
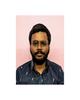
- Open Access
- Authors : Kaithi Poojith Raj Patel, Gujjala Manikanta Reddy
- Paper ID : IJERTV12IS050346
- Volume & Issue : Volume 12, Issue 05 (May 2023)
- Published (First Online): 13-06-2023
- ISSN (Online) : 2278-0181
- Publisher Name : IJERT
- License:
This work is licensed under a Creative Commons Attribution 4.0 International License
Sustainable FDM Additive Manufacturing of PA6GF30 Components with Emphasis on Energy Minimization and Less Carbon-Footprint Construction
Kaithi Poojith Raj Patel(1) Gujjala Manikanta Reddy(2)
(2)L&T Technology Services
ABSTRACT :- Fused Deposition Modelling (FDM) is a popular additive manufacturing technique that may be used for quick prototyping and manufacture. The current study was focused on assessing the process sustainability to ensure lightweight construction with low environmental impact and printing time, in light of the growing trend of sustainable manufacturing. Having extensive applications in electronics, aviation, automobile application, etc. Polyamide 6 reinforced with 30% glass fibre (PA6GF30) was used as the test material. A Design of Experiments (DoE) using the Taguchi method composed of L9 array tests was conducted by varying four different printing parameters namely wall thickness, fill density and feed rate. During the test, three critical metrics of sustainable manufacturing (energy, power, and carbon emissions) were measured. The DoE findings were subjected to analysis, which demonstrated that the printing parameters in question had a considerable impact on the specified sustainability metrics. Finally, optimal printing parameters for the FDM technique are recommended to assure long-term printing
Key words : Glass fibre , 3D Printing , Polyamide, Prototype
INTRODUCTION
The most widespread additive manufacturing technology is fused deposition modeling (FDM), which is followed by selective laser melting (SLM). The technique allows for a high degree of shape flexibility, obviating the necessity for shape- dependent tooling. In comparison to competing for traditional manufacturing, direct manufacturing from CAD models saves lead time and hence enables the production of small quantities in less time and at a lower cost. The process' inherent flexibility to adapt to any complicated design aids rapid manufacturing of bespoke parts, providing a cost-effective solution to the contemporary market need for customization and small-batch production. The FDM technique has been shown to have a wide range of applications in a variety of fields. Biomedical and fast tooling are two prominent industries that have profited from FDM[3]. A range of biomedical parts has been produced as reviewed in Refs. These include tissue engineering scaffolds and prosthetics. FDM has shown to be a dependable and cost-effective method of producing tools for a variety of production processes. In this regard, sacrificial patterns for investment casting, sand casting patterns, and injection molding molds are all worth discussing. FDM also allows for the creation of functioning prototypes, which allows for the fulfillment of
designs. Biomedical, plastics, automotive, and electronics are among the industries that have benefited from FDM in varied capacities in terms of functional components or prototypes [3]. FDM's application scope is now expanding to include drug delivery devices and aerospace manufacturing, such as unmanned aerial vehicles (UAVs) and military systems, thanks to the discovery of new filament materials [4]. To reap the full benefits of additive manufacturing in the years ahead, efforts to design ways to make it a more competitive manufacturing method in numerous fields are currently ongoing. With rising environmental consciousness and stricter environmental regulations, the concept of sustainable manufacturing is gaining traction among manufacturers. Nowadays, producing products with the least amount of energy use is the primary goal. To reach this goal, new techniques, materials, and tactics are being sought out and implemented. Two crucial foundations of sustainable production are energy usage and time efficiency. In FDM, only a little amount of effort has been made in this direction. The goal of this research was to find out how machine architecture and process influences on power consumption affect energy consumption. Even though power usage was studied, just a few factors (such as speed and material flow) were examined, and the data were analyzed using a two-level factorial design. To the best of the author's knowledge, such a test design is typically used to narrow down the influential parameters in order to undertake further in-depth analysis[1]. As a result, in order to acquire a comprehensive understanding of the subject, full research on energy consumption should be conducted, taking into consideration the missing factors. This is also crucial in terms of environmental impact, as the amount of energy spent in a process is thought to have a direct impact on carbon emissions. Aside from saving energy, lightweight construction contributes to product sustainability by reducing component mass, lowering material costs, and accompanying emissions. Similarly, printing time has an impact on sustainability because it influences energy consumption, machine utilization, and labor costs, all of which affect the entire product cost[2]. In light of the foregoing considerations, the purpose of this research is to examine the FDM process in order to enable efficient construction while consuming the least amount of energy and a fewer carbon emissions. PA6GF30(Polyamide 6 Glass Fibre30) is a 30% reinforced glass fiber with polyamide 6 composite with very high
strength, good wear properties, high dimensional stability, good machinability, lightweight, and less fragility. Having these excellent properties[3]. It is used in the automobile Industry, Boats and Marine, Aviation and Aerospace, and Home and Furniture. Moreover, having a high melting point, it is being widely used as a heat resistant in electrical applications. Therefore, PA6GF30 is used as the testing material [2]. Three different printing parameters of the FDM process are adjusted across a large range, and the consequences of these variations on three crucial sustainability indicators, namely energy consumption, product mass, and printing time, are rigorously examined [4]. On the basis of the findings, optimum conditions for achieving long-term product printing are devised.
