
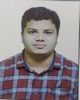
- Open Access
- Authors : Ajinkya Ramrao Yadav , Rahul D. Shelke , Navnath S. Kalyankar
- Paper ID : IJERTV9IS120111
- Volume & Issue : Volume 09, Issue 12 (December 2020)
- Published (First Online): 17-12-2020
- ISSN (Online) : 2278-0181
- Publisher Name : IJERT
- License:
This work is licensed under a Creative Commons Attribution 4.0 International License
Study and Comparative Analysis of Effect of SiC and Graphite Composite on Aluminiun using RSM Methodology
Mr. Ajinkya Ramrao Yadav ,
-
, Mechanical Engineering,
Everest College of Engineering and Technology Aurangabad.
Prof. Rahul D. Shelke, Associate professor,
Mechanical Engineering, Everest college of Engineering And Technology Aurangabad.
Prof. Navnath S. Kalyankar Assistant professor,
Mechanical Engineering, Everest college of Engineering And Technology Aurangabad.
Abstract:- In this present work, systematic study has been conducted to investigate the wear phenomenon by adding micron size silicon carbide and graphite particles into Al6061 base. Al6061 compound was taken as the base lattice to which SiC and graphite particulates were utilized as fortifications. 3 wt. %, 6 wt. %, & 9 wt. % of SiC and 3 wt. %, 6 wt. %, & 9 wt. % of graphite were introduced to the base framework. The wear behavior analysis, which uncovered the uniform appropriation of SiC and graphite content in the Al matrix. Pin on-disc equipment was utilized to assess the volumetric wear loss of arranged samples, in which EN32 steel disc was utilized as the counter face. The outcomes uncovered that the volumetric wear misfortune was expanded with increment in applied load, disc sp eed and sliding distance for every one of the specimens. The outcomes additionally showed that the volumetric wear loss of the Al 6061-9 % SiC-9 % graphite composite was smaller than the Al 6061-9 % SiC-9 % graphite. The worn out surfaces were portrayed by RSM analysis.
-
INTRODUCTION
-
Metal Matrix Composite
The metal matrix composites (MMCs) are very attractive materials for several applications. For many researches the term MMCs is often equated with the term light metal matrix composites. Substantial progress in the development of light metal matrix composites has been achieved in recent decades, so that they could be introduced into the most important applications.
Aluminum matrix composites (AMCs) are the competent material in the industrial world. Efforts have been made to develop aluminium metal matrix composites in recent years due to their low density, high strength, and superior creep resistance and have great potential in automotive and aerospace applications. Aluminium (Al) is the second most widely used metal in the world today after iron. It has a low density (2.7 g/cc), superior malleability, excellent corrosion resistance, good thermal conductivity (237 W/mK), very low electrical resistivity (2.65*10-8m) and good formability. Its Youngs modulus is 70 GPa and its Vickers hardness is 60 to 70 VHN. Al has a melting point of 660.32°C and at high temperatures, the strength of Al decreases. However, the demand for Al and its alloys having a much higher strength is increasing [3].
Al matrix composites (AMCs) have been widely used in automobile and aerospace industries due to their excellent physical and mechanical properties. To overcome these shortcomings and to meet the ever increasing demand of modern day technology, composites are one of the most promising materials [3].
-
Alloy – Aluminium 6061
6061 (UNS designation A96061) is a precipitation-hardened aluminum alloy, containing magnesium and silicon as its major alloying elements. Originally called "Alloy 61S", it was developed in 1935. It has good mechanical properties, exhibits good weld ability, and is very commonly extruded (second in popularity only to 6063). It is one of the most common alloys of aluminum for general-purpose use. It is commonly available in pre-tempered grades such as 6061-O (annealed), tempered grades such as 6061-T6 (solutionized and artificially aged) and 6061-T651 (solutionized, stress-relieved stretched and artificially aged).
6061 Aluminum Alloy Composition by Mass %
Al
Mg
Si
Fe
Cu
Cr
Zn
Ti
Mn
Remainder
95.85 – 98.56
0.8 – 1.2
0.40 – 0.8
0.0 – 0.7
0.15 – 0.40
0.04 – 0.35
0.0 – 0.25
0.0 – 0.25
0.0 – 0.15
0.05 each, 0.15 total
Table 1: Chemical Composition of Al-6061
-
Reinforcement
-
Silicon Carbide (SiC)
Silicon carbide (SiC), also known as carborundum semiconductor, is a containing silicon and carbon. It occurs in nature as the extremely rare mineral moissanite. Synthetic SiC powder has been mass-produced since 1893 for use as an abrasive. Grains of silicon carbide can be bonded together by sintering to form very hard ceramics that are widely used in applications requiring high endurance, such as car brakes, car clutches and ceramic plates in bulletproof vests. Electronic applications of silicon carbide such as light-emitting diodes (LEDs) and detectors in early radios were first demonstrated around 1907. SiC is used in semiconductor electronics devices that operate at high temperatures or high voltages, or both. Large single crystals of silicon carbide can be grown by the Lely method and they can be cut into gems known as synthetic moissanite.
