
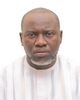
- Open Access
- Authors : A.M. Mukaddas , A. M. Maleka , A. Saidu , A. Shu’Aibu
- Paper ID : IJERTV11IS070056
- Volume & Issue : Volume 11, Issue 07 (July 2022)
- Published (First Online): 27-08-2022
- ISSN (Online) : 2278-0181
- Publisher Name : IJERT
- License:
This work is licensed under a Creative Commons Attribution 4.0 International License
Behaviour of Rubberised Fibre Sandcrete Hollow Blocks In Building As Masonry Structural Element
1* 2 3
-
Mukaddas
*1,2,3 4
, A. M. Maleka , A. Saidu , A. Shuaibu4
CivilEngineeringDepartment,Federal
Polytechnic,Bauchi,BauchiState,Nigeria.
Abstract:- The high increase in construction cost has dictated the need for the utilization of waste recycling and eco-friendly materials in the production of sustainable building products. Rubberised fibre reinforced sandcrete blocks have been developed by employing treated crumb rubber 10%-30% partial replacement of sand at 10% increment with 1.0% oil palm fruit fibre (OPFF) addition in the matrix. It was aimed at developing structural elements, typically load bearing masonry wall and beam. Rubberised fibre sandcrete block (RFSB) beam of size 705 x 150 x 243 mm using 1:2.75 mix ratio with 0.48 w/c ratio and infill matrix. Subsequently, a wall panel size 1m high by 0.9m length and 0.15m thick consisting of 12units stretcher blocks (S) and 6 units of half stretcher block (HS) was also constructed and tested. A systematic investigation of the 4 set of batch of rubberised fibre mortar (FRM) cubes, 25 RFSB beams and 3 units of RFSB wall panels were produced and tested under vertical load compression. Results were experimentally analysed and compared with theoretical predictions, crack patern were equally observed including first crack with corresponding load to failure. RFM Blocks were used to produce beams of size 705 mm x 150 mm x 243 mm by joining them with 1:2.75 mortar and the hollow infilled with plain mortar, rubberised fibre mortar and concrete mix proportions, cured and tested at 28 days. The experimental results revealed that only the maximum design load of 125.78kN/m rose beyond the allowable design load (87.62kN/m) derived from the theoretical analysis and design, while the minimum design load is slightly at par with it. This is mainly due to the energy absorption characteristics of the crumb rubber and OPFF used in the matrix. However, the minimum experimental design load falls short of the allowable theoretical analysis and design load by close to half as expected. However, results of the first phase were lower than the theoretical predictions. Although the tests samples generally didnt fail due to flexure but failed due to shear stresses at the supports by cracking and peeling which was attributed to strength and density variations between the infill and sandcrete blocks as well as the rubberised fibre sandcrete blocks. The first cracks appeared at 25% of its ultimate load at 0.75 of wall height. The cracks rarely appeared showing that RSFBW panel is not having much of tensile stress as the load increases but crushing cracks appeared most between the blocks bed joints. However, as the load reached 150 kN, tensile cracks becomes critical at the left side of walls until it failed at 200 kN.
Keywords: Treated crumb rubber; Oil Palm fruit fibre; Rubberised fibre sandcrete hollow block; In-Plane loading; Masonry Structural Element.
-
INTRODUCTION
From the last decade, construction cost in Nigeria has been increasing significantly. This situations lead to incapability of middle class people to own their house as most of the stakeholders aimed for bigger projects such as apartment and estate and sell it for higher prices. Hence, the need to develop affordable and sustainable low and medium cost house/building elements to help the lower income people to have their own house. Due to various project-related factors which delayed the completion time of projects or make construction cost higher, the individuals are faced with an uphill task to acquire building. The high cost of conventional building materials in Nigeria and its continues increase and the countrys inability to embrace and adopt the locally available and processed materials system have continue to instill hindrances created by the construction materials sector in low-cost Housing delivery [1]. Over dependence on reinforced concrete structural elements such as beams and columns in single and double building structure is on the increase thereby increasing construction cost. Hence, the need to significantly reduce the dependence on reinforced concrete elements in single to double storey buildings by the production of those reinforced concrete elements by the utilization of unconventional building materials (green materials) such as rubberized fibre sandcrete blocks applications as load bearing structural elements. Green materials as composites are rapidly gaining attention in the construction, automobile, marine, aerospace, and locomotive systems as sustainable construction materials.
Vegetable fibre reinforced concrete blocks have gained special attention due to low-cost and large availability globally. They are known for the enhancement of mechanical properties of cement based matrix. Similarly, there is increase in tensile strength, toughness, ductility, absorption of energy from applied loads/impact thereby controlling openings and minimizing crack propagation while giving room for large deformation of the matrix without losing its structural integrity.
