
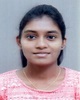
- Open Access
- Authors : Megha Bhujbal , Ankita Deshmukh , Kalpesh Gaikwad , Sagar Bhoring, Pallavi Dongare
- Paper ID : IJERTV10IS050292
- Volume & Issue : Volume 10, Issue 05 (May 2021)
- Published (First Online): 31-05-2021
- ISSN (Online) : 2278-0181
- Publisher Name : IJERT
- License:
This work is licensed under a Creative Commons Attribution 4.0 International License
Use of Industrial Waste Water in Concrete
Megha Bhujbal
Civil Engineering Vishwaniketans (iMEET) Khalapur, India
Ankita Deshmukh
Civil Engineering Vishwaniketans (iMEET) Khalapur, India
Kalpesh Gaikwad
Civil Engineering Vishwaniketans (iMEET) Khalapur, India
Sagar Bhoring
Civil Engineering Vishwaniketans (iMEET) Khalapur, India
Pallavi Dongare
(Mentor) Civil Engineering Vishwaniketans (iMEET) (Professor) Khalapur, India
Abstract – In construction industry there is no substitution for concrete and concrete needs potable water. Concrete is 2nd industry to consume more water. In concrete industry, approximately 150 lit of water is required per cubic meter of concrete mixture. Nowadays, scarcity of water is becoming a worldwide problem and some extra efforts should be taken to resolve this problem. So, use of waste water discharged from different types of industries or locations in construction industry may help to reduce the problem of scarcity of water. This research aims to check whether treated waste water from oil industry can be used in construction industry or not to reduce the load on nature.
Waste water collected from dairy, car wash center, sewage treatment plant, etc. is used as 100 percent substitution while making concrete. Cubes are supposed to be tested against compression load on 7, 14 and 28 days by casting and curing it with water from oil industry. Three concrete cubes are supposed to be tested during each and every test. So, 9 cubes are prepared by using waste water substitution which are willing to be compared with 9 cubes which are prepared by using potable water.
Keywords:- W aste water, concrete, water scarcity, compressive strength, potable water.
INTRODUCTION
Water scarcity is an ongoing water crisis and it is affecting nearly 1 million people each year. The way water scarcity affects huge rural and urban population, it also affects the ecosystem and agriculture too. India has only 4% of the world's fresh water resources over a population of 1.3 billion people. India is facing water scarcity problem since long time. Per capita water availability is less than 1,700 m3 and the present value in India is noticed as 1,545 m3. According to prediction of water ministry, water availability could reduce to 1,341 m3 in 2025 and it could be noticed as 1,140 m3 by 2050.
Scarcity of water has affected all the industries in India and it includes construction industry as well. Large amount of water is needed in construction industry for various purposes. In the beginning, water is needed to mix cement, sand and other raw ingredients that are needed in the concrete mix. To make the plaster as well as
construction strong and solid, water is sprayed on the built surface so that mortar absorbs the water and makes it tougher. Large amount of water is needed for the same, depending on the volume of the construction project. Waste water releasing from different types of industries is getting waste by just adding to the surface water and it also reduces quality of surface water. In many areas, surface water is used as replacement of potable water for drinking purpose. Reduced quality of surface water may affect the health of human beings or aquatic life. Reuse of this industrial waste water is a better solution to maintain the quality of surface water. And if it is to be used in construction industry, it may reduce major load on demand of fresh potable water.
OBJECTIVES
-
To find the alternatives of basic material water which is used in construction.
-
To find sustainable or economical solution for construction industry by replacing potable water to industrial waste water.
-
Prevent or to reduce pollution of surface water.
-
To reduce the demand of potable water.
-
Reuse of waste water which has no use.
CONCRETE MATERIALS
Concrete is a construction material which is composed of cement, fine aggregates, coarse aggregates and water. All the materials are mixed in specific proportions to obtain the required strength of concrete. Strength of mix is specified as M5, M7.5, M10, M15, M20, M25, M30 etc.
Cement.
A cement is a binder material which is used in concrete to bind other materials together. Cement have different grades. Grade of Cement shows strength of cement. Three grades of cement in which cement gets available are 33, 43 and 53.
Cement used for experiment is OPC 53 grade cement. Aggregates
The term concrete aggregate covers coarse as well as
fine grade. Coarse aggregates have size greater than 4.75 mm. Fine aggregates are any material which can pass through a 4.75mm sieve. Aggregates make up 60% to 80% of volume of concrete and 70% to 85% of mass of concrete. Aggregate is very important constituent for strength, thermal and elastic properties of concrete.
