
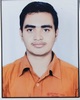
- Open Access
- Authors : Joel Verghese , Sanjay , Sagar , Prajjwal Saxena
- Paper ID : IJERTV10IS030135
- Volume & Issue : Volume 10, Issue 03 (March 2021)
- Published (First Online): 26-03-2021
- ISSN (Online) : 2278-0181
- Publisher Name : IJERT
- License:
This work is licensed under a Creative Commons Attribution 4.0 International License
Study and Designing of An Automobile Thermo-Electic Generator Module for Bikes
( MADE ON ROYAL ENFIELD CLASSIC 350 )
Joel Verghese
GGSIPU
Dr. Akhilesh Das Gupta Institute of Technology and Management New Delhi, India
Prajjwal Saxena
GGSIPU
Dr. Akhilesh Das Gupta Institute of Technology and Management New Delhi, India
Sagar
GGSIPU
Dr. Akhilesh Das Gupta Institute of Technology and Management New Delhi, India
Sanjay
GGSIPU
Dr. Akhilesh Das Gupta Institute of Technology and Management New Delhi, India
Abstract The non-consumed heat energy by bikes or any other automobile when released in the atmosphere proves harmful to the environment and increases global warming. Thus, to reduce these effects and increasing the efficiency of the vehicle the thermoelectric generators can be utilized. These TEGs use waste gas heat of the engine and converts this heat into corresponding electrical EMF which can be stored in batteries and can be used along with the IC engines in order to improve the performance of the vehicle. Thus, several researches are going on for fabrication of semiconductors based on nano-fabrication processes that can work at higher temperatures and can provide efficiencies along with durability. The TEG technology has become a promising alternative green technology. Seebeck effect states that when a temperature difference is established across junction of two dissimilar metals or semiconductors a Voltage can be observed to be generated. This voltage is called Seebeck Voltage. This voltage can be utilized to power a load. The location of TEGs plays a vital role in the harnessing of waste heat thus weve placed our module over the muffler of a two-wheeler bike. The reference of dimensions is taken from the muffler of Royal Enfield Classic 350.Analysis is performed on the muffler for finding the heat distribution at the surface. The temperature becomes the input for the analysis of the Peltier module which further is analyzed for finding corresponding electrical voltage output. The hotter end of the plate is connected to the surface of the muffler while the cold end is attached to the fins and fins enclosure. The fins create a temperature difference by dissipating the heat in the atmosphere whereas the enclosure traps and guides the air perfectly over the fins increasing the time of contact for maximum heat convection. TEG module contains two sets of four Peltier modules connected in series with each set having its own set of fins at each end. The Peltier modules are separated by heavy insulation from each other in order to direct maximum heat to the ceramic hot plate ends of each Peltier module and also v protects the wire connecting the Peltier modules in series. The case has also been designed taken into consideration the dimensions of the muffler as described earlier. Each of the Peltier module is also designed and assigned with proper material properties through investigating various research papers and other sources available. With all the necessary information of load capacity, resistances and with the help of a proper circuit design having SEPIC DC-DC converter, a single
set of module (having 4 Peltier modules) is made to charge a 9V, 14Ah battery. The obtained results show the successful execution of designing a TEG system that can be used in two wheelers and works perfectly.
Keywords TEGs , Seebech Effect , Peltier module , SEPIC DC-DC Convertor , Waste Gas
-
INTRODUCTION
The energy wasted in terms of heat and parasitic losses during the conversion of chemical energy of the fuel to the mechanical energy by IC engine when emitted in atmosphere is harmful and contributes heavily in global warming. Thus, a lot of research and study is getting focused on the automotive industry for the purpose of creating engine models that have a better efficiency and are also green i.e. environment friendly. One such study includes harnessing the exhaust or waste gas heat for creating electrical energy that can be stored and later be utilized to increase performance of the vehicle simultaneously making the vehicle greener.
-
Termo Electric Generator (TEG)
The device that converts heat energy into electrical energy is called thermoelectric generator. As the name suggests therm- heat; electric- electricity; a TEG generates electricity from the heat energy it receives. This function is carried out by the virtue of Seebeck effect.
-
Seebech Effect
Seebeck Effect discovered by Thomas Johann Seebeck in 1821.When a temperature difference is established between hot and cold junctions of two dissimilar materials (metals or semiconductor), a voltage is generated i.e. Seebeck voltage. This effect occurs because of uneven energy/electrons distribution at hot and cold ends and due to kinetic energy absorbed by the electrons.
