
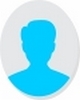
- Open Access
- Authors : Priya S , Dr. Brijesh P
- Paper ID : IJERTV10IS110103
- Volume & Issue : Volume 10, Issue 11 (November 2021)
- Published (First Online): 25-11-2021
- ISSN (Online) : 2278-0181
- Publisher Name : IJERT
- License:
This work is licensed under a Creative Commons Attribution 4.0 International License
Studies on Crude Glycerol Degradation and Hydrogen Production by Photofermentation
Priya S
Assistant Professor Department of Chemical Engineering,
Dayananda Sagar College of Engineering, Bengaluru, Karnataka.
Dr. Brijesh P
Associate Professor Department of Chemical Engineering,
Ramaiah Institute of Technology, Bengaluru, Karnataka.
Abstract:- Hydrogen is considered as an efficient green energy carrier that can be produced in an by biological methods. Photofermentation is one of the biological methods that is said to be effective for biohydrogen production. The bacteria used in the process are facultative anaerobes that are also capable of utilizing waste organic effluents from various process industries as carbon substrates. The current study was based on use of crude glycerol, obtained as a byproduct from biodiesel plant, as carbon substrate for the photofermentative bacteria, Rhodobacter meghalophilus, for hydrogen production. The inoculum size and the light intensity was varied to study their impact on the bacterial growth and hydrogen production process. The inoculum size was varied at 1 ml/L, 2 ml/L and 4 ml/L of the fermentation medium and LED lights of 5W, 10W and 15W was used to supply light source needed for photofermentation. Increasing the inoculum size was found to aid in better degradation of crude glycerol but 2ml/L of inoculum size was found to be effective for hydrogen production. Use of LED light source showed that 10W was sufficient for photofermentation as light intensity at 15W was found to inhibit the bacterial growth and did not help in to increase hydrogen production. Thus, highest yield of hydrogen gas was obtained with 2 ml/L of inoculum size and light capacity of 10W. These results showed that inoculum size and light source are among the crucial parameters governing hydrogen production by photofermentation.
Keywords: Alternate fuel source, biohydrogen, photofermentation, crude glycerol.
-
INTRODUCTION
.
.
Mans strive for modernization and development, is leading to rapid drying up of the oil wells, which is being a major source of energy boost for all technical advancements happening around us. To meet our energy demands and to sustain the development, the urge to provide an alternative solution has become an utmost necessity. Of the many alternative sources being explored for energy, hydrogen is considered as a versatile replacement for energy. The calorific content of hydrogen is considered to be higher which makes it a promising substitute and a highly reliable energy carrier to meet most of our energy needs. Hydrogen gas has many industrial applications in production of ammonia, petrochemicals and is also extensively required in refineries (1)
Steam methane reforming, partial oxidation of hydrocarbons (2), coal gasification (3) etc, are the major producers under the chemical method (2). Biological method could be more advantageous for hydrogen given its low production cost, versatility to use a variety of feed stocks and ecofriendly. Biological methods such as photo-fermentation, dark fermentation, anaerobic fermentation (2) is studied extensively
to optimize the production process. The bacteria employed in these processes can derive energy from many hydrocarbons such as glucose, sucrose, maltose (4) etc. However, these bacterial sources can also feed upon many waste organic materials, rich in hydrocarbons such as agricultural residues (5), food wastes (6), industrial organic effluents (7) etc, and thus help to make the process economical and minimize the potential hazards that arise due to disposal of these organic materials. Biological processes require mild to moderate process conditions such as pressure and temperature, making it economically stable. Unlike chemical processes, biological process produce only water as its by-product and thus, is more ecofriendly. These qualities of a biological process are advantageous over chemical route and therefore, hydrogen by biological processes is being explored as part of the green energy technology.
-
LITERATURE SURVEY
-
Photofermentation
Biological routes mainly consist of direct and indirect photolysis, photo-fermentation, anaerobic fermentation and dark fermentation methods. Among these, dark fermentation and photo-fermentation are the most preferred process and are often carried out as a combined process given their increased efficiency and does not involve any complicated system design (8, 9). Photofermentation involves anaerobic process carried out in the light by purple non sulfur bacteria. Dark fermentation is a simple, anaerobic process that decomposes the organic matter in the absence of light. The process can be carried out at room temperature and pressure. The potential of the both the processes to incorporate a wide variety of organic compounds as its substrate has drawn most researchers to explore the use of diverse industrial organic effluents for bio-hydrogen production (10, 11). The key aspects of fermentation for hydrogen production are it is inexpensive, has lesser maintenance, simple bioreactor designs and capability to incorporate a wide range of waste organic materials as substrates. These factors are advantageous compared to chemical methods such as steam methane reforming or autothermal reforming that are energy dependent processes and also work on the fossil fuel feedstocks. On the other hand, some bottlenecks that still impair the scale up process of biological processes are its low stability, separation of hydrogen from biogas, formation of by- products such as organic acids and alcohol, low energy efficiency of the process etc (12).