Aluminumsilicon alloys exhibit several features of tribological behavior which are similar to those of aluminum- based MMCs. Zum Gahr (1987) has summarized the effect of silicon content in AlSi alloys in dry sliding wear. Wear resistance is improved in mild wear conditions if the silicon content in AlSi alloys is increased. Andrews. (1985) measured mild wear of several hypereutectic AlSi pins with approximately the same matrix composition sliding against an M2 steel disc. The wear resistance of each alloy increased with primary silicon content up to a maximum at 17% Si (total matrix and primary Si content of 26%). A transition load at which wear rates changed from mild to severe was also identified for different silicon contents and sliding speeds. Based on data from Andrews. (1985), a loadvelocity diagram is plotted in that indicates the beneficial effect of silicon content on resistance to severe wear. The onset of severe wear occurred at a characteristic transition load, at which a small quantity of aluminum adhered to the steel disk. This transferred deposit grew in size and initiated gross plastic deformation and fracture of the aluminum alloy pin as the test progressed. Material removal occurred by subsurface crack propagation in a composite transfer layer of aluminum and crushed silicon particles during mild wear, and by subsurface cracking at silicon particles in the highly deformed wear zone during severe wear.
-
Graphite (Gr)
-
The materials are commonly used for self-lubricating plain bearings or electrical contacts. They are proprietary materials owned by the Graphite Metallizing Corp. Graphite/metal alloys take advantage of graphites special properties: it is compared to a deck of cards: individual layers slide off the top surface easily. This phenomenon gives the material a self-lubricating ability found in no other material. Grapalloys self-lubricating features mean the operator can eliminate grease or oil that normally evaporates, congeals, or solidifies causing premature failure. The graphite matrix can be filled with a variety of impregnates to enhance chemical, mechanical and tribological properties. The material provides a constant, low coefficient of friction rather than just a surface layer, helping to protect against catastrophic failure. Lubrication is maintained even during linear motion; lubricant is not drawn out, and dust is not pulled in. Graphalloy wear components also improve reliability during low speed operation, frequent starts and stops, and switchovers from standby to continuous running. Graphalloy bushings are available in more than 100 grades of material in any desired size or geometry, including cylindrical, with or without grooves; flange or double flange; split; and metal-backed.
-
-
EXPERIMENTAL SET-UP
Work Material
Al-6061 + SiC + Gr
-
Chemical composition of base alloy
Sr. No.
Material
Minimum
Maximum
1.
Silicon
0.4%
0.8%
2.
Iron
no minimum
0.7%
3.
Copper
no minimum
0.15%
4.
Manganese
0.8%
0.4%
5.
Magnesium
0.04%
1.2%
6.
Chromium
no minimum
0.25%
7.
Zinc
no minimum
0.15%
8.
Titanium
0.05% each
0.15% total
9.
Remainder aluminium (95.8598.56%)
Table 2: Chemical Composition of Base Alloy
-
Experimental Flow chart
Fig 1: Experimental Flow Chart
Matreial Selection
Material Purchasing
Stir Casting Of aluminium 6061 + composite
DOE by using RSM Methodology
Forming Pins Of 12 X 30
Mm Size
PIN ON DISC
Experimentation
Wear Parameters Testing
Comparison of Results And Graphical RSM Analysis Of Experimentation Results
Result & Conclusion
-
Fabrication of Al MMC (AL 6061 + vol. % of SiC + Vol. % Gr) by Stir Casting
Aluminium Al6101 of commercial grade was used as the matrix material SiC and graphite particles with size varying from 26 to 30 m was used as the reinforcement material. Table 1 displays the chemical composition of Al6101 used in this research work. An orthodox casting technique was used for the manufacturing of composites. Set-up for stir casting technique is displayed in Fig. The proper amount of Al6101 was heated in a graphite crucible placed in an electric furnace. The graphite was also preheated to 720 C with the help of a separate electric furnace. After melting the Al6101 in the electric furnace, graphite reinforcement particles (preheated) were added and mixed molten mixture was stirred at 550 rpm for 10 min by using an electric motor which is fitted with a mechanical stirrer. The temperature was kept constant (800 C) during whole stirring.
Fig 2: Stir casting machine
The molten aluminium alloy split into droplets because of shear force imparted by the stirrer at the presence of graphite. Now the molten mixture was exiled from the graphite crucible into a permanent preheated (500 C) steel mould. The molten mixture was allowed to solidify in steel mould. The casted composite was subjected to T6 heat treatment. Heat treated composite was tested for various tests. The same procedure was followed to manufacture all other composition. The composites were manufactured at 3, 6 and 9 wt. % of SiC & graphite reinforcement particles.
-
-
WEAR TESTING
-
Technical Specification of Pin-On-Disc Machine ASTM G99 Standard.
Sr. No.