For this experiment, Coarse Aggregates of maximum size 20 mm and fine aggregates of zone II are used.
Water
The amount of water used in concrete controls fresh and hardened properties of concrete like workability, compressive strengths, water tightness, permeability, weathering, durability, drying shrinkage and potential for cracking. For all these reasons, limiting and controlling the amount of water in a concrete is important for both constructability and service life.
Potable and treated industrial waste water is used for this experiment.
LITERATURE REVIEW
-
Amir Hossein Askariyeh (2019) Investigating the Possibility of Using Recycled Industrial Wastewater Instead of Potable Water in Concrete Mixture:
The study concluded that when treated industrial wastewater remained under the sun for 7 days there was a reduction in compressive strength of concrete when compared with samples prepared with the same water remained in shade. However, strength properties of concrete in both cases were higher than those prepared with potable water.
-
Vijay H (2017) Reusing Treated Effluents for Making Concrete:
This study concluded that there is no noticeable side effect on strength of concrete when it is prepared with the use of treated effluents, auto service stations (garage) water and dairy wastewater. The compressive strength of the plain concrete cast and cured with reused wastewater effluent increased with the curing period and the physio-chemical properties. The replacement of fresh water by treated effluent conserved the natural water resources and increased the strength of concrete. Study therefore recommends the reuse of treated effluents with acceptable physio-chemical properties for use in plain concrete works.
-
Miss. Kirtimala Laxman Narkhede and Mr.
F. I. Chavan (2017) Effect of Treated Waste Water on Strength of Concrete:
This study deals with Effect on strength of concrete by using different type of treated water like PTWW, STWW and Domestic waste water with Potable water. This study concluded that STWW contains fewer impurities and it fits within IS standards. Consistency, initial setting time and final setting time of cement paste by mixing STWW is within the IS limit. Compressive strength of concrete which is prepared with STWW gives same strength as concrete prepared with potable water. Any significant difference in tensile strength was not observed but Flexural strength is improved by using STWW.
-
E.W. Gadzama (2015) Effect of Sugar Factory Waste Water as Mixing Water on the Properties of Normal Strength Concrete:
This paper deals with use of sugar factory waste water in concrete cubes to determie the strength of concrete as compare to concrete cubes which are prepared by mixing potable water. Different percentage of waste water is substituted while preparing different concrete cubes to determine the compressive strength effect of waste water on concrete.
According to result, the setting time of wastewater increases with an increase with percentage replacement. At 28th day, target strength was not achieved but it ranged from 83% to 91%. When the curing duration was extended to 90 days, strength of concrete reached to target strength.
-
R.A. More and S.K. Dubey (2014) Effect of Different Types of Water on Compressive Strength of Concrete:
This study concluded that concrete made with different qualities of water samples such as ground water, packed drinking water, waste water etc. have compressive strength equal to or at least 90% of the strength of concrete specimen prepared with clean water.
-
F. Adeyemi and G. Modupeola (2014) Experimental Investigations on the effect of sea water on the compressive strength of concrete:
This paper deals with the study of effect of sea water on the compressive strength of concrete as compare to fresh water. Increase in compressive strength of concrete is noticed when it is casted and cured with sea water. It was noticed that compressive strength of the concrete was affected when the concrete was cast with fresh water and cured with salt water and vice-versa.
-
Vidhya Lakshmi and Arul Gideon (2014) "Secondary treated waste water in construction"
Test showed that secondary treated wastewater increases the load carrying capacity and 9.62% increase in strength was observed in compressive strength more in case of primary treated wastewater.
-
Marka Silvia and T. R. Naik (2010), Sustainable use of resources
This study concluded that compressive strength of cubes with sewage treatment plant shows increase in compressive strength during 3 to 28 days and it is improved by 91 days.
METHODOLOGY
-
Tests on Materials
-
Tests on Cement
-
Field Tests
Quality of cement is first analyzed by field tests. It should fulfill following requirements:
Color test-Cement had a uniform color. It was greyish in color with light green shade.
Temperature test-When hand is inserted in a cement bag, it felt cool.
Float test-When a small quantity of cement is thrown in bucket of water, the particles for some time float before it
sinks.
Date of Packing-It is important to check the manufacturing date of the cement because strength of cement reduces with time. Cement should be used within 3 months after manufacturing.
-
Laboratory Test
Specific gravity test is done to check the specific gravity of cement. As per result of test, specific gravity of cement was 3.15.
