
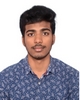
- Open Access
- Authors : K. V. S. L. Dathathreya , Ravindra Andukuri , T. Lakshmi Prathyusha , V. Ramakoteswara Rao, T. Venkata Ratnam
- Paper ID : IJERTV11IS010072
- Volume & Issue : Volume 11, Issue 01 (January 2022)
- Published (First Online): 22-01-2022
- ISSN (Online) : 2278-0181
- Publisher Name : IJERT
- License:
This work is licensed under a Creative Commons Attribution 4.0 International License
An Experimental Study of the TiB2-Reinforced AA7075 Manufactured by the Stir Casting Technique
K.V.S.L. Dathathreya
Department of Mechanical Engineering, RVR & JC College of Engineering, Guntur, India
-
Lakshmi Pratyusha
Department of Mechanical Engineering, GVP College of Engineering Visakhapatnam, India
Ravindra Andukuri Department of Mechanical Engineering, GITAM Institute of Technology, GITAM
Visakhapatnam, India
T. Venkata Ratnam
Naval Science & Technological Laboratory Visakhapatnam, India
V. Ramakoteswara Rao
Department of Mechanical Engineering, RVR & JC College of Engineering, Guntur, India
Abstract – Metal matrix composites based on the aluminium 7075 alloy are widely utilised in structural, aerospace, marine, and automotive applications due to their high strength, light weight, and low manufacturing costs. In this study, an attempt was made to produce an Aluminium Matrix Composites (AMCs') using reinforced AA7075 with TiB2 and compared the characteristics of AMCs by using the stir casting method. AA7075/TiB2 specimens were made with varying wt. % (3, 6, 9, and 12) of TiB2 particles. The results obtained by the experimental studies regarding mechanical properties indicate that increasing the weight percentage of TiB2 in the composition improves the mechanical characteristics such as tensile strength, hardness, impact strength, density, and porosity. A salt spray test was performed to examine the corrosion behaviour of reinforced composites in relation to the parent material. Optical microscopy is used to examine the microstructure of reinforced composites with TiB2 for uniform particle distribution in the aluminium molten phase, and the results are also presented in this paper. The particles of TiB2 were characterised by their uniform distribution, strong connection and excellent AA7075 bonding. The deposition of TiB2 particles improved the AMCs' microhardness and ultimate tensile strength.
Keywords – Stir Casting, Metal Matrix Composites, Microstructure, Mechanical Properties
-
INTRODUCTION
Conventional materials cannot meet the demand for new materials with unexpected combinations of features. Metal matrix Composites (MMCs) have emerged as critical materials for structural, electrical and thermal applications. Modern technologies demand not only strength but also lightweight and improved performance. They are preferred over monolithic commercial composites because they have a higher strength-to-weight ratio and cheaper manufacturing costs. Due to their higher strength, high elastic modulus, and increased
wear resistance over conventional base alloys, reinforced MMCs based aluminium alloys have matured into high- performance materials for the aerospace, chemical, automotive, and transportation industries.
For this, wide range of outstanding features of metal matrix composite with TiB2 reinforcement, many researchers studied and experimented with the mechanical characteristics of Aluminium alloy with TiB2 reinforced matrix composites. AA7075 materials have been widely employed in recent decades to manufacture desirable aerospace and marine applications, turbine casings, missile tail cones, bicycle components, and automotive engine casings, among other things [1,2]. In particular, AMCs' had high strength and increased fatigue and wear resistance [3]. Recent research interests include the AMCs' ability to alter physical, mechanical, and tribological properties, etc., by changing the phase of the component or filler material [4]. The mechanical properties have been significantly improved by adding different wt. % of reinforcing ceramic particles in aluminium alloys. The addition of TiB2, SiC, Al2O3, BaCl2 and reinforced particulates in aluminium increases tensile strength, compressive strength, yield strength, hardness, and bending strength, while ductility decreases [5-9]. TiB2 is a potential choice for AMCs among numerous ceramic reinforcements, due to its multiple desired features. TiB2 is a resistant compound that has outstanding qualities such as a high thermal conductivity, strong hardness and good modular properties. At the reinforcing and matrix contact, TiB2 does not react with aluminium to generate a reaction product [10].
