
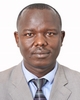
- Open Access
- Authors : Paul Christopher Kimali Kioko
- Paper ID : IJERTV10IS020176
- Volume & Issue : Volume 10, Issue 02 (February 2021)
- Published (First Online): 22-02-2021
- ISSN (Online) : 2278-0181
- Publisher Name : IJERT
- License:
This work is licensed under a Creative Commons Attribution 4.0 International License
An Assessment Into the use of Crushed Glass as Partial Replacement for Fine Aggregates
Paul Christopher Kimali Kioko
Department of Civil Engineering, School of Engineering & Technology South Eastern Kenya University
Abstract:- Glascrete is composed of cement, aggregate which is partially replaced with glass and water. The replacement of sand with glass is done in specified percentages and in a fine aggregate range in order to compare the effect of particle size on expansion.
I carried out this research to assess the effect of crushed clear pane glass on concrete and how the effect varies by using different particle sizes and percentages.
The test method I used was according to ASTM 1260 which is the standard test method for potential alkali reactivity of aggregates [mortar-bar method]. The test method provides a means of detecting the potential of an aggregate intended for use in concrete for undergoing alkali-silica reaction resulting in potentially deleterious internal expansion.
Test conducted in this project include the Alkali Aggregate Reaction, grading of sand and organic content on sand.
Results from the tests are presented in form of line graphs and discussed in reference to ASTM 1260 specifications. The results showed that alkali aggregate reaction is dependent on particle size and percentage of partial replacement of sand. Hence it is recommended from this report to use glass to mitigate alkali-aggregate reaction in glascrete.
-
DEFINITION OF GLASCRETE
CHAPTER 1
1.0 INTRODUCTION
Glascrete is known as a concrete in which the aggregates wholly or partially consist of crushed glass, where the glass is a unique material that could be recycled many times without changing its chemical or mechanical properties. It has been used for certain purposes where the aesthetical aspect is one of the main considerations. At the present time, numerous studies have been conducted to investigate the performance of concrete composites that contained waste glass, either as an aggregate substitution or as a pozzolanic material.
Glascrete is composed of cement, aggregates especially glass and water. Glascrete has an attractive appearance due to its smooth and colorful glass aggregates which makes it suitable for various architectural and decorative applications.(Shakir A.Al- Mishhadani 2007).
-
HISTORICAL DEVELOPMENT OF THE USE OF GLASCRETE
As early as 4000BC, glass was used in the Middle East as a glaze to decorate beads. By 1550BC, colored glass vessels were widespread and used for cooking and drinking. The earliest known clear glass was a vase found in Nineveh in Assyria, dating from around 800BC which is now in the British Museum in London. Until the 18th and 19th centuries, glass was very expensive and was used for limited applications such as stained glass windows for churches.
Large scale glass manufactures began with the industrial revolution with the mass production of glass containers beginning at the onset of the 20th century and glass light bulb production automated in 1926. Nowadays glass is much less expensive and is taken for granted as packaging material in addition to its use in windows and construction.
Waste glass is a major component of the solid waste stream in many countries. It can be found in many forms, including container glass, flat glass such as windows, bulb glass and cathode ray tube glass(http:/www.britglass.co.uk/under history).
In this project we are focused on the use of clear pane glass as an aggregate in the making of concrete. Glass aggregates are very reactive such that when added into Portland cement concrete, they result in a long-term durability problem, called alkali-silica reaction.
-
CURRENT USE OF GLASCRETE.
Glascrete has been used in the construction industry in making of several products as discussed below:
Making of glass concrete tiles.
There are manufacturers which are producing tiles that utilize expensive specialty aggregates such as marble chips. Crushed glass constitutes a relatively low-cost alternative to such materials, even if the glass needs to be sorted by color. Efforts are now under way to mass-manufacture Glass Concrete tiles.
Plate 1.3a:glass concrete tile
Source:www.concrete international.co.uk/ 2003
Concrete Masonry Block
These are used in the construction of building walls.
Paving Stone.
Paving stone are composed purely of glass aggregate. They have reflective properties of the glass which cannot be obtained by using natural aggregate like sand.
Plate 1.3b:glass concrete paving stone Source:www.concrete international.co.uk/ 2003
Decorative Applications
They exist in the architectural and decorative fields. We can create surface textures and appearances using colored glass. (Christian meyer 2003)
-
CHALLENGES IN THE USE OF GLASCRETE
The use of glass as an aggregate for concrete has been used in the construction industry, but the so called alkali-silica reaction (ASR) causes a severe problem. Alkali-silica reaction is now well known in the concrete industry, as it can occur also with natural aggregates that contain certain kinds of reactive silica. In the presence of moisture, the ASR gel swells and can cause severe concrete cracking and development of surface pop-outs. This is a long-term problem that may manifest itself in concrete after many years(Jin,W. 1998,Christian Meyer 2000)
-
JUSTIFICATION OF THE PROPOSAL
Beneficial use of glass as aggregates in the making of concrete:
Glass as a material offers several advantages that can be exploited in concrete products-
-
Glass aggregates improve the flow properties of fresh concrete so that very high strength can be obtained even without the use of higher range water-reducing admixtures.
-
Finely ground glass has pozzolanic properties and can therefore serve as partial cement replacement and filler.
-
The excellent hardness of glass gives the concrete an abrasion resistance that very few natural stone aggregates can match. Glass is one of the most durable materials known to man because it has basically zero water absorption (Christian Meyer 2003).
-
Crushed glass can give excellent parameters for design (proper shape, surface texture, durable grading to minimize void content & high workability).
-
Use of crushed glass will greatly mitigate environmental degradation associated with the wanton harvesting and sand depletion.
-
Use of crushed glass is a solution to inherent concrete deficiencies brought about by creep, elasticity & shrinkage.
-
Creation of jobs for the youth with the establishment of Small and Medium Enterprises towards industrialization by the year 2030.
-
Obviate solid waste menace that pervades virtually all third world countries with a multiplicity of public health implications (reduces waste in landfills).
-
Source Substitution
-
Technically, presents itself as low-cost construction and apt to command wide application.
For instance, comparative typical costs are as underneath:-
PRODUCT
COST[KSHS.] PER SQUARE METRE.
