
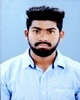
- Open Access
- Authors : Mahesh A. Lokhande
- Paper ID : IJERTV10IS120099
- Volume & Issue : Volume 10, Issue 12 (December 2021)
- Published (First Online): 20-12-2021
- ISSN (Online) : 2278-0181
- Publisher Name : IJERT
- License:
This work is licensed under a Creative Commons Attribution 4.0 International License
Structural Audit of RCC Building in Kolhapur City
Mr. Mahesh A. Lokhande
Assistant professor, Department of technology, Shivaji University Kolhapur, Maharashtra, India,
Abstract A structural audit is required for framed structures in order to propose suitable corrective actions for all sorts of structural flaws and damages. So that it can continue to meet the requirements for strength and serviceability. A structural audit should be performed at least once every five years for any structure. A structural audit should be performed every three years for structures older than 15 years. Corrosion and ageing appear to be the most common causes of structural member deterioration. Dampness and leakage from slabs, fractures in walls, and other factors cause corrosion in structural elements. As a result, the building's strength and serviceability can be improved by performing the following steps: slabs for water proofing.
KeywordsRCC building, strenght, nondestructive testing, corrosion, serviceabilty.
-
INTRODUCTION
-
Structural Audit
Structural Audit is an overall health and performance checkup of a building like a doctor examines a patient. It ensures that the building and its premises are safe and have no risk. It analyses and suggests appropriate repairs and retro fitting measures required for the buildings to perform better in its service life. Structural audit is done by an experienced and licensed structural consultant.
-
Need of structural
Structural Audit Structural audit is carried out in order to
-
To increase life of property.
-
To know the health of building and its expected life.
-
To check actual reliability of the structure.
-
In order to recommend rehabilitation techniques.
-
In order to highlight the critical areas and repair the immediately
-
For structural audit certificate required by municipality and other authorities.
-
-
Structural audit by-laws
As per clause No.77 of revised Bye-Laws of Cooperative Housing Societies: The society shall cause the Structural Audit of the building as follows:
-
For building aging between 15 to 30 years once in 5 years
-
For building aging above 30years once in 3year.
-
-
Objectives of structural audit
-
Performing preliminary inspection of the building.
-
Preparation of architectural, structural plan of the building.
-
Visual inspection to highlight critical area.
-
Performance of NDT tests.
-
E-TABS modeling of the building.
-
Finding actual strength of the building.
-
Suggesting remedial measures
-
Noting of all visible defects, deterioration and its quantification.
-
These are marked on floor drawings from which he estimates is worked out.
-
Diagnosis of damages
-
Suggest remedial measures
-
Submission of the conditions survey and structural audit report, priority wise estimate for rehabilitation, condition survey drawings, photographs.
-
Necessity of non destructive testing will be decided after inspection of structure.
-
-
Scope of the work
-
Surveyingthepremisesfromtheinsides&outsidesi.e.eac h&everypremisestobe surveyed to get a proper idea of its present structural condition. This physical survey will be carried out with hammer tapping on the RCC members to ascertain the degree of distress.
-
Identifying and noting allied problems pertaining to leakages & Seepages & any Additions/ Alterations carried out in the premises (which may be detrimental to the present health of the structure)
-
Identifying the nature of damages, extent of damages and its severity.
-
Carrying out NDT tests at required locations
-
Analyzing various defects observed, identifying the likely causes of all such damages.
-
Finally suggesting remedial measures to be adopted to restore the Structural health of the presently diseased Structure with a view to enhance its Structural Stability and Durability as per the priorities required.
-
Submitting detailed Survey Report containing our observations, suggestions, recommendations and photographic log.
-
-
-
LITERATURE REVIEW
ShahI. H. has stated structural audit is an important tool for knowing the real statusof the old buildings. The audit should highlight and investigate all the risk areas,critical areas and whether the building needs immediate attention. If the bldg. haschanged the user, from residential to commercial or industrial, this should bring out the impact of such a change. This Publication gives step by step guidelines for carrying out structural audit of old buildings.