The incorporation of vegetable fibre in building materials influences mechanical properties to advantage as reported by many researchers [2-3]. They reported that mechanical, thermal and physical properties of cement-based composites is enhanced when cellulosic or vegetable fibre are incorporated in the cementitious matrix thereby resulting in the increase in flexural strength,
toughness and impact resistance, reduce shrinkage, thermal conductivity and sound absorption increment. Various species of vegetable fibre had been incorporated into cementitious matrix for both structural and non-structural applications amongst which are: rice husk [4], luffa fibres [5], bamboo fibres [6,7], jute [6], palm leaves [8], Hemp [9], pineapple leaf [10], Sisal [11 13], and oil palm fruit fibre [1417] e.t.c.
Similarly, Use of tyres waste such as crumb rubber as sand replacement produce flowable concrete which results showed successful lightweight concrete (1.2 1.6g/cm3) with a 28 days compressive strength ranging between 0.269 1.194 MPa [18]. Flowable concrete can be applicable in bridge abutment fills, trench fills and foundation fills. Apart from that, Aruntas et al. [19] mentioned that a high volume replacement of sand by rubber waste (1-4mm) has lower durability performance assessed by freeze-thaw exposure, seawater immersion and high temperature cycles. The use of a 10% replacement is feasible for regions without harsh environmental conditions.
This research is to employ the usage of waste materials; scrap tyre waste and Oil Palm Fibre. Previous works on scrap tyre as aggregates replacement in concrete by many researchers [1923] etc. have concluded that scrap tyre replacement will reduce the compressive strength of concrete. Hence, Aziz et al. [15] and Mukaddas et al. [17] had conducted a research to improve the mechanical and durability properties of mortar with scrap tyre replacement by adding the oil palm fibres and succeeded with positive outcome. Consequently, this research seek further the viability of utilizing rubberized fibre mortar in the production of blocks used as structural masonry element in buildings as a way to reduce cost and over dependence on concrete elements for a single to double story structures for the low income earners.
Therefore, rubberized fibre sandcrete hollow blocks was used as main materials in the production of the prototype structural elements in this study. However, the application of rubberized fibre sandcrete hollow locks as reinforced concrete masonry element has not yet been established. As a load-bearing walls element, the strength and behavior of blocks unit and as a reinforced element are primary important factor needed to be concerned with. Therefore, an investigation to its performance in terms of its structural response as a masonry structural element was investigated. Masonry load bearing wall have been used since the early civilizations. However, due to huge rise in the cost of land and bricklayer, structural frame was introduced and it replaced the use of structural masonry (Sinha, 2002).
As the knowledge grows by years, masonry has been used again as load bearing wall especially in countries where steel industry is absent, masonry construction becomes the most economical structure. Cement concrete blocks was first used in USA in 1940s and later widely used in 1950s as load bearing wall construction in concrete blocks became popular. On the other hand, Thailand introduced concrete hollow block as partition wall due to low quality production, subsequently it was improved and the product was used resulting in springing up of 15 functional major plants in 1980s. The popularity of the hollow blocks construction also spread to China during the same years where 10 to 12 storey building was constructed using masonry blocks [25].
Similar research had been conducted in Great Britain but the masonry units involved have always been manufactured under factory control conditions. Rubberized fibre sandcrete hollow blocks are not going to be manufactured under such conditions and it also contains waste tyre rubber and oil palm fruit fibre and theses will probably vary in strength. Part of the project is to determine such strength variations. Similarly, Crawford [26] conducted research on the initial phase into the feasibility of locally produced sandcrete hollow blocks being used as reinforced masonry structural element in buildings.
2.1. Cement
-
MATERIALS
Ordinary Portland Cement (OPC) conforming to type I cement was used throughout the research.
-
Fine aggregates
Sand was obtained from a local quarry along Bauchi-Dass road in Nigeria and it has a maximum grain size of 2.36 mm passing sieve no.4 in accordance with ASTM C33[27] specification for fine aggregates. and can be classified as fine sand in zone II of aggregates for concreting as shown in Figure 1 having specific gravity, particle density and absorption of 2.63, 1702 kg/m3 and 2.0% respectively.
Sand & crumb rubber
Figure 1: Sand and crumb rubber grading
-
Crumb rubber aggregates (CR)
Crumb rubber as in Figure 2(a) shredded locally by shoe coblers in a local market in Bauchi state, Nigeria was used to replace fine aggregate. It particles sizes ranges from 4.75 mm to less than 150 µm. It was clean as no impurities such as steel, thread or any other materials that could be detrimental to its performance was observed. The crumb rubber was graded in the same particle size as the fine mineral aggregate passing ASTM sieve no.4 and was pre-treated with cement paste before used in the mix in accordance with [15] and [17] to improve its mechanical and durability properties respectively.The crumb rubber pre- treatment process was carried out by soaking it in water for a minimum period of one (1) day, then it was dried in an open air container until a saturated surface dry (SSD) condition was reached. After which it was mixed with dry composite cement powder in a tilting concrete mixer until a homogeneous mix was achieved. The treated crumb rubber (TCR) was then air dried as shown in Figure 2(b). The compacted density and fineness modulus of the treated crumb rubber aggregate was determined to be 668 kg/m3 and 0.9 respectively in accordance with [28] as presented in Table 1. Moisture content (MC) and water absorption (WA) of the TCR were not determined due to the fact that, the cement coating on the crumb rubber will be washed off during the testing process. The crumb rubber is also a non absorbant material, thus repel water on its surface. The crumb rubber used in this research is from cracker mill process.