GRANITO TILES
2,500/=
CRUSHED GLASS TILES
275/=
4 CABBRO PAVING BLOCKS
1,650/=
MASONRY BLOCKS
1,200/=
CRUSHED GLASS BLOCKS
40/=
Source:Own computation
-
Our streets,dumping sites,institutions,hospitals,constructions and demolition sites constitute sizeable chunks of waste glass.Solid waste glass generation statistics in Nairobi alone in 2005 stands at 2400 tonnes per day out of which 8% in glass.This translates to 192 tonnes per day of waste glass,an equivalent of 14 no trucks each 14 tonnes.(JICA,1988),(KARANJA,2005).
-
-
PROBLEM STATEMENT
Waste glass is a major component of the solid waste stream in many countries. It can be found in many forms, including container glass, flat glass such as windows, bulb glass and cathode ray tube glass.
There have been problem in coming up with a safe disposal of glass in many countries. Therefore, use of waste glass in the construction industry is one of the recent ways of getting rid of waste glass. In this project we are focused on the use of clear pane glass as an aggregate in the making of concrete.
Glass aggregates are very reactive such that when added into Portland cement concrete, they result in a long-term durability problem, called alkali-silica reaction (ASR). The product of ASR is called ASR gel, which swells with the absorption of moisture. Sometimes the generated pressure due to ASR gel insufficient to induce the development and propagation of fractures in concrete. Therefore, the major problem to solve for utilization of glass aggregate is how to reduce the long-term damage of concrete due to ASR expansion.
-
OBJECTIVE OF THE PROJECT General objective
-
Mitigating alkali-aggregate reaction in glasscrete.
Specific objectives
-
To check the effect of increase of amount of glass in making of glascrete by replacing 10% and 20% sand replacement by glass.
-
To obtain the pessimum size of glass.Pessimum size is the size of glass which would produce the highest expansion.
-
-
COMPOSITION OF GLASS
Glass products include three types of materials:
-
FORMERS
CHAPTER 2
-
LITERATURE REVIEW
These are the basic ingredients. Any chemical compound that can be melted and cooled into a glass is a former. (With enough heat, 100% of the earth's crust could be
made into glass.)
Most commercial glass is made with sand that contains the most common former, Silica.
Other formers include:
-
Anhydrous Boric Acid
-
Anhydrous Phosphoric Acid.
Melting sand by itself is too expensive because of the high temperatures required (about 1850°C, or 3360°F).
-
-
-
FLUXES
Fluxes help formers to melt more readily and at lower temperatures (1300°C, or 2370°). These include:
-
Soda Ash
-
Potash
-
Lithium Carbonate
Fluxes also make the glass chemically unstable, liable to dissolve in water or form unwanted crystals.
-
-
STABILIZERS
They combine with formers and fluxes to keep the finished glass from dissolving, Crumbling, or falling apart.
They are added to make the glass uniform and keep its special structure intact. These include:
-
limestone
-
alumina
-
zinc oxide
-
magnesia etc
-
-
ADDITIVES
-
These additives act as Coloring agents in container glass, they include: Iron for brown or green colour, Chromium for green, Cobalt for blue colour, Lead to alter the refractive index, Alumina for durability, Boron to improve the thermal options. (http:/www.aroglass.co.uk/a resource for glass)
-
BENEFICIAL USE OF GLASS AS AGGREGATES
Glass as a material offers several advantages that can be exploited in concrete products:
-
Glass aggregates improves the flow properties of fresh concrete so that very high strength can be obtained even without the use of higher range water-reducing admixtures.
-
Very fine ground glass has pozollanic properties and therefore can serve both as partial cement replacement and filler.
-
The excellent hardness of glass gives the concrete an abrasion resistance that very few natural stones aggregate can match.
-
Glass is one of the most durable materials known to man because it has basically zero water absorption. (Christian meyer 2003/concrete international)
-
-
PROPERTIES OF GLASS
-
Strong
Glass has great inherent strength. It is weakened only by surface imperfections, which give everyday glass its fragile reputation. Special tampering can minimize surface flaws.
-
Hard
The surface of glass resists scratches and abrasions.
-
Elastic
Given under stress-up to a breaking point but rebounds exactly to its original shape.
-
Corrosion-resistant
Glass is affected by few chemicals. It resists most industrial and food acids.
-
Shock resistant
Glass withstands intense heat or colds as well as sudden temperatures changes.
-
Heat absorbent
Glass retains heat rather than conducting it. It absorbs heat better than metal.
Other properties include:
-
Glass reflects,bends,transmits,absorbs light with great efficiency
-
Glass strongly resists electric current. It stores electricity very efficiently.
Characteristic
Symbol
Value
1.Density
e
2.5g/cm3
2.Youngs Modulus
E
7x1010N/mm2
3.Thermal conductivity
1W/m.k
4.Hardness
6units(Mohs scale)
5.Poissons Ratio
0.2
6.Specific heat capacity
c
0.72x103j(Kg.k)
7.Average coefficient of linear expansion
9×10-6K-1
8.Mean refractive index to visible radiation
n
1.5
Source:KS 1535:Part 1:2000
(http:/www.aroglass.co.uk/a resource of glass)
-
-
EFFECT OF THE COLOUR OF GLASS ON ASR EXPANSION
Graph 2.4
Clear glass which is the most common kind in waste glass is the most reactive, followed by brown glass. Green glass does not appear to cause ASR-induced expansion. This is because of the chromium oxide manufacturers add to the glass to obtain its green colour.
Depending on the size of glass particle, green glass of fine particles can reduce the expansion. This implies that finely ground green glass has the potential for an inexpensive ASR suppressant(Yunping Xi & Yue Li,USA).
-
EFFECT OF TYPE OF GLASS ON ASR EXPANSION
Various types of glass aggregate including soda-lime glass which is used in most Beverage containers, Pyrex glass, and fused silica cause different ASR expansion. Window glass, plate glass, and windshield glass cause negligible ASR expansion in the ASTM C1260 tests(Yunping Xi & Yue Li,USA).
-
EFFECTS OF PARTICLE SIZE ON ASR EXPANSION
Graph 2.6
The particle size of glass aggregate has a major influence on ASR expansion. ASR reaction is clearly a surface-area dependent phenomenon, therefore the ASR expansion increases with aggregate fineness. However, there exists a size of the aggregate at which the maximum expansion occurs. This is called "pessimum" size. For regular soda lime glass, the pessimum size is about
#16 or #30 mesh size. For aggregate finer than the pessimum size, the ASR expansion decreases with further decrease in particle size. This means that the ASR expansion increases with increasing fineness of glass particles.
(Yunping X & Yue Li,USA).
-
EFFECT OF THE PERCENTAGE OF REPLACEMENT
Samples without glass show basically no expansion.
