
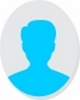
- Open Access
- Authors : Amandeep Singh , Vikas Khandelwal
- Paper ID : IJERTV9IS100053
- Volume & Issue : Volume 09, Issue 10 (October 2020)
- Published (First Online): 13-10-2020
- ISSN (Online) : 2278-0181
- Publisher Name : IJERT
- License:
This work is licensed under a Creative Commons Attribution 4.0 International License
To Study the Effect of Pet Fiber (Polyethylene Terephthalate Fiber) on Geopolymer Concrete by using GBBS and Fly Ash
Amandeep Singh
Student of M.E, Structural Engineering, Chandigarh University, Punjab, India
Er. Vikas Khandelwal
Assistant Professor, Department of Civil Engineering, Chandigarh University, Punjab, India
Abstract:- The demand of utilization of the waste product from the industries is at its peak therefore, several experimental investigations have been carried out to examine their physical and chemical properties when they are used as a replacement material in concrete. In this investigation the fly ash and GGBS were utilized to make the Geopolymer concrete and PET fibers or strands were present in it with various quantities. The fly ash and ggbs based Geopolymer concrete was utilized with equivalent amount (half fly ash and half ggbs) and PET strands were utilized in it (volume division of fine totals/weight level of fine totals) with various rate for example 0%, 2%, 3% and 4% to consider the mechanical properties. The Geopolymer concrete containing PET Fibers were restored with two strategies for example Broiler relieving/Oven curing (24 hours at 600oC) and encompassing restoring/room temperature curing. The PET strands measurements was utilized relating to 45 perspective proportion 90x2mm (length x width). The prepared samples were tested at 7 and 28 days. This study has been done on the fresh property, compressive strength, elasticity/tensile and flexure strength of PET fiber exemplified Geopolymer concrete. The compressive quality improved a step by step with the joining of PET fibers, rigidity and flexural quality tests gave huge improvement over controlled example.
Key words: Geopolymer concrete, fly ash, GGBS, PET fiber.
-
INTRODUCTION
Concrete is the development material that is comprehensively utilized in development industry. Concrete is a man-made material enormous zone utilized for development reason. Concrete is a blend of, coarse total, sand, concrete and water. The solid is legitimate drawn out period previously so. Advantageous mineral admixtures are joined in best quantum by the concrete change an immense property. The utilization of industrial facility squander has upgraded in zone of development of solid production since, it's put at deficiency the ordinary utilization of naturalistic methodology. At, the ongoing past, significant examination considers have been perform to discover all conceivable reusing and use again strategy. Development useless materials that is copper slag, fly ash, steel slag, iron slag and others numerous materials have been conceded at better places in asphalts establishment, roadway, and numerous development fields, ill-equipped item to the erection by conventional Portland concrete.
A few nations are proving the quick amplification to the development processing plant that incorporates the use of inartificial methodology to the advancement of structure. Consequently, locaters develop useless lead strategy to apply for replacement of fine total for select prerequisite. The useless material is utilized in the main secure area of development industry, which decrease the issues of ecological, issues of room and development cost. Utilization of useless materials as a replacement for sand and concrete in concrete characterizes recovery in mechanical characters correlation with common cement and have discovered their use in the various structures.
It very well may be inferred that that the Geopolymer cement might be the material which can be utilized for the development reason and economical material for our development businesses and condition. Geopolymer concrete arranged by utilizing crude material of mechanical waste from warm force plants and steel ventures by the salt enactment of pozzolanic materials. Geopolymer solid wording was first presented by a researcher to be specific Davidovits et al. (1984, 1988,1989, 1994,2005). To deliver Geopolymer solid, we need the materials which have pozzolanic properties, for example, GGBS which is a waste material from steel industry, class c or class f fly debris which is a side-effect from warm force plant and antacid initiated arrangements by the blend of watery arrangements of sodium hydroxide and sodium silicate. The response of polymerization with pozzolanic materials utilizing soluble arrangements prompts a few cycles. The different cycles can be obliteration of covalent bond, disintegration, coagulation, gelation, buildup and redesign which at last outcomes in solidifying and polymerization of Geopolymer concrete by expulsion of overabundance of water from grid. Geopolymer solid outcomes in items which transforms it math from undefined to solidify calculation structure.
