
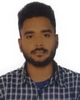
- Open Access
- Authors : Dinesh Bikram Singh , Iswar Man Amatya
- Paper ID : IJERTV10IS090001
- Volume & Issue : Volume 10, Issue 09 (September 2021)
- Published (First Online): 14-09-2021
- ISSN (Online) : 2278-0181
- Publisher Name : IJERT
- License:
This work is licensed under a Creative Commons Attribution 4.0 International License
Treatment Efficiency of Rapid Sand Filters on Intermittent Use
Dinesh Bikram Singp, Iswar Man Amatya1 1Dept. of Civil Engineering, Pulchowk Campus, Institute of Engineering, Tribhuvan University Lalitpur, Nepal
AbstractThe removal efficiency of the rapid sand filter(RSF) situated at Nayabazar, Balaju, Kathmandu, which was used intermittently, was monitored. The experimental set- up included a deep well source, tray aerators, hydraulic flocculator, tube settler, RSF, chlorinator and clear water reservoir. The study included analyzing the removal efficiency and backwashing of the RSF, and also, finding ways to improve the efficiency. The study was conducted at two different discharges 630 l/min and 720 l/min taking three different cycles for each discharge. The effective size of the sand media was 0.3 mm, and the coefficient of uniformity was 2.67. At first, an increase in removal efficiency was observed because of the increment in clogging, which is due to the decrease in pore spaces. And, then, a decrease in removal efficiency was observed mainly due to the cracks formed from drying of the sand media during the offline hours. The maximum head loss of 1.14m was observed for both discharges. The filter run time for discharge 630 l/min and 720 l/min was 26 hours and 24 hours respectively. The backwash duration obtained was 45 minutes and backwashing discharge was obtained as 84 l/min/m2. The longer backwashing duration may be mainly due to the lesser head created by the pump during backwashing. When RSF are used intermittently, a decrease in efficiency may be observed after few hours of run which may be due to the cracks formed during the offline hours as a result of drying of sand media.
KeywordsRapid sand filter; intermittent use; turbidity removal; sand media; drying of sand media
-
INTRODUCTION
-
Background
The concept of water treatment focuses on collecting water from the best available sources and treating it so that the resultant water is of good physical quality, free from unpleasant taste or odour and, free from everything that has a negative health significance. It aims at improving the quality of water. It limits the level of certain quality parameters within the guidelines. Among them, turbidity is considered as one of the major water quality parameters.
On simple terms, turbidity can be understood as the cloudiness or murkiness of a fluid. It is defined as the measure of resistance to the passage of light through it [1]. It makes the water cloudy or opaque which is caused by the presence of suspended particles such as clay, silt, finely divided organic and inorganic matter, soluble coloured organic compounds and microorganisms. Turbidity can provide food and shelter to the disease-causing organisms. So, higher the turbidity, higher is the negative health impact. Turbidity is of major
consideration in public water supply because of three reasons which are aesthetics, filterability and disinfection. It is expressed in parts per million (ppm) or milligram per litre (mg/l) on silica scale. The standard unit of turbidity is the turbidity produced by one milligram of Fullers earth in the form of finely divided silica in one litre of distilled water, is considered as the standard unit of turbidity. The units depend on the process and equipment used for the measurement. Generally, Nephelometer Turbidity Unit (NTU) is used for turbidity measurement. The permissible value for turbidity is 5 NTU for drinking water, but the turbidity up to 10 NTU may be tolerated [1]
Slow sand filters (SSF) were the first effective method devised for the treatment of water contaminated by pathogenic bacteria. However effective in removing the turbidity and pathogens, it has a large land area and filter media requirement which is the reason it was superseded by Rapid sand filters (RSF). RSF quickly gained popularity due to its less land requirement and high filtration rate. Due to the greater effective size and the lesser uniformity coefficient than that of SSF, the void space in the filter media is increased which results in a higher rate of filtration [1]. The filtration rate of the RSF is expected to be 4,000 12,000 litres per hour per square metre of surface [2]. So, in the context of a larger population to distribute and less land availability, RSF is more fitting. Therefore, it will be a subject of interest for years to come.
This study aims at studying the RSF situated at the water treatment plant in Nayabazar, Balaju, Kathmandu. The RSF was operated intermittently. The study mainly intends to analyze the removal efficiency of the RSF. It also includes analyzing of backwash, and looking for possible improvements to improve the efficiency of the RSF.
