
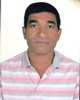
- Open Access
- Authors : Suresh Kumar Meena , Sanjeet Singh
- Paper ID : IJERTV12IS010070
- Volume & Issue : Volume 12, Issue 01 (January 2023)
- Published (First Online): 27-01-2023
- ISSN (Online) : 2278-0181
- Publisher Name : IJERT
- License:
This work is licensed under a Creative Commons Attribution 4.0 International License
Synthesis and Characterization of N-(4-Nitrophenyl) Maleimide and Copolymerized with Cinnemic Acid
Suresh Kumar Meena1 and Sanjeet singp Department of Chemistry Government college , Kota, Rajasthan
Abstract- Copolymers containing N-(4-Nitro phenyl) maleimide (PNPMI) and Cinnemic Acid copolymerization under the identical conditions and different compositions have been prepared by radical copolymerization with different mole ratios. The free-radical-initiated copolymerization of PNPMI with Cinnemic acid carried out in THF and DMF solvent using free radical initiator as AIBN and BPO. Percentage yield were calculated at different time and different solvent variations. The monomers and copolymers were characterized by FTIR, 1H-NMR spectral studies. The copolymer compositions were evaluated by nitrogen content in polymers. The molecular weights (Mw and Mn) and Polydispersity index of the polymers were determined by using gel permeation chromatography. Thermogravimetric analysis of the polymers reveals that the thermal stability of the copolymers increases with an increase in the mole fraction of Structure in the copolymers. Thermal stability of polymer was determined by the TGA techniques. Shape of the polymer in given solution were determined by the Kuhan mark Sakwada Equations . Polymerization process observed by the Polydispersity index. Intrinsic viscosity determined by the using Ubbelohde viscometer. Solubility of the Homopolymer and copolymer determined in different solvent.
Keywords-Polymerization, TGA, AIBN, BPO, DMF
-
INTRODUCTION
Design and synthesis of materials with novel properties is becoming an interestingly important aspect of polymer chemistry. Synthesis of polymers with controlled molecular architecture has been discussed due to the rising demands for the specialty polymers. Living polymerization is an essential technique for synthesizing polymers with controlled structure (narrow molecular weight distributions and controlled molecular weight). Living polymerization has largely been achieved using living anionic and group transfer .In today's time, it has been seen that where iron used to be used earlier, polymers are being used today, Today's time polymers have taken it. Where the usefulness of another polymer is increasing, its polymer pollution is also increasing, it is often seen that using iron is very difficult for everyone, we know that as well as using polymer is very difficult for us. itself is getting polluted but for this the Indian government should make a very important policy for the use of very important utilities so that it can be joined despite using it.
Poly(methyl methacrylate) (PMMA) sheets have a wide variety of applications due to its properties like light
weight, excellent weather resistance, light transmittance, and good insulating properties [1,2]. But the low softening temperature limits their applications [3,4]. Methyl methacrylate (MMA) has been copolymerized with a variety of vinyl monomers to yield polymers with improved thermal stability, better impact strength and abrasion resistance [57].Extensive work has been done in our laboratories on the copolymerization of MMA with N- arylsubstituted maleimides and itaconimides and a significant increase in the glass transition temperature has been observed [89]. It is well known that N-substituted maleimide and styrene represent monomer pairs with a strong tendency toward radical alternating copolymerization moreover, after copolymerization, the thermal stability of polystyrene, which is widely used as a conventional plastic, will be greatly improved. So far, the copolymerization of N-butyl maleimide (NBMI) and styrene, N-4-hydroxy phenyl maleimide (NHPMI) and styrene has been reported in literature [10-13]. In your previous work we are synthesis of newly substituted N- Phenyl maleimide polymers which are showing excellent thermal stability [14,15]. Acidic comonomers such as acrylic acid (AA), methacrylic acid (MAA) and itaconic acid (IA) provide supplemental dye sites, modify the fibre morphology, increase the hydrophilicity and facilitate the cyclization of nitrile groups during thermo-oxidative stabilization of acrylic fibres prior to carbonization [16].
In this article we are prepared some new N- Phenylmaleimide monomers and copolymerized with Cinnemic acid and investigated their thermal stability.