Replacing 10% of the natural aggregates with clear glass leads to a 14 day expansion that is twice the ASTM limit of 0.1%, and bars with 100% glass aggregates exhibit extraordinary expansion of 1.4%.
A clear size effect can be detected by replacing 10% of the natural aggregates with an equal amount of crushed glass of a specific size and plotting the 14 day mortar bar expansions obtained in the ASTM C 1260 tests as a function of glass particle size.
The pessimum size of clear glass is the mesh size #16(Yunping Xi & Yue Li,USA).
-
ALKALI-SILICA REATION
ASR is a reaction between alkali hydroxides in Portland cement and siliceous phase present in the aggregates composed of silicon dioxide. Problems with expansion arise when soluble silica reacts with the alkalis forming an alkali silica hydrate gel which exhibits directional growth and keeps cao from entering the complex. In concrete, cao is associated with silica and forms a non swelling calcium silicate hydrate gel during hydration as a key reaction related to cementation. It has been proposed that cao deficiency coupled with high alkali on aggregate surfaces or high concentrations of soluble silica allows the alkalis to react with the silica by diluting the cao leaving sites open for alkali incorporation. Glass is often added to mitigate expansion as a result of ASR(S.C.Maiti 2005 and Nicholas Adams 2002)
-
FEATURES OF ALKALI-SILICA REACTION
Alkali-silica reaction (ASR) is a chemical reaction between alkali ions (Na+ and K+) and hydroxide ions (OH-) in the concrete pore solution, generally derived from the Portland cement, and silica (SiO2), generally occurring in the aggregate. The reaction produces anhydrous alkali-silica gel. Formation of the gel alone does not cause cracking, rather cracking occur when the gel adsorbs water and swells causing expansion. It often results in greater pressures than the concrete can withstand and so produces cracks in the concrete.
A complicating feature of ASR is that the reaction is often quite slow, such that expansion and cracking are not observed for many years. Therefore, the reaction must be accelerated in laboratory tests.
An interesting feature of ASR is that expansion, which depends on the amount of reactive silica in the aggregate, usually shows a maximum value at some intermediate proportion of the reactive silica. At low levels of reactive silica increasing the amount increases the expansion, but at some amount the expansion peaks, and at high levels of reactive silica increasing the amount decreases the expansion. This is termed a pessimum effect, because expansion is greatest, or pessimum, at this intermediate proportion of reactive Silica. For some reactive constituents (e.g., opal) the pessimum occurs at a very low proportion, perhaps only a few per cent, and decreases sharply at higher levels.
For other reactive constituents (e.g., chert) the pessimum occurs at around 50% and decreases only gradually at higher levels. Glass does not usually show a pessimum, expansion increases even up to 100% glass. A similar feature is observed with particle size of the reactive aggregate. Large sized particles (say, centimeters in diameter) are slow to react and produce little expansion, at least at early ages. Crushing the same material to sand size speeds up the reaction and produces more expansion at early ages. Grinding the same material to a powder (micrometers in diameter) fundamentally changes the chemical reaction, producing calcium silicate hydrate (a normal hydration product of Portland cement), which has little tendency to absorb water and swell, instead of alkali silica gel, so expansion is reduced. Materials that are reactive as sands are pozzolanic as powders. Aggregate reactivity depends directly on the alkalinity (typically expressed as pH) of the solution in the concrete pores. This alkalinity generally primarily reflects the level of water-soluble alkalis (sodium and potassium) in the concrete.
-
MECHANISM FOR WHICH GLASS CONTROL ALKALI-SILICA REACTION
Glass dilutes the alkali content in the cement and also removes some from the pore solution by binding them into cao-silica hydrate gel.
Glass reduces the concrete permeability and diffusivity by the silica reacting with calcium hydroxide produced by the hydration of the cement to form calcium silicate hydrate. Calcium silicate hydrate takes up more space than calcium hydroxide, the more systems becomes finer and less continous.The reduced porosity limits the ability of the alkalis to migrate and therefore reduces the ability of alkali-silica gel to form(Meyer,S. and Baxter S. 2000)
-
EFFECT OF ALKALI-SILICA REACTION ON CONCRETE
-
Formation of ASR surface pop outs
Pop outs are small cone-shaped cavities in concrete surface left after a near surface aggregate has expanded and fractured. The cavities range from 6mm to few mm in diameter. Alkalis from cement causes an environment of high PH which causes the breakdown of silica and formation of an ASR gel, which absorbs water and expands removing a small portion of the surface mortar with it. They are typically small and accompanied by a small spot that is discolored and appears to be dump .Pop outs make it easier for water and other harmful chemicals to enter the concrete which can lead to deterioration such as corrosion of steel reinforcement(Richard H.Campbell 1974).
Source:www.cement.org
Plate2.9.2a: ASR Pop-out
How to avoid concrete ASR Pop outs
-
Use of low alkali cement or non-reactive aggregate.
-
Flushing the surface with water after the concrete has hardened and before applying the final curing. This may remove the alkali that may have accumulated at the surface as a result of evaporation of bleeded water.
-
Permitting use of class F fly ash or slag cement as a partial cement substitute to reduce the permeability of the paste and mitigate deleterious reactions due to ASR(Richard H.Campbell 1974).
-
-
Cracks
A key chemical reaction between hydrating cement and aggregate is the alkali silica reaction. It produces expansion and cracking and leads to reduction in strength and early failure of the concrete.
-
-
MITIGATION OF ALAKALI-AGGREGATE REACTION
If reactive aggregate is to be used in concrete without damage due to ASR, it is necessary either to limit the alkali level in the concrete or to use admixtures that mitigate the expansion. Use of a low-alkali cement (<0.6% total alkali) is often sufficient to prevent damage. If low-alkali cement is not available in the market area or if additional mitigation is desired, then it is necessary to use chemical or mineral admixtures.
Potential admixtures must be tested to determine their effectiveness and dosage. Mineral admixtures are known to be effective ways to mitigate ASR expansion. These
materials include fly ash; ground, granulated, blast-furnace slag; metakaolin; and silica fume.
Mitigation options for Alkali-silica reaction are as follows:-
-
Making glass alkali-resistant
This is done by coating glass with zirconium, a solution chosen by the glass fiber industry but impractical for post-consumer waste glass.
-
Sealing of concrete
ASR needs three factors to thrive [alkali, silica and moisture].sealing the concrete to keep it dry or using it in interior dry environment can minimize or avoid the problem.
