and its terminus is called the end effector.
Articulated arms are the manipulators that emulate the characteristics of a human arm. All the joints in such arms are rotary in nature. The motion of articulated robot arms varies from the motion of the human arm. While robot joints have fewer degrees of freedom, they will move through greater angles. For example, the elbow of an articulated robot can bend up or down whereas an individual can bend their elbow only in one direction concerning the straight arm position. Many applications don't require arms with articulated (or revolute) geometries. Simple geometries that involve prismatic or sliding joints are usually adequate. Prismatic and revolute joints represent the other extremes of a universal screw. In a revolute joint, the screw pitch is zero, constraining the joint to the pure rotation. In a prismatic joint, the pitch is generally infinite, constraining the joint fixed to pure sliding motion. Revolute joints are often preferred due to their strength, low friction and reliability of ball bearings. Joints that allow a combination of translation and rotation are not used to join the links of robot arms. Manipulators are grouped into classes in consistent with the combination of joints utilized in their construction.
The end effector, or robotic hand, are often designed to perform any desired task like welding, gripping, spinning, etc., counting on the appliance. For instance in industrial application, robotic arms in assembly lines perform a spread of tasks like welding and parts rotation and placement during assembly. In some scenarios, robots are designed to conduct bomb disarmament and disposal, where having close emulation of the human hand is desired.
A Cartesian geometry arm (sometimes called a gantry crane) uses only prismatic joints and may reach any position in its rectangular workspace by Cartesian motions of the links. By replacing the waist joint of a Cartesian arm with a revolute joint, a cylindrical geometry arm is made. This arm uses a combination of rotation and translation and can reach any point in its cylindrical workspace (a thick-shelled cylinder). If the shoulder joint is additionally replaced by a revolute joint, an arm with a polar geometry is made. The workspace of this arm is a half thick spherical shell and its end effector positions are labelled using polar coordinates.
Finally, replacing the elbow joint with a revolute joint result in a revolute geometry, or articulated arm. The workspace of an articulated arm is a complex thick-walled spherical shell. The outside of the shell may be a single sphere, but the within may be a set of intersecting spheres.
The kinematics problem is defined because the transformation from the Cartesian space to the joint space and the other way around . The Denavit-Harbenterg (D-H) model of representation is used to design robot links and joints and during this study both the forward and inverse kinematics solutions for this educational manipulator are presented. An effective method is suggested to decrease multiple solutions in inverse kinematics [1]. The SCORBOT-ER Vplus may be a 5-dof vertical articulated robot and every one the joints are revolute. The kinematics problem is defined because the transformation from the Cartesian space to the joint space and the other way around . The Denavit- Harbenterg (D-H) model of representation is employed to model robot links and joints during this study alongside 4×4 homogeneous matrix. SCORBOT-ER Vplus may be a dependable and safe robotic system designed for laboratory and training applications [2]. As for the links of a robot arm, the Denavit-Hartenberg (D-H) coordinate transformation method is usually used. The six axes data of the robot arm are often obtained from the Inverse Kinematics analysis. Through the Simulink function of Matlab software, we will make the forward or inverse kinematics computation of the robot arm. In the
control aspect, the PC based controller and therefore the DSP based 8 axis motion control card were wont to control the robot arm [3]. The goal of trajectory planning is to explain the requisite motion of the manipulator as a time sequence of joints/link/end- effectors locations and derivatives of locations, in our work we aim to style a serial robot which is suitable for welding application for a curved profiles , where forward kinematics
,inverse kinematics are calculated and simulation of end effector is done for given joint and link parameters and final work space of arm is identified and graphs associated with motion of manipulator as a time sequence of joints ,links are achieved using roboanalyzer software [4].