-
EXPERIMENTAL
-
Materials
Maleicanhydride were recrystallized from acetone. Methylmethacrylate (CDH) was shaken two to three times with 5% NaOH to eliminate hydroquinone inhibitor, dried over anhydrous CaCl2 for 6 hours and distilled [15]. The head and tail fractions were discarded. AIBN (2,2_-azobis isobutironitrile (spectorchem.)) was recrystallized twice from methanol prior to use. BPO (benzoyl peroxide CDH) was used as received. THF was purified by distillation after being refluxed for 2 h in the presence of sodium. Dioxane and DMSO were used after distillation. DMF and methanol used in the present work were of analytical grade and were used as received.
-
Measurements
1H-NMR spectra of monomer and polymer samples were taken in DMSO-d6 on a Bruker DPX-200/DPX-300 spectrometer at 200/300 MHz. The internal reference used was TMS. FT-IR spectra of the monomer and polymer sample were recorded on a Shimadzu 8201 PC (4000-400 cm-1) FT-IR spectrometer, using KBr pellet technique. The viscosity measurements were carried out in DMF at 30±0.2
°C, using an Ubbelohde suspended level viscometer. Elemental analysis was made on Carlo Erba Model NA 500 series analyzer. The thermograms in air were obtained on a Mettler TA-3000 system, at a heating rate of 10 °C/min
-
Methods
Preparation of N-(4-Nitorphenyl) maieimide (PNPMI): Nitroaniline (13.8 gm for 0.1mol) and 9.8 gm maleic anhydride were taken in 30 ml DMF. The solutions kept stirring for three hours at 25°C. The reaction mixture was poured in crushed ice. Yellow solid precipitate was obtained, then filtered and dried under vacuum. It was recrystallized from methanol to obtained pure N-(4- Nitrophenyl) maleamic acid. Yield was 70%, m.p. 145°C. N-(4-Nitrophenyl) Maleimide:Cyclodehydration of the 4- Nitromaleamic acid, an intermediate to maleimide was carried out by treating former with conc. H2SO4 and P2O5. The solution stirring for three hours at 65°C. Then the solution poured in crushed ice or cooled water, obtained to yellow solid precipitate filtered and washed with water and
dried.N-(4-Nitrophenyl) maleimide was recrystallized from ethyl alcohol solvent. The yield was 65%, m.p. 120°C.
SCHEME-I
+ H2N
NO2
DMF O
COOH
NH
O O O
Temp. 25°C,
3 hours
Maleic anhydride 4-Nitroaniline
NO2
N-(4-Nitrophenyl) maleamic acid (PNPMA)
O NH
COOH
Conc. H2SO4 P2O5,65°C,
3 hours
O N O
NO2
NO2
N-(4-Nitrophenyl) maleamide (PNPMI)
Homopolymerization of N-(4-Nitrophenyl) maleimide (PPNPMI)
4-Nitrophenylmaleimide (2.18 gm, 0.01 mol) were taken in
30 ml THF solvent in round bottom flask with reflux condenser. To this solution 20 mg AIBN was added and the reaction mixture was refluxed on heating mental at 65°C for 12, 24, 36 and 48 hours. Yield was obtained 32.33% for 24 hours. The synthesized polymer was isolated in excess quantity of methanol water mixture. It was dried under vacuum at 55°C.
SCHEME – 02
n
NO2) [19]. 967 (CH=CH) [20]. 856(1,4 disubstituted
benzene) these are consistent with the structure of PNPMI. 1H-NMR spectra (Fig. 2, 400 MHz TMS, DMSO-d6, , ppm) of PNPMI shows two methie (CH=CH) protons at
6.82 (s) ppm; two aromatic protons (o-group in phenyl ring) at 7.13-7.15 (d) ppm; two aromatic proton (m-group in phenyl ring) at 7.63-7.64 (d) ppm .