Monteria.J.,Pathak, N.J. have estimated the soundness of existing structures whose life has crossed the age of thirty years. Concrete constructions are generally expected to give trouble free service throughout its intended design life.Thedeteriorationofbuildingscanbearesultofvariousfactorsin cludingfiredamage,frostaction,chemicalattack,corrosionofsteel etc.duringthelifespanofthestructure. The investigation of soundness is thus essential for finding the present serviceability of the structure and its scope for future developments or for the change in its utilization
Balayssac J.-P., Laurens S., has stated the management and maintenance of the buil the ritage is one of the main concerns of the owners of concrete structures. Combining NDT methods is currently considered as one of the most appropriate ways to improve the quality of the diagnosis of concrete structures. This paper describes a French project named SENSO (Strategy of non-destructive evaluation for the monitoring of concrete structures) devoted to developing a methodology for the non-destructive evaluation of concrete based on a multi-technique approach
Villain Geraldine Sbartai, Zoubir Mehdihave, implement ted non-destructive techniques (NDTs) for surveying concrete structures in marine environments, non- destructive measurement results must be correlated with concrete durability indicators such as porosity and water and chloride contents. For this purpose, tests introducing two electromagnetic methods (GPR and the capacitive technique), as well as the impact-echo method, were run on six different concrete mixes containing various porosities, with five water content values and three chloride concentrations.
-
METHODOLOGY
As we know concrete is widely used as a construction material because of its highstrength- costratioinmanyapplications.Concreteconstructionsaregenerall yexpected to give trouble free service throughout its intended design life. However, these expectations are not realized in many constructions because of structural deficiency, material deterioration, unanticipated over loadings or physical damage and thus Civil structures like buildings, dams, bridges subjected to continuous deterioration over the years For structural auditing we have chosen a residential building situated at Kolhapur and an investigation can be carried out us in the following methods:
-
Visual examination
-
Non-Destructive Testing.
-
Steps of Audit
In order to carry out structural audit old RCC building is selected of age around30years. Steps involved in structural audit carried out are as follows:
Step1: Preparation of architectural and structural plan of the building: Achitectural and structural plans are helpful in structural calculation, identifying or highlighting critical areas in the building.
Step2: Loading assumption:
Making assumption of load based on the intended use of the building i.e. whether it is commercial, residential. Finding which code requirement has been met.
Step3: Preliminary inspection of the building:
This inspection involves,
-
Visual inspection
-
Tapping observation.
-
Step4: Field Test:
After highlighting critical area in the building next step is to recommend the appropriate test to evaluate the structure which may include like
-
Destructive Testing
-
Nondestructive Testing
Step5: Recommendation of remedial or retrofitting methods.
Step6: Preparation of structural audit report.
-
-
VISUAL INSPECTION
-
Introduction
Visual testing is probably the most important of all non- destructive tests. It can often provide valuable information to the well trained eye. Visual features may be related to workmanship, structural serviceability, and material deterioration and it is particularly important that the engineer is able to differentiate between the various signs of distress which may be countered. These include for instance, cracks, pop-outs, palling, disintegration, colour change, weathering, staining, surface blemishes and lack of uniformity. Extensive information can be gathered from visual inspection to give a preliminary indication of the condition of the structure and allow formulation of a subsequent testing program.
The visual inspection however should not be confined only to the structure being investigated. It should also include neighboring structures, the surrounding environment and the climatic condition. This is probably the most difficult aspect of the whole structural investigation or any diagnostic works since what appears obvious tone may not be so to another. The importance and benefits of a visual survey should not is underrated. Often the omission of what appears to be insignificantevidencecanleadtoawrongconclusionbeingmade.T headvantageofatrainedeyeisbestdescribedbySherlockHolmesw henhewrote:Iseenomorethanyoubut I have trained myself to notice what I see.