-
Fly ashes and silica fumes
It is effective in controlling expansion caused by ASR, provided that sufficient dosages are used. Fly ash is categorized as either Class F or C, according to its SiO2 content. Class F fly ashes, with CaO less than about 20 percent; tend to be more effective than higher CaO ashes, requiring less fly ash to suppress expansion. However, even fly ashes with CaO contents in excess of 25 percent are effective in suppressing expansion, but higher dosages are needed, in some cases up to 40 percent (by mass of total cement). To reduce the required fly ash dosage, ternary blends containing fly ash plus either silica fume or ultra-fine fly ash, are quite effective. Fly ash mitigates ASR mainly by producing calcium silicate hydrate that complexes alkali in the pore solution and thereby reduces the pH. Silica fume mitigates ASR in much the same way.
-
Other SCMs, such as slag and metakaolin
These are quite effective in suppressing ASR, again provided that sufficient dosages are used. The required amount of any SCM (or SCMs for ternary blends) will depend on the aggregate reactivity, total alkali loading, and exposure conditions. Slag and
metakaolin mitigates ASR by creating calcium aluminosilicate hydrate that both reduce diffusion of alkali and water to aggregate reaction sites and complexes alkali in the pore solution.
-
Reduction of alkali loading in plain concrete (without SCMs)
This is an effective method of preventing ASR-induced expansion and cracking, but it has been shown that for highly-reactive aggregates, even low alkali loadings (e.g., 3.5 lbs/yd3) resulted in significant cracking in exposure blocks.
-
Lithium nitrate
The use of a chemical admixtures containing lithium is also considered to be a promising way to mitigate ASR expansion. The most common admixture is lithium nitrate. It can be added to new concrete or applied to existing concrete.
With addition of lithium, ASR gel forms but is not deleteriously expansive. The mechanism by which lithium-based admixtures prevent expansion
is not well understood. It is found that some aggregates require substantially more lithium nitrate than the typical 100 percent dosage (based on manufacturers recommended dosage of 0.55 gallons of 30-percent lithium nitrate solution per pound of Na2Oe in mixture). Thus, it is not possible to prescriptively select the amount of lithium needed to control ASR.
(Kevin J.Folliard,Ryan Bowbork march 2006)
-
-
ALKALI SILICA REACTION TEST METHODS
In order to prevent this damage, it is essential to recognize aggregates that have the potential to react in this manner. A simple way to prevent damage due to ASR is to recognize and avoid reactive aggregate. The American Society for Testing and Materials (ASTM) has approved and developed several standard test methods to evaluate aggregates. Some of the test procedures are quick (1 day to 2 weeks), i.e. accelerated mortar bar test while one is quite long (1 year), i.e. the concrete prism test.
The methods are discussed here:
The accelerated mortar bar test
Probably most widely used is the ASTM Standard Test Method for Potential alkali Reactivity of Aggregates (Mortar Bar Method) (C 1260). This method is used to test combinations of aggregate and cement. Aggregates in the form of sands are used to prepare mortar bars. The bars are stored in a concentrated (1 N) sodium hydroxide solution at 80°C for two weeks and removed for measurement of length changes using a dial gauge designed for this purpose.
NOTE: Expansion less than 0.10% is generally considered to be innocuous, expansion between 0.10% and 0.20% is potentially innocuous, and expansion greater than 0.30% is potentially deleterious.
(ASTM C 1260), is a reasonable indicator of aggregate reactivity or a reasonable means of assessing various mitigation measures.
-
Scope
The accelerated mortar bar method permits the detection of the potential of alkali-silica reaction in mortar bars within 16 days.
-
Significance and use
The method provides a mean of detecting the potential of an aggregate to undergo alkali-aggregate reaction and its capability for use in the making of concrete.
-
Drawbacks of this method
ASTM C 1260 is that it tends to be overly severe when testing some aggregates, resulting in expansions exceeding the failure limit, even though these aggregates pass the concrete prism test and perform well in field applications. This trend has been well documented over the years, and for this reason, it is not recommended that the results of ASTM C 1260 be used by themselves alone to deem an aggregate as being reactive. If an aggregate fails this test, the results should be confirmed using the concrete prism test.
(Kevin J.Folliard,Ryan Bowbork march 2006).
The concrete prism test
A concrete test, ASTM Standard Test Method for Determination of Length Change of Concrete due to Alkali-Silica Reaction (C 1293), is often used to verify results of the rapid tests. Concrete prisms are stored in a humid environment at 37.8°C for one year and removed for measurement of length changes using a dial gauge. Expansion less than potentially deleterious. (ASTM C 1293) is, in general, the most appropriate laboratory test method for predicting field performance.
The test should be run for 1 year for testing aggregates and 2 years for testing SCMs or lithium compounds, with an expansion limit of 0.04 percent.
-
Drawback of this method
-
ASTM C 1293 is its long duration (1 or 2 years). Efforts were made to accelerate this test by increasing the storage temperature from 100 °F to 140 °F. However, it has been shown that expansions at the higher temperatures are significantly reduced because of increased leaching, increased specimen drying, and potential changes in pore solution chemistry.
In addition, the effects of non-reactive aggregates in this test were found to be dramatic in some cases. Specifically, some fine aggregates will yield vastly different expansions when tested under the two different temperature regimes, even though these aggregates meet the requirements for non-reactive under ASTM C 1293.One technical deficiency of ASTM C 1293 is that it is not well-suited for determining the effects of cement alkalinity on expansion, most likely because of leaching of alkalis during the course of the test
(Kevin J.Folliard,Ryan Bowbork march 2006).
CHAPTER 3
-
METHODOLOGY
-
ALKALI-SILICA REACTION [MORTAR-BAR METHOD]
-
MATERIALS
-
Cement
Pozzolanic cement KSEAS 18-1:2001 CEM IV/B 32.5N was used. This cement has very low alkali content, thus can mitigate ASR.
Plate 3.1.1a: pozzolanic cement
-
Sand replacement materials (CRM)
0%, 30% and 70% crushed clear pane glass were used to replace part of the sand.
Plate 3.1.1b: crushed clear pane glass
-
Fine aggregate (FA)
Machakos Sand was used as fine aggregate in glascrete.
Plata 3.1.1c: Machakos sand
-
Reagents
-
Sodium hydroxide
Sodium hydroxide (NaOH) of concentration which lies between 0.99N and 1.01N may be used.
Each litre of solution shall contain 40 grams of NaOH dissolved in 900ml of water, and shall be diluted with additional distilled or deionized water to obtain 1.0L of solution.
