
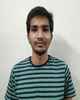
- Open Access
- Authors : Sandeep Kumar Singh , Shruti Sharma , Roshan Singh , Sajal Jain
- Paper ID : IJERTV10IS070087
- Volume & Issue : Volume 10, Issue 07 (July 2021)
- Published (First Online): 15-07-2021
- ISSN (Online) : 2278-0181
- Publisher Name : IJERT
- License:
This work is licensed under a Creative Commons Attribution 4.0 International License
Study of Heat Transfer and Friction Factor Investigation of Various Roughness Geometries used in Solar Air Heaters
Sandeep Kumar Singp*, Shruti Sharma1, Roshan Singp, Sajal Jain1
1B.Tech, Final Year Mechanical Engineering, JSS Academy of Technical Education,
Noida
Abstract:- Solar air heater is the cheapest and extensively used solar energy collection device for drying of agricultural products, space heating, seasoning of timber and curing of industrial products. The use of an articial roughness on a surface is an effective technique to enhance the rate of heat transfer to uid ow in the duct of a solar air heater. Use of articial roughness in solar air heater has been topic in research for the last thirty years. In the present article an attempt has been made to present holistic experimental investigations of square cross section roughness geometry used for creating articial roughness in solar air heater for performance enhancement by experimental approaches. The effects of various rib parameters on heat transfer and uid ow processes are also discussed
INTRODUCTION:
Energy is the primary force in the universe. Energy denes the Earths biomes and sustains life. All life, from single-celled microbes to blue whales, exists in a continuous process of consuming, using, and storing energy [1]. In general, energy is the ability of a system to cause exterior impacts, for instance a force across a distance. Input or output of work changes the energy content of a body.
Solar air heater is one of the basic equipment through which solar energy is converted into thermal energy. The main applications of solar air heater are space heating, seasoning of timber, curing of industrial products and these can also be effectively used for curing/drying of concrete/clay building components. A solar air heater is simple in design and requires little maintenance. However, the value of the heat transfer coefcient between the absorber plate and air is low and this results in a lower thermal efciency. The thermal efciency of solar air heater is low because of low value of convective heat transfer coefcient between the owing air and absorber plate (heat transferring surface) due to the formation of thin laminar viscous sub-layer on its absorber plate. The efciency of solar air heater can be improved by modifying the boundary layer developed on the
heated surface. One of the well-known methods of modifying the boundary layer is to break the laminar viscous sub-layer formed on the heat transfer surface by creating articial roughness in the form of repeated ribs, grooves or combination of ribs and grooves. The articially roughened surface has wide application namely in cooling of gas turbine blades, nuclear reactors, solar air heating systems etc. The articial roughness breaks the laminar viscous sub-layer and create local wall turbulence due to the ow separation and ow reattachment between the consecutive ribs, which reduces the thermal resistance, increases heat transfer and thereby efciency. The application of articial roughness enhances the heat transfer at the cost of increased value of friction factor and power penalty. The efforts of the researchers are always directed towards the proper selection of the shape and arrangement of the articial roughness, which modies the boundary layer, enhances the heat transfer coefcient with minimum pressure drop i.e. power penalty [7]. Hence, it is necessary to review different types of articial roughness used on the heat transferring surface to study effect of roughness on the heat transfer coefcient (Nusselt number) and friction factor.
Numbers of experimental investigations involving roughness elements of different shapes, sizes and orientations with respect to ow direction have been carried out in order to obtain an optimum arrangement of roughness element geometry. The objective of present article is to present our experimental investigation on articial roughness geometry used and tested experimentally in solar air heater for performance enhancement.
PARAMETERS AFFECTING THE FLOW PATTERNS:
Rib height (e) Ribs of certain height and alignment affect the flow by obstructing it and separating it from the main flow. Secondary flow can be seen along the ribs and its mixing with the main flow. Vortices are also generated in the downside of flow behind the roughness element which causes turbulence, thus enhancing the heat transfer from the surface. For some types of ribs, the flow separation, free shears layer formation and vortices formation. In addition to that the frictional loss as well tends to occur due to vortices formation. The rib height is approximately 15% of the plate separation distance.
