
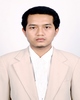
- Open Access
- Authors : Mirza Pramudia, Rifky Maulana Yusron
- Paper ID : IJERTV10IS100185
- Volume & Issue : Volume 10, Issue 10 (October 2021)
- Published (First Online): 23-11-2021
- ISSN (Online) : 2278-0181
- Publisher Name : IJERT
- License:
This work is licensed under a Creative Commons Attribution 4.0 International License
The Effect of Alkalization on Mechanical Behavior of Sugarcane Bagasse Fiber Reinforced Polymer Matrix Composites
Mirza Pramudia1
1 Department of Mechanical Engineering, University of Trunojoyo Madura, Indonesia
Rifky Maulana Yusron2
2 Department of Mechanical Engineering, University of Trunojoyo Madura, Indonesia
Abstract In this study was carried out on the use of sugarcane fiber waste as reinforcement on polymer composites with polyester matrix. The purpose of this study was to determine the value of tensile strength, sugarcane / polyester fiber composites and see the effect of the fiber alkalization process on mechanical properties. The research using variation of alkalization duration 0.5 hours, 1 hour, 1.5 hours and 2 hours. The alkalization process is expected to increase the bond between the automatic and the fiber which in turn can increase the tensile strength of the composite. Mechanical testing is carried out with a tensile testing machine and using the ASTM D 638 test standard. Tensile test results show that for the duration of the alkalization process 0.5 hours, 1 hour, 1.5 hours, and 2 hours produces tensile strength of 10 Mpa, 16 Mpa, 18 Mpa, and 15 MPa. This shows that the 5% NaOH treatment for
-
hours is the most effective treatment for increasing the strength of sugarcane fiber reinforced composites. In composites that are reinforced with fibers without treatment, the bond (mechanical bonding) between the fiber and the polyester matrix becomes imperfect because it is blocked by the presence of a waxy / lignin coating on the surface of the fiber.
Keywords Sugarcane Bagasse, tensile strength, alkalization
-
INTRODUCTION
-
The use of composite materials in the field of engineering is growing. This is due to the superior composite properties compared to other conventional materials that is; lightweight, has good mechanical properties, durable, corrosion resistant, easily fabricated and relatively inexpensive manufacturing costs. Along with the rapid development of plastic technology since the 1990s, polymer composite technology has also experienced growth with growth reaching around 3.8% per year. Even in the past decade, the trend in the development of composite materials has shifted to the reuse of natural fibers instead of synthetic fibers. This is supported by several advantages possessed by natural fibers which are elastic, strong, low density, renewable, the production process requires low energy and is environmentally friendly, and has properties as a good heat and acoustic insulator. The reuse of natural fibers was also triggered by regulations regarding the consumable requirements of automotive component products for European Union countries and parts of Asia. Since 2006, European Union countries have recycled 80% of automotive components, and will increase to 85% in 2015 [1,2]. In Asia especially Japan, around 88% of automotive components have been recycled in 2005 and will increase in 2015 to 95%. Advances in science and technology in the industry have
driven an increase in demand for composite materials. The development of science and technology in the industry began to complicate conventional materials such as metals to meet the needs of new applications. The aircraft manufacturing industry, shipping, car and transportation industry are examples of industries that are currently applying materials that have low density, rust resistant, strong, resistant to wear and fatigue as well as economical as industrial raw materials [3,4].
This encourages the development of composite material manufacturing technology to develop more rapidly to respond to market demand, especially the demand for the fabrication industry. Thought and research on the combination of chemicals or structural elements with various objectives has been carried out. In Indonesia, the research and development of science and technology in the field of manufacturing various kinds of composite materials to meet various purposes / needs has been widely carried out both from education and industry. This research is reasonable due to the availability of abundant reinforcement raw material from organic composite reinforcing fibers (bamboo fiber, pineapple fiber, sugar cane fiber, banana fiber, and palm fiber) as well as inorganic reinforcing fibers and the need / demand of processed composite material which is quite high in market [5,6].