PPNPMI
In Fig. 3, for PPNPMI, the specific characteristic absorption bands observed are at 3088 (C-H aromatic), 2981 (C-H stretch alkene), 1778, 1715 (symmetric and
asymmetric stretching of C=O group) 1614, 1651, 1563,
1444, 1596 (C=C stretch aromatic), 1504, 1331 (symmetric and asymmetric, Ar-NO2 group), 1255 (asymmetric C-O-C
O N O
NO2
AIBN, THF 20 mg, 65°C,
12,24,36 hours
O N O
NO2
stretch), 1110, 1168 (symmetric C-O-C stretch), 856 (1,4 disubstituted benzene) and 690, 605 (out of plane aromatic ring C=C bend) are consistent with the structure of PPNPMI. In Fig.4, the 1HNMR spectrum of PPNPMI is observed at 7.508.08 (d). 2H in CHCH group have appeared at 3.54.0 ppm. 1HNMR of PPNPMI monomer shows chemical shift at 6.82 (s) ppm characteristic of CH=CH group. The disappearance of this in polymer PPNPMI shows that the radical polymerization proceed through the double bond [ 21-24].
Copolymerization of N-(4-Nitrophenyl) maleimide with MMA (CPNPMI)
Equal amount of 4-Nitrophenylmaleimide and Cinnemic acid in 30 ml THF solvent were taken in a round bottom flask. The reaction was carried out at 65°C for 12, 24 ,36 hours. Copolymer samples were isolated in water containing 20 % methanol. The copolymer were purified
PNPMCCA
In fig. 5, 3064,2936 (Aromatic,C-H), 2679.6 (-
COOH),1713, 1776 (C=O), 1560 (C=C stretch,
aromatic),1560(-NO2 group) 1461.9 (C-H band, CH2), 1390 (due to overlapping of C-N), 1251.3 (Ar-O-C-), 1560
(-NO2) 830.7 (1,2-disubstituted benzene) and 772.6, 772.2 cm1 (out of plane C-H band of benzene ring, and 664 (out
1
by first dissolving in THF and then, reprecipitating in
of plane (aromatic ring C=C band).
H-NMR of
excess quantity of methanol water mixture. The precipitated copolymers were washed with methanol several times and dried at 60°C under vacuum. Yield was 48.81%.
SCHEME-3
PNPMCCA data showing In Fig. 6, values from 7.5 to
8.1 due to present of phenyl ring and a signal of showing at 4.0 it means present of the unit, signal values obtained in 3.2 to 3.5 appearance of polymerization precede via single bond.
PNPMI
-
-
RESULTS AND DISCUSSION
FT-IR spectra (Fig.1, in cm1) with characteristic absorption frequencies 3091.3,2980.8 (aromatic and alkene C-H stretch), 1797 and 1708 (symmetric and asymmetric stretching of C=O in a five member imide ring.[15,16] 1634(CH=CH, alkene), 1564 1456 (C=C, aromatic) [17,18].1335,1504 (symmetric and asymmetric stretch of
Figure 1. FTIR for PNPMI
Figure 2. 1H-NMR of PNPMI
Figure 3. FTIR of PPNPMI
Figure 4. 1H-NMR of PPNPMI
Figure 5. FTIR of PNPMCCA
Figure 6. 1H-NMR OF PNPMCCA
-
Effect of time on yield
Prepared monomer copolymerized with Cinnemic Acid with at different time hours and percentage yield was given in table.1, it is seems that no any percentage yield or polymer formation found around the 12 hours, only percentage yield obtained upper to 12 time hours.
Table: 1 . Percentage Yield of Homopolymer and copolymer given in table with respect to time Hours.
viscosity determined by Ubbelohde suspended viscometer. For commercial purposes, the molar mass is usually characterized from measurement of the viscosity of dilute solutions. It has been shown that, for dilute solutions, the relation between the viscosity and the molar mass (in this case the viscosity average molar mass) may be given by the relationship[]= K Ma, where K and a are constants,
M is the molar mass,[] is the intrinsic viscosity or limiting viscosity number.
This is obtained by plotting ( 0)/0c against concentration c and noting its extrapolated value at infinite dilution. In this case, is the viscosity of the polymer solution and 0 the viscosity of the pure solvent. Intrinsic viscosity obtained by (fig.7,8) Hugging plots reduced viscosity verses concentration .
