
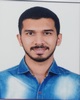
- Open Access
- Authors : Nikhil Dinesh Rokade , Dr. Sachin B. Mulay
- Paper ID : IJERTV11IS060283
- Volume & Issue : Volume 11, Issue 06 (June 2022)
- Published (First Online): 30-06-2022
- ISSN (Online) : 2278-0181
- Publisher Name : IJERT
- License:
This work is licensed under a Creative Commons Attribution 4.0 International License
Structural Health Monitoring of T-Girder Bridge
Nikhil Dinesh Rokade M.tech Structures (Student) Sandip University
Nashik, India
Dr. Sachin B. Mulay Associate Professor Sandip University Nashik, India
AbstractStructural Health Monitoring (SHM) is an easy way to determine the strength as well as failure of any structure. This paper studies and represents a report on health monitoring of a RCC t-girder bridge showing graphs and models for axial force, shear force vertical and horizontal, torsion and moments about horizontal and vertical axis are analyzed for entire bridge section. After the run analysis graphs are generated and results are observed and suitable gauges are placed at different locations for determining the deflection or fracture caused at that place.
KeywordsStructural Health Monitoring(SHM), Axial Force(P), Shear Vertical (V2), Shear Horizontal(V3), Torsion (T), Moment about vertical axix(M2), Moment about horizontal axis(M3).
-
INTRODUCTION
Structural health monitoring (SHM) system is a method of evaluating and monitoring structural health. In SHM process, dynamic responses, extraction of damage-sensitive features, andstatistical analysis are used to monitor the structure.
Need of Structural Health Monitoring?
-
Unsatisfactory monitoring and inspection of existing structure.
-
Corrosion of conventional steel with concrete.
-
Increased design load requirements over time.
-
Over all deterioration or aging or structure.
Koo, K.Y., et al., 2013[1] This paper presents experiences and lessons from the structural health monitoring practice on the Tamar Bridge in Plymouth, UK, a 335-m span suspension bridge opened in 1961. A structural monitoring system comprising wind, temperature, cable tension and deck level sensors was installed to monitor the bridge behaviour during and after the upgrading. The structural monitoring system (SMS) installed by Fugro Structural Monitoring was used to provide engineering information on the performance and condition of the bridge during and after the strengthening and widening. The sampling frequency of data acquisition was changed to 0.1 Hz from 1Hz so as to save the hard disk space. Temperature sensors, strain gauges, wind sensors and displacement sensors were set up for the study. The results showed that Tamar Bridge has proved to be a rather complex structure, a hybrid of cable stay and suspension bridges, with unusual boundary conditions. Lee, C., et al., 2012[2] This paper presents study of the principle of the 2D DIC technique and its historical development. Three potential techniques for taking strain measurements was presented and compared: single readings, averaged linear readings, and an approach on the basis of Mohrs circle. The Mohrs circle approach was found to be the most accurate and was not susceptible to
image misalignment. Strain measurement accuracy was also found to be affected by the bias error of the subpixel interpolation scheme, but the use of an 8 coefficient B-spline was found to produce satisfactory results within the error of conventional strain gauges. The 2D-DIC strain measurement has been shown to have the same level of accuracy as conventional strain gauges, it is worthwhile to pursue techniques to reduce laboratory and experimental errors, such as camera motion and misalignment, illumination changes, image acquisition inconsistencies, and lens distortion. Lynch, J.P., et al., 2006[3] This paper presents a study of Geumdang Bridge, Korea, installed with a network of wireless sensors to monitor the bridge response to truck loading. In total, 14 wireless sensors were installed in the concrete box girder span of the Geumdang Bridge to record acceleration responses to forced vibrations introduced by a calibrated truck. The fully assembled wireless sensor was roughly of size 6.4 X 8 X 10 cm3. The trucks were used to dynamically excite the instrumented box girder by driving the trucks, one at a time, over the bridge at a fixed velocity in the southward direction. Three velocities were used during testing: 40, 60, and 80 km h-1. After the trucks traversed the bridge, they were driven over the bridge at 10 km h-1 to return to their original position on the northern side of the bridge. The wireless monitoring system was shown capable of locally processing measurement data at the sensors. Based upon fast Fourier transform (FFT) and peak picking algorithms, Fourier spectra were calculated by the individual wireless sensors using time-history response data. Middleton, C., et al., 2014[4] This paper investigates the manner in which Structural Health Monitoring systems are currently designed, deployed and utilised for bridges has led to a re-evaluation of their effectiveness. The study states that SHM systems have not delivered on the promise of providing reliable, objective, real-time information that can be used to inform decision- making and actions for all the different stakeholders responsible for the bridge infrastructure. The greatest challenge is to develop new sensors that can measure the key parameters that bridge engineers require, rather than other parameters that are simpler and more convenient to measure.Moore, M., et al., 2001[5] The report provides overall measures of the accuracy and reliability of Routine and In-Depth Visual Inspections, studying the influence of several key factors that affect Routine and In-Depth Inspections, and studying the differences between State inspection procedures and reports. Ten inspection tasks were performed at seven test bridges using State bridge inspectors. The sample of participating inspectors included 49 inspectors from 25 State agencies. Inspectors were provided with common information, instruction, and tools. Inspector characteristics were measured through self-report questionnaires, interviews, and direct measurements. Two