Some investigations of aluminium AMCs reveal a reduction in the friction coefficient and an increase in the weight of percent of graphite particles [11]. The presence of TiB2 particulates in aluminium alloy improves the dimensional
stability while conducting thermal cycling tests. [12]. The AA7075/TiB2 AMCs were manufactured and the hardness, tensile strength and yield over the matrix were improved. [13]. Aluminium provides increased strength, flexibility, high temperature and electric conductivity, but poor stiffness, whereas carbide and fly ash are stronger, stiffer and more resistant to good high temperatures [14, 15].
All processing processes are divided into two groups – solid state processing and liquid state processing. Every method has a limit on AMCs with particular matrix alloy and ceramic particle combinations. Therefore, much focus is put on research in the development of processing techniques for the production of AMCs. Due to its simplicity, ease of modification and application for huge volumes, the liquid processing method is beneficial. The liquid processing approach either includes introducing ceramic particles to the molten metal outside or manufacturing them in the melt. The target underlying the development of aluminium and titanium diboride metal matrix composites to enhance the mechanical properties. Numerous strategies of production of metal-based composites are powder metallurgy, spray deposition, liquid metal infiltration, compression casting, and agitation casting [16-20]. Despite the availability of numerous processes, the stir casting technique is used in large-scale commercial manufacturing of reinforced AMCs. This approach is used in this study because of its simplicity.
The significant impacts of this paper are given as follows:
-
Fabricated AA7075/TiB2 Metal Matrix Composites with varied TiB2 weight percentages using the stir casting or liquid state method.
-
Examined the microstructure of the Metal Matrix Composites for distributing the Aluminium 7075 alloy based TiB2 reinforced particles.
-
Experimentally evaluated the mechanical characteristics of the MMCs and compared them to the base metal Al 7075 and achieved remarkable results.
-
-
MATERIALS AND METHODOLOGY
In the present study, attempted to manufacture AMCs from commercial TiB2. The authors used AA7075 alloy as matrix material to manufacture the AA7075/TiB2 AMCs. Titanium diboride (TiB2) is purchased from M/s. Innovative Growth Enterprises, Luthiana, Punjab, India. AA7075 is commercially available in the local market.
-
Aluminium 7075 Alloy
Aluminium 7075 is one in all the strongest Aluminium alloys obtainable, and it's commonly used for structural components that are subjected to a lot of stress. Zinc is the major alloying element in Aluminium 7075. It has a higher tensile strength than many steel products, as well as good fatigue strength and machinability. It has a weaker corrosion resistance than many other Aluminium alloys, yet it possesses great strength. In AA7075, copper presence makes it more prone to corrosion, but this is a necessary trade-off for such a strong-yet-workable alloy. Gears, shafts, aeroplane parts,
valve parts, low-volume plastic mould tools, and blow moulds for plastic bottles are all examples of applications. s a result, the material for this study was identified. The AA7075 chemical compositions is shown in Table 1.
TABLE 1. AA7075 CHEMICAL COMPOSITIONS
Element
% of composition
Si
0.10 -0.40
Fe
0.2 – 0.50
Cu
1.2 – 2.0
Mn
0.05 – 0.3
Mg
2.1 2.9
Cr
0.18 0.28
Zn
5.1 6.1
Ti
0.2
Others Total
0.15
Al
Balance
-
Titanium diBoride (TiB2)
At high temperatures, titanium diBoride (TiB2) may be a hard ceramic metal with great strength, durability, and wear resistance. Its usage in armour sections is due to its high density along with high modulus of elasticity and compressive strength. Most chemical reagents have little effect on it, and it has exceptional wettability and stability in liquid metals like zinc and aluminium. Crucibles for molten metal, cutting tools, and wear-resistant coatings are also made from it.
In terms of chemical stability, TiB2 is more stable against pure iron than tungsten carbide or silicon nitride. TiB2 resists oxidation in air, hydrochloric, and hydrofluoric acids at temperatures up to 1100°C, but reacts with alkalis, nitric acid, and sulphuric acid. The structure of TiB2 and units in hexagon layers are shown in Figure 1. The TiB2 chemical composition is given in Table 2.