The Pravak Robot Arm is defined as a 5-Degree of Freedom robot having all the joints as revolute. The kinematics problem is defined because the transformation from the Cartesian space to the joint space and the other way around . In this study the Denavit- Hartenberg (D-H) model is employed to model robot links and joints. Pravak Robot Arm may be a simple and safe robotic system designed for laboratory training and research applications [5]. The inverse kinematic model & robotic arm control was employed using LabVIEW and ARM microcontroller. LabVIEW uses parallel communication to transfer joint angles of the robot arm to the ARM. ARM microcontroller uses five PWM (Pulse Width Modulation) signals so as to regulate the robot arm, which was ready with servo motors. Robot arm is ideally controlled manually through the LabVIEW GUI (Graphical User Interface) controls [6]. A representation D-H forward and inverse matrix is obtained generally. An analytical solution for the forward and inverse kinematics of 5 DOF robotic arm presented, to research the movement of arm from one point in space to a different point. The 5 DOF robotic arm is a vertical articulated robot, with five revolute joints [7]. A plethora of complex mathematical processes is reduced using basic trigonometric within the modeling of the robotic arm. Modelling and analysis approach is usually tested and a 5 DOF arm with a gripper tpe of styling end effector which is mounted to an iRobot Create mobile platform [8]. The inverse kinematic solutions are obtained employing a hybrid combination of Neural Networks and symbolic logic Intelligent. The experimental validation was also attempted on robotic manipulator to trace a desired trajectory [9]. The new formulation method is predicated on screw theory and quaternion algebra. Screw theory is an efficient thanks to establish a worldwide description of a rigid body and avoids singularities thanks to the utilization of the local coordinates. The dual quaternion, the foremost compact and efficient dual operator to a precise screw displacement was used as a screw motion operator to get the formulation during a compact closed form. Inverse kinematic solutions were obtained using Paden-Kahan subproblems [10]. The humanoid arm consists of 6 RC servo motors, main controller board & a mechanical structure and its trajectory is generated using geometrical analysis. Here total length of robot arm and angle of rotation are considered at each joint. To get the required position provided by user, each joint moves in such way that optimal motion path is generated [11].
-
COMPUTER AIDED DESIGN
Computer Computer Aided Design also named as CAD, is a technique in which a blend of man and machine knowledge are put into problem solving team, intimately coupling the best characteristics of each. The result of this agglomeration works better than either man or machine would work alone and by using a multi discipline approach, it offers wide advantages of integrated team work.
The advances in Computer Science and Technology emerged a very powerful hardware and software tool. It is used in the entire design process resulting in improved quality of design. The emergency of CAD as a field of specialization will help the engineer to acquire the knowledge and skills needed in the use of these tools in an effective way on the design process.
CAD is an interactive process, where the exchange of information between the designer and the computer is made as simple and effective as possible. Computer aided design encompasses a broad variety of computer based methodologies and tools for a spectrum of engineering activities . It is more concerned with the use of computer-based tools to support the entire life cycle of engineering system
-
PRO/ENGINEER
PRO/ENGINEER is a feature based program used for parametric solid modeling. As such, it's use significantly differs from conventional drafting programs. In conventional drafting which can be either manual or computer assisted, various views of a part are created in an attempt to describe the geometry. Here, each view incorporates various featural aspects like surfaces, cuts, radii, holes and protrusions but the features are not individually defined while in feature based modeling, each feature is individually described then later integrated into the part.
Another unique attribute of Pro/ENGINEER is that it is a solid modeling program and the design procedure is to create a model, view it and assemble parts as required, then generate any drawings which are required. It should be noted that for many uses of Pro/E, complete drawings are never created, like any other software's out in the market it is continually being developed to include new functionality.
Pro/Engineer is a parametric, feature-based modeling architecture incorporated into a single database philosophy with advanced rule-based design with multiple capabilities. The capabilities of the product is split into the three main labelled heading of Engineering: Design, Analysis and Manufacturing. The software also offers a range of tools to enable the generation of a complete digital representation of the product being designed.
-
SOLID WORKS
SolidWorks is a 3D mechanical CAD program which uses Parasolid-based solid modeler, and utilizes a parametric feature- based approach to make models and assemblies. Parameters request constraints whose values determine the form or shape of the model or assembly and inputs may be numeric parameters
like line lengths, circle diameters, geometric parameters. Numeric parameters are often related to one another through the utilization of relations, which allows them to capture design intent.