Specifications
Values
1
Disc rotation Speed
1000 rpm
2
Pin Diameter Range
ø30×12 mm
3
Disc Size (mm)
ø165×8 mm thickness
4
Sliding speed
1000 rpm
5
Wear Track Diameter
ø60×70 mm
6
Material
EN31
7
Disc hardness
58-60 HRC
8
Standard Used
G99 ASTM
Table 3: Technical Specification of Pin-On-Disc Machine
-
Wear testing (Pin-On-Disc Machine G99 ASTM)
The size of plate is 12 mm diameter x 700 mm, Experiment did partening of material on lathe machine the final size of matreial is 12 x 30 mm.
The pin was held against the counter face of a rotating disc (EN32 steel disc) with wear track diameter 80 mm. The pin was loaded against the disc through a dead weight loading system. The wear test for all specimens was conducted under the normal loads of 50N, 100N, 150N, 200N.
Fig 3: Wear Testing Setup
The pin samples were 30 mm in length and 12 mm in diameter. The samples and wear track were cleaned with acetone and weighed (up to an accuracy of 0.0001 gm. using microbalance) prior to and after each test. The wear rate was calculated from the height loss technique and expressed in terms of wear volume loss per unit sliding distance.
-
Procedure of Experimentation
In this study, Pin-on-Disc testing method was used for tri-biological characterization. The test procedure is as follows:
-
Run-in-wear was performed in this stage. This stage avoids initial turbulent period associated with friction and wear curves Final stage/ third stage is the actual testing called constant/ steady state wear.
-
This stage is the dynamic competition between material transfer processes (transfer of material from pin onto the disc and formation of wear debris and their subsequent removal). Before the test, both the pin and disc were cleaned with ethanol soaked cotton.
Fig 4: Test Specimen
3.3.1 Weight Loss & Wear Loss
The alloy and composite samples are cleaned thoroughly with acetone. Each sample is then weighed using a digital balance having an accuracy of ± 0.1 mg. After that, the sample is mounted on the pin holder of the tribo-meter ready for wear test. The specific wear rates of the materials were obtained by
W = m /×L×F Where,
W denotes specific wear rates in mm3 /N- w is the weight loss measured in grams,
p density of the worn material in g/mm3 and F is the applied load in N.
L Sliding Distance in m
The experimentation is performed on the EN 31 disc rotating at a maximum speed of 500, 1500 & 2000 rpm with the various loads of 50 N, 100 N, 150 N, and 200 N. The results we got from the experimentation is as plotted below in the form of table.
-
-
EXPERIMENTAL WEAR CALCULATION.
-
4.1 Specific Wear Rate Calculation.
-
with (Al94% Sic3% Gr3%) Variation of wear with load (N)
Sr. No.
Speed
Load
Time
wear m
Sliding Velocity (V)
Sliding Distance
Specific wear rate
Rpm
N
Sec
gm.
m/sec
m
mm³/Nm
500
50
600
0.0194
1.5708
942.45
1.519E-04
2
500
100
600
0.0754
1.5708
942.45
2.952E-04
3
500
150
600
0.1197
1.5708
942.45
3.124E-04
4
500
200
600
0.1758
1.5708
942.45
3.442E-04
5
1000
50
600
0.1089
3.1415
1884.9
4.264E-04
6
1000
100
600
0.2568
3.1415
1884.9
5.027E-04
7
1000
150
600
0.4965
3.1415
1884.9
6.480E-04
8
1000
200
600
0.6906
3.1415
1884.9
6.760E-04
9
1500
50
600
0.8690
4.7123
2827.35
2.268E-03
10
1500
100
600
1.8340
4.7123
2827.35
2.394E-03
11
1500
150
600
2.8556
4.7123
2827.35
2.485E-03
12
1500
200
600
4.1581
4.7123
2827.35
2.713E-03
Table 4: With (Al94% Sic3% Gr3%) Variation of wear with load (N)
-
With (Al88% Sic6% Gr6%) Variation of wear with load (N)
Sr. No.
Speed
Load
Time
wear m
Sliding Velocity (V)
Sliding Distance
Specific wear rate
Rpm
N
Sec
gm.
m/sec
m
mm³/Nm
1
500
50
600
0.0174
1.5708
942.45
1.363E-04
2
500
100
600
0.0670
1.5708
942.45
2.623E-04
3
500
150
600
0.1060
1.5708
942.45
2.767E-04
4
500
200
600
0.1701
1.5708
942.45
3.329E-04
5
1000
50
600
0.0930
3.1415
1884.9
3.642E-04
6
1000
100
600
0.2208
3.1415
1884.9
4.323E-04
7
1000
150
600
0.3865
3.1415
1884.9
5.044E-04
8
1000
200
600
0.5906
3.1415
1884.9
5.781E-04
9
1500
50
600
0.7540
4.7123
2827.35
1.968E-03
10
1500
100
600
1.6740
4.7123
2827.35
2.185E-03
11
1500
150
600
2.6320
4.7123
2827.35
2.290E-03
12
1500
200
600
3.8760
4.7123
2827.35
2.529E-03
Table 5: With (Al88% Sic6% Gr6%) Variation of wear with load (N)
-
With (Al82% Sic9% Gr9%) Variation of wear with load (N)
Sr. No.