-
(B)
-
Fig 1. (A) Hexagonal TiB2 unit cell (B) Hexagonal layered TiB2 structure [21,22]
TABLE 2. TiB2 CHEMICAL COMPOSITIONS
Element
Titanium
Boron
Carbon
Oxygen
Nitrogen
Iron
Zr
%
67-69
29-32
0.50
0.50
0.20
0.02
0.015
-
-
EXPERIMENTAL METHODOLOGY
-
Stir Casting & preparation of specimens
For the manufacture of AMCs specimens, the stirred casting process also known as liquid casting methodis used, in which a dispersed phase is mechanically mixed with molten metal. After that, the liquid composite material is cast using traditional casting techniques and treated with conventional metal forming technologies.
AMCs were reinforced with TiB2 at a composition of 0, 3, 6, 9, and 12 % by weight. AMCs were fabricated by using a stir casting process, also known as a liquid metallurgical technique. The required quantity of AA7075 was weighed on an electric scale, then filled in a crucible and placed inside the induction furnace. In three hours, the furnace temperature is increased to 800°C, AA7075 melts to a molten form at 800°C. Simultaneously, a mould for casting specimens is prepared. The interior surface of the mould is coated with graphite powder, which provides adhesion. The schematic diagram of stir casting process is illustrated in fig 2. In the muffle furnace, TiB2 in the weight of AA7075 is preheated at 250°C at the same time. The purpose of preheating is to remove moisture from TiB2, to increase the reaction rate when mixed with the base metal.
In the process of stir casting, stirring is performed at 400 rpm to form a vortex in the molten metal. When the vortex is formed, the preheated TiB2 is poured at a constant discharge into the base metal. After mixing, stirring is performed for 6 minutes. While stirring, an inert gas (Argon) was continuously supplied, such that molten metal does not react with atmospheric air. The crucible containing molten AA7075 is taken out and poured into the mould cavity. It is then cooled at room temperature.
Fig 2. Schematic diagram of Stir Casting method
Similarly, the same operations are performed for the remaining types of specimen composites. In AMCs manufacturing, preheated reinforcements are poured simultaneously into the vortex to get proper mixing and then poured into the mould and cooled at room temperature. The process of Sir casting and preparation of mould process is shown in Fig 3.
Fig 3. Stir casting and moulding process
-
Microstructure study
The Microstructures study was carried out for the samples prepared with different AA7075 compositions with different TiB2 percentages of reinforcements using Metascope metallurgical microscope. KELLAR'S REAGENT Etchant is used to etch Aluminium alloys to reveal their grain boundaries and orientations. The Microstructural analysis is performed to ascertain uniform distribution of TiB2 reinforcement in AA7075 metal matrix.
-
Mechanical properties observation
-
Hardness
This test method covers the determination of the Rockwell cum Brinell hardness of metallic materials, using load of 250 kgf, and the size of indenter diameter is 5mm. The test method is carried out according to the test procedure IS 1500:2005 [23]. Brinell hardness number, HBW is a number associated to the applied load and the surface area of the permanent impression. Taking the impression values and calculated the average as a final result of hardness in HBW 5mm/250.
Where, F = Force in N
D = Diameter of the ball in mm
d = mean diameter of the indentation = (d1+d2)/2 in mm
-
Tensile strength
The tensile strength test is performed in line with ASTM E-8 [24] using a computerised Universal Testing Machine. The crossbeam speed is 5.0 mm/min, and the sample rate is
9.103 pts per second. To calculate the final tensile strength, yield strength, and stretch %, a typical tensile test specimen of gauge length 36 mm is utilised. The specimen used for tensile strength is shown in Fig 4.
Fig4. Tensile strength test specimen (ASTM E-8)
-
Charpy impact test
The Charpy impact test (Fig. 5) is used to determine the impact resistance of AA7075/TiB2 at room temperature, according to IS 1757 (Part 1) 2014 [25]. The test piece dimensions are 55mm x 10mm x 10mm in size and must be squarely against the supports, with the notch's plane of symmetry being within 0.5mm of the striker's plane of swing. End stoppers are used to position the specimen test piece length to tolerances in order to achieve this.
Fig 5. Schematic of Charpy impact test
-
Density and porosity
The practical density values of the composite specimens have been obtained experimentally by using a density kit. The theoretical density values are calculated by applying the mixture rule in accordance with reinforcement wt. %. The porosity of the reinforced composite is also calculated and the results are presented in the results and discussion section.
