
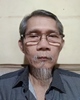
- Open Access
- Authors : Herbert Siahaan, Armansyah Halomoan Tambunan, Desrial, Soni Solistia Wirawan
- Paper ID : IJERTV9IS090035
- Volume & Issue : Volume 09, Issue 09 (September 2020)
- Published (First Online): 19-09-2020
- ISSN (Online) : 2278-0181
- Publisher Name : IJERT
- License:
This work is licensed under a Creative Commons Attribution 4.0 International License
Utilization of Gas Fuel as an Alternative Fuel in Internal Combustion Engine: A Review
Herbert Siahaan
Agricultural Engineering Study Program Graduate School of IPB University, Dramaga Bogor, Indonesia
Armansyah Halomoan Tambunan
Department of Mechanical and Biosystem Engineering IPB University, Dramaga
Bogor, Indonesia
Desrial
Department of Mechanical and Biosystem Engineering IPB University, Dramaga
Bogor, Indonesia
Soni Solistia Wirawan
Agency for the Assessment and Application of Technology (BPPT) Jakarta, Indonesia
Abstract-The increasing of energy need and the depletion of fossil oil content, it is necessary to look for alternative source or diversification of substitute energy. One of them is the use of natural gas as a fuel oil substitute. Many studies from different researchers use gas fuel with a variety of different methods. From the results of the study that apply gas fuel to the internal combustion engine, it can operate properly, no different from the original engine operation, it can reduce exhaust emission content and also operating costs. Biogas can be used as fuel in Otto motorcycles with simple modifications and at low cost. Good combustion quality can be reached by improving mixing and adjusting the air-fuel amount before entering the combustion chamber. With increased combustion through better air-fuel mixture in the combustion chamber, it will improve performance which has an impact on reducing exhaust emissions, so that the system of air-fuel mixture before entering the combustion chamber is worth considering. Therefore, the study of biogas fuel in the internal combustion engine as an electric generator is feasible to do. This paper examines one of the most important alternatives, namely the use of biogas and the intake system and provides a comprehensive overview of the impact on engine parameters including exhaust emissions.
Keywords:-Internal combustion engine, gas fuel, performance, emissions.
-
INTRODUCTION
Most of today's fuels use energy derived from fossil fuels in the combustion system. The depletion of fossil energy reserves is in line with the very significant increase in community needs for various purposes. Therefore it is necessary to search for alternative energy exploration, including gas energy as fuel. Many researches on natural gas including biogas have even applied it as fuel energy, including for the internal combustion engine as a driving force for various purposes such as electric generators. Digester reactors for producing biogas are often found in rural areas which are supported by the availability of local raw materials. The raw material for making biogas, which is easily available as feedstock, comes from various agricultural sector wastes, including from livestock manure. The fuel properties are an important role in determining the performance of the Otto motor such as: good evaporation (ability to mix homogeneously), does not contain destructive
elements (it can shorten component life), octane number which corresponds to good anti-knock properties (ability to avoid knock). Therefore, biogas can be used as a fuel from the digester directly with raw materials from the scope of agriculture in rural areas. The engine output depends on the properties and quality of the air-fuel mixture in order to produce combustion heat to be converted into mechanical energy. Thus the output power produced by biogas combustion depends on the heating value, the methane concentration in the biogas and the quality of the air-biogas mixture. The heating value of biogas combustion is influenced by the concentration of methane in the biogas composition which varies depending on the feed material and the conditions of the digester. Beside that, the caloric value of biogas also depends on the carbon dioxide and water content and has sufficient combustibility to produce heat energy. A number of researcher have been research on biogas as a fuel by considering the feed of biogas intake system into the combustion chamber through the intake manifold. Engine performance is influenced by the heat of combustion resulting from variations in the supply of the air-fuel mixture. Modification of a gasoline engine on a carburetor is relatively easy when the engine is designed to operate with the air-fuel mixture and maximize ignition distribution. Biogas produces low levels of exhaust gas emissions such as CO, CO2 and HC so that it is categorized as an alternative energy that is environmentally friendly and also is a renewable energy. This paper focuses on the effect of mixing air and biogas before entering the combustion chamber. This provides a comparison of the effects of using a mixer in producing the combustion performance parameters. So that the effect of the quality of mixing air and biogas on combustion parameters to produce output performance is discussed after studying various related research papers.