-
LITERTAURE REVIEW
Duxson et al., (2007) examined that the utilization of cement is quickly expanding each day as the requirement for cover and financial exercises are expanding, additionally because of the globalization and industrialization more infrastructural offices were created which utilize concrete. It has been perceived that the manufacturing of OPC discharges gigantic amount of energy
and carbon dioxide to the general condition. Along these lines, it is fundamental to locate a substitute folio to create ecological agreeable cement.
Rovnanik (2010) investigated that restoring temperature has a significant impact on solidifying and Geopolymerization of mineral-based Geopolymer. At a mood and higher temperature, the example for all intents and purposes set in the initial 4 hours. Unexpectedly, the setting was additionally delayed for a time of 4 days when the blend was taken care of at temperature of at most 10 °C, yet this doesn't influence the evaluation and properties of cemented Geopolymer item at the age of 28 days. Quickened quality arrangement was seen on rock based Geopolymer restored at 40 to 80°C temperature. It merits referencing that the impact of temperature is depended on term of restoring. Relieving for a shorter period in broiler didn't respect noteworthy changes in quality turn of events, however stretched out restoring cycle to at any rate 20 hours was the caused for an observable quick pace of response rate and brought about early quality picked up.
Vijai et al., (2010) studied the couple of varieties of strands yield more significant impact, scratched spot, and break obstacle in concrete. For essential applications, fiber concrete has various novel inclinations when stood out from the ordinary assistant concrete and recorded as a hard copy it has been represented that may look at bunches have investigated the effect of thought of fibers in concrete involving either 100% bond or fragmented replacement of bond by fly blazing remains. In the current work, an assessment has been had to consider the effect of volume of steel fibers on mechanical properties of Geopolymer concrete orchestrated using 90% fly powder and 10% GGBS under incorporating and warmth soothing conditions.
Hasan et al., (2011) examined that solid in pressure and delicate in strain to beat this difficult strands are utilized in concrete. He took a shot at mechanical conduct of fortified cement with miniature manufactured strands. He arranged four blends: one without any filaments and staying three with three distinctive fiber measurements 0.32, 0.43 and 0.50 percent separately. He projected the solid shapes for the assurance of mechanical conduct, for example, rigidity, stress-strain connections, compressive quality and shear quality. He inferred that a large scale manufactured fiber upgrades the compressive quality fundamentaly. For large scale manufactured filaments at 0.33, 0.42 and 0.51 percent volume parts a definitive shear quality was expanded by in any event 15, 45 and 65 percent separately contrasted with control radiates.
Olivia and Nikraz (2011) dissected that the water penetrability of Geopolymer concrete made with fly debris proportion of
0.36 0.46 exposed to broiler relieving at sixty-degree Celsius temperature for 24 hours. They found that Geopolymer concrete demonstrated lower water porousness esteems (2.454.65 x 10-11 m/s) than the standard cement in view of its denser blend and little between pore connect. They likewise expressed that the most significant limitation influencing the properties of Geopolymer concrete was its water-Geopolymer proportion.
Naidu (2017) analyzed progressed work Class F fly debris and ground granulated impact heater slag (GGBS) are utilized in comparable extents (FA_50-GGBS_50) with basic activator arrangements. Manufactured strands (Polypropylene and Polyester filaments) are utilized at fiber measurement of 0, 0.2, 0.25, 0.3, 0.35 and 0.4 percent individually and different progressed mechanical properties are tentatively contemplated. The greatest compressive quality of Geopolymer concrete for 7 days, 28 days and 90 days relieving period is 35.85 N/mm2, 46.81 N/mm2 and 52.65 N/mm2 individually by incomplete supplanting with ideal level of engineered filaments of 0.3 percent substitution. The most extreme split pliable specialty of Geopolymer concrete for 7days, 28days and 90 days restoring period is 3.27 N/mm2, 4.26 N/mm2 and 4.53 N/mm2 individually by fractional supplanting with ideal level of manufactured filaments of 0.3 percent substitution
-
MATERIALS AND METHODS
Fly Ash:
The fly ash is the residual obtained from the combustion of powered coal and transferred by flue gases and collected by electrostatic precipitation. It has surface area of 0.3-0.70 m2/g. Its particles are finer than cement particle. It is light grey, dark grey in Colour. Fly Ash was obtained from Ropar Thermal Power Plant. The class F fly ash used is this research. It is low calcium based fly ash, calcium content is low in it. The specific gravity of ash is 2.24. The annual production of fly ash in India is 225 million tons.