Theoretical density= (Density A* Mass fraction of A)+(Density B* Mass fraction of B)
The Porosity values are calculated using the values obtained by theoretical and practical densities as given below:
Porosity= ((Theoretical Density-Practical Density)/Theoretical density) *100
-
Salt Spray (Fog) test:
In the present work, a salt spray test has been performed in accordance with ASTM B117 [26], in which the specimens are exposed in a closed chamber at 95oF (35oC) to fog emanating from a 5% sodium chloride (NaCl) solution. Rubber wires are used to hang specimens inside the test chamber so that they are sprayed evenly on all sides. The salt spray tests were conducted at M/s. Hyderabad Engineering Lab (M/s. HEL), Hyderabad. All test specimens are placed for five hours in a salt spray chamber before being removed, cleaned with distilled water, and inspected by counting pits.
-
-
-
RESULTS AND DISCUSSIONS
-
-
Microstructure Analysis
Figures 6(a) to 6(d) shows the reresentative microstructures for varied wt. % composition of TiB2 (i.e., 3
%, 6%, 9%, 12%) reinforced with AA7075 AMCs produced by stir casting method. When particulates are introduced externally, a number of variables, including poor weight, poor agitation and density difference between matrix alloy and TiB2 particles, lead to cluster formation. Further, when particles are introduced externally, local melt temperature lowers. The connection between particles is weak in clusters, resulting in low mechanical characteristics. However, the reaction shows excellent bonding in particles in clusters produced by the stir casting approach.
Fig 6. Microstructure of (A) AA7075 + 3% of TiB2 (B) AA7075 + 6% of TiB2 (C) AA7075 + 9% of TiB2 (D) AA7075 + 12% of TiB2
The microstructure of the composites exposed that TiB2 particles are scattered equally and uniform particles are existing in the metal matrix. This indicated that stir casting process used for the manufacture of the specimens are satisfactory. Furthermore, the microstructure of AA7075/TiB2 made by stir casting indicated a strong bond between the matrix alloy and the reinforcement particles.
-
Mechanical properties
The mechanical properties including hardness, tensile strength, percentage elongation, impact strength, density, porosity, and corrosion test results of AA7075/ TiB2 specimens are examined experimentally for this study.
-
Hardness
The Rockwell cum Brinell hardness tester has been used to test the hardness of all test samples using a ball indenter, and the hardness results were recorded. In Figure 7, the hardness number (HBW) is plotted for varied percentage of TiB2 composites. The mechanical hardness of the AA7075 is improved the inclusion of wt.% of TiB2.
Fig 7. Comparison of hardness with wt. % of TiB2
The test results depicted that, the hardness is enhanced with the increase of weight % of TiB2 in AA7075. This is owing to the increased surface area of the matrix and the smaller grain size of TiB2 particles, which are harder than AA7075 particles. The presence of hard TiB2 particles controls the deformation of the Hardness tester during indentation.
-
Tensile test
A computerised Universal Testing Machine is used to test the ultimate tensile strength and percentage of elongation. Figure 8 depicts that the tensile strength and percentage of elongation output of the test results for varied wt. percent of TiB2.
From the test results, the tensile strength is improved and the elongation % is reduced compared to the basic material with the addition of TiB2 particulates. The tensile strength of the base material to AMCs increased from 80.17 N/mm2 to
199.8 N/mm2 respectively. Subsequently, % of elongation of the base material to AMCs also decreased from 2.6 to 1.2 respectively. The incorporation of increased wt. percent of TiB2 with the basic material produces the best results in comparison with the AA7075. The tensile test specimens are also shown in the Figure 8.
Fig 8. Tensile strength with variation % of TIB2
The displacements obtained when ultimate load acting on different samples varied wt. % of TiB2 reinforced with AA7075 is shown as Tensile Load Vs Displacement curves (Fig. 9).
Fig 9. Tensile Load vs Displacement graph
The stir casting technique results in defect-free TiB2 particles that maintain their integrity under tensile loading. The TiB2 particle refines aluminium grains, providing more surface area to withstand the stress. The transparent and excellent bonding interfaces delay particle separation from the aluminium matrix. Thus, TiB2 particles increased the AMC's hardness and tensile strength. The higher the TiB2 weight %, the more the above-mentioned variables affect the mechanical characteristics. When the TiB2 weight % is increased, the % of elongation of the AMCs will drops. Similar results have been verified in the literature survey [18,19].
-
Impact Test
The impact tests are performed on the test specimens with a notch depth of 2 mm and a notch angle of 45o is considered. The impact values obtained for AA7075 and TiB2 composites are shown in Figure 10 for the test samples.
