
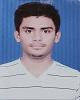
- Open Access
- Authors : Mehul Rathod , Vikas Jotangiya , Ankit Shrimali , Mo. Mohatsim Pathan
- Paper ID : IJERTV9IS030577
- Volume & Issue : Volume 09, Issue 03 (March 2020)
- Published (First Online): 07-04-2020
- ISSN (Online) : 2278-0181
- Publisher Name : IJERT
- License:
This work is licensed under a Creative Commons Attribution 4.0 International License
A Research on Development of Induction Oven for Food Delivery Vehicles
Vikas Jotangiyaa , Mo. Mohatsim Pathana , Ankit Shrimalia , Mehul Rathodb aResearch Scholar, LJ Institute of Engineering and Technology, Sarkhej , Gujarat, 382210, India bResearch Scholar , Gandhinagar Institue of Technology, Gandinagar, Gujarat – 382721, India.
Abstract:- In this era of dynamic changes and cut throat competition; to survive and to thrive , people are busy in earning like never before. They want to spend minimum time possible in doing things like cooking , travelling , house cleaning which are necessary yet not priority. So they look for alternate less time consuming options to get this chores done in a way that it has least affect on their working schedules. Eating healthy food and maintaining health is another aspect that can not be compromised to keep up with the competition. So people look for food which along with satisfying their taste buds ,is healthy for their digestion system. As cooking quality food takes time,so being an generation which for the most problems of their lives, looks for a solution on internet, people started relying more upon food of hotels and their instant deliveries on their door steps which turned out to be the primary reason of success for global food delivery brands like Uber eats, Grubhub, Just Eat , Olo , Snap finger and etc. They have established their centers world wide and keep expanding their boundaries rapidly.We have visited some of them and were talking about problems they faced while they have been receiving orders and problems regarding delivery of food. The primary problem way,in many cases,the house or office of customer were far from delivery start point so it became tough for them to deliver fresh food to customer. After receiving several problems of similar manner , they started using a mechanism of heating the food in the delivery vehicle itself but it uses battery as a source for heating the food and hence they have to charge the battery in short intervals, change it when its lifetime is over which has its own drawbacks like more consumption of time and increased cost of delivery so it is not preferable.As part of the solution to this problem, we particularly focused on Induction heating used in Heat Treatment Processes but we have used this concept of induction heating in heating the food until it is not delivered to the customer. This research paper gives in depth idea about a device which can keep the food as warm as possible using engine power in a way that it does not affect engine efficiency and also keeps the food warm until it is not delivered to the customers.
1. INTRODUCTION:
The main and necessary requirement of customers is, they want fresh and warm food when they receive it . The actual problem is that how can companies deliver warm food at any time after backing it.There is a time period of approximately 15 minutes from making food to delivering it at required place and in this period the food gets cool and sometimes the quality is also diluted. To overcome this problem, initially companies needed to establish more than one centre approx. at each and every 6 km distance.Due to which, they had to do huge investment and face management problems.
An alternate and effective solution to this problem is to keep the food as warm as possible until it is not delivered to the customers without using any kind of external battery , rotational energy of engine shaft is used here to produce electricity by the use of alternator or dynamo and this electricity is passed through heating coils which is wrapped around the strip placed between main storage box & outer box which keeps the food warm.Thus it works without utilizing any kind of external source.
-
MARKET SURVEY:
Visits of different food delivery companies like Dominos, Pizza hut, etc. concluded following information for us :
-
The pizza box is supposed to allow the transport of a baked pizza with the minimum loss in quality possible. To reduce heat flow, the box has to be closed as firmly as possible to keep the warm air inside. Consumers consider a temperature between 70 and 85°C to be ideal for pizza consumption. On the other hand, the box should keep the pizza from getting soggy, so that the crust and the covering are crisp on arrival. To ensure this, the condensation caused by the pizza must be let out (airing holes and some diffusion through the cardboard) or absorbed by the box.
-
There are special padded transport bags and boxes for delivery. Some of these bags can be heated in order to keep the temperature at the desired level. Mostly, they can either be plugged to a socket or powered by the 12 volt car battery. This means that the insulation of pizza boxes themselves is less important. Carry bags insulate best when their lid is connected to the rest of the bag on one side and the remaining three sides can be attached to lid by a zip. A bag can contain about three to five pizza boxes.
-
REQUIRED COMPONENTS SPECIFICATIONS
-
Sr. no.