-
LITERATURE REVIEW
Reference [1] in their research using a gas fuel intake system (LPG) with a mixer and at relatively constant loading and rotation requires a limited maximum air flow rate. For test purpose, they used mixing chamber with cross flow type, where part of the original air intake of the engine was
replaced by a modified one. The air-biogas mixing arrangement uses a long venturi-type mixer, but the motor is still able to operate normally despite varying loads. In conclusion, the use of gas as fuel in the Otto motor driving an electric generator with a capacity of 1.5 kW motor can operate with a smooth motor sound even at varying loads. In addition, the Otto motor provides better mixing and combustion quality resulting in lower fuel consumption. The use of gas in a small capacity generator gasoline engine has an impact on improving the quality of mixing and better combustion, resulting in lower fuel consumption. It is one of the most cost-effective ways to run the engine on LPG, while maintaining the functionality of the system when it comes back to gasoline. The fuel used is synthetic biogas mixed with CO2 with 55%, 60%, 65% and 70%. The maximum output power is reduced by 20% when using biogas CH4 60% or more. Performance with reduced maximum load capacity. This study recommends small-scale power plants in the scope of agriculture and poultry, using raw materials for making biogas from plants in rural Bangladesh.
Reference [2] with the use of a pressurized biogas-fueled engine, the engine can operate well even though with a slightly decreased performance compared to a gasoline engine. Biogas is an attractive energy source for rural areas because it can be produced from cow and animal dung as well as renewable agricultural waste. Purification of CO2 from biogas will increase methane as its calorific value increases. Pressurized biogas with a purity above 90% is almost similar to CNG. The engine works well on pressurized biogas, it can improve fuel consumption; brake power and brake heat efficiency. An engine with the throttle position and the fuel intake valve produces less power when running under pressure biogas compared to gasoline. Analysis of gasoline exhaust emissions and compression of biogas fueled engines, HC and CO from biogas fueled engines with relatively the same pressure as gasoline-fueled vehicles. With compressed biogas fuel the engine can be operated directly. The focus now is shifting more towards the renewable sources of energy as a nonpolluting and in India the main sources of renewable energy are biomass and biogas.
Reference [3] suggest that fuel savings and reduction in exhaust emissions can be done by adjusting the pressure on the intake manifold. Adjusting the air intake pressure in the duct is done by adjusting the degree of throttle plate opening and the venturi effect that draws fuel into the combustion chamber of the engine being tested, namely the 4 stroke single cylinder SI engine. The experiment was carried out using a 5 kW dynamometer at various speeds and engine loading using a single four-stroke SI cylinder engine. The results show that the standard air intake system produces rich combustion which causes incomplete combustion due to lack of air availability. So that the availability of air is sufficient by removing the air filter so that there is no restriction of air flow through the air intake system. With the availability of sufficient air, it results in better combustion and less unburned fuel. Air with a higher intake pressure is required to increase air density for better combustion in a limited time thus increasing economically on fuel consumption, output power and exhaust emissions. To identify combustion quality and measure the composition of exhaust gas emissions, a gas
analysis is used. Complete combustion results in the reduction of unburned components such as carbon, hydrogen, carbon monoxide and hydroxide as emissions in exhaust gases.
Reference [4] suggest designing modifications with a turbulent vortex system to improve combustion quality and efficiency in single cylinder and direct injection 4 stroke diesel engines. And to get a good combustion efficiency, the engine must run at low speed to shorten combustion so that mechanical losses are low. To produce a high turbulence vortex, an intake channel with a helical shape is required before the combustion chamber. Experimentally using a helical-shaped intake manifold produces a vortex effect on engine performance characteristics as well as on the formation of exhaust emissions. So an engine with a helical intake manifold can produce more efficient engine performance, increased mechanical efficiency and reduced pollutant gases. In other words, by modifying the intake manifold, the air flow regulation can produce a better quality mixture to produce better combustion in the combustion chamber. Compared to normal manifolds, helical manifolds can improve thermal efficiency and improve engine and bsfc performance. Beside that, the use of helical manifolds has an impact on reducing CO2 and HC emissions.