Speed
Load
Time
wear m
Sliding Velocity (V)
Sliding Distance
Specific wear rate
Rpm
N
Sec
gm.
m/sec
m
mm³/Nm
1
500
50
600
0.0149
1.5708
942.45
1.167E-04
2
500
100
600
0.0570
1.5708
942.45
2.232E-04
3
500
150
600
0.0990
1.5708
942.45
2.584E-04
4
500
200
600
0.1400
1.5708
942.45
2.741E-04
5
1000
50
600
0.0840
3.1415
1884.9
3.290E-04
6
1000
100
600
0.2018
3.1415
1884.9
3.951E-04
7
1000
150
600
0.3265
3.1415
1884.9
4.261E-04
8
1000
200
600
0.4806
3.1415
1884.9
4.704E-04
9
1500
50
600
0.6740
4.7123
2827.35
1.759E-03
10
1500
100
600
1.4138
4.7123
2827.35
1.845E-03
11
1500
150
600
2.2340
4.7123
2827.35
1.944E-03
12
1500
200
600
3.1086
4.7123
2827.35
2.029E-03
Table 6: With (Al82% Sic9% Gr9%) Variation of wear with load (N)
-
Graphical Comparison of specific wear rate.
-
Load vs. wear rate at 500 rpm
4.00E-04
Load Vs. wear rate @500 rpm
4.00E-04
Load Vs. wear rate @500 rpm
3.50E-04
3.00E-04
2.50E-04
2.00E-04
AL94%+Sic3%+Gr3%
3.50E-04
3.00E-04
2.50E-04
2.00E-04
AL94%+Sic3%+Gr3%
50
100
Load
150
200
50
100
Load
150
200
1.50E-04
1.50E-04
AL88%+SiC6%+Gr6%
AL88%+SiC6%+Gr6%
1.00E-04
1.00E-04
AL82%+SiC9%+Gr9%
AL82%+SiC9%+Gr9%
5.00E-05
0.00E+00
5.00E-05
0.00E+00
Wear rate mm³/Nm
Graph 1: Load vs. Wear rate at 500 rpm
-
Load vs. wear rate at 1000 rpm
8.00E-04
7.00E-04
Wear rate mm³/Nm
Wear rate mm³/Nm
6.00E-04
5.00E-04
4.00E-04
3.00E-04
2.00E-04
1.00E-04
0.00E+00
Load Vs. wear rate @1000 rpm
AL94%+Sic3%+Gr3% AL88%+SiC6%+Gr6% AL82%+SiC9%+Gr9%
50 100
Load
150 200
Graph 2: Load vs. Wear rate at 1000 rpm
4.2.2 Load vs. wear rate at 1000 rpm
3.00E-03
Load Vs. wear rate @1500 rpm
2.50E-03
Wear rate mm³/Nm
Wear rate mm³/Nm
2.00E-03
1.50E-03
1.00E-03
AL94%+Sic3%+Gr3% AL88%+SiC6%+Gr6% AL82%+SiC9%+Gr9%
5.00E-04
0.00E+00
50 100
Load
150 200
Graph 3: Load vs. Wear rate at 1500 rpm
-
-
ANALYSIS OF RESULTS AND DISCUSSION BY USING RSM METHODOLOGY
-
RSM Experimental Design & Analysis
Response Surface Methodology, RSM (also known as Response Surface Modeling) is a technique to optimize the response(s) when two or more quantitative factors are involved. The dependent variables are known as responses, and the independent variables or factors are primarily known as the predictor variables in response surface methodology. While p-values are used for a particular point such as to test the hypothesis of whether the 70-degree Fahrenheit is the most comfortable temperature or not, the response surface is useful in determining a range of temperatures for the same comfort level. As maintaining the temperature exactly at a 70-degree could be very expensive, maintaining the temperatures within a range is often desired for cost-effective solution. Moreover, keeping very cool in summer or very hot in winter would be very wasteful. Response Surface Methodology, RSM, is very useful to optimize variables/factors more practically as compared to just the statistical significance test for a particular point (point estimate is the statistical jargon). Minitab 19 Software is used for RSM.
-
Components of Experimental Design
Consider the following diagram of a cake-baking process. There are three aspects of the process that are analyzed by a designed experiment:
-
Factors, or inputs to the process. Factors can be classified as either controllable or uncontrollable variables. In this case, the controllable factors are the ingredients for the cake and the oven that the cake is baked in. The controllable variables will be referred to throughout the material as factors. Note that the ingredients list was shortened for this example – there could be many other ingredients that have a significant bearing on the end result (oil, water, flavoring, etc). Likewise, there could be other types of factors, such as the mixing method or tools, the sequence of mixing, or even the people involved. People are generally considered a Noise Factor (see the glossary) – an uncontrollable factor that causes variability under normal operating conditions, but we can control it during the experiment using blocking and randomization. Potential factors can be categorized using the Fishbone Chart (Cause & Effect Diagram) available from the Toolbox.