Component name
Material & Specification
1.
Heating coil
Copper – 4 gauge , 7.9m length
2.
Strip
Iron -15inch, 25.4mm dia.
3.
Main storage box
Aluminum 606 – 15*15*15inch
4.
Outer box
Fiber -24*24*20 inch
5.
Insulating material
Glass wool 2 inch layer
6.
Support plates
Iron
7.
Connecter
——-
8.
Electric wires
Copper
9.
Rectifier
——–
10.
Invertor
——–
11.
Alternator / Dynamo
12V , 55 Amp maruti800 car alternator
11.
Pulley & Belt
Cast iron pulley , Fabric belt
12.
Battery
12 V , Exide Xplore (12XL5L-B)
13.
Fan
Sun Robotics DC Fan – 80X80X25MM (12V)
14.
Thermostat
———-
15.
Panel circuit
———–
-
-
COMPONENTS:
-
HEATING COIL – It is mainly used to heat our main storage box at desired temperature.It is placed inside the outer box and wrapped around strips which are made of ferrous material, so heating is produced inside the core of heating element.
-
STRIP – Strips are made of ferrous material like as Cast Iron which is used as heating coil core.They are placed at outside the main storage box and welded to it.
-
MAIN STORAGE BOX- The food is being stored in a main storage box and it gets heated by the heating coils.
-
OUTER BOX- The outer box carries main storage box & heating coils. It also reduces the heat loss.
-
INSULATING MATERIAL- The main function of insulating material i.e. Glass wool is to reduce heat loss by convection & radiation (conduction is negligible.).
-
SUPPORT PLATES- The main function of support pltes in our product is to support the assembly of main storage box, heating coils & outer box. It is able to withstand the load of the assembly.
-
CONNECTOR – Connector is used to connect the heating coils with input phase wires which are connected through Alternator as input source.
-
ELECTRIC WIRES – The main function of electric wires is to allow the electricity to flow from one device to the other.
-
RECTIFIER- Rectifier is previously attached to the Alternator which is generally used in automobile industries and can be used as converter of current from A.C. to D.C.
-
INVERTOR – Invertor is a device used for conversion of Current from D.C. to A.C. current and furthermore it can be used to increase phase current frequency and amplitude .
-
ALTERNATOR / DYNAMO- Alternator is used to produce an electric current by means of conductive material loop cuts the permanent magnetic field and hence produces the phase current. It mainly produces an A.C. current. Dynamo can be optionally used instead of Alternator.
-
PULLEY & BELT – The main function of the pulley- belt drive is to transmit power engine shaft to alternator pulley.
-
BATTERY- Battery is used to provide start up power to the Alternator we have used in our project.
-
FAN – Fan is placed outside the main storage box and is used to maintain air circulation inside the box.
-
THERMOSTAT – Thermostat is used to control the fluctuation of temperature inside the box which is aroused due to the fluctuation of input phase current.
-
PANEL CIRCUIT – Circuit board used in our project to indicate the temperature state.
-
DESIGN CALCULATION:
[3D MODEL OF STORAGE BOX] [ACTUAL MODEL ON DELIEVRY VEHICLE]We have to maintain 70 temperature inside the main storage box with the help of heating coils for maintaining quality of the food.
Design calculations for maintaining 70 inside the main storage box:- For air:
= ()
= mass of air inside main storage box =
= Density of air = 1.225 kg/3 at 25
V = volume of air inside main storage box = 0.381*0.381*0.381 3
= 0.0553 3
= 1.225*0.0553 = 0.0677 kg
() = 0.718 kJ/kg-k
= 1 2
1= Temperature inside the main storage box = 70
2= Lowest atmospheric temperature = 18
= 70 18 = 52
= 0.0677*0.718*103*52
= 2529.23 J
For Aluminum box
=
= mass of aluminum box =
= Density of aluminum = 2700 kg/3
Calculation of mass of aluminum box: Iteration 1:
Assume thickness of aluminum sheet = 16 gauge
= 1.291 mm
= 0.001291 m
Volume of aluminum box = 0.381*0.381*0.001291
= 1.8740*104 3
= 2700*1.8740*104 = 0.5 kg This is quite light.
Iteration 2:
Assume thickness of aluminum sheet = 14 gauge
= 1.628 mm
= 0.001628 m
Volume of aluminum box = 0.381*0.381*0.001628
= 2.36*104 3
= 2700*2.36*104 = 0.638 kg
This is suitable mass for aluminum box.