From the Figure 10, it can be observed that, the impact strength of 16.67 % increased on addition of wt. % of TiB2 with base material.
Fig10. Comparison of Impact Strength of various % of TIB2
-
Density test and Porosity
-
Theoretical densities are calculated for the composite specimens by using formulas and practical density tests are also performed on all the samples by using density kit to find out practical density values. These density values are plotted and compared in Figure 11. It can be seen that, TiB2 reinforced composite densities are higher than the AA7075 base metal due to increasing the mass properties of composites. Higher wt.% of TiB2 exhibited to the higher density and the matrix composites are sufficient strength to support secondary processing like sintering, machining or extrusion etc,.
The porosity results of the samples are computed and plotted as shown in Figure 12. In general, the porosity due to the increasing the wt.% of TiB2 exhibited a downward trend except for the composites reinforced with wt. 3% of TiB2.
6. Salt Spray (Fog) test:
The samples were inspected for rust particles and pitting marks after conducting 5 hours of salt spray test in a closed chamber. The corrosion was indicated after 5 hrs in the case of bare material AA7075, whereas the corrosion was not generated in the case of AA7075/TiB2 reinforced composites. All the test specimens are in good condition and found free from corrosion. Consequently, it is not necessity to further corrosion test for the test specimens.
CONCLUSIONS
From the results obtained for AA7075/TiB2 AMCs, the mechanical properties increased with the addition of wt.% of TiB2 reinforcements to the base metal. Through microstructure study, a fairly uniform distribution of materials is observed. The ultimate tensile strength is increased from 80.171 N/mm2 to 199.80 N/mm2 by varying the wt.% of TiB2 particulates to the base material. The AMCs have a higher hardness value than the base alloy by increasing the wt. % of TiB2. It is observed that the increasing hardness from 97.93 HBW to
106.73 HBW of AMCs', and that the reinforced composites with a higher hardness results have better wear resistance. The results of the impact test for AMCs' increased from 21 Joules of the base material to 25.1 Joules of TiB2 reinforced composites. The density of the reinforced alloy is greater than the AA7075 base alloy due to the addition of hard TiB2 reinforcement particulates having a higher density into the alloy matrix. Due to this reason, the composite with TiB2 as the reinforcement material will have a high porosity value. Finally, the composition of AA7075/ TiB2 has good corrosion resistance within the specified time compared to the base material and also it is suitable to industrial applications.
ACKNOWLEDGEMENT
The authors wish to acknowledge M/s. Hyderabad Engineers Laboratory, Hyderabad for providing laboratory facilities and colleagues who have directly or indirectly
contributed information to this paper and suggestions on the present work.
REFERENCES
-
Toptan F, Alves AC, Kerti I, Ariza E, Rocha LA. Corrosion and tribocorrosion behaviour of Al-Si-Cu-Mg alloy and its composites reinforced with B4C particles in 0.05M NaCl solution, Wear [Internet]. 2013;306(12):2735. Available from: http://dx.doi.org/10.1016/j.wear.2013.06.026
-
Keshavamurthy R, Mageri S, Raj G, Naveenkumar B, Kadakol PM, Vasu K. Microstructure and Mechanical Properties of Al7075-TiB 2 in-situ composite., Res J Mater Sci. 2013;1(10):610.
-
Bisadi H, Abasi A. Fabrication of Al7075/TiB2 Surface Composite Via Friction Stir Processing,. Am J Mater Sci. 2012;1(2):6770.
-
Kurt A, Uygur I, Cete E. Surface modification ofaluminium by friction stir processing, J Mater Process Technol [Internet]. 2011;211(3):3137. Available from: http://dx.doi.org/10.1016/j.jmatprotec.2010.09.020
-
Sharma R. A Review of the Aluminium Metal Matrix Composite and its Properties Design and Optimization of Cross Flow Heat Exchanger View project Modeling Of Evacuated Tube View project , 2017;83242. Available from: https://www.researchgate.net/publication/313881521
-
Krishna MV, Xavior AM. An investigation on the mechanical properties of hybrid metal matrix composites,. Procedia Eng [Internet]. 2014;97:91824. Available from: http://dx.doi.org/10.1016/j.proeng.2014.12.367
-
Rahman MH, Al Rashed HMM. Characterization of silicon carbide reinforced aluminum matrix Composites, Procedia Eng [Internet]. 2014;90:1039. Available from: http://dx.doi.org/10.1016/j.proeng.2014.11.821
-
Uvaraja VC, Natarajan N. Optimization of Friction and Wear Behaviour in Hybrid Metal Matrix Composites Using Taguchi Technique, J Miner Mater Charact Eng. 2012;11(08):75768.