-
Levels, or settings of each factor in the study. Examples include the oven temperature setting and the particular amounts of sugar, flour, and eggs chosen for evaluation.
-
Response, or output of the experiment. In the case of cake baking, the taste, consistency, and appearance of the cake are measurable outcomes potentially influenced by the factors and their respective levels. Experimenters often desire to avoid optimizing the process for one response at the expense of another. For this reason, important outcomes are measured and analyzed to determine the factors and their settings that will provide the best overall outcome for the critical-to-quality characteristics – both measurable variables and assessable attributes.
Fig 5: Factors, Level & Response
-
-
Experimental Result of wear Test on (Al 94% SiC3% Gr3%) by using RSM Methodology
Load (N)
Speed (RPM)
Time (sec)
Wear (mm³/Nm)
StdOrder
RunOrder
Blocks
PtType
50
500
600
1.519E-04
1
1
1
1
100
500
600
2.952E-04
2
2
1
1
150
500
600
3.124E-04
3
3
1
1
200
500
600
3.442E-04
4
4
1
1
50
1000
600
4.264E-04
5
5
1
1
100
1000
600
5.027E-04
6
6
1
1
150
1000
600
6.480E-04
7
7
1
1
200
1000
600
6.760E-04
8
8
1
1
50
1500
600
2.268E-03
9
9
1
1
100
1500
600
2.394E-03
10
10
1
1
150
1500
600
2.485E-03
11
11
1
1
200
1500
600
2.713E-03
12
12
1
1
Table 7: wear test on (Al94% SiC3% Gr3%) by RSM
-
Response Surface Regression: Wear (mm³/Nm) versus Load (N), Speed (RPM), (Al 94% Sic3% Gr3%)
-
Coded Coefficients
Term
Coef
SE Coef
T-Value
P-Value
VIF
Constant
0.000569
0.000026
21.79
0.000
Load (N)
0.000146
0.000016
8.88
0.000
1.00
Speed (RPM)
0.001095
0.000015
73.10
0.000
1.00
Load (N)*Load (N)
-0.000011
0.000028
-0.38
0.714
1.00
Speed (RPM)*Speed (RPM)
0.000807
0.000026
31.12
0.000
1.00
Load (N)*Speed (RPM)
0.000062
0.000020
3.11
0.021
1.00
-
Model Summary
S
R-sq
R-sq(adj)
R-sq(pred)
0.0000424
99.91%
99.83%
99.46%
-
Analysis of Variance
Source
DF
Adj SS
Adj MS
F-Value
P-Value
Model
5
0.00011
0.000002
1280.12
0.000
Linear
2
0.000010
0.000005
2711.07
0.000
Load (N)
1
0.000000
0.000000
78.92
0.000
Speed (RPM)
1
0.000010
0.000010
5343.21
0.000
Square
2
0.000002
0.000001
484.41
0.000
Load (N)*Load (N)
1
0.000000
0.000000
0.15
0.714
Speed (RPM)*Speed (RPM)
1
0.000002
0.000002
968.67
0.000
2-Way Interaction
1
0.000000
0.000000
9.66
0.021
Load (N)*Speed (RPM)
1
0.000000
0.000000
9.66
0.021
Error
6
0.000000
0.000000
Total
11
0.000011
-
Regression Equation in Uncoded Units
Wear (mm³/Nm)
=
0.001545 + 0.000001 Load (N) – 0.000004 Speed (RPM)
– 0.000000 Load (N)*Load (N) + 0.000000 Speed (RPM)*Speed (RPM)
+ 0.000000 Load (N)*Speed (RPM)
-
-
Factorial Plots for Wear (mm³/Nm), (AL 93% Sic 3% Gr3%)
Graph 4: Main effects plot for wear (Al 94% Sic3% Gr3%)
Graph 5: Interaction plot for wear (Al 94% Sic3% Gr3%)
-
Contour Plot of Wear (mm³/Nm) vs. Speed (RPM), Load (N) (AL 94% Sic 3% Gr3%)
Graph 6: Contour Plot of Wear (mm³/Nm) vs. Speed (RPM), Load (N) (AL 94% Sic 3% Gr3%)
-
Surface Plot of Wear (mm³/Nm) vs. Speed (RPM), Load (N) (AL 94% Sic 3% Gr3%)
Graph 7: Surface Plot of Wear (mm³/Nm) vs. Speed (RPM), Load (N) (AL 93% Sic 3% Gr3%)
-
-
Experimental Result of wear Test on (Al88% SiC6% Gr6%) by using RSM Methodology
Load (N)
Speed (RPM)
Time (sec)
Wear (mm³/Nm)
StdOrder
RunOrder
Blocks
PtType
50
500
600
1.363E-04
1
1
1
1
100
500
600
2.623E-04
2
2
1
1
150
500
600
2.767E-04
3
3
1
1
200
500
600
3.329E-04
4
4
1
1
50
1000
600
3.642E-04
5
5
1
1
100
1000
600
4.323E-04
6
