
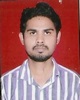
- Open Access
- Authors : Nilesh V. Sawadekar , Jeevan J. Salunke
- Paper ID : IJERTV10IS080193
- Volume & Issue : Volume 10, Issue 08 (August 2021)
- Published (First Online): 02-09-2021
- ISSN (Online) : 2278-0181
- Publisher Name : IJERT
- License:
This work is licensed under a Creative Commons Attribution 4.0 International License
An Analysis of Surface Roughness (Ra, Rz), Material Removal Rate and Residual Stresses in Cylindrical Grinding of Hardened OHNS
Mr. Nilesh V. Sawadekar
Mechanical Engineering Department
Deogiri Institute of Engineering and Management Studies Aurangabad (M.S), India
Abstract -Cylindrical grinding is the most important abrasive metal cutting processes used in the finishing operations. Surface finish (Ra, Rz) is the important output responses in the production as per as quality of surface is concerned.
The aim of this analysis was to study the effect of the cylindrical grinding parameters: like work speed, feed rate, and number of passes on surface roughness (Ra and Rz) and material removal rate and generation of residual stresses during the grinding of hardened OHNS material. The DOC (Depth of cut) and work speed was kept constant. The experiment was carried out on Schleif SA 5/2 U x 1000. Oil hardened non-Shrinkage is an important material used mainly used for making wear resistant products such as dies, punches, measuring tools, thread cutting tools, Milling cutters, broaches, and spline gauges.
Keywords-Cylindrical grinding, MRR, Surface finish, Ra, Rz ANOVA, Residual Stress (RS), RSM
-
INTRODUCTION
In this modern world with the advancement in science and technology every manufacturer wants to manufacture the product with high quality. Cylindrical grinding is an abrasive metal removing process which is used in the finishing operation. Cylindrical grinding is a most important process for final machining of components requiring smooth surfaces and precise tolerances.[1]
Surface appearance, defined in terms of surface roughness, flaws, lay and waviness are concerned with the geometric irregularities of the texture of a workpiece. Surface integrity with economical production and manufacturing processes is the fore most requirement of industry. Surface roughness is a measure of the quality of a product which greatly influences the manufacturing cost also. Surface roughness describes the geometry of the machined surfaces and combined with the surface texture. The fact behind the formation of surface roughness is complicated and is depends on manufacturing process. [2]
The residual stress formation during grinding process is due to plastic deformations and phase transformations which are affected by grinding parameters such as speed and feed rate. It is known that the differences in speed of the grinding wheel produce different residual stress profiles. Along With high rotational speeds of the workpiece, there is increase in the tensile residual stresses. This is because of the heat which is created due to higher friction rates as well as other mechanical factors such as the load being applied on the components surface.[3]
Grinding Residual stresses are those stresses that
Prof. Jeevan J. Salunke Asst. Professor
Mechanical Engineering Department
Deogiri Institute of Engineering and Management Studies Aurangabad (M.S), India
remain in an object even the external forces and loading is removed. In many cases, residual stresses result in significant plastic deformation, leading towards the distortion of an object. In others, they are cause of for fracture, crack propagation and fatigue. When the residual stress on the surface exceeds ultimate strength of workpiece, there will be cracks and microcracks. According to the experimental studies and experiments performed, suggest that the grinding compressive residual stress can improve the fatigue life and stops the initiation of crack propagation of the workpiece, rather the tensile residual stress has negative effect on the fatigue life of workpiece [4]
In this experimental work, the work speed (rpm), feed(m/min), and number of passes were selected as the input parameters. Grinding Wheel speed and depth of cut (DOC) was kept constant. The effect of these parameters on surface roughness (Ra, Rz) and material removal rate (MRR) was analyzed to reach an optimum level and to find the effect of these parameter on generation of residual stress after cylindrical grinding on OHNS material.