After the discovery of various kinds of synthetic fibers made chemically, scientists are now competing to switch to doing research on natural fibers. Scientists began to research natural properties and carry out mechanical tests on existing natural fibers [7]. The study was conducted after the known weaknesses in synthetic fibers, including; the price is relatively expensive, can not be degredated naturally, poisonous and limited in number. Therefore, scientists are trying to research and find natural fiber substitutes for synthetic fibers that have properties, among others; easy to obtain, naturally decomposed, cheap and non-toxic, but has the mechanical strength or better than synthetic fibers. One of the many natural fibers found in Indonesia is baggase. Post- harvest activities and processing of agricultural / plantation products, including the use of by products and the rest of the processing is still less than optimal [8,9]. In the sugar cane processing industry into sugar, the amount of bagasse produced can reach 90% of each cane processed. So far, the utilization of sugarcane bagasse as raw material for making particle board, boiler fuel, organic fertilizer and animal feed is limited and has low economic value. Utilization of sugarcane bagasse as a reinforcing material for composite
materials will have a very important meaning in terms of utilization of industrial waste, especially the sugar manufacturing industry in Indonesia, which has not been optimized in terms of economics and utilization of its processed products [10].
Sugarcane bagasse is a waste from the sugar processing that has not been used optimally. Based on data from the Indonesian Sugar Plantation Research Center (P3GI) bagasse produced 32% of the weight of ground sugar cane [11]. As much as 60% of the sugarcane bagasse is used by sugar factories as fuel, raw material for paper, raw material for brake canvas, mushroom industry and others. So that it is estimated as much as 40% of the sugarcane bagasse has not been utilized. Utilization of sugar cane fiber as a composite material reinforcement has not been maximized. So far, sugarcane bagasse is only used as a substitute fuel for firewood. Judging from the potential availability of raw materials, this research is directed at utilizing sugarcane fiber from sugarcane bagasse as a reinforcing fiber for composite materials [12]. Utilization of sugarcane bagasse as a reinforcing fiber for composite materials will have a very important meaning in terms of utilization of sugarcane plantation waste in Indonesia that has not been optimized in terms of economics and utilization of processed products.
This study aims to determine the effect of NaOH alkalization time on tensile strength and bending strength of sugarcane fiber composite materials using a polymer matrix.
-
RESEARCH METHODS
-
Raw Material Preparation
This process involves the preparation of sugarcane fiber which will be used as the main ingredient and equipment needed in the process of making biocomposites. Bagasse fiber is first separated from the bagasse skin manually and then cleaned with distilled water with the aim to prevent sugarcane fiber from impurities.The results of the process are then dried up to a maximum of 10% sugarcane fiber moisture content. This study uses an polymer type Unsaturated Polyester Resin with the trademark YUKALAC 157 BQTN- EX. In this study, the fiber making process was performed manually. Hammers, scissors, and cutters were used in separating fibers from bamboo sticks. Fiber obtained on average was obtained with a diameter of 0.7 mm. Fiber separation is indeed quite easy, but to obtain good fiber, it requires sufficient precision so that it is separated one by one.
-
Alkalization
Alkalization process is carried out using a chemical solution of NaOH with a purity level of 98%. Before the alkalization process is carried out, the NaOH solution is mixed with pure distillation water until the concentration of the solution drops to 5%. Furthermore, sugar cane fiber is soaked in 5% NaOH solution in a period of soaking for 0.5, 1, 1.5, and 2 hours. Sugarcane fiber that has been through the alkalization process is carried out the cleaning process using distilled water and drying in the drying furnace until the water content in the sugarcane fiber ranges from 3-5%.
-
Composite manufacturing process
Sugarcane fiber reinforced composite specimen with polyester was made using the vacuum infusion method shown in Figure 1.
Figure 1. Vacuum infusion process
Vacuum Infusion is a method of making composite materials by using an impermeable vacuum to press a laminate from the matrix, fibers and other layers of the mold until the layers are integrated as a composite material. The working principle of vacuum infusion is to utilize atmospheric pressure as a pressure tool. The next process is making composite which molded according to ASTM standard tensile and bending tests as shown in the following figure 2:
(a)
(b)
Figure 2. (a) Tensile test specimen size based on ASTM D638-03
(b) Flexure test specimen size based on ASTM D7264
2.3. Tensile Test
Tensile testing is carried out to determine the magnitude of the tensile strength of the composite material. Testing is done using a Universal Testing Machine type tensile testing machine. The loading process in the tensile test is carried out axially or parallel to the direction of the sugarcane fiber until the main data in the form of yield stress and ultimate tensile stress are obtained. Tensile testing on composite specimens is carried out using the SHIMADZU brand tensile testing instrument.