-
Rapid Sand Filter
It is of two types: gravity type and pressure type. The RSF of gravity types are most commonly used in water treatment systems. The RSF under study is also gravity type filter. . It consists of the following units:
Fig. 1. Typical rapid sand filter
-
Enclosure tank
It is a watertight open rectangular tank which is constructed of stone or masonry or concrete. The depth of the tank is about 2.5-35 m whereas surface area may vary from 10 to 50 m2. Depending on the surface areas, the required number of filter units are provided. The length to width ratio of the tank is generally kept 1.25 to 1.35.
-
Filter media
The filter media consists of sand layers having a thickness of 60 to 75 cm. Its effective size varies from 0.45 to 0.70mm. The uniformity coefficient Cu of sand is in the range of 1.3 to
1.7. Due to the higher value of effective size and lower value of uniformity coefficient than that of SSF, the void space in the filter media is more which results in a higher filtration rate.
-
Base material
Gravel serves as the base material for the support of the sand layer. The gravel bed is 45 to 60 cm thick which is graded and laid in layers. The topmost layer should be of small size gravel and the bottom-most layer should be of bigger size gravel.
-
Underdrainage system
The main purpose of the under drainage system is to collect the filtered water uniformly over the area of the gravel bed and provide uniform distribution of backwash water without disturbing or upsetting the gravel bed and the filter media. The commonly used drainage systems are a perforated pipe system and pipe strainer system.
-
Appurtenances
-
The more important appurtenances are wash water troughs, air compressors and rate control device. Wash water troughs are provided at the upper portion of the filter tank to collect the backwash water as it emerges from the sand and to conduct it to the wash water drain. Air compressor is used to agitate the sand grains during the backwashing of the filter. The rate control device is used to maintain a constant filtration rate. The increase in the filtration rate may cause water to break through the filter material without treatment while the sudden reduction in the rate may release a bubble of gas entrapped in the sand, causing it to make a hole through the
filter bed. Other appurtenances include head loss indicators, meters for measuring the flow rate and so on.
Rapid sand filtration is a purely physical treatment process which can be explained by two physical principles: mechanical straining and physical adsorption [3]. Firstly, Mechanical straining: larger suspended particles get stuck between the sand particles as they pass through the filter media. Secondly, Physical adsorption: smaller particles adhere to the sand particlesdue to the Van der Waals force of attraction. An additional chemical such as a coagulant or flocculant can be added to increase the adhesion process. RSFs are incapable of providing safe drinking water without adequate pre-treatment and final disinfection[3]. Due to this reason, usually, coagulation and flocculation, and chlorination are applied in the water treatment systems.
During the course of filtration, more and more particles get stuck in the filter media which leads to the clogging of the filter and a decrease in the filtering rate of RSF. So, to re- achieve the previous performance of the filter, cleaning should be done. Cleaning is done by backwashing. The flow of water is reversed so that the treated water flows backwards through the filter. During this process, the sand is resuspended and the solid particles are suspended in the surface water. Generally, the air is used for agitation and further aids the cleaning process. The filter is again put back to its original operation when most of the particles are washed out and back flowing water is clear.
RSF are found to perform well when it comes to turbidity removal. A well-operated RSF reduces turbidity to less than 1 NTU and often less than 0.1 NTU [2]. The RSF are also found to be highly effective in colour removal. It brings the colour down below 3 on the cobalt scale [1]. However, RSFs are less effective in bacterial removal. Most literatures suggest that they remove about 80-90% of the initial bacterial load.
The size of sand required for a particular purpose will vary depending on the purpose. To increase the surface area of sand grains in the sand depth of the bed, the finer the suspended particles to be cleaned, the smaller the sand size should be [4]. Due to the greater effective size and the lesser uniformity coefficient than that of SSF, the void space in the filter media is increased which results in a higher rate of filtration [1].
-
-
METHODOLOGY
-
Expeimental Set-up
The source for the water supply is a deep well which is situated near the project area. The major characteristics of the water of the well is observed as electrical conductivity of 932
µs/cm, pH of 7.2, total iron 4.6 mg/l, total ammonia 32 mg/l and total hardness of 264 mg/l as CaCO3.
The different treatments units of the project are as follows:
-
Aerator
The aeration system consists of five number of tray aerators. It is important for the removal of impurities like iron and dissolved gases like ammonia which are present in the source water. During the aeration process, scrubbing action and oxidation takes place. Scrubbing is caused by turbulence created which removes the dissolved gases from water. Oxidation is the process in which the impurities like iron and manganese are oxidized to form precipitates. These precipitates remain suspended in the water and can be removed through other processes in the treatment like filtration.