-
Tools and Equipments for visualization
An engineer carrying outa visualsurvey shouldbe well equipped with tools to facilitate the inspection.Theseinvolveahostofcommonaccessoriessuchasmea suringtapesorrulers,markers,thermometers,anemometersandot hers.Binoculars, telescopes, borescopes and endoscopes or the more expensive fibre scopesmay be useful where access is difficult. A crack width microscope or a crack widthgauge is useful, while a magnifying glass or portable microscope is handy for close upexamination. A good camera with the necessary zoom and micro lenses and otheraccessories, such aspolarized filters,facilitatespictorial documentationof defects,andaportablecolourchartishelpfulinidentifyingvariation inthecolourofthe concrete. A complete set of relevant drawings showing plan views, elevations andtypicalstructural detailsallows recordingofobservations to bemade.
-
General procedure for visualization
Before any visual test can be made, the engineer must peruse all relevant structuraldrawings,plansandelevationstobecomefamiliarwithth
estructure.Availabledocumentsmustalsobe examinedandthese include technicalspecification,pastreports of tests or inspection made, construction records, details of materials used,methodsand dates ofconstruction,etc.
The survey should be carried out systematically and cover the defects present, the current and past use of the structure,the condition of adjacentstructuresandenvironmental condition. All defects must be identified, the degree classified, similartothose used for fire damaged concrete and, where possible, the causesidentified.The distribution and extent of defects need to be clearly recognized. For examplewhether the defects are random or appear in a specific pattern and whether the defectisconfined to certainlocations of membersor is presentall overthestructure.
Visual comparison of similar members is particularly valuable as a preliminary totesting to determine the extent of the problems in such cases. A study of similarstructures or other structures in the local area constructed with similar materials canal so be helpful inproviding casestudyevidence, particularlyifthoseotherstructures vary in age from the one under investigation. There is a need to identifyassociated or accompanying defects, especially which particular defect predominates. Segregation or excessive bleeding at shutter joints may reflect problems with theconcrete mix, as might plastic shrinkage cracking, whereas honeycombing may be anindicationofalowstandardofconstructionworkmanship.Lacko fstructuraladequacy may show itself by excessive deflection or flexural cracking and this mayfrequentlybethereason foran insitu assessment ofastructure.
Long term creep defections, thermal movements or structural movements may cause distortion of door frames,crackingofwindows,orcrackingofastructureoritsfinishes
. Material deterioration is often indicated by surface cracking of the concreteand examination of crack patterns may provide a preliminary indication of the cause.Systematic crack mapping is a valuable diagnostic exercise when determining thecauses and progression of deterioration. Observation of concrete surface texture and colour variations may be a useful guide to uniformity. Colour change is a widely recognized indicator oftheextentoffiredamage.Visualinspectionisnotconfinedto the surface but may also include examination of bearings, expansion joints, drainage channels and similar features of a structure. Any misuse of the structure canbeidentifiedwhencomparedtotheoriginaldesignedpurposeof thestructure.Anassessment may also need to be made of the particular environmental conditions to which each part of the structure has been exposed.
Inparticularthewettinganddryingfrequencyandtemperaturev ariationthatanelement is subjected to should be recorded because these factors influence various mechanisms of deterioration in concrete. For example, in marine structures it is important to identify the splash zone. Settlement of surrounding soil or geotechnical failures need to be recorded.Accountmustalsobetakenofclimaticandotherexternale nvironmentalfactorsatthelocation, since factors such as freezethawconditionsmaybeofconsiderableimportancewhenass essingthecausesofdeterioration. A careful and detailed record of all observations should be made as theinspection proceeds. Drawings can be marked, coloured or shaded to indicate the
localseverityof each feature.Defects that commonlyneed recordinginclude
-
cracking which can vary widely in nature and style depending on the causative mechanism
-
surface pitting and spalling
-
surfaces taining
-
differential movements or displacements
-
surface voids
-
honey combing
-
bleed marks
-
constructional and lift joints
-
exudation of efflorescence.
