
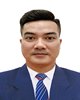
- Open Access
- Authors : Tuan Anh Nguyen , Ha Manh Bui
- Paper ID : IJERTV11IS060014
- Volume & Issue : Volume 11, Issue 06 (June 2022)
- Published (First Online): 07-06-2022
- ISSN (Online) : 2278-0181
- Publisher Name : IJERT
- License:
This work is licensed under a Creative Commons Attribution 4.0 International License
A Novel Approach to Roller Compacted Concrete Construction Technology for Bridge and Road Construction
Ha Manh Bui1, Tuan Anh Nguyen2,*
1Hoang Ha Industrial Construction JSC., Ho Chi Minh City, Vietnam
2Ho Chi Minh City University of Transport, Ho Chi Minh City, Vietnam
Abstract – Currently, Roller Compacted Concrete (RCC) technology is widely used in hydropower and irrigation projects. However, the application of this technology for road and bridge works has not been studied yet. This paper uses experimental methods to compare roller compacted concrete with asphalt concrete and conventional concrete in various aspects to highlight the advantages of RCC construction technology, thereby proposing a quality control process. RCC volume in traffic works. Research results show that RCC has the ability to develop greater strength than conventional concrete, with R90 of 145% and 115% respectively, with R180 of 170% and 120% respectively. RCC technology is best used for bridge decks and pavements of class II and below, or pavements of grade I but with a vehicle speed of not more than 60 km/h. In the case of using RCC technology as the roadbed, it can be applied unlimitedly to all road grades.
Keywords – Roller compacted concrete, road and bridge construction, strength, quality, technology.
-
INTRODUCTION
The Government's policy in recent years is to increase the use of cement concrete for road works to make full use of the capacity of domestic cement factories, to stimulate domestic production without spending foreign money. currency to import plastic, making the life of the road longer. Therefore, the research and development of an optimal method to construct cement concrete roads quickly, with high mechanization, saves a large amount of cement, takes advantage of many types of waste products of power plants (such as ash and ash flying, blast furnace slag …), being able to apply in practice is an urgent requirement.
As is known, the strength of concrete strongly depends on the water/cement ratio. If the amount of mixing water is reduced, it is possible to reduce the amount of cement in the mixture without changing the concrete strength. Due to the reduced amount of mixing water, the concrete is as dry as the soil. If you want to compact it, you must use a vibrator instead of a hammer like traditional concrete. Roller compacted concrete – the type of concrete that can be mechanically constructed with little cement – is born from such simple ideas. In the world, advanced countries have applied roller compacted concrete technology since the 30s of the last century. Vietnam has also applied this technology to hydropower dams and irrigation. However, the application of roller compacted concrete construction technology for road
and bridge construction has not been given due attention.
For dyke projects for hydropower and irrigation, RCC has been widely used since the 60s of the 20th century. In 1961, there was a dike around the center wall of the Shimen dam in Taiwan China, until 1980 – 1984 in Japan, UK, USA also
applied RCC technology to build concrete dams. In 1986 – 1989 in China, construction of roller compacted concrete dams Khangkou, Thien Sinh Bridge, Long Mon Than, Phan Gia Khau, etc. [5].
For road and bridge construction, in early 1930, RCC was first studied and applied to road pavement in Switzerland. In 1942, the US Army used roller compacted concrete to build the runway at Yakima, Washington. In 1970, Canada built roads and parking lots. From the 1980s onwards, the US Army Corps of Engineers researched and applied RCC for military purposes [10].
Up to now, in the world, roller compacted concrete has been applied by many countries to urban roads, intersections, parking lots, roads in industrial parks, warehouses, and heavy cargo ports. In Vietnam, many hydropower projects have started to pay attention to the use of roller compacted concrete to build gravity dams for reservoirs, such as Dinh Binh, Dong Nai 3, Dong Nai 4, Son La dams… However, the application of roller compacted concrete for road and bridge construction in Vietnam is still very limited [5].
This paper focuses on comparing roller compacted concrete with asphalt concrete and conventional concrete in many different aspects to highlight the advantages of this technology. At the same time, study the necessary conditions for RCC technology to promote its advantages well.
-
RESEARCH OVERVIEW
-
Roll compacted concrete
RCC for pavement structure is classified as hard pavement. When RCC reaches its design strength, it has great stiffness, it absorbs most of the load caused by the vehicle and transmits that load to the foundation over a very large area, so the RCC sheet is the main bearing layer. [1].
However, in actual construction, the RCC pouring block must be stable right after the compaction is completed (immediate stability). To meet this requirement, the freshly laid RCC layer must be compacted to a high degree of compaction and allow construction equipment and transport vehicles to travel on it before hardening. This property belongs to the semi-rigid pavement structure, which is a type of pavement with a sandstone-graded foundation reinforced with cement and additives [2].
So, we can split it into two stages to be able to provide a solution to behave in accordance with the working principle of RCC materials: 1) The RCC phase is under construction, has not fully cured, and has not yet reached its strength. design (180 days from the date of laying RCC): concept of RCC as semi-rigid pavement; and 2) Phase RCC is put into use, has
reached design strength (after 180 days): Concept of RCC as hard pavement.
Because the basic characteristic of RCC is to use less cement, RCC pavement can arrange horizontal expansion joints 15-20m apart, no need for longitudinal joints and no arrangement of transmission rods, but require layers. The underlying foundation is completely similar to traditional cement-concrete pavement structures, the underlying foundation layer does not participate in large loads, but the quality must be uniform, it must be stable with water and not accumulate residual deformation.
RCC pavements must be designed to have all the same durability criteria as conventional cement concrete pavements such as: must have high flexural strength, must have sufficient reserve strength to withstand the restoring effect of loads. vehicle running and of the temperature, withstanding the wear and tear of the vehicle. In case the design of repairing the existing road is in traffic, requiring traffic to be cleared immediately after RCC is laid but not enough time to allow the RCC to harden to reach the strength, the designer must consider the RCC as a semi-rigid pavement to calculate.
With the advantages of rigid pavement, RCC pavement can withstand the large loads commonly found in road constructions, can also limit cracking caused by heavy truck axles, and the phenomenon of buckling or tearing when the vehicles turn around or brake at container yards, parking lots, docks and intersections.