-
Flocculator
A Baffled type hydraulic mixing flocculator has been used. At the beginning of the flocculator, a separate chamber for the mixing of alum is provided. As the coagulant is added to the water, the colloidal particles are destabilized and they start to aggregate. When the water strikes the baffles, a mixing effect is created which increases the chance of particle collisions and hence, facilitates the aggregation. Also, it holds the bigger flocs in suspension which allows them to grow even bigger. The flocculator is designed for 10 minute detention time.
-
Tube settler
The water from the flocculator is then sent forward for the sedimentation process. For sedimentation, a single unit of tube settler has been provided. The tubes are 50 mm dia High Density Polyethylene (HDPE) pipes. The tubes provide larger effective settling areas due to which the area requirement for the tube settlers are much less than the conventional tanks.
-
Rapid sand filter
The two units of the RSF are provided which receive water from the tube settlers separately. The RSFs are run simultaneously to get the purer water. A set of four valves are provided which can be easily used to get one filter running while the other is undergoing backwashing. The interval between successive backwashing depends on the quantity of floc not settled down in the sedimentation tank. The water for backwashing is pumped from the clear water reservoir. For this purpose a vertical pump of 7.5 HP capacity is used. The under drainage system consists of main fold and laterals of HDPE pipe
.
-
Chlorinator
The water obtained after filtration is disinfected with bleaching powder solution. A chlorine dozer is installed to feed bleaching powder solution from a 200 l capacity solution tank . It is installed in the section of the pipe line from filter to reservoir. The dosing is adjusted based on chlorine demand. The chlorination process is for the pathogen removal, So, after the filtration process all other parameters except the pathogens should be under the desirable range.
-
Clear Water Reservoir
An underground RCC reservoir has been constructed for the storage of the treated water. The shape of the reservoir is circular and its roof is dome shaped. The volume of the reservoir has been worked out on the basis of the water consumption pattern recommended for small towns of Nepal. The capacity of the reservoir is taken as 500 cubic meter with
a radius of 6.6m. The water reserve to be used in case of emergency like firing has not been taken into consideration.
-
-
Test Procedure
The test procedure was followed for each discharge taken in consideration during the experiment.
-
Turbidity measurement
Turbidity was measured in NTU. Turbidity measurement procedure was:
-
First, the instrument was set on and left for stabilization at least for 30 minutes.
-
The instrument was set to zero using distilled water and then it was calibrated up to 100 using standard 100 NTU solution.
-
The cuvette was rinsed with distilled water and again with the sample and then the turbidity of the sample was measured.
-
The zero set and 100 calibration was checked in between the readings.
-
The turbidity values for both influent and effluent were taken several times during the filter run.
-
The filter run time at which the sample was taken was also noted.
-
-
Head loss measurement
The head loss was measured as:
-
A level pipe was fitted at each outlet pipe of the filter.
-
The top of the filter was taken as the datum level.
-
The level of water above the sand media was taken from the datum level. Then, from the same datum level, water level in the level pipe was measured.
-
The difference between the two readings gave the required head loss.
-
The head loss was measured several times during the filter run.
-
The filter run time at which the head loss was measured, was also noted.
-
-
Backwash measurement
-
Different data were taken for the analysis of backwash which are:
-
The head over the crest was noted and discharge was calculated using weir formula
where, CD is coefficient of discharge, B is length of weir and H is the head over the crest.
-
The backwashing duration was also measured.
-
This was done for each filter cycle.
-
-
RESULTS AND DISCUSSIONS
-
Removal Efficiency
From the values of influent and effluent turbidity, efficiency was obtained. The efficiency values was then plotted against the filter run time to which they belonged.
For the discharge of 630 l/min, the plot of removal efficiency against filter run for the filter during three cycles are shown in the figure 3.1, 3.2 and 3.3 below. For all the
cycles, an increase in the removal efficiency during the first 6 to 8 hours was observed. This is because during the course of filtration, deposition of materials take place which decreases the pore sizes available in the media and hence, results in the increment of removal efficiency. The efficiency should increase until the end of the filter cycle but, an decrease in the removal efficiency was obtained which was mainly due to the formation of cracks in the sand media. These cracks provides a passage for the escape of the trapped turbidity which decreases the removal efficiency. The plant was operated intermittently, and during the offline hours, the sand media was subjected to dryness. Also, the effective size (d10) size of the sand was found as 0.3mm which was less than typically expected size 0.45mm to 0.7mm for a rapid sand filter(RSF). So, the presence of finer sands and drying of sand media during the offline hours may be the major reasons for the formation of the cracks. The decrease of removal efficiency in the later stages may also be due to the material breakthrough.