-
Water
-
Plate 3.1.1d: NaoH solution
Pure distilled water conforming to type IV of specification D 1193.
Plate 3.1.1d:Distilled Water
-
-
EQUIPMENT
-
Measuring cylinder
Plate 3.1.2a: measuring cylinder
-
Vernier caliper
This was used for measuring change in length of the prisms
-
Water bath
Plate 3.1.2b: vernier caliper
This was used instead of an oven to provide the required temperature of 80 degrees.
Plate 3.1.2c: water bath
-
Dial gauge reading
Plate 3.1.2d: Dial gauge reading
-
Moulds
The moulds were use to cast the prisms.
Plate 3.1.2e: mould
-
Sieves
For sieving of glass to the required size and for grading of sand.
Plate 3.1.2f: sieves
-
Mass balance
Thiswas used to measure the masses of sand, glass and cement.
Plate 3.1.2g: mass balance
-
Mixer, paddles and mixing bowls
-
Tamper and trowel
Tamper was used for compacting the mortar in the moulds and towel was used to dry the prisms.
Plate 3.1.2h: mixing bowls
Plate 3.1.2i: prism placed on a towel
-
Oil
This was used to lubricate the inside of the moulds.
-
Crushing equipment used
-
-
Plate 3.1.2j: Impact value abrasion apparatus
Plate 3.1.2k: Los Angeles Abrasion equipment
-
MATERIAL PREPARATION
-
Collected Clear pane glass
Plate 3.2a: collected clear pane glass
-
Crushing of pane clear glass to required particle size by use of Los Angeles Abrasion equipment.
Plate 3.2b: crushing process
Plate 3.2c: crushing process
-
Crushed glasses of different colours; clear, brown and green.
-
Sieving of clear pane glass
Plate 3.2d: Crushed glass
Plate 3.2e: sieving of clear pane glass
-
Ground glass having particle passing a #35, #52 and #100 sieve.
Plate 3.2f: sieved clear pane glass
-
-
-
PREPARATION OF TEST SPECIMEN
1 Mould
-
Construction of the moulds
Plate 3.3a: construction of the mould
The interior surface of the moulds was covered with a release agent, i.e., oil, before casting.
Plate 3.3b: application of the release agent
-
Aggregates
Glass was crushed and sieved to achieve the required sieve size. The sand was graded by sieving through different sieve sizes.
Plate 3.3c: sieving of sand
Plate 3.3d: sieved sand
Plate 3.3e: sieved clear pane glass
-
Mortar bar prisms
The mortar bar prisms were prepared according to ASTM C-1260.
Two mortar bar prisms were made for each cement aggregate combination.
-
Proportioning of the mortar
-
The dry materials for the mortar were proportioned using 1 part of cement to 2.25 parts of aggregate mass. The quantities of materials mixed to make three mortar bar prisms were 300 grams of cement and 660 grams of aggregates.
Batching process
Plate 3.3f: batching process
Plate 3.3g: weight quantities of cement, sand and glass ready for mixing
Mixing
Plate 3.3h: Dry mixing of the measured quantities
Plate 3.3i: Wet mixing of measured quantities
-
Molding of test specimen
The test specimens were molded within a total elapsed time of not more than 2 minutes and 15 seconds after the mixing of the mortar. The moulds were filled in layer and compacted each time with a tamper. The mortar was cut off at the top and smoothened on the surface.
Casting process
Plate 3.3j: casting of the prisms
Plate 3.3k: compacting of mortar using a tamper
-
Documentation of the whole process
-
Plate :Stripping / Demoulding Process
Plate 1:mortar bars placed in plastic containers after stripping / demoulding
Plate 3:mortar bars placed in plastic containers ready for curing
Plate 4:Addition of sodium hydroxide{1N} and Distilled Water.
Plate 5:curing of the mortar bar prisms in a water bath
Plate 6:curing process with temperature maintained at 80oc
Plate 7:Drying of mortar bar prisms ready for measuring
-
-
-
PROCEDURE
-
ALKALI-AGGREGATE REACTIVITY
There are two standards that guide to alkali aggregate reactions test:
ASTM: C1260-01
BS:812-123:1999
Comparison of the two standards is as shown below:-
BS:812-123:1999
ASTM: C1260-01
principle
Concrete test prisms are prepared and stored for 52 weeks. The reaction is accelerated by:
Concrete test prisms are prepared and stored for for 14 days after the zero reading.
The reaction is accelerated by:
Sample size
Concrete prisms of length (250±50) mm and crossections of (75±2) mm are used.
Concrete prisms of length (250±50) mm and crossections of (25±2) mm are used.
Reagents
High alkaline Portland cement.
Potassium sulfate to increase the alkalinity of cement
5.1 Sodium Hydroxide (NaOH) with a concentration lying between 0.99N and 1.01N.
-
Formulating the concrete to posses higher than average cement alkali content.
-
Storing the prisms at higher humidity and comparatively high temperature(380C) to increase the rate of chemical reaction
-
Immersing the mortar bar in 1N sodium hydroxide(NaOH).
-
Storing the prisms at high temperatures (80±20C) in an oven or water bath.
The procedure was carried out in accordance with the ASTM C 1260 as shown in appendix A.
-
-
ORGANIC IMPURITIES TEST
The procedure was based on AASHTO T21 as described in appendix A.
-
GRADING OF SAND
1292 grams of sand were graded by sieving through different sieve sizes.
-
RESULT
-
ALKALI- SILICA REACTIVITY
Raw results of dial gauge reading are as shown in appendix B.
-
ORGANIC IMPURITIES TEST
Light colour was shown.