-
Micro-organisms for photofermentation and dark fermentation
Hydrogen producing microorganisms are said to be either facultative or strict anaerobes. Microorganisms employed for photofermentation are facultative anaerobic bacteria such as Rhodobacter sphaeroides, Rhodospirillum rubrum, Rhodobacter capsulatus (13, 14) etc. while bacteria employed in dark fermentation are anaerobic, fermentative bacteria belonging to the species Clostridium butyricum, Enterobacter aerogenes (10). These bacteria are a few among the potential microorganisms that are suitable for hydrogen production. While these organisms can feed on a range of monosaccharides such as glucose, sucrose, maltose, fructose etc, as their carbon substrate, it is crucial to select the bacterial species that are capable to acclimatize to the type of waste organic material, used as carbon substrate for hydrogen production. Waste effluents released from many process industries are rich in carbon matter. Agricultural residues are also rich source of carbohydrates and thus, these waste sources can be used as potential feedstocks in biological hydrogen production processes. Effluents from breweries (15), beverage industries and food processing plants (16, 17, 18), dairy units (19) etc and
agricultural crop residues such as wheat (20, 21, 22), potato (23, 24), molasses (25) etc are being considered as feedstocks.
Biodiesel, one of the alternative fuels, finds extensive use in transportation sector, as a blend with conventional diesel. Biodiesel production plants are being commercialized for large scale production. Biodiesel is produced by transesterification of vegetable oils and fats using solvents and catalyst, where glycerol is removed in the process. This is collected as by- product that accounts for 10% of biodiesel production. Solvents such as methanol and sodium salts, used as catalyst are also obtained along with glycerol in this byproduct. Glycerol can be conveted to many value added products such as 1,3- propanediol (26), propanoic acid, n-butanol, citric acid, ethanol
(27) etc. As glycerol being a high carbon source, it can also be used as feed stock for hydrogen production through biological processes (28).
-
-
MATERIALS
Crude glycerol used as substrate in the current study was procured from the Biofuel Park, Gandhi Krishi Vignyana Kendra, University of Agricultural Sciences, Bangalore. The chemicals used for the medium preparation was procured from SRL chemicals of AR grade. The culture of Rba. meghalophilus was obtained from Jawaharlal Nehru Technological University, Hyderabad. The bacterium was first sub-cultured in the growth medium, as per the composition defined in Rhodospirillaceae medium, modified, DSMZ medium 27, with 0.3% sodium pyruvate.
-
METHODS
The free glycerol in the crude mixture was determined by a reaction of crude glycerol with sodium periodate that forms formic acid. This is then reacted with acetyl acetone that forms 3- diacetyl 1,4-dihydrolutidine, which is a yellow coloured complex. The intensity of this yellow colour is directly proportional to the glycerol content. The absorbance of the coloured sample was measured at a wavelength of 440 nm and the concentration of glycerol was determined from the calibration chart for glycerol.
Glass reagent bottles of 1000 ml capacity fitted with stopper, was used as reactor. The stopper was fitted with nitrogen flushing tube and gas collection tube. The outlet of the gas collection tube was inserted into an inverted cylinder, placed in a water containing trough. The gas produced during the fermentation process was collected by volume displacement method. The reagent bottle was placed on a magnetic hot plate and photofermentation experiments were carried by supplying light energy. As photofermentation occurs in the presence of visible light, LED bulbs were used to supply the required light energy. Rba. meghalophilus is a mesophilic bacterium and the process temperature was maintained at 30C. Crude glycerol is viscous in nature and the presence of fatty acids or the esters make it immiscible with the medium components. To ensure uniform mixing of the nutrients, the stirrer speed was set at 150RPM. 250 ml of the fermentation medium was used for experiments. Once the medium was transferred to the reagent bottle, it was autoclaved at 121C for 20 minutes and cooled down. Nitrogen was flushed in the reagent bottles to ensure anaerobic environment in the reactor. Rba. meghalophilus was inoculated in the sterile medium and the size of the inoculation was varied at 1 ml/L, 2 ml/L and 4 ml/L of the fermentation medium to study their effect on glycerol degradation. Studies carried out initially showed that crude glycerol volume of 15 ml/L is effective for hydrogen production. The bacteria also use visible light for fermentation. LED bulbs of 5W, 10W and 15W were used to subject the photofermentation process to different light intensities. The gas produced during the photofermentation process was collected as a function of time to analyze the gas production rate and to determine the hydrogen yield. The residual glycerol in the fermented broth was determined by spectroscopic analysis. The gas collected was analyzed by gas chromatography with thermal conductivity detector. The flow process of the experimentation is shown in figure 1.
