
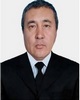
- Open Access
- Authors : Khaidarov Khabibullo Hamidullaevich, Ismailov Nurulla Tuychiboevich
- Paper ID : IJERTV9IS020259
- Volume & Issue : Volume 09, Issue 02 (February 2020)
- Published (First Online): 16-03-2020
- ISSN (Online) : 2278-0181
- Publisher Name : IJERT
- License:
This work is licensed under a Creative Commons Attribution 4.0 International License
The Effect of Torsion on the Mechanical Properties of Reinforced Yarn
Ismailov Nurulla Tuychiboevich
Senior Lecturer, Department:
"Higher Mathematics" Namangan Engineering Technology Institute, (Namiti), Republic of Uzbekistan. Namangan City
. . . – . .
Abstract.The article presents the results of a study of the properties of curved fibrous waste. Standards determined the availability of fibers of acceptable length for the production of yarn from used fibers. Cleaning options are available depending on the type of waste in different plants. A spinning plan is developed and the test results of the physicomechanical properties of yarn samples are analyzed. The possibility of obtaining medium-density yarn with attachment in a mixture of spins of the group directly under conditions of maximum purification and high uniformity of mixing of the components is shown.
: , , , , , – .
Keywords: yarn, spinning, linear density, quality, spinning method, rotor spinning machine.
At present, improving the quality of textile products, in particular yarn from the same raw materials, is an urgent task to help increase the export opportunities of relevant market demand products. The production of high- quality competitive products in the world market, based on the use of new, more advanced technologies, is the most important task of the textile industry. The quality of textile products depends largely on the uniformity, purity and strength of the yarn. Improving the quality of textile products can be achieved through the introduction and use of modern equipment based on advanced technological principles [1 … 9].
The efficiency of spinning production largely depends on the rational use of raw materials, which to a greater extent affects the cost of yarn. The release of fibrous waste from textile fiber processing is known in spinning machines and engravers. Direct waste is of great importance among them, since it allows to save high- quality fiber and reduce the cost of production [1 … 9].
In production conditions, to produce [8] fabric, reinforced yarn was used as weft, and linear density 25 tex yarn was used as the main threads.
Table 1. Physics mechanical indicators of harsh tissue are given
Linear density, in T-text |
Width fabrics cm |
Density per 10cm .. |
Gap load in kg |
Elongation AT % |
Elongation AT% |
Fabric weight In g |
|||||
The basis |
weft |
The basis |
weft |
The basis |
weft |
The basis |
weft |
The basis |
weft |
||
69 |
107,6 |
260 |
159 |
50 |
71 |
13 |
20 |
6,1 |
8,2 |
210,6 |
195,2 |
108,6 |
260 |
161 |
51 |
78 |
13 |
22 |
7,0 |
7,4 |
208,7 |
192,8 |
|
/ |
108,7 |
256 |
161 |
49 |
68 |
13 |
21 |
5,2 |
8,2 |
210,3 |
193,5 |
/ |
105,9 |
264 |
159 |
50 |
66 |
10 |
18 |
4,3 |
7,4 |
167,7 |
158,3 |
The table shows that the properties of the harsh fabrics of I twisted yarn meet the requirements of GOST, and the properties of the fabric fabric from reinforced yarn are higher than these requirements.
For an hour, the breakage of the yarn on the looms was checked. There are 10 cliffs in the reinforced yarn of all: 6 of them are in the base, and 4 in the duck; and in twisted yarn there are only 15 clippings: 7 at the base of 8 in the duck. The productivity of looms is 3.54 m / hour of twisted yarn 3.01 m / hour.
From the indicators it is seen that the use of reinforced yarn increases the quality indicators of the fabric.
The prepared harsh fabrics were rewound onto a roll, and the LBOX FIRM "Kyoto" bleaching machines were filled with E, where they bleached, steamed, washed and dried the fabric. We checked the capillarity and whiteness of the fabric leaving the machine.
Table 1. Results are shown.
Fabrics |
Capillarity, in mm. |
White, in% |
HB-50 VIS-50 |
72 |
78 |
HB-50 PF-50 |
70 |
74 |
US-33.333 PF-33.333 VIS-33,333 |
72 |
85 |
HB -67 VIS-33 |
64 |
71 |
According to the technical conditions |
60-70 |
70-78 |
The table shows that laboratory tests for all samples meet the requirements of technical conditions, and capillarity is higher than standard.
To improve the properties of the tissue, it was emulsified using an emulsifying unit.
After emulsification, tissue samples are refueled on pile machines. Samples of three variants of the fabric obtained from reinforced yarn gave a satisfactory result in
the yield of nap even at one transition, and the serial fabric was released repeatedly, because in the first combing, the pile of fabric came out unsatisfactorily. If you change the parameters of the machines, the material will deteriorate.