-
GRADING OF SAND
SIEVE SIZE |
CUMULATIVE PASSING% |
2.83 |
100.0 |
1.41 |
87.3 |
1 |
74.5 |
0.707 |
60.6 |
0.5 |
40.9 |
0.297 |
14.4 |
0.149 |
0.0 |
100 |
-
ANALYSIS OF THE RESULTS
-
EXPANSION CURVES
Table 4.2.1a 10% $ 20% REPLACEMENT
DAY
C0NTROL
10 % REPLACEMENT,% EXPANSION
20 % REPLACEMENT,% EXPANSION
RETAIN.52
RETAIN.100
PASS.100
RETAIN.52
RETAIN.100
PASS.100
2
0.00
0.00
0.00
0.00
0.00
0.00
0.00
3
0.01
0.15
0.15
0.15
0.15
0.15
0.15
7
0.06
0.23
0.22
0.21
0.24
0.22
0.22
10
0.11
0.25
0.23
0.22
0.28
0.27
0.26
14
0.12
0.26
0.24
0.23
0.31
0.28
0.27
16
0.12
0.28
0.26
0.24
0.33
0.29
0.28
0.35
0.35
0.3
0.25
0.2
0.15
0.1
0.05
0
% expansion against time(control)
% expansion against time(clear pane glass,10% passing 35)
% expansion against time(clear pane glass,10% passing 52)
% expansion against time(clear pane glass,10% passing 100)
% expansion against time(clear pane glass,20% passing 35)
% expansion against time(clear pane glass,20% passing 52)
% expansion against time(clear pane glass,20% passing 100)
0.3
0.25
.2
0.15
0.1
0.05
0
% expansion against time(control)
% expansion against time(clear pane glass,10% passing 35)
% expansion against time(clear pane glass,10% passing 52)
% expansion against time(clear pane glass,10% passing 100)
% expansion against time(clear pane glass,20% passing 35)
% expansion against time(clear pane glass,20% passing 52)
% expansion against time(clear pane glass,20% passing 100)
0 5 10 15 20
0 5 10 15 20
Figure 4.2.1a
0.2
0.2
Table 4.2.1b EXPANSION CURVES-10% REPLACEMENT
DAY
CONTROL
RET.52
RET.100
PASS.100
2
0.00
0.00
0.00
0.00
3
0.01
0.15
0.15
0.15
7
0.06
0.23
0.22
0.21
10
0.11
0.25
0.23
0.22
14
0.12
0.26
0.24
0.23
16
0.12
0.28
0.26
0.24
Expansion curves-10% replacement
Expansion curves-10% replacement
0.3
0.3
0.25
0.25
0.05
0.05
0
2
3
days
7
10
14
16
0
2
3
days
7
10
14
16
0.15
0.1
0.15
0.1
control ret. On 52 ret.100
pass 100
control ret. On 52 ret.100
pass 100
% expansion
% expansion
Figure 4.2.1b
Table 4.2.1c EXPANSION CURVES-20% REPLACEMENT
20 % REPLACEMENT, % EXPANSION
DAY
CONTROL
RET.52
RET.100
PASS.100
2
0.00
0.00
0.00
0.00
3
0.01
0.15
0.15
0.15
7
0.06
0.24
0.22
0.22
10
0.11
0.28
0.27
0.26
14
0.12
0.31
0.28
0.27
16
0.12
0.33
0.29
0.28
0.35
0.3
% expansion
% expansion
0.25
0.2
0.15
0.1
0.05
0
Expansion curves-20% replacement
2 3 7 10 14 16
Figure 4.2.1c
control ret. On 52 ret.100 pass 100
Table 4.2.1d ASR PESSIMUM SIZE-10% REPLACEMENT
10 % REPLACEMENT ,% EXPANSIONS
SIEVE SIZE 3TH DAY
7TH DAY
10TH DAY
14TH DAY
16TH DAY
CONTROL
0.01
0.06
0.11
0.12
0.12
35-52
0.15
0.23
0.25
0.26
0.28
52-100
0.15
0.22
0.23
0.24
0.26
>100
0.15
0.21
0.22
0.23
0.24
0.35
0.3
% expansion
% expansion
0.25
0.2
0.15
0.1
0.05
0
ASR Pessimum size-10%replacement
0 1 2 3 4 5
particle size range
3 day
7 day
10 day
14 day
16 day
Figure 4.2.1d
Table 4.2.1e ASR PESSIMUM SIZE-20% REPLACEMENT
20 % REPLACEMENT ,% EXPANSIONS
SIEVE SIZE
3TH DAY
7TH DAY
10TH DAY
14TH DAY
16TH DAY
CONTROL
0.01
0.06
0.11
0.12
0.12
35-52
0.15
0.24
0.28
0.31
0.33
52-100
0.15
0.22
0.27
0.28
0.29
>100
0.15
0.22
0.26
0.27
0.28
0.4
0.35
% expansion
% expansion
0.3
0.25
0.2
0.15
0.1
0.05
0
ASR pessimum size-20%replacement
pessimum size
0 1 2 3 4 5
particle size range(mm)
3 day
7 day
10 day
14 day
16 day
Figure 4.2.1e
INDIVIDUAL % EXPANSION FOR EACH SIEVE SIZE
Table 4.2.1f CONTROL SAMPLE-0%REPLACEMENT
DAY
% EXPANSION
2
0.00
3
0.01
7
0.06
10
0.11
14
0.12
16
0.12
0.14
0.12
% expansion
% expansion
0.1
0.08
0.06
0.04
0.02
0
control sample-0% replacement
2 3 7 10 14 16
days
Figure 4.2.1f
Table 4.2.1g
10% REPLACEMENT,RETAINED ON SIEVE SIZE 52,PASSING 35
DAY
% EXPANSION
2
0.00
3
0.15
7
0.23
10
0.25
14
0.26
16
0.28
10% replacement -retained on sieve size 52,passing 35
10% replacement -retained on sieve size 52,passing 35
0.3
0.25
0.2
0.15
0.1
0.05
0
0.3
0.25
0.2
0.15
0.1
0.05
0
2
3
da7ys
10
14
16
2
3
da7ys
10
14
16
% expansion
% expansion
Figure 4.2.1g Table 4.2.1h
10% REPLACEMENT,RETAINED ON SIEVE SIZE 100,PASSING 52
DAY
% EXPANSION
2
0.00
3
0.15
7
0.22
10
0.23
14
0.24
16
0.26
10% replacement-retained on sieve size 100,passing 52
0.3
0.25
% expansion
% expansion
0.2
0.15
0.1
0.05
0
2 3 7 10 14 16
Figure 4.2.1h
Table 4.2.1i
10% REPLACEMENT,PASSING SIEVE SIZE 100
DAY
% EXPANSION
2
0.00
3
0.15
7
0.21
10
0.22
14
0.23
16
0.24
10% replacement- passing sieve size 100
10% replacement- passing sieve size 100
0.3
0.25
0.2
0.15
0.1
0.05
innocous
0.3
0.25
0.2
0.15
0.1
0.05
innocous
0
0
0
2
days
4
6
8
0
2
days
4
6
8
% expansion
% expansion
20% REPLACEMENT,RETAINED ON SIEVE SIZE 52,PASSING 35
DAY
% EXPANSION
2
0.00
3
0.15
7
0.24
10
0.28
14
0.31
16
0.33
20% REPLACEMENT,RETAINED ON SIEVE SIZE 52,PASSING 35
DAY
% EXPANSION
2
0.00
3
0.15
7
0.24
10
0.28
14
0.31
16
0.33
Figure 4.2.1i Table 4.2.1j
20% replacement-retained on sieve size 52,passing 35
0.35
0.3
% expansion
% expansion
0.25
0.2
0.15
0.1
0.05
0
2 3 7 10 14 16
days
Figure 4.2.1j
Table 4.2.1k
20% REPLACEMENT,RETAINED ON SIEVE SIZE 100,PASSING 52
DAY
% EXPANSION
2
0.00
3
0.15
7
0.22
10
0.27
14
0.28
16
0.29
20% replacement-retained on sieve size 100,passing 52
0.35
0.3
% expansion
% expansion
0.25
0.2
0.15
0.1
0.05
0
2 3 days7 10 14 16
20% REPLACEMENT,PASSING SIEVE SIZE 100
DAY
% EXPANSION
2
0.00
3
0.15
7
0.22
10
0.26
14
0.27
16
0.28
20% REPLACEMENT,PASSING SIEVE SIZE 100
DAY
% EXPANSION
2
0.00
3
0.15
7
0.22
10
0.26
14
0.27
16
0.28
Figure 4.2.1k Table 4.2.1l
20% replacement-passing sieve no.100
20% replacement-passing sieve no.100
0.3
0.25
0.2
0.15
0.1
0.05
0
0.3
0.25
0.2
0.15
0.1
0.05
0
2
3
7
10
14
16
2
3
7
10
14
16
% expansion
% expansion
Figure 4.2.1l
-
ORGANIC IMPURITIES TEST
The soil was found to be good.