-
(b)
Figure 2: Soaked and Treated (TCR) crumb rubber aggregate.
Table 1: Physical properties of fine and crumb rubber aggregates used
*
*
*Treated crumb rubber is a non-absorbent material, hence MC and WA not determined.
-
-
Oil palm fruit fiber (OPFF)
-
-
The OPFF was obtained freely from a palm oil plantation in Nigeria having an average diameter of 0.025 mm. The length of OPFF ranges between 30 to 50 mm length in order to prevent yarning and unevenly distributing itself within the mortar mix. This will overcome the fibre balling effect with the view of achieving the optimum result [29]. The amount of OPFF added in the mortar mix is based on the weight of cement.
3 EXPERIMENTAL WORKS
RFM Blocks were used to produce beams of size 705 mm x 150 mm x 243 mm by joining them with 1:2.75 mortar and the hollow infilled with plain mortar, rubberised fibre mortar and concrete mix proportions, cured and tested at 28 days. In all, 25 beams were tested.
-
Sandcrete and rubberised fibre sandcrete hollow blocks (RFSB) were produced.
-
Theoretical analysis and design was carried out to obtain allowable design loads and reinforcements required for a known beam size.
-
Structural steel rods were prepared as per the designed output.
-
25 Nos. Sample beams of size 705 mm x 150 mm x 243 mm were produced by joining blocks with 1:2.75 mortar and the hollow infilled with the following mix proportions:
-
1:6 mix ratio: – mortar – 5Nos beams
-
1:2.75 mix ratio: – F0CR0 – 5 Nos beams
-
F1.0CR10 – 5Nos beams
-
F1.0CR20 – 5 Nos beams
-
-
1:3:2 mix ratio : – concrete – 5Nos beams
-
-
The samples were cured for 28 days and tested for flexure by determining the flexural load at first crack and at failure, the failure modes was also observed and noted.
-
Results were then compared with the theoretical predictions.
-
Mix Proportions/ Mixing, Curing and Testing
The adopted mix design was in accordance with ASTM C270 [30] having a water cement ratio of 0.48 and cement to a FA ratio of 1: 2.75 in line with [16]. Minimum target strength of 17 MPa is designed as the control mortar mix. The optimum crumb rubber substitution of 0%, 10% and 20% by volume fraction of aggregate was used. While addition of oil palm fibre (OPFF) of 0% and 1.0% by weight of cement content and mixing processes was adopted in tanderm with [1517]. Mix designs were prepared and the detail of the mixes is presented in Table 2. The pan mixer was used for the production of the mix throughout for the production of the mortar for block production as well as the mix for the infills.
-
The hollow block was placed on a 250 mm x 250 mm oiled wooden platform in a vertical position and wetted with water.
-
Infill was poured in the block hollow up to the cover depth for the reinforcement and the reinforcement cage inserted into the hollow.
-
Infill was added to fill up the block hollow containing reinforcement cage in 3 approximate equal layers and each layer tamped 21 times with 16 mm diameter steel rod.
-
After filling the first hollow block, 25 mm 1:2.75 mix mortar was place around the thickness of the block before the next block was placed on it by guiding it around the protruding reinforcement cage.
-
The process of wetting, filling and compaction were repeated up to the last block to complete the beam.
-
The beam is now complete and allowed to set by staying overnight Figure 3. The beam was then placed horizontally and covered with jute sack and wetted twice daily for 7 days thereafter left under lab condition until testing at 21 days.
-
The beam was place on the flexural testing apparatus and load gradually applied until failure while noting/recording the maximum load causing failure and the failure mode.
-
Table 2: Mix Design for TCR and Fibre Mortar (1.0 m3)
Mix Percentage (%) |
Cement Content (g) |
Fine Aggregate (g) |
Crumb Rubber (g) |
Water Content (g) |
Fibre (g) |
F0 CR0 |
740.0 |
2035.0 |
0.0 |
399.6 |
– |
F1.0 CR10 |
740.0 |
1831.5 |
80.0 |
395.5 |
7.4 |
F1.0 CR20 |
740.0 |
1628.0 |
159.8 |
391.5 |
7.4 |
F1.0 CR30 |
740.0 |
1424.5 |
239.8 |
387.4 |
7.4 |
In the first column of the table under mix percentage, the samples are notated as F0CR0 where ;F is OPFF, the first ;0 is % content of fibre, CR is crumb rubber and the second,0 is the % content of the crumb rubber. The same notations are applied in explaining the samples.