For the prepared materials shown in Figure N
-
prepared the following ink composition in the printing shop in table 3
Table 3. It is proposed that the following ink composition is prepared in the print shop.
1
Black reagent
2/1
16 kg
2
Active yellow
2/1
12 kg
3
Cybecron a Olive
2/1
16 kg
4
Zeron Ali
2/1
16 kg
Samples of the fabrics obtained from the printing shop are shown in Fig. 1., 2., 3., 4.
Figure 3. Finished fabric from reinforced yarn, cholopolysphere waste.
Figure 1. Finished fabric from reinforced cotton viscose waste
Figure 2. Finished fabric from reinforced yarn of cotton-polyester waste.
Figure 4. Finished fabric from twisted yarn of cotton viscose fibers in production
Table 3. Physico – mechanical propertes of finished fabrics are given
Sample Average
Shrinkage
Width Vs., with edges
Massa v1m2
The number of threads per 100 mm
Bursting load strips 50×200
Elongation at break
by basis of
by duck
by basis of
by duck
by basis of
by duck
by basis of
by duck
COTTON AND VISCOSE WASTE
86,7
207,1
320
158 54 41 14
42
5,5
4,6
86,5
225
332
152 59 60 II
48
6,0
4,0
COTTON – VISCOSE AND POLYESTER WASTE
85,0
214,8
331
157 55 41 12
47
5,0
4,0
COTTON VISCOSE FIBERS IN PRODUCTION
91,6
163,5
308
158 44 32 10
30
4,7
3,1
From the table it is visible that the physicomechanical properties of the prepared fabric from reinforced yarn are inferior to the series of it.
CONCLUSIONS
-
In order to study the consumer properties of yarn in Namangan A.O. Shoyi made fabric samples of HB / VIS, HB / PF, HB / VIS / PF.
-
Studies of the physical and mechanical properties of harsh and finished fabrics showed that the fabrics meet the requirements of the standard and even surpass these requirements in some indicators.
-
The economic effect of the introduction of cotton-yarn and their products i.e. fabric will be 154965, 5871 yew. total 1998 prices by reducing the cost of raw materials, increasing
-
LISTOFREFERENCES.
-
.., .., .., . : – , 1987.-300 ( – ).
-
.., .. . :,1987.159-160
-
62-238 30 , D 01 7/02. / . . 4.04.86, N 60-126598,.19.10.87.
-
.., .. ., .. , , .. , . –
-
.. . .-19 3.
-
. ., .. . «»5(134),1,2020.58
-
Kh. Kh. Khaidarov, N. T. Ismailov Effect of torsion on the mechanical properties of reinforced yarn. International Journal of Engineering Research and Technology (IJERT) Volume 9 Issue 02, February 2020. 860-862 p
-
. . , . , . «Universum: » 3 (72).2020.12 .
LISTOFREFERENCES.
[1]. Polyakova D.A., Ermilov G.A., Drozdov N.A., et al. Rotary method of spinning and reinforcing M: Legprom-bytizdat, 1987.-300s (Course to accelerate scientific and technological progress). [2]. Polyakova D.A., Drozdov N.A. and other Rotary method of spinning and reinforcing M: Legprombytizdat, 1987. From 159- 160 [3]. Application 62-238830 Japan, MKI D 01 H 7/02. Device for manufacturing reinforced yarn / Shinoko Matsu no. Claim 4.04.86, N 60-126598, publ. 10.19.87. [4]. Grekova S.V., D.A. Polyakova., N.A. Drozdov Central Scientific Research Institute of Chemical Biology, Moscow, L.V. Kartisheva VNIITT, Yaroslavl. Rotary reinforcement technology is one of ways to save natural fiber. Textile industry. Moscow. 1990, pp. 40-42. [5]. Pat. 4899529 USA, MKI D 01 H 13/16, D 01 G 15/00. A methodof manufacturing a reinforced yarn. Fumio Tanay. Declared 12.12.88 283308, publ. 02/13/90
[6]. Bezin P.V. Optimization of the technology for the production of reinforced yarn on a ring spinning machine. The dissertation for the degree of candidate of technical sciences. St. Petersburg 1993. . . 1990,.40-42.
5. .489 529 A, D 01 13/16, D 01 G 15/0 .
. / . .12.12.8
[7]. [8].H. Kh. Khaidarov, N.T. Ismoilov The expediency of using
reinforcing yarn for the disposal of fibrous waste. Journal of the Internauka No. 5 (134), Part 1, 2020. 58 s
Kh. Kh. Khaidarov, N. T. Ismailov Effect of torsion on the mechanical properties of reinforced yarn. International Journal of Engineering Research and Technology (IJERT) Volume 9 Issue 02, February 2020. 860-862 p
283 08,.13.02.90
[9]. N. T. Ismoilov, H. Kh. Khaidarov, Choice of twist parameters for reinforced yarn. Journal Universum: Technical Sciences No. 3 (72) .2020.12 p.