Reference [5] in his research that uses a mixture of biogas and LPG fuels resulting in lower emission of combustion exhaust gases (CO, CO2 and HC) compared to emissions produced from gasoline-fueled Otto motorcycles. Therefore, biogas is categorized as one of the alternative energy which is environmentally friendly and is a renewable energy. Testing at 50% blending especially at full load results in specific fuel consumption and high thermal efficiency when compared to gasoline, LPG. High ecanic efficiency is produced from a mixture of 50% gasoline and LPG, while a mixture of 40% produces low CO, HC and NOX emissions. Biogas is superior because it can be produced in rural areas with available raw materials and has high knock resistance properties. Compared to biogas, fuel oil produces more emissions. Thus, biogas can be a promising fuel for the future.
Reference [6] refer to the results of studies of various researchers have been determine the performance of a CI engine with dual fuel (solar-biogas) to increase performance the original machine by conducted energy analysis of the combustion chamber using the laws 1 and 2 of thermodynamics quantitatively and qualitatively. Analysis performed by secondary data from other researchers such as measurements of air, fuel, engine load, and temperature. From the energy balance and engine exergy, several parameters of performance and energy efficiency and exergy of the engine are obtained with diesel fuel and dual fuel (solar-biogas). The results show that performance test of dual fuel engine is same as the diesel fuel engine, the same thing happens to the exergetic performance parameters. According to existing research; using exergy as a measure of quality shows that diesel fuel is better than biogas because of the diesel calorific value is greater than biogas. Biogas has a property with a low energy conversion efficiency, so a larger amount of biogas is required to travel the same distance. Exergy losses occur due to heat transfer and wasted through
exhaust gases. This research also reveals that the results of the analysis of the combination of energy and exergy are much better and more realistic. There is almost no deterioration in performance at all speed levels from the dual fuel engine. During the test, machine can be operated in stable conditions without modification to the engine or injection system.
Reference [7] the amount of heating energy of biogas combustion depends on the methane content and the heating value it contains under standard thermodynamic parameter conditions (temperature 273 K, pressure 101,325 kPa) has a specific heat of 2,165 kJ/kg.K, molecular weight of 16,043 kg/kmol and density 0.606 kg/m3. Calorific value, biogas has an adequate heating value with the highest heating value of HHV (higher heating value) and the lowest heating value of LHV (lower heating value) which determines the amount of combustion heat produced to be converted into output energy. The different properties of biogas with gasoline fuel require modification of the air-fuel mixture intake system in the air main channel before the intake manifold to adapt to the combustion conditions of the gasoline-fueled motor. In the use of biogas fuel, efforts are needed to design a mixing apparatus that can produce a mixture for good combustion. Modifying the biogas intake system is considered easier and cheaper than other treatments in the combustion chamber. By increasing the need for fuel consumption in such a way that the performance of the Otto motorbike fueled by biogas can be increased. This is cause the volumetric efficiency produced by biogas is lower than gasoline that causes a decrease in the maximum power of the biogas fueled engine.
Reference [8] suggested that the difficulty of using biogas as a fuel in internal combustion engine could be overcome by modifying some parts and engine specifications. In his research, he concluded that in the operation of the Otto motorbike with dual mixed fuels (biogas and gasoline). As a supplement biogas can reduce gasoline fuel consumption so that the cost is relatively economical where a mixture ratio of 20:80 gives the best engine operation. In addition, the use of biogas provides a positive contribution to a sanitary environment and its waste is useful as fertilizer and can have an impact on reducing the resulting pollution. Biogas is categorized as one of the alternative energy which is environmental friendly and usually called is a renewable energy.
Reference [9] explained that research was conducted on stationary electric generator propulsion engines and internal combustion engines for light duty tractors and trucks. The main aspect is focused on analyzing the techno-economic and environmental impact of a stationary electric generator driven internal combustion engine used as an option for agriculture in isolated rural areas. The problem concerns the use of biogas as fuel in the internal engine generators of the SI and CI combustion engines. The limited properties and characteristics of the biogas fuel require modification of the CI engine by changing to SI ignition system, lowering compression ratio 10-12, air-biogas intake system with venturi mixer type and AFR adjustment. Meanwhile, modifications to the SI engine are relatively easy, namely the use of an air-biogas mixer as a substitute for a carburetor. Machine control is carried out by varying the supply mix. A
lower specific fuel consumption and higher power output are obtained.
