
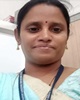
- Open Access
- Authors : B. Sarada , Mutha Harika , L. Durga Prasanna , G. Rama Devi, K. Gnanesh
- Paper ID : IJERTV12IS050049
- Volume & Issue : Volume 12, Issue 05 (May 2023)
- Published (First Online): 13-05-2023
- ISSN (Online) : 2278-0181
- Publisher Name : IJERT
- License:
This work is licensed under a Creative Commons Attribution 4.0 International License
Voice Controlled Robot using Bluetooth
Ms. B. Sarada , Mutha Harika , L. Durga Prasanna , G. Rama Devi, K. Gnanesh
Sanketika Vidya Parishad Engineering College
Abstract: A rescue robot is a robot that has been designed for the purpose of aiding most rescue teams. In most of common circumstances that skill rescue robots are mining fortunes, urban ruins, and imprisoned situations, blasts. This robot will help us in these situations by helping humans. The major objective of this project is to control the robot by using voice commands and to use it in disaster regions. It is aimed for the users to control a devices through voice commands. Here, the user can control all the movements of the robot through voice commands to remove the objects in disaster regions. It uses a microphone to convert the given voice. Commands to electrical signals, and this signal is recognized using voice recognition by means of a voice sensor. This sensor is known as the VR Module. It will produce an output which is used by a controller to produce a control output. This output will drive the motor, and robotic action will take place. It consists of L293D IC, which will as a
driving mechanism of the pick-and-place robot. Also, it has a servomotor that helps with the movement of the arms. The Two micro servos are used in gripping the objects at a distance. The VR module is used here to recognize the voice and give the output to the microcontroller. If the signal is the same as that of the trained signal on the keypad, the Servos will work according to it.
Keywords AT mega 328, L293D, Radio Frequency
-
INTRODUCTION
Robotics is advancing rapidly in all areas. Presently, various industries are moving from automation to robotization to increase productivity and also deliver uniform quality. Currently, everyone finds substitutes. For himself to carry out his orders and to work in a hostile environment. Robots and robot-like manipulators are now commonly used in hostile environments, such as at various places like atomic plants, chemical plants, bomb detection areas, etc. One type of commonly used manipulator in industries for various applications is the robotic arm, also known as a robotic manipulator. Now a days, robots are having wide applications in various fields. In many industries, robots are used to perform different functions. Robots are more accurate and efficient as compared to human beings. The use of robots in industries can increase the quality of products and their production rates. As compare to earlier days, today robots are used in various areas such Amede fence, ands defense medical fields, in industries, etc. Many areas of the world are affected by natural calamities. Disasters are exceptional, unstoppable events that are either man-made or natural. A voice- controlled robot is an interesting project, mainly used for industrial and surveillance applications. This is a system that will act automatically. When the voice command is reached. These voice commands should ensure the various operations that are to be performed. Our project is aimed at demonstrating the workings of a device using voice commands at calamity affecting regions.
-
LITERATURE REIVEW
-
This proposed system was finalized after checking out various references given and the implementations with methodologies was also discussed. Past ten years of reference papers was used for it. The detailed report on these references are given below,
Sotiris Stavridis, Pietro Falco, Zoe Doulgeri, Pick-and place in dynamic environments with a mobile dual-arm robot equipped with distributed distance sensors, Mobile bimanual manipulation in an exceedingly dynamic and unsure environment requires the continual and fast adjustment of the robot motion for the satisfaction of the constraints imposed by the task, the robot itself, and also the environment. We formulate the pick-and-place task as a sequence of mobile manipulation tasks with a mix of relative, global and native targets.[1]
Hae-Chang Kim, In-Hwan Yoon, Jae-Bok Song, Target Position Estimation for Pick-and-Place Tasks using a Mobile Manipulator, A mobile manipulator uses marker detection and hand-eye calibration to catch up on the performance limitation of position estimation during pickand-place tasks. However, whether these methods are applied or not, a mistake occurs proper to the limitation of camera calibration, so it's tough to locate the object within the correct position. [2]
Muhammad Affan, Syed Umaid Ahmed, Riaz
Uddin, Pick-and-Place Task using Wheeled Mobile Manipulator, A Control Design Perspective, This paper is aimed at students and roboticists to produce the concise theoretical and applied knowledge necessary for the control design of mobile manipulators. For this purpose, topics like kinematics, motion planning, and control theory are explored. Moreover, this information is integrated from the attitude of the Mecanum wheeled 5-R mobile manipulator for the pick-and-place task of the cube.[3] Fengyi Wang, J.Rogelio Guadarrama Olvera,
Optimal Order Pick-and-Place of Objects in Cluttered Scene by a Mobile Manipulator", In this paper, we present a quick method for autonomously plane manipulation tasks for mobile manipulators. An optimal order is defined by the planner to perform operations from a cluttered scene to specific deposit areas considering both, manipulator and mobile base motion. The grasping feasibility of the objects was examined by the first method with an inverse reachability map. [4]
K.N.V. Sriram, Suja Palaniswamy, Mobile Robot Assistance for Disabled and Senior Citizens Using
Hand Gestures, Numbness and movability impairments impact the autonomy of elder people while performing their independent tasks. Gesture role acts as a bridge between humans ad machines. This work focuses on Human-Robot Interaction (HRI), designed for the
assistance of wheelchairbound people with the assistance of mobile robots.[5]
-
METHODOLOGY
The design circuit consists of two main components; Hardware (That describes the system's physical Components
ARDUINO: The ATmega328/P provides the following features: 32Kbytes of in-system programmable flash memory with read-write capabilities, 1Kbytes of EEPROM, 2Kbytes of SRAM, 23 general-purpose I/O lines, and 32 generalpurpose working registers, a real-time counter (RTC), three flexible timer/counters with compare modes and PWM, and serial programmable USARTs, 1 byte
oriented 2-wire serial interface (I2C), a 6-channel 10bit ADC (8 channels in TQFP and QFN/MLF packages), a programmable watchdog timer with an internal oscillator, an SPI serial port, and six software-selectable power saving modes.