Design intent is how the creator of the part wants it to reply to changes and updates. Building a model basically starts by drawing a 2D sketch which consists of geometry such as points, lines, arcs, conics and splines. Dimensions are added to the sketch to define the size and site of the geometry. Relations dont define attributes like perpendicularity, tangency, parallelism and concentricity. The parametric nature implies that the size and relations drive the geometry, not the opposite way around. The dimensions within the sketch are often controlled independently, or by relationships to other parameters inside or outside of the sketch. SolidWorks also includes advanced mating features. These features enable modeled gear assemblies to accurately reproduce the rotational movement of an actual gear train. Finally, drawings are by taking parts or assemblies which are modelled and the views are automatically generated by the solid model, and notes. The drawing module includes most basic paper sizes generally used and standards of modelling.
-
MOTION ANALYSIS
Motion Analysis is generally employed to accurately simulate and analyze the motion of an assembly while incorporating the consequences of time and motion study elements. This includes forces, springs, dampers, and friction. The study combines time and motion study elements with mates in motion calculations. Consequently material properties, motion constraints, mass and component contact are included within the solver calculations. This study analysis also calculates loads which will define load cases for structural analyses.
With SOLIDWORKS Simulation added in, one can perform multiple analysis such as stress, factor of safety or deformation analysis of components. This can be done without fixing loads and boundary conditions. The required loads are obtained automatically from a calculated study. One can use the strain analysis results to display the consequences of motion loads on deformations and stresses for one or more components. One can calculate results for isolated times and time ranges. The stress analysis results don't change the time and motion study results. For detailed stress analysis study, one can export hundreds of inputs at a time to SOLIDWORKS Simulation and perform a combined rigid-flexible body analysis.
-
SOLID WORKS SIMULATION
SolidWorks Simulation represents a design analysis system fully integrated with SolidWorks. SolidWorks Simulation accommodates one screen solution for stress, frequency, buckling, thermal, and optimization analyses and is powered by fast solvers. This software enables you to unravel large problems quickly using your pc and comes in several bundles to satisfy your analysis needs.
This software shortens time to plug by saving time and energy in checking out the optimum geometry. A development cycle generally includes the subsequent steps:
-
Building your model.
-
Building a prototype of the design.
-
Testing the prototype in the field.
-
Evaluating the results of the field tests.
-
Modifying the design considering the field test results as a base.
-
The above steps are repeated until a satisfactory solution is reached. Further analysis can help us accomplish the following tasks:
-
Cost reduction by simulating the testing of model on the computer rather than expensive field tests.
-
Market time reduction by reducing the number of product development cycles.
-
Improve product quality by testing multiple concepts and cases before making a final decision giving a cushion of time for the design concepts.
Te software uses the Finite Element Method (FEM). FEM may be a numerical technique for analyzing engineering designs. FEM is accepted because of its standard analysis method. Thanks to its generality and suitability for computer implementation. FEM divides the model into many small pieces of straightforward shapes called elements, effectively replacing a complex problem by many simple problems that require to be solved simultaneously. Elements share common points called nodes. The process of dividing the model into small pieces is named meshing.
The behavior of every element is well-known under all possible support and cargo scenarios. The finite element method utilizes elements with various shapes. The response at any point in a component is interpolated from the response at the element nodes. Each node is fully described by variety of parameters counting on the analysis type and therefore the element used. For example, the temperature of a node completely describes its response in a thermal analysis. For structural analyses, the response of a node is described, generally, by three translations and three rotations. These are called degrees of freedom (DOFs). Analysis using FEM is named Finite Element Analysis (FEA). The software formulates the equations governing the behavior of every element taking into consideration its connectivity to other elements. These equations respond to known material properties, restraints, and loads. Next, the program organizes the equations into an outsized set of simultaneous algebraic equations and solves for the unknowns. For example, in stress analysis, the solver finds the displacements at each node followed by the program that calculates strains and stresses.
-
-
MOTION ANALYSIS OF ROBOTIC ARM
Fig. 1: Models of various components in Solid Works
Firstly, we model each component of robotic arm as shown in Figure1 in the Solid Works software. Later we will have to check the SolidWorks Motion Add-In feature and make sure that SolidWorks Motion Add-In is activated.
To do so:
-
Click Tools, Add-Ins. The Add-Ins dialog box appears.
-
Make sure that the check boxes next to SolidWorks Motion are checked.
