
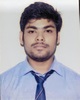
- Open Access
- Authors : Mafiz Uddin Ahmed
- Paper ID : IJERTV12IS040058
- Volume & Issue : Volume 12, Issue 04 (April 2023)
- Published (First Online): 24-04-2023
- ISSN (Online) : 2278-0181
- Publisher Name : IJERT
- License:
This work is licensed under a Creative Commons Attribution 4.0 International License
Valve Actuation using Piezo Technology
Mafiz Uddin Ahmed
Cyient Ltd. (Hyderabad)
Abstract This paper deals with the application of piezoelectric valves in pneumatic applications. It describes the design of a system consisting of a pipe to which a pressure sensor is fitted and the flow through pipe is controlled with the help of a piezo actuated valve. The pipe is a hollow pipe of square cross- section. The actuator is a micro cantilever beam which covers the exit hole at the surface of the pipe and opens the hole when the pressure at the inlet of the pipe exceeds a limit. The micro cantilever beam is a three- layered, bimorph beam. The beam is connected onto a hollow, cubical casing which acts as a fixed support to the cantilever beam. The square cross-sectional pipe goes through the hollow cubical casing to which it is joined by interference fit. The fluid assumed is a viscous fluid, similar to the human blood but not blood. The main objective of this project is to relieve the pressure which is in excess at the pipe inlet. This is done by allowing some mass of fluid to exit through the hole at the surface of the pipe. The entire process of the beam deflection and the fluid flow through pipe, both are simulated in COMSOL Multiphysics 2.0. The properties taken in the simulation are density and dynamic viscosity similar to that of blood. No other property has been considered because research is still going on as to how a human blood flows through a pipe. Some initial boundary conditions were assigned before the simulation and the results obtained for a 2.26 liters per minute flow through the pipe was compared to a table showing different properties for different mass flows of fluid through a 1.25 m tube-catheter. The results obtained were found to be in the range of the tabulated results. The drop in pressure across the pipe after simulation is in the range of the pressure drop as shown in the table. Hence, our aim of reducing the excess pressure across the pipe is achieved.
Keywords Piezoelectric valves; micro cantilever beam; bimorph beam; direct piezoelectric effect; inverse piezoelectric effect
-
INTRODUCTION
Nowadays many areas are seeing the use of piezo technology in valve actuation such as non- destructive handling of fragile work pieces, industrial adhesive applications, in ophthalmology, in pneumatic applications, inflating air cushions etc. This technology is replacing the conventional technology of actuation mainly manual, hydraulic, pneumatic, electric and spring. Piezo driven actuators are preferred over these conventional technologies because they provide following advantages:
-
Unlimited resolution (there is no friction element in them)
-
they are able to generate high force per unit area
-
No wear and tear
-
Low energy consumption
-
No magnetic fields
-
Able to operate at cryogenic temperatures
-
Rapid response compared to other technologies
-
Move precisely and powerfully
The piezoelectricity effect was discovered in 1880 when Pierre and Jacques Curie discovered the effect in several substances such as the quartz crystal. Piezoelectric effect refers
to a change in electric polarization that is produced in certain materials when they are subjected to mechanical stresses. This stress-dependent change in polarization manifests as a measurable potential difference across the material. This is referred to as the direct piezoelectric effect, this phenomenon is observable in many naturally available crystalline materials, including quart, Rochelle salt and even human bone to name a few. Engineered materials such as lithium niobite and lead zirconate titanate (PZT) exhibit a more pronounced piezoelectric effect. This process is also reversible. The inverse piezoelectric effect refers to the deformation of the piezoelectric materials that results from the application of an electric field. The deformation could lead to either tensile or compressive strains and stresses in the material depending upon the direction of the electric field, the preferred direction of polarization in the material, and how the material is connected to other adjacent structures. [1]
-
Motivation
The medical field is seeing growing use of piezo technology especially in mobile oxygen therapy devices or mobile ventilators. In such cases, solenoid valve could have been used as they also need electricity as the power source same as piezo but these devices in order to work properly need to have specific requirements:
-
be light weight
-
less noisy
-
should consume little or no power
-
should be durable [2]
The piezo valve achieves all the above requirements. Besides this, they are anti-magnetic unlike solenoid and does not heat up like solenoid valves thus, making them a better prospective. But the work is still going on over the development of such micro piezo valves for different pneumatic application. And, the research on human blood is still going on due to its complex chemical structure. Hence, the reason for selecting a viscous fluid different from blood.