Rib pitch (P): As the rib height and pitch changes there is a change in the flow pattern also. Due to the height, the flow in the downstream side of the roughness element is separated and if the pitch is not maintained properly reattachment of the flow does not occur. The reattachment of the shear layer does not occur for pitch ratio less than 8, and it will result in poor heat transfer from the surface. Maximum heat transfer occurs at the reattachment point. The local heat transfer coefficients in the separated
flow region are larger than those of an undisturbed region. When the relative roughness height ratio (e/Dh) is kept constant the reattachment can be achieved by reducing the relative roughness pitch (P/e). As P/e increases from its lowest value, the friction factor and the heat transfer also increases. The maximum value of P/e occurs at about 10.
Effect of rib alignment (p): Rib alignment in the surface affects the performance of the solar air- heater; the friction factor falls rapidly as the angle of attack decreases from 90o to 15o. Secondary flow is generated along the rib surface which helps in increasing the heat transfer. However, it also increases the friction factor. Fluid vortices are generated in the upstream and downstream side of rib. The two vortices meet the mainstream at the tail end while moving along the rib surface. These moving vortices mix up with the cold stream of air thus increasing the temperature of leading edge. The rib alignment has a very modest effect on the friction factor and the heat transfer.
EFFECT OF GEOMETRICAL DIMENSIONS ON PERFORMANCE OF SOLAR AIR HEATER:
Aspect ratio (W/H): The aspect ratio has effect on the performance of solar air heaters. In large aspect ratio ducts friction is increased with increase in turbulence. The lower aspect ratio duct provides a better heat transfer performance. For equal pumping power, the heat transfer performance of square channel is better than that of rectangular duct with aspect ratio 2 and 3. The collector efficiency increases with the increase in collector aspect ratio. As the aspect ratio increases, the cross-sectional area of the air duct decreases and the velocity of flow increases so the convective heat transfer from the surface of the absorber plate to flowing air increases. In addition to enhancement in heat transfer it also increases the pumping power of the blower of pump leading to the increase in the operating cost of the equipment. Increase in heat transfer with increase in mass flow rate is also evident from the experiments with other type of heat exchangers like recuperators where when mass flow rate is increased there is net increase in the heat transfer to the flowing fluid.
Duct height (H): Solar air heaters with lower duct height have higher efficiency. Lowering of duct height increases the air velocity. The effective efficiency decreases rapidly as the mass flow increases wing to the pumping power requirement which is proportional to (1/H3). Solar air heater efficiency can be maximized by decreasing the depth of solar air heater along the length but in long channel along the length of the solar air heater causes substantial pressure drop causing high pumping losses. An optimum mass flow rate corresponds to an optimum flow channel depth which is required to minimize annual cost to useful heat ratio. At the optimum channel depth to length ratio the outlet temperature becomes equal to the absorber plate mean temperature.