-
Click OK.
Fig. 2: Complete assembly of modelled parts
-
Switch to SolidWorks Motion by clicking the Motion Study 1 tab in the bottom left hand corner.
Fig. 3: Switching to SolidWorks Motion Manager
-
Fixed and moving components in SolidWorks Motion are determined by their Fix/Float status in the SolidWorks model. In our case, Bottom component (i.e) part name First -1 is fixed while the other three links are moving.
Fig. 4: Fixing moving components and applying mates
-
Mates applied in assembly. Rotate Link2 by 3 degrees clockwise about the Base. To do this we will impose a rotary motion to Link2 at the location of the concentric mate simulating the pin connection with the Base. The angular displacement needs to be achieved in 1 sec and we will use a step function to ensure that Link2 rotates smoothly from 0 to 3 degrees.
-
Click on the Motor icon to open the Motor dialog. Under Motor Type select Rotary Motor.
-
Under Component/Direction, select the cylindrical face of Link2 pinned to the Bottom (see the figure) for both the Motor Direction and Motor Location fields. The motor will be located at the center of the selected cylindrical face.
SolidWorks offers three types of the assembly motion simulation:
-
Animation is simple motion simulation ignoring the components inertial properties, contacts, forces and similar. Its use is suited for the verification of the correct mates or basic animations, for example.
-
Basic Motion offers some level of realism by accounting for the inertial properties of the components for example. It does not, however, recognize externally applied forces.
-
Motion Analysis is the most sophisticated motion analysis tool reflecting all required analysis features such as inertial properties, external forces, contacts, mate friction etc.
-
-
Under Type of Study on the left hand side of the SolidWorks Motion Manager, select Motion Analysis.
SPEED 1000rpm
Results Forces Motor torque magnitude – Rotarymotor3
Fig. 5: Results Forces Motor torque magnitude – Rotarymotor3
The above plot diagram represents the initial results of torque or rotary motor 3 which is plotted against time at 1000 rpm. We observe that the frequency increases and decreases in stepped pattern.
Fig. 6: Results Forces Motor Torque Magnitude Rotarymotor4
The above plot diagram represents the initial results of torque or rotary motor 4 which is plotted against time at 1000 rpm. We observe that the frequency gradually and reaches a peak value at 1.02 seconds and then decrease while remaining constant throughout.
-
-
STRUCTURAL ANALYSIS OF ARISTO ARM CONSIDERING LOADS FROM MOTION ANALYSIS
Once the loads from motion analysis are obtained, we perform structural analysis on each modelled part of the aristro arm and determine loads, stess and strain for each part. The following selections are made for all the components at the beginning of out analysis.
-
Select Add in Simulation
-
Select Simulation Import Motion Loads
-
Select Parts to Import motion loads First, Second, Third and Fourth Enter Frame No.
-
MATERIAL STEEL
-
BASE PART (FIRST)
TABLE 1: LOADS AND FIXTURES FOR FIRST PART
The above table represents the various loads and fixtures applied for the base part.
TABLE 2: LOAD DETAILS FOR FIRST PART
The above table represents the various loads applied at each location and their reference points.
Name
Type
Min
Max
Stress1
VON: von Mises Stress
2.75868e-012
N/mm^2 (MPa)
Node: 116
2.03681e-
006
N/mm^2 (MPa)
Node: 26
FIRST-1-CM2-ALT-Frame-40-Stress-Stress1
Name
Type
Min
Max
Displacem ent1
URES:
Resultant Displacement
0 mm
Node: 1
6.74869 e-010
mm Node: 257
FIRST-1-CM2-ALT-Frame-40-Displacement- Displacement1
Name
Type
Min
Max
Stress1
VON: von Mises Stress
2.75868e-012
N/mm^2 (MPa)
Node: 116
2.03681e-
006
N/mm^2 (MPa)
Node: 26
FIRST-1-CM2-ALT-Frame-40-Stress-Stress1
Name
Type
Min
Max
Displacem ent1
URES:
Resultant Displacement
0 mm
Node: 1
6.74869 e-010
mm Node: 257
FIRST-1-CM2-ALT-Frame-40-Displacement- Displacement1
TABLE 3: STUDY RESULTS FOR FIRST PART
The above table represents the study results of stress, displacements and the strain developed in the first part on application of various loads.
