
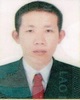
- Open Access
- Authors : Sane Souvanhnakhoomman , Dr. Alvin Y. Chua
- Paper ID : IJERTV10IS110036
- Volume & Issue : Volume 10, Issue 11 (November 2021)
- Published (First Online): 16-11-2021
- ISSN (Online) : 2278-0181
- Publisher Name : IJERT
- License:
This work is licensed under a Creative Commons Attribution 4.0 International License
Stress Distribution Analysis of A New Horizontal Axis Wind Turbine Blade using Siemens NX 10.0
Sane Souvanhnakhoomman Mechanical Engineering Department, De la Salle University
Dr. Alvin Y. Chua Mechanical Engineering Department,
De la Salle University
Abstract This paper introduces a modeling experimental analysis for a new Horizontal axis wind turbine using Siemens NX 10 software. The HAWT wind turbine's geometrical model was created based on a real parameter of the type of airfoil, the length of the chord, the angle of twist as well as the location of the centers of the airfoil in each radial segment. The analyzed wing profile of the object was designed using NRELs S823 and S822 airfoils. A numerical analysis was performed in order to determine the reliability of the structure evaluated under specific wind velocity V=20 m/s (wind sped). Also understanding in depth, the stress distribution in wind turbine blades could improve the design of wind turbine blade. The structure displacement in the wind turbine rotary blade maximum is 1.99E+006mm and the structure display stress element maximum is 1.12E+006MPa.
Index: Siemens NX 10, HAWT, NRELs S823 and S822 airfoils.
-
INTRODUCTION
In terms of versatility, a blade for a wind turbine can be divided into two fields of concern, as seen in Fig.1. The first one the field applies to the aerodynamic aspects of the blade- Aerodynamic field, while the second one refers to the aerodynamic region resistance of the blade-structural region [1].
Figure 1. HAWT blades areas.
When designing an aerodynamic area, the primary objective is to transfer wind kinetic energy into lift, which is used to produce torque. The structural area, on the other hand, is designed to withstand high bending torque values that reach a peak value at the hub, where the blade is attached to the central shaft.
The wind turbine blade configuration requires the selection of a set of airfoils with defined geometrical parameters, i.e., the type of airfoil, the length of the chord, the angle of twist as well as the location of the centers of the airfoil in each radial segment. [2] There are various basic airfoils which can be selected according to the specified specifications from open access databases. Aerodynamic airfoils generally have a chord length of the unit and are commonly accessible via their x and y cartesian coordinates. For instance, Figure 2 [3,4] airfoil S823 are displayed, which are commonly used in the development of wind turbines.
(a)
(b)
Figure 2: (a) NREL's S822 Airfoil. (b) NREL's S823 Airfoil
The airfoil type, chord length, twist angle as well as the position of 2D airfoils are scaled and twisted according to airfoil centers in each radial section during the first design phases of a wind turbine blade. However, there are many motives on a conical surface, the wind flow encountered by any segment of regular airfoils that can be picked from open access along a blade, which could be condensed to a cylinder [5]. The radial distance of the segment of the airfoil to the center of rotation allows the original 2D airfoil to be transformed into a 3D airfoil which could enhance aerodynamic efficiency
In order to support the work of designers, the rapid technological development of computers has introduced a number of tools to the engineering industry. In addition to computer-aided design (CAD) and development (CAM) systems, computer-aided engineering (CAE) is one of the methods for eliminating unnecessary costs arising from design errors. It allows sufficient strength checks to be carried out and the weakest areas of the system to be identified [6,7].
In literature review, Work has proposed simulation experiments using software based on the Finite Element Method (FEM) [8,9]. The efficiency and aerodynamic location of the vertical wind turbines axis (VAWT) is presented. The results of the wind speed, number of rotor blades and diameter of the rotor were investigated. The effect of blade material on the performance of wind turbines was compared in article [10]. The subject of wind turbine simulation research that has been
addressed most often is computer fluid dynamics (CFD) in progress [11]. The effect of the turbine enclosure was studied in paper on the torque characteristics of a vertical axis wind turbine with a straight blade [12]. The Antonius-rotor vertical axis wind turbines were analyzed numerically using Fluent software [13,14]. Displays the FEM study under working conditions of composite wind turbine blades [15].