Reference [10] suggest based on a review that the use of biogas as a fuel is the best alternative to the current SI engine because it can significantly reduce emissions such as HC, CO2, and CO. Besides, it is easier to convert an SI engine with biogas fuel than a CI engine. Therefore, LPG as fuel in the CI engine driving the generator with high loading can produce environmentally friendly emissions. The performance test is analyzed on various variations of the mixture of diesel and LPG including pure diesel. However, due to the high ignition temperature of LPG and its low flame speed, it requires a higher ignition energy to produce complete combustion. In order to improve the compatible performance for various engine parameters the SI that affects performance must be optimized. Improving performance is done by modifying it with a simple system, namely increasing the diameter of the LPG intake as a secondary fuel besides diesel fuel in the generator engine. Using biogas fuel in the SI engine produces 8-14% less power than CI engines and a 20% reduction in efficiency. One way to improve the performance and emission performance of LPG-fueled SI engines is by optimizing ignition energy. By optimizing the combustion energy parameters, it can improve the performance and emission of LPG dual fuel engines and reduce NOX emissions in CI engines. This review of the study can contribute important data for the design and optimization of the biogas-fueled Otto engine for improved performance and reduced emissions.
Reference [11] explained that the modification in the combustion chamber is simpler than the modification in the combustion chamber, although the results of the modification test on the SI engine driving the biogas-fueled electric generator show a decrease in power. In principle, the power output of the SI engine with low CNG fuel is due to the loss of volumetric efficiency, low flame speed and differences in the calorific value of the two fuels. To anticipate this, this research will focus on developing the intake system for the SI engine with CNG fuel. The system is based on a stirring mixer applying a pressurized and turbulent flow. Modifying the CNG intake system is considered easier and cheaper than other treatments in the combustion chamber. The aim of modification and design of mixing equipment is to produce a mixture for good combustion. The difference in the properties of biogas with gasoline fuel requires modification of the air- fuel mixture intake system in the air main channel before the intake manifold to adapt to the combustion conditions of the SI motor with biogas fuel. CNG is suitable for use as a secondary fuel resulting in lower performance compared to gasoline.
Reference [12] suggested setting the compression ratio level within a certain limit, setting the ignition timing and improving the quality of the air-fuel mixture having a positive impact on performance parameters such as increased thermal efficiency, reduced fuel consumption and reduced exhaust emissions. Thus, a decrease in output power, average effective pressure and combustion efficiency can be improved.
Reference [13] in his experiment concluded that with an increase in the flow rate of gas fuel in the engine causes the
fuel combustion rate to increase, thereby decreasing the duration of combustion. Therefore cylinder pressure and cylinder temperature are higher compared to gasoline. The combustion of gaseous fuels occurs relatively almost uniformly and the gaseous fuel free of lead which has a very low sulfur content leaves the combustion chamber clean from the formation of soot. The consumption of gasoline is lower than that of natural gas due to the different energy content, where the energy content of gas is 46.23 MJ/kg while the energy content of gasoline is 44.4 MJ/kg. On the other hand, the volatility of the gas causes the air-gas mixing to occur more rapidly. With a decrease in fuel consumption in engines that use gas, the application of alternative energy use in machines can operate at a more economical cost. Along with the increase in the relatively high compression ratio, thermal brake efficiency, higher octane value, therefore the engine can operate effectively without knocking. CO and HC emissions increase due to compression ratio, speed and the need for increased load, but these emissions are lower when compared to gasoline engines.
Reference [14] In planning the use of biogas as fuel, the equation used in the analysis of the flow of the air and fuel mixture before entering the combustion chamber is: the velocity of the air-biogas mixture obtained from the velocity relationship through the distributor nozzle hole. The number and diameter of the nozzles are calculated based on the flow rate of the mixture through the air main channel. Reynold number, about similarity and dimensionless number shows flow classification (laminar, transition or turbulent) based on a function formulation: density (kg/m3), flow velocity (m/s), channel diameter (m) and dynamic viscosity (kg/ms).
