
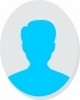
- Open Access
- Authors : K. S. Gayathri , R. Swetha , R. Swetha , Dr. D. Govardhan
- Paper ID : IJERTV10IS050485
- Volume & Issue : Volume 10, Issue 05 (May 2021)
- Published (First Online): 17-06-2021
- ISSN (Online) : 2278-0181
- Publisher Name : IJERT
- License:
This work is licensed under a Creative Commons Attribution 4.0 International License
Structural Design and Analysis of A Metallic Fuel Tank of A UAV
K. S. Gayathri1, R. Swetha2, R. Sabari Vihar3, Dr. D. Govardhan4
1,2UG Student, Department of Aeronautical Engineering, IARE, Hyderabad, India
3Assistant Professor, Department of Aeronautical Engineering, IARE, Hyderabad, India
4Head of the Department, Department of Aeronautical Engineering, IARE, Hyderabad, India.
Abstract: This work includes the structural design and analysis of a center fuel tank, port and starboard side fuel tanks. The geometry of center fuel tank consists of topcover, bottom cover, center scoop and plates at both ends. L & V stiffeners are provided on the outer shell of the tank to strengthen the tanks shell. Thegeometry ofthe side fuel tank consists of top cover,bottom cover, side-plate and plates at both the ends. L-Stiffeners are provided on the side fuel tank to strengthen the tank. Both the tanks are provided with baffle plates in the tank to prevent sloshing and also to strengthen the tank structure. The fuel tank models are designed using Catia V6 software. The finite element model is developed using hyper mesh. The structureis meshed with shell elements (QUAD4 andTRIA3). The material properties and thicknesses are assigned to the elementsand the pressure distribution is applied on the shell elements of the tank. Inertia load is applied to the whole tank model. The boundary conditions involve the front and rear plates of the tank model to be fixed in translation along the x-direction. Element edge length of 10 mm was used for meshingthe tank model. The static analysis to checkthe stresses and deflections in the tank model has been carried out using MSC PATRAN and NASTRAN softwares. From the linear static analysis, it is clear that the design of the side fuel tank is stableand is strong enough to bear the loads. The results obtained for the linear static analysisof center fuel tank and side fuel tank show that the material used will yield up to 220 n/mm2 and after this the material will fracture. Within the limit of margin of safety both the fuel tanks are safe.
Keywords: UAV, fuel-tank, pressure, MSC PATRAN, NASTRAN
-
INTRODUCTION
-
Unmanned Aerial Vehicles
An unmanned aircraft system (UAS) consists of various sub-systems whichinclude the aircraft [UAV – Unmanned Aerial Vehicle], aircrafts payload, the control stations, aircraft launch andrecovery sub-systems, support sub- systems, communication sub-systems, transport sub- systems, etc.
Unmanned Aerial Vehicle is one of thecomponents of the UAS. The aircraft[UAV] is similar to that of a manned aircraft except for the fact that it is designedin a manner that it can be operated without the aircrew aboard. The aircrew is instead substituted by an electronic intelligence andcontrol sub-systems. UAVs are specificallydesigned for various purposes like covertroles, dull & dirty roles, surveillance, research roles, military, navy, etc.
A UAV can receive controls via the up-linkfrom the control station. It will procure dataat the site of the event and will in turn sendthe images and the information via the down- link to the operators. Latest UAVs are incorporated with artificial intelligence so that the aircrafts can take smart decisionseven during the absence of the operators. The Unmanned Aerial Vehicle technology is being expanded extensively since the last30 years with the implementation of a widevariety of state-of-the-art technologies
Figure 1 General Atomics MQ-9 Reaper
-
UAV Fuel Tank
In general UAVs run on the batteries but thelater UAVs were designed in such a way they are capable of carrying fuel tank. These UAVs come under either HALE or MALE. The fuel tank of an UAV is one of the major and important components. The size and shape of an UAV fuel tank isdesigned according to the UAV design which makes it almost similar with normalaircraft. UAV fuel tank can be designed single or with a combination of two ornumber of fuel tanks with different sizes. Here we have used three fuel tanks, one center fuel tank and two side fuel tanks. The center fuel tank is connected to the engine of the UAV and the side fuel tanks areconnected to the center fuel tank. It is a one-way passage and once the valve of the side fuel tank is opened and allowed to enter the center fuel tank, the fuel cannot return backto the tank even though the center fuel is full. For this reason, side fuel tanks are of less capacity when compared with the center fuel tank. The fuel tanks of this UAVare welded.
-
-
METHODOLOGY
-
Design of Fuel Tanks:
The center fuel tank consists of filler cap, baffles, anti-g tank, fuel transfer lines, drainport, vent lines, fuel pumps,
flapper valves and fuel level sensors. Major raw material selected for the fabrication of the tank is 5083 aluminum alloy.
C-channels are provided on the tank to mount it on the airframe. Baffles are provided in the tank to prevent sloshing andalso to strengthen the tank structure. The fuel tank is fabricated from 1.5 mm thick 5083 aluminum alloy using TIG welding tomeet the strength requirements. The outlineof the center fuel tank is shown in figure 2.
Figure 2 Model of the center fuel tank of the UAV
The geometry of the side fuel tank consistsof top cover, bottom cover, side-plate and plates at both the ends. L- Stiffeners are provided on the tank to strengthen the tank. 6 mounting lugs are provided to mount the tank on the airframe. The fuel tanks are fabricated from 1.5 mm thick 5083 aluminum alloy.
Both the fuel tank models have been designed using CATIA V6 software.