-
Material composition
The materials used to make RCC include: binder (cement), aggregate (sand, stone), water, and fine-grained ingredients. Materials with physical and mechanical properties, technical standards, particle composition, etc. applicable to conventional concrete can be used for RCC [6].
However, because the main feature of RCC mixture is no slump and a low amount of cement used, the composition of materials used in RCC is different from conventional concrete, and the fine-gained content is an important factor determining the properties of RCC mixtures when hardening to reach the strength.
The fine-grained composition in RCC is a material with a particle size of less than 0.075mm (similar to the size of cement particles), that is inert, and produces no heat when mixed with water and can be used as the padded substance of cement to insert the empty holes in the RCC mixture during mixing and compaction.
The fine-grained composition used in RCC is typically the product of grinding the fly ash (the waste of the thermal power plants whose fuel is coal) and blast-furnace slag (obtained by sudden cooling of blast-furnace slag melting in water), and its main composition includes SiO2, Al2O3, CaO in crystal and amorphous form [11].
The appropriate selection and use of fine-grained composition for RCC is directly related to the construction site, concrete requirements and quality, supply ability and construction cost.
-
RCC technology construction process
RCC technology construction process is shown in Fig. 1 to Fig. 14.
Figure 1. RCC equipment line: Mixing RCC mixture at the station, transporting to the field by conveyor and dump truck, leveling and compacting
Figure 2. Stone aggregate crushing and screening station of all sizes according to the correct gradation
Figure 3. Roll-compacted concrete batching station
Figure 4. Roll-compacted concrete batching station
Figure 5. Conveyor feeding rocks to the mixer
Figure 6. Conveyor feeding sand to the mixer
Figure 7. RCC mixer
Figure 8. Cement and fly ash storage silos
Figure 9. Portion of the water feeding to the RCC mixture is cooled to ice
Figure 10. Adding ice to lower the inlet aggregate temperature
Figure 11. Transport equipment
Figure 12. Leveling RCC by bulldozer in hydropower project
Figure 13. Compacting RCC by compactor, in hydropower project
Figure 14. Application of RCC spreader for road works, similar to hot asphalt concrete carpeting
Figure 15. Application of rubber wheel roller to smooth RCC surface for road works, similar to hot asphalt concrete
Figure 16. Application of iron wheel roller to smooth RCC surface for road works, similar to hot asphalt concrete
-
-
COMPARISON OF ROLLER COMPACTED CONCRETE CONSTRUCTION TECHNOLOGY FOR
ROAD AND BRIDGE CONSTRUCTION WITH ASPHALT CONCRETE AND CONVENTIONAL CONCRETE
-
The level of economical use of materials, making use of local materials
Stone and sand aggregates for asphalt roads can be utilized, but only asphalt must be imported. Every year, Vietnam needs
$60 million to import asphalt for transportation construction.
All of the aggregate components of stone and sand used to make concrete for conventional concrete roads are locally sourced. The use of cement for road construction is encouraged by the state to make full use of the capacity of domestic cement factories, thereby stimulating domestic production.
For RCC, in addition to the advantages of conventional concrete, RCC offers the advantage of utilizing a cement amount that is about 35% less expensive than conventional concrete with the same strength. Furthermore, the fine-grained composition for RCC can be derived from power plant wastes (such as fly ash, blast-furnace slag, etc.), which would be exceedingly wasteful if there was no way to use it.
Table 1. Experimental results on cement savings of RCC [10]
Rate of using fly ash to replace cement
0%
25%
30%
35%
Cement (kg)
301
240
225
212
Fly ash (kg)
0
76
92
109
Stones 5-20 (kg)
1 136
1 136
1 136
1 136
Sand (kg)
895
895
895
895
Water (litre)
149
130
127
124
Compressive strength after 7 days (MPa)
28.68
26.62
24.86
23.76
Compressive strength after 28 days (MPa)
35.30
33.38
33.03
32.21
Compressive strength after 56 days (MPa)
42.90
40.45
38.35
37.20
Splitting tensile strength after 7 days (MPa)
3.33
3.12
2.83
2.32
Splitting tensile strength after 28 days (MPa)
3.60
3.20
3.01
2.65
Resilience Module after 7 days (MPa)
26.189
25.228
24.381
23.832
Resilience Module after 28 days (MPa)
29.050
28.251
28.104
27.750
Water penetration depth (m)
120
42
35
31
Average abrasion (g/cm2)
0.37
0.42
0.31
0.34
The asphalt roads must be scraped off and dumped away at the end of their useful lives because the asphalt materials have aged and degraded. However, for RCC and conventional concrete, they can be completely reused as a road foundation material.
Through the above analysis, it is seen that RCC uses a variety of domestic materials that Vietnam can self-produce rather than import, such as sand, stone, cement, and fly ash. Despite this, RCC also employs a cement amount that is 35% less expensive than conventional concrete of the same strength.
-
Level of mechanization application
In fact, conventional concrete is being constructed by manual labor, some of which can be mechanized, such as mixing concrete at the station, transporting concrete by mixer truck and concrete pump or using a crane to lift the concrete buckets to the pouring location. Only on large projects with stringent technical requirements and a compressed construction schedule can mechanized concrete pouring and leveling lines be used. Conventional concrete roads are rarely utilized because pouring concrete manually is difficult to ensure uniform quality, progress is very slow, and the workload of pavement construction is very large for each road construction project in general.
Asphalt concrete has been mechanized throughout the entire process such as from mixing asphalt at the station, to transporting to the pouring location by dump trucks, spreading asphalt concrete with specialized spreaders, and compressing asphalt concrete with 10 ton vibratory rollers first and then pneumatic tyred rollers.
RCC is also mixed at the centralized station, then use a dump truck to transport it from the batching plant to the RCC spreaders on site (using an asphalt spreader) to level the RCC into layers, then use a 25T vibrating roller to compact the RCC mixture to the design weight, using a combination of 10T iron and tire rollers to complete the surface and create a flatness of the road surface.
Thus, RCC construction technology has both mechanized and synchronous characteristics like asphalt concrete construction technology, but uses materials with properties similar to conventional concrete.
-
Compare product prices
The goal of comparing prices at a particular point in time, and at a particular site, is to provide more intuitive parameters to gauge the savings of each type of technology applied.