Figure 3: Hollow block beam assembly with reinforcement and infill
-
Blocks Production
Control samples of sandcrete blocks (CSB) and rubberised fibre sandcrete blocks (RFSB) were produced under laboratory conditions in the Concrete Workshop of Civil Engineering Department, Federal Polytechnic Bauchi (FPTB). The mix was as described in section 3.1. The mix was poured into the mould in three approximately equal layers and tamped 25-27 times each and demoulded immediately by slipping the mould upwards away from the mortar. Visual inspections of the blocks were done immediately for any possible defect such as the existence of any segregation and skewness of the block due to tamping and during slipping of the mould upward. Blocks which have satisfied conditions were then covered with polythene sheet for 24 hours before transferring them into the curing tank for ponding and some covered with jute sack for 28 days curing.
-
Test Wall Setup
Wall specimen was prepared according to BS 5628-1 [31] with a minimum cross-sectional area of 0.125 m2. The size of wall panel used was 1 m in height, 0.9 m length and 0.15 m thickness which consist of 12 units of stretcher blocks (S) and 6 units of half stretcher blocks (HS) for each type of wall sample. These blocks are stacked on top of each other with approximately 25 mm mortar joint layers and painted white so that the crack deformation can be easily and clearly observed.
-
Compressive Strength
The test was done in accordance to BS 1881-116 [32] where the horizontal dimension of the specimen were checked. Cube having size 50 mm x 50 mm x 50 mm was used for sampling of mortar cubes for the compressive strength test. The compressive strength test was done to 3 samples each at 3 days, 7 days and 28 days respectively. The maximum load and stress applied to the cube was recorded.
-
Individual Block Strength Test
Test on 20 samples each of stretcher and half stretcher blocks for both CSB and RFSB were performed to determine compressive strength at 28 days only. Two wooden platens were placed at top and bottom of the blocks to ensure even distribution of load.
-
Test of Block Wall Panel under Vertical Load
Only 1 unit of Control Wall and 2 units of RFSB Wall were tested resulting in 3 units of wall panel tested under vertical load compression where: Control WallBlocks produced with sandcrete mortar only; and RFSB WallBlocks produced with rubberised fibre mortar
The wall performance was obtained by using steel frame connected to hydraulic jack and steel spreader beam which transfers the load from the jacks to the walls as shown in Figure 6. A total of 6 unit Linear Variable dial gauge were used for wall deformation measurements.
-
Wall Panel Test
-
The panel wall was assembled inside the main frame test as shown in Figure 4, while the secondary frame used to hold Dial guage placed at both sides of the wall surface at 1/4, 1/2 and 3/4 heights from the bottom of wall panel to measure both lateral and in-plane deformation of wall. Two Dial guage were placed at the both side on the top of wall with its needle touched the spreader beam in order to measure the vertical deformation of the wall. Boundary condition at the top of wall was arranged to allow rotation and prevent lateral deformation at the top by using two steel shafts of 50 mm in diameter, with two steel channels in both ends were clamped to the main frames by four clamps. At the bottom of the wall the boundary condition was arranged to prevent rotation and lateral deformation by using steel beam at both sides. Rubber was placed at the top of the wall to provide a level surface. A spreader beam was placed at the top of the wall to transfer the applied load at a rate of 1 N/mm2 per minute.
Figure 4: Wall Test Set-up
4 RESULTS AND DISCUSSION
-
Compressive strength
The compressive strength test was conducted using 50 mm cube specimens produced from hydraulic cement mortar in accordance with the requirement of ASTM C109 [33] at 3, 7 and 28-days. The cube specimens were cured until the test day. The strength behaviour of the specimens in compression was compared to all samples produced based on the effect of treated crumb rubber (TCR) substitution, oil palm fruit fibre (OPFF) addition, and the combine effect of the two materials. The summary of the average compressive strength of the samples is presented in Table 3. The addition of 1.0% OPFF resulted in the significant strength improvement. This showed that OPFF can be added to produce RFM with compressive strength up to 33MPa at 20% TCR with a similar trend for 30% TCR. The increase in the mix can be attributed to the homogeneity and improved parking of the constituents cement mix. This similar behaviour was also mentioned by [34, 35]. It further showed that by increasing OPFF improves bond strength where the fibre positively contributed to improving strength because of its interconnectivity and inter-wovenness which absorbs and resist stresses from load. These happens as it stretches out due to its tensile abilities and transfer its stresses to the constituent materials resulting in the sustenance of the applied load on the specimen with increase in the compressive strength due to the even distribution of the fibre within the matrix as also demonstrated by Aziz et al. [15].
Table 3: Average compressive strength of mortar sample
S/N. Mix Ref.