Voice Recognition Module: The module could recognise your voice. It receives configuration commands or responds through the serial port interface. With this module, we can control the car or other electrical devices by voice. This module can store 15pieces of voice instruction. Those 15 pieces are divided into 3 groups, with
5 in one group. First, we should Record the voice instructions group by group. After that, we should import one group by serial command before It could recognise the five voice instructions within that group. If we need to implement instructions in other groups, we should import the group first. This module is speaker-independent. If your friend speaks the voice instruction instead of you, it may not identify the instruction. Please note that speaker independence requires strictly good MIC. The MIC we supply is not good enough for it to be speaker-independnt.
RF Tx and Rx: This RF module comprises an RF transmitter and a RF receiver. The transmitter/receiver (Tx/Rx) pair operates at a frequency of 434 MHz. An RF transmitter receives serial data and transmits it wirelessly through RF through its antenna connected at pin 4. The transmission occurs at a rate of 1Kbps – 10Kbps.The transmitted Data is received by an RF receiver operating at the same frequency as that of the transmitter. The RF module is often used along with a pair of encoder/decoders. The encoder is used for encoding parallel data. data for transmission feed while reception is decoded by a decoder. HT12E-HT12D, HT640-HT648, etc. are some commonly used encoder/decoder pair ICs.
-
BLOCK DIAGRAM
The implementation of proposed system mainly involves RF Tx and Rx, Motor Driver, using ARDUINO AT Mega 328 microcontroller based. The block diagram of the system is shown in Figure
Figure 1: Transmitter Section
Figure 1: Transmitter Section
The system's power supply ranges from 3.3V to 5V.Voice Command is given to the voice recognition module v-3. It has There are three groups, each with five commands. The voice recognition is connected to the UART of the Arduino. At mega 328. At the transmitter side, HT12E is used to encode the voice command and transmit the data to the receiver. At receiver, it contains the RF receiver, which is the HT12D, to decode the data and send it to the Arduino to drive the motor using the motor driver IC LD29D.
-
CIRCUIT DIAGRAM
Figure 3: Circuit Diagram
[1] [2] -
FINAL RESULT
Figure 4: Final Result
CONCLUSION
We learned the basics of some new technologies, including Arduino programming and an easy VR sensor. The project also helped us learn how to manage a project. We have designed the voice command-based robot, which can act as a calamity-response robot. This robot can work with the given voice commands. But only standard commands can be used here to perform the robotic operation. Standard commands mean the trained commands. To perform the robotic operation, we will train the robot to perform different operations. Since the difficult portion of the construction was voice recognition of input commands, voice-controlled robotic. The arm for picking and placing an object was successfully designed. The robot control was found to be user friendly.
FUTURE SCOPE
Future work of this paper includes additional enhancement of the framework by employing different voice control like pick and place by using an arm and control by using a motor. Newly developed connectivity improvements can be used for quick information transfer in combination. Additionally, new IoT-enabled frameworks might be built for more application areas.
REFERENCES
[1] Chan Zhen Yue et al (2016). Design of Voice Controlled Vehicle, International Conference on Advances Automotive Technologies 2016, Yildiz Technical University, Instanbul, Turkey, AAT2016. [2] Lens. Thomas., Kunz. Jurgen, and Stryk. Oskar Von., BioRob- Arm: A Quickly Deployable and Intrinsically Safe, Light-Weight Robot Arm for Service Robotics Applications, 41st International Symposium on Robotics. Germany, pp. 905-910, June 2010. [3] Ghorabi. Hasan, Maddahi. Yaser., Monsef. Seyyed Mohammad Hosseini., and Maddahi, Ali., Design and Experimental Tests of Robot: Theoretical and Experimental Approaches, 9thWSEAS international Conferences on Application of Electrical Engineering. Penang, Malaysia, pp. 144-150, March 2010. [4] Kannan, K. & Selvakumar, J. (2015). Arduino Based Voice Controlled Robot, International Research Journal of Engineering and Technology (IRJET), Vol. 02, p-ISSN: 23950072, e-ISSN: 23950056. [5] Muhammed, J. N., Neetha, J, Muhammed, F., Midhun, M., Mithun, S. & Safwan, C. N. (2015). Wireless Control Robotic Arm Using an Android Application, International Journal of Advanced Research in Electrical, Electronics and Instrumentation Engineering, Vol. 4. (An ISO 3297: 2007 Certified Organization)].