
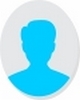
- Open Access
- Authors : Karthik Jagadeesh , Rajashekar J S
- Paper ID : IJERTV10IS070267
- Volume & Issue : Volume 10, Issue 07 (July 2021)
- Published (First Online): 03-08-2021
- ISSN (Online) : 2278-0181
- Publisher Name : IJERT
- License:
This work is licensed under a Creative Commons Attribution 4.0 International License
Use of Super Capacitor in PMSM Drive for Electric Vehicle Application
Karthik Jagadeesh
Department of Electronics and Instrumentation, Dayananda Sagar College of Engineering,
Shavige Malleshwara Hills, Kumaraswamy Layout, Bengaluru-560078, India
Rajashekar J S
Department of Electronics and Instrumentation, Dayananda Sagar College of Engineering,
Shavige Malleshwara Hills, Kumaraswamy Layout, Bengaluru-560078, India
Abstract – As the demand for electric vehicles are increasing, the energy usage from the battery needs to be efficient in order to achieve maximum distance on a single charge of battery. In this paper, the effective use of super capacitor in electric vehicles having a Permanent magnet synchronous machine drive is analysed. The Permanent magnet synchronous machine drive is speed regulated for motoring and braking action. The simulated results on state of charge of the battery with and without the use of super capacitor is compared.
Keywords – Regenerative braking, Permanent magnet synchronous machine (PMSM) drive, Super capacitors, Electric vehicle (EV), State of charge (SoC)
-
INTRODUCTION
The growth of electric vehicles industry increasing day by day due to EV's greater efficiency, less emission, low noise level and no oil fuels required when compared to combustion engines. The battery holds the significant role in improving the performance of the EVs. As it is the main source of energy that drives an EV due to which need for reducing electrical losses and quick charging of battery is being developed. The performance of the battery can be improved with the means of battery management systems, helps in increasing the distance coverage of EVs on single charge[3][5].
The use of electric drives has an advantage that it can also be used as an electric generator, hence utilized for regeneration of energy during braking[4][6]. Electric power can also be generated by other forms, such as solar photovoltaic cells installation on top of the vehicles and also by the use of micro wind turbines. Due to the fast charging and discharging period, energy storage device like super capacitors are used with the help of a hybrid energy storage system[1]. The super capacitors have low energy density and high power density enabling the use of these devices more handy. The stored energy can be utilized during the peak demand for current such as building up of initial torque[2].
-
HYBRID ENERGY STORAGE SYSTEM
Fig.1Block diagram representation of the PMSM system
In the Fig 1 shows the block diagram representation of super capacitor based PMSM drive system with regenerative braking system. In the normal drive mode battery bank provides the necessary power to drive PMSM motor through a DC/DC converter. Regenerative braking method is used deaccelerating to reduce the speed and also bring the vehicle to a halt. The PMSM drive acts as generator and the energy which is generated is stored in a super capacitor bank during regenerative braking. A different DC/DC converter is used to convey the energy from PMSM drive to the super capacitor bank. The stored energy in the super capacitor banks are utilized during the initial high torque building phase of the PMSM drive, when the motoring action is started from the EVs halt position. The battery supply is only used for powering the motor after and not utilised during the initial torque building phase. But, if the super capacitor has a energy density less than 20%, then battery is even used as the supply for the initial torque building phase.
-
CONTROL STRATEGY
The control strategy used to drive the PMSM machine is a PI controller in order to control speed of the EV. The error signal of desired speed and rotor speed is given as an input to the PI controller, which outputs a current reference value. Depending on the current reference, rotor angle and rotor current values PWM pulses are generated. The pulses are fed to both the DC/DC converter depending on the mode of operation. Two switches are connected from battery and super capacitor to the DC/DC converter 1 namely Sbat and Ssc switches respectively.
During motoring mode, the switch Sbat is turned on and the switch Ssc is turned off. The power to run the motor is only powered by battery during this mode.
During regenerative braking mode the PWM of pulses are provided to DC/DC converter 2. Both the switches Sbat and Ssc are turned off. The PMSM machine generates power and the energy is stored in the super capacitor banks in this mode.
During accelerating mode the switch Ssc is turned on and switch Sbat is turned off. During this mode only super capacitor banks provide the power to the PMSM machine to perform motoring action.
-
SIMULATION AND ANALYSIS
The simulation is executed in MATLAB/simulink as represented in the Fig 2 for all the modes of operation. The following specification are consider for the model simulation. A Li-ion battery having 96V, 30Ah, 100% SoC is considered. Motor having a maximum power rating of 350W and torque 10Nm. The super capacitor of 25F is used for simulation.