Minimum Strength(MPa) 28 days compressive strength(MPa) [36]
1. F0 CR0 37.5
-
F1.0 CR10 28.4 Above the limit of 17 MPa
-
F1.0 CR20 33.0 being the optimum strength for structural lightweight
-
F1.0 CR30 20.8 mortar
-
-
Test Beams Result
The results for the test for the beams at failure were determined by dividing the dial gauge readings with the beam span and self- weight of beam subtracted (this is done because the theoretical design load does not include beam self-weight). The analysis of the raw data is presented Table 4. The experimental results indicated that the type of infill made a significant impact to the
flexural and shear strength of the beam, just as it made to the compressive strength. Hence, the analyses for all the results were combined in Table 4 to experimentally determine the minimum design load based on statistical and probability theories as presented.
Table 4: Statistical Results of Infill Test Beams
Beam Ref
X
X-Xa
(X-Xa)^2
A1
58
-20.2
408.04
A2
34
-44.2
1953.64
A3
41
-37.2
1383.84
A4
50
-28.2
795.24
A5
39
-39.2
1536.64
B1
41
-37.2
1383.84
B2
49
-29.2
852.64
B3
50
-28.2
795.24
B4
41
-37.2
1383.84
B5
33
-45.2
2043.04
C1
118
39.8
1584.04
C2
107
28.8
829.44
C3
102
23.8
566.44
C4
101
22.8
519.84
C5
95
16.8
282.24
D1
103
24.8
615.04
D2
99
20.8
432.64
D3
95
16.8
282.24
D4
101
22.8
519.84
D5
96
17.8
316.84
E1
99
20.8
432.64
E2
103
24.8
615.04
E3
107
28.8
829.44
E4
95
16.8
282.24
E5
98
19.8
392.04
x =
1955
(
) =
21036
= 78.2,
=
95
=
()^ = 29.01
=
100
= 37.097%
=
3( )
1.737
The distribution data from the result is acceptable and its considered a normal univariate distribution as it falls between the
range of ± 2 [37].
Minimum design load will be:
= 1.64 = 30.62/
Maximum design load:
. = + 1.64 = 125.78 , Mean design load = = 78.2
The experimental results revealed that only the maximum design load of 125.78kN/m rose beyond the allowable design load (87.62kN/m) derived from the theoretical analysis and design, while the minimum design load is slightly at par with it. This is mainly due to the energy absorption characteristics of the crumb rubber and OPFF used in the matrix. However, the minimum experimental design load falls short of the allowable theoretical analysis and design load by close to half as expected.
-
Beam Failure Mode Crack Pattern
The beam failure mode was characterized by shear failure at the supports which occurred first as cracks at the supports and propagate gradually in size resulting in peeling at the edges and supports as shown in Figure 5 and Figure 6 respectively. These failure characteristics is commonly associated with conventional hollow block systems [38]. However, Test beams series D and E exhibited flexural cracking at the centre in form of hair line crack then gradually propagated in size until failure (rupture) as expected due to the crumb rubber and fibre within the matrix.
Figure 5: First mode of failure showing hairline cracks at the supports only
Figure 6: Final failure mode showing wider cracks and peeling at the supports
However, results of the first phase were lower than the theoretical predictions. Although the tests samples generally didnt fail due to flexure but failed due to shear stresses at the supports by cracking and peeling which was attributed to strength and density variations between the infill and sandcrete blocks as well as the rubberised fibre sandcrete blocks.
-
Compressive Strength of Block Wall
The compressive test were conducted on a series of hollow blocks made from 1:2.75 mortar and rubberised fibre sandcrete mortar in accordance with BS5628-1 [31]. The strength was calculated by dividing ultimate load achieved to bearing area of cross section of the panel while the ultimate design load calculated as earlier presented. The ultimate load achieved by wall panel is an important result in this investigation to conclude the acceptance of lightweight rubberised fibre mortar block as a load bearing structural element. The summary of this results tabulated in Table 5.
Table 5: Summary of Compressive Strength of Masonry Walls
Sample |
Pre-compressive Load from spreader beam |
First Crack Load |
Ultimate Design Load, ND |
Ultimate Testing Load, NE |
Compressive strength, E |
(kN) |
(kN) |
(kN) |
(kN) |
(N/mm2) |
|
Control |
1.23 |
70.35 |
169.73 |
280.35 |
3.89 |
10% TCR |
1.23 |
33.76 |
101.65 |
168.02 |
2.33 |
30% TCR |
1.23 |
46.63 |
124.71 |
205.97 |
2.86 |
-
Crack Pattern of Wall Panel
The failure of pattern of rubberised fibre sandcrete block wall panel is as shown in Figure 7. The first cracks appeared at 25% of its ultimate load at 0.75 of wall height. The cracks rarely appeared showing that RSFBW panel is not having much of tensile stress as the load increases but crushing cracks appeared most between the blocks bed joints. However, as the load reached 150 kN, tensile cracks becomes critical at the left side of walls until it failed at 200 kN.