Table 1 Fly Ash Chemical Composition and its Properties
Particulars |
Class F fly ash |
Silica (SiO2) |
65.67% |
Alumina (Al2O3) |
28.01% |
Iron Oxide (Fe2O3) |
3.01% |
Lime (CaO) |
1% |
Magnesia (MgO) |
1% |
Titanium Oxide (TiO2) |
0.54% |
Sulphur Trioxide (SO3) |
0.21% |
Loss on Ignition |
0.30% |
Physical properties |
|
Specific gravity |
2.25 |
Fineness (m2/Kg) |
360-365 |
GBBS:
GGBS is a waste product obtained from the iron manufacturing plant. It is termed as ground granulated blast furnace slag. GGBS is produced when steel is heating at high temperature and waste is come out after that process and that waste is grind up
and powder is made, that powder is known as GGBS. It was obtained from Ecogen Industries Private Limited, Dehradun. The specific gravity of GGBS is 2.86. It is non-metallic and it is in slag form and powered into small particles that can be replace cement or fly ash. It is rich in calcium silicate and imparts strength to concrete. Now a days GGBS based cement is coming.
Table 2 Chemical Composition and Properties of GGBS
Particulars |
GGBS |
Silica(SiO2) |
30.63% |
Alumina(Al2O3) |
16.25% |
Iron Oxide(Fe2O3) |
0.597% |
Lime(CaO) |
34.49% |
Magnesia(MgO) |
6.80% |
Titanium Oxide (TiO2) |
– |
Sulphur Trioxide (SO3) |
1.89% |
Loss on Ignition |
2.12% |
Physical properties |
|
Specific gravity |
2.89 |
Fineness (m2/Kg) |
402 |
PET Fiber:
PET bottles were acquired from the nearby piece seller, at that point these bottles cut into long ropes. From that point onward, these ropes are cut into an angle proportion of AR45 for example 90mm length and 2mm broadness. The covering of epoxy gum has been done to shield the fiber from the compound assault. The level of PET Fiber's utilized in this examination are 0,2,3,4 percent volume of portion of fine total. (it dependent on past the examination did on concrete based cement).
Properties of polyethylene terephthalate Density:1.37~1.40g/mm3
Melting Point: 215-256oC
FINE AGGREGATE:
It was gotten after strainer of fine total which went through 4.75mm from zone II. The fineness modulus of sand was 2.93 and explicit gravity was 2.68. IS 383-2016 code use for fine totals.
Table 3 Sieve analysis of fine aggregate
Indian standard Sieve Size |
Retained Weight (grams) |
Retained % Weight |
Cumulative% Weight of Retained |
Cumulative % of passing |
4.75 |
95 |
4.75 |
4.75 |
95.25 |
2.36 |
148 |
7.4 |
12.15 |
87.85 |
1.18 |
230 |
11.5 |
23.65 |
76.35 |
600 |
796 |
39.8 |
63.45 |
36.55 |
300 |
543 |
27.15 |
90.6 |
9.4 |
150 |
158 |
7.9 |
98.5 |
1.5 |
Pan |
28 |
1.4 |
— |
— |
Total |
293.1 |
Fineness modulus= 2.9
COARSE AGGREGATE:
It is obtained from a local source. This coarse aggregate used size 20mm and 10mm with specific gravity is 2.54. Aggregates 20mm were used 60% of the total weight of coarse aggregate and 10mm aggregates were used 40% of the total weight of coarse aggregate. IS 383-2016 code use for coarse aggregate.