primary types of data were collected with the help of two primary media. The primary data collected for evaluating In- Depth Inspection were the inspectors field notes generated during the inspections. Specifically, inspector identification of deficiencies was the principal information used to evaluate the In-Depth Inspection results.Nair, A., Cai, C.S., 2010[6] This paper gives a brief review of the acoustic emission technique and its applications to bridge health monitoring. The emphasis was given on available techniques of AE data processing, both qualitative and quantitative. Acoustic monitoring system essentially requires two integral components: a material deformation that becomes the source, and transducers that receive the stress waves that are generated from the source. In this study both the substructure and superstructure of bridges exhibit typical damage modes, which may include corrosion, cracking, and physical damage due to impact, fire, or fatigue cracking. While monitoring the superstructure, it must be assessed thoroughly in critical sections such as shear zones, tension zones, bearing regions, corrosion prone areas, etc. The conclusions showed that a credible amount of information was collected and the analysis of this information gives an insight into the structural response of the local area monitored under live load conditions, of intensity charts may help to better estimate the damage severity, although clearly marked zones of damage are not yet prescribed for certain materials such as concrete and steel.Park, H.S., et al., 2007[7] The paper presents a study on displacement measurement model to improve the accuracy of the measurement. The model is tested experimentally on a simply supported steel beam. Measurements wre made using three different techniques:
(1) linear variable displacement transducers (LVDTs), (2) electric strain gages, and (3) a long gage fiber optic sensor. Three-dimensional coordinates of a target structure acquired using TLS can have maximum horizontal and vertical errors of about 10 mm and maximum distance error of about 7 mm when the TLS is located at a distance of about 100 m from the structure. Vertical deflections of the simply supported beam under the action of a point load are used as serviceability assessment criterion. For each loading step, direct measurements of vertical deflections from LVDTs at L/4, 3L/8, L/2, 5L/8, and 3L/4 positions of the steel beam were used as the reference for the comparison. Maximum stress was used as safety assessment criterion for the simply supported beam under the action of a point load. The values obtained for the three loading steps using the TLS model were compared with those obtained from the electric strain gage and the long gage fiber optic sensor. The results showed that the maximum deflections estimated by the TLS model are less than 1 mm and within 1.6% of those measured directly by LVDT. The maximum stress estimated by the TLS model is also in close agreement with the directly measured value obtained from the long gage fiber optic sensor for a range of stresses from 0.24 to 0.76Fy. Psimoulis, P.A., Stiros, S.C., 2013[8] In this study Robotic Total Station (RTS) was used for the first time to measure the deflections of a short-span bridge in response to passing trains. The RTS measurements aimed to a reflector which was set on one of the mid-spans of the historical Gorgopotamos Bridge in Greece permitted to identify the measurement noise up to
-
mm when no trains were passing, and deflections with peaks of 2.56 mm during intervals when small or larger trains were passing. RTS measures reflectors changing instantaneous coordinates in a fixed coordinate system. This study focused on three-dimensional displacements of the middle of the central span, in which maximum displacement was expected. The measurement point was on the handrail of the deck, where a high-accuracy prismatic reflector by AGA Geotronics AG was fixed. The results showed that, apparent displacements along the lateral axis, were much larger, of the order of ±1.6 mm. To the passage of light service wagon apparent displacements were confined to a zone ±1.3-mm wide for the longitudinal and lateral axes, as well as for the vertical axis for the intervals before and after the train passage. It is therefore evident that from the periods of no excitation of the bridge span, the noise level is of the order of
