
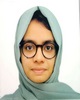
- Open Access
- Authors : Haleema Nawrin , Binu. P
- Paper ID : IJERTV9IS060961
- Volume & Issue : Volume 09, Issue 06 (June 2020)
- Published (First Online): 06-07-2020
- ISSN (Online) : 2278-0181
- Publisher Name : IJERT
- License:
This work is licensed under a Creative Commons Attribution 4.0 International License
Structural Performance of FRP Columns with Splice Connection in Modular Buildings
Haleema Nawrin1, Binu. P2 1Mtech Student; 2Associate Professor Department of Civil Engineering
Sree Narayana Gurukulam College of Engineering and Technology, Ernakulam, Kerala.
Abstract Modular buildings are prefabricated buildings that involves constructing sections away from the building site, then delivering them to the intended site. Different types of materials are used for modular constructions such as wood, fiber reinforced polymer (FRP), concrete, cold form steel etc. Pultruded Fibre Reinforced Polymer (FRP) members are increasingly favoured in civil engineering as they are lightweight and corrosion resistant. However, due to the challenge in connecting them, their application is limited especially in tubular members with closed sections. A splice connection is developed for tubular Fibre Reinforced Polymer (FRP) members and this steel Fibre Reinforced Polymer (FRP) connection system consists of two components which includes a bonded sleeve joint coupling fibre reinforced polymer and steel tubes adhesively, and a bolted ange joint connecting two steel hollow sections through llet weld. The Bonded Sleeve Joint reduces stress concentration in the fibre reinforced polymer compared to bolt fastening, while the Bolted Flange Joint enables convenient installation and imparts ductility to the system (through steel yielding). Bending performance of this innovative splice connection is evaluated for various sections of columns such as hexagonal, rectangular, square etc with varying bond lengths to find the most effective model.
KeywordsFibre Reinforced Polymer; Tubular members; Splice connection; Moment capacity; Bolted flange joint; Bonded sleeve joint.
-
INTRODUCTION
Modular buildings and modular homes are prefabricated buildings or houses that consist of repeated sections called modules. It is a construction method that involves constructing sections away from the building site, then delivering them to the intended site. Modular buildings can be constructed using wood, Fibre Reinforced Polymer (FRP), concrete, cold form steel etc. Fibre Reinforced Polymer (FRP) is a composite material made of polymer matrix reinforced with fibres. The fibres are usually glass (GFRP), carbon (CFRP), aramid or basalt. The polymer is usually an epoxy, vinyl ester, or polyester thermosetting plastic. Application of Fibre Reinforced Polymer (FRP) composites in civil engineering structures has shown an increase in the past two decades. These lightweight and corrosion-proof materials through their applications in the rehabilitation and strengthening of existing structures have attained much recognition worldwide. Glass Fibre Reinforced Polymer (GFRP) composites have been considered as load-carrying structural members in civil engineering because of their light weight, high strength, corrosion resistance, and low maintenance requirements. They are now produced through pultrusion techniques with various structural sections, such as I – shaped and tubular sections,
showing great potential for frame and building applications. Such implementations, however, require reliable connection systems between GFRP beams and columns. Glass FRP (GFRP) composites are credited with sucient strength and stiness at moderate cost. Due to the advances in the pultrusion manufacturing technique, FRP composites also have great potential as load-bearing members in new construction. Examples include bridge decks, beams, columns, and floor systems. Connection designs for these members should consider the brittle and anisotropic nature of FRP materials. Comparing with open section proles (I or channel proles), closed section proles (circular or rectangular tubular proles) shows better resistance against torsional and global buckling. Yet these merits of tubular GFRP members coexist with the diculty of connecting the members into truss and frame assemblies, due to the material anisotropy and the closed section shape [1]. In the development of a connection form for axially loaded tubular FRP proles, the use of a steel tubular sleeve connector which was inserted into and bolt-fastened to the tubular FRP prole was commonly used. This steel sleeve connector facilitated versatile connection forms to adjacent members. Despite the convenience of in-situ installation, bolt fastening requires hole-drilling on the composite material, creating problems such as damaged bre architecture, stress concentration, and exposure of the weak in-plane shear strength of the FRP composites [1]. Adhesive bonding, as an alternative, oers structural integrity, reduced stress concentration and also improved fatigue resistance. Combining these benets of the adhesive bond and the steel sleeve connector, bonded sleeve connections for joining circular GFRP truss members to nodal joints was proposed [1].