Reference [15], in their research stated that the timing of the ignition through the crank angle position has a significant impact on engine performance. Too advanced ignition where combustion ends long before the end of the compression stroke can increase peak pressure and an expansion curve at optimum ignition where excessive pressure can result in a decrease in engine performance and efficiency. Conversely, late ignition can lower the peak pressure and expansion curve. This causes abnormal combustion. Both result in low engine efficiency.
Reference [16] Conclusion based on the review found that biogas is the best alternative to current IC machines. By modifying the air intake system and gas fuel as the second fuel in diesel and applying it as a gas fuel instead of fuel energy in the diesel engine driving the generator to produce heat energy which can be converted into mechanical energy. The experimental arrangement was made with simple modifications to the existing generator set to supply LPG as secondary fuel to Diesel. Demonstrate the feasibility of LPG as a dual fuel with diesel fuel replacing conventional diesel as it reduces emissions of major pollutant gases. The use of biogas can eliminate large amounts of emissions such as HC, CO2 and CO. The observations also concluded that dual fuels have shown the overall performance of the genset to show better results including NOX reduction. In addition, it is said that fuel with a composition of 70% diesel & 30% LPG as the best dual fuel mixture is recommended for loading more than 70% to 120%. With a decrease in the consumption of fuel that is replaced by gas, resulting in a much more economical
engine operating costs. In conclusion, it can also result in a reduction in fuel consumption equivalent to a 22% reduction in natural gas operating costs compared to the cost of the original engine.
Dieter and Angelika (2008) [17] biogas with methane containing heat energy can be used like natural gas or liquid fuels such as gasoline. The biogas content with the main component of methane gas in the range of about 45-70% from the digester reactor is the simplest hydrocarbon compound in the gas form so that biogas can be used as fuel. Meanwhile, the presence of other elements in biogas such as CO2, N2, H2, H2S and H2O can reduce the calorific value of biogas. The output power depends on the calorific value of a particular fuel to produce the maximum energy that can be released from that fuel through a chemical reaction of complete combustion of the mass or volume of the fuel.
Reference [18] suggested the use of natural gas when operated at high loading on a single cylinder Otto motor resulting in increased power and torque at various levels of compression ratio when compared to the original Otto motor. In addition, machines that are operated at various levels of compression ratio have decreased CO and HC emissions on natural gas engines compared to the original engines. This occurs at higher compression in proportion to the increase in the flow rate of higher gas fuel consumption. and results in reduced exhaust emissions.
Reference [19] suggest that the best power and torque for biogas are obtained by making the right adjustments to the compression ratio, air and fuel intake system and combustion ignition settings to produce good efficiency. By analyzing the engine Otto cycle evaluated on a dynamometer, produces a characteristic curve of torque and power. The optimal conditions obtained from the Otto engine tested using biogas fuel were carried out by using a venture-type mixer in the air- biogas mixing process, setting the compression ratio level to
12.5 and ignition advancing 450. On the other hand, with the use of BBG, at 3600 rpm engine speed, generator generate electricity up to 15% higher than the use of biogas.
-
CONCLUSION
Biogas can be used as fuel in the motor of internal combustion engine with a simple modification and low cost. The combustion yield parameter depends on the amount of air and fuel as well as the quality of the mixture before entering the combustion chamber. To improve the adequate combustion quality of biogas with limited properties compared to fuel oil, it is necessary to modify the air intake system and the biogas fuel before the intake manifold. Increasing the quality of combustion has an impact on performance and also reduces exhaust emissions.
REFERENCES
-
Ehsan Md. and N. Naznin, Performance of a Biogas Run Petrol Engine for Small Scale Power Generation, Journal of Energy & Environment, vol. 4, 2005, pp. 1 9.
-
Jayesh D.Vaghmashi, Mr.D.R.Shah, Mr.D.C.Gosai, An Experimental Study of Petrol Engine Using Compressed Biogas as a Fuel, International Journal for Scientific Research & Development, vol. 2, issue 04, pp. 3630-3632, 2014.
-
Nik Rosli Abdullaha, Nafis Syabil Shahruddina, Aman Mohd. Ihsan Mamata, Salmiah Kasolanga, Aminuddin Zulkiflia and Rizalman Mamatb, Effects of Air Intake Pressure to the Fuel Economy and Exhaust Emissions on a Small SI Engine, The Malaysian Tribology
Society (MYTRIBOS), Department of Mechanical Engineering, Universiti Malaya, 50603 Kuala Lumpur, Malaysia, Procedia Engineering 68, 2013, pp. 278 284.
