
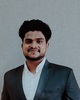
- Open Access
- Authors : Reema Pius, Bristo K Benny, Abin Joseph, Sreekutty Sasi
- Paper ID : IJERTV13IS040342
- Volume & Issue : Volume 13, Issue 04 (April 2024)
- Published (First Online): 07-05-2024
- ISSN (Online) : 2278-0181
- Publisher Name : IJERT
- License:
This work is licensed under a Creative Commons Attribution 4.0 International License
Structural Optimization of I Section Web with Varied Corrugation Patterns
Reema Pius
Civil Engineering Adi Shankara Institute of Engineering And Technology Ernakulam, India
Abin Joseph
Civil Engineering Adi Shankara Institute of Engineering And Technology Ernakulam, India
Bristo K Benny
Civil Engineering Adi Shankara Institute of Engineering And Technology Ernakulam, India
Sreekutty Sasi
Civil Engineering Adi Shankara Institute of Engineering And Technology Ernakulam, India
Abstract Corrugation profoundly impacts the strength and durability of I-section structures in structural engineering. This project focuses on analyzing two distinct types of corrugationstrapezoidal and triangularusing advanced computation platforms like Ansys Workbench for Finite Element Analysis (FEA). Our primary objective is threefold: firstly, to discern how these different corrugation forms influence the robustness and weight distribution within an I-section structure. Secondly, by leveraging FEA simulations on the Ansys Workbench platform, we aim to precisely compute and compare their individual strength-to-weight ratios, providing crucial insights into their structural performance. Lastly, the project aims to formulate definitive conclusions from these analyses, offering valuable inputs for future studies or applications in materials science and civil architecture disciplines where such knowledge is indispensable. Through this investigation, we seek to advance understanding in structural engineering and contribute to the optimization of design methodologies, thereby fostering innovation in related fields
Keywords Corrugation, I-Section, FEA
-
INTRODUCTION
-
sections have a high strength-to-weight ratio and effective stiffness qualities, which make them useful in a variety of engineering structures. Nonetheless, the web of an I-section frequently continues to be a somewhat inefficient component since a large amount of material is concentrated in places that don't really add to the overall strength or stiffness. By carefully adding more material and raising the web's moment of inertia, corrugation can provide a viable way to increase efficiency. Because of the element's increased stiffness and rigidity from its corrugated design, it can support a greater load without bending or deflecting unduly. This is especially helpful for bridges, which must sustain high traffic volumes. When designing corrugated shapes, less material is needed than for flat ones to have the same strength. This may result in less
money being spent and a lighter structurewhich is necessary for lengthy spans. Additionally, by more efficiently channelling loads, the corrugated design can increase the structure's efficiency. This may lengthen life and assist lower concentrations of stress. An eye-catching accent can be added with corrugated shapes. This may be particularly crucial for vehicles or aircraft. Aerospace and automotive structures utilize corrugate
structure stiffness without appreciably increasing its bulk.In order to save weight and maximize strength and stiffness, corrugated steel webs are utilized in both automotive and aviation constructions. The corrugations give the structure stiffness without appreciably increasing its mass since they function similarly to ribs.
-
-
OBJECTIVES
-
To find the better corrugated pattern on the I- section.
-
To evaluate the following Parameters with different dimensions of corrugation
-
Load Bearing Capacity
-
Total Deformation
-
-
METHODOLOGY LITERATURE REVIEW
MODELLING OF STRUCTURES
IMPORTING INTO FEA SOFTWARE
APPLYING MATERIALS
APPLYING BOUNDRY CONDITIONS AND LOAD
SOLVING FEA MODELS
READING THE RESULT
-
MEASUREMENT
Table Column Head
More table copya
copy
Table Head
Figure. 4.1 Measurement of I-Section
Table column subhead Subhead Subhead
Figure. 4.2 Required Material Property
-
BOUNDARY CONDITION
Figure. 5.1 Boundary Condition a.
-
MESH DEPENDENCY
When performing finite element analysis (FEA) simulations with Ansys or other comparable software, mesh dependency is a crucial factor to take into account. It speaks about the simulation results' sensitivity to changes in the mesh density and quality that are applied to the geometric model. The density of the mesh, which is determined by the quantity and dimensions of finite elements utilized to discretize the model, has a major impact on the analysis's precision and computing effectiveness. Although a finer mesh frequently necessitates more computer power and longer simulation durations, it can capture more minute aspects of the geometry and produce results with more realism. The quality of the mesh's elements is just as important as its density. Highly deformed or skewed elements are examples of poorly shaped elements that can cause numerical instability and imprecise forecasts. Ansys provides instruments for evaluating and enhancing element quality, guaranteeing the mesh's resilience and dependability. To assess mesh dependency, mesh convergence studies are frequently carried out. These investigations involve running simulations with increasingly finer meshes until a stable solution is reached. Convergence study results are useful in figuring out the ideal mesh density needed to produce precise and trustworthy results for a certain investigation. In mesh dependency management, accuracy and computational efficiency must be balanced. Based on the intricacy of the model, the physics involved, and the required degree of detail in the output, engineers must optimize the mesh density. In crucial areas of the model, local mesh refinement can be used to improve resolution were enquired without sacrificing total effectiveness. To further evaluate the accuracy of the model, simulation findings must be validated against experimental data. This validation procedure depends on mesh dependency studies, which guarantee that the simulation faithfully captures the physical behaviour of the system under study.