Polymer Code
Number Average( Mn)
Weight Average( Mw)
Polydis persity (Mw/M n)
Start Mw
Intrinsic Viscosity
PPNPMI
456
519
1.138
2779
0.0423
PNPMC CA
680
1832
2.573
2660
0.238
Table: 3 Shows the number molecular weight and Intrinsic viscosity of PPNPMI and PNPMCCA
Polymer Code
12Hr.
24Hr.
30Hr.
36Hrs.
Colour
PPNPMI
18.78
33.23
38.12
40.78
Yellow
PNPMCC A
38.9
40.3
41.8
44.2
Yellow
Polymer code
Conc. (c) g/dl
rel
sp
red
Intrinsic viscosity
PPNPMI
0.1
1.0055
.0055
0.055
0.0423
0.2
1.0138
.0138
0.069
0.3
1.0255
.0255
0.085
0.4
1.0380
.0380
0.095
0.5
1.0560
.0560
0.112
0.6
1.0732
.0732
0.122
Table: 4 Typical data of Viscosity measurements of PPNPMI summarized in DMF at 30°C
-
Effect of solvent and Initiator system
Synthesis homopolymer and copolymer were carried out in different THF and DMF solvent System and effect of the solvent on percentage yield was calculated and result are summarized in the table.2.
Table: 2 Shows the result of percentage yield in DMF- AIBN and DMF-BPO Solvent system
Table 5. Typical data of Viscosity measurements of PNPMCCA summarized in DMF at 30°C
Polymer Code
Solvent
AIBN
BPO
Colour
PPNPMI
THF
35.32
29.77
Yellow
DMF
40.72
36.29
Yellow
1,4
DIOXANE
34.21
31.72
Light yellow
Polymer code
Con c.(c) g/dl
rel
sp
red
Intrinsic viscosity
PNPMCCA
0.1
1.0244
0.0244
0.2
44
0.238
0.2
1.0508
0.0508
0.2
54
0.3
1.0789
0.0789
0.2
63
0.4
1.1068
0.1068
0.2
67
0.5
1.1380
0.1380
0.2
76
0.6
1.1692
0.1692
0.2
82
From table .2 indicate that percentage yield was in AIBN- DMF system is more suitable as comparative BPO- DMF solvent system .AIBN-DMF system gives to more yield.
-
Relation in between intrinsic viscosity and molar mass
Molecular weight of synthesis compounds determined by the Gel permission Chromatography and relation find out in between molar mass and intrinsic viscosity, Intrinsic
From comparison of the table 4 and 5 are showing that intrinsic viscosity of Copolymer having more than of Homopolymer it is due to present of both are unit in the structure of copolymer and molecular weight of copolymer is more than as compare to homopolymer.
Fig. 7. for PPNPMI
Figure. 8 for PNPMCCA
-
Solubility Behavior of Polymers
The solubility of monomers and polymers were observed by finely grounded polymer powder which was placed into test tube and two to three ml solvent was added and stirred at 30C. same procedure repeat for each sample. Solvent was taken were as follows: THF,DMF,DMSO,Benzene.Methylacetate,,1,4Dioxane,Xy lene,dichloromethane,2Butanol,cyclohexanon,water,metha nol and carbon tetrachloride. Solubility of any polymeric materials depends upon the composition. Solubility of homopolymer is less than copolymer although same
condition is not found regular. Solubility of homopolymer and copolymer summarized in table
Table. 6: Relative solubility of homopolymer and copolymer are summarized
Solvents
PPNPMI
PNPMICCA
Colour
Chloroform
Soluble
Soluble
Yellow
THF
Soluble
Soluble
Yellow
DMF
Soluble
Soluble
Yellow
DMSO
Soluble
Soluble
Yellow
Dioxane
Soluble
Soluble
Yellow
Acetone
Soluble
Soluble
Yellow
Ethyl acetae
Soluble
Soluble
Yellow
Xylene
In Soluble
Insoluble
Yellow
Toluene
Soluble
Soluble
Yellow
Carbon tetrachloride
Soluble
Insoluble
Yellow
Cyclohexanone
Partial Soluble
Partial Soluble
Yellow
Dichloromethane
Soluble
Soluble
Yellow
n-Hexane
Partial Soluble
Partial Soluble
Yellow
Ethanol
Soluble
Soluble
Yellow
Methanol
Soluble
Soluble
Yellow
Benzene
Soluble
Partial Soluble
Yellow
-
Thermal behavior
Synthesis homopolymer and copolymer and their Thermal stability were determined by Perkin Elmer USA Pyris TGA-A Techniques and thermal degradation rate of homopolymer and copolymer are summarized in table.. and Thermograms of synthesis PPNPMI and CPNPMI are shown in Fig.9 and 10. Initial temperature Ti and Final temperature Tf range shown in Table 7 and 8 shows decomposition rate, integral procedural decomposition temperatures and The results of percentage weight loss suffered from 100 oC to 550 oC .