= 0.921 kJ/kg-k
= 1 2
1= Temperature inside the main storage box = 70
2= Lowest atmospheric temperature = 18
= 70 18 = 52
= 0.638*0.921*103*52
= 30561.60 J
Total heat requirement:
= 2529.23 + 30561.60
= 33090.83 J
Time up to which we required amount of heat = 5 min
= 300 sec
Power required = / time
= 33090.83 / 300
= 110.30 watts Input power (source power): P = V*I
V = Voltage of alternator = 14.4 v at full load condition
I = Current from alternator = 55 Amps (maximum capacity)
P = 14.4*55
= 792 watts
Dimension calculation of heating coil:
Outer diameter of strip on which heating coil is wrapped
= 35.4 mm (assume)
Perimeter of the strip = D
= 0.1112 m
Length of the coil / strip = (0.1112)*0.381 / d Where, d = diameter of heating coil
We know that, P = I2*R
110.3= 552*R
R = 0.036
We know that,
R =
= Resistivity of heating coil material
Iteration 1:
We take Nichrome as a heating coil material.
nichrome = 1.1*106 .m
6
6
0.036 = 6* [1.110
0.11120.381 ]
d = 21.46 mm
( )
2
2
4 d
This is a very large diameter of heating coil which is not suitable.
Iteration 2:
Now, we take Copper as a heating coil material.
copper = 1.72*108 .m
8
8
0.036 = 6* [1.7210
0.11120.381)]
d = 5.36 mm
(
2
2
4 d
This is quite suitable diameter as compared to nichrome diameter.
d = 5.36 mm = 4 gauge
So, length of wire / strip = (0.1112)*0.381 / 5.36*103
= 7.9 m
Ltotal = 6*7.9 m = 47.42 m
Temperature generated on the strip:
=
= 33090.83 J
= 0.385 kJ/kg-
= mass of copper wire =
= Density of copper wire = 8960 kg/3
V = volume of copper wire = 2 = 0.005362 7.9
4 4
= 1.78*104 3
= 8960*1.78*104 = 1.6 kg
33090.83 = 1.6*385*(1 25)
1= Temperature generated on the strip 25 = Surrounding temperature
1= 78.7 80
Heat loss calculations:
Internal convective resistance = 1
Calculation of h (heat transfer coefficient):
Fan given below is used for proper circulation of hot air inside heating box so that it can be kept warm uniformly leading to increased efficiency of heating box.
Specification of fan: Length: 40mm Width: 40mm Thickness: 15mm Voltage: 12V Current: 0.9Amps RPM: 12000
Air flow: 14 CFM (Cubic feet per minute)
Conversion of CFM: Image given above shows conversion of unit of air flow from CFM to m/s using online convertor [3]. From above figure,
14 CFM = 0.05 m/s (air velocity)
Graph of h vs. air velocity From graph it is clear that value of h for air = 22 W/m2-k Internal convective resistance = 1
22(0.3810.381)
= 0.313 k/W
Internal conductive resistance in aluminium sheet
=
Thickness of sheet = 0.001628 m
= 235 W/m-k
Internal conductive resistance in aluminium sheet
= 0.001628 235(0.3810.381)
= 4.77*105 k/W (Negligible) Total resistance = 0.313 k/W
Power loss ( ) = 12
= 8070
0.3136
= 5.32 watts
POWER LOSS = 5.32 W
-
CONCLUSION:
After shortlisting certain materials for heating box and coil, calculations were carried out to finalize the materials for same along with them calculations for temperature generated on strip using this material, for power loss in conduction ,convection and radiation were also done and here is a summary of all the calculations:
Considering extreme conditions of achieving 52 degree celsius temperature difference,under which this system might have to operate, using aluminium box of 14 guage thickness is preferable with heating coil having copper as a material. Resistivity of copper is perfectly suitable for this system as diameter calculated based on it satisfies space criterion of this system. Applying all these specifications, temperature generated on strip comes out to be approximately around 80 degree celsius along with power loss of 5.32 watt which is viable for industry requirements.
-
REFERENCES:
-
-
-PORTABLE WARMER by Charles A. Walton, 19115 Overlook Rd., Los Gatos, Calif. 95030
-
-Food delivery hot bag with electric hot plate by Harold D. Solomon , Wayne R. Greve
-
– http://www.kylesconverter.com/flow/cubic-feet-per-minute-to-cubic-meters-per-second