Table 2. Compare prices per 1m3 concrete
Unit: VND/m3
Names of work
Total (VND)
Material gradation
Production at the station
Transport to the dump site, distance of 1km
Unit
m3
m3
m3
Fine-grained hot asphalt concrete
3.094.164
150.848
98.419
3.343.431
hydropower RCC M120
828.170
65.368
36.975
930.514
RCC road bridge M200
989.229
81.182
98.419
1.168.829
Conventional concrete M200
1.160.772
81.182
118.692
1.360.646
The material price parameters for comparison were taken in June 2013, in Son Ha District – Quang Ngai Province, including the transportation of materials to the foot of Dakdrinh Hydropower Plant [12].
Comments:
RCC used for hydropower dam has a much lower price than conventional concrete and hot asphalt concrete when calculated in m3 products are manufactured and transported to the place of dumping, because the characteristics of hydropower projects are concentrated in a focal area, concrete has a large volume and size, so it is necessary to minimize the amount of cement to prevent shrinkage due to the dehydration of cement, the hydropower dam is a gravity dam, so the strength of the RCC dam core is only 120MPa, the construction equipment has a very large capacity: 250m3/h batching plant, 22 tons of trucks, construction roads are designed specifically for specialized transport vehicles.
To be able to apply RCC to road and bridge construction, we need:
Increase the amount of cement from 70kg/m3 up to 212kg/m3 so that RCC can ensure the strength of 200MPa, the amount of fly ash that can replace cement is 109kg/m3 and not to exceed 35% of the total cement applied to conventional concrete of the same strength,
Capacity of RCC station should only choose 60m3/h when applying RCC for road and bridge works to suit the long- distance construction, the volume of one-time dumping is not too large, often interrupted, and the truck only chooses up to 12T to take advantage of existing transport system.
When applying the above adjustments, we see 1m3 RCC M200 applied to roads and bridges also has a much higher economic value than the other two technologies: with conventional concrete, RCC saves 15%; With hot asphalt concrete, RCC saves up to 65%.
-
Scope of application of each type for road and bridge works
-
Conventional concrete:
Applicable to works with steep slope and large curvature such as Ho Chi Minh road when passing through passes and mountains.
Roads are likely to be overflowed by water when the flood season arrives, often found in the Central region,
Wharfs, airport runways, heavy loads.
Rural roads, villages, border areas and small traffic works are also often used.
– Hot asphalt concrete:
Currently, hot asphalt concrete is being applied in most types of pavement for all road levels because of its smoothness, ease of construction and rapid construction with large volumes.
When necessary, additional admixtures can be mixed to improve some properties of asphalt concrete such as: high fatigue resistance, wheel rutting resistance, good shear resistance, low temperature sensitivity, etc., so asphalt concrete is increasingly dominant and widely used.
The disadvantage of asphalt concrete is that the life of the plastic is not high, it cannot be reused when repairing and renovating roads and especially the cost of this material is too high.
– RCC:
RCC differs from conventional concrete in its construction method, machine compaction and RCC mortar without slump make RCC surface finishing more difficult, therefore, RCC is recommended to be applied only to level II pavement and below.
RCC is suitable for pavements of all grades if covered with asphalt pavement.
RCC, when reaching the design strength, has all the characteristics of conventional concrete, so all kinds of roads with steep slopes, needing high grip, anti-slip, and heavy loads are suitable for RCC.
-
-
The suitability of equipment and technology for roller compacted concrete construction for road and bridge works
We have compared the technologies on three aspects: Economical use of materials, utilization of local materials, degree of mechanization, and calculation of cost per square meter3 material. To determine the applicability of RCC for road and bridge construction, we consider some more aspects as follows:
-
Production process
Hot asphalt concrete requires high temperature for aggregates, so it consumes a lot of energy.
Conventional concrete and RCC are manufactured by cold process, not heating.
-
Repair and maintenance
Conventional concrete and RCC roads are easy to repair, when they need to be repaired, the repair range is also less than that of asphalt concrete roads, but because the durability of these two types of roads is quite large, almost no annual maintenance is required.
-
Time allowed for traffic:
Asphalt concrete roads can be used immediately after the carpet is completed, creating favorable conditions for traffic to solve traffic jams, especially construction at existing road repair and improvement works.
Conventional concrete roads take 28 days to cure the concrete until it reaches the design strength to open to traffic.
It took 180 days for the RCC to reach its design strength, but due to the instantaneous stability of the RCC dump, it was allowed to open for traffic within 24 hours.
-
Reliability:
Conventional and RCC concrete roads are durable, have an average service life of 30 to 50 years, withstand heavy loads, and still develop strength over time.
For lower strength asphalt roads, ruts may form because the asphalt mixture has a weak resistance to high temperatures in summer even when the vehicle is stopped on the road or has accumulated damage under load of a vehicle traveling at high speed. And due to the impact of sunlight, air and other climatic factors, it changes the chemical composition of the asphalt, making it hard and brittle, causing aging and peeling, so the service life is not long.
-
Safety:
Conventional concrete and RCC roads are easy to create roughness during construction, making vehicles running on this type of road have high traction, due to the hardness of concrete, the rough edges are durable over time, the concrete surface has a light color, so can reflect light, improving visibility for drivers.
Asphalt concrete roads when it is sunny, there is a phenomenon of "plastic flow", making the road surface slippery, reducing the vehicle's grip, and the road surface is black, so it is not good for drivers' vision at night.
-
Smoothness
The smoothness of the asphalt concrete road is the highest
For conventional concrete roads, we have to design joints, expansion joints both horizontally and vertically, the density of joints is quite thick, the horizontal joints are about 5-7m apart and so the vehicle is not smooth when entering the gap or entering concrete slab corner
For the RCC road, there is no shrinking joint, no longitudinal joint, only spacing joints are arranged quite far apart, about 20-30m, this type of road belongs to a relatively smooth form.