Fig 1: Flow process for biohydrogen production from crude glycerol by photofermentation.
-
RESULTS AND DISCUSSION
The crude glycerol sample was analyzed by spectrophotometric method and the concentration of free glycerol in the sample was determined from the glycerol calibration chart. The glycerol content in the crude sample was found to be 0.58 mg/ml. 15 ml/L of crude glycerol was used as carbon substrate in the fermentation study. Therefore, the actual free glycerol available for bacterial fermentation was found to be 8.7 g/ L.
-
Effect of inoculum size
Inoculum size of Rba.meghalophilus was varied as 1 ml/L, 2 ml/L and 4 ml/L respectively. Hydrogen is produced as primary metabolite during the growth of the bacteria. Thus, monitoring the gas produced as a function of time, reflects the growth
nature of the bacteria. The bacteria was found to have fast acclimatization to crude glycerol as the accumulation of gas could be noticed with respect to water displacement in the inverted cylinder with the inoculum size of 1 ml/L. The initial lag period was observed to be 3 days. It could be observed that as the inoculum size varied, the duration of lag phase in the growth cycle of the bacteria also varied. Increasing the inoculation volume, helped to reduce the lag period. For inoculum size of 2 ml/L, the lag period was considerably reduced to 1 day and substantial increase was also observed in the volume of gas accumulated. The growth period was found to be longer than the lower inoculum size. For 4 ml/L of inoculation, the lag period was very negligible and the duration of gas generation was also observed to be shorter. The observations are shown in figure 2. This showed that inoculum size has an impact on the bacterial growth and production of gas as its primary metabolite.
1 ml/L 2ml/L 4 ml/L
1 ml/L 2ml/L 4 ml/L
of 2 ml/L was considered as effective for hydrogen production process.
-
Effect of light intensity
With inoculum size of 2 ml/L, found to facilitate good bacterial growth and hydrogen production, the photofermentation experiments were carried out at three different light intensities. LED bulbs of 5W, 10W and 15W were used to supply light at varying intensities. The bacterium was found to be receptive of light source as it was found that increasing light energy, helped to boost the bacterial growth. The growth period of the bacteria, for all the three light intensities, did not change from the growth period without light source. But a considerable difference was noticed in the volume of gas produced, with varying light intensity. When LED bulb of 10W was used, the volume of gas generated was found to be significantly higher than that generated at 5W. This was ascertained with the increase in the gas volume that was monitored over a period of time.
5W 10 W 15 W
160
140
120
100
80
60
40
20
0
160
140
120
100
80
60
40
20
0
Gas volume collecetd, ml
Gas volume collecetd, ml
Gas volume collected, ml
Gas volume collected, ml
600
500
400
0
10
Time, Days
15
0
10
Time, Days
15
Fig 2: Effect of inoculum size on bacterial growth and hydrogen gas production
300
200
100
0
5
5
0 1 2 3 4 5 6 7 8 9 10 11 12 13
Time, days
With varying inoculum size, the substrate to inoculum size ratio was calculated and was obtained as 15, 7.5 and 3.75. It could be seen that the ratio decreased with increase in the inoculum size. The bacterial population in the fermentation medium was also larger as the inoculum size increased. Thus, the higher microbial population helped in faster bacterial activity that was conducive to reduce the lag period. This condition also resulted in rapid substrate consumption with the crude glycerol in the medium being limited to 15 ml/L. This could be related to the faster growth of the bacteria with 2 ml/L of inoculation. Thus, the rate of substrate depletion could have been higher with 4 ml/L of inoculation that led to shortened growth period and slowdown in the gas production. The substrate conversion was calculated with respect to the free and the residual glycerol in the fermentation medium. the amount of residual glycerol in the fermentation medium was determined to be 3.35g, 5.49 g and 5.81 g and the substrate conversion was calculated to be 38.5% for 1 ml/L inoculum size, 63.10% for 2 ml/L of inoculum size and 66.78% for 4 ml/L of inoculum size. his showed that crude glycerol degradation was favored by higher inoculum size. The hydrogen content in gas samples from fermentation with 1 ml/L, 2 ml/L and 4 ml/L inoculum size were analyzed by GC- TCD and was found that inoculum size of 2ml/L, showed highest hydrogen with 15% (v/v). Therefore, inoculation size
Fig 3: Effect of different light capacity on gas production by photofermentation
As hydrogen is produced as a primary metabolite, the increase in gas volume shows that the bacteria uses light energy as additional energy source to break down the crude glycerol molecules in the medium. This in turn helps in better uptake of the nutrients, as a result of which, the volume of the gas produced also increased. In order to find the extent of gas production with increase in light intensity, 15W LED bulb used to supply the light energy for photofermentation. The volume of gas produced, exhibited the same trend as that with the use of 10W LED source, with negligible increase in the gas volume, as shown in figure 3. This implies that intensity of light with 15W LED source could have exposed the bacteria to excess energy which could have been detrimental, affecting the metabolic productivity of the bacteria. Thus, the volume of gas produced did not increase with increase in light energy. The volume of hydrogen collected with 5W, 10W and 15W LED light sources were found to be 44.8 ml, 78.4 ml and 81.6 ml respectively.