Roughness elements used in channel flow: The initial efforts on using artificial roughness for improving heat transfer characteristics were confided with the areas of nuclear reactors, gas turbines blades, pipes carrying fluids and compact heat exchangers. Several types of artificial roughness elements were used extensively to improve the heat transfer characteristics in these equipments. The roughness elements of two dimensions, three dimensions and of irregular shapes were used by investigators like Nikuradse, Nunner and Dippery. Prasad et al.[8] covers a wide range of e/Dh ratio with P/e values of more than 10 in his experiments in flow through pipes where the ribs were aligned normal to the mainstream direction. The experiments conducted with roughness in one wall, two walls and four walls of absorber plate. The roughness element in one wall is favored by most of the investigators as discussed below in the range of Re 300030,000. Different correlations for heat transfer and friction factor were developed based on the experiments done by different investigators. Prasad and Saini [9] demonstrated that the efficiency of solar air heaters can be increased by decreasing the channel depth along the length. Prasad and Mullick [10] optimized the channel height of different types of the solar air heater. Verma and Prasad [11] investigated the effects of rib shape, angle of attack and pitch to the height ratio on the friction factors and heat-transfer on symmetric and staggered ribs. They found that the ribs at 45o of attack angle have better performance than that at 90o attack angle. Gupta et.al [12] investigated the combined effects of the rib, angle-of-attack ( =90o, 60o, 45o and 30o) and the channel aspect ratio (W/H = 1, 2, 4) on the heat transfer coefficient in short rectangular channels (L/D = 10 and 15) with two opposite rib- roughened walls. They concluded that the highest heat transfer, and the highest pressure drop can be obtained at =60o in the square channel; the highest heat transfer and the pressure drop occur at = 90o with W/H=4 in the rectangular channel, and the values of highest heat transfer and pressure drop differs marginally at =60o for W/H=2. They found that secondary flow or swirling flow moves along the rib surface producing higher Nusselt number towards the wall as compared to centerline. They also concluded that the highest heat transfer and highest pressure drop occur at =90o. The heat transfer and friction correlations were also obtained for the surface. Gupta et.al [13] investigated the effects of the aspect ratio and the initial boundary-layer thickness on low speed forced convective heat transfer near two- dimensional transverse ribs. They also derived the correlation for average Nusselt number. Saini and Saini [14] investigated for turbulent flow on staggered ribs in a square duct with two opposite rib- roughened walls using the parameters of relative roughness height (e/DH) = 0.19; relative roughness pitch(P/e) = 5.31 and Reynolds number. (Re) = 13,000130,000. The temperature distribution and correlation between Nusselt number and Reynolds number was established. The heat transfer rate was calculated to be 2.024.60 times higher than the fully developed turbulent flow in smooth duct for Re = 13.000. Momin et.al [15] investigated the thermo-hydraulic performance for a low aspect ratio channel with staggered lit ribs on top and bottom walls with the parameters of rib area open ratio (1)=24%, 37%, 46%; P/e=10,15,20; W/H=0.081; Re=10,00050,000.They concluded that the arrangement of ribs gives a higher heat transfer enhancement with lower pressure drop for the same solid rib height and spacing. Also the friction factor decreases for an increase in rib open area ratio. They also developed the general friction and the heat transfer correlations
have been developed. Bhagoria et.al [16] investigated the heat transfer and pressure drop in a rectangular duct with staggered ribs of various parameters as the aspect ratio (W/H) =18; relative roughness height (e/DH) = 0.06; angle of attack () = 60o; Reynolds number (Re) = 10006000. They observed that secondary flow causes span wise variation of the heat transfer coefficients along the rib length, and reattachment occurs between two ribs. They concluded that the V downstream ribs induce the highest friction factor than V upstream and parallel ribs with least friction factor. V downstream has stronger secondary flow and gives higher heat transfer when compared to V upstream and parallel ribs also the parallel rib has better performance at higher Reynolds number than V upstream. Saini and Saini [17] investigated on laminar and turbulent flow with transverse or angled rib turbulators of angle of attack of 60o or 90o in a square channel. They concluded that heat transfer is highest in front of the rib, and laminar flow has the lesser effect on the flow field with ribs than turbulent flow as a result the velocity and temperature profiles have lesser differences than the turbulent case. Verma and Saini [18] investigated on five different types of roughness element in rectangular duct with e/DH=0.0476, P/e = 8, and W/H=2.33, to understand the comparative thermo- hydraulic performance due to these elements. He concluded that the triangular rib has the highest heat transfer capacity and Nusselt number is higher in the case of square and triangular ribs when compared to semi-circular ribs. The square ribs have the highest friction factor. Karmare and Tikekar [19] investigated the effect with varying number of transverse ribbed walls with the parameters Re=10,00080,000; P/e=8; e/DH=0.0625 channel length to the hydraulic ratio (L/Dh) = 20 for fully turbulent flow in the square channel. They concluded that one ribbed wall has the heat transfer increase of 2.431.78 for Re = 12,000 75,000, with two opposite ribbed walls the increment was 2.641.92, with three ribbed walls, the increment of 2.812.01 and with four ribbed walls, an increment of 2.992.12 which is the maximum when compared to all the types. The maximum increase in the friction factor was found to be 9.50 with four sided ribbed walls and minimum with one ribbed wall of 3.14. They also compared the performance factor {(Str/Stss)/ (fr/fss)} of four cases and concluded that, it is highest at 1.78 1.17 for one wall ribbed surface. Kumar et.al [20] investigated for heat transfer coefficient distribution in the rectangular channel with transverse continuous, transverse broken and V-shaped broken ribs with the parameters W/H=5; =45o or 60o.