-
EXPERIMENTAL PROCEDURE
-
Workpiece material
The experiment was carried out on Oil Hardened Non-Shrinkage rounds of 28 mm diameter and 125 mm length. The OHNS material was selected keeping in mind the application of this material for manufacturing of dies, punches, measuring tools, thread cutting tools, milling cutters, broaches, and spline gauges in industries. After the cylindrical grinding process the surface finish required is of much importance.
The raw OHNS hardened to 47- 49 Rc. The chemical composition observations for specimen (OHNS) are shown in table 1.
Sr.
No.
Chemical composition of OHNS in
Percentage
1
C
0.96
2
Mn
1.37
3
Cr
0.42
4
Ni
0.21
5
Mo
0.03
6
W
0.52
7
S
0.045
8
P
0.048
9
Si
0.40
Table 1
The figure1 shows the workpieces before grinding were carried out.
EXPERIMENTALCONDITIONS
The values of the parameters for carrying the analysis are as shown in table 2.
Parameter
Low
Medium
High
Unit
Feed
2
3.5
5
m/mi n
Speed
250
300
350
RPM
No. of Passes
4
5
8
—
-
Machine specifications
Figure1
Table2
3.
3.
The work speed was kept constant to 1430 RPM and the depth of cut was 12.5 m. Table 3 shows the experimental design matrix obtained by response surface methodology by using Mini tab14 software.
Run Order
Work Speed
Feed
No of Pass
Ra
Rz
MRR
1
300
3.5
4
0.37
1.52
0.22
2
350
3.5
6
0.35
1.43
0.39
3
300
2
6
0.33
1.33
0.22
4
300
3.5
6
0.36
1.43
0.35
5
300
3.5
6
0.37
1.48
0.33
6
250
5
8
0.36
1.48
0.36
7
250
3.5
6
0.35
1.48
0.33
8
300
3.5
6
0.35
1.45 0.37
9
350
2
4
0.33
1.45
0.18
10
350
5
8
0.36
1.36
0.37
11
250
2
8
0.35
1.45
0.20
12
250
5
4
0.40
1.5
0.22
13
350
5
4
0.39
1.49
0.33
14
300
3.5
8
0.37
1.47
0.46
15
300
3.5
6
0.35
1.46
0.30
16
300
3.5
6
0.35
1.46
0.32
17
250
2
4
0.35
1.46
0.10
18
300
3.5
6
0.35
1.46
0.31
19
350
2
8
0.33
1.32
0.26
20
300
5
6
0.34
1.45
0.33
Run Order
Work Speed
Feed
No of Pass
Ra
Rz
MRR
1
300
3.5
4
0.37
1.52
0.22
2
350
3.5
6
0.35
1.43
0.39
3
300
2
6
0.33
1.33
0.22
4
300
3.5
6
0.36
1.43
0.35
5
300
3.5
6
0.37
1.48
0.33
6
250
5
8
0.36
1.48
0.36
7
250
3.5
6
0.35
1.48
0.33
8
300
3.5
6
0.35
1.45
0.37
9
350
2
4
0.33
1.45
0.18
10
350
5
8
0.36
1.36
0.37
11
250
2
8
0.35
1.45
0.20
12
250
5
4
0.40
1.5
0.22
13
350
5
4
0.39
1.49
0.33
14
300
3.5
8
0.37
1.47
0.46
15
300
3.5
6
0.35
1.46
0.30
16
300
3.5
6
0.35
1.46
0.32
17
250
2
4
0.35
1.46
0.10
18
300
3.5
6
0.35
1.46
0.31
19
350
2
8
0.33
1.32
0.26
20
300
5
6
0.34
1.45
0.33
The experiment was carried out on Schleif SA5/2U x 1000 cylindrical grinding machine as shown in the figure.2. The grinding wheel specifications are 300 mm X 127 mm X 40 mm Al2O3.