-
-
Importance of the problem
Since a few companies are working in this area, not much extensive work has yet been done. Moreover, in most cases the fluid considered is air or water similar to that used in ventilator. Hence, our work is significant as the design is different from any other design or device fabricated. Its not much sophisticated and the fluid considered is a viscous fluid thats similar to blood. So, our design can be used for other viscous fluids and for different applications.
-
Aim, Objectives and Scope of the project
-
Aim To relieve excess pressure in the pipe using a piezo valve
-
Objectives Designing a system consisting of a micro cantilever beam attached to a hollow cross-sectional pipe (all on micro level) besides considering a viscous fluid with certain properties similar to blood and simulating its laminar flow through the pipe using a software while the pressure is being relieved simultaneously by means of a piezo valve.
-
Scope The aim of pressure relief must be achieved while making sure that the pipe itself is not damaged
or no unwanted flow of liquid happens through the exit orifice
-
-
Background
The use of piezo actuating valve in pneumatic applications is still in early phase. They are gaining prominence in different applications due to the various advantages that piezoelectric materials offer. Their use in pneumatic applications has opened ways for other fields to benefit from this technology, one being medical. But the fluid most extensively being used is either air or water or saline solution (nothing remotely similar to human blood). The blood being a non-Newtonian fluid with complex chemical properties. Upon research and on advice of our mentor, we decided to base our project on a viscous fluid which might have one or two properties similar to human blood. This could lay groundwork for future research.
-
-
DESIGN:
percent phthalates by weight. Phthalates are esters of phthalic anhydride. They are added as softeners or plasticizers to plastics to increase their flexibility, durability, transparency and longevity. Thus, this grade of PVC is an ideal material for our project. [3]
The pipe designed is a hollow pipe with square cross- section. For simplicity purpose, the cross-section is a square so that the connection of the piezo valve can be done ithout difficulty. Following are the dimensions of the pipe:
-
Length of pipe is 100 mm.
-
The square cross-section is 5 mm x 5 mm.
-
The hole on the surface of the pipe through which some mass of fluid will exit is of dimension 4mm x 2mm.
-
Pipe
Several materials which are compatible with the blood like fluid are CBAS (Carmeda Bio- Active Surface) and Metallocene Polyethylene. But CBAS is not easily available and is costly whereas Metallocene Polyethylene is not suitable for medical purposes.
The other material that can be considered for the pipe is medical grade PVC. It is widely used in medical field. Some of the prevalent uses include: [3]
-
Blood bags and tubing
-
Caps
-
Catheters
-
Dialysis equipment and tubing
-
Drainage tubing
-
Surgical wires
-
Jacketing
-
IV containers and components
-
Drip chambers. [3]
But the reasons why PVC is widely used in medical field:
-
Safety
-
Low cost
-
Sterilisation
-
Bio Compatibility
-
Chemical stability
-
Flexibility, durability and dependability
-
Recyclable [3]
Such wide usage and reasons behind popularity of PVC makes it an ideal material for the pipe through which blood like fluid will flow. This medical grade PVC contains 20-40
Figure 1: Pipe created in Solid works
-
-
Cantilever beam
This is a crucial aspect to our design. There are two types of piezoelectric actuator:
-
Stack Actuator: Discrete stacks are composite structures made by stacking separately finished piezoelectric ceramic discs or rings and metal electrodes foils with an adhesive. They offer low stroke and a high blocking force.
