
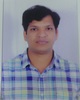
- Open Access
- Authors : Ashwinkumar Patil , Manjunath V S , Praveen Ahuja
- Paper ID : IJERTV10IS020264
- Volume & Issue : Volume 10, Issue 02 (February 2021)
- Published (First Online): 08-03-2021
- ISSN (Online) : 2278-0181
- Publisher Name : IJERT
- License:
This work is licensed under a Creative Commons Attribution 4.0 International License
Structural Integrity of ADAS Camera Module
Ashwinkumar Patil Lead Engineer, CAE CoE HCL Technologies
Praveen Ahuja
Global Program Manager, CAE CoE HCL Technologies
Manjunath V S
Technical Manager, CAE CoE HCL Technologies
Abstract Advanced Driver Assistance Systems are supporting the driver in their primary driving task. They inform and warn the driver, provide feedback on driver actions, increase comfort, and reduce the workload by actively stabilizing or maneuvering the car. ADAS assist the driver and do not take over the driving task completely, thus the responsibility always remains with the driver. Automotive cameras are the eyes of the vision-based advanced driver assistance systems in a vehicle. While front cameras in vehicles are used to detect lane markings, pedestrian and traffic signs, the side and rear cameras help in cross-traffic alerts, blind spot detection, and parking assistance. This paper describes static and dynamic simulation approaches to check structural integrity of camera when subjected to different types of loads. It also demonstrates test to FE result validation.
Keywords ADAS camera, static, dynamic, FEA
-
INTRODUCTION
The development of safety systems used in vehicles has been progressing throughout the automotive history. In recent years, significant progress has been made and a new era has emerged with the introduction of Advanced Driver Assistance Systems (ADAS). As an essential component of the ADAS system, cameras deliver data both to the driver and to the onboard computer. Cameras may be monocam, tricam, or full surround, and placed in areas such as dashboards and windshields. ADAS cameras used for object tracking, lane recognition, blind spot identification, autonomous driving applications, and much more, camera visibility is key to effective operation. The information captured by ADAS cameras is quickly analyzed by supporting software and used to trigger a response by the vehicle to improve safety. For smooth & flawless operation, it is important to ensure structural integrity of camera for various types of static and dynamic loads when mounted on vehicle.
Below pictures show different types of cameras used in automotive, camera attachment to windshield and different parts of camera.
Fig. 1a. Monocam Fig. 1b. Tricam Fig. 1c. Remote head
Fig. 1d. Camera attachment to windshield Fig. 1e. Camera parts
-
PROBLEM DEFINITION
ADAS functions are more complex because of more advanced algorithms and the use of new environment sensors. For purpose of driver safety and to avoid accident, camera should deliver clean and high-quality image. If any damage to camera, then it may fail to deliver expected output. Image processing algorithms provide direct control of the braking system and initiate the emergency braking function if pedestrians are detected or if there are vehicles in front which are too close. Image processing units mounted on the printed circuit board (PCB). Hence, PCB deflections/strains under various loading conditions are very critical which might cause failure of electronic joints. PCB with electronic components is enclosed within structural components like housing and cover and is assembled with screws. As vehicle travels on irregular road, camera mounted on vehicles will experience the dynamic loads. The effect of screw pre-load and dynamic loads on camera module needs to be simulated to check its structural integrity and predict fatigue failure if any. Some of the functions of camera are shown in below figures.
Fig. 2a. Adaptive cruise control Fig. 2b. Lane keeping assist
Fig. 2c. Blind spot detection Fig. 2d. Automatic emergency Breaking
-
SOLUTION AND IMPLEMENTATION
Static analysis
Design
no
Assembly analysis
PCB
Strain < allowable
yes
Snap analysis
Bracket stress < allowable
yes
Design release
Design
no
Fig. 3. Static analysis flowchart
Dynamic analysis
Design
Modal analysis
Design
Modal analysis
Random vibration analysis
Random vibration analysis
Frequencies
no are in
allowable limit
yes
Shock analysis
Shock analysis
no
Design release
Component stress < allowable
yes
-
Static analysis
Static analysis carried out on camera systems for screw pretention and snap fit load conditions. Pretension loads act at time of assembly of and its effect needs to be checked for PCB. Snap loads occur while mounting or dismantling on camera system from mount bracket.