Table 3. Comparison table of 3 construction technologies [3, 6-8]
Targets
Hot asphalt concrete
Roller compacted concrete
conventional concrete
The level of economical use of materials, making use of local materials
Low
High
Medium
Degree of
mechanization
High
High
Low
Price per 1m3 product
High
Low
Medium
Production process
Heated
Cold process
Cold process
Repair and
maintenance
Difficult
Easy
Easy
Time allowed for traffic
Right after spraying
24 hours
28 days
Reliability
10-15 years
30-50 years
30-50 years
Safety
When it's sunny, the road surface is slippery, reducing traction
Easy to roughen the road surface High traction
Easy to roughen the road surface High traction
Smoothness
High
Medium
Low
If rated, RCC will be a material in the middle -middle grade-compared to hot asphalt and conventional concrete: Acceptable quality, fast construction, cheap price.
-
-
-
Conditions for construction technology of roller compacted concrete to promote its advantages in road and bridge construction
In case only RCC is used as a road foundation, the road surface is covered with hot asphalt:
The roadbed – the ground surface before placing RCC – must meet the standards for hard pavement: Since the RCC is designed as a rigid foundation, it is necessary to ensure that the RCC plates evenly distribute the pressure on the ground and
that the ground deformations are within the allowable limits. In addition, the thickness of the RCC road foundation layer needs to be calculated to be large enough to ensure the strength of vehicle load bearing capacity for each road grade as prescribed.
In case the road foundation is weak but the soft soil layer is not too thick: can proceed to pour two or more layers of RCC road foundation. The bottom layer adjacent to the ground can be thought of as a soft foundation (such as a cement-reinforced rock foundation) that allows settlement depending on the stiffness of the ground during the time the RCC is consolidating; the upper layer is poured after layer 1 has subsided and reached the design strength, at this time, the upper layer is a hard foundation on the foundation (layer 1) with high load capacity.
Because the thickness of the foundation layer is usually large, it is necessary to arrange expansion joints between 10- 15m apart to avoid cracks due to heat shrinkage and cement hydration.
In case RCC is used as pavement layer and bridge deck cover:
RCC surface has 20-30m horizontal expansion joints, difficult to finish and difficult to ensure surface flatness, so RCC is recommended to be used only for pavement and bridge deck coatings of grade II or lower, or grade I road surfaces but with a vehicle speed not exceeding 60km/h;
-
-
RCC CONCRETE QUALITY CONTROL PROCESS
-
RCC experiment
-
RCC aggregate experiment
– Facts should be known when designing RCC aggregate: For roller compacted concrete mixes: Working time Vc,
strength, waterproofing, setting time of the concrete mix.
For sand: Specific gravity, particle composition. For stone: Dmax, particle composition, density.
For cement: Compressive strength at 28 days old, density, volumetric weight.
For active mineral additives: Specific gravity, percentage of mineral additives in the binder.
-
Working time (Vc)
Working time (Vc) is a property of the roller-compacted concrete mix, through which it is possible to determine the ability to pour and compact the roller-compacted concrete mix with the appropriate type of construction equipment without causing segregation or adverse effects. to the quality of the structure.
Working time (Vc) of the roller compacted concrete mix depends on the cement content, the amount of mixing water, the content of finely ground mineral admixtures and chemical admixtures, the mix grade, the aggregate shape, the proportion of large aggregates and small aggregates.
-
Intensity
Roller compacted concrete is a poor cement concrete, the decisive factor to the strength of roller compacted concrete is
the water/cement ratio, so when using less cement, it is necessary to minimize the amount of water put into the RCC mix.
In addition, the strength of roller compacted concrete also depends on the compaction, the instantaneous stability of the poured mass and the compaction technology.
-
Waterproofing
The waterproof ability of roller compacted concrete determines the ability to resist the aggressiveness of the environment for the building. The durability of a construction from roller compacted concrete depends, in addition to its strength, on its waterproofing ability.
Roller compacted concrete is designed with a low cement content so its water repellency is often inferior to conventional concrete of the same strength. Therefore, in order to protect the cement-poor roller compacted concrete structures against environmental influences, it is necessary to calculate and design a layer of concrete richer in cement to cover the outer surface or it may be necessary to use waterproof membranes.
-
Rough aggregates
Largest size (Dmax) of large aggregates often affect stratification during transportation and leveling of roller compacted concrete mixes. With construction technology and advanced construction equipment, for gravity dam works, aggregates with Dmax up to 150mm. Usually, however, Dmax of large aggregates usually only up to 50mm.
-
Water content
Mixing water content affects the strength and waterproofing of roller compacted concrete. However, if the water content is too low, the workability Vc large, difficult to construct during compaction. Therefore, it is necessary to use water-reducing plasticizers to optimize the amount of water mixed in the roller compacted concrete mix.
-
General principles of RCC composite component design
Purpose of designing roller compacted concrete mix composition: In order to determine the content of cement ingredients, active mineral additives, large aggregates, small aggregates, water in 1m3 roller compacted concrete mix so that the roller compacted concrete mix meets the design requirements.
Design composition of roller-compacted concrete mix according to absolute volume method, taking into account that the air content in the roller-compacted concrete mix is 1% – 10% excluding voids of the concrete mass caused by construction.
The total amount of binder (cement + fine particles) in roller compacted concrete should not be less than 130 kg/m3.
Large aggregate is Dmax= 50mm.
The suitable finely ground mineral admixture content in roller compacted concrete ranges from 30 – 70% of binder weight.
Water/binder ratio < 0.7
Working degree VOc at the mouth of the appropriate mixer is Vc=10 30 seconds;
Use the least amount of cement to reduce the heat effect of the hydration process.
Create RCC mix capable of minimizing stratification in RCC construction stages.
– RCC gradation recommended: Cement PC40 : 80 kg.
Adhesive materials : 155 kg.
Water : 133 kg.
Sand :743 kg.
Macadam:
Grain size 25 – 50mm : 175.7 kg.
Grain size 12.5 – 25mm : 451.8 kg.
Grain size 5 – 12.5mm : 627.6 kg. Total: 1379 kg.
Mortar and paste ratio : 42 %.
Amount of aeration : 1.03%.
RCC gradation will be accurate on the basis of field testing.
In the event of a change in the supply of the binder materials, a design program, and a mix test with the new source
of materials, must be conducted to determine the properties of the RCC prior to permiting its application.
-
-
Laboratory test to determine the compressive strength of samples R28, R90, R180.
One of the most common methods of testing concrete quality is to determine the strength of compressive samples according to the age of the sample [4].