This paper studies the rotary blade of the wind turbine using Siemens NX 10. A geometric model was developed based on a real object included using NRELs S823 and S822 airfoils, selected material of wind turbine blade is fiberglass reinforced plastic GR. In order to establish the strength of the structure tested at the particular wind speed and stress distribution in HAWT.
-
BLADE SHAPE PARAMETERS AND MATERIAL
PROPERTIES
The geometry sections were modelled as shown in figure 3 then skin loft was applied to generate a shell based on the five cross-sections as shown in the figure. In order to realize the structure, the first step is the CAD model of the blade of the turbine in Figure 4, which is achieved by importing the curves that form the aerodynamic airfoils. At the Table 1. For each segment of interest, the main characteristics of the blade are provided as well as the type of airfoil used [1].
: PARAMETERS OF AIRFOILS BLADE
Section
Radius [m]
Chord [m]
Twist Angle [º]
Airfoil Type
S1
0.28
0.183
16
S823
S2
0.29
0.188
16
S823
S3
0.39
0.178
14
S823
S4
0.55
0.162
11
S822
S5
0.855
0.132
2
S822
S6
1.5
0.067
-2
S822
Apart from parameters of Airfoils blade, to find the coordinated of X and Y axis of Airfoils S822 and S823 according to Airfoils Tools website. After that we use code section each parameter to realize model on Siemens NX 10.0 software.
Figure 3: Sketch of the airfoil distribution along the blade
Figure 4: 3D CAD model of the blade
In this paper, material of wind turbine blade is fiberglass reinforced plastic GRP. Its physical and mechanical properties are given below [16].
-
Density =1800 kg/m3
-
Modulus of Elasticity = 20700 MPa
-
Tensile Strength at break = 85 MPa
-
Compressive Strength at yield or break = 200 MPa
-
Poissons Ratio = 0.3
The force F acting on the wind turbine blades can be determined using the formula for aerodynamic resistance [17,18]
(1)
where: is the density of air, A is a variable reference area, V is the wind velocity and CD is a dimensionless drag coefficient.
-
-
SIMULATION TESTS
The paper presents only simulation tests of a wind turbine rotary blade, which after using the appropriate Siemens NX10.0 tools provide a full description of mechanical phenomena in the analyses horizontal wind turbine. Simulation tests included static and dynamic analysisof the tested structure.
In static analysis it was assumed that the model (Fig. 5) was affected by the force of gravity and centrifugal force caused by blades rotation. The wind force was also taken into account in accordance with formula (1). It was assumed that the blades coating (shell) was made of fiberglass. Cyclic symmetry fixture was set as the boundary condition, which allows simplification of the simulation model by analyzing only one rotary blade. The generated mesh of finite element simulation was a curvature-based mesh with 323 445 nodes and 175 719 elements in figure 6. For the purposes of simulation, the following measures were adopted: V=20 m/s (wind speed), T=15 980 kNm (torque), n=60 rpm (rotor speed).
Figure 5: Boundary conditions (blue color) and loads (red color) during simulation
Figure 6: the element nodes display in the body
IJERTV10IS110036
www.ijert.org
104
In figure 7, the total deformation displacement in millimeter along the blade length. The maximum total deformation is at the tip of the blade and is about 1.99E+006mm. This blade has airfoil cross section NRELs S823 airfoils. Figure 8 displayed the highest stress value equals 1.12E+006 MPa were noticed at the place of the blade and turbine hub connection. An increase in stress at the transition point of S6 to S5 were also observed.
Figure 7: The structure displacement in the wind turbine rotary blade Maximum is 1.99E+006mm
Figure 8: The structure display stress element Maximum is 1.12E+006MPa
This research can be expanding by performing CFD analysis and longitudinal scale model testing in the wind tunnel using the PIV system. Fatigue research is also predicted to assess the running time of the wind turbine being analyzed.
