
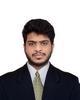
- Open Access
- Authors : Ijaz Masee Qureshi , Kaab Edroos , Acharwala Furquan , Khan Zaid
- Paper ID : IJERTV10IS120119
- Volume & Issue : Volume 10, Issue 12 (December 2021)
- Published (First Online): 24-12-2021
- ISSN (Online) : 2278-0181
- Publisher Name : IJERT
- License:
This work is licensed under a Creative Commons Attribution 4.0 International License
Steering Controlled Headlight Mechanism
Ijaz Masee Qureshi, Kaab Edroos
Dept. of Mechanical Engineering Rizvi College of Engineering Mumbai, India
Acharwala Furquan, Khan Zaid
Dept. of Mechanical Engineering Rizvi College of engineering Mumbai, India
Abstract:- The aim is to design and develop a Steering Controlled Headlight Mechanism which acts as directional headlights. This is doneby connecting headlights and steering. Present day automobiles dont have effective lighting system. Due to this many accidents are taking place during night times especially in ghat sections. The accidents can be avoided by incorporating Steering Control Headlight Mechanism. The rack and pinion steering gear mechanism are used for this project. When the steering wheel is rotated androtary motion is converted to translatory motion through the rack and pinion mechanism. When the front wheels are steered, the headlights follow the same path and the light is focused on more divergent area. In the present project, it is planned to design Steering Controlled Headlight Mechanism and a live model unit is fabricated.
Keyword: Steering Control Headlight Mechanism, The rack and pinion steering gear mechanism.
INTRODUCTION
Present day automobiles dont have effective lighting system. Due to this many accidents are taking place during night times especially in ghat sections. Conventional Head lights tend to illuminate the side of the road while cornering or shine off the road entirely, which can lead to unsafe condition. To overcome this problem an idea has been developed by introducing Steering Controlled Head Light Mechanism.
Steering Controlled Head Light Mechanism includes Headlights, Steering System which are interconnected by using linkages. The actual Steering Controlled Headlight Mechanism is the headlights follow the motion of front wheels. For this the headlights are connected to the rack of the steering system but not directly to the steering. Generally, thiscan be done by using Mechanical linkages. We can also use cables to connect headlights to the steering. Usage of cables has a great advantage of occupying less space compared to mechanical linkages.
Apart from turning the Headlights using cables mechanically, we can also turn this electrically using switches and cables as well. Electrically we can connect headlights directly to the steering by arranging a power window motor in this system. Here again, cables are used to connect power window motor and headlights. By introducing this Steering Controlled Headlights Mechanism, the Headlights cast their beam in the direction of curve and ensure better visibility during night drives on ghat roads. This provides smooth and safety ride, mind free ride for the motorist, and it is a safety system for automobile. By implementing this in the automobiles, we can provide the nation with accident-free roads for some extent.
STEERING SYSTEM:
Primary function of the steering system is to achieve angular motion of the front wheels to negotiate a turn. This is done through linkage and steering gear which convert the rotary motion of the steering wheel into angular motion of the front wheel
-
To provide directional stability of the vehicle when goingstraight ahead.
-
To provide perfect steering condition, i.e., perfect rollingmotion of the road wheels at all times.
-
To facilitate straight ahead recovery after completing a turn.
-
To minimize tyre wear.
Requirements of a good steering system are:
-
The steering mechanism should be very accurate and easyto handle.
-
The effort required to steer should be minimal and must not be tiresome to the driver.
-
The steering mechanism should also provide directional stability. This implies that the vehicle should have a tendency to return to its straight-ahead position after turning.
Rack and Pinion Steering Gear:
The system consists of a pinion attached to the steering shaft, which meshes with the flat rack on the drag line. Pinion imparts left or right motion to the rack, which causes the tie rods to move the road wheels consequently. This mechanism is usually adopted universally in all the cars that are available today with some major improvements. Earlier, steering system was robust, though it was quite difficult and heavy to use. The need of more flexible and smooth system was desired and as such some of the vital experiments in 1920 gave birth to the power steering system. The entire credit goes to Francis W. Davis who was an engineer in automotive company. With his efforts, power steering system began to be used commercially in all the cars.
HEAD LIGHTS:
A headlamp is a lamp attached to the front of a vehicle to light the road ahead. Headlamp performance has steadily improved throughout the automobile age, spurred by the great disparity between daytime and nighttime traffic fatalities: the U.S. Administration states that nearly half of all traffic-related fatalities occur in the dark, despite only 25% of traffic travelling during darkness.