Based on further studies on connecting steel tubular members, a splice connection is developed for connecting tubular Fibre Reinforced Polymer (FRP) members (Fig.1) and this steel FRP connection system consists of two components: a Bonded Sleeve Joint (BSJ) coupling FRP and steel tubes adhesively, and a Bolted Flange Joint (BFJ) connecting two steel hollow sections through llet weld. The BSJ reduces stress concentration in the FRP compared to bolt fastening, while the BFJ enables convenient installation and imparts ductility to the system (through steel yielding) [2]. Splice connection allow connecting two collinear elements using additional plates on webs and/or flanges.
Fig.1. Proposed Splice connection for tubular FRP members.
-
LITERATURE REVIEW
All previous studies conducted on splice connected FRP tubular members reveals that these splice connections imparts considerable ductility to a structure made of brittle FRP members and shows improved rotational stiffness and yield moment [1][2]. According to [3] the multi continuum method is practically the best suited method for composite analysis since it gives complete insight about the fibre failure in all the layers of the material. FRP tubular members with bolted sleeve joints under axial loading (tension and compression) shows linear elastic deformation followed by a brittle and catastrophic failure in the case of bolt tension specimens and in the case of compression specimens linear deformation occurred only to a certain level along with an ultimate loading owing to a bearing failure which was pseudo-ductile failure. Shear-out failure was the ultimate joint failure for all ordinary bolt specimens regardless of loading direction [7]. From the failure modes observed experimentally, it was found specimen with a longer bond length failed initially by yielding of the steel plate whereas specimen with shorter bond length failed initially by cohesive failure. After the yielding of steel plate, transverse compressive failure was observed on the web walls of specimens with longer bond lengths. As per [8], for splice joints transverse stiffness increases linearly as the bolt torque increases. Incorporating two different pultruded directions within one slab structure of FRP shows sufficient mechanical performance under static loading and prevents formation of longitudinal cracking commonly observed in existing FRP structures [1]. According to [9] bolted flange-plate connections in FRP structures shows good yielding capacity for the connections. This connection provides adequate ductility and energy dissipation capacity which is advantageous for seismic applications [4].
-
NUMERICAL ANALYSIS
In order to verify the accuracy of a numerical model using finite elemnt software, numerical analysis from a journal is reciprocated using its model dimensions and other input parameters. The details from journal [2] were opted for the validation of mathematical model using the finite element software ANSYS 16.1.The model named as B-170-4 was taken for validation purpose where B stands for bending loading; 170
is the bond length/splice length of the steel-FRP bonded sleeve joint in mm; and 8 is the number of bolts used. A grade 355 steel square tube of size 80 x 80 x 6 mm was joined to a 6 mm thick grade 250 steel flange plate by fillet welds with a leg length of 6 mm approximately. The other end of the steel tube was coaxially coupled into and bonded to a pultruded glass fibre reinforced polymer square tube of size 102 x 102 x 9.5 mm. Two of the bonded assemblies are fastened together at the steel flange-plate with 8.8 bolts having M12 grade. GFRP material has a Transverse flexural strength of 88.5 MPa; Youngs modulus as 25200 MPa; and Poissons ratio as 0.3. While steel flange plate has Yield strength of 311.8 MPa; Youngs modulus of 2.01 x 105 MPa; and Poissons ratio as 0.3.Steel square tube has yield strength of 420.1 MPa; Youngs modulus of 2.09 x 105 MPa; and Poissons ratio as 0.3. 8.8 bolts have yield strength of 640 MPa; Youngs modulus as
2.01 x 105 MPa; and Poissons ratio as 0.3. After proper modelling and meshing of B-170-8, the model is analysed under push over analysis. The maximum bending moment corresponding to the maximum displacement obtained from the validation is 9.2 kNm while the maximum bending moment obtained from the journal is 9kNm. Therefore the percentage error obtained is less than 5%.
Parametric study on splice connected FRP tubular column using pushover analysis to find the best model having better stiffness and load carrying capacity is aimed in this study.
-
MODELLING OF FRP COLUMN
Numerical modeling of the splice connected FRP columns performed by the finite element software ANSYS 19 WORKBENCH. Various sections of columns are considered for the analysis such as square, rectangle and hexagonal FRP columns each of these sections having splice length 170mm, 150mm, 190mm simultaneously. A square FRP column with an L stiffener is also introduced in order to improve the flange strength. The FRP square column is of size 102 x 102 x 9.5 mm, rectangle is of size 92 x 112 x 9.5 mm and hexagonal column is of size 63.28 x 9.5 mm. The model's material property was chosen from the engineering data section of the ANSYS software. This data section consists of pre-assigned values for each material. Poissons ratio and density used for each material is 0.3 and 7850 kg/m3 respectively. Sikadur-330 adhesive was used as the epoxy material. The material properties given for the model is shown in the below tables.