±1.3 mm, but during the excitation of Events 1 and 3, a deflection of 2.56 mm was recorded. The only exception is the apparent displacement along the lateral axis is ±1.6 mm. Rodrigues, C., et al., 2010[10] This work is focused on the development and application to concrete bridges of new and reliable optical based transducers, more specifically, a vertical displacement transducer and a strain transducer to be embedded into concrete, both based on Fiber Bragg Grating (FBG) sensing technology. The conception, validation and application of these transducers, presenting its installation and integration in the case of the advance optical based structural monitoring system applied to the LezÃria Bridge, are also described in this paper. The strains in the bottom and top slab of the box girder were measured in critical cross- sections by means of a pair of strain transducers embedded into concrete. Additionally, deflections of all the main bridge mid-spans are also measured. Stajano, F., et al., 2010[11] In this research the author instrumented large civil engineering infrastructure items, such as bridges and tunnels, with sensors that monitor their operational performance and deterioration. The purpose of our research project, is to develop a system for continuous monitoring of such infrastructure using wireless sensor networks which, compared to wired systems, are easier and cheaper to deploy and also offer the opportunity for straightforward expansion. Domain experts such as bridge and tunnel engineers are still far from being able to buy a turnkey WSN system and apply it to their own problem: instead, they are forced to become co-developers of the WSN system and to build and sharpen their own tools. Staquet, S., et al., 2007[12] In this study loading test was performed in Belgium on a railway bridge deck consisting of simply supported composite Preflex beams. The bridge was 30 years old at the time of the test so the time dependent stress redistribution between the steel of the girders and the concrete was almost stabilised. The bridge deck was loaded progressively by two heavy diesel-electric locomotives. A 4 m long zone situated at the mid-span of the deck was instrumented and monitored during the loading test. The following measurements were taken: the mid-span deflection; the slopes in five locations; the length variations of 16 extensometers of 250 mm length situated near the bottom fibre of the beam and acoustic emission. The mix proportions for the first phase concrete were: river sand 07 mm, 500 kg/m3 ; limestone aggregates 414 mm, 525 kg/m3 ;
limestone aggregates 1428 mm, 790 kg/m3 ; early age high strength Portland cement P500 (class 3 CEB-MC90), 400 kg/m3 ; water, 172 l/m3 and water-reducing admixture (Melment): 7 l/m3 . The average compressive strength at 7 days on cubes with 200 mm sides was fc20,7 = 45 MPa (corresponding to the minimum required value of concrete strength at the transfer of pre-stressing) and fc20,28 = 60 MPa at 28 days, which corresponds nowadays to concrete grade C40/50. The second concrete phase corresponded to concrete grade C30/37 with a minimum required value of concrete strength at 28 days of 35 MPa. It could be concluded that, an excellent correlation between the measurements and the computed values was found for the deflections, slopes, curvatures and strains by assuming linear elastic and non- cracked behaviour for the beam. The appearance of cracks is a discrete phenomenon that could be undetected in the observation of global behaviour such as deflection. Vann, A.M., et al., 1996[13] The purpose of this paper is to describe how computer-based techniques can be used to facilitate data gathering from, and analysis and interpretation of, performance of civil engineering constructions in service. This paper comprises of case study of four bridges which are The Milton Bridge M74, Kessock Bridge, Goresten Fish Farm and LA Collette Breakwater. The results show that the techniques are intended to provide high quality data sets which are easy to work with and understand. This will assist engineers in their need to understand and improve their products. Washer, G., et al., 2010[14] This paper addresses the effect of solar loading on thermal imaging for the detection of subsurface deterioration in concrete bridge components. To evaluate the effect of environmental influences, a large test block was constructed. The test block was 2.4 m X 2.4 m with a thickness of 0.9 m, supported on a concrete footing as shown in the figure. Styrofoam sheets 300 mm X 300 mm in area and 13 mm thick were used as embedded targets to provide a subsurface feature that would affect thermal transfer in the block. The IR camera used in the study has a thermal sensitivity of the 0.08°C. Images are captured with a 14-bit resolution by a 320 X 240-pixel focal plane array over a temperature range from -40 to 1, 500°C. The results showed quantitative data on the effect of maximum solar load, the total solar loading energy over the course of a day, and the time of day at which maximum contrast occurs for the subsurface targets. The results of this study are significant in providing data to guide in the application of IR thermography for highway bridge inspection. Also, the results indicate that there can be a dramatic delay between the solar loading on a concrete structure and the observation of subsurface features, and that periodic cloud cover canreduce the thermal contrast observed in the IR images. Webb, G.T., et al., 2014[15] This paper describes some installed monitoring systems on the Hammersmith Flyover, a major bridge located in central London. This paper aims to show that value can be derived from detailed analysis of measurements from a number of different sensors, including acoustic emission monitors, strain, temperature and displacement gauges. Two structural monitoring systems are described, a wired system installed by a commercial contractor on behalf of the client and a research wireless deployment installed by the University of
Cambridge. The analysis showed that successful deployment of a robust and reliable SHM system is a challenging exercise; for such a system to be useful, consideration also needs to be given to how the collected data are to be interpreted. Also, measurements from both the Commercial and Research Systems have indicated that two of the flyovers pier bearings are partially restrained, rather than freely allowing longitudinal movement as had been intended by the designers.