-
Stripe Actuator: Also called a bending actuator, is designed to produce a relatively large mechanical deflection in response to an electrical signal. In stripe actuator, two thin layers of piezoelectric ceramic are bonded together, usually with the direction of polarization coinciding, and are electrically connected in parallel. When electrical input is applied, one ceramic layer expands and the other contracts causing the actuator to flex. [4]
The micro cantilever beam is made of piezoelectric material and acts as a striped actuator. The beam is a three- layered bimorph beam. There are two types of connection in a bimorph beam:
-
Series connection: The two piezoelectric layers have opposite polarization directions, and an electric field is applied across the total thickness of the bimorph.
-
Parallel connection: The two piezoelectric layers have the same polarization directions and the electric field is applied across each individual plate with opposite polarity. [4]
We chose parallel connection for the bimorph beam because of the following reasons:
-
The driving voltage for a bimorph actuator in the parallel connection can be reduced to half the value for a bimorph in the series connection while remaining the same electric strength and keeping the same actuation capability.
-
With the same driving voltage, the actuation capability of a parallel bimorph is twice that of series bimorph.
-
With the same external force, the electric charges generated by a parallel bimorph is twice the value generated by a series bimorph due to which stronger electric field will be generated.
-
For actuating applications, a low driving voltage is generally desired.
Figure 3: Bimorph beam created in Solid Works
The deflection of the bimorph beam is given by the formula shown below:
The working of the design will depend mostly on the amount of deflection in the bimorph beam. The deflection is according to the inverse piezoelectric effect which states that on application of an electric field, the piezoelectric elements will get strained and will deform or deflect. Thus, opening the hole on the surface of the pipe through which some mass of
beam is:
Figure 4: Formula for beam deflection [4]
In the formula shown above, the deflection of the
fluid will exit. The amount of deflection depends on how strong is the electric field. Hence, the reason for choosing bimorph design over unimorph design.
Figure 2: a) Series connection; b) Parallel connection [4]
A bimorph beam has two active layers of piezoelectric material and a passive layer whereas a unimorph beam has only one active layer and one passive layer.
Here, the top and bottom layers are of PZT-5H (lead zirconate titanate) and the middle, passive layer is of Al (Aluminium).
-
directly proportional to the square of the length of the
beam (L2)
-
directly proportional to the modulus of elasticity of the beam (E3)
-
directly proportional to the coupling coefficient (d31)
-
inversely proportional to the thickness of the beam (h)
Although there are 3 types of PZT series: PZT-5A, PZT-5J and PZT-5H but we are selecting PZT-5H because besides PZT being a widely used material, the PZT-5H has a modulus of elasticity of 5.0 x 1010 which is similar to the other PZT series but has the highest coupling coefficient among the PZT series and it varies from (0.44 to 0.75). Aluminium is used because of its conductivity, low cost compared to copper (Cu), gold (Au) etc., and is light in weight.
The dimensions of the beam are 4 mm x 2 mm x 0.03 mm.
-
-
-
Casing
Figure 5: Casing created in Solid Works
It acts as fixed support for the bimorph beam. The pipe passes through it and the size of the rectangular hole is 4mm x 2mm. Figure 6 shows the interference fit between the casing and the pipe. There is no relative motion between them.
Figure 6: Assembling of casing and pipe created in Solid Works
-
-
THEORY AND WORKING
-
What is Piezoelectric effect?
Piezoelectric Effect is the ability to cause an electric charge by certain materials in response to applied mechanical stress. One of the unique features of the piezoelectric effect is that it is reversible which means that materials exhibiting the direct piezoelectric effect (the creation of electricity when stress is applied) also shows the converse piezoelectric effect (the creation of stress when an electric field is applied).
When piezoelectric material is put under mechanical stress, a movement of the positive and negative charge centres in the material takes place, which then consequences in an external electrical field. When it is reversed, an outer electrical field either extends or presses the piezoelectric material.
The piezoelectric effect is very handy within many implementations that involve the production and detection of sound, creation of high voltages, generation of electronic
frequency, microbalances, and ultra-fine distinction of optical assemblies. It is also the ground of many scientific instrumental techniques with atomic resolution like scanning probe microscopes (STM, AFM). The piezoelectric effect also has its application in many mundane uses as well like fill-in as the ignition source for cigarette lighters.