-
GRADING CURVE OF MACHAKOS SAND
-
Sand particle size distribution curve
100
90
80
70
% passing
% passing
60
50
40
30
20
10
0
0.01 0.1
Sieve size (mm)
1 10
5.1 INTERPRETATION OF TEST RESULTS
CHAPTER 5
5.0 DISCUSSION
All the mortar bars prisms showed a significant expansion at the age of 16 days. The results of percentage expansion at the 16th day were interpreted as shown in the table 5.1 below:
Table 5.1
% REPLACEMENT |
SIEVE SIZE |
% EXPANSION |
INTERPRETATION |
10% REPLACEMENT |
#35 |
0.28 |
Deleterious |
#52 |
0.26 |
Deleterious |
|
#100 |
0.24 |
Deleterious |
|
20% REPLACEMENT |
#35 |
0.33 |
Deleterious |
#52 |
0.29 |
Deleterious |
|
#100 |
0.28 |
Deleterious |
-
PARTICLE SIZE EFFECT
From the results, the expansion due to ASR depended on the particle size of glass used.
Glass particle passing sieve size 35 and retained on sieve size 52 showed a much higher expansion for both 10% and 20% replacement.
This is followed by particle size passing sieve size 52 and retained on sieve size 100.
Particle size passing sieve size 100 showed the least expansion for both 10% and 20% replacement.
-
EFFECT OF PERCENTAGE REPLACEMENT
From figure 4.2.1a, replacing sand with 20% of glass showed a much higher expansion than replacing sand with 10% of glass at the 16th day.
Particle size passing sieve size 35 and getting retained on sieve size 52 for 20% replacement showed a higher expansion at the 16th day.
Particle size passing sieve size 100 for 10% replacement showed the least expansion at the 16th day; hence this shows their effectiveness in the mitigation of ASR in glascrete.
5.3 EFFECT OF COLOUR AND TYPE OF GLASS
From the result analysis of both the glasses which were used in the making of glascrete,clear pane glass showed a higher expansion than the others.
Clear pane pane glass caused a higher expansion, followed by a combination of clear glass and brown glass. Green glass showed the least expansion of all the different types and combinations of glass used.
-
CONCLUSION AND RECOMMENDATIONS
-
CONCLUSION
In accordance with the objective of this project.The following conclusion can be made: The expansion of glascrete depend on the following factors:
-
The size of glass particles
Glass particle passing sieve size 35 and getting retained on sieve size 52 showed a higher expansion.
-
The % replacement of sand with glass
Expansion of glass increases with the increase of the percentage of glass replacement.The expansion was higher for 20% replacement of sand with glass.
-
The colour of glass and type of glass
Clear pane glass showed a higher expansion when compared with other glasses such as brown,green and other combinations. Hence it is recommended from this report to use glass to mitigate alkali-aggregate reaction in glascrete.
REFERENCES
-
ASTM 2004: Test ASTM C1260 Accelerated Mortar Bar American society for Testing Material.
-
Christian Meyer(2003).Glascrete-putting sustainability to work in a decorative way, Columbia university
-
Christian Meyer (2007).Recycled Glass From Waste Material to Valuable Resource,Department of Civil Engineering and Engineering Mechanics,
Columbia University, New York, NY
-
Dent Glasser.LS and Kataoka, N.(1981).The chemistry of Alkali-Aggregate reaction cement and concrete research.
-
http://www.concrete.org
-
Jin,W.(1998),Alkali-Silica reaction in concrete with glass aggregate, A chemo-physicomechanical approach; PHD thesis, Columbia Uuniversity
-
Karanja,2005,JICA,1988
-
Kenya Standards 1535:Part 1:2000
-
Kevin J.Folliard,Ryan Bowbork(2006).Preventing Alkali-Silica Reaction and delayed ettringite formation in concrete.Center for transportation research,University of Texas at Austin.
-
Meyer,C.and Baxter,S.Glascrete(2000)-concrete with glass aggregate,ACI material journal
-
NICHOLAS Adams and David B.Stokes (2002).Using Advanced Lithium Technology to combact ASR in concrete.
-
Richard H.campbell,Wendell haoding(1974).surface popouts,ACI journal,American Concrete Institute,June pp 284-288
-
R.landgren,and D.W.Hadley,surface popouts caused by alkali-aggregate reaction,Portland Cement Association,RD121
-
S.C.Maiti(2005)-Discussion Forum,Concrete for hydro-electric projects:Combacting alkali aggregate reaction
-
Shayan, A.(1991).Alkali Aggregate Reaction and its prevention. Division of building, construction and engineering Australia.
-
Woods H.(1968).Durability of concrete construction. Published jointly by American Concrete Institute Detroit Michigan $ the lowa State University press Ames lowa.