TABLE I. MATERIAL PROPERTIES OF STEEL SQUARE TUBE
Item
Steel Square tube
Modulus of elasticity
2 x 105 N/mm2
Yield strength
415 MPa
TABLE II. MATERIAL PROPERTIES OF GFRP MATERIAL
Item
GFRP Material
Modulus of elasticity
X direction: 25200MPa Y direction: 6200 MPa Z direction: 6200 MPa
Yield strength
330 MPa
TABLE III. MATERIAL PROPERTIES OF FLANGE PLATE
Item
Steel Flange Plate
Modulus of elasticity
2 x 105 N/mm2
Yield strength
311 MPa
Item
Epoxy
Modulus of elasticity
4500 GPa
Yield strength
32.2 MPa
Item
Epoxy
Modulus of elasticity
4500 GPa
Yield strength
32.2 MPa
TABLE IV. MATERIAL PROPERTIES OF EPOXY
TABLE V. MATERIAL PROPERTIES OF 8.8 BOLT
Item
8.8 bolt
Modulus of elasticity
2 x 105 N/mm2
Yield strength
1043 MPa
In this analysis FRP tubular columns in various sections and dimensions which are connected by using splice connection are considered. In each model a steel tube will be joined to a steel flange plate by using fillet welds. The other end of the steel tube will be coaxially coupled into and bonded to a pultruded glass fiber reinforced polymer (GFRP) square tube with Sikadur-330, a two-component epoxy based adhesive. So in this connection system a bonded sleeve joint (BSJ) is coupling GFRP and steel tubes adhesively and a bolted flange joint (BFJ) is connecting two steel hollow sections through fillet weld. The modeling is done using ANSYS 19 WORKBENCH. Comparison study of square, rectangular and hexagonal tubular columns each having bond lengths 170mm, 150mm and 190mm is conducted here. Flange thickness is 6mm. FRP column length is 890mm. Number of bolts used is 8.
This parametric study is conducted to bring out the best model with a suitable section and splice length. This involves study of splice connected square FRP tubular columns having varying sections with different bond lengths. As mentioned earlier the sections considered for the study includes square, rectangle and hexagonal columns having depth of 890 mm. Various bond lengths considered for the study are 170, 150 and
190. Deformation and stiffness of the models are determined and compared. Out of these the best model having better stiffness and load carrying capacity is selected as effective and is used for further analysis. The engineering data section of the software consists of pre-assigned values for each material.
The models used in the FRP column splice connection parametric study are S-170-8, REC-170-8, HEX-170-8, S-170- 8-Stiffener, S-150-8, REC-150-8, HEX-150-8, S-150-8, S-190-
8, REC-190-8, HEX-190-8 which is in the form B-x-y where B is the column section, x is the splice length and y is the number of bolts. In S-170-8-Stiffener, an additional L-stiffener is used. This will helps to improve the flange strength. Fig.2 shows the splice connected FRP column (S-170-8).
Fig.2. Splice connected Square FRP column (S-170-8)
A. Support and Loading conditions
Support and loading was given to each models after modeling. Fixed support was given at a distance of 0.42m from the ends of the two connected columns and a loading was given at a distance of 0.12m from the connection to both the columns.
-
RESULTS AND DISCUSSIONS
-
Static Analysis
From the analysis, an equivalent plastic strain was observed in each model. Fig.3 shows the equivalent plastic strain distribution in HEX-170-8 model. The plastic strain observed is mainly concentrated in the flange plate region of splice connection and thereby creating the plastic deformation in face of the connection plate.
-
Comparison study
In this objective, a comparative study is done in order to find out the most effective model based on varying sections and splice length by push-over analysis. The square, rectangular and hexagonal models each having splice length 170mm, 150mm, 190mm and model with an L-stiffener is compared based on their load carrying capacity and deformation.