-
-
Application of visual inspection
For existing structures, presence of some feature requiring further investigation isgenerally indicated by visual inspection, and it must be considered the single mostimportantcomponentofroutinemaintenance.Itwillalsoprov idethebasisforjudgments relating to access and safety requirements when selecting test methods andtestlocations.
Asmentionedearlier,avisualinspectionprovidesaninitialindi cationofthecondition of the concrete to allow the formulation of a subsequent testing programme.It is also through suchinspectionsthatproperdocumentationofdefectsandfeaturesi n the concrete structure can be effected. With a trained eye, visual inspection can reveal substantial information regarding the structures uchas the construction methods, weathering, chemical attack, mechanical damae, physical deterioration, abuse, construction deficiencies or faults and many others. In this building is thoroughly inspected from flat to flat noting racks, spells, crazing, seepage etc. Highlighting critical area of investigation and repair same is marked on the plan of the building.
-
Need of visual
-
To inspectionTorecognizethetypesofstructuraldefects
-
To identifyanysigns ofmaterialdeterioration.
-
To identify any signs of structural distress and deformation.
-
To identify any alteration and addition in the structure, misuse this may result in over loading.
-
-
Structural system of building
Sub structure: Settlement of columns or foundations, Settlement of walls and floors,Deflection and cracks in Retaining wall, Soil bearing capacity through trial pits orfromadjacent soil data.
Super structure: Materials used and framing system of structure, Identification of the critical structural members like floating columns, Transfer beams, slender members, rusting of exposed steel and its extent.
Mention the status of all building elements like beams, slabs, columns, balconies, canopy, false ceiling, chajja, parapet and railings with respect to parameters deflection, cracks, leakages and spalling of concrete. Likewise, verify the status of water tank, staircase, lift and lift machine room.
Fig.1:- Sketch of exposed aggregate
Fig.2:- Cracks due to bending and share stresses
-
-
FIELD TEST Afterhighlightingcriticalareainthebuildingnextstepistoreco
mmendtheappropriatetest to evaluate thestructurewhich mayincludelike
-
DestructiveTesting
-
Non-DestructiveTesting
1) Destructive Testing:-
Destructive testing are carried out to understand the specimen's failure, specimensperformance or material behaviour under different loads. These tests are generallymuch easier to carry out, yield more information, and are easier to interpret than non-destructive testing. Destructive testing is most suitable, and economic, for objectswhichwillbe mass- produced,asthecostofdestroyingasmallnumberofspecimensis negligible. It is usually not economical to do destructive testing where only one orvery few items are to be produced. Analyzing and documenting the destructive failuremode is often accomplished using a high-speed camera recording continuously until the failure is detected.
Detecting the failure can be accomplished using a sound detector or stress gaugewhich produces a signal to trigger the high-speed camera. These high-speed camerashaveadvancedrecordingmodestocapturealmostanytype ofdestructivefailure.After the failure the high-speed camera willstop recording. The captureimagescanbe played back in slowmotion showing precisely what happen before,during andafter thedestructiveevent, image by image.
Sometypes of destructivetestingare
-
Stress Tests
-
Hardness test
-
Crash Tests
-
Metallographic Tests
2) Non-Destructive Testing:-
Non-destructive testing (NDT) is a wide group of analysis techniques used in scienceand technology industry to evaluate the properties of a material, component or systemwithout causing damage. The terms Non-destructive examination, Non-destructiveinspection and Non-destructive evaluation are also commonly used to describe thistechnology, because NDT does not permanently alter the component being inspected,itisahighly valuabletechniquethatcansavebothmoney and time in product evaluation, trouble shooting, and research. Analyzing and documenting a non-destructive failure mode can also be accomplished using a high-speed camera recording continuously (movie-loop) until the failure isdetected. Detecting the failure can be accomplished using a sound detector or stressgauge which produces a signal to trigger the high-speed camera. These high-speed cameras have advanced recording modes to captures omenon- destructivefailures. After the failure the high-speed camera willstoprecording.The captureimages can be played back in slow motion showing precisely what happen before,duringand
after thenon-destructiveevent, image by image.