How to do the experiment:
Casting samples: Because the slump of RCC is zero, it is not possible to fabricate compression, bending and splitting test samples as with conventional concrete, but proceed by applying the mixture to the cylindrical mold into 2 to 3 layers and consolidating each layer of concrete on the vibration table. Vibration for each layer is continued until the grout is evenly spread over the entire surface area and the application of a loading weight is necessary to achieve this consolidation.
Sample maintenance: Samples manufactured in the laboratory must be cured in accordance with ASTMC-192.
The author referred to the results of sample compression with the cylindrical sample size of 15x30cm of Dakdrinh hydropower project [12] and the statistics in Table 4.
Table 4. Compressive strength test results of the RCC specimen in the laboratory
(Mark of RCC design: 12MPa, R180, Dmax50; Hardness VUc 7-17 seconds; Mineral Additives: Dau Voi mountain)
No.
Dump block number
Date of sampling
Date of test
Sample age (days)
Sample compression test
Compression strength (MPa)
% achieved compared to design
180 days
1
L(46-2) – C4
10/07/2012
06/01/2013
180
13.12
109.33%
2
L(47-2)+L48-KV1-C4
11/07/2012
07/01/2013
180
13.02
108.50%
3
L49+50-KV1-C4
12/07/2012
08/01/2013
180
12.93
107.75%
4
L51+52+53-KV1-C4
13/07/2012
09/01/2013
180
12.93
107.75%
5
L54+55+56-KV1-C4
14/07/2012
10/01/2013
180
13.21
110.08%
6
L57+58-KV1-C4
15/07/2012
11/01/2013
180
12.83
106.92%
7
L59-KV1-C4
16/07/2012
12/01/2013
180
12.74
106.17%
8
L60-KV1-C4
17/07/2012
13/01/2013
180
12.93
107.75%
9
L61+62-KV1-C4
18/07/2012
14/01/2013
180
12.36
103.00%
10
L63-KV1-C4
19/07/2012
15/01/2013
180
12.74
106.17%
11
L(46-2+47-2)-KV2-C4
27/07/2012
23/01/2013
180
12.74
106.17%
12
L48+49+50+51-KV2-C4
28/07/2012
24/01/2013
180
13.12
109.33%
13
L52+53+54-KV2-C4
29/07/2012
25/01/2013
180
12.83
106.92%
14
L55-1+55-2-KV2-C4
30/07/2012
26/01/2013
180
13.12
109.33%
15
L56+57-KV2-C4
31/07/2012
27/01/2013
180
12.83
106.92%
16
L58+59+60-KV2-C4
01/08/2012
28/01/2013
180
13.49
112.42%
90 days
1
L46-2-C4
10/07/2012
08/10/2012
90
10.59
88.25%
2
L47-2+L48-KV1-C4
11/07/2012
09/10/2012
90
11.89
99.08%
3
L49+50-KV1-C4
12/07/2012
10/10/2012
90
10.79
89.92%
4
L51+52+53-KV1-C4
13/07/2012
11/10/2012
90
10.95
91.25%
5
L54+55+56-KV1-C4
14/07/2012
12/10/2012
90
11.42
95.17%
6
L57+58-KV1-C4
15/07/2012
13/10/2012
90
11.04
92.00%
7
L59-KV1-C4
16/07/2012
14/10/2012
90
10.68
89.00%
8
L60-KV1-C4
17/07/2012
15/10/2012
90
12.83
106.92%
9
L61+62-KV1-C4
18/07/2012
16/10/2012
90
10.59
88.25%
10
L63-KV1-C4
19/07/2012
17/10/2012
90
10.95
91.25%
11
L(46-2+47-2)-KV2-C4
27/07/2012
25/10/2012
90
10.95
91.25%
12
L48+49+50+51-KV2-C4
28/07/2012
26/10/2012
90
10.81
90.08%
13
L52+53+54-KV2-C4
29/07/2012
27/10/2012
90
10.85
90.42%
14
L(55-1+55-2)-KV2-C4
30/07/2012
28/10/2012
90
10.79
89.92%
15
L56+57-KV2-C4
31/07/2012
29/10/2012
90
10.53
87.75%
16
L58+59+60-KV2-C4
01/08/2012
30/10/2012
90
10.59
88.25%
28 days
1
L46-2-C4
10/07/2012
07/08/2012
28
6.61
55.08%
2
L47-2+L48-KV1-C4
11/07/2012
08/08/2012
28
8.4
70.00%
3
L49+50-KV1-C4
12/07/2012
09/08/2012
28
7.93
66.08%
4
L51+52+53-KV1-C4
13/07/2012
10/08/2012
28
8.3
69.17%
5
L54+55+56-KV1-C4
14/07/2012
11/08/2012
28
8.87
73.92%
6
L57+58-KV1-C4
15/07/2012
12/08/2012
28
8.4
70.00%
7
L59-KV1-C4
16/07/2012
13/08/2012
28
8.3
69.17%
8
L60-KV1-C4
17/07/2012
14/08/2012
28
6.61
55.08%
9
L61+62-KV1-C4
18/07/2012
15/08/2012
28
5.28
44.00%
10
L63-KV1-C4
19/07/2012
16/08/2012
28
6.98
58.17%
11
L(46-2+47-2)-KV2-C4
27/07/2012
24/08/2012
28
6.83
56.92%
12
L48+49+50+51-KV2-C4
28/07/2012
25/08/2012
28
7.17
59.75%
13
L52+53+54-KV2-C4
29/07/2012
26/08/2012
28
7.55
62.92%
14
L(55-1+55-2)-KV2-C4
30/07/2012
27/08/2012
28
7.55
62.92%
15
L56+57-KV2-C4
31/07/2012
28/08/2012
28
8.3
69.17%
16
L58+59+60-KV2-C4
01/08/2012
29/08/2012
28
8.4
70.00%
According to table 4 statistics, the average: 28 days: reach 63.3% of design strength 90 days: reach 91.8% of design strength 180 days: reach 107.8% of design strength
We can see, with hydropower projects that have to be built for a very long time, designers have taken advantage of the strength development properties over time of concrete to reduce cement, save materials, reduce the heat of hydration of cement.