-
-
RESULT AND DISCUSSION
-
NaOH soaking effect analysis of sugarcane fiber with polyester matrix composite toward composite tensile strength.
The results of tensile test of sugarcane fiber composite specimens reinforced with polyester resin are shown in Figure 3.
Figure 3. Tensile test results of sugarcane fiber reinforced composite polyester specimens
Tensile test results showed that the alkalization process duration of 0.5 hours, 1 hour, and 1.5 hours experienced an increase in tensile strength of 10 MPa, 16 MPa, and 18 MPa, then in the alkalization process for 2 hours, the composite tensile strength dropped to 15 MPa. . Sugarcane fiber composites have the highest tensile strength at 5% NaOH fiber treatment for 1.5 hours, as shown in Figure 3. This shows that the 5% NaOH treatment is the most effective treatment to increase the strength of sugarcane fiber reinforced composites. In composites that are reinforced with fibers without treatment, the bond (mechanical bonding) between the fiber and the polyester matrix becomes imperfect because it is blocked by the presence of waxy / lignin-like layers on the surface of the fiber. NaOH treatment aims to dissolve wax-like layers on the surface of fibers, such as lignin, hemicellulose, and other impurities. With the loss of this waxy layer, the bond between the fiber and the matrix becomes stronger, so the tensile strength of the composite becomes higher. However, prolonged NaOH treatment can cause damage to the cellulose element. In fact, cellulose itself as the main element supporting the strength of fiber. As a result, fibers that are subjected to alkali treatment for too long experience significant strength degradation. As a result, sugarcane fiber reinforced composites with longer duration of alkali treatments have lower strength.
The stress of sugarcane fiber reinforced composite materials also shows the optimization of the treatment of 5% NaOH fiber. Figure 3. shows that NaOH treatment for 1.5 hours is the most optimum treatment. In cane fiber reinforced composites without treatment, failure is dominated by loose bonds between the fiber and the matrix caused by shear stresses on the fiber surface. The failure is dominated by the release of fiber and matrix ties. This type of failure is often referred to as "fiber pull out". In this failure condition, the matrix and fiber are actually still able to withstand a greater load and stretch. However, because the bond between the fiber and the matrix failed, the composite also failed earlier. The amount of strain and stress when it fails also becomes lower. By giving fiber NaOH treatment, the bond between the fiber and the matrix becomes stronger so that failure can occur together. The amount of stress and strain that occurs will increase. Based on the description above, if the NaOH treatment takes too long then the fiber experiences a strength degradation.
-
NaOH soaking effect analysis of sugarcane fiber with polyester matrix composite toward composite flexure strength
The results of bending test on sugarcane fiber composites are presented in Figure 4. Analysis of the effect of alkali fiber treatment on the bending strength of sugarcane fiber reinforced composites with a polyester matrix.
Figure 4. Bending test results of sugar cane fiber reinforced composite polymer polyester specimens
The highest bending stress occurs in composites with alkali treatment for 2 hours is 84.28 MPa, while the lowest bending stress occurs in composites with 0.5 hour alkaline treatment at 49.72 MPa. The longer the alkali treatment of the fiber, the more fiber is eroded by the alkaline solution. The erosion of the fiber by an alkaline solution will cause the degradation of the strength of the fiber to hold the received force. The bending stress of sugarcane fiber reinforced reinforced wastes decreases with the length of immersion of the fiber in 5% NaOH alkaline solution. Fiber degradation due to alkali treatment causes a reduced ability to stretch the fiber, so the bending stress decreases.
-
-
CONCLUSION
Based on research data, it can be concluded that sugarcane fiber composites have the highest tensile strength at 5% NaOH treatment for 1.5 hours. This shows that the 5% NaOH treatment for 1.5 hours is the most effective treatment to increase the strength of sugarcane fiber reinforced composites. The highest bending stress occurs in composites with alkali treatment for 2 hours is 84.28 MPa, while the lowest bending stress occurs in composites with 0.5 hour alkaline treatment at 49.72 MPa. The longer the alkali treatment of the fiber, causes the fiber is increasingly eroded by an alkaline solution so as to allow the erosion of cellulose
/ lignin in the fiber, so that the bond between the matrix and fiber will become stronger.