-
Pretension analysis
Printed circuit board (PCB) is a critical component in ADAS camera. PCB consists of a metallic layer of traces bonded to a dielectric layer. PCBs are designed to mechanically support and electrically connect an electronic component assembly. The process of assembling the electronic components induces a certain state of strain and deformation in
Fig. 4. Dynamic analysis flowchart
Finite element (FE) method can be used to simulate various physical test conditions for ADAS/camera systems (including geometry, constraints and loading conditions) through numerical approach to assist development of safe & reliable systems. Further, it allows multiple what-if scenarios to be tested quickly and effectively and reduces the amount of prototype building and testing. It has therefore attracted much more attention in engineering design, manufacturing, and assembly. Structural simulations for camera through FE save considerable amount of time comparing with traditional physical test approach. Failure in camera system may occur for dynamic loads due to vibration fatigue or shock impulse. Simulation helps to remove a substantial hurdle in achieving a rigor in the testing to make the ADAS structures safe and reliable. Finite element simulations are extensively used predict results as shown below.
-
Strain distribution across the PCB: It is important to know the strain distribution across PCB surface to avoid positioning of sensitive components (such as microprocessors bounded to PCBs via BGAs or small electronic components) in critical areas.
-
Connection between mating parts (gap/interference) can be checked through FEA. With dynamic loads on camera, inside parts of camera may get separated and or collide on other parts.
-
To check effect of residual stresses, which occur because of interference of components.
-
To get snap-in / snap-out force for camera mounting on bracket as camera is manually assembled and disassembled from bracket. FEA carried out to check force required to assemble camera into bracket also to check snap strength of bracket. Based on stress analysis results, bracket optimization can also be done through FEA.
-
To check the load carrying capacity of glue for misuse and dynamic loadcases.
To ensure structural integrity of camera, static analyses such as assembly condition, pretension analysis and dynamic analysis such as modal, shock and random vibration analysis are performed. Figure 3 & 4 shows the analysis flow chart for static and dynamic analysis, respectively. FE simulations are carried out using Ansys workbench software. Geometry clean- up and modelling of missing parts are done through either Design Modeler or Ansys Spaceclaim.
the PCB. The main components affected are microprocessors due to the way they are glued to PCBs with BG – Ball grid arrays (BGA). There are two PCB in camera, one which attaches with lens mount and another main PCB where microprocessor and EyeQ are mounted.
PCB is clamped with lens mount with help of screws. Strain gauges are placed in x, y and 45o direction on imager PCB at BGA location to check strains generated after screw preload application.
Pretension analysis is carried out in below steps:
-
Bolt preloading at gauge location 1
-
Bolt preloading at gauge location 2
-
Test setup FEA Model PCB strain result Fig. 5. Test setup and FEA result
Finite element simulation approach is carried out in line with the test. Strain allowable for PCB is 700 microns. Pretension load applied in FE model in the same way as applied in test condition. First tighten the screw at location 1 and then tighten the screw at location 2 as shown in figure 5. Table 1 shows the test and FE strain correlation for pretension analysis. FE and test correlation helps to calibrate the FE simulation methodology.
TABLE 1: TEST AND FE RESULT SUMMARY
Test Result (micron)
FEA result (micron)
Guage 1
484
468
Guage 2
390
420
-
-
Snap simulation
Snap-in and snap-out are two simulations carried out to simulate assemble/insertion and disassemble of camera into bracket, respectively. Objective of snap analysis is to check bracket strength and snap-in/snap-out forces. Contact between bracket and camera assembly are frictional contacts for snap in and snap out conditions. When snaps open to maximum position, high stress regions develop at snap root region. Bracket strength analysis has been performed by comparing stresses generated at this time with the allowable strength limit.