Fig. 2.1 Seebeck effect
-
-
WORKING OF TEG
A. Selecting a Template When a temperature difference is established between hot and cold junctions of two dissimilar materials (metals or semiconductor), a voltage is generated i.e. Seebeck voltage. This effect occurs because of uneven energy/electrons distribution at hot and cold ends and due to kinetic energy absorbed by the electrons. At the hotter end, the Fermi distribution of electrons is soft or there is higher concentration of electrons above the Fermi level while on the cold side the distribution is sharp. This means there is a higher Fermi energy on the hotter side than the colder end thus electrons will move from the hotter end to the colder end because of energy gradient. This flow of electrons is what gives electricity at the opposite direction. Semiconductors of p-n type are used in junctions for more current and are arranged in a manner as shown in figure 2.1 Here it can be observed that the top end of both the semiconductors consists of a plate that is heated (source) while the other end is kept as the cold (sink). The motion of electrons and holes can be observed, the arrangement is such that the current is achieved in one direction and this can be used to power a load or the energy can be stored in a battery.
-
ATEG DEVICE
The ATEG device can be broadly divided into two major parts, the mechanical part (clamping module), and the electronic part (stabilizer module):
-
Clamping Module
Define The study of components of the apparatus is as follows:
-
The mainframe consists of 2 major parts: the aluminum sheet cover and thermal insulation. At one end, the circular sheet is connected by a hinge joint and at the other end 2 permanent magnets are provided to keep the center of gravity as low as possible that eliminates tilting of the mainframe during vehicle in motion, locks and secures the apparatus to the muffler. The thermal insulation is provided on the inner surface of the Aluminum frame to insulate excess heat reaching the wire connecting modules and
concentrates the heat zones to the hot end ceramic5 plates of the 4 Peltier module set connected electrically in series. There are two such sets meaning 8 Peltier modules connected to the battery. The mainframe is such designed to fit on muffler of Royal Enfield Classic 350.
Fig. 2.3 labeled different views of clamping module.
-
The fins and the fin casing. Fins are provided on the outer end of the main frame over the Peltier modules to maximize heat dissipation at the cold end plate of each Peltier module. The fin increases surface contact which increases rate and area of convective heat dissipation into the atmosphere. The enclosure is uilt over the fins to channel the air directly to the fins and to delay the motion of the air in order to increase the time of contact of fins with trapped air which adds to the heat dissipation. The enclosure /case also protect the thin fins from any external physical damage.
Fig. 2.4 labeled cut-section view of clamping module
-
-
Stablizer module
-
Peltier Module
The Peltier module consists of 119 thermo electric element units connected in series with each unit having a p- and n- type semiconductor block connected at the top by means of copper plate and each semiconductor has its own copper plate at the bottom. The upper common plate is
connected to the ceramic5 plate at hot end while the bottom individual copper plates are connected to the colder ceramic5 plate of the Peltier module. The units are connected to each other in series by sharing bottom copper plates. A single module has one end of wire connected to the p-type semiconductors end and the other wire connected at the other end on an n-type semiconductor which is last in the series. The sequence of connection is p-n-p-n in a manner to pack maximum no. of units in a single module of 40 X 40 X 3 mm dimension.
fig. 2.5 Peltier module
Table 2.1
Working principle
SEPIC exchanges energy between capacitors and inductors in order to convert from input voltage to output voltage.The amount of energy convert is regulated by switch which is a MOSFET. The closing and opening of switch is controlled by pulse of required duty cycle produced from a pulse generator. Hence we can say that output of the converter depends on the duty cycle.
Duty cycle is the percentage of active Switch signal and is given by:-
Ceramic5
Plates (hot and cold)
Copper
(link b/w semiconductors and ceramic plates)
p type custom
k= 1.46 W/mK; = 1.87 X 10-4 V/K; = 1.6 X
10-5 m
n type custom
k= 1.46 W/mK; = -1.87 X 10-4 V/K; = 1.6 X
10-5 m
Ceramic5
Plates (hot and cold)
Copper
(link b/w semiconductors and ceramic plates)
p type custom
k= 1.46 W/mK; = 1.87 X 10-4 V/K; = 1.6 X
10-5 m
n type custom
k= 1.46 W/mK; = -1.87 X 10-4 V/K; = 1.6 X
10-5 m
fig. 2.6 thermoelectric element dimensions
-
SEPIC CONVERTER
The SEPIC is stand for single -ended primary inductance converter. A SEPIC converter is Boost converter followed by buck converter similar to traditional Buck boost converter. It is a non-inverting DC-DC converter that allows the electrical voltage at its output to be greater than, less than, or equal to that at its input. If suddenly battery discharges from rated voltage to a low voltage and any component need high voltage in this case SEPIC converter is effective as well. In SEPIC the input current is non- pulsating, but the output current is pulsating.
D= to*f
If duty cycle is below 0.5 output voltage is less than the input voltage a.k.a. stepping down and if it is above 0.5 than output voltage is more than input voltage a.k.a. Stepping up. When switch is close inductor L1 is charge by input voltage and L2 is charge by capacitor C1, diode is in off state and output is maintained by capacitor C2. As the switch closes the polarity of Inductors (L1,L2) get reversed and start discharging because of Lenz law that state that the direction of current remains same and capacitor C2 is charged from L2 through Diode and C1 from both L1 and input supply. In this way C2 maintain the constant electric voltage at output in same polarity as in input.