-
-
Tests on Coarse Aggregate
-
Impact Test
The aggregate impact value should be measured to check capacity of aggregate of resistance to sudden impact or shock. This characteristic is measured by impact value test.
-
Crushing Test
The strength of coarse aggregates is measured by crushing test. The aggregate crushing value shows resistance capacity of aggregates against crushing under a gradually applied compressive load.
-
Specific Gravity Test
Specific gravity test of coarse aggregates is done to measure the quality of the material. Value of specific gravity of coarse aggregate is used in mix design.
-
Water Absorption Test
water absorption test is done to check the water holding capacity of the coarse aggregates. That value is used in mix design.
-
Shape Test
The shape test gives a rough idea of the relative shapes of aggregates. Flaky and elongated particles should be avoided in concrete.
Table No. 1 – Tests on Coarse Aggregate
Sr. No.
Test
Result
1
Impact Test
19.615%
2
Crushing Test
34.33%
3
Specific Gravity Test
2.64
4
Water Absorption Test
0.81%
5
Shape Test
Flakiness Index
14.7%
Elongation Index
20.3%
-
-
Tests on Fine Aggregate
-
Specific Gravity Test
Specific gravity test of fine aggregates is done to measure the quality of the material. Value of specific gravity of fine aggregate is used in mix design.
-
Water Absorption Test
water absorption test is done to check the water holding capacity of the fine aggregates. That value is used in mix design.
-
Fineness Modulus Test
Fineness modulus shows an average size of the fine aggregate particles. Size of aggregates plays an important role in strength and workability of concrete.
Table No. 2 – Tests on Fine Aggregate
Sr. No.
Test
Result
1
Specific Gravity Test
2.65
2
Water Absorption Test
1.1%
3
Fineness Modulus Test
2.75
-
-
Tests on Water
-
pH Test
pH determines the acidity or alkalinity of water or waste water. The pH of water is a very important measurement to know the quality of water.
-
Turbidity Test
Turbidity test determines suspended particles which are responsible for loose of transparency of water. Water can be considered as more healthful when it has less turbidity.
-
Total Hardness Test
Water Hardness is nothing but the concentration of Calcium and Magnesium Ions in Water. As hardness causes the development of an insoluble curdy precipitate in the water, it prevents soap from lathering.
-
Alkalinity Test
Alkalinity test gives an idea about how much acid can be added to a liquid without causing a major change in pH.
-
Total Suspended Solids
Total suspended solid test gives a general idea of quality of the water. It represents suspended solids in water.
-
COD Test
The chemical oxygen demand (COD) gives an idea about quality of water. The COD test is often used to understand the water treatment plant efficiency.
Table No. 3 – Tests on Water
Sr.
N0.
Test (Unit)
Result
Potable Water
Industrial Waste Water
1
pH Test
7.1
7.2
2
Turbidity Test (NTU)
0.9
1.3
3
Total Hardness Test (mg/L)
110
123
4
Alkalinity Test (mg/L)
47
64
5
Total Suspended Solids (mg/L)
13
18
6
COD Test (mg/L)
3
35
-
-
-
Slump Cone Test
Slump test is the method of measuring consistency of concrete. This test can be employed either in laboratory or at site of work also. Very wet or very dry consistency of concrete is not suitable for this method.
In this experiment, the difference between height of top of the mold and the displaced original center of the top surface of the specimen is observed as 50 mm.
The pattern of slump is shown as True slump.
The slump of concrete 50 mmindicates Medium degree of workability.
-
Mix Design
Desired Compressive Strength = 20MPa Nominal size of aggregate = 20mm
Fine Aggregate = Zone II Type of Exposure = Severe Slump = 50mm
W/C Ratio = 0.45
Cement grade = OPC 53 grade Specific gravity of Cement
= 3.15
Specific gravity of Course Aggregate = 2.64 Specific gravity of Fine Aggregate = 2.65 Water Absorption of Coarse Aggregate = 0.81% Water Absorption of Fine Aggregate = 1.1%
Step 1 – Calculation of Target Mean Strength Target mean strength = fck + 1.65 x s
= 20 + 1.65 x 4
= 26.6 MPa
Step 2 – Selection of W/C Ratio
From IS 456-2000, Page No. 20, Table No. 5 Maximum W/C Ratio = 0.50
For severe exposure, maximum nominal size of aggregate 20mm Adopted W/C Ratio = 0.45<0.50 Hence, it is OK.