WATER:
Very less amount of water was used in the Geopolymer concrete. Normal water was used to full fill the demand for solid content present in the alkaline solution. It is according to the amount of solid content present in sodium silicate liquid.
MIXTURE:
As there was no specific code for making the Geopolymer concrete, a study carried out from the past research work and from the IS codes IS 456:2000 and IS 10262:2009 this mix was made.
Table 4 Mixture
% of PET Fiber |
Fly Ash Kg/m3 |
GGBS Kg/m3 |
Fine Aggregate Kg/m3 |
Coarse Aggregate Kg/m3 |
Sodium silicate Kg/m3 |
Sodium hydroxide Kg/m3 |
Extra water Kg/m3 |
Admixture Kg/m3 |
0% |
189 |
189 |
553 |
1293 |
124 |
50 |
15 |
3.78 |
2% |
189 |
189 |
553 |
1293 |
124 |
50 |
15 |
3.78 |
<>3% |
189 |
189 |
553 |
1293 |
124 |
50 |
15 |
3.78 |
4% |
189 |
189 |
553 |
1293 |
124 |
50 |
15 |
3.78 |
CURING:
In this examination work, two sorts of restoring procedures were utilized one is stove dry relieving and other is room temperature restoring. In stove dry relieving example place in the broiler at 600C for 24 hours, after that example place in the room restoring for the 7 days and 28 days testing. In the room temperature relieving examples were not put in the stove, examples were kept in the space for restoring for the 7 days and 28 days relieving. Two unique techniques for relieving were utilized to check the distinction between the stove dry restoring and room temperature relieving. In this sort of relieving no water is required, that is helping us to spare the water. The relieving utilized in the examination appeared in figure 1 and 2.
Figure 1 Room Temperature Curing
Figure 2 Oven Dry Curing
4 RESULTS AND DISCUSSION:
-
Compressive Strength Test:
Compressive strength testing is done under universal testing machine, to determine the strength of the different grade of concrete by casting cubes of size 150x150x150 mm (under over drying curing and room temperature curing). All the test samples were prepared and tested according to code IS 516-1959. The results of the compressive strength show good up to 3% PET fibers adding, after that the results were converted into lower side as shown in graph 5.1(a) and 5.1(b). The overall result shows that the Oven dry curing samples shows good strength as compared to the room temperature cured samples.
Table 5 Results of Compressive Strength Test (Oven Dry Curing)
PERCENTAGE OF PET FIBER
COMPRESSIVE STRENGTH (MPA)
7 Days
28 Days
0%
20.82
30.61
2%
21.58
31.73
3%
24.79
35.58
4%
3.24
32.56
Table 6 Test Results of Compressive Strength Test (Room temp. curing)
PERCENTAGE OF PET FIBER
COMPRESSIVE STRENGTH (MPA)
7 Days
28 Days
0%
18.23
28.68
2%
20.59
30.79
3%
24.38
32.39
4%
22.39
29.71
-
Flexural Strength Test:
The main aim of the Flexural strength test to measure the strength of concrete by casting a beam of size 500x100x100 mm. In this test, the crack width is measured with the ultimate load on the prepared samples. The three beams were casted to calculate the flexural strength with the help of universal testing machine as per code IS 516-1959. The result of Flexural Strength is higher for Geopolymer concrete with PET fiber as compared with the Geopolymer concrete without PET fiber. Strength of Geopolymer concrete increase with the increase in the percentage of PET fiber up to 3%, after that it starts Maximum flexural strength was obtained at 3% PET fiber. curing
Flexural Strength for Oven Dry
8
Flexural strength in Mpa
Flexural strength in Mpa
7
6 7
Days
2
1
0 2 3
Percentage of PET Fiber
7 Days and 28 Days Testing Results
Graph 1 Showing the results of Flexural Strength Test (Oven dry curing)
Flexural Strength for room temp.