Fig. 4. Removal efficiency against filter run for discharge 630 l/min for cycle 3
For the discharge of 720 l/min, the plot of removal efficiency against filter run for the filter during the three cycles are shown in the figure 3.4, 3.5 and 3.6 below. Similar trend of efficiency as that of the previous discharge was obtained in all the cycles. The peak was obtained at first 4 to 5 hours of the filter run. Also, at this discharge lower efficiency is observed at the end than that of the previous discharge. This is due the greater solid loading at the greater discharge which further enhance the escape of trapped turbidity.
Fig. 2. Removal efficiency against filter run for discharge 630 l/min for cycle 1
Fig. 5. Removal efficiency against filter run for discharge 720 l/min for cycle 1
Fig. 3. Removal efficiency against filter run for discharge 630 l/min for cycle 2
Fig. 6. Removal efficiency against filter run for discharge 720 l/min for cycle 2
Fig. 7. Removal efficiency against filter run for discharge 720 l/min for cycle 3
On sieve analysis, the d10 size obtained was 0.3mm and the coefficient of uniformity Cu was obtained as 2.7. The expected d10 size for the RSF is 0.45mm to 0.7mm and the expected Cu is 1.2 to 1.7. The higher Cu value corresponds to well graded sand media and lesser d10 value means more finer sand at the top layers. So, this tells that the sand media was more compact with lesser pore spaces. This contribute to lesser filtration rate and faster clogging of the sand media.
-
Head Loss
For the discharge of 630 l/min, the plot of head loss against filter run the filter during three cycles is shown in the figure 3.7, 3.8 and 3.9 below. In all the cases, the maximum head loss loss of 1.14m was obtained at 26 hours of filter run.
Fig. 8. Head loss against filter run in hours for for discharge 630 l/min for cycle 1
Fig. 9. Head loss against filter run in hours for for discharge 630 l/min for cycle 2
Fig. 10. Head loss against filter run in hours for for discharge 630 l/min cycle 3
For the discharge of 720 l/min, the plot of head loss against filter run in hours for the filter during three cycles are shown in the figure 3.10, 3.11 and 3.12 below. In all cases, the maximum head loss loss of 1.14m was obtained at 24 hours of filter run. In this discharge, the head loss reached to maximum 2 hours earlier than the previous discharge of 630 l/min as the solid loading will be more for greater discharge.
Fig. 11. Head loss against filter run in hours for for discharge 720 l/min for cycle 1
Fig. 12. Head loss against filter run in hours for for discharge 720 l/min for cycle 2
Fig. 13. Head loss against filter run in hours for for discharge 720 l/min for cycle 3
-
Backwashing
The backwash duration was observed to be 45 minutes. The pump used for backwashing could only create a head of 2.8m which may be the major reason for longer backwashing duration. The backwashing discharge was obtained 84 l/min/m2.
-
-
CONCLUSIONS
When RSF is used intermittently, a decrease in efficiency may be observed after few hours of filter run. The decrease in efficiency may be mainly due to the cracks formed during the offline hours as a result of drying of the sand, which can provide a passage for the escape of the trapped turbidity. The repeated drying and wetting of the sand media during the offline and online hours can further facilitate the cracking of the media. Further studies need to be carried out to properly establish the reasons for the decreasing trend of efficiency. A longer backwashing time was observed which may be due the lesser head created by the pump.
ACKNOWLEDGMENT
My sincere thanks to Kathmandu Upatyaka Khanepani Limited, Chhetrapati Branch, Kathmandu, Nepal for providing me necessary permissions and materials to properly conduct my study.
REFERENCES
-
Kansakar, B. R. (2015). Water Supply Engineering. Prakash Man Shakya
-
WHO. (1996). Fact Sheets on Environmental Sanitation.
-
Bruni, M., & Spuhler, D. (2020). Rapid Sand Filtration. SSWM. Retrieved jan 26, 2020, from https://sswm.info/sswm-university- course/module-6-disaster-situations-planning-and-preparedness/further- resources-0/rapid-sand-filtration
-
Punmia, B.C., Jain, A. K., & Jain, A. K. (1995). Water Supply Engineering. Laxmi Publications.
-
Bruni, M. A., & Spuhler, D. (2020). Slow Sand Filtration. SSWM. Retrieved jan 26, 2020, from https://sswm.info/sswm-university- course/module-6-disaster-situations-planning-and-preparedness/further- resources-0/slow-sand-filtration