Step 3 – Selection of Water Content
From IS 10262-2009, Page No. 3, Table No. 2 Maximum water content = 186lit
Step 4 Calculation of Cement Content From IS456-2000, Page No. 20, Table No. 5 For Severe Exposure,
Minimum Cement Content = 250kg/m3 Water Cement Ratio = 0.45
Water Content = 186 lit
Cement Content = Water Content / 0.45
= 186/0.45
= 413.33 kg/m3
Calculate Cement Content Value is 413.33kg/m3 which is greater than 250kg/m3.
Hence, it is OK.
Step 5 Volume of Entrapped Air
From IS10262-2009, Page No. 3, Table No. 3
For Nominal Maximum 20mm Size of Coarse Aggregate,
Entrapped Air = 1% of Volume of concrete
Step 6 Proportion of Volume of Coarse Aggregate and Fine Aggregate
From IS10262-2009, Page No. 3, Table No. 5 Volume of Coarse Aggregate corresponding to 20mm size per unit volume of Total Aggregate for Zone II of Fine Aggregate and 0.50 W/C Ratio = 0.62
Adopted W/C ratio is less by 0.05 by Maximum W/C Ratio
The coarse aggregate is increased at a rate of 0.01% for every decrease in W/C ratio of 0.05
… Corrected proportion of volume of Coarse Aggregate = 0.62+0.01 = 0.63
Volume of Fine Aggregate = 1 – 0.63 = 0.37
Step 7 Mix Calculation Volume of Concrete = 1 m3 Volume of Cement = Mass of Cement / Specific
Gravity of Cement x 1000
= 413.33 / 3.15×1000
= 0.131m3
Volume of Water = Mass of Water / Mass Density
= 186 / 1×1000
= 0.186 m3
Volume of Entrapped Air = 0.01 m3 Volume of All Aggregates
= Volume of Concrete (Volume of Cement + Volume of Water + Volume of Entrapped Air)
= 1 (0.131 + 0.186+0.01)
= 0.673 m3
Mass of Course Aggregate
=Volume of All Aggregate x Specific gravity of Course Aggregate x Volume of Course Aggregate x 1000
= 0.673 x 2.64 x 0.63 x 1000
= 1193.33 kg
Mass of Fine Aggregate = Volume of All Aggregate x Specific gravity of Fine Aggregate x Volume of Course Aggregate x 1000
= 0.673 x 2.65 x 0.37 x 1000
= 659.88 kg
Cement = 413.33 kg Water = 186 kg
Fine Aggregate = 659.88 kg Coarse Aggregate = 1193.33 kg
Step 8 Calculation for Adjustment of Moisture Content
New Mass of Fine Aggregate
= [Mass of Fine Aggregate in normal condition / 1+(Water Absorption/100)]
= [659.88/1+(1.1/100)]
= 652.70 kg
Extra Water = 659.88-652.70 = 7.18 kg New Mass of Coarse Aggregate
= [Mass of Coarse Aggregate in normal condition / 1+(Water Absorption/100)]
= [1193.33/1+(0.81/100)]
= 1183.74 kg
Extra Water = 1193.33-1183.74 = 9.59 kg New Water Content
= 186+7.18+9.59
= 202.77 kg
Step 9 Mix Proportion Water = 202.77 kg Cement =
413.33 kg
Fine Aggregates = 652.70 kg Coarse Aggregate = 1183.74 kg
Cement = 413.33 / 413.33 = 1
Fine Aggregate = 652.70 / 413.33 = 1.58
Coarse Aggregate = 1183.74 / 413.33 = 2.86 Mix Proportion for M20 concrete is 1:1.58:2.86
-
Casting of Cubes
-
Oiling of Moulds
For casting, all the moulds were cleaned properly. Then oiling of moulds were done. There dimensions were properly checked before casting. Care was taken that
there are no gaps left, where there is any possibility of leakage of slurry. Size of mould is 15cmx15cmx15cm.
-
Weighing of Material
Weight of all the materials is taken according to mix design.
-
Dry Mixing
Measured quantity of course aggregate is spread evenly. Required quantity of cement and fine aggregates are added to the aggregates. Mixing is properly done such that it is thoroughly mixed. On the water tight platform cement and aggregates are mixed thoroughly until a uniform color is obtained.
-
Wet Mixing
Water is added to the mixture according to W/C ratio making sure no water is lost during mixing. Extra care should be taken while adding water to the dry mix. Excessive amount of water may lead to the formation of bleeding in concrete.