-
Applications
High voltage and power sources: The electric cigarette lighter where pressing a button originates a spring-loaded hammer to hit a piezoelectric crystal, thereby producing a necessarily high voltage that electric current flows across a small spark gap, heating and igniting the gas is an example of implementation in this area. Most types of gas burners and ranges have a in-built piezo based injection systems.
Sensors: The most familiar sensor application is the detection of pressure variations in the form of sound which is seen in piezoelectric microphones and piezoelectric pickups for electrically amplified guitars.
Piezoelectric motors: As very high voltages correspond to only minute changes in the width of the crystal. The width of the crystal can be handled with better micrometer precision making piezo crystals an essential tool for arranging objects with extreme accuracy. Thus, making them perfect for use in motors, such as the various motor series provided by Nano motion.
Concerning piezoelectric motors the piezoelectric element collects an electrical pulse and then put in directional force to an opposing ceramic plate which causes it to move in the wanted direction. Movement is created when the piezoelectric element moves opposed a static platform for example, ceramic strips.
-
Working
Figure 7: Final Assembly created in Solid Works
A microfluidic pressure sensor is attached on the inlet of the pipe. This microfluidic pressure sensor is a low volume pressure sensor. It is capable of measuring pressure of liquid and gas anywhere in the system. It has a great accuracy (down to 0.2% full scale). It works as gauge sensors, measuring positive and negative pressure relatively to atmospheric pressure.
The microfluidic pressure sensor measures the gauge pressure at the inlet of the pipe. The cantilever beam is a three- layered bimorph beam. The top and bottom layer is the piezo material and the middle layer is the substrate. The substrate is
made of aluminium whereas, the piezo material is made of Lead Zirconate Titanate. The piezo material will be connected to the terminals of a piezoelectric device and when we supply voltage to the piezoelectric device, mechanical deformation will be developed in the beam which is finally used to control the pressure requirement in the pipe. So, basically, we used the inverse piezoelectric effect.
Here, a microfluidic pressure sensor is installed in the system to measure the pressure of the fluid. When the pressure of flowing fluid exceeds the requirement, it is required to relieve the excess pressure. For this, a voltage is applied across the piezoelectric beam. The principle is same as the inverse piezoelectric effect. This causes the beam to mechanically deform, opening the orifice on the surface of pipe. The orifice area for the exit keeps on increasing with the deflection of beam until the value of deflection reaches the maximum corresponding to the maximum voltage. The limit of voltage applied is from 0V to 700V i.e., the deflection is maximum at 700V. The discharge of fluid through the orifice keeps on increasing with increasing beam deflection. Hence, the aim of relieving the excess pressure is satisfied.
-
-
SIMULATION
-
Simulation software
The software used here is COMSOL Multiphysics. It is a cross-platform finite element analysis, solver and Multiphysics simulation software. It allows conventional physics-based user interfaces and coupled systems of partial differential equations. Engineers and scientists use the COMSOL Multiphysics software to simulate designs, devices and processes in all fields of engineering, manufacture and scientific research.
Multiphysics is one major enabler in eliminating assumptions. It couples related applications together to include all the necessary factors for a complete model.
The steps used in COMSOL simulation-:
-
We need to set up the model conditions according to the project requirements.
-
Then build the geometry in COMSOL or either
import the pre designed geometry.
-
Select the desired material in accordance with the project requirement
-
Then apply the mesh size as per our requirement and generate it.
-
Define the initial boundary conditions to get the optimal result.
-
Run the simulation with correct boundary conditions.
-
Post-process the result from the simulation with different boundary conditions.
-
-
Meshing
Finite Volume Analysis is carried out to understand and predict the behavior of parts/models under analysis so that expensive experimental setups can be avoided. Computers are used to perform these analyses because it would be impossible for a human to carry out the necessary calculations and properly predict the results for a large model in a short time.
Finite volume analysis breaks up the entire model into smaller elements and studies the behavior of these elements under the application of boundary conditions using the necessary governing equations to predict the behavior of the entire model.