Table.6.1. Mesh Dependency
Figure.6.2 Equivalent Stress Maximum Vs Mesh Element
-
RESULT
Figure.7.1 Total deformation (Corrugation pitch 80mm)
Figure.7.2 Equivalent stress (Corrugation pitch 80mm)
Figure.7.4 Total deformation (Corrugation pitch 60mm)
Figure.7.5 Equivalent stress (Corrugation pitch 60mm)
Figure.7.6. Load Vs Displacement
Load vs Displacement
250000
200000
150000
100000
50000
0
0
2
4
6
8
10
12
14
Displacement in mm
TC-80
Force Reaction in N
Figure.7.3. Load Vs Displacement
Figure.7.7 Total deformation (Corrugation pitch 1000mm)
Figure.7.8 Equivalent stress (Corrugation pitch 100mm)
Figure.7.10 Total deformation (Corrugation pitch 50mm)
Force Reaction in N
Force reaction in N
Figure.7.11Equivalent stress (Corrugation pitch 50mm)
Load vs Displacement
250000
200000
150000
>
100000
50000
0
0
2
4
6
8
10
12
14
Displacenment in mm
TC-100
Load vs Displacement
250000
200000
150000
100000
50000
0
0
2
4
6
Toral displaceemnt in mm
8
10
12
TC-50
Figure.7.12. Load Vs Displacement
Figure.7.9. Load Vs Displacement
Force reaction in N
Figure.7.13 Total deformation (Corrugation pitch 120mm)
Figure.7.14 Equivalent stress (Corrugation pitch 120mm)
Figure.7.15 Load Vs Displacement
Load vs Displacement
250000
200000
150000
100000
50000
0
0
2 4 6
8
10
12
14
16
Total displacemnet in mm
TC-80
TC-60
TC-100
TC-50
TC-120
Figure.7.16 Companied Graph
REFERENCES
-
B. and Dunaj Geri, L (2021). Nonlinear imperfect analysis of corrugated web beams subjected to lateral-torsional buckling. Engineering Structures, 245, p.112888.
-
Guo, C., Mao, J. and Xie, M. (2022). Analysis of energy absorption characteristics of corrugated top beams of anti-impact hydraulic supports. Alexandria Engineering Journal, 61(5), pp.3757-3772.
-
Farzampour, A., Mansouri, I., Lee, C.H., Sim, H.B. and Hu, J W(2018). Analysis and design recommendations for corrugated steel plate shear walls with a reduced beam section. Thin-walled structures, 132, pp.658- 666
-
Nie, J.G., Zhu, L., Tao, M.X. and Tang, (2015). Shear strength of trapezoidal corrugated steel webs. Journal of constructional steel research, 85, pp.105-115
-
Hao Liang, Krishanu Roy, Zhiyuan Fang and James B. P. Lim, (2021) A Critical Review on Optimization of Cold-Formed Steel Members for.
Better Structural and Thermal Performances
-
Hafsamol, Ranjan Abraham (2020) International Research Journal of Engineering and Technology (IRJET) Finite Element Analysis of Corrugated Web Beams, Column and Slab Connection Under Loading Condition.
-
MDPI, Moussa Leblouba, Abdul Saboor Karzad, Sami W. Tabsh and Samer Barakat, (2021) Plated versus Corrugated Web Steel Girders in Shear: Behavior, Parametric Analysis, and Reliability-Based Design Optimization
-
Harini, B. Lingeshwaran, N, Perumal, K. Aravinthan, K (2020). Sustainable design of cold formed steel. Mater. 881885. Harini, B. Lingeshwaran, N. Perumal, K. Aravinthan, K. Sustainable design of cold formed steel.
-
Pengfei Xu, Yingjie Wei, Yuyou Yang, Xiong Zhou (2022) Application of fabricated corrugated steel plate in subway tunnel supporting structure
-
Alexandria Engineering Journal, Chenghu Guo, jun Mao, Miao Xie, (2021) calculating the elastic shear buckling strength of trapezoidal corrugated steel webs considering three different shear buckling modes
.