-
Finite Element Analysis of theFuel Tanks:
The finite element model is developed using hyper mesh. The structure is meshed with shell elements (QUAD4 and TRIA3). The material properties are assigned to the fuel tanks with required offsets. Thicknesses assigned to shell, baffle plates, stiffeners are 1.5 mm each. The pressure distribution of 0.3 bar is applied on the shellelements of the tank. Inertia load of 3g is applied to the whole tank model. The side fuel tanks rests on three bulkheads and mounting lugs are used to attach the tank tothe three bulkheads using bolted joints. Element edge length of 10 mm was used in meshing the model. The full meshed modelalong with boundary conditions is done. The static analysis to check the stresses anddeflections in the side tank model has been carried out.
The center fuel tank is first designed in CATIA V6 software using part modeling, sheet-metal design, wireframe and assembly modeling workbenches. This model is imported to hypermesh and therethe meshing of the model is done. The meshtype is quad and element size is 10 mm. Byadjusting the mesh all over the model and checking for connectivity and quality indexthe meshing is done.
Then this meshed model of the side fuel tank is exported to PATRAN. In PATRAN, the meshed model is constrained at the side near the stiffeners and then a pressure is applied as load on the tank is applied at the outer walls of the tank. Then in Analysis, linear static type is selected and the output file type .XDB is selected.
After applying loads and boundary conditions in Patran the file is exported to Nastran to run the analysis.
After the analysis is done a file with .XDB extension, gets created. To know if there isany error in the analysis, we check for FATAL in that file. If there no FATAL thenthe analysis is done successfully. If there isFATAL then there is an error and the process of applying loads and boundary conditions has to be repeated. For results, the .XD is imported in Patran and results can be viewed.
-
-
RESULTS OBTAINED
Results for static analysis (deflections and Von-Mises stress) of the center fuel tank area deflection of 3.46 mm, Von-Mises stress of 196 N/mm2 with a material allowable stress of 220 N/mm2 and margin of safety of0.122.
Results for static analysis (deflections and Von-Mises stress) of the side fuel tank area deflection of 4.97 mm, Von-Mises stress of 217 N/mm2 with a material allowable stress of 220 N/mm2 and margin of safety of0.013.
-
CONCLUSION
From the results, we can conclude that for the fixed boundary condition, the fuel tank deflection is minimum and the margin of safety for the center fuel tank and the side fuel tank is 0.122 and 0.013 respectively. The material – Aluminum alloy 5083 has a von-mises stress limit of 220 N/mm2. Hence, the center and the side fuel tanks are safe structurally. For a pressure of 0.3 bar and 3g inertia load, the deflection of the center fuel tank and side fuel tank is 3.46 mm and 4.96mm respectively. This deflection is acceptable.
For this type of design, the major problem is sloshing – the movement of the fuel insidethe tank. Without the baffle plates, the structural design might fail due to excessive sloshing in the inner walls of the fuel tank. Baffle plates reduce the movement of the fuel and hence the pressure experienced bythe fuel tank will be decreased.
The theoretical assumption of the result, matches with the experimental results. This type of structural design of center fuel tankwith two side fuel tanks, can also be used in upcoming modern UAVs other small aircrafts.
Although the fuel gets exhausted, the location of the fuel tanks helps in maintaining the stability of the UAV. The compatibility of the fuel tank with the UAVis of major concern. Due to its complexity in design of the fuel tank, it is difficult to adjust it in a UAV. But it might be useful for combat UAVs. New models can be designed from this type of fuel tank which are suitable for the latest upcoming aircrafts.
-
FUTURE WORK
For a fuel tank, dynamic analysis poses a greater importance when compared to linear static and normal
mode analysis. Thedynamic analysis of the fuel tank gives the pressure due to the moving fluid inside the tank which is also known as sloshing. Theeffect of sloshing on the walls of the fuel tank, can be reduced by restricting the fluidmovement inside the tank by placing baffle plates at different locations in the tank. Toobtain minimum sloshing effect, the baffle plates must be placed in such a way that thefuel will have an inconsiderable movementeven when a UAV is maneuvering at very high speeds. This reduces 70% of the pressure inside the fuel tank and henceforth reducing the loads acting on the fuel tank. In further works, dynamic analysis can be performed on the fuel tank.
Largely, many components that experiencedirect loads are made up of metals. In aerospace industry also, many of the components of the aircraft are made up of composites other than the ones which haveto bear direct stresses. Metals are used vastly because they possess the capacity towithstand higher degrees of loads. Usage of metals implies a dis-advantage of increasing the weight of the vehicle. Hence,the components can be made by using composites which are lighter in weight and have a comparatively higher rate of strengthand resistance than the metals. Researchactivities are being conducted to find out the composites which are corrosiveresistant and can withstand high temperatures to retain a longer life.
Further improvements in the center as wellas the side fuel tanks can be made by manufacturing the tanks by using CFRP composites instead of Aluminum alloys. CFRP composites can help in reducing the weight of the UAV.
-
REFERENCES
-
A. Saravanan, P. Suresh, B. Aravindha and P. Kumaravel, Deformation and Stress Analysis of a Fuel Tank under Static Loading, Elsevier, pp. 1-10, 2020.
-
C. V. Jacob, N. Subramanya, M. S.Quamar and P. Bhuneshwar, Fabrication and Qualification Studies of AluminiumFuel Tank for Experimental UAV,Elsevier, pp. 1-7, 2017.
-
G. Nitin S., Practical Finite Element Analysis, 2008.
-
S. K. Bairoju, Design Optimization ofAircraft Fuel Tank by Using Finite ElementAnalysis, Journal of Aircraft, pp. 1-10,2017.
-
R. Austin, Unmanned Aircraft Systems,Chichester: John Wiley and Sons, Ltd., 2010.