-
-
AIM AND OBJECTIVE
-
Design and analysis of two-lane T-Girder bridge on Sap2000.
-
Run-analysis to determine maximum and minimum values of shear, torsion and moments.
-
Assign gauges as per the maximum and minimum values.
-
-
METHODOLOGY
The project consists of a RCC T-Girder double lane bridge.
The specifications of the model as follows: –
-
No. of spans= 3
-
Span Length= 25m
-
Width of bridge= 10m
-
No. of Lanes= 2
-
Width of lane= 3.6m
-
Width of median= 0.3m
-
Total Width= Footpath width + Lane1 + median + Lane2 + Footpath
1.25 + 3.6 + 0.3 +
3.6 + 1.25
= 10m
-
No. of Longitudinal Girders= 3
-
No. of Cross Girders= 6 (2 at support and 4 between supports)
Figure 1 :-Composition of pier and pier cap (mm)
Number of Shell Response Points
6608
Number of Plane Response Points
0
Number of Solid Response Points
0
Number of Link Response Points
108
DEAD LAOD ON ENTIRE BRIDGE
Figure 2: – Cross-section of Bridge (mm)
Axial Force (P)
Shear Vertical (V2)
Shear Horizontal (V3)
Figure 3: – Model showing lanes of Bridge
RESULTS AND DISCUSSIONS
After the model is complete, the run analysis of the model is carried out for two cases. Case1 being when no vehicle is passing over the bridge i.e. dead load and Case2 when vehicular load is applied as per the IS codes i.e. IRC_A_TR1 and IRC_AA_T. The run analysis automatically generates the data for the determination of gauge as per the maximum and minimum value of the moment, shear and torsion.
Table 1: – Vehicle Live load analysis: –
Description
Value
Number of lanes
2
Number of vehicles
2
Number of Vehicle Classes
2
Number of Load Points
522
Method of Calculation (Quick or Exact)
Exact
Number of Displacement Response Points
1808
Number of Spring Response Points
1808
Number of Reaction Response Points
8
Number of Frame Response Points
1336
Torsion (T)
A
For
Moment Vertical (M2)
S
Ve (
Moment Horizontal (M3)
S
Hor
(
xial ce (P)
hear rtical V2)
hear izontal V3)
Torsion (T)
VEHICULAR LIVE LOAD ON ENTIRE BRIDGE
Moment Vertical (M2)
Moment Horizontal (M3)
ACKNOWLEDGMENT
It is a pleasant task to express my thanks to all those who contributed in many ways to the success of this study and made it an unforgettable experience for me. I would like to express my gratitude to guide Dr. Sachin B. Mulay Sir for his continue support and encouragement. He has been a pillar of strength write during the preparation this report. I would like to express my sincere thanks to all our other teachers of structural engineering department. My special thanks to Dr. P. L. Naktode, Head of Civil Engineering Department, for his constant inspiration and all the facilities provided to successfully complete this work. I would also like to thank Dr. A. S. Maheshwari, Associate Dean of the Institute who has provided me this opportunity to present this dissertation. I would also like to thank to all the faculty members of the department for their valuable guidance and support during the course of my work. Also, I would like to thank all my friends who have directly or indirectly helped me in my project work throughout the course.
Table 2: – Final Observations
Description
Dead Load
Vehicular Load
Axial Force(P) (KN)
2.342*10-11
-3647.81
306.43
-3560.58
Shear Vertical(V2) (KN)
1525.45
-1525.45
4512.98
-4512.98
Shear Horizontal (V3) (KN)
1.49*10-05
-1.38*10-05
987.04
-987.04
Torsion (T) (KN-mm)
-0.0451
-0.0501
8937865
-8937665
Moment Vertical (M2) (KN-mm)
0.2891
-0.0835
17717915
-17717914
Moment Horizontal (M3) (KN-
mm)
3517844
-5451150
23435089
-5313683
CONCLUSIONS
-
After the run analysis it is observed that there is change in value of axial force, shear strength, torsion and moment from positive to negative or vice versa at point where girder is placed i.e., junction or connection of the deck slabs. So, at this point load cell i.e., beam load cell can be set up to monitor the section.