-
Front View (b) Left View
-
Figure 7: Failure of RFSBW panel
4.6 Vertical-Displacement of Wall Panel
The axial displacement of un-stiffened rubberised fibre sandcrete block wall (RFSBW) tested panels is shown in Figure 8 which are control cement mortar matrix panel 1:2.75 and RFSBW with 10% and 30% CR replacement and 1.0% OPFF addition tested under the action of axial load. The panels recorded different structural responses were the control and RFSBW-10 specimen displayed similar trend and having almost same initial value of stiffness which was higher than that of RSFBW-30. The increase in initial stiffness upon increase in applied load could be as a result of the presence of composite materials (crumb rubber and OPFF) which gave the mortar the ability to absorb more energy, as also demonstrated in [38]. The panels displacement increased up to 2.8 mm, 5.29 mm and slightly higher for panel RFSBW-30 which rosed up to 6.14 mm before a change in pattern occurs. This is particular possible because of the increase in quantity of crumb rubber. After the initial displacement, the wall started to act as a rigid body hence the response became different compared to conventional masonry. This is a normal behavior of composite masonry walls where the material exhibits absorption characteristics of the applied load. After this point, the displacement rates become more constant and the panels strength increased significantly with the applied load until it reached its ultimate capacity of 176 N, 291 kN and 220 kN with maximum deflections of 5.91 mm, 10.49 mm and 11.60 mm for control panel, RSFBW-10 and RSFBW-30 respectively.
Figure 8: Load-Deflection Relationship of Wall Panel showing first crack
4.7 Out of Plane Lateral Displacement of Wall Panel
The Lateral displacement of wall shell was determined by recording readings of the dial gauges located along the centerline of the tested panel at 1/4, 1/2 and ¾ from the bottom of wall height as earlier shown in Figure 6. Uniform compression load was applied from the top of the walls which was distributed and transferred to the wall shells in each side resulting in lateral displacement of the walls. The behavior of wall was assessed by measuring the wall lateral deflection over its own height as shown in Figure 9 and Figure 10. The deflection profiles against the height of wall are plotted at 10 kN load increment up to the maximum applied load.
1
Height of wall(m)
0.75
0.5
0.25
0
10
20
30
40
50
60
0 200 400 600 800 70
Deflection(mm) 80
Fig 13: Lateral Deflection Profile of Panel with 10% Rubberized Fibre Mortar (RFM)
From the plotted profile (Figure 9), it showed that the wall deflected with an increase in applied load, the deflection propagates gradually when more load was been applied. Although when the deflection occurred, it has shown that the highest deflection occurred at 0.75 panel height as expected with a value of 599µmm at 80 bar (Figure 10). The wall panel containing 30% CR showed that the wall deflected with increase in load, the deflection occur as more load was been applied although as the deflection occur it has shown that at 0.75, occur the highest deflection with the value 183µmm at 80 pressure (bar).
1
Height of wall
0.75
0.5
0.25
0
10
20
30
40
50
60
70
0 50 100 150 200 250 80
Dflection (µmm)
Fig 14: Lateral Deflection Profile of Panel with 30% Rubberized Fibre Mortar (RFM)
-
Conclusions
5 CONCLUSIONS AND RECOMMENDATIONS
The behaviour of the rubberised fibre sandcrete hollow blocks as masonry structural element in building were investigated with respect to load bearing hollow block walls and infill block column under in-plane vertical and column axial load. The walls subjected to in-plane loads exhibited a nonlinear lateral displacement with increasing stiffness upon increasing the pre- compressive vertical load applied on the test walls. The pre-compressive vertical load was able to increase the lateral load carrying capacity of the walls which was as a result of equal strength material used for both mortar joints and the block itself. It was also shown that, when the pre- compressive load increases, shear resistance also increases. The failure modes of the rubberised sandcrete hollow block walls under in-plane loading were controlled by diagonal shear failure or moderate toe crushing depending on the level of the pre-compressive vertical loading. Shear failure characterised by the development of sliding along bed joints and opening of vertical joints contributed to a stepped diagonal opening without visible cracking in the blocks for low and moderate pre-compressive loads. The results obtained can be further summarised as follows and recommendations made:
-
The theoretical allowable design loads differs with the experimental minimum and mean design loads by 186.15% and 12.05% respectively.
-
There is every likelihood that the rubberised fibre sandcrete blocks could be used as structural members due to the stress resistance they exhibited during testing and the non spalling/explosive failure mode observed which was attributed to composite materials of this nature.
-
When reinforced as a flexural element, with little or no shear stresses, the experimental tests results had favourably compared with the theoretical predictions in terms of mean and maximum design loads respectively.