6
1
1
150
1000
600
5.044E-04
7
7
1
1
200
1000
600
5.781E-04
8
8
1
1
50
1500
600
1.968E-03
9
9
1
1
100
1500
600
2.185E-03
10
10
1
1
150
1500
600
2.290E-03
11
11
1
1
200
1500
600
2.529E-03
12
12
1
1
Table 8: wear test on (Al88% SiC6% Gr6%) by RSM
-
Response Surface Regression: Wear (mm³/Nm) versus Load (N), Speed (RPM), (Al 88% SiC6% Gr6%)
-
Coded Coefficients
Term
Coef
SE Coef
T-Value
P-Value
VIF
Constant
0.000474
0.000029
16.41
0.000
Load (N)
0.000155
0.000018
8.56
0.000
1.00
Speed (RPM)
0.000996
0.000017
60.09
0.000
1.00
Load (N)*Load (N)
-0.000008
0.000030
-0.26
0.806
1.00
Speed (RPM)*Speed (RPM)
0.000778
0.000029
27.11
0.000
1.00
Load (N)*Speed (RPM)
0.000089
0.000022
4.00
0.007
1.00
-
Model Summary
S
R-sq
R-sq(adj)
R-sq(pred)
0.0000469
99.86%
99.75%
99.10%
alysis of Variance
Source
DF
Adj SS
Adj MS
F-Value
P-Value
Model
5
0.000010
0.000002
887.04
0.000
Linear
2
0.000008
0.000004
1842.19
0.000
Load (N)
1
0.000000
0.000000
73.28
0.000
Speed (RPM)
1
0.000008
0.000008
3611.11
0.000
Square
2
0.000002
0.000001
367.43
0.000
Load (N)*Load (N)
1
0.000000
0.000000
0.07
0.806
Speed (RPM)*Speed (RPM)
1
0.000002
0.000002
734.79
0.000
2-Way Interaction
1
0.000000
0.000000
15.98
0.007
Load (N)*Speed (RPM)
1
0.000000
0.000000
15.98
0.007
Error
6
0.000000
0.000000
Total
11
0.000010
alysis of Variance
Source
DF
Adj SS
Adj MS
F-Value
P-Value
Model
5
0.000010
0.000002
887.04
0.000
Linear
2
0.000008
0.000004
1842.19
0.000
Load (N)
1
0.000000
0.000000
73.28
0.000
Speed (RPM)
1
0.000008
0.000008
3611.11
0.000
Square
2
0.000002
0.000001
367.43
0.000
Load (N)*Load (N)
1
0.000000
0.000000
0.07
0.806
Speed (RPM)*Speed (RPM)
1
0.000002
0.000002
734.79
0.000
2-Way Interaction
1
0.000000
0.000000
15.98
0.007
Load (N)*Speed (RPM)
1
0.000000
0.000000
15.98
0.007
Error
6
0.000000
0.000000
Total
11
0.000010
-
An
-
Regression Equation in Uncoded Units
Wear (mm³/Nm)
=
0.001610 + 0.000000 Load (N) – 0.000005 Speed (RPM)
– 0.000000 Load (N)*Load (N) + 0.000000 Speed (RPM)*Speed (RPM)
+ 0.000000 Load (N)*Speed (RPM)
-
-
Factorial Plots for Wear (mm³/Nm) (Al 88% SiC6% Gr6%)
Graph 8: Main effects plots for wear (AL88% Sic6% Gr6%)
Graph 9: Interaction plot for wear (AL88% Sic6% Gr6%)
-
Contour Plot of Wear (mm³/Nm) vs. Speed (RPM), Load (N) (Al 88% SiC6% Gr6%)
Graph 10: Counter plots for wear (AL88% Sic6% Gr6%)
-
Surface Plot of Wear (mm³/Nm) vs. Speed (RPM), Load (N) (Al 88% SiC6% Gr6%)
Graph 11: Surface plots for wear (AL88% Sic6% Gr6%)
-
-
Experimental Result of wear Test on (Al82% SiC9% Gr9%) by using RSM Methodology
Load (N)
Speed (RPM)
Time (sec)
Wear (mm³/Nm)
StdOrder
RunOrder
Blocks
PtType
50
500
600
1.167E-04
1
1
1
1
100
500
600
2.232E-04
2
2
1
1
150
500
600
2.584E-04
3
3
1
1
200
500
600
2.741E-04
4
4
1
1
50
1000
600
3.290E-04
5
5
1
1
100
1000
600
3.951E-04
6
6
1
1
150
1000
600
4.261E-04
7
7
1
1
200
1000
600
4.704E-04
8
8
1
1
50
1500
600
1.759E-03
9
9
1
1
100
1500
600
1.845E-03
10
10
1
1
150
1500
600
1.944E-03
11
11
1
1
200
1500
600
2.029E-03
12
12
1
1
Table 9: wear test on (Al82% SiC9% Gr9%) by RSM
-
Response Surface Regression: Wear (mm³/Nm) versus Load (N), Speed (RPM) (Al82% SiC9% Gr9%)
-
Coded Coefficients
Term
Coef
SE Coef
T-Value
P-Value
VIF
Constant
0.000417
0.000015
28.01
0.000
Load (N)
0.000093
0.000009
9.99
0.000
1.00
Speed (RPM)
0.000838
0.000009
98.16
0.000
1.00
Load (N)*Load (N)
-0.000021
0.000016
-1.36
0.223
1.00
Speed (RPM)*Speed (RPM)
0.000651
0.000015
44.02
0.000
1.00
Load (N)*Speed (RPM)