Figure2
-
Measurements
The surface roughness (Ra, Rz) values were measured on Taylor Hobson surtronic 3 for 0.8 mm of cut off length over a length of 4 mm normal to grinding surface as shown in figure 3.
MRR is calculated by taking the difference in the weights of the work piece, before and after grinding, and dividing by the time required for machining the workpiece.
Table 3
Figure3
Figure 4. Grinding of OHNS material
4.RESULTS
The main effects plot for Ra is shown in Graph.
Graph 1
Graph 2
Graph 3
With reference to above graph, as the speed increases from 300 to 350 RPM the value of Ra decreases from 0.362 to 0.352m. With the increase in feed leads to increases the Ra value from 0.357 to 0.39 m. The Ra value sub side from the value of 0.357 to 0.356 as the number of passes increases from 6 to 8, but as from the trend of the graph it can be concluded that even if the number of passes is increased beyond 8 there should not be many changes seen in the Ra value. Thus, with a low feed value and high workpiece speed with six number of passes we can obtain a Ra value in the range of 0.35 to 0.36 m and Rz in the range of 1.32 to 1.5 m.
The main effects plot for MRR is shown in Graph
Graph 4
Graph 5
Graph 6
Thus, with reference above graphs for MRR verses work speed, feed, and number of passes. The increase in feed (m/min) will give the more value of MRR. As surface roughness is the most important response in cylindrical grinding to obtain the Ra value between 0.35 to 0.36 and Rz value from 1.32 to 1.5 m, the metal removal rate will be in the range of 0.2 to 0.3 gms/sec. Thus, the increase in work speed results in better value of Ra and Rz with higher metal removal rate of 0.34 gms/sec.
The main effects plot for Rz is shown in Graph.
Graph 7
Graph 8
Graph 9
It is clear from the above graphs that as the speed increases from 300 to 350 RPM the value of Rz decreases from1.48 to1.32 m. Though the increase in the feed increases the Ra value from 1.32 to 1.5 m. The Rz value decreases from1.52 to1.32 m as the number of passes increases from 6 to 8.
Residual Stress Result for Specimen 01,19,13,17and 14 (Min Ra, Max Ra and Min MRR, Max MRR)
Spec imen No.
Residual Stress
Residual Stress (MPa) at Various Psi
900
1800
1350
Before Grinding
01
56.2
-304.9
-124.3
After Grinding
19
-781.3
-157.6
-385.3
13
205.7
-272.5
-33.4
17
70
-268.3
-99.2
14
363.3
194.8
279.0
Table 4
Fig. 5. XRD analysis of an OHNS at Ø 900 for Minimum Ra and Rz
Fig.6. XRD analysis of an OHNS at Ø 1800 for Minimum Ra and Rz
Fig. 7. XRD analysis of an OHNS at Ø 1350 for Minimum Ra and Rz
Stress tensor
Fig. 8 XRD analysis of an OHNS at Ø 900 for Maximum Ra and Rz
Fig. 9 XRD analysis of an OHNS at Ø 1800 for Maximum Ra and Rz
Fig. 10 XRD analysis of an OHNS at Ø 1350 for Maximum Ra and Rz
Stress tensor
Fig. 11. XRD analysis of an OHNS at Ø 900 for Minimum MRR
Fig. 12. XRD analysis of an OHNS at Ø 1800 for Minimum MRR
Fig. 13. XRD analysis of an OHNS at Ø 1350 for Minimum MRR
Stress tensor
Fig. 14. XRD analysis of an OHNS at Ø 900 for Maximum MRR
Fig. 15. XRD analysis of an OHNS at Ø 1800 for Maximum MRR
Fig. 16. XRD analysis of an OHNS at Ø 1350 for Maximum MRR
Stress tensor
4.CONCLUSION
After conducting the cylindrical grinding experiment on OHNS rounds work piece the following conclusions are made:
-
Work speed (rpm) and number of passes are the main effecting parameters for surface finish. Whereas feed(m/min) plays an important role in deciding the metal removal rate (MRR).