Fig 2 Simulink model of the PMSM drive with super capacitors
The simulation is carried out with and without super capacitor connection. The Fig 3 shows the current waveform of the PMSM drive where all the three modes are carried out. The time period between 13-14 second is the regenerative mode, time period between 14-15 second is the accelerating mode and rest of the time period is the motoring mode.
Fig 3 Rotor current waveform of the PMSM drive
The simulation first carried out without the use of super capacitor bank. In order to carry out this scenario the battery system is only considered for driving the machine. The current drawn from the battery is shown in the Fig 4 waveform. The PMSM motor is brought to a halt using regenerative braking mode from 13th second to 14th second and then acceleration mode from the 14th second onwards is executed. Since super capacitor bank is not connected to the system, battery is used to supply the energy by turning on the Sbat switch even during acceleration mode. The current required for the motor to accelerate reaches peak high value during this period.
Fig 4 Current waveform of the battery without super capacitor
The Fig 5(a) shows the current waveform of the battery when super capacitor bank is connected. The super capacitor provides the energy to the motor for a duration of 1 second between 14 to 15th second. The battery supply is cut down during this period as it is in the accelerating mode (switch Sbat is off and Ssc is on). The peak demand of the PMSM drive is handled by the super capacitor bank. The current waveform of the super capacitor bank during acceleration mode is shown in the Fig 5(b).
Fig 5(a) Current waveform of the battery with super capacitor
Fig 5(b) Current waveform of super capacitor bank during acceleration mode
The comparison between the EV system with and without the use of super capacitor is made based on the SoC of battery. The simulation is conducted for a sample period of
100 seconds with SoC of battery at 100% initially. All the three modes motoring, braking and acceleration is carried out on a repetitive sequence and the simulation pattern remains same for both the system with and without the super capacitor bank connection. The TABLE 1 represents the SoC of battery with and without super capacitor bank connection to the system. The SoC of battery without the super capacitor is shown in the Fig 6(a). Similarly, SoC of battery with super capacitor is shown in the Fig 6(b).
TABLE 1 Comparison of the systems
Parameters
Initial SoC of battery (%)
Final SoC of battery (%)
Increase in SoC of battery (%)
System with only Battery
100
99.765
–
System with super capacitors
100
99.786
0.021
Fig 6(a) SoC of the battery without super capacitor
Fig 6(b) SoC of the battery with super capacitor
-
CONCLUSION
Utilization of super capacitor for PMSM drive has been discussed in this paper. The simulation results are the comparison between battery energy with and without super capacitor bank. The stored energy during regenerative braking in the super capacitor is used during the acceleration of the EV from the halt position as it requires huge value of current. The SoC of the battery increases by 0.021% for the test duration of 100s, due to the utilization of super capacitor. It can be concluded that the life of the battery increases, as the current from the battery to the motor for acceleration is avoided. Hence, the charge on the battery is also increased on a single charge resulting in increase in distance coverage of EVs.
REFERENCES
-
Chinmaya Patnaik, Makarand M. Lokhande and Sagar B. Pawar, "Hybrid Energy Storage System using super capacitor for Electric Vehicles", 2019 Innovation in Power and Advanced Computing Technique (i-PACT).
-
Gurusivakumar Guruvareddiyar and Ramachandran Ramaraj, "Super Capacitor Based Energy Recovery System from Regenerative Braking used for Electric Vehicles Application", 2019 IEEE.
-
G Subramanian and Joseph Peter, "Integrated Li-Ion Battery and Super Capacitor based Hybrid Energy Storage System for Electric Vehicles", 2020 IEEE.
-
Amritha Anand, Nandan G and Najma Habeeb, "A Novel Method of Energy Regeneration in Electric Vehicle", NFTPCOS-18, IJIREEICE.
-
Bao-Huy Nguyen, Joao P Trovao, Roman German and Alain Bouscayrol, "An Optimal Control-Based Strategy for Energy Management of Electric Vehicles using Battery/Super capacitor", 2017 IEEE.
-
Nikolay Lyuboslavov Hinov, Dimitar Nikolov Penev and Gergana Ilieva, "Ultra Capacitors Charging by Regenerative Braking in Electric Vehicles", Proc: XXV International Scientific Conference Electronics – ET2016, Sozopol, Bulgaria.
-
Xiao Peng, Quan Shuhai and Xie Chaungjun, "Simulation of a Li- ion battery/super capacitor hybrid system for electric vehicle based on secondary development of ADVISOR" 2018 5th International Conference on Electric Vehicular Technology (ICEVT), Surakarta, Indonesia.