-
REFERENCES
-
Anggono, et all. 2016. The Use of Sugarcane Bagasse in PP Matrix Composites: A Comparative Study of Bagasse Treatment Using Calcium Hydroxide and Sodium Hydroxide on Composite Strength. AIP Conference Proceedings.
-
Autar, K. Kaw. 2006. Mechanics of Composite Materials, University of South Florida.
-
Cao Y., Shibata S., Fokumoto I. (2016). Mechanical properties of biodegradable composites reinforced with bagasse fiber before and
after alkali treatment. Composites Part A, Applied Science and Manufacturing 37 (2016) 423429
-
Cerqueira, et all., 2011. Mechanical Behaviour of polypropylene reinforced Sugarcne Bagasse Fiber Composites. Procedia Engineering.
-
Dhibar, B. 2018. Sugarcane Bagasse Reinforced Polyester Composites. International Research Journal of Engineering and Technology (IRJET) : Vol 5. Issue 5. ISSN : 2395-0056.
-
Gibson, 1994. Principle Of Composite Material Mechanics. New York
: Mc Graw Hill,Inc.
-
Groover. Mikell P. 2010. Modern Manufacturing Materials, Process, and System. America: John Willey and Sons, Inc.
-
Kanagaraj, S, Fatimah R Varanda, Tatiana V Zhiltsova, Monica S.A Oliveira dan Jose A.O Simoes. 2010. Mechanical Properties of High Density Polyethylene/Carbon Nanotube Composites. Portugal. Journal of Composites Science and Technology Vol. 67, No. 15:3072-3074
-
Kaw, Autar K. 2010. Mechanics of Composites Material 3rd edition.
New York: Taylor and Francis
-
Tewari, M, et all. 2012. Evaluation of Mechanical Properties of Bagasse- Glass Fiber Reinforced Composite. Journal of Material Science 3 (1) (2012) 171-184 , ISSN : 2028-2508.
-
Kanagaraj, S, Fatimah R Varanda, Tatiana V Zhiltsova, Monica S.A Oliveira dan Jose A.O Simoes. 2010. Mechanical Properties of High Density Polyethylene/Carbon Nanotube Composites. Portugal. Journal of Composites Science and Technology Vol. 67, No. 15:3072-3074
-
Martin, J. Puls, et.al. (2011). Effect of Glycerol Preatreatment On Component Recovery and Enzymatic Hydrolysis of Sugarcane Bagasse, Cellulose Chemistry and Technology, 45, 487-494.
-
S.N. Monteiro, R.J.S. Rodriquez, M.V. De Souza, J.R.M. D'Almeida. (2015). Sugar Cane Bagasse Waste as Reinforcement in Low Cost Composites, Advanced Performance Material, 5(3), 183-191.
-
S. Shibata, et.al. (2015). Effect of Bagasse Fiber On The Flexural Properties of Biodegradable Composites, Journal of Polymer Composite, 26, 689-694
-
Schwardz M.M . 1984. Composite Material Handbook, Singapore : Mc Graw hill.
-
Kalpakijan, Serope. Schmid, Steven R. 2001. Manufacturing Engineering and Technology 4th Edition. New Jersey : Prentice Hall. Inc.
-
Mathew, F. L, and R. D. Rawlings. 1994. Composite Materials : Engineering and Science. London : Chapman & Hall.
-
Verma, et.all. (2012). Bagasse Fiber Composite-A Review. J. Mater. Environ. Sci. 3 (6) (2012) 1079-1092. ISSN ; 2028-2508.
-
Shinichi Shibata, Yong Cao, Isao Fukumoto. (2015). Effect of bagasse fiber on the flexural properties of biodegradable composites, Journal of polymer composite, 26 (2015) 689-694.
-
ASTM D7205/ D7205M-06. 2016. Standard Test Method for Tensile Properties of Fiber Reinforced Polymer Matrix Composite Bars. ASTM International.
-
Callister, William D. 2011. Materials Science and Engineering an Introduction 8th edition. USA: University of Utah.