-
Manoj Prajapati danDipak.M.Patel, Performance Investigation Of Intake Manifold Geometry On 4-Stroke Single Cylinder Diesel Engine, International Journal For Technological Research In Engineering, vol. 3, issue 11, 2016, pp. 3177-3180
-
Venkata Ramesh Mamilla, V. Gopinath, C.V. Subba Rao and Dr.G. Lakshmi Narayana Rao, Performance and Emission Characteristics of 4 Stroke Petrol Engine Fuelled with Biogas/LPG Blends, International Journal of Advanced Engineering Technology. vol.II/ issue I, pp. 209- 213, 2012.
-
Harilal S. Sorathia and Hitesh J.Yadav, Energi Analysis to a CI- Engine Using Diesel and Bio-Gas Dual Fuel – A Review Study, International Journal of Advanced Engineering Research and Studies, vol. I (II), pp. 212-217, 2012.
-
Mitzlaff KV, Engines for biogas, Theory, Modification, Economic Operation. A publ. of Dt. Zentrum für Entwicklungstechnologien-Gate in: Dt.Ges. fur Techn. Zusammenarbeit (Gtz) GmbH. Africa, 1988.
-
Awogbemi, Omojola, Adeyemo and Sunday Babatunde, Development And Testing of Biogas-Petrol Blend As An Alternative Fuel For Spark Ignition Engine Awogbemi, Omojola, International Journal of Scientific & Technology Research, vol. 4, issue 09, pp. 179-186, 2015.
-
Stefan MIHIC, Biogas Fuel For Internal Combustion Engine. Annuals of The Faculty of Engineering Hunedoara. 2(3); pp. 179-190, 2014.
-
Ankit B Joshi, Pratik B Umrigar, Akash B Patel and Karan A Patel, Using Biogas in SI Engine by Changing Ignition Parameter and Compression Ratio, International Jurnal for Scientific Research & Development. 3 (2), pp. 751-756, 2015.
-
Rosli Abu Bakar, Design and Development of a New CNG (Compressed Natural Gas) Engine, Pusat Pengurusan Penyelidikan Universiti Teknologi. Malaysia, 2002.
-
Przybyla, G.A. Szlek and L. Ziolkowski, Assessment of the Performance of a Small Capacity SI Engine Fuelled with Model Lean Mixture of Biogas, International Journal of Thermodynamics (IJoT) Vol. 16 (No.4), pp. 179-188, 2013.
-
Thirumal mamidi and J.G. Suryawnshi, Investigations on S.I. Engine Using Liquefied Petroleum Gas (LPG) as an Alternative Fuel, International Journal of Engineering Research and Applications (IJERA), vol. (1), pp. 362-367, 2012.
-
Frank M White, Fluid Mechanics, University of Rhode Island, Fourth Edition, Mc Graw Hill in Mechanical Engineering, Madison, 1990.
-
Dabhadkar Tiwari Chowk and Yavatmal, Effect OF Ignition Timing On The Performance Of LPG Fuelled SI Engine, International Journal of Engineering Science and Technology. ISSN : 0975-5462, vol. 5 no.05S, ex-plore 13, pp. 24-28, 2013.
-
K. Mohan Kumar and Dr. D. Azad, An Experimental Investigation of Performance and Emissions of LPG as Dual Fuel in Diesel Engine Generator, International Journal of Engineering Research and Applications, vol. 4, issue 11 (version 2), pp. 41-53, 2014.
-
Dieter Deublein and Angelika Steinhauser, An Introduction, Biogas from Waste and Renewable Resources. WILEY-VCH Verlag GmbH & Co. KGaA, Weinheim, 2008.
-
Syed Youfuddin and Syed Nawazish Mehdi, Performance and Emission Characteristics of LPG-Fuelled Variable Compression Ratio SI Engine, Turkish J. Eng. Env. Sci. 32 pp. 7 12, 2008.
-
Cassiano Rossetto, De Souza S. N. M, Santo R. F, De Souza Juliano and Klaus O. L, Performance of an Otto Cycle Engine Using Biogas as Fuel, African Journal of Agricultural Research, vol. 8(45), pp. 5607-5610, 2013.