0.000030
0.000011
2.61
0.040
1.00
-
Model Summary
S
R-sq
R-sq(adj)
R-sq(pred)
0.0000241
99.95%
99.91%
99.69%
-
Analysis of Variance
Source
DF
Adj SS
Adj MS
F-Value
P-Value
Model
5
0.000007
0.000001
2336.50
0.000
Linear
2
0.000006
0.000003
4867.88
0.000
Load (N)
1
0.000000
0.000000
99.86
0.000
Speed (RPM)
1
0.000006
0.000006
9635.90
0.000
Square
2
0.000001
0.000001
969.97
0.000
Load (N)*Load (N)
1
0.000000
0.000000
1.85
0.223
Speed (RPM)*Speed (RPM)
1
0.000001
0.000001
1938.09
0.000
2-Way Interaction
1
0.000000
0.000000
6.82
0.040
Load (N)*Speed (RPM)
1
0.000000
0.000000
6.82
0.040
Error
6
0.000000
0.000000
Total
11
0.000007
-
Regression Equation in Uncoded Units
Wear (mm³/Nm)
=
0.001230 + 0.000001 Load (N) – 0.000004 Speed (RPM)
– 0.000000 Load (N)*Load (N)
+ 0.000000 Speed (RPM)*Speed (RPM)
+ 0.000000 Load (N)*Speed (RPM)
-
-
Factorial Plots for Wear (mm³/Nm) (Al82% SiC6% Gr6%)
Graph 12: Main Effects plot for wear (AL82% Sic9% Gr9%)
Graph 13: Interaction plot for wear (AL82% Sic9% Gr9%)
-
Contour Plot of Wear (mm³/Nm) vs. Speed (RPM), Load (N) (Al82% SiC6% Gr6%)
Graph 14: Counter plot for wear (AL82% Sic9% Gr9%)
-
Surface Plot of Wear (mm³/Nm) vs. Speed (RPM), Load (N)
-
-
(Al82% SiC6% Gr6%)
Graph 15: Surface plot for wear vs. Speed, Load (AL82% Sic9% Gr9%)
CONCLUSION
-
Aluminium alloy & its composite SiC, graphite have been effectively fabricated by stir casting method using two step addition of particles in the melt.
-
Al6061, SiC & Graphite composites were shown uniform distribution of reinforcement particles in the base matrix material.
-
The wear resistance of Al6061 alloy increased after addition of SiC & Graphite particle. The Volumetric wear loss affected by load & Sliding speed.
-
Wear loss decrease with increase in percentage of Sic & Graphite composite. I.e. Addition of SiC 9Vol% and Gr 9Vol% to Al6061 decrease the Specific wear rate.
-
The hardness, ultimate tensile strength as well as percentage of elongation reduce with increase in SiC & Graphite content.
-
Hardness increases with increase in wt % of SiC & Gr
-
Tensile Strength, Yield Strength and % Elongation increases with increase in wt % of SiC & Gr upto 15 %
-
From the results, the use of steel particles as replacement of conventional reinforcements such as SiC & Gr in AMCs, has great promise for applications where high specific strength, toughness and wear resistance are desired in service.
-
The hardness of the composites increased approximately by 15% with increase in steel particles from 3 to 9 wt.% of SiC & Gr; also, for the same range of steel concentration, the ultimate tensile strength increased with increase in steel wt.% and were all higher than that of 9 wt.% reinforced SiC & Gr.The specific strength and fracture toughness equally followed the same trend with respect to steel concentration, and comparison with SiC & Gr reinforced composite composition
REFERENCES
-
Kenneth Kanayo Alaneme, Adetomilola Victoria Fajemisin, Nthabiseng Beauty Maledi Development of aluminium-based composites reinforced with steel and graphite particles: structural, mechanical and wear characterization. Received 2 November 2017 Accepted 30 April 2018
-
Pardeep Sharmaa, Krishan Paliwal, Ramesh Kumar Garg, Satpal Sharmac, Dinesh Khanduja A study on wear behaviour of Al/6101/graphite composites, Received 13 October 2016 Received in revised form 22 December 2016 Accepted 26 December 2016 Available online 7 January 2017.
