
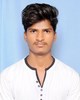
- Open Access
- Authors : Nagaraj , Sandeep G , Tejaswini K , Shwetha H K, Shri Harsha J
- Paper ID : IJERTV12IS040051
- Volume & Issue : Volume 12, Issue 04 (April 2023)
- Published (First Online): 24-04-2023
- ISSN (Online) : 2278-0181
- Publisher Name : IJERT
- License:
This work is licensed under a Creative Commons Attribution 4.0 International License
Design and Simulation of High Voltage Gain Buck-Boost Converter for Electric Vehicle using MATLAB
1Nagaraj,2Sandeep G 3,Tejaswini K 4,Shwetha H K ,5Shri Harsha J
1Student, VVIET, Mysore, Karnataka, India. 2Student, VVIET Mysore, Karnataka, India. 3Student, VVIET, Mysore, Karnataka, India. 4Student, VVIET, Mysore, Karnataka, India.
5Assistant Professor, VVIET, Mysuru, Karnataka, India.
Abstract: This research describes a revolutionary voltage-lift switched inductor (VLSI) cell-based high step-up DC-DC multilevel buck-boost converter. Cascade of traditional DC- DC converters is not a workable solution to reach high conversion ratio. In this study, a VLSI cell is used to improve the multilevel buck-boost converter's boost capabilities. The suggested DC-DC multilevel topology's key benefit is that it achieves large conversion ratios without the use of coupled inductors, transformers, or high duty cycles. The 200W-rated buck-boost multilevel converter that is being suggested has three stages and a 220V output voltage. The duty cycle is 70%, the switching frequency is 50 kHz, and the input supply voltage is 12 V.
Keywords: Voltage multiplier, voltage-lift switched inductor (VLSI) cell, multilevel buck-boost converter.
-
INTRODUCTION:
The use of a normal DC-DC converter in conjunction with a voltage multiplier cell[10], a voltage raise switching inductor cell, and a five level buck-boost converter allows for large voltage gain. The voltage multiplier cell, also known as a Cockcroft Walton multiplier, is used to generate high output voltage from low level AC or pulsating DC input voltage. Television, particle accelerators, and many other electronic devices still use voltage multiplier cells to obtain high output voltage. X-ray machines, televisions, and photocopiers are a few devices that use voltage multiplier cells[13]. Step up transformers are typically used to get high output voltage, however they are expensive, take up a lot of space, and produce current and voltage with a significant degree of ripple. The voltage multiplier cell resembles a ladder network and is made up of diodes and capacitors.
-
PROPOSED CONVERTER TOPOLOGY
Figure 1 shows the power circuit for a VLSI[14] cell and voltage multiplier-based five-level DC to DC buck boost converter. A single switch, 13 diodes, two inductors, and 10 capacitors are used in the converter design [2]. The five level buck boost converter's key benefit is that high voltage gain is achieved without the use of a transformer, coupled inductor, or an excessive duty cycle.
Fig. 1 Five level buck boost Converter.
When switch S is in the ON position, the supply voltage Vin will charge both inductors L1 and L2 in parallel through the corresponding diodes D10 and D12[5][8]. Through diodes D11 and D12, supply voltage Vin also charges capacitor C10 during this time. When diode D2 is forward biassed, the voltage across capacitor C1 charges capacitor C2 across the diode. Finally, voltage across capacitors C1 and C3 charges capacitors C4 through the diode D4. Additionally, voltage across capacitors C1,C3 and C5 charges capacitors C6 through the diode D6, and voltage across[15] capacitors C1,C3,C5,and C7 charges capacitor C8 through the diode D8, resulting in voltage V0 across capacitors C1,C3,C5,C7and C9. Figure 2 describes how the switch S operates in mode 1, or when it is turned on.