7
Flexural strength in Mpa
Flexural strength in Mpa
6
5
5
7
Days
2
1
0 2 3 4
Percentage of PET Fiber
7 Days and 28 Days Testing Results
-
Split Tensile Strength Test:
Graph 2 Showing the results of Flexural Strength Test (Room Temp. curing)
The split tensile test is a type of destructive test in which a sample is destructed to check the strength of the material. The size of the specimen is 150 mm diameter and 300 mm length of the cylinder. The compressive testing machine is used for testing the split tensile strength. All the procedures of this test were performed according to the code IS 5816-1999.
Table 5.3(a) Test Results of Split Tensile Strength Test (Oven Dry Curing)
PERCENTAGE OF PET FIBER
SPLIT TENSILE STRENGTH (MPA)
7 Days
28 Days
0%
2.07
3.31
2%
2.49
3.70
3%
2.98
3.96
4%
2.65
3.50
Table 5.3(b) Test Results of Split Tensile Strength Test (Room Temp. Curing)
PERCENTAGE OF PET FIBER
SPLIT TENSILE STRENGTH (MPA)
7 Days
28 Days
0%
1.31
1.98
2%
1.60
2.33
3%
1.69
2.54
4%
1.54
2.21
-
UPV (Ultrasonic Sonic Pulse Velocity) TEST:
It is a type of non-destructive test and this test helps us to find out the quality of the concrete with the help of ultrasonic sonic pulse velocity machine according to IS 13311(part-1)-1992. Test conducted on cubes after 28 days for 24 samples.
Pulse Velocity in m/sec
Pulse Velocity in m/sec
3900
3800
3700
3600
3500
3400
3300
UPV Test for oven dry Samples
28 Days
3200
0
4
Percentage of PET
28 Days Testing Results
Graph 3 Showing the Result of UPV Test Result (Oven Dry Curing)
Pulse Velocity in m/sec
Pulse Velocity in m/sec
3700
3600
3500
3200
3100
UPV Test for room temp. Samples
28 Days
0 2 3 4
Percentage of PET Fiber
28 Days Testing Results
Graph 4 Showing the Result of UPV Test Result (Room temp. Curing)
5 CONCLUSION:
-
Compressive strength
-
The maximum compressive strength result for Geopolymer concrete with 3% PET fiber for 7 days is 24.79 MPa and 28 days is 35.58 MPa in oven drying curing. On the other hand, the maximum compressive strength result for Geopolymer concrete with 3% PET fiber for 7 days is 24.38 MPa and 28 days is 32.39 MPa with room temperature curing.
-
The strength is maximum for both oven drying curing and room temperature curing with 3% PET fibers.
-
-
Flexural strength
-
The strength of oven drying curing and room temperature curing shows maximum results with 3% PET fibers adding in Geopolymer concrete.
-
The strength values for over drying curing for 7 days is 5.48 MPa and for 28 days is 7.62 MPa. Similarly, the values for room temperature curing for 7 days is 4.20 MPa and for 28 days is 5.93 MPa
-
-
Split tensile strength
-
The split strength of oven drying curing and room temperature curing shows maximum results with 3% PET fibers adding in Geopolymer concrete.
-
The strength values for over drying curing for 7 days is 2.98 MPa and for 28 days is 3.96 MPa. Similarly, the values for rom temperature curing for 7 days is 1.70 MPa and for 28 days is 2.54 MPa
-
-
UPV (Ultrasonic Sonic Pulse Velocity)
-
In UPV test, the maximum velocity value shows for over drying curing is 3850 m/s, the values for room temperature curing is 3630 m/s.
-
The maximum values show by adding 3% percent PET fibers.
-
REFERENCES
-
Albitar, M., "Assessing behaviour of fresh and hardened geopolymer concrete mixed with Class-F fly ash." KSCE Journal of Civil Engineering 19.5 (2015): 1445-1455.
-
Bandodkar, L. R., et al. "Pulverised PET bottles as partial replacement for sand." International Journal of Earth Sciences and Engineering 1009 (2011): 1009-1012.
-
Chowdhury, Swaptik, Aastha Tashkant Maniar, and Om Suganya. "Polyethylene terephthalate (PET) waste as building solution." Int. J. Chem. Environ. Biol. Sci.(IJCEBS) 1.2 (2013): 308-312.