-
LINK 1 (SECOND PART)
TABLE 4: LOAD AND FIXTURE DETAILS FOR SECOND PART
The above table represents the various loads applied and fixture locations for the second part.
TABLE 5: STUY RESULTS FOR SECOND PART
Name
Type
Min
Max
Stress1
VON: von Mises Stress
0.634561
N/mm^2 (MPa)
Node: 22010
4666.3
N/mm^2 (MPa)
Node: 57519
SECOND-1-CM2-ALT-Frame-101-Stress-Stress1
Name
Type
Min
Max
Displacement1
URES:
Resultant Displacement
0.00348095
mm Node: 29528
3.77132
mm Node: 369
SECOND-1-CM2-ALT-Frame-101-Displacement-Displacement1
Name
Type
Min
Max
Strain1
ESTRN:
Equivalent Strain
2.17286e-006
Element: 7262
0.0156498
Element: 17985
SECOND-1-CM2-ALT-Frame-101-Strain-Strain1
Name
Type
Min
Max
Strain1
ESTRN:
Equivalent Strain
4.76671e-017
Element: 26042
6.54421e-012
Element: 11566
FIRST-1-CM2-ALT-Frame-40-Strain-Strain1
Name
Type
Min
Max
Strain1
ESTRN:
Equivalent Strain
4.76671e-017
Element: 26042
6.54421e-012
Element: 11566
FIRST-1-CM2-ALT-Frame-40-Strain-Strain1
The above table represents the study results of stress, displacements and the strain developed in the second part on application of various loads.
-
LINK 2 (THIRD PART)
TABLE 6: LOAD AND FIXTURE DETAILS FOR THIRD PART
THIRD-1-CM2-ALT-Frame-101-Displacement-Displacement1
Name
Type
Min
Max
Strain1
ESTRN:
Equivalent Strain
3.41446e-006
Element: 564
0.0179628
Element: 8778
THIRD-1-CM2-ALT-Frame-101-Strain-Strain1
THIRD-1-CM2-ALT-Frame-101-Displacement-Displacement1
Name
Type
Min
Max
Strain1
ESTRN:
Equivalent Strain
3.41446e-006
Element: 564
0.0179628
Element: 8778
THIRD-1-CM2-ALT-Frame-101-Strain-Strain1
The above table represents the various loads applied and fixture locations for the third part.
TABLE 7: STUDY RESULTS FOR THIRD PART
The above table represents the study results of stress, displacements and the strain developed in the third part on application of various loads.
-
LINK 3 (FOURTH PART)
Name
Type
Min
Max
Stress1
VON: von Mises Stress
0.455
N/mm^2 (MPa)
Node: 62551
5013.41
N/mm^2 (MPa)
Node: 7044
THIRD-1-CM2-ALT-Frame-101-Stress-Stress1
Name
Type
Min
Max
Displacement1
URES: Resultant Displacement
0 mm
Node: 1
5.93568
mm Node: 489
Name
Type
Min
Max
Stress1
VON: von Mises Stress
0.455
N/mm^2 (MPa)
Node: 62551
5013.41
N/mm^2 (MPa)
Node: 7044
THIRD-1-CM2-ALT-Frame-101-Stress-Stress1
Name
Type
Min
Max
Displacement1
URES: Resultant Displacement
0 mm
Node: 1
5.93568
mm Node: 489
TABLE 8: LOAD AND FIXTURE DETAILS FOR THIRD PART
The above table represents the various loads applied and fixture locations for the fourth part.