-
Specific hydrogen production rate
The specific hydrogen production rate is defined as the volume of hydrogen gas generated with respect to the amount of substrate consumed per unit time of fermentation. The formula for specific hydrogen production rate is given in equation 1.
The substrate conversion rate helps to analyze the rate of hydrogen gas generation and will be crucial data for designing a continuous fermenter.
Specific hydrogen production rate
-
G. Mahidhara, H. Burrow, C. Sasikala, et al. Biological hydrogen production: molecular and electrolytic perspectives, World Journal of Microbiology and Biotechnology, vol.35, 116, 2019.
-
Ahmed Aidid Ibrahim., Hydrogen Production from Light Hydrocarbons, Advances in Hydrogen Generation Technologies, 2018.
-
S Eker, & M. Sarp, Hydrogen gas production from waste paper by
=
————–(1)
dark fermentation: Effects of initial substrate and biomass concentrations, International Journal of Hydrogen Energy, vol. 42(4), pp. 25622568, 2017.
-
A. Tawfik, A H Salem, Optimization of hydrogen production from
The volume of hydrogen produced with 1 ml/L, 2 ml/L and 4 ml/L inoculum size was found to be 26.4 ml, 73.6 ml and 57.6 ml respectively. The specific hydrogen production rate was thus calculated to be 0.075 m3/kg.s, 0.139 m3/kg.s and 0.103 m3/kg.s. The highest specific hydrogen production rate was thus found to be for inoculum size of 2 ml/L.
-
-
CONCLUSION
The inoculum size of the bacteria and the light source of varying intensities showed that both of these can be crucial parameters that affect the substrate utilization rate and the hydrogen yield. It was found that increase in inoculum size led to better substrate utilization as the substrate conversion rate was found to increase with increase in inoculum size. The highest substrate conversion rate obtained with 4 ml/L of inoculum size with 66.78%. Even as the substrate conversion rate was higher for larger inoculum, it did not show similar trend for hydrogen yield. The yield of hydrogen was found to increase with increase in inoculum size from 1 ml/L to 2 ml/L while it decreased as the inoculum size was increased to 4 ml/L. This was due to the substrate depletion, caused with higher microbial population. Studies conducted with varying light intensity showed that at light energy supplied with 10W LED bulb, the bacteria were able to absorb light energy for effective production of hydrogen gas. The bacterial growth was observed to have slowed down with further increase in light energy, as excess energy led to bacterial growth inhibition caused by photo effect. This was correlated with respect to the gas volume produced, that did not show any significant variation compared to gas volume obtained with 10W light source. The parameters of inoculum size and the light intensity that could lead to effective crude glycerol degradation and yield hydrogen gas was determined to be 2 ml/L and 10W LED light source. Therefore, determination of photosynthetic active radiation is essential for effective utilization of light energy by photofermentative bacteria.
-
ACKNOWLEDGEMENT
We thank the management of Dayananda Sagar College of Engineering and Ramaiah Institute of Technology for their support and encouragement for the research work. We also thank Mr. Rajesh, Young Scientist, Biofuel Park, Gandhi Krishi Vignyana Kendra, UAS Bengaluru and Dr. Ch. Sasikala, Professor and Head, Centre for Environment, Institute of Science and Technology, Jawaharlal Nehru Technological University Hyderabad, for their help and guidance.