-
To obtain the surface finish of 0.35 to 0.36 m the work speed can be kept in the range of 300 to 350 rpm with 6 numbers of passes and feed of 2m/min.
-
The MRR can be obtained in the range of 0.30 to 0.32gms/sec for the above parameters
-
The residual stress results for Surface Roughness and MRR shows that as the speed increases the compressive residual stress are developed in specimen for obtaining surface roughness in range of 0.35 to 0.36 m. As the metal removal rate is increases for 0.2 to 0.3 gms/sec tensile stresses are developed
-
The X-Ray diffraction (XRD) is the best methods available for residual stress determination. The results were obtained for minimum and maximum average roughness to be – 781.3, -157.6, -385.3, 205.7, -272.5, and – 33.4 in the X- direction. The results were obtained for minimum and maximum MRR to be 70, -268.3 -99.2, 363.3, 194, and 279.0 in the X- direction for cylindrical grinding for various phi angles
-
The negative values of residual stresses which mean the state of residual stresses exist are compressive and positive values are tensile stress which are detrimental and tensile residual stresses decrease the fatigue, increases the possibility of crack initiation, and may cause fatigue failure
-
Residual stresses are algebraically summed with applied stresses. The surface residual tensile stresses with applied tensile stress can reduce the reliability of the material. Residual tensile stresses are consistently sufficient to cause stress corrosion cracking.
-
REFERENCES
-
-
I.S. Jawahir, E. Brinks Meier, R.M Saoubi, D.K. Aspinwall, J.C. Outeiro, D. Meyer, D. Umbrello and A.D. Jayal, Surface integrity in material removal process: Recent advances, Manufacturing Technology, vol. 60, issue2, pp.603-626, January2011.
-
Manchao Zhang, Zhenqiang Yao, Sheng Xu, Optimization of Roughness and Residual Stresses in Path Controlled Grinding of Crankpin (2015), pp (177-222)
-
Shrikant Thorat, Mudigonda Sadaiah The effect of residual stresses, grain size, grain orientation, and hardness on the surface quality of Co-Cr L605 alloy in Photochemical Machining Journal of Alloys and Compounds 804 (2019) 84-92
-
Suleyman Neseli, Ilhan Asilturk and Levent Celik, Determining the optimum process parameter for grinding operations using robust process, Springer, May 2012.
-
V. Saravana Kumar, Hridul Pavithran and Sachin K.V, Optimization of process parameters on SS410 in cylindrical grinding process, IJERT, vol. 3 Issue 4, April 2014.
-
Karanvir Singh, Pralad Kumar and Khushdeep Goyal, To study the effect of input parameters on surface roughness of cylindrical grinding of heat treated AISI4140 steel, AJME, vol. 2, May 2014.
-
K. Mekala, J. Chandrada S, K. Chandrasekaran, T T M kannan, E Ramesh and R Narasing Babu, Optimization of cylindrical grinding parameters of austentic stainless steel rods (AISI316) by Taguchi method, IJMERR, vol.3, April 2014.
-
M. Ganesan, S. Karthikey and N. Karthikeyan, Prediction and optimization of cylindrical grinding parameters for surface roughness using Taguchi method, IOSR-JMCE, pp.39-46.
-
EI- Helieby & G.W. Rowe, Influences of Surface Roughness and Residual Stress on Fatigue Life of Ground Steel Components (2013) pp, (221-225)
-
M. Kiyak, O. Cakir and E. Altan, A study on surface roughness in cylindrical grinding, Achievements in Mechanical and Materials Engineering, pp.459-462,2003.
-
Dayananda Pai, Shrikantha S. Rao, Rio D Souza, Multi objective optimization of surface grinding process by combination of response surface methodology and enhance on dominated sorting genetical algorithm, IJCA, vol.36, December 2011.