Table 7 :Thermal degradation of Homopolymer and copolymer samples
Polymer Code
Degrdation step
Ti oC
Tma x oC
Tf oC
Residue at 500 oC
PPNPMI
I
240
340
370
20.88
II
370
410
550
PNPMCCA
I
225
275
342
17.09
II
342
448
560
Table 8:.Percentage weight loss of Homopolymer and copolymer at various temperature.
Polymer Code
200 oC
300 oC
400 oC
500 oC
550 oC
PPNPMI
-0.8
-20.8
-72.8
-79.1
-79.2
PNPMCCA
-0.21
-62.14
-79.83
-82.91
-82.72
From the table 7 and 8 gives the comparative study because percentage degradation in homopolymer shows very less, while percentage degradation in copolymer shows very high it is due to homopolymer having only one unit while copolymer having two units and percentage degradation of the thermal curves are shows in fig.9 and 10.
VI. REFERENCES
Figure: 9 , Thermogram curve of PPNPMI
Figure: 10 Thermogram curve for PNPMCAA
-
-
CONCLUSION
Thermal stability of the homopolymer shows in excellent stability, while copolymer shows the less stability to because of homopolymer having single unit and copolymer having both are unit. Synthesis homopolymer and copolymer shows the excellent solubility in THF,DMF
,DMSO, Chloroform .Ethyl acetate and solubility of any polymeric materials depends on the composition like as texture and length ,molecular weight, Intrinsic viscosity. Polymerization process through the free radical polymerization reactions, this is approved by the Polydispersity index Molecular weight of copolymer is more than of homopolymer it is due to copolymer having both are unit. Weight average and number average molecular weight determined by the Gel permeation chromatography.
-
ACKNOWLEDGEMENT
We are thankful to CDRI Luck now and SICART Vallabh- Vidhyanagar for analysis work. Authors Shiv NarayanPaliwal and Suresh Meena is thankful to UGC (RGNSF), DST FIST ,New Delhi for financial assistance.
[1] Rahman, S., Usmani, T., & Saeed, S. H. (2013). Review of Electronic Nose and application. Int. J. Comput. Corp. Res.(IJCCR), 3, 1-9. [2] Matsumoto, A., Kubota, T., & Otsu, T. (1990). Radical polymerization of N-(alkyl-substituted phenyl) maleimides: synthesis of thermally stable polymers soluble in nonpolar solvents. Macromolecules, 23(21), 4508-4513. [3] Braun, D., & Czerwinski, W. K. (1987). Kinetische analyse dercopolymerisationsgeschwindigkeit von Nvinyl2pyrrolidon mit styrol und methylmethacrylat. Die Makromolekulare Chemie:
Macromolecular Chemistry and Physics, 188(10), 2389-2401.
[4] Mansour, A. F., Killa, H. M. A., Abd El-Wanees, S., & El-Sayed,M. Y. (2005). Laser dyes doped with poly (ST-Co-MMA) as fluorescent solar collectors and their field performance. Polymer Testing, 24(4), 519-525.
[5] Cornejo-Bravo, J. M., & Siegel, R. A. (1996). Water vapour sorption behaviour of copolymers of N, N-diethylaminoethyl methacrylate and methyl methacrylate. Biomaterials, 17(12), 1187-1193. [6] Bharel, R., Choudhary, V., & Varma, I. K. (1995). Physicomechanical properties of poly (methylmethacrylatecoNarylmaleimides). Journal of applied polymer
science, 57(6), 767-773.