TABLE 9: STUDY RESULTS FOR FOURTH PART
Name
Type
Min
Max
Stress1
VON: von Mises Stress
0.180572
N/mm^2 (MPa)
Node: 52764
770.486
N/mm^2 (MPa)
Node: 62219
FOURTH-1-CM2-ALT-Frame-101-Stress-Stress1
Name
Type
Min
Max
Displacement1
URES:
Resultant Displacement
0 mm Node: 8489
0.139476
mm Node: 61965e:
489
FOURTH-1-CM2-ALT-Frame-101-Displacement- Displacement1
Name
Type
Min
Max
Strain1
ESTRN:
Equivalent Strain
6.64156e-007
Element: 12162
0.00249797
Element: 10446
FOURTH-1-CM2-ALT-Frame-101-Strain-Strain1
The above table represents the study results of stress, displacements and the strain developed in the fourth part on application of various loads
-
RESULTS TABLE
TABLE 10: RESULTS OF EACH PART AT DIFFERENT RPM
BASE PART
LINK 1
LINK 2
LINK 3
1000
rpm
STRESS (N/mm2)
5.28E-7
3.523
8.518
92.1269
DISPLACEMENT
(mm)
1.75E-10
0.0135
0.01
0.0216
STRAIN
1.699E-12
1.068E-5
2.644E-5
0.00029
2000
rpm
STRESS (N/mm2)
2.037E-6
4666.3
5013.41
7704.86
DISPLACEMENT
(mm)
6.74E-10
3.77132
5.935
13.9
STRAIN
6.55E-12
0.0156
0.01796
0.0249
The above table is the compilation of results of stess, strain and displacement of all the parts at a rpm of 1000 and 2000.
-
-
STRUCTURAL ANALYSIS ON TOTAL ASSEMBLY
After performing individual analysis on each part, er now perform the same analysis on the complete assembeled part. The followig observations are made as shown below.
Model name: total_assm Current Configuration: Default
<L_MdInf_SldBd_Nm/>
Treated As
Volumetric Properties
Imported1
Solid Body
Mass:0.287925
kg Volume:3.7392 8e-005 m^3 Density:7700 kg/m^3 Weight:2.8216 6 N
Imported1
Solid Body
Mass:0.255933
kg Volume:3.3238 1e-005 m^3 Density:7700 kg/m^3 Weight:2.5081 4 N
Imported1
Solid Body
Mass:0.19195
kg Volume:2.4928 5e-005 m^3 Density:7700 kg/m^3 Weight:1.8811 1 N
Imported1
Solid Body
Mass:1.67231
kg Volume:0.0002 17183 m^3
Density:7700 kg/m^3 Weight:16.388 6 N
Model name: total_assm Current Configuration: Default
<L_MdInf_SldBd_Nm/>
Treated As
Volumetric Properties
Imported1
Solid Body
Mass:0.287925
kg Volume:3.7392 8e-005 m^3 Density:7700 kg/m^3 Weight:2.8216 6 N
Imported1
Solid Body
Mass:0.255933
kg Volume:3.3238 1e-005 m^3 Density:7700 kg/m^3 Weight:2.5081 4 N
Imported1
Solid Body
Mass:0.19195
kg Volume:2.4928 5e-005 m^3 Density:7700 kg/m^3 Weight:1.8811 1 N
Imported1
Solid Body
Mass:1.67231
kg Volume:0.0002 17183 m^3
Density:7700 kg/m^3 Weight:16.388 6 N
TABLE 11: MODEL INFORMATION OF THE ASSEMBLY
The above table represents the model information of the complete assembly along with the information when each component is selected individually.
TABLE 12: STUDY PROPERTIES OF ASSEMBLY MODEL
Study name
Static 2
Analysis type
Static
Mesh type
Solid Mesh
Thermal Effect:
On
Thermal option
Include temperature loads
Zero strain temperature
298 Kelvin
Include fluid pressure effects from SolidWorks Flow Simulation
Off
Solver type
FFEPlus
Inplane Effect:
Off
Soft Spring:
Off
Inertial Relief:
Off
Incompatible bonding options
Automatic
Large displacement
Off
Compute free body forces
On
Friction
Off
Use Adaptive Method
Off
The above table represents the study properties of the complete assembly which we are going to use in our analysis.
TABLE 13: UNITS
assembly file. The material we have considered is steel and these properties are defined for it.
Imported1
Solid Body
Mass:3.77859
kg Volume:0.0004 90726 m^3
Density:7700 kg/m^3 Weight:37.030 2 N
The above table represents the units that we are going use in our analysis.