CONCLUSIONS:
It can be concluded from the present review that lot of work has been carried out to investigate the effect of artificial roughness of different shapes and sizes on heat transfer and friction factor. Substantial enhancement in the heat transfer can be achieved with little penalty of friction.
ERFERENCES:
-
Foster R, Ghassemi M, Cota A. Solar energy: renewable energy and the environment. New York: CRC Press Taylor & Francis group; 2010.
-
Kaltschmitt M, Streicher W, Wiese A. Renewable energy: technology, eco- nomics and environment. 1st ed.. New York: Springer;2007.
-
Quaschning V. Understanding renewable energy systems. 3rd ed.. London: Earthscan; 2005.
-
Twidell J, Weir T. Renewable energy: sources. 2nd ed.. New York: Taylor & Francis; 2006.
-
Sukhatme SP, Nayak JP. Solar energy. 3rd ed.. New Delhi: Tata McGraw Hill;2011.
-
Date AW. Introduction to computational uid dynamis. 1st ed.. New York: Cambridge University Press; 2005.
-
Chung TJ, editor. Cambridge UK: Cambridge University Press; 2002.
-
Prasad BN, Saini JS. Optimal thermohydraulic performance of articially roughened solar air heaters. Solar Energy1991;47(2):916.
-
Prasad BN, Saini JS. Effect of articial roughness on heat transfer and friction factor in a solar air heater. Solar Energy 1988;41(6):55560.
-
Prasad K, Mullick SC. Heat transfer characteristics of a solar air heater used for drying purposes. Applied Energy1983;13:8393.
-
Verma SK, Prasad BN. Investigation for the optimal thermo-hydraulic performance of articially roughened solar air heaters. Renewable Energy 2000;20(1): 1936
-
Gupta D, Solanki SC, Saini JS. Heat and uid ow in rectangular solar air heater ducts having transverse rib roughness on absorber plates. Solar Energy1993;51(1):317
-
Gupta D, Solanki SC, Saini JS. Thermohydraulic performance of solar air heaters with roughened absorber plates. Solar Energy 1997;61(1):33 42.
-
Saini RP, Saini JS. Heat transfer and friction factor correlations for articially roughened ducts with expanded met.al mesh as roughened element. International Communications in Heat and Mass Transfer 1997;40(4):97386.
-
Momin AME, Saini JS, Solanki SC. Heat transfer and friction in solar air heater duct with v- shaped rib roughness on absorber plate. International Communications in Heat and Mass Transfer 2002;45:338396.
-
Bhagoria JL, Saini JS, Solanki SC. Heat transfer coefcient and friction factor correlations for rectangular solar air heater duct having transverse wedge shaped rib roughness on the absorber plate. Renewable Energy 2002;25:34169.
-
Saini SK, Saini RP. Development of correlations for Nusselt number and friction factor for solar air heater with roughened duct having arc-shaped wire as articial roughness. Solar Energy2008;82:111830.
-
Saini RP, Verma J. Heat transfer and friction factor correlations for a duct having dimple- shaped articial roughness for solar air heaters. Energy 2008;33:127787.
-
Karmare SV, Tikekar AN. Heat transfer and friction factor correlation for articially roughened duct with met.al grit ribs. International Journal of Heat and Mass Transfer 2007;50:434251.
-
Kumar A, Bhagoria JL, Sarviya RM. Heat transfer enhancement in channel of solar air collector by using discrete W-shaped articial roughened absorber. In: 19th National & 8th ISHMT-ASME heat and mass transfer conference; 2008.