Fig. 2 Mode-1 operation when switch s is ON
There will be no connection between the input power supply and the load while switch S is in the OFF position[3][4]. The inductors L1, L2, and capacitor C10 will be connected in series under this circumstance. This series configuration of capacitor C10, inductors D1, and D13 charges the capacitor C1. A series of inductors L1, L2, capacitors C2, C10, and diodes D3 and D13 charges capacitors C1 and C3 when D3 is forward biassed. The series configuration of inductors L1, L2 and capacitors C10, C2, C4, C6 charges the capacitors C1, C3, C5 and C7 through diodes D7 and D13. The series configuration of inductors L1, L2 and capacitors C10, C2, C4, C6 charges the capacitors C1, C3, C5 and C7 through diodes D5 and D13. Finally, the capacitors C1, C3, C5, C7, and C9 are charged through diodes D9 and D13 by the series
VL2 = Vin (2)
VL1 = VL2 = VL = Vin (3)
Vc10 = Vin (4)
Vc2 = Vin+ Vc1 (5)
Vc2 + Vc4 =Vin + Vc1 +Vc3 (6) Vc2 + Vc4+Vc6+Vc8=Vin + Vc1+Vc3+Vc5+Vc7 (7) V0 = Vc1 + Vc3+ Vc5+Vc7+Vc (8)
When switch S is in OFF condition
VL1 + Vc10 VL2-Vc1= 0 (9)
Vc3 = Vc2 (10)
Vc3 + Vc5 =Vc2 + Vc4 (11)
VL1 + Vc10 -VL2 Vc1 Vc3 Vc5+VC4 + Vc2
(12)
Vc3 + Vc5 + VC7 = Vc2 + Vc4 + Vc6 (13)
VL1 + Vc10 – VL2 Vc1 Vc3 Vc5VC7 + Vc6 +
Vc4 + Vc2 (14)
VC3 + VC5 -VC7 VC9 = VC2 + VC4+VC6 + VC8
(15)
VL1 + Vc10 – VL2 Vc1
Vc3 Vc5VC7 V9VC8 + Vc6 + Vc4 + Vc2
(16)
Substitute equation (3) in (9)
10 1
combination of inductors L1, L2, and capacitors C10, C2,
C4, C6, and C8. When switch S is OFF, or in mode 2[6], as
VL = 2
(17)
shown in Figure 3, the system[11][12] operates.
By inductor volt second balance
vinD +
10 1 (1-D)=0 (18)
2
vC1=
2 Vin D +V (19)
C10
1D
VC1 = 2 = 10
(20)
Vin
(1)
Substitute equation (4) in (20)
VC1 = 2
+1=1+
(21)
Vin
(1)
1
Fig. 3 When switch S is OFF (mode2)
Substitute equation (5) in (21)
VC2 = 2
(22)
Vin
(1)
When switch S[1] is in ON condition
VL1 = Vin (1)
Substitute equation (10) in (22)
V3 = 2
(23)
DC motor specification details given in table 2 is used as a
(1)
load for five level buck boost converter
Similarly from (6) and (11)
4 =5= 2
(24)
Table 2 DC motor specification
(1)
Power rating
150W
Armature voltage
400V
Field voltage
400V
No load current
0.198A
Full load current
0.5A
No load speed
1375rpm
Full load speed
1284rpm
Full load torque
0.8N-M
2 Vin
2 = 3 =4 = 5 = 7 = 9 = 1D (25)
Vo u t = VC1 + V3 + V5 +V7 +V9
(26)
Vin
Vin
Thus voltage gain ratio for five level buck boost converter
is
= 9+ (27)
5
(1)
-
DESIGN DETAILS:
The five level buck boost converter has been designed for 200W load and 400V output voltage. The duty cycle needed to get 400V output voltage from 12V input will be 70.8% with a switching frequency of 5KHZ [7].
-
SIMULATION RESULTS:
Open loop SIMULINK model of five level buck boost converter with resistive load
DC to DC five level buck boost converter with 800 resistive load is designed to get output voltage of 400V from input voltage of 12V. The SIMULINK model is shown in Figure 4. It consists of one ideal switch (with internal diode resistance Ron= 0.001 & Snubber resistance Rs=1e5), two 25mH inductor with 0.05 series resistor, ten number of 330µF capacitors and thirteen
2 2 number of diodes (with internal diode resistance
R=0 ) = 400 = 800
Ron=0.001 & Snubber resistance Rs=1e5). Duty cycle
200
the critical inductance LC value is calculated from below expression
of 70.8% is required to get 400V output voltage from 12V
input voltage.
1 = 2 =
(1) 2
Where, f = Swiching frequency in Hertz
R = Resistive load in ohm
The critical inductance value will depends on duty ratio, switching frequency and resistive load.