TABLE 14: MATERIAL PROPERTIES OF THE ASSEMBLY
Properties
Name: Alloy Steel
Model type: Linear Elastic Isotropic
Default failure criterion: Max von Mises Stress Yield strength: 6.20422e+008 N/m^2 Tensile strength: 7.23826e+008 N/m^2 Elastic modulus: 2.1e+011 N/m^2 Poisson's ratio: 0.28
Mass density: 7700 kg/m^3
Shear modulus: 7.9e+010 N/m^2
Thermal expansion 1.3e-005 /Kelvin
coefficient:
Imported1
Solid Body
Mass:1.83917
kg Volume:0.0002 38853 m^3
Density:7700 kg/m^3 Weight:18.023 9 N
Imported1
Solid Body
Mass:0.963455
kg Volume:0.0001 25124 m^3
Density:7700 kg/m^3 Weight:9.4418 6 N
The above table represents the various material properties of our
Imported1
Solid Body
Mass:3.77859
kg Volume:0.0004 90726 m^3
Density:7700 kg/m^3 Weight:37.030 2 N
The above table represents the units that we are going use in our analysis.
TABLE 14: MATERIAL PROPERTIES OF THE ASSEMBLY
Properties
Name: Alloy Steel
Model type: Linear Elastic Isotropic
Default failure criterion: Max von Mises Stress Yield strength: 6.20422e+008 N/m^2 Tensile strength: 7.23826e+008 N/m^2 Elastic modulus: 2.1e+011 N/m^2 Poisson's ratio: 0.28
Mass density: 7700 kg/m^3
Shear modulus: 7.9e+010 N/m^2
Thermal expansion 1.3e-005 /Kelvin
coefficient:
Imported1
Solid Body
Mass:1.83917
kg Volume:0.0002 38853 m^3
Density:7700 kg/m^3 Weight:18.023 9 N
Imported1
Solid Body
Mass:0.963455
kg Volume:0.0001 25124 m^3
Density:7700 kg/m^3 Weight:9.4418 6 N
The above table represents the various material properties of our
TABLE 15: LOAD AND FIXTURE DETAILS FOR ASSEMBLY PART
The above table represents the various loads applied and fixture locations for the assembly part.
Mesh type
Solid Mesh
Mesher Used:
Standard mesh
Automatic Transition:
Off
Include Mesh Auto Loops:
Off
Jacobian points
4 Points
Element Size
10.7628 mm
Tolerance
0.538139 mm
Mesh Quality
High
Remesh failed parts with incompatible mesh
Off
Total Nodes
20945
Total Elements
11074
Maximum Aspect Ratio
13.939
% of elements with Aspect Ratio < 3
85.5
Mesh type
Solid Mesh
Mesher Used:
Standard mesh
Automatic Transition:
Off
Include Mesh Auto Loops:
Off
Jacobian points
4 Points
Element Size
10.7628 mm
Tolerance
0.538139 mm
Mesh Quality
High
Remesh failed parts with incompatible mesh
Off
Total Nodes
20945
Total Elements
11074
Maximum Aspect Ratio
13.939
% of elements with Aspect Ratio < 3
85.5
TABLE 16: MESH DETAILS FOR ASSEMBLY MODEL
Unit system:
SI (MKS)
Length/Displacement
mm
Temperature
Kelvin
Angular velocity
Rad/sec
Pressure/Stress
N/m^2
% of elements with Aspect Ratio > 10
0.515
% of distorted elements(Jacobian)
0
Time to complete mesh(hh;mm;ss):
00:00:03
% of elements with Aspect Ratio > 10
0.515
% of distorted elements(Jacobian)
0
Time to complete mesh(hh;mm;ss):
00:00:03
The above table represents the study results of stress, displacements and the strain developed in the assembly part on application of various loads
The above table represents the details of the mesh we are going to use before performing the analysis.