-
Nagaral M1, Auradi, Parashivamurthy and Kori a Comparative Study on Wear Behavior of Al6061-6% sic and Al6061- 6% Graphite Composites, Nagaral, J Appl Mech Eng 2016.
-
Siddabathula Madhusudan, Mohammed Moulana Mohiuddin Sarcar b, Narsipalli Bhargava Rama Mohan Rao Mechanical properties of Aluminum-Copper(p) composite metallic materials, 2016
-
Navnath Sambhaji Kalyankar, Rahul D. Shelke study of properties of al lm-25/sic metal matrix composite fabricated by using stir casting method International Journal of Mechanical Engineering and Technology (IJMET) Volume 7, Issue 5, SeptemberOctober 2016, pp.133141, Article ID: IJMET_07_05_016.
-
Md. Habibur Rahmana, H. M. Mamun Al Rashed, Characterization of silicon carbide reinforced aluminum matrix composites,2013
-
Pardeep Sharma, Dinesh Khanduja, Satpal Sharma, Parametric Study of Dry Sliding Wear of Aluminium Metal Matrix Composites by Response Surface Methodology, 4th International Conference on Materials Processing and Characterization, 2015.
-
Viney Kumara, Rahul Dev Guptab N K Batra Comparison of Mechanical Properties and effect of sliding velocity on wear properties of Al 6061, Mg 4%, Fly ash and Al 6061, Mg 4%, Graphite 4%, Fly ash Hybrid Metal matrix composite. 3rd International Conference on Materials Processing and Characterization (ICMPC 2014).
-
S. C. Patnaik, P. K. Swain, P. K. Mallik, S. K. Sahoo1 Wear Characteristics of Aluminium-Graphite Composites Produced by Stir Casting Technique, ISSN: 2231-3818 (online), ISSN: 2321-4236 (print) Volume 4, Issue 3.
-
Ricardo Augusto Gonçalves and Márcio Bacci da Silva Influence of Copper Content on 6351 Aluminum Alloy Machinability
-
R. L. Deuis, C. Subramanian & J. M. Yellup dry sliding wear of aluminium composites-a review (Received 25 February 1996 revised 30 August 1996; accepted 14 October 1996).
-
M. S. Prabhudeva, V. Auradib , K. Venkateswarluc N. H. Siddalingswamyd and S. A. Kori Influence of Cu Addition on Dry Sliding Wear Behavior of A356 Alloy. 12th global congress on manufacturing and management, 2014
-
Mechanical properties of aluminium metal matrix composites under impact loading. Hamouda and M.S.J. Hashrni
-
Palanisamy Shanmughasundaram Investigation on the Wear Behaviour of Eutectic Al-Si Alloy Al2 O3 – Graphite Composites Fabricated Through Squeeze Casting. Received: December 7, 2013; Revised: May 11, 2014
-
Devaraju Aruri, Kumar Adepua, Kumaraswamy Adepub, Kotiveerachari Bazavada Wear and mechanical properties of 6061-T6 aluminum alloy surface hybrid composites [(sic+ Gr) and (sic+ Al2O3)] fabricated by friction stir processing
-
Michael Oluwatosin Bodunrina,b, Kenneth Kanayo Alaneme, Lesley Heath Chownb Aluminium matrix hybrid composites: a review of reinforcement philosophies; mechanical, corrosion and tribological characteristics. Received 6 September 2014 Accepted 5 May 2015 Available online 9 June 2015.
-
Wear properties of brass samples subjected to constrained groove pressing process M. Ebrahimi, Sh. Attarilar, F. Djavanroodi, C. Gode, H.S. Kim,
-
Adel Mahmood Hassan, Sulieman Z.S. Al-Dhi Improvement in the wear resistance of brass components by the ball burnishing process, Received 22 March 1998
-
Monika Walkowicza, Impact of oxidation of copper and its alloys in laboratory-simulated conditions on their antimicrobial efficiency.
-
Mechanical properties of aluminium metal matrix composites under impact loading.
-
Leaching and recovery of zinc and copper from brass slag by sulfuric acid I.M. Ahmed, A.A. Nayl, J.A. Daoud
-
Salim ªahýn, Nilay Yüksel, Hülya Durmu, Simge Gençalp, WEAR BEHAVIOR OF Al/sic/GRAPHITE AND Al/feb/GRAPHITE HYBRID COMPOSITES.
-
Z. B. Luklinska and j. E. Castle, microstructural study of initial corrosion product of aluminium-brass alloy after exposure to natural seawater, 1983
-
Performance of aluminium alloy graphite bearings in a diesel engine B.P. Krishnan, N. Raman, K. Narayanaswamy and P.K. Rohatgit
-
HIROSHI TOKISUE, Friction and Wear Properties of Aluminum-Particulate Graphite Composites, 1977.
-
Wear characteristics of metals T. S. Eyre
-
Fabrication methods used to prepare Al metal matrix composites- A review Prem Shankar Sahu, R. Banchhor
-
V. K. Dodiya J. P. Parmar, a Study of Various Wear Mechanism and its Reduction Method, 2016