NDT tests are applicable in testing the condition of the bridges, highways, buildingetc.NDT allows users to determine following properties of the object
-
Strength
-
Durability
-
Density
-
Moisture content
-
Elastic properties
-
Extent of visible crack
The final benefit of non-destructive testing may be hard to quantify, but its the most important of all. Knowing that your equipment is functioning the way it should (and that future accidents can be prevented with simple check-ups) adds years to the life of a beleague.
Non-destructive test:-
-
Ultra-sonic pulse velocity method
-
Rebound hammer test
-
Bar locator/Cover meter
Sr. No.
Description
Details
1
Building name
Shri Vishwanath co. housing society, E ward Kolhapur
2
Date of starting structural audit
23/11/2017
3
Year of
construction
1979
4
No. of building
Total-7
A-type 2No. B-type 3No. C-type 2No.
5
Area of plot
4023.70 Sq.m
6
Existing floor area
3760.30 Sq.m
7
Total built up area
4015.60 Sq.m
8
Structure
RCC framed structure
9
Foundation
Simple footing, Pile foundation
10
Plaster
Cement plaster with dry distemper and water proof cement paint
Sr. No.
Description
Details
1
Building name
Shri Vishwanath co. housing society, E ward Kolhapur
2
Date of starting structural audit
23/11/2017
3
Year of
construction
1979
4
No. of building
Total-7
A-type 2No. B-type 3No. C-type 2No.
5
Area of plot
4023.70 Sq.m
6
Existing floor area
3760.30 Sq.m
7
Total built up area
4015.60 Sq.m
8
Structure
RCC framed structure
9
Foundation
Simple footing, Pile foundation
10
Plaster
Cement plaster with dry distemper and water proof cement paint
-
-
CASE STUDY
11
Flooring
Roomsplane cement tiled Kitchen-1.5inchblackkadappastone
12
Skirting Dado
Whiteglazedtiled5 inch forallrooms
13
Doors
Main entrance Teak wood paneled All internal doors Nova teak wood
Any other sustainable material paneled with MS angle frame
14
Windows
MS glazed with 3/8 inch square barsasa security bars
15
Year of last repair
Generally 4 to 5 years ago
16
Details of last repair
17
-Yes
-No
-Yes
18
Mode of
inspection
-Yes
-Yes
-
Structural repair
-
Roof or any other waterproofing
-
External finish(paint)
-
Plumbing
-
None
-
Done for some of the buildings
-
Done for all buildings
-
Done for all buildings
-
Plan and Drawing
-
Architectural plan
-
Structural plan
-
Building plan
-
Visual inspection
-
Field test(NDT)
11
Flooring
Roomsplane cement tiled Kitchen-1.5inchblackkadappastone
12
Skirting Dado
Whiteglazedtiled5 inch forallrooms
13
Doors
Main entrance Teak wood paneled All internal doors Nova teak wood
Any other sustainable material paneled with MS angle frame
14
Windows
MS glazed with 3/8 inch square barsasa security bars
15
Year of last repair
Generally 4 to 5 years ago
16
Details of last repair
17
-Yes
-No
-Yes
18
Mode of
inspection
-Yes
-Yes
-
Structural repair
-
Roof or any other waterproofing
-
External finish(paint)
-
Plumbing
-
None
-
Done for some of the buildings
-
Done for all buildings
-
Done for all buildings
-
Plan and Drawing
-
Architectural plan
-
Structural plan
-
Building plan
-
Visual inspection
-
Field test(NDT)
-
-
REMEDIAL MEASURES
Following corrective measures should be taken in order to enhance the life of the building structure:
At the place of Leakage and Dampness:
1) Grouting:
Grouting in civil engineering refers to the injection of pumpable materials into a soilor rock formation to change its physical characteristics. It is one of the ways in whichground water can be controlled during civil engineering works. Grouting is suitablewhere soil permeability would create a heavy demand on pumping or where groundconditionsmean it maybeeconomicallyinefficient to borewells.