-
With higher compressive strength results achieved (33MPa) and a high early first crack value, RFSMB beams can be used in comparison with RC beam in flexure for small dwelling units.
-
-
Recommendations
Based on the outcome of the study, the conclusions suggest the following further areas for further studies:
-
Cost analysis for RFSMB should be performed to determine the economic viability of its usage for building construction.
-
More higher strength block beams should be considered for shear and tensile resistance.
-
Rerun of the experimental work with the use of state of modern testing equipments such as data logger, strain gauges and LVDTs should be employed for accuracy.
-
ACKNOWLEDGEMENTS
The authors are indebted for thetechnical support provided by Civil Engineering Technology Department of The Federal Polytechnic Bauchi, Nigeria and financial support provided by the Tertiary Education Trustfund (TETFUND) under the institution based research.
DISCLOSURE STATEMENT
No potential conflict of interest was reported by the authors
REFERENCES
[1] Y. M. D. Adedeji, Materials preference options for sustainable low-income housing in selected cities in Nigeria, FEDERAL UNIVERSITY OF TECHNOLOGY, AKURE, 2007. [2] F. Pacheco-Torgal and S. Jalali, Cementitious building materials reinforced with vegetable fibres: A review, Constr. Build. Mater., vol. 25, no. 2, pp. 575581, 2011, doi: 10.1016/j.conbuildmat.2010.07.024. [3] M. Ardanuy, J. Claramunt, and R. D. Toledo Filho, Cellulosic fiber reinforced cement-based composites: A review of recent research, Constr.Build. Mater., vol. 79, pp. 115128, 2015, doi: 10.1016/j.conbuildmat.2015.01.035.
[4] A. L. G. Gastaldini, M. P. Da Silva, F. B. Zamberlan, and C. Z. M. Neto, Total shrinkage, chloride penetration, and compressive strength of concretes that contain clear-colored rice husk ash, Constr. Build. Mater., vol. 54, pp. 369377, 2014. [5] Y. Tong et al., Improving cracking and drying shrinkage properties of cement mortar by adding chemically treated luffa fibres, Constr. Build.Mater., vol. 71, pp. 327333, 2014.
[6] K. Okubo, T. Fujii, and Y. Yamamoto, Development of bamboo-based polymer composites and their mechanical properties, Compos. Part A Appl.Sci. Manuf., vol. 35, no. 3, pp. 377383, 2004.
[7] A. A. R. Corrêa, L. M. Mendes, N. P. Barbosa, T. de Paula Protásio, N. de Aguiar Campos, and G. H. D. Tonoli, Incorporation of bamboo particles and synthetic termite saliva in adobes, Constr. Build. Mater., vol. 98, pp. 250256, 2015. [8] F. A. Al-Sulaiman, Mechanical properties of date palm fiber reinforced composites, Appl. Compos. Mater., vol. 9, no. 6, pp. 369377, 2002. [9] H. N. Dhakal, Z. Y. Zhang, and M. O. W. and Richardson, Effect of water absorption on the mechanical properties of hemp fibre reinforced unsaturated polyester composites, Compos. Sci. Technol., vol. 67, no. 78, pp. 16741683, 2007. [10] R. M. N. Arib, S. M. Sapuan, M. Ahmad, M. T. Paridah, and H. M. D. K. Zaman, Mechanical properties of pineapple leaf fibre reinforced polypropylene composites, Mater. \& Des., vol. 27, no. 5, pp. 391396, 2006. [11] F. D. Tolêdo Romildo D., K. Ghavami, G. L. England, and K. Scrivener, Development of vegetable fibre-mortar composites of improved durability,Cem. Concr. Compos., vol. 25, no. 2, pp. 185196, 2003, doi: 10.1016/S0958-9465(02)00018-5.
[12] H. Savastano Jr, S. F. Santos, M. Radonjic, and W. O. Soboyejo, Fracture and fatigue of natural fiber-reinforced cementitious composites, Cem.Concr. Compos., vol. 31, no. 4, pp. 232243, 2009.
[13] H. Savastano, P. G. Warden, and R. S. P. Coutts, Mechanically pulped sisal as reinforcement in cementitious matrices, Cem. Concr. Compos., vol.25, no. 3, pp. 311319, 2003, doi: 10.1016/S0958-9465(02)00055-0.
4, pp. 525529, 2009.
[15] F. N. A. Farah Nora, S. M. Bida, N. A. M. Nasir, and M. S. Jaafar, Mechanical properties of lightweight mortar modified with oil palm fruit fibre and tire crumb, Constr. Build. Mater., vol. 73, no. October, pp. 544550, 2014, doi: 10.1016/j.conbuildmat.2014.09.100. [16] M. Ahmad Musa, F. N. A. Abdul Aziz, and N. A. Mohd Nasir, Effect of Curing Methods on Carbonation Depth of Rubberised Fibre Mortar, Appl.Mech. Mater., vol. 802, no. September, pp. 124129, 2015, doi: 10.4028/www.scientific.net/amm.802.124.