METHODOLOGY
To perform sustainability analysis on FDM printing of PA6GF30 material, the Taguchi method was used. Among various design options, tensile load testing was applied as this allows us to conclude the best printing parameters to build a strong component with a minimum carbon footprint[5].
The following three print parameters were opted as the variables of the Taguchi method.
Wall Thickness |
Tw in mm |
Infill Density |
ID in % |
Feed Rate |
F in mm/min |
Wall thickness(tw): Wall thickness is the distance from the
Fig.1. All the printing Parameters Using Taguchi method on minitab |
The material used :
PA6GF30: PA 6 GF30, also known as TECAMID 6 GF30
black, is a 30 percent glass fiber reinforced polyamide that we create. It outperforms unreinforced polyamide 6 in terms of strength, stiffness, creep strength, and dimensional stability. These qualities of PA6 GF30 make it ideal for parts that are subjected to high static loads for extended periods of time in high temperatures. Glass-filled nylon 6 is less suitable for sliding applications because glass fibers have a noticeable abrasive effect on mating
surfaces in some circumstances.
MAIN FEATURES
external part to the internal part of a 3D print model surface. Very high strength
Also known as a shll, it plays an important role in supporting Resistant to many oils, greases and fuels 3D print models. However, when it is not optimized, several
defects such as warping and straining can occur. Good wear properties Consequently, getting the best wall thickness for 3D printing is
an important decision you should make.
-
Good weldable and bondable
Infill density(ID): Infill density is the fullness of the inside High dimensional stability of a part. In slicers, this is usually defined as a percentage
between 0 and 100, with 0% making a part hollow and 100%, Good heat deflection temperature
completely solid. As you can imagine, this greatly impacts a
parts weight: The fuller the interior of a part, the heavier it is. Good machinability
Besides weight, print time, material consumption, and
buoyancy are also impacted by infill density. So, too, is strength, albeit in combination with many other elements such
TARGET INDUSTRIES
as materialand layer height.
-
Mechanical engineering
Feed rate (F): Print speed is the main speed setting that will Electronics influence your 3D prints. Print speed determines how fast the
motors of your printer move. This includes the motors Automotive industry
controlling the X- and Y-axes, as well as the extruder motor. These settings were chosen based on best practices and printer
limitations. The other parameters that include layer thickness, bed temperature, print temperature, and nozzle diameter are fixed and tabulated below.
ASTM D638 type 1
The first stage was to design the test specimens, which would be created using additive manufacturing techniques such as Fused Deposition Modeling (FDM). The test specimens created using the FDM process were subjected to tensile testing. The specimens must conform to ASTM standards,
such as a standard dog bone shape specimen for tensile testing. These include a standard block form specimen for compressive testing as well as a standard block shape specimen for hardness testing. As illustrated in the figure below, specimens were created as 2D sketches Creo 8.0.
Fig.2 ASTM D638 Type 1 |
Fig.3 ASTM D638 Model |
Fig.4. Slicing in ultimaker cura |
The test specimen has a gripping head or a holding head that allows it to be easily secured on both ends of the UTM's work holding jaws. This grasping head measures 32.86mm in length and 19mm in width. The test specimen has a gauge length of 57mm and a gauge breadth of 13mm, with the properties of the polymers subjected to the corresponding test as given in the figure.