-
Model EDS-12V Vibrating Wire Sister Bar Strain Meter will be best suited for the monitoring of the deformation at an interval of every 500m to 1000 m and at a depth of 200mm to 300mm in the deck slab.
-
REFERENCES
[1] Koo, K.Y, J.M.W. Brownjohn, D. I. List, R. Cole. Structural health monitoring of the Tamar suspension bridge. Structural Control Health Monitoring. Volume 20 (4), (2013), 609625. [2] Lee, C., Take, W.A., Hoult, N.A. Optimum accuracy of two- dimensional strain measurements using digital image correlation. Journal of Computing in Civil Engineering, Volume 26 (6), (2012), 795803. [3] Lynch, J.P, Yang Wang, Kenneth J Loh, Jin-Hak Yi, Chung-Bang Yun. Performance monitoring of the Geumdang Bridge using a dense network of the high-resolution wireless sensors. Smart Materials and Structures. Volume 15 (6), (2006), 15611575. [4] Middleton C, Vardanega, P. J., Webb, G., Fidler, P. Smart infrastructureare we delivering on the promise? Paper presented at the 6th Australian Small Bridges Conference, Sydney, Australia, and May 2728, 2014. [5] Moore, M. Brent Phares, Benjamin Graybeal, Dennis Rolander. Reliability of Visual Inspection for Highway Bridges. vol. 1 US Department of Transportation. Federal Highway Administration, Washington, DC. Report No. FHWA-RD-01-020. [6] Nair, A., Cai, C.S. Acoustic emision monitoring of bridges: review and case studies. Engineering Structures. Volume 32 (6), (2010), 17041714. [7] Park, H.S, H. M. Lee. A new approach for health monitoring of structures: terrestrial laser scanning. Computer Aided Civil and Infrastructure Engineering. Volume 22 (1), (2007), 1930. [8] Psimoulis, P.A., Stiros, S.C. Measuring deflections of a short- span railway bridge using a robotic total station. Journal of Bridge Engineering. Volume 18 (2), (2013), 182185. [9] Rodrigues, C, Carlos Félix, Armindo Lage, Joaquim Figueiras. Development of a long-term monitoring system based on FBG sensors applied to concrete bridges. Engineering Structures. Volume 32 (8), (2010), 19932002. [10] Stajano, F, Neil Hoult, Ian Wassell, Peter Bennett, Campbell Middleton, Kenichi Soga. Smart bridges, smart tunnels: Transforming wireless sensor networks from research prototypes into robust engineering infrastructure. Ad Hoc Networks. Volume 8 (8), (2010), 872888. [11] Staquet, S, G. Kalogiannakis, H. Detandt, D. Van Hemelrijck andB. Espion. Field testing of a 30-year-old composite Preflex railway bridge. Proceedings of Institute of Civil Engineers- Bridge Engineers. Volume 160 (2), (2007), 8998.
[12] Vann, A.M, J. Carins, J. P. Davis, B. T. Linfoot. Intelligent logging strategies for civil engineering applications. Proceedings of Institute of Civil Engineers-Struct. Build. Volume 116 (2), (1996), 194203. [13] Washer, G., Fenwick, R., Bolleni, N. Effects of solar loading on infrared imaging of subsurface features in concrete. Journal of Bridge Engineering. Volume 15 (4), (2010), 384390. [14] Webb, G.T, Paul R.A Fidler, Peter G. Hill, Campbell R.Middelton. Analysis of structural health monitoring data from Hammersmith Flyover. Journal Bridge Engineering. Volume 19 (6), (2014), 05014003-(1-11). [15] White, D.J., Take, W.A., Bolton, M.D. Soil deformation measurement using particle image velocimetry (PIV) and photogrammetry. Geotechnique. Volume 53 (7), (2003), 619631.
[16] Wong, K.Y. Instrumentation and health monitoring of cable- supported bridges. Structural Control and Health Monitoring. Volume 11 (2), (2004), 91124. [17] Zhi, X, Ahmed Shalaby, Dan Middleton, and Alan Clayton. Evaluation of weigh-in-motion in Manitoba. Canadian Journal of Civil Engineering. Volume 26 (5), (1999), 655666. [18] P. J. Vardanaga, Webb G.T, Fidler P.R.A. Middleton C.R. Bridge Monitoring. Innovative bridge design handbook, (2016), 759-775.