-
Dai, Jian-Guo, Lik Lam, and Tamon Ueda. "Seismic retrofit of square RC columns with polyethylene terephthalate (PET) fibre reinforced polymer composites." Construction and Building Materials 27.1 (2012): 206-217.
-
Duxson, Peter, et al. "Geopolymer technology: the current state of the art." Journal of materials science 42.9 (2007): 2917-2933.
-
Fataniya R.,2015, Experimental investigation of concrete masonry unit with plastic bottle core & PET fiber. International Journal for Scientific Research & Development (IJSRD), Volume 3(04), ISSN :2321-0613.
-
Hardjito, Djwantoro, and B. Vijaya Rangan. "Development and properties of low-calcium fly ash-based geopolymer concrete." (2005). ACI Materials Journal, Title no. 101-M52.
-
Hasan, M. J., M. Afroz, and H. M. I. Mahmud. "An experimental investigation on mechanical behavior of macro synthetic fiber reinforced concrete." International Journal of Civil and Environmental Engineering 11.3 (2011): 18-23.
-
Hirde, Suchita, and Pravin Gorse. "Effect of Addition of Ground Granulated Blast Furnace Slag (GGBS) on Mechanical Properties of Fiber Reinforced Concrete." (2015).
-
IS 10262 (2009). Guidelines of mix proportioning. Bureau of Indian Standards, New Delhi.
-
IS 12089 (1987). Specifications for granulated slag for manufacture of Portland slag cement. Bureau of Indian Standards, New Delhi.
-
IS 13311 Part 1(1992). Guidelines for Ultrasonic Pulse Velocity. Bureau of Indian, New Delhi. IS 3812 (1981). Specifications for fly ash for use as pozzolanic and admixture. Bureau of Indian Standards, New Delhi.
-
IS 383(2016). Specification of fine and coarse aggregate. Bureau of Indian Standards, New Delhi.
-
IS 456 (2000). Plain and reinforced concrete code for practice. Bureau of Indian Standards, New Delhi.
-
IS 516 (1959). Guidelines of Compressive Strength and Flexural Strength. Bureau of Indian Standards, New Delhi.
-
IS 5816 (1999). Guidelines of Split Tensile strength. Bureau of Indian Standards, New Delhi.
-
Memon, Fareed Ahmed, et al. "Effect of sodium hydroxide concentration on fresh properties and compressive strength of self-compacting geopolymer concrete." Journal of Engineering Science and Technology 8.1 (2013): 44-56.
-
Nath, Pradip, and Prabir Kumar Sarker. "Use of OPC to improve setting and early strength properties of low calcium fly ash geopolymer concrete cured at room temperature." Cement and Concrete Composites 55 (2015): 205-214.
-
Olivia, Monita, and Hamid Nikraz. "Strength and Water Penetrability of Fly Ash Geopolymer Conrete." Journal of Engineering and Applied Sciences 6.7 (2011): 70-78.
-
Patankar, Subhash V., S. S. Jamkar, and Y. M. Ghugal. "Effect of sodium hydroxide on flow and strength of fly ash based geopolymer mortar." Journal of structural Engineering 39.1 (2012): 7-12.
-
Ramujee, Kolli. "Development of Low Calcium Fly Ash Based Geopolymer Concrete." International Journal of Engineering and Technology 6.1 (2014): 1.
-
RovnanÃk, Pavel. "Effect of curing temperature on the development of hard structure of metakaolin-based geopolymer." Construction and building materials 24.7 (2010): 1176-1183.
-
Singh, B., "Geopolymer concrete: A review of some recent developments." Construction and building materials 85 (2015): 78-90.
-
Vijai, K., R. Kumutha, and B. G. Vishnuram. "Effect of types of curing on strength of geopolymer concrete." International journal of physical sciences 5.9 (2010): 1419-1423.
-
Vora, Prakash R., and Urmil V. Dave. "Parametric studies on compressive strength of geopolymer concrete." Procedia Engineering 51 (2013): 210-219.