-
CONLUSION
The study addresses a geometrical model and a horizontal axis wind turbine simulation test. The geometric model was arranged using the Siemen NX.10 software based on a real HAWT object. On the basis of obtained knowledge, NRELs S822 and S823 airfoils rotary blade profile has been determined. The material of wind turbine blade is fiberglass reinforced plastic GRP. For mechanical analysis, the Simulation module of the Siemen NX.10 software was used. The model was separated by the curvature-based mesh in tetrahedral parabola. The stresses have been defined based on
The relation of the spinning blade to the center of the turbine is an interpretation of the numerical simultaneous effects (Fig. 8). At the tip of the rotor blade the greatest displacement (Fig. 7) was observed. The reduction in the cross section along the blade length is responsible. The results obtained explicitly show that efficient stresses on the measured turbine do not surpass the permitted stresses. This ensures that the turbine analyzed will carry out work at wind rates 20m/s
REFERENCE
-
Lon Malael, Ioana Octavia Bucur, tefan Breban (2019) writes, Horizontal-axis wind turbine blade mold manufacture by using cutting processes Competitiveness Operational Program, supported by the EU and Romanian Minister of Research and Innovation funds, (p.35)
-
] J. Zayas and M. Johnson (2016). Transforming wind turbine blademmold manufacturing with 3D printing. DOEEE (USDOE Office of Energy Efficiency and Renewable Energy), United States.
-
J. L. Tangler and D. M. Somers, NREL Airfoil Families for HAWTs, National Renewable Energy Laboratory, Washington, DC (United States), Tech. Rep. NREL/TP-442-7109, Jan. 1995.
-
http://airfoiltools.com
-
Hoschek J, Müller R. Turbine blade design by lofted B-spline surfaces. Journal of Computational and Applied Mathematics 2000;119(12)235.
-
L. Tangler and D. M. Somers, NREL Airfoil Families for HAWTs, National Renewable Energy Laboratory, Washington, DC (United States), Tech. Rep. NREL/TP-442-7109, Jan. 1995.
-
-
Kolbasin A, Husu O 2018 Computer-aided design and Computer-aided engineering MATEC Web Conf. 170 01115
-
Cekus D, Posiadaa B, Wary_ P 2014 Integration of modeling in Solidworks and Matlab/Simulink environments Arch. Mech. Eng. 61 (1), 57-74
-
Alonso-Martinez M, Adam JM, Alvarez-Rabanal FP, del Coz Diaz JJ 2019 Wind turbine tower collapse due to flange failure: FEM and DOE analyses Eng. Fail. Anal. 104, 932-949
-
Alonso-Martinez M, Adam JM, Alvarez-Rabanal FP, del Coz Diaz JJ 2019 Wind turbine tower collapse due to flange failure: FEM and DOE analyses Eng. Fail. Anal. 104, 932-949
-
Petruela M, Blazek V, Miák JVS 2018 3D analysis of vertical axis wind turbine with enclosure IEEE Int. Sci. Conf. Electric Power Eng. (EPE), 1-5
-
Belmili H, Cheikh R, Smail T, Seddaoui N, Biara RW 2017 Study, design and manufacturing of hybrid vertical axis Savonius wind turbine for urban architecture Energy Procedia 136, 330-335
-
Ozdamar G, Mertcan M, Ozdamar A 2018 Numerical Comparison of the E_ect of Blade Material on Wind Turbine E_ciency Acta Phys. Pol. A 134 (1), 156-158
-
Cristobal URN, Gallegos-Munoz A, Manuel RAJ 2012Numerical Analysis of a Rooftop Vertical Axis Wind Turbine Proc. ASME 5th Int.
Conf. Energy Sustainability, 2059-2068
-
Douvi EC, Douvi DC, Margaris DP, Drosis IE 2016 Performance and Aerodynamic Attitude of KIONAS, a New Configuration of a Vertical Axis Wind Turbine Int. Rev. Mech. Eng. 10 (3) 8873
-
Tarfaoui M, Nachtane M, Boudounit H 2020 Finite Element Analysis of Composite Offshore Wind Turbine Blades Under Operating Conditions
-
Therm. Sci. Eng. Appl. 12 (1) 011001
-
-
Armaghan Ahmad, Zohaib Elahi, Muhammad Bab 2013. CAD-CAE Integration of Horizontal Axis Wind Turbine. Horizon Research Publishing all rights reserved. Advances in Energy and Power 1(2): 56- 61.
-
Cekus D, Gnatowska R, Kwiato_ P 2019 Impact of Wind on the Movement of the Load Carried by Rotary Crane Appl. Sci. 9 (18) 384
-
Cekus D, Gnatowska R, Kwiato_ P 2018 Influence of wind on the movement of the load J. Phys.: Conf. Ser. 1101 012005
the HAWT fixed point. The wind power effect has been
deItJeErmRTinVe1d0bISy1t1h0e0a3e6rodynamic drag force.
www.ijert.org
105