However, with road and bridge works to be renovated and upgraded, the requirement to clear traffic and put the works into use immediately after spreading is an essential requirement. So RCC will have to be designed and calculated to work in two phases:
Period before 180 days: RCC has not reached the design strength, RCC pavement should be considered as semi-rigid pavement for appropriate design, construction, maintenance and use calculations.
Period from 180 days onwards: RCC reaches design strength, used as conventional concrete pavement.
-
Field tests determine the thickness of the pour layer, the type of compactor and the number of times of compaction
Similar to soil materials, RCC is also tested to determine the thickness of the pour layer corresponding to each compactor and the number of compactions to achieve the required compaction.
Experimental embankment is usually arranged at a location near the site at least 1 month before the construction of the road surface. The test embankment must be large enough to accommodate a team consisting of: vibrating rollers, wheel rollers, and wheel rollers to determine the correlation between the specific gravity in the laboratory and the density determined by field tests and to correct the relationship between the number of times of rolling and the density. The recommended minimum size of the embankment is 3 spreading streaks, each of which is 3.5-4m wide and 450m long. Of which, 1 and a half streaks are spread on the first day and the remaining 1 and a half streaks are spread on the next
day. The test track shall have two longitudinal and transverse joint joints and two wet longitudinal joints.
Dress thickness: The maximum thickness of an RCC layer depends on the capacity of the spreader. The maximum unfilled thickness is usually 25-30cm. The unrolled thickness can be approximated by multiplying the design thickness by
1.25 to account for the reduction in thickness due to compaction. The minimum thickness of a layer is 10cm.
If the total unrolled thickness exceeds the capacity of the spreader, it shall be laid in two or more layers, thus creating a transverse joint (a horizontal junction between the layers) in the RCC pavement. If the junction is sufficiently adherent (upper and lower layers are spaced within 1 hour) then a full- body single-layer thickness design may be used. If the spreading time is more than 1 hour, it must be designed as a hard coat over the hard road foundation. The surface of the lower layer must be kept moist and clean until the top layer is applied and the top layer must be spread and compacted within 1 hour of the completion of the bottom layer to ensure adhesion of the two layers.
Compaction times: In the field test, after each compaction, a nuclear density meter is used to determine the optimal number of compaction times of each type of compactor to set the required compaction. Made with a special device to make a compaction hole in the pavement. After each pass of the vibrating roller, push the nuclear probe into the hole to determine the tightness. This process of rolling and compaction is carried out continuously until successive readings change by less than 1%. These data are used to calibrate the nuclear instrument to a specified density in the laboratory in order to determine the number of compactions required. However, the minimum number of times of vibrating is not less than 4 times.
Figure 17. Diagram of test road segment
Figure 18. Nuclear experimental apparatus for measuring density
-
Experiment to evaluate RCC quality by core drilling
Practical experience when assessing the quality of roller compacted concrete shows that: The results of determining the quality of concrete according to the sample test method are only preliminary, the final conclusion about the quality of roller compacted concrete must be based on the quality of core drilling at the construction site.
To properly assess the quality of concrete, each time it is poured from 1,000m3 – 2,000m3 concrete, it is necessary to drill no less than 3 samples. The location of the boreholes is selected based on the following points:
Drilling locations for sampling are typical of the project, Locations with doubts about the quality of concrete:
Unsatisfactory mix aggregate, poor compaction quality,
poured concrete being eroded by rain, improper handling of layers according to technical procedures.
-
Core drilling
Core drilling is carried out according to the normative process using drilling equipment with diamond drill bits.
The core drill diameter should be 3 times the maximum grain size diameter in roller compacted concrete. Increasing the core diameter makes it possible to obtain more reliable results in terms of concrete quality.
Figure 19. Drilling for compressive strength test specimen
Figure 20. RCC drill core
Immediately after removing the core from the borehole, a complete description of the core must be recorded, it is necessary to mark the boundary of the roller compacted concrete layer and determine the sample rate. The boundary of the roller compacted concrete layer shall be marked with an unfading paint.
Drill cores should be stored in separate wooden crates and bore hole data, location and core drilling level recorded.
When the core is withdrawn from the borehole, the hole shall be immediately covered with a plug or plastic.
No more than 1-2 days, after core drilling is completed, it must be taken to a construction laboratory to preserve them in conventional conditions.
-
Core test
When testing the core, it is necessary to determine:
Density of concrete in dry state (after being stored for 5-7 days outdoors in the laboratory).
Concrete density in saturated state Water absorption of concrete.
Compressive strength of concrete. Tensile strength of concrete.
If core diameter is 150mm, then the height will be 200- 250mm which means one core per layer of roller compacted concrete.
Store cores in dry conditions for not less than 5-7 days (in the laboratory or outdoors, under a cover).
Core weighing was carried out with an accuracy of 1 gram, using a ruler to measure the diameter and height with an error of not more than 1%.
Before proceeding to the next operations, it is necessary to check whether the core is defective or not (cracks, honeycomb
voids, layering, insufficient compaction of concrete mix…). The test results will be recorded in the sample test book.
The samples were then immersed in water for not less than 2 days at a temperature of (20 ± 5)0C. After two days, the sample was removed from the water, wiped clean with a rag, and weighed again.
From the above parameters we can determine the density and water absorption of concrete.
It is necessary to process the sample before the compression test by: Cutting the cylindrical sample into lengths from 0.85 to 2 times the core diameter, cover the surface of the sample with a layer of molten sulfur and allow it to harden to make the surface of the specimen to be tested in contact with the surface of the compression table, see figure 21.
When the compressive resistance test is continuously loaded at the press at a rate of 6±4kg/cm2 for 1 second until the core breaks. Thus, the loading time is not less than 30 seconds. Do not adjust the speed while the specimen is rapidly morphing just before breaking.
The characteristics of the drill core are broken.
Porosity, honeycomb porosity (with a volume of more than 1cm3).
The size of aggregate particles is greater than 1.5 Dmax, clay lumps, and concrete are stratified.
This test result serves as a basis to exclude unsatisfactory test results.
The compressive strength R of concrete is calculated according to the following formula:
R= (P/F)* K1. (1)
In which:
P: Breaking load, kg.
F: Cross-section (bearing) of the core, cm2.
K1: The factor, calculated as the ratio of the core height h and the diameter D, is applied according to table 5.