Sample |
Energy (KWh) |
CO2(KG ) |
UltimateTensile strength(Mpa) |
1 |
0.55 |
0.31 |
16.879 |
2 |
0.49 |
0.27 |
28.546 |
3 |
0.44 |
0.24 |
47.19 |
4 |
0.41 |
0.26 |
19.143 |
5 |
0.36 |
0.18 |
29.755 |
6 |
0.73 |
0.4 |
50.195 |
7 |
0.75 |
0.46 |
18.36 |
8 |
0.67 |
0.37 |
31.176 |
9 |
0.51 |
0.29 |
48.457 |
Table 2. Energy emissions and carbon emission during 3D printing |
An ASTM D638 type 1 test sample was selected as the target print geometry. The printingwas carried out utilizing the experimental setup . An FDM printer (Model: ULTIMAKER S5), a PA6GF30 filament spool, and a clamp meter are included. The voltage and current consumed by the single-phase printer during printing were measured using a clamp meter (MAKE: Mastech)
sample |
Ultimate Tensile Strength(MPa) |
Ultimate Load(KN) |
Yield Stress(MPa) |
Yield Load(KN) |
1a |
16.098 |
1.6 |
10.263 |
1.02 |
1b |
16.572 |
1.64 |
12.328 |
1.22 |
1c |
17.967 |
1.76 |
11.229 |
1.1 |
2a |
27.149 |
2.64 |
15.426 |
1.5 |
2b |
31.307 |
3.08 |
20.736 |
2.04 |
2c |
27.183 |
2.68 |
18.46 |
1.82 |
3a |
50.861 |
5.02 |
42.553 |
4.2 |
3b |
44.593 |
4.8 |
36.603 |
3.94 |
3c |
46.117 |
4.84 |
38.876 |
4.08 |
4a |
18.781 |
1.8 |
12.73 |
1.22 |
4b |
17.448 |
1.66 |
15.346 |
1.46 |
4c |
21.2 |
2 |
16.324 |
1.54 |
5a |
31.964 |
3.12 |
21.719 |
2.12 |
5b |
27.552 |
2.68 |
20.973 |
2.04 |
5c |
29.75 |
2.82 |
25.53 |
2.42 |
6a |
47.863 |
4.86 |
36.242 |
3.68 |
6b |
50.846 |
4.96 |
41.21 |
4.02 |
6c |
51.877 |
5.1 |
46.18 |
4.54 |
7a |
19.434 |
1.86 |
13.374 |
1.28 |
7b |
19.802 |
1.9 |
18.343 |
1.76 |
7c |
15.844 |
1.54 |
12.346 |
1.2 |
8a |
32.851 |
3.18 |
31.405 |
3.04 |
8b |
29.199 |
2.86 |
22.46 |
2.2 |
8c |
31.478 |
3.02 |
25.433 |
2.44 |
9a |
50.176 |
5 |
32.715 |
3.26 |
9b |
48.044 |
4.84 |
26.206 |
2.64 |
9c |
47.153 |
4.72 |
39.361 |
3.94 |
Table 1. Results obtained from UTS test |
RESULTS
Fig 3 Graph between energy,co2 and ultimate strength |
CONCLUSIONS :
Two significant performance criteria of sustainable manufacturing are energy consumption and carbon foot print. The effects of several variables were statistically evaluated in this study printing settings with the goal of reducing energy consumption and printing time while reducing the CO2 emission FDM additive manufacturing was used to create PA6GF30 components.The following are the study's key findings:
-
All the sampes having an infill density of 100% have been tested to have a higher tensilestrength.
-
Samples having lesser infill density have less tensile strength. Concluding that less infill density affects the strength of the component.
-
Same is the case with the wall thickness the greater the wall thickness the strength of the components have been tested to have a greater strength.
-
Components printed with high feed rate tend to have finer finishes as compared to the components having less feed rate
-
The CO2 emission and energy consumption was recorded one of the lowest for the 3rd parameter and that happens to have the highest tensile strength
-
The tensile sample having a wall thickness of 0.6 feed rate of 80mm/s and an infill density of 100% proved to have high tensile strength and less energy consumption as well as CO2 emission.
FUTURE WORK:
The analysis will be extended by incorporating the mechanical properties of PA6GF30 components into performance measures considered herein study
REFERENCES
[1] [1] M. Heidari-Rarani, N. Ezati, P. Sadeghi, and M. R. Badrossamay, Optimization of FDM process parameters for tensile properties of polylactic acid specimens using Taguchi design of experiment method,J. Thermoplast. Compos. Mater., vol. 35, no. 12, pp. 24352452, 2022, doi: 10.1177/0892705720964560.
[2] T. P. Sathishkumar, S. Satheeshkumar, and J. Naveen, Glass fiber- reinforced polymer composites a review, 2014, doi: 10.1177/0731684414530790. [3] M. A. Caminero and M. A. Caminero, NU, 2017, doi: 10.1016/j.matdes.2017.03.065. [4] K. A. Al-ghamdi, Sustainable FDM additive manufacturing of ABS components with emphasis on energy minimized and time efficient lightweight construction, Int. J. Light. Mater. Manuf., vol. 2, no. 4, pp. 338345, 2019, doi: 10.1016/j.ijlmm.2019.05.004. [5] G. Fiber and R. Samples, Tensile Strength Analysis of Thin-Walled Polymer, 2020.