-
Visual Inspection of buidings:-
Results:- Wing A:
-
Leakage from slab
-
Diagonal cracks near opening
-
Dampness in walls and slab
-
Uneven settlement in flooring
-
Separation of balcony
-
Separation of balcony(Gap)
-
Separation of balcony Wing B:
-
Reinforcement is visible
-
Cover removal of slab
-
Diagonal cracks to wall
-
Major cracks to below of staircase cap
-
Leakage from pipes
-
Major leakage
-
Settlement of floor
-
Reinforcement is visible
Wing C:
-
Slab detached out in balcony
-
Diagonal cracks above opening
-
Major Dampness in wall
-
Major leakage
-
Major horizontal cracks above window
-
Plaster damage
-
Patches removed
Fig.3- Grounting
-
-
Injection method:
Typically, grouting is carried out is by driving pipes or boring holes into the ground, and then pumping the grout solution at high pressure through inserted tubes. The extent of grouting required for a particular area is determined through investigation of ground conditions and the calculation of a drilling pattern. This considers the size, spacing and depth of the holes required. The type of grout and the particular ground conditions will influence the spacing of the holes.
-
Grouting material:
There are several different types of material used for grouting:
-
Cement grouting:
Cement (or cementitious grout) is used for grouting materials with a high permeability. Neat cement and water or a mixture of sand (4 parts) to cement (1 part)is the usual composition. Holes are bored in a radius around the area to be excavated before being injected with a thin grout, the viscosity of which is then increased byreducing the water-cement ratio. If required, secondary holes are bored between the primary holes to ensure the complete grouting of the area.
-
Bentonite grouting:
Bentonite is produced from clay which has thixotropic properties, meaning it forms ahighly water-resistant gel which, when mixed with additives, can create a permanent barrier to water flow. This is used where soil particles are too small for cement grouting, most commonly to combat seepage in alluvial soils beneath the foundations of dams or other water- bound structures.
-
Chemical grouting:
Chemical grouting is used in soils of medium to coarse grading. Materials such as sodium silicate and calcium chloride are mixed together in liquid form and solidified into age.
There are two main processes:
Two-shot process:
Pipes are driven into the ground. One chemical is injected followed by another meaning that there action, and soil strengthening, is rapid.
One-shot process:
This involves chemical mixing prior to injection, with the hardening being delay by the composition. This allows for wider bore hole spacing.
Chemical grouting has the advantages of allowing economical spacing of bore holes,greaterpenetrationofthe grout,andmoreflexibilityintermsofthetimeof grouting.
-
Chemical grouting:
As opposed to chemical grouts, resin grouts have a very low viscosity which are ableto penetrate fine sands. The type of resin used depends on the chemical content of the local water table and may result in different times for setting. Common types include:
-
Tannin-basedgrouts.
-
Phenol-formaldehyde.
-
Resorcinolformaldehyde.
-
-
Resin grouting:
Bitumen emulsion can serve as a suitable grouting material that can be injected into fine sands as an impermeable barrier to water. Soil strength will not be increased, but cut-off walls beneath dams and other water-bound structures can be formed effectively.
a) Bitumen painting:
Applying thin layer of bitumen on surface of wall externally to avoid the entry of rainwater.
-
-
Water proofing:
Waterproofing is the process of making an object or structure waterproof or water-resistant so that it remains relatively unaffected by water or resisting the ingress of water under specified conditions. Such items may be used in wet environments orunder water to specified depths.
Water resistant and water proof often refer to penetration of water in its liquid state and possibly under pressure, whereas damp proof refers to resistance to humidity or dampness. Permeation of water vapor through a material or structure is reported as a moisture vapor transmission rate.
The hulls of boats and ships were once waterproofed by applying tar or pitch. Modern items may be waterproofed by applying water-repellent coatings or by sealing seams with gaskets or o-rings. Waterproofing is used in reference to building structures (such as basements, decks, or wet areas), watercraft, canvas, clothing (raincoats or waders),electronic devices and paper packaging(such as cartons for liquids).