Table 5. Factor K1
h/D
K1
h/D
K1
0,85-0,94
0.96
1,45-1,54
1.13
0,95-1,04
1.00
1,55-1,64
1.14
1,05-1,14
1.04
1,65-1,74
1.16
1,15-1,24
1.08
1,75-1,84
1.18
1,25-1,34
1.10
1,85-1,94
1.19
1,35-1,44
1.12
1,95-2,00
1.20
-
Test result report
The report on the results of the compression test of the roller compacted concrete drill sample should have the following contents:
Sample symbols;
Sample shape and size (diameter, height of cylinder); Cross section;
Sample age at compression; Maximum pressing force; Compressive strength of each sample; Broken form by sample
Sample defects (if any).
-
-
-
The difference between the application of roller compacted concrete for hydropower dams, and the application of roller compacted concrete for road and bridge construction
-
Thermal stress in bulk concrete and road concrete.
After RCC has been poured into the pouring block, the temperature in the pouring block will constantly increase due to hydration of the cement. After that, due to exothermic heat, the temperature in the pouring block will gradually decrease to a stable temperature. RCC uses less cement than conventional concrete, so the heat of hydration in the RCC block is smaller. RCC is usually built on a large area, so it has the ability to absorb more solar radiation, contributing to the warming of the building.
The heat of hydration of cement in concrete, if not promptly dispersed and accumulated, will cause the interior of the concrete block to generate a relatively high temperature rise. Changes in the temperature of the concrete block cause it to change shape and produce stress. Concrete that hardens during the process of increasing heat forms a compressive pressure, but during the cooling process, shrinkage occurs. When shrinkage is constrained, internal concrete generates tensile stress. When the tensile stress exceeds the tensile strength, the concrete cracks. The type of stress caused by temperature is called thermal stress.
Thermal cracking lowers the structural integrity of the concrete, its waterproofing and durability, and reduces the overall safety of the structure. The cause of cracking is due to internal and external binding stress generated during the process of concrete hydration during setting and cooling of shrinkage.
External binding much of it is the difference in temperature between newly poured concrete and the foundation or previously poured concrete. Due to external constraints, cracks can develop throughout the entire concrete structure, causing great damage, so it is necessary to find a way to avoid it completely.
Table 6. Comparison table of factors causing thermal stress for large block RCC and RCC for road
Factors causing thermal stress
For RCC large block
For RCC background and pavement
Cement hydration in RCC
The same amount of cement, the same heat of hydration.
The same amount of cement, the same heat of hydration.
The temperature difference between the center of the pour mass and the surface of the pour, the temperature distribution and variation (internal constraint)
It is difficult to escape heat because the dimensions of the pouring blocks are large, a cooling water system is required inside the pouring block to eliminate the step temperature.
Since the RCC for the foundation and pavement is thinner in thickness than in the other two directions, the fill can quickly dissipate heat in one direction (thickness).
The temperature difference between the new pour and the previous foundation or block. (external binding)
It is necessary to reduce the highest temperature when the RCC hydration is close to the stable temperature of the pour. Therefore, RCC for large dams is forced to cool the incoming aggregates.
For the pavement and pavement, the RCC will mostly be placed in contact with the subgrade. Therefore, it is necessary to cool the inlet aggregate to eliminate this type of thermal stress.
Absorb solar radiation
The large block RCC develops the pile height on a fixed area, so it can be shielded to reduce solar radiation or use steam to spray moisture on the surface of the pouring block.
RCC for the foundation and pavement develop along the road length, subject to more solar radiation because the dump area is very large. A suitable method to reduce solar radiation is to use steam to moisten the surface of the pouring block.
The internal constraint is caused by the uneven distribution and change of the temperature of the concrete block itself. The causes of internal constraints are many, but due to internal constraints leading to cracks, most of them are surface cracks, and the damage is relatively small.
Depending on the type of crack, there are suitable heat control principles:
To prevent the type of cracks caused by binding near the foundation or old concrete, the main rule is to lower the maximum temperature of the concrete so that the temperature difference between the stable temperature and the maximum temperature can be minimized.
To prevent this type of surface cracking due to internal constraints, the main problem is to eliminate the step temperature completely, reduce the temperature difference between the inside and the outside, but not to lower the absolute temperature. of concrete.
-
Waterproofing dam body, anti-wear of road surface
-
Waterproofing of the dam body
Hydropower dams have high requirements for waterproofing, so designers increase the amount of cement in RCC at locations such as: Upstream surface, downstream surface, surface of vertical wall structure of corridors in the dam body, face adjacent to the spillway boundary walls. Cement-rich RCC concrete is a method of modifying the workability of RCC to the point where it can be compacted like conventional concrete.
Cement-enriched concrete layers with a width of 0.6m are applied in layers with a thickness of 0.3m concurrently with RCC layers.
The construction process of cement-enriched RCC concrete layer is as follows:
Immediately before spreading the layer of RCC mixture on the side facing the formwork, the cement mortar must be spread, the volume of cement mortar used is about 8 liters/md along the face of the formwork.
After placing the RCC mixture on the cement mortar, the RCC enriched cement concrete layer will be compacted with a stick compactor until the concrete is tight and no air bubbles emerge. At this point, the cement grout should be visible on
the concrete surface. Then use a vibrating compactor (table dress) to flatten the face.
Minimize walking on the area covered with cement mortar before pouring the RCC mixture.
-
Anti-abrasion of road surface:
RCC when reaching the design strength has all the properties of conventional concrete, therefore, the road surface roughening spikes are very hard and durable over time, the coefficient of friction of the concrete road and the wheel is quite large, the properties of the road surface are quite large. This method of conventional concrete has been proven and applied to road works going through steep passes such as Ho Chi Minh road in the central part of our country.
RCC pavement materials have high wear resistance, which plays a very important role in enhancing the friction between the wheel and the road surface.
However, it is necessary to design RCC pavement with a large horizontal slope, ensuring complete surface drainage to maintain surface roughness. Because the road surface is good, but dirty, wet, it is very slippery. When the road surface is dusty and does not drain well, a thin layer of mud will form to prevent contact between the wheels and the road surface.