Fig. 2.8 SEPIC converter circuit (a) Closed (b) Open
Abbreviations
Words
Bi2Te3
Bismuth telluride
PbTe
Lead telluride
ATEG
Automotive Thermo electric generator
L1
Inductor 1
L2
Inductor2
C1
Capacitor1
C2
Capacitor2
R
Resistance
DC
Direct Current
AC
Alternate Current
D
Duty Cycle
f
Frequency
to
Pulse Width
b/w
Between
Max
Maximum
Min
Minimum
kW
kilowatt
CO2
Carbon dioxide
I
Current
V
Volt
Vc
change in capacitance Voltage
IL
change in inductor current
Abbreviations
Words
Bi2Te3
Bismuth telluride
PbTe
Lead telluride
ATEG
Automotive Thermo electric generator
L1
Inductor 1
L2
Inductor2
C1
Capacitor1
C2
Capacitor2
R
Resistance
DC
Direct Current
AC
Alternate Current
D
Duty Cycle
f
Frequency
to
Pulse Width
b/w
Between
Max
Maximum
Min
Minimum
kW
kilowatt
CO2
Carbon dioxide
I
Current
V
Volt
Vc
change in capacitance Voltage
IL
change in inductor current
There are two modes in which circuit works: –
-
Continuous mode-
A SEPIC is said to be in continuous-conduction mode ("continuous mode") if the currents through inductors L1 and L2 never fall to zero during an operating cycle. During a SEPIC's steady-state operation.
-
Discontinuous mode-
A SEPIC is said to be in discontinuous-conduction mode or discontinuous mode if the current through either of inductors L1 or L2 is allowed to fall to zero during an operating cycle. As in our case the inductor current IL1 and IL2 never fall to zero during an operating cycle so we work in Continuous mode if inductor current falls to zero than output supply gets discontinues.
Symbol
Units
°F
Degree Fahrenheit
°C
Degree Celsius
K
Kelvin
Kg
kilogram
m
metre
mm
millimetre
cm
centimetre
J
Joule
W
Watt
Ohm
s
Second
A
Ampere
H
micro Henry
p>F micro Farad
Ah
Ampere-Hour
d,
Density
Cp
Specific heat
k ,
thermal conductivity
thermal diffusivity
Symbol
Units
°F
Degree Fahrenheit
°C
Degree Celsius
K
Kelvin
Kg
kilogram
m
metre
mm
millimetre
cm
centimetre
J
Joule
W
Watt
Ohm
s
Second
A
Ampere
H
micro Henry
F
micro Farad
Ah
Ampere-Hour
d,
Density
Cp
Specific heat
k ,
thermal conductivity
thermal diffusivity
-
-
-
Units
Abbreviations
Words
TEG
Thermo electric generator
TE
Thermo electric
Emf
Electromotive force
dir.
directional
a.k.a
as known as
QH
hot side heat flow rate
QL
cold side heat flow rate
ZT
Figure of merit
S
Seebeck Coefficient
electric conductivity
T
Temperature
Abbreviations
Words
TEG
Thermo electric generator
TE
Thermo electric
Emf
Electromotive force
dir.
directional
a.k.a
as known as
QH
hot side heat flow rate
QL
cold side heat flow rate
ZT
Figure of merit
S
Seebeck Coefficient
electric conductivity
T
Temperature
-
Abbreviations
CONCLUSION
The successful completion of project proves the possibility of implementation of ATEGs in two wheelers. Although TEG has less efficiency and its applications is limited due to working temperature range, researches are going on for fabrication of semiconductors based on nano-fabrication processes that can work at higher temperatures and can provide efficiencies of about 20% along with durability. Referring to the proposed research and expectation results, this project was successfully able to provide an alternative approach of harnessing electricity. The obtained results show that successful execution of designing a ATEG system of high efficiency will be possible in near future.
REFERENCES
[1] https://iopscience.iop.org/article/10.1088/1757-899X/402/1/012174/pdf-
https://www.ijariit.com/manuscripts/v3i2/V3I2-1451.pdf
-
https://en.wikipedia.org/wiki/Automotive_thermoelectric_generator
-
https://www.ijert.org/generation-of-power-using-heat-from-exhaust- gas-by-heat-generator
-
https://creativecommons.org/licenses/by/4.0/
-
https://thermoelectric-generator.com/wp- content/uploads/2014/04/CMO-25-42S-OXIDE-NEW.pdf
-
https://www.researchgate.net/publication/257554998_Lead_telluride_al loy_thermoelectrics
-
http://edge.rit.edu/edge/P11462/public/Battery%20Chargers/TE%20bat tery%20charger%20paper.pdf