Finite volume analysis consists of the following steps:
-
Pre-processing
-
Processing
-
Post processing
The entire model is broken up into smaller elements in the Pre-processing step. The process of breaking down the entire model into smaller elements is called Discretization. When the discretized model is viewed in its entirety, it will seem as a meshed body. Hence, the process is also called as meshing.
Mesh profile used in our project is given below:
-
For Micro-Cantilever beam
Figure 8: Mesh profile for beam obtained from COMSOL Multiphysics
-
For fluid flow in a pipe
Figure 9: Mesh profile for fluid flow obtained from COMSOL Multiphysics
-
-
Simulation of bimorph beam
A cantilever structure consists of greater length as compare to its width with optimal thickness.).
Figure 10: Formula for beam deflection [4]
Geometry:
Figure 11: Geometry as shown in simulation
Units:
Length unit
mm
Angular unit
Deg
Table 1: Units
Material Considered:
-
Lead Zirconate Titanate (PZT-5H)
Properties:
Density:
7800 kg/m3
Youngs modulus:
5 x 10 N/m2
Coupling coefficients: k33
0.75
k31
0.44
Table 2: Properties of Lead Zirconate Titanate (PZT-5H) [5]
-
Al Aluminum
Density:
2.6898 g/cm3
Modulus of elasticity:
68.3
Poissons ratio:
0.34
Properties:
Meshing:
Figure 12: Mesh profile for beam obtained from COMSOL Multiphysics
Parametric Sweep:
Parameter name
Parameter value list
Parameter unit
Vo
range(100,50,700)
V
It shows that voltage is the parameter considered in finding the beam deflection with minimum value at 100 V and maximum value at 700 V.
-
-
Simulation of fluid flow in the pipe
Boundary conditions-:
When our team is going through the simulation phase of Fluid flow in the pipe, we use different simulation softwares such as Ansys CFX, Ansys Fluent, and COMSOL. During this, we test different boundary conditions on these softwares to understand the effect of boundary condition on result of simulation. From this we were able to get the correlation between the boundary condition and the output.
The boundary conditions used in our project are-:
-
At inlet, the velocity of fluid is 2 m/s.
-
At hole, we apply the pressure of 0 kPa.
-
With these boundary conditions we were able to get the pressure of about 1.08 kPa at pipe outlet. So, with this we were able to get a pressure drop of about 1.14 kPa in 100 mm long pipe. The boundary conditions used in fluid flow simulation are shown below.
Table 3: Properties of Aluminum [6]
Figure 13: Inlet boundary condition obtained from COMSOL Multiphysics
Figure 14: Hole boundary condition obtained from COMSOL Multiphysics
GEOMETRY
Figure 15: Geometry of pipe obtained from COMSOL Multiphysics
Units:
Length unit
m
Angular unit
deg
Table 4: Unit
MESHING
Figure 16: Depiction of Meshing obtained from COMSOL Multiphysics
-
-
RESULTS AND DISCUSSION
-
For bimorph beam
Figure 17: Dataset: Study 1/Solution 1 obtained from COMSOL Multiphysics
PLOT GROUPS
Stress (solid):
Figure 18: Von Mises stress on the surface of beam (N/m2) obtained from COMSOL Multiphysics
The figure shows the stresses on different sections of the top surface of the beam. The yellow region indicates the area where maximum stress is induced. The magnitude of stress keeps on decreasing as we go towards the free end of the beam. The maximum stress induced on the beam is 9 x 108 N/m2 corresponding to Von-Mises theory of failure.
Electric Potential (es):
Figure 19: Multislice: Electric potential (V) obtained from COMSOL Multiphysics
The figure shows the range of applied voltage across the surfaces of the beam in the simulation ranging from 100 V to 700 V. The strength of electric field increases with the increasing voltage.
Displacement (solid):
Figure 20: Total displacement (mm) obtained from COMSOL Multiphysics
The figure shows the displacement at the free end of the beam. The red highlighted section sows that there is maximum displacement at the free end of the beam. The value being 1.58 mm at 700 V.