[7] Bharel, R., Choudhary, V., & Varma, I. K. (1993). Thermal and mechanical properties of copolymers of methyl methacrylate withNphenyl maleimide. Journal of applied polymer science, 49(1),
31-38.
[8] Mishra, A., Sinha, T. J. M., & Choudhary, V. (1998). MethylmethacrylateNchlorophenyl maleimide copolymers: Effect of structure on properties. Journal of applied polymer science, 68(4),
527-534.
[9] Choudhary, V., & Mishra, A. (1996). Studies on thecopolymerization of methyl methacrylate and Naryl maleimides. Journal of applied polymer science, 62(4), 707-712.
[10] Coleman Jr, L. E., & Conrady, J. A. (1959). Nitrogencontaining monomers. I. Copolymerization reactions of Nalkyl maleamic acids and Nalkyl maleimides. Journal of PolymerScience, 38(133), 241-245.
[11] Lokaj, J., Sikora, A., Holler, P., & Konený, D. (1998). Synthesisand characterization of styreneNbutyl maleimide copolymers using iniferters containing thiyl end groups. Journal of applied
polymer science, 67(4), 755-762.
[12] Zhou, X., Hao, Y., Yuan, L., Pradhan, S., Shrestha, K., Pradhan, O., … & Li, W. (2018). Nano-formulations for transdermal drug delivery: a review. Chinese Chemical Letters, 29(12), 1713-1724. [13] Zhao, Y., Li, H., Liu, P., Liu, H., Jiang, J., & Xi, F. (2002).Reactivity ratios of free monomers and their chargetransfer complex in the copolymerization of Nbutyl maleimide and
styrene. Journal of applied polymer science, 83(14), 3007-3012..
[14] Suresh, M.,(2022).Recent Study of Some New Maleimide Copolymers and Their Electrolyte Study in Solvent, International Journal of Engineering Research & Technology11(12) [15] Suresh ,K. , Bharat, S M., Manju., Hiran B.L., (2019). Thermal Study and Characterization of New Synthesis N- Benzylmaleimide and N- Phynyl Maleiide Polymers, International Journal of Engineering Research & Technology, 8 : 07, [16] Bajaj, P., Sreekumar, T V., & Sen, K., 2001). Thermal behaviour of acrylonitrile copolymers having methacrylic and itaconic acid comonomers. Polymer , 42(4): 1707-1718. [17] Riddick, J. A., Bunger, W. B., & Sakano, T. K. (1986). Organic solvents: physical properties and methods of purification. [18] Education, A., & Ghosh, M. Criminalising Abortion: Women's Rights (Ed) Issue no: 16, Apr 17-23, p. 729 Women and Abortion; Amar Jesani and Aditi Iyer (P). [19] Beekman, P., Enciso-Martinez, A., Pujari, S. P., Terstappen, L. W., Zuilhof, H., Le Gac, S., & Otto, C. (2021). Organosilicon uptake by biological membranes. Communications Biology, 4(1), 1-8. [20] Patel, M. H., & Oswal, S. B. (2011). Synthesis and Characterization of Homo-and Copolymers of N-4-Azodiphenyl Maleimide with Methyl Methacrylate and Styrene. International Journal of Polymeric Materials, 60(8), 542-561. [21] Otsu, T., Yasuhara, T., & Matsumoto, A. (1988). Synthesis, characterization, and application of poly [substituted methylene]s. Journal of Macromolecular ScienceChemistry, 25(5-7), 537- 554.
[22] Matsumoto, A., Kubota, T., & Otsu, T. (1990). Radical polymerization of N-(alkyl-substituted phenyl) maleimides: synthesis of thermally stable polymers soluble in nonpolar solvents. Macromolecules, 23(21), 4508-4513. [23] Silverstain R.M.; Bassler G.C. and Morril T.C.; Spectrometric Identification of Organic Compounds, 4th Edn. John Wiley and Sons. Inc. New York (1991).