-
REFERENCES
-
F. Ausfelder, A. Bazzanella, Hydrogen in the Chemical Industry Hydrogen Science and Engineering: Materials, Processes, Systems and Technology, pp. 19 40, 2016.
pretreated rice straw waste in a mesophilic up-flow anaerobic staged reactor, International Journal of Energy Research, vol.38, pp. 1155 1161, 2014.
-
Giovanna Cappai., et al. Biohydrogen Production from Food Waste: Influence of the Inoculum-To-Substrate Ratio, Sustainability, vol. 10, pp. 4506, 2018.
-
D. Das, A Road Map on Biohydrogen Production from Organic Wastes. Transactions of the Indian National Academy of Engineering, vol.2, pp. 153160, 2017.
-
A. Thitirut Assawamongkholsiri, Alissara Reungsang, Photo- fermentational hydrogen production of Rhodobacter sp. KKU-PS1 isolated from an UASB reactor, Electronic Journal of Biotechnology, vol.18, pp. 221230, 2015.
-
Y. Li, Y. Qiu, X. Zhang, et al, Strain screening and optimization of biohydrogen production by Enterobacter aerogenes EB-06 from glycerol fermentation, Bioresources and Bioprocessing vol. 6, pp. 15, 2019.
-
Cardoso V., Romao B.B., Silva F.T.M., Santos J.G., Batista F.R.X., Ferreira J.S., 2014, Hydrogen production by dark fermentation,
Chemical Engineering Transactions, 38, 481-486
-
Prakash K. Sarangi, Sonil Nanda, Biohydrogen Production Through Dark Fermentation, Chem. Eng. Technol. 2020, 43, No. 4, 601612,
-
Boboescu et al. Revealing the factors influencing a fermentative biohydrogen production process using industrial wastewater as fermentation substrate, Biotechnology for Biofuels 2014, 7:139
-
E. Fascetti, E. DAddario, O. Todini, A. Robertiello, Int. J. Hydrogen Energy 1998, 23 (9), 753760.
-
J. Cai, Y. Zhao, J. Fan, F. Li, C. Feng, Y. Guan, R. Wang, N. Tang, J. Biotechnol. 2019, 302, 1825.
-
S. Vijaya Krishna, et al., Biohydrogen production from brewery effluent in a batch and continuous reactor with anaerobic mixed microbial consortia, Biofuels. Vol. 8(6), pp. 701707, 2016. doi:10.1080/17597269.2016.1206409.
-
S. Sharma, D. Ortega, N. P. Minton, V. K. Dubey, V. S. Moholkar, Bioresour. Technol. 2019, 284, 168177.
-
A. A. Tsygankov, D. N. Tekuchev, in State of the Art and Progress in Production of Biohydrogen (Eds: N. Azbar, D. B. Levin), Bentham Science Publishers Ltd, Sharjah 2011, 7893.
-
M. Krishnaveni, Bio-Hydrogen Production from the Dairy Waste Water using Anaerobic Sequence Batch Reactor, International Journal for Scientific Research & Developmen, vol.6 (4), 2018. ISSN (online): 2321-0613.
-
J. Z. Li, B. K. Li, G. F. Zhu, N. Q. Ren, L. X. Bo, J. G. He, Int.J. Hydrogen Energy 2007, 32, 32743283.
-
J. Masset, S. Hiligsmann, C. Hamilton, L. Beckers, F. Franck, P. Thonart, Int. J. Hydrogen Energy 2010, 35, 33713378.
-
J. Miyake, T. Wakayama, J. Schnackenberg, T. Arai, Y. Asada, J. Biosci. Bioeng. 1999, 88, 659663.
-
N. Nasirian, M. Almassi, S. Minaei, R. Widmann, Int. J. Hydrogen Energy 2011, 36, 411420.
-
T. A. Ngo, M. S. Kim, J. S. Sim, Int. J. Hydrogen Energy 2011, 36, 58365842. [40] Y. Oda, S. K. Samanta, F. E. Rey, J. Bacteriol. 2005, 187, 77847794.
-
L. Mitrea, M. Trif, A.F Ctoi, et al, Utilization of biodiesel derived- glycerol for 1,3-PD and citric acid production, Microbial Cell Factories, vol. 16, pp. 190, 2017.
-
Vijay Kumar Garlapati, Uttara Shankar, Amrita Budhiraja, Bioconversion technologies of crude glycerol to value added industrial products, Biotechnology Reports, Volume 9, 2016, Pages 9-14.
-
Rahul Mangayil, Matti Karp, Ville Santala., Bioconversion of crude glycerol from biodiesel production to hydrogen, International Journal of Hydrogen Energy, vol.37 (17), pp. 12198-12204, 2012.