1D Point Graph
Figure 21: Point Graph for Total displacement (mm) vs Applied Voltage (V) obtained from COMSOL Multiphysics
The graph shows the linear relationship between the applied voltage and the displacement produced at the free end of the beam.
1D Plot Group
Figure 22: Line Graph for Total displacement (mm) vs Applied voltage (V) obtained from COMSOL Multiphysics
The graph shows the increasing value for the displacement at the free end of beam with the increasing voltage. The initial voltage applied is 100 V for which the displacement value is found to be 0.2 mm. The final voltage applied is 700 V for which the displacement value is found to be 1.58 mm.
-
For fluid flow inside the pipe
Figure 23: Dataset: Study 2/Solution 2 obtained from COMSOL Multiphysics
PLOT GROUPS
Velocity:
Figure 24: Slice: Velocity magnitude (m/s) obtained from COMSOL Multiphysics
In the figure, the red zone at the pipe inlet shows that the velocity of the fluid entering is very high with its magnitude being almost 2 m/s. The velocity starts to decrease from the point where the hole is open and starts to decrease till the velocity is around 1.5 m/s at the outlet of pipe
Pressure:
Figure 25: Contour: Pressure (bar) obtained from COMSOL Multiphysics
In the figure, the red zone at the pipe inlet shows the excess pressure of the fluid. The magnitude of pressure being around
22.71 x 10-3 bar. The pressure starts to decrease from the point where the hole is located. The pressure at the hole being around
4.13 x 10-3 bar. The magnitude of pressure at the pipe outlet is around 11 x 10-3 bar.
Mass flow through hole:
Figure 26: Slice: Mass flow through hole (kg/s) obtained from COMSOL Multiphysics
Figure 36 shows the mass flow of fluid through the hole at the surface of the pipe. The mass flow rate of the fluid through the hole due to beam deflection comes out to be 8.1 x 10-3 kg/s or 0.4585 litre per minute.
Mass flow through pipe:
Figure 27: Slice: Mass flow through pipe (kg/s) obtained from COMSOL Multiphysics
Figure 31 shows the mass flow rate of fluid through the pipe. The mass flow rate of the fluid comes out as 0.04 kg/s or 2.26 litres per minute
-
-
CONCLUSION
The figure above tabulates the values for pressure drop in a pipe and pressure drop across the valve as well as the shear stress in a 1.25 m tube-catheter pipe (made of medical grade PVC) for a given amount of blood flow. We are concerned with the pressure drop in the pipe.
Through COMSOL, the flow rate of blood like fluid through the pipe comes out to be 2.26 liters per minute. According to the above table, the pressure drop in pipe should be around 0.4 bars. COMSOL simulation gives us the velocity of fluid flow slightly greater than and equal to 2 m/s. The pressure drop in the pipe given by the simulation is nearly 11 x 10-3 bar. This is verified by the tabulated values as shown in the figure i.e., according to the velocity range, our value of pressure drop lies in the range of the results that were found experimentally.
We are not considering mass flow rate because the pipe used in that experiment had circular cross-section and the pipe used in our design has square cross-section. Also, the length of the tube used is much greater than the length of the tube in our design. The pressure drop is proportional to the length of the pipe. For two pipes of same diameter, pressure drop is more in longer pipe. So, the values of pressure drop from simulation doesnt match the values given in the table.
REFERENCES
[1] https://www.electronicdesign.com/power- management/article/21801833/what-is-the-piezoelectric-effect [2] https://festoblog.com/piezo-valve-technology-in-pneumatic- systems/ [3] https://pvc.org/pvc-applications/pvc-in-healthcare/ [4] Introduction to Piezoelectric Transducers by Rob Carter and Richard Kensley.https://piezo.com/pages/piezoelectric-actuators
[5] https://www.memsnet.org/material/leadzirconatetitanatepzt/ [6] https://www.theworldmaterial.com/al-6061-t6-aluminum-alloy/ [7] Xiaoli Liu, Lin Yuan, Dan Li, Zengchao Tang, Yanwei Wang, Gaojian Chen, Hong Chen and John L. Brash. 2010. Blood compatible materials: state of the art, pp. 3-11