-
Casting of Cubes
During the placing of concrete in the mould, concrete is placed in 3 layers and each layer is compacted with tamping bar and tampered for 25 strokes per layer. And the surface is levelled properly and evenly.
-
Removal of cubes
These specimens were kept in steel mould for the 24 hours. After that, these were demolded with care so that no edges were broken. After demolding the specimen by loosening the screws of the steel mould, the cubes were placed in the water.
-
Curing
After demolding, the specimens are placed in water for 7, 14 and 28 days.
-
-
Compressive Testing of Cubes
The compressive strength test of concrete cube gives an idea about compressive strength of concrete against compressive load. By this single test, we can judge whether concreting has been done properly or not. Compressive Strength can be measured using Universal Testing Machine (UTM) or Compressive Testing Machine (CTM). Here we test 9 concrete cubes of Potable water and 9 concrete cubes of industrial treated waste water. Every 3 out of 9 cubes were tested to check 7, 14, and 21day strength. Compressive strength is calculated as ratio of force applied on cubes to the area of concrete cube.
RESULT
Cubes of grade M20 were designed and casted by using potable water and treated industrial waste water from oil company. Total 18 cubes were casted. Out of that 18, nine cubes were casted and cured with potable water and 9 were casted and cured with treated industrial waste water. Each three out of nine were tested on 7, 18 and 28 day to check the compressive strength.
Cubes casted as per mix design desired to achieve target compressive strength as 26.6MPa. Cubes casted with potable water gave average strength of 27.5MPa at 28th day which is more than target mean strength. And cubes which were casted with treated industrial waste water
gave average compressive strength as 23.1Mpa at 28th day which is less than target mean strength but more than characteristic strength.
CONCLUSION
According to BIS, only potable water should be used for concrete to achieve the required strength. But various studies showed that treated waste water from various industries gives the required target strength to the concrete. According to Literature Review, treated waste water from car wash center, dairy, sewage treatment plant, etc. gives the strength more than concrete casted with potable water. This research is done to check whether treated water from oil industry can be use in concrete or not. The concrete casted and cured with potable water gives strength to the concrete which is more than target mean strength. On the other hand, the concrete which is casted and cured with industrial waste water gave strength less than target mean strength but more than characteristic strength.
As results shows strength of concrete cube less than target mean strength but more than characteristic strength then we can say that water used in secondary concreting work can be replaced with treated industrial waste water. Examples of secondary concreting works are PCC, Compoundwalls, etc.
REFERENCES
-
Amir Hossein Askariyeh (2019) Investigating the Possibility of Using Recycled Industrial Wastewater Instead of Potable Water in Concrete Mixture:
-
Vijay H (2017) Reusing Treated Effluents for Making Concrete.
-
Miss. Kirtimala Laxman Narkhede, Mr. F. I. Chavan (2017) Effect of Treated Waste Water on Strength of Concrete.
-
E.W. Gadzama (2015) Study on the Effect of using Sugar Factory Waste Water as a Mixing Water on the Properties of Normal Strength Concrete.
-
R.A. More and S.K. Dubey (2014) Effect of Different Types of Water on Compressive Strength of Concrete.
-
F. Adeyemiand (2014) Experimental Investigations on the effect of sea water on the compressive strength of concrete.
-
Vidhya Lakshmi, Arul Gideon (2014) "Secondary treated waste water in construction".
-
Marka Silvia and T. R. Naik (2010), Sustainable use of resources.
-
Shetty, MS (2005) Concrete Technology Theory & Practice, Published by S. Chand & Company, Ramnagar, New Delhi.
-
IS 10262-2009 Recommended Guidelines for Concrete Mix Design. Bureau of Indian Standards.
-
IS 456-2000 Code of Practice for Plain and Reinforced Concrete. Bureau of Indian Standards.
-
IS 2386-1963 Methods of test for aggregate for concrete.
-
IS 383-1970 Indian Standard specifications for coarse and fine aggregate.
-
IS 10500-1991 Indian Standard specifications for drinking water.
-
IS 4031-1996 Indian Standard specification for method of physical test for hydraulic cement.
-
IS 3025-1984 Indian Standard specification for Methods of sampling and test for water and waste water.
Fig No. 1 – Concrete Cubes
Chart Title
30 1.2
25 1
20 0.8
15 0.6
10 0.4
5 0.2
0 0
Day 7 Day 14 Day 28
Potable Water Industrial Water
Fig No. 2 – Compressive Strength Test