-
-
Surface finishing of roller compacted concrete for dam and pavement
-
For dams
We need to complete the surface upstream and downstream of the dam to ensure the correct shape and size of the dam. Surface formwork upstream and downstream of the dam is usually designed to be anchored to the RCC block under construction to rise without needing support trees underneath. The formwork circulation, the time to remove the bottom formwork layer to move to the upper layer must be enough for the RCC to solidify and not peel off during dismantling.
Roller compacted concrete is cement-enriched at the surfaces and locations adjacent to other structural members, the thickness of the cement-rich RCC layer is usually 0.6m, can be applied by ramming like conventional concrete, they are structured as an outer shell of the dam, with high aesthetics, good waterproofing ability.
-
For road surface
The road surface cannot use formwork because the surface area is wide, nor can the cement-enriched RCC be used as a coating because the RCC for the road is usually not too thick.
The solution for road surface finishing is the use of wheel and wheel stationary compactors with the proper compaction sequence:
Immediately after vibrating is completed, 2 or more rounds of static compaction of the tire shall be carried out to seal the voids and cracks in the surface, forming a closed surface structure.
Next, a 10T light weight two-wheeled static compactor can be used to flatten the compaction streaks on the surface, the iron wheel static compaction must be performed until a flat surface according to the design is obtained, with few compacted streaks on the edge of the compactor drum.
-
-
Strength development over time of roller compacted concrete.
-
According to table 4 statistics, the average: 28 days: 63.3% of design strength
90 days: 91.8% of design strength
180 days: 107.8% of design strength
Based on the above statistical results, we can calculate and compare the strength development over time between roller compacted concrete and conventional concrete as shown in Table 7.
It can be concluded that: Roller compacted concrete has a greater ability to develop post-strength than conventional concrete.
For hydropower projects, the nature of strength development over time has been taken into account by the designers and saves a large amount of cement.
Concrete type
R28
R90
R180
Roller Compacted Concrete
100%
145%
170%
Conventional concrete
100%
115%
120%
Table 7. Strength development situation of roller compacted concrete
However, with road and bridge works to be renovated and upgraded, the requirement to clear traffic and put the works into use immediately after spreading is an essential requirement. The long-term strength development of RCC is an advantage for hydropower, but it is a factor that needs attention and proper treatment when applied to road and bridge construction.
The proposed solution is: RCC will need to be designed and calculated to work in two phases:
Period before 180 days: RCC has not reached the design strength, RCC pavement should be considered as semi-rigid pavement for appropriate design, construction, maintenance and use calculations.
Period from 180 days onwards: RCC reaches design strength, used as conventional concrete pavement.
-
-
CONCLUSIONS AND RECOMMENDATIONS
-
Conclusions
The article has reviewed, compared, analyzed, synthesized, evaluated and achieved the following basic objectives:
-
RCC is confirmed as a material of good quality, fast construction, and low cost. Especially with the goal of sustainable development and ecological environment protection, RCC will be a highly appreciated material in the future, namely:
-
RCC uses locally available materials such as: sand; cement consumption of domestic cement factories – stimulating domestic production, and especially RCC using waste products of thermal power plants: fly ash, blast furnace slag. RCC has many advantages for sustainable development and environmental pollution reduction.
-
Compare the cost per m3 products, RCC has the highest economic efficiency when compared with asphalt concrete and conventional concrete.
-
RCC construction equipment line in current conditions can be completely mechanized synchronously, easily speeding up construction progress, and soon putting traffic works into use.
-
RCC quality when reaching design strength is equivalent to conventional concrete.
-
-
Determining the scope of application of RCC technology:
-
RCC technology is best used for bridge decks, road surfaces of grade II or lower, or pavements of grade I but with vehicle speed not exceeding 60km/h;
-
In the case of using RCC technology as the roadbed, it can be applied without restriction to all road grades.
-
-
Provide the necessary conditions for RCC construction technology to promote its advantages in road and bridge construction.
-
-
Recommendations
-
RCC needs to be divided into two phases to calculate the design and construction to suit the actual working conditions of the material:
Phase 1: from the time on which the RCC is finished spreading until the RCC reaches the design strength (about 180 days). RCC acts as a semi-rigid pavement, allowing partial traffic.
Phase 2: When RCC reaches design strength, RCC works as hard pavement.
-
It is recommended that the competent authorities soon approve a temporary quality management process for RCC construction applied to road and bridge works, and at the same time have more in-depth research topics on this issue.
-
It is recommended to allow RCC trial application and temporary quality management process application to some actual traffic works to more fully evaluate RCC's working with
-
each specific condition: Ground geology, topography of the route passing through, weather, materials, etc., progressing to perfecting the process of design, construction, and RCC quality management for road and bridge works.
REFERENCES
[1] Nguyen Quang Chieu, Pham Huy Khang (2007), Construction of road surface for cars, Transport Publishing House, Hanoi. [2] Nguyen Quang Chieu (2008), New pavement textures, Construction Publishing House, Hanoi. [3] Do Ba Chuong (2013), Design motorways volume 1, Vietnam Education Publishing House, Hanoi, 2013. [4] Nguyen Hai (2005), Stress analysis by experiment, Science and Technology Publishing House, HCMC. [5] Bui Manh Ha (2014), Research and application of roller compacted concrete construction technology for road and bridge construction. Master thesis. Ho Chi Minh City University of Transport. [6] Pham Duy Huu (2011), Concrete technology and special concrete, Construction Publishing House, Hanoi. [7] Vu Duy Khang (2007), Norms of construction cost estimates Construction part, Transport Publishing House, HCMC. [8] Pham Huy Khang (2010), Construction technology of cement concrete pavement, Construction Publishing House, Hanoi. [9] Tran Dinh Ngo (2013), Methods of supervision and acceptance of construction works, Financial Publishing House, HCMC. [10] Nguyen Thanh Sang (2013), Experimental study on roller compacted concrete for road pavement structure", Transport Magazine, No. 7/2013, pp. 11-13. [11] Nguyen Viet Trung, Nguyen Ngoc Long, Nguyen Duc Thi Thu Dinh (2010), Additives and chemicals used in concrete, Construction Publishing House, Hanoi. [12] Technical documents for RCC construction, RCC test results in the laboratory and in the field, images of RCC construction of Dakdrinh Hydropower Project – Son Ha District – Quang Ngai, 2013.