Fig.3. Equivalent plastic strain of HEX-170-8
SPLICE LENGTH
SECTION
MOMENT
(kNm)
DEFORMATION
(m)
170-8
Square
15.887
0.15499
170-8
Square-stiffener
17.726
0.14618
170-8
Rectangle
21.919
0.13799
170-8
Hexagon
15.685
0.17921
150-8
Square
15.283
0.15793
150-8
Rectangle
21.659
0.12072
150-8
Hexagon
15.549
0.17258
SPLICE LENGTH
SECTION
MOMENT
(kNm)
DEFORMATION
(m)
170-8
Square
15.887
0.15499
170-8
Square-stiffener
17.726
0.14618
170-8
Rectangle
21.919
0.13799
170-8
Hexagon
15.685
0.17921
150-8
Square
15.283
0.15793
150-8
Rectangle
21.659
0.12072
150-8
Hexagon
15.549
0.17258
TABLE VI. COMPARISON OF RESULTS
190-8
Square
16.085
0.15751
190-8
Rectangle
21.889
0.16508
190-8
Hexagon
15.784
0.17258
The models having splice length 170mm and 150mm shows better stiffness and load carrying capacity while models having splice length 190mm failed up taking lesser load compared to models having splice length 170mm and 150mm. Out of this S-170-8 and HEX-170-8 has almost equal moments and load carrying capacity. But in the case of hexagonal columns deformation is larger compared to other columns hence rotation angle will increase. In rectangular sections, moment is larger while deformation is varying much larger while increasing the splice length and width. This makes it less effective compared to other sections. From all these results it is concluded that square sections having 170mm bond length is much effective in stiffness and load carrying capacity. Out of this, square section having an L-stiffener will helps to improve the flange strength thereby failure at flanges can be reduced. Comparing with S-170-8 it has larger moment. Hence S-170-8- Stiffener is used as the best model applicable to building frames as per ASTM Standards.
Fig.4. Comparison of Moment-deformation curve having splice length 170mm
Fig.4. Comparison of Moment-deformation curve having splice length 150mm
Fig.4. Comparison of Moment-deformation curve having splice length 190mm
-
-
CONCLUSION
This paper investigated the comparative study of splice connected FRP tubular columns having sections such as square, rectangle and hexagon each having varying bond lengths(150mm,170mm,190mm) in order to find the best model applicable to building frames as per ASTM standards. Based on the results from Finite Element modeling it is concluded that splice connected square tubular column having splice length 170mm with the use of an L-stiffener (S-170-8- Stiffener) gives better results in moment capacity and stiffness. It also imparts strength to the flange plate thereby reduces flange failure.
REFERENCES
-
Chengyu Qiu, Chenting Ding, Xuhui He, Lei Zhang and Yu Bai, Axial Performance of Steel Spliced Connection for Tubular FRP Column Members, Composite Structures, ELSEVIER, Vol. 25, pp. 498-509, February 2018.
-
Chengyu Qiu, Yu Bai, Lei Zhang and Li Jin, Bending Performance of Splice Connections for Assembly of Tubular Section FRP Members: Experimental and Numerical Study, Journal of Composite Structures, ASCE, Vol.23, pp. 55-70, 2019.
-
Emayavaramban.E and Pravin Raj E.L, Finite Element Analysis of Different Composite Materials using Multi Continuum Method, Journal of Mechanical and Civil Engineering, IOSR, Vol. 11, pp. 94-99, March 2014.
-
En-Feng Denga, Liang Zonga, Yang Dinga, Xiao-Meng Daia, Ni Louc and Yang Chend , Monotonic and Cyclic Response of Bolted Connections with Welded Cover Plate for Modular Steel Construction, Engineering Structures, ELSEVIER, Vol. 17, pp. 407-419, 2018.
-
F. Ascione, M. Lamberti, A.G. Razaqpur and S. Spadeav, Strength and Stiffness of Adhesively Bonded GFRP Beam-Column Moment Resisting Connections, Composite Structures, ELSEVIER, Vol. 5, pp. 1-10, November 2016.
-
F. Ascione, M. Lamberti, A.G. Razaqpur and S. Spadeav, Pseudo Ductile Failure of Adhesively Joined GFRP Beam-Column Connections: An Experimental and Numerical Investigation, Composite Structures, ELSEVIER, Vol. 20, pp. 864-873, 2018.
-
Fu Jia Luo, Yu Bai, Xiao Yang, and Ye Lu, Bolted Sleeve Joints for Connecting Pultruded FRP Tubular Components, Journal of Composite Structures, ASCE, Vol. 20, pp. 1-11, 2016.
-
Geoffrey John Turvey and Xavier Cerutti, Flexural Behaviour of Pultruded Glass Fibre Reinforced Polymer Composite Beams with Bolted Splice Joints, Composite Structures, ELSEVIER, Vol. 119, pp. 543-550, September 2015.
-
Juan E. Carrion, Keith D. Hjelmstad and James M. LaFave, Finite Element Study of Composite Cuff Connections for Pultruded Box Sections, Composite Structures, ELSEVIER, Vol. 70, pp. 153-169, September 2004.
-
Sindu Satasivam, Yu Bai and Xiao-Ling Zhao, Adhesively Bonded Modular GFRP WebFlange Sandwich for Building Floor Construction, Composite Structures, ELSEVIER, Vol. 11, pp. 381-392, 2014.