-
Fiber Wrapping:
A Fiber Reinforced Polymer (CFRP) composite is defined as a polymer (plastic) matrix, either thermo set or thermoplastic, that is reinforced(combined)with a fibre or other reinforcing material with a sufficient aspect ratio to provide a discernablere n forcing function in one or more directions. FRP composites are different from traditional construction materials such as steel or Aluminum. FRP composites are an isotropic where as steel oral. Aluminum is isotropic (uniform properties in all directions, independent of
applied load). Therefore, FRP composite properties are directional, meaning that the best mechanical properties are in the direction of the fiber placement.
Reinforced concrete buildings may be vulnerable to progressive collapse due to a lack of continuous reinforcement. Carbon fiber reinforced polymer (CFRP) may be used to retrofit existing reinforced concrete beams and provide the missing continuity needed to resist progressive collapse. A Fiber Reinforced Polymer (FRP) composite is defined as a polymer (plastic)matrix, either thermo set or thermoplastic, that is reinforced (combined) with a fiber or other reinforcing material with a sufficient aspectratio(length to thickness) to provide a discernable reinforcing function in one or more directions.
-
-
CONCLUSION
For framed structure structural audit is necessary so that appropriate remedial measures can be recommended for all types of structural defects and damages .So that it continues to serve strength and serviceability requirement. For any structure it is necessary to carry out structural audit at least once In the five years. For structure older than 15years structural audit should be carried out once in 3years.
From above observation we conclude that even though heavy reinforcement is provided for the structural members and demand to capacity ratio is less than one for all structural members. Reinforcement provided is in very bad condition and lost its Strength due to corrosion. Due to corrosion there is reduction in the cross section of the reinforcement resulting on deflection under their own weight therefore unsafe to carry any further load.
It is observed that main cause of damage of the structural members is due to corrosion and ageing. Corrosion in structural members is observed due to dampness and leakage from the slabs, cracks in walls etc. So the strength and serviceability of the building can be increased by taking necessary measures such as: Water proofing slabs and walls to stop seepage of water into structural members so as to avoid further corrosion. Providing polymer mortar treatment recasting of slab etc.
ACKNOWLEDGMENT
Based on the foregoing observations, we may deduce that, despite considerable reinforcing, the demand-to-capacity ratio for all structural elements is less than one. Because to corrosion, the given reinforcement is in poor condition and has lost its strength. The cross section of the reinforcement is reduced due to corrosion, resulting in deflection under their own weight, making them unable to support any further load.
REFERENCES
-
I.HSHAH:Structural audit of RCC Building2008
-
National disaster management division: Condition assessment of the building and seismic upgradation
-
CentralPublicWorksDepartment(CPWD),GovernmentofIndia,NewDelh i CPWD Handbook on Repair and Rehabilitation of RCC Structures,Published2002.
-
Dr. G.S.SureshSeismic performance and evaluation.
-
B.H Chafekar,O.F.KadamStructural AuditInternational Journal Of Civil And Structural Engineering Research (IJCSER), Vol. 1, Issue 1,
Published2013
-
Guwahati Metropolitan Development Authority Bhangagarh, Guwahati-781005:DETAILED PROCEDURE OF TECHNICAL SAFETY AUDITPublished2012.
-
M.RodriegiesRepairandstrengtheningofexistingbuildingforearthquaker esistancePublished1988
-
Listof IndianStandardsforNonDestructiveTesting
-
IndianStandardSEISMICEVALUATIONANDSTRENGTHENINGOF EXISTINING REINFORCED CONCRETE BUILDINGS GUIDELINESIS15988:2013
-
PatilS.R, Prof SayyedStructural auditIOSR Journal of Mechanical and Civil Engineering (IOSRJMCE) e-ISSN : 2278-1684, p-
ISSN :2320334XPP6064,Published2015
-
K.RSonawane,DrA.WDhawaleStructural audit case study of RCC building in Nasik Indian journal of research, ISSN-2250-1991, VOL4, issue6, Published2015.