-
Yunping Xi,Yue Li.Utilization of solid waste(waste glass)as aggregate in concrete, University of Colorado,Boulders,co 80309,USA
APPENDIX A PROCEDURE
-
ALKALI-AGGREGATE REACTIVITY The prisms were casted as per ASTM C1260 as described below:
ASTM C 1260 uses a mortar bar composed of 1 part cement to 2.25 parts aggregate with particles between the No. 4 and No. 50 sieves (coarse aggregates have to be crushed to provide this material) and a water-to-cement ratio of 0.47. After two days of curing, initial length measurements of the bar are made and the mortar bars are placed in 1-normal sodium hydroxide solution at 176 °F (80 °C) for 14 days. Length measurements are periodically made, and if at the end of the 14 days soaking in sodium hydroxide (16 days after casting) the length has increased by more than 0.08 percent, the aggregate is considered potentially reactive.
-
ORGANIC IMPURITIES TEST
The test is used to determine the presence of organic compounds in fine aggregates, i.e. sand, to be used for making of mortar.
Reagents and apparatus
-
NAOH solution made up of 3 parts of NAOH in 97 parts of water.
-
Organic plate number to compare the colour of the liquid in the tested sample.
Procedure
The based is based on AASHTO T21.
-
The test material which is sand was divided to obtain the test sample approximately 450 grams.
-
The sand was air dried to constant weight
-
A glass bottle was filled to 130ml with the sand
-
The sodium hydroxide solution was added until the volume of sand and the solution reached 200ml.
-
The glass bottle was closed and shaken vigorously and then allowed to stand for 24 hours.
-
The colour was compared with an organic plate number.
-
-
GRADING OF SAND
-
-
-
1292 grams of sand was sieved through different sieve size.
APPENDIX B
Raw data for change in length of specimens and computed percentages. All values are in dial gauge readings.
DAY 3
% REPLACEMENT |
SIEVE SIZE |
PRISMS |
ORIGINAL LENGTH[Lo] |
LENGTH AT DAY 3[L3] |
AVERAGE EXPANSION |
% EXPANSION |
10% |
35 |
1 |
9978 |
9987.5 |
14.5 |
0.15 |
2 |
9972 |
10001 |
||||
52 |
1 |
9987 |
9999.5 |
15 |
0.15 |
|
2 |
9980 |
9997 |
||||
100 |
1 |
9988 |
10002 |
15 |
0.15 |
|
2 |
9990 |
10006 |
||||
20% |
35 |
1 |
9990 |
10003 |
15 |
0.15 |
2 |
9988 |
10005 |
||||
52 |
1 |
9983 |
9986.5 |
15 |
0.15 |
|
2 |
9964 |
9991 |
||||
100 |
1 |
9954 |
9972 |
15 |
0.15 |
|
2 |
9956 |
9968 |
DAY 7
% REPLACEMENT |
SIEVE SIZE |
PRISMS |
ORIGINAL LENGTH[Lo] |
LENGTH AT DAY 3[L7]] |
AVERAGE EXPANSION |
% EXPANSION |
10% |
35 |
1 |
9978 |
10002 |
23 |
0.23 |
2 |
9972 |
9994 |
||||
52 |
1 |
9987 |
10004 |
22 |
0.22 |
|
2 |
9980 |
10007 |
||||
100 |
1 |
9988 |
10011 |
21 |
0.21 |
|
2 |
9990 |
10009 |
||||
20% |
35 |
1 |
9990 |
10012 |
24 |
0.24 |
2 |
9988 |
10014 |
||||
52 |
1 |
9983 |
9995 |
22 |
0.22 |
|
2 |
9964 |
9996 |
||||
100 |
1 |
9954 |
9974 |
22 |
0.22 |
|
2 |
9956 |
9980 |
DAY 10
% REPLACEMENT |
SIEVE SIZE |
PRISMS |
ORIGINAL LENGTH[Lo] |
LENGTH AT DAY 3[L10] |
AVERAGE EXPANSION |
% EXPANSION |
10% |
35 |
1 |
9978 |
9998 |
25 |
0.25 |
2 |
9972 |
10002 |
||||
52 |
1 |
9987 |
10003 |
23 |
0.23 |
|
2 |
9980 |
10008 |
||||
100 |
1 |
9988 |
10010 |
22 |
0.22 |
|
2 |
9990 |
10012 |
||||
20% |
35 |
1 |
9990 |
10019 |
28 |
0.28 |
2 |
9988 |
10015 |
||||
52 |
1 |
9983 |
9999 |
27 |
0.27 |
|
2 |
9964 |
10002 |
||||
100 |
1 |
9954 |
9980 |
26 |
0.26 |
|
2 |
9956 |
9982 |
DAY 14
% REPLACEMENT |
SIEVE SIZE |
PRISMS |
ORIGINAL LENGTH[Lo] |
LENGTH AT DAY 3[L14] |
AVERAGE EXPANSION |
% EXPANSION |
10% |
35 |
1 |
9978 |
10000 |
26 |
0.26 |
2 |
9972 |
10002 |
||||
52 |
1 |
9987 |
10006 |
24 |
0.24 |
|
2 |
9980 |
10009 |
||||
100 |
1 |
9988 |
10011 |
23 |
0.23 |
|
2 |
9990 |
10013 |
||||
20% |
35 |
1 |
9990 |
10016 |
31 |
0.31 |
2 |
9988 |
10024 |
||||
52 |
1 |
9983 |
10001 |
28 |
0.28 |
|
2 |
9964 |
10002 |
||||
100 |
1 |
9954 |
9982 |
29 |
0.29 |
|
2 |
9956 |
9986 |
DAY 16
% REPLACEMENT |
SIEVE SIZE |
PRISMS |
ORIGINAL LENGTH[Lo] |
LENGTH AT DAY 3[L16] |
AVERAGE EXPANSION |
% EXPANSION |
10% |
35 |
1 |
9978 |
10001 |
28 |
0.28 |
2 |
9972 |
10005 |
||||
52 |
1 |
9987 |
10007 |
26 |
0.26 |
|
2 |
9980 |
10012 |
||||
100 |
1 |
9988 |
10011 |
24 |
0.24 |
|
2 |
9990 |
10015 |
||||
20% |
35 |
1 |
9990 |
10021 |
33 |
0.33 |
2 |
9988 |
10023 |
||||
52 |
1 |
9983 |
10001 |
29 |
0.29 |
|
2 |
9964 |
10004 |
||||
100 |
1 |
9954 |
9981 |
28 |
0.28 |
|
2 |
9956 |
9985 |