Force plot for snap-in Force plot for snap-out Fig. 6. Snap-in & Snap-out force plots
Fig. 7. Cross section view at snap time Fig. 8. Bracket
Initially snap-in force starts increases upto snaps open to max position. At time when snap face and bracket faces becomes parallel to each other, snap-in force decreases till bracket stiffener comes in contact with camera. Figure 7 shows cross section view at time of snap. When bracket stiffener comes in contact with camera then snap-in force starts increasing. Sharp increase in reaction force is observed due to impact force generated at the time of complete snap-in.
Snap-out condition simulated for disassembly of camera from bracket. Snap out force increases till snap is in contact with camera and thereafter it decreases continuously because of snap loses contact with camera. Assemble and dis-assemble force can be quickly analyzed with the help of reaction force vs time plots as shown in figure 6.
-
-
Dynamic analysis
It is important to know the camera response to dynamic loads. Dynamic loads are applied as a function of time or frequency. This time or frequency-varying load application induces time or frequency-varying response (displacements, velocities, accelerations, forces, and stresses).
-
FEA simulation for shock loads
-
Transient dynamic analysis is used to determine the response to general time-dependent loads. Transient loads are short time loads, these loads die out after some time. Transient analysis also referred as shock analysis wherein shock pulse is characterized by peak amplitude and time taken. Shock loads are taken from International standard for the environmental testing of electrotechnical products by International Electrorechnical Commision, IEC 60068-2-27 [1]. Shock analysis is carried out to check glue and bracket strength.
In order to calculate half sine pulse loading, below empirical equation can be used:
Acceleration (g) = A*Sin (*n/R) Where,
g: Acceleration in g's n: Data points 1,2,3
A: Peak acceleration R: Number of Acceleration resolution data point
Test setup FEA model
Glue stress result
Fig. 9. Test setup, FE simulation model and Result
As lens is attached to lens mount with the help of glue, it should not get detach from lens mount due to shock pulses. Figure 9 shows test setup, FEA simulation model and result for shock load. Shock load input is 500m/s^2 for 6ms half sine curve. The shock test is defined as three half sine shocks being applied to the test sample in each applicable orthogonal direction, in both the positive and negative senses. Strength check carried out for glue after comparing stress with glue allowable stress. For given shock load stress on glue is lower than the glue allowable stress.
FEA model
Bracket stress result
Fig. 10. FE simulation model and Result
Camera is assembled into bracket and bracket is glued to windshield as shown in figure 1d. Camera and bracket must withstand series of shock pulses. These pulses result from unevenness of road, hump on the road. When transient loads act on bracket then there are chances that camera may get separate from bracket also camera parts contact will detach. FE analysis carried out to check bracket and camera strength for shock loads. Contact between bracket and camera are frictional contacts.
By looking at stress distribution on bracket in figure 10, it can be conclude that bracket is safe for given shock load
-
-
CONCLUSION
Development of more reliable ADAS camera systems requires extensive physical testing for various loading scenarios which it undergoes when mounted on vehicle. However, extensive physical testing leads to higher lead time for camera development and more time to market. Whereas virtual test simulations using FEA technique leads to lower proto-typing costs and overall, less lead time. Hence well- defined FE simulation methodology to study & validate the structural integrity of the ADAS camera systems along with few physical tests results in very less overall lead time to market & proto-typing costs. FE Simulations provides higher flexibility in terms studying the model behaviour and fix issues if any. FE simulation results are co-related with physical test results for assembly load condition.
REFERENCES
-
International standard for the environmental testing of electrotechnical products by International Electrorechnical Commision, IEC 60068-2-27.
-
Alexandru Falk, Liviu Marsavina, Octavian Pop, Analysis of Printed Circuit Boards strains using finite element analysis and digital image correlation
-
Praveen Ahuja, WhitePaper Novel design approach for electronic equipment, fea based methodology
-
Ansys 2020R1 user manual