LC1=LC2=
(10.708)(800) 25000
=25mH
The critical capacitance value can be obtained from the below expression[4]
C N2
Critical 2Fs2L
C = = 310*10
F
52 6
Critical (52)(25)
Fig. 4 SIMULINK model of open loop five level buck boost converter with resistive load
The five level buck boost converter is fed with input voltage of 12V with 800 resistive load. The response of converter in the given case is shown in the Figure 5 and 6
The five level buck boost converter specification details for 200W load is given in table 1
Power
200W
Input Voltage
12 volts
Input Current
16 ampere
Duty cycle
70.8
Output Voltage
400 volts
Output Current
0.5 ampere
Inductors
25mH
Capacitors
330µF
Table 1 Five level buck boost converter specification
Fig. 5 Output voltage
Figure.5 shows voltage waveform drawn regarding with time. From the result, it is observed that the overshoot (%)
value of output voltage will be 32.87% and settle to 400V at a settling time of 0.7S.
Fig. 6 Output current
Figure.6 shows current waveform drawn regarding with time. From the result, it is observed that the overshoot (%) value of output current will be 32.94% and settle to 0.5A at a settling time of 0.7S.
SIMULINK model of closed loop five level buck boost converter with resistive load
Five level buck boost converter with resistive load designed to get output voltage of 400V. The SIMULINK model is shown in Figure 7. It consists of one ideal switch (with internal diode resistance Ron= 0.001, Snubber resistance Rs=1e5), two 25mH inductor with 0.05 series resistor, ten number of 330µF capacitors and thirteen number of diodes (with internal diode resistance Ron=0.001 & Snubber resistance Rs=1e5). Here PI controller is used to set constant output voltage under variable loads.
Fig. 7 Closed loop SIMULINK model of DC to DC five level buck boost converter with resistive load
Here PI controller is used to get constant speed under variable loads. Here the output speed is sensed and compared with the reference speed which gives error signal. Then the error signal is than given to PI controller by setting Kp=5 and Ki=5 value. The output of PI controller is multiplied with pulse generator which is of 70.8% duty cycle and switching frequency of 5KHZ which gives the gate pulse for ideal switch.
The DC-DC five level buck-boost converter is fed with input voltage of 12V with 800 resistive load. Here PI
controller is used to maintain constant output voltage of 400V under variable loads. The response of converter in the given case is shown in the Figure 8 and 9.
Fig. 8 Output voltage
Fig. 9 Output current
Table 3 Five level buck-boost converter with resistive load test conditions
Output voltage in V
Output current in A
Resistive load in
400
0.5
800
403.4
0.448
900
405.3
0.405
1000
406.7
0.37
1100
408
0.34
1200
418
0.052
8K
420
5.25
800K
Results for open loop DC to DC five level boost converter with DC motor as a load
The DC to DC five level buck boost converter is fed with input voltage of 12V with 150W DC motor at no load. The response of converter with DC motor in the given case is shown in the Fig 10(a, b, c, d, and e)
Fig 10 (a) Output voltage
Fig 10 (b) Output current
Fig 10 (c) Output speed
Fig 10 (d) Electrical torque
Fig 10 (e) armature current
Table 10.1 Five level buck boost converter with DC motor load test conditions
10.1.1 Results for closed loop DC to DC five level buck boost converter with DC motor as a load for constant output voltage
The DC-DC five level buck-boost converter is fed with input voltage of 12V with 150W DC motor at no load. Here PI controller is used to maintain constant output voltage of 400V under variable loads. The response of converter in the given case is shown in the Fig 10.1.1 (a, b, c, d and e)
Fig 10.1.1 (b) Output current
Fig 10.1.1 (c) Output speed
Fig 10.1.1 (d) Electrical torque
Fig 10.1.1(e) armature current
6.4.5 Results for closed loop DC to DC five level buck boost converter with DC motor as a load for constant speed output
The DC-DC five level buck-boost converter is fed with input voltage of 12V with 150W DC motor at no load. Here PI controller is used to maintain constant speed
139 under variable loads. The response of converter in
the given case is shown in the Fig 11(a, b, c, d & e)
Fig 11(a) Output voltage
Fig 11 (b) Output current
Fig 11 (c) Output speed
Fig 11 (d) Electrical torque
Fig 11 (e) armature current
-
CONCLUSION
The voltage-lift switched-inductor cell is used to improve the five level buck boost converter's boost capacity. This converter topology is appropriate for applications requiring unidirectional power transfer and high gain supply voltage escalation. When compared to traditional buck boost converters, this converter offers high gain for a specific number of levels. The duty cycle and number of output levels affect the gain of the five-level buck-boost converter. To maintain a steady output with changing loads, PI controllers are employed. The software programme MATLAB / Simulink was used to simulate the DC-DC five buck-boost converter for resistive load with PI controller to maintain constant output voltage under fluctuating load.
-
REFERENCES
-