Name
Type
Min
Max
Stress1
VON: von Mises Stress
0
N/mm^2 (MPa)
Node: 1
37.9092
N/mm^2 (MPa)
Node: 12215
total_assm-Static 2-Stress-Stress1
Name
Type
Min
Max
Displacement1
URES:
Resultant Displacement
0 mm
Node: 1
0.0017066
3 mm Node: 5633
total_assm-Static 2-Displacement-Displacement1
Name
Type
Min
Max
Strain1
ESTRN:
Equivalen t Strain
0
Element: 1
0.000130404
Element: 4425
total_assm-Static 2-Strain-Strain1
Name
Type
Min
Max
Stress1
VON: von Mises Stress
0
N/mm^2 (MPa)
Node: 1
37.9092
N/mm^2 (MPa)
Node: 12215
total_assm-Static 2-Stress-Stress1
Name
Type
Min
Max
Displacement1
URES:
Resultant Displacement
0 mm
Node: 1
0.0017066
3 mm Node: 5633
total_assm-Static 2-Displacement-Displacement1
Name
Type
Min
Max
Strain1
ESTRN:
Equivalen t Strain
0
Element: 1
0.000130404
Element: 4425
total_assm-Static 2-Strain-Strain1
TABLE 17: STUDY RESULTS FOR ASSEMBLY PART
-
CONCLUSION
In this paper, a robotic arm with 3 degrees of freedom is designed and modeled using Pro/Engineers and Solid Works. Static analysis is performed to calculate the stresses by considering the forces. The material used is Steel .By observing the results, the stress values are less than the strength of the material. By applying load of 2000Kgs on the arm, motion analysis is performed on the robotic arm manipulator to calculate position forces. The analysis is performed at different motor speed of 1000rpm, 2000rpm.
Structural analysis is performed on the individual parts of the assembly by importing motion loads from motion analysis. By results we observe that the robotic arm is failing at the speed of 2000rpm since the stresses developed are greater than the allowable stress value of steel. So we can conclude that Aristo Robot Arm rotating at 1000rpm is better combination.
REFERENCES
-
Koyuncu, B. and Güzel, M., 2007. Software development for the kinematic analysis of a Lynx 6 robot arm. World Academy of Science, Engineering and Technology, 30, p.2007.
-
Verma, A. and Deshpande, V.A., 2011. End-effector position analysis of scorbot-er vplus robot. International Journal of Smart Home, 5(1), pp.1-6.
-
Zou, J.T. and Tu, D.H., 2011, May. The development of six DOF robot arm for intelligent robot. In 2011 8th Asian Control Conference (ASCC) (pp. 976-981). IEEE.
-
Kumar, K.K., Srinath, A., Anvesh, G.J., Sai, R.P. and Suresh, M., 2013. Kinematic analysis and simulation of 6-DOF KUKAKr5 robot for welding application. International Journal of Engineering Research and Applications, 3(2), pp.820-827.
-
Shah, J.A., Rattan, S.S. and Nakra, B.C., 2013. End-effector position analysis using forward kinematics for 5 DOF pravak robot arm. IAES International Journal of Robotics and Automation, 2(3), p.112.
-
Mouli, C.C., Jyothi, P., Raju, K.N. and Nagaraja, C., 2013. Design and implementation of robot arm control using labview and arm controller. IOSR Journal of Electrical and Electronics Engineering, 6(5), pp.80-84.
-
Deshpande, V. and George, P.M., 2014. Kinematic Modelling and Analysis of 5 DOF Robotic Arm. International Journal of Robotics Research and Development (IJRRD), 4(2), pp.17-24.
-
Clothier, K.E. and Shang, Y., 2010. A geometric approach for robotic arm kinematics with hardware design, electrical design, and implementation. Journal of Robotics, 2010.
-
Manjaree, S., Agarwal, V. and Nakra, B.C., 2013. Kinematic analysis using neuro fuzzy intelligent technique for robotic manipulator. International Journal of Engineering Research and Technology, 6(4), pp.557-562.
-
Sariyildiz, E. and Temelta, H., 2012. A new formulation method for solving kinematic problems of multiarm robot systems using quaternion algebra in the screw theory framework. Turkish Journal of Electrical Engineering & Computer Sciences, 20(4), pp.607-628.
-
Pirjade, Y.M., Londhe, D.R., Patwardhan, N.M., Kotkar, A.U., Shelke, T.P. and Ohol, S.S., 2020, February. Design and Fabrication of a Low-cost Human Body Lower Limb Exoskeleton. In 2020 6th International Conference on Mechatronics and Robotics Engineering (ICMRE) (pp. 32-37). IEEE.