[17] A. M. Mukaddas, F. N. A. Abd Aziz, N. A. Mohd Nasir, and N. Mohamed Sutan, Water Permeability and Chloride and Sulphate Resistance of Rubberised Fibre Mortar, J. Civ. Eng. Sci. Technol., vol. 10, no. 2, pp. 135146, 2019, doi: 10.33736/jcest.1741.2019. [18] E. Ganjian, M. Khorami, and A. A. Maghsoudi, Scrap-tyre-rubber replacement for aggregate and filler in concrete, Constr. Build. Mater., vol. 23, no. 5, pp. 18281836, 2009, doi: 10.1016/j.conbuildmat.2008.09.020. [19] H. Y. Aruntacs, S. Cemalgil, O. Simcsek, G. Durmucs, and M. Erdal, Effects of super plasticizer and curing conditions on properties of concrete with and without fiber, Mater. Lett., vol. 62, no. 19, pp. 34413443, 2008. [20] A. M. Brandt, Fibre reinforced cement-based (FRC) composites after over 40 years of development in building and civil engineering, Compos.Struct., vol. 86, no. 13, pp. 39, 2008, doi: 10.1016/j.compstruct.2008.03.006.
[21] A. J. Aref and W. I. Alnahhal, Experimental evaluation of a hybrid FRP-concrete bridge superstructure system under negative moment flexural loads, Jordan J. Civ. Eng., vol. 1, no. 4, pp. 336343, 2007. [22] M. Hsie, C. Tu, and P. S. Song, Mechanical properties of polypropylene hybrid fiber-reinforced concrete, Mater. Sci. Eng. A, vol. 494, no. 12, pp.153157, 2008, doi: 10.1016/j.msea.2008.05.037.
[23] M. A. E.-G. Ismail, Vot 78238 Study on the Properties of Palm Oil Fiber Mohamed Abdelkader El-Gelany Ismail Faculty of Civil Engineering, 2009. [24] B. SINHA, Development and potential of structural masonry, Semin. sobre Paredes Alvenaria, PB Ed. , pp. 116, 2002. [25] Y. Akao and Q. F. D. QFD, Abdullah, MR, Kamar, KAM, Nawi, MNM, Haron, AT, \& Arif, M.(2009). Industrialised building system: A definition and concept. Proceeding in ARCOM conference, Nottingham, UK 7-9 September 2009 Abdul-Rahman, H., Kwan, CL, \& Woods, CP (1999). Quality functio, J. Qual. \& Reliab. Manag., vol. 16, no. 6, pp. 591605. [26] D. Crawford, Feasibility of Locally Produced Sandcrete Hollow Blocks Being Used As Reinforced Masonry Structural Elements in Building. Dept. of Civil Engineering Technology, Federal Polytechnic, Bauchi. Unpublished Project Report. P1-2., Bauchi, 1994. [27] C. ASTM and others, Standard specification for concrete aggregates, Philadelphia, PA Am. Soc. Test. Mater., 2003. [28] ASTM C128, Standard Test Method for Density, Relative Density (Specific gravity) and Absorption of Fine Aggregates., Philadelphia, PA Am.Soc. Test. Mater., 2007.
[29] M. A. Ismail and H. Bin Hashim, Palm oil fiber concrete, 3rd ACF Int. Conf. ACF/VCA, no. c, pp. 409416, 2008, [Online]. [30] ASTM C270, Standard specification for mix design of hydraulic cement mortars., Philadelphia, PA Am. Soc. Test. Mater., 2005. [31] BS 5628 Part 1, Code of Practice for Use of Masonry., Br. Stand. Inst., 2000. [32] BS 1881 Part 116, Code of Practice for Determination of Compressive Strength of Concrte Cubes, Br. Stand. Inst., 1983. [33] ASTM C109, Standard test method for compressive strength of hydraulic cement mortars (using 2-in, or 50-mm cube specimen), Am. Soc. Test.Mater. West Conshoshocken, PA., 2005.
[34] N. M. Al-Akhras and M. M. Smadi, Properties of tire rubber ash mortar, Cem. Concr. Compos., vol. 26, no. 7, pp. 821826, 2004. [35] T. Gupta, S. Chaudhary, and R. K. Sharma, Assessment of mechanical and durability properties of concrete containing waste rubber tire as fine aggregate, Constr. Build. Mater., vol. 73, pp. 562574, 2014. [36] A. M. Neville and others, Properties of concrete, vol. 4. Longman London, 1995. [37] D. George and P. Mallery, SPSS for Windows step by step. A simple study guide and reference (10. Bask), GEN, Boston, MA Pearson Educ. Inc, vol. 10, 2010. [38] A. Al-fakih, B. Mohammed, and W. Alaloul, Interlocking Bricks for Masonry, no. September, 2018.