-
Sharanabasappa R patil, B.S. Motgi. A Study on Mechanical Properties of Fly Ash and Alumina Reinforced Aluminium Alloy (LM25) Composites, IOSR J Mech Civ Eng. 2013;7(6):416.
-
Zeeshan Ahmad, Sabah Khan. A reviews paper on tribological and mechanical properties of Aluminium metal matrix composites manufactured by different route, Int. J Current Eng and Sc Research (IJCESR)[Internet]. 2014;1(4): 23940697
-
Kala H, Mer KKS, Kumar S. A Review on Mechanical and Tribological Behaviors of Stir Cast Aluminum Matrix Composites, Procedia Mater Sci [Internet]. 2014;6(Icmpc):195160. Available from: http://dx.doi.org/10.1016/j.mspro.2014.07.229
-
Ramesh A, Prakash JN, Gowda ASSS, Appaiah S. Comparison of the Mechanical Properties of AL6061/Albite and AL6061/Graphite Metal Matrix Composites, J Miner Mater Charact Eng. 2009;08(02):93106.
-
Tjong SC, Tam KF, Wu SQ. Thermal cycling characteristics of in- situ Al-based composites prepared by reactive hot pressing, Compos Sci Technol. 2003;63(1):8997.
-
Manjunatha HS, Mallesh G, Pradeepkumar VG. Mechanical Characterization of Aluminum-TiB 2 Metal Matrix Composites by In-Situ Method, 2020;(June):298304.
-
Chen Z, Kang H, Zhao Y, Zheng Y, Wang T. The role of TiB2 in strengthening TiB2 reinforced aluminium casting composites, IOP Conf Ser Mater Sci Eng. 2016;117(1).
-
Prabu SB, Karunamoorthy L, Kathiresan S, Mohan B. Influence of stirring speed and stirring time on distribution of particles in cast metal matrix composite, J Mater Process Technol. 2006;171(2):26873.
-
Christy TV, Murugan N, Kumar S. A Comparative Study on the Microstructures and Mechanical Properties of Al 6061 Alloy and the MMC Al 6061/ TiB<sub>2</ sub>/12<sub>p</ sub>, J Miner Mater Charact Eng. 2010;09(01):5765.
-
Han Y, Liu X, Bian X. In situ TiB2 particulate reinforced near eutectic Al-Si alloy composites, Compos – Part A Appl Sci Manuf. 2002;33(3):43944.
-
Michael Rajan HB, Ramabalan S, Dinaharan I, Vijay SJ. Synthesis and characterization of in situ formed titanium diboride particulate reinforced AA7075 aluminum alloy cast composites, Mater Des
[Internet]. 2013;44:43845. Available from: http://dx.doi.org/10.1016/j.matdes.2012.08.008 -
M. Sambathkumar a, Navaneethakrishnan P, Ponappa.K SKS. Mechanical and Corrosion Behavior of Al7075 ( Hybrid ) Metal Matrix Composites by Two Step Stir Casting Process, Lat Am J Solids Struct. 2016;7075:24355.
-
Nai SML, Gupta M. Influence of stirring speed on the synthesis of Al/SiC based functionally gradient materials, Compos Struct. 2002;57(14):22733.
-
Ronad G Munro. Material properties of titanium diboride, J. Res.
Natl. Inst. Stand. Technol. 2000; 105: 709-720
-
Hardness FORB, For T. Method For Brinell Hardness Metallic Materials ( Third Revision ), 2005;(August).
-
ASTM E8. ASTM E8/E8M standard test methods for tension testing of metallic materials 1, Annu B ASTM Stand 4. 2010;(C):127.
-
Standard I. for Charpy Impact Test ( V-Notch ) on Metallic Material, 2003;13.
-
ASTM SP. B 0117 Operating Salt Spray (Fog) Apparatus. ASTM [Internet]. 2011;112. Available from: http://www.galvanizeit.com/uploads/resources/ASTM-B-117- yr11.pdf