While it is common for the term headlight to be used interchangeably in informal discussion, headlamp is theterm for the device itself, while headlight properly refers tothe beam of light produced and distributed by the device.
Other vehicles, such as trains and aircraft, are required to have headlamps. Bicycle headlamps are often used on bicycles, and are required in some jurisdictions. They can be powered by a battery or a small electrical generator on the wheel.
There are a number of different adaptive headlight technologies, but they are all designed to improve the drivers sight distance at night. Most adaptive headlight systems improve sight distance in corners, but some are also capable of adjusting in response to weather conditions, the presence of other vehicles, and other factors. Various types of adaptive headlights have been around throughout nearly the entire history of automobiles, but a resurgence of interest in the technology has occurred in recent years.
The Rise and fall of The Car Headlamp:
Automotive headlamps have come a long way throughout the years, the earliest being fueled by acetylene or oil in the late 1880s. Acetylene was popular because the flame was resistant to wind and rain making them standard equipment by a number of automotive manufacturers by 1904. Peerless made electrical headlights standard in 1908. In 1912, Cadillac integrated their vehicle's Delco electrical ignition and lighting system creating the modern vehicle electronics system.
Soon the innovations in vehicle electronic systems brought low and high beam headlights that could be operated by a hand lever or foot operated dimmer switch. By 1940 there was a standardized 7 inch sealed beam headlight which was required for all vehicles sold in the United States. Britain, Australia and Japan used the sealed beams, but they were never widely accepted in Europe which began the different front-end designed cars they imported into the US.
The United States Department of Transportation outlawed covered headlights in 1968, such as those used on the Jaguar E-Type, VW Beetle, Porsche 356 and Ferrari Daytona, changing again the look European models sold in the United States. Quad headlights, the use of two small rather than one large lamp per side of the vehicle, was introduced in 1952 when the Prevost Car Company included them in its Citaden bus model. Europe adopted rectangular lamps in 1961 but were prohibited in the United States where round lamps were required up until 1975.
An automotive battery is a type of rechargeable battery that supplies electric energy to an automobile. Usually this refers to an SLI battery (starting, lighting, and ignition) to power the starter, the lights, and the ignition system of a vehicles engine. Automotive SLI batteries are usually lead-acid type, and are made of six galvanic cells in series to provide a 12 volt system. Each cell provides 2.1 volts for a total of 12.6 volt at full charge. Heavy vehicles such as highway trucks or tractors, often equipped with diesel engines, may have two batteries in series for a 24-volt system, or may have parallel strings of batteries. Lead-acid batteries are made up of plates of lead and separate plates of lead dioxide, which are submerged into an electrolyte solution of about 35% sulfuric acid and 65% water. This causes a chemical reaction that releases electrons, allowing them to flow through
conductors to produce electricity. As the battery discharges, the acid of the electrolyte reacts with the materials of the plates, changing their surface to lead sulfate. When the battery is recharged, the chemical reaction is reversed: the lead sulfate reforms into lead dioxide and lead. With the plates restored to their original condition, the process may now be repeated.
CONSTRUCTION
The implementation of the steering controlled headlight mechanism requires simple construction and it is very easy process the following are the four steps that have to be followed in the arrangement of steering controlled mechanism:
Step: 1 Construction of frameStep: 2 Fixing of headlights
Step: 3 Imparting rotational movement to the headlights Step: 4 Connecting headlight and steering
The above four steps include the building of steering controlled headlight mechanism.
Working:
Mechanical Working of Steering Controlled Head Light Mechanism:
The above figure represents the working of the STEERINGCONTROLLED HEADLIGHT
MECHANISM. The main
aim of this mechanism is to provide the improved lighting in the cornering.
In the above figure the blue lines represent the old view angle of the four-wheeler before imparting the steering controlled head light mechanism. The angle of the light falling range is very low and most part of the light is not useful and is not falling in required area. Due to this the drivers do not get the better vision in curvatures especially during night times. To overcome this problem steering controlled headlight mechanism is imparted in the vehicle. In this mechanism the headlight and the steering are connected to each other so that the head light take the turns along with the vehicle to improve the corner lighting.
In the above figure the red line refers the new width of the light falling on the road after introducing the headlight steering mechanism in the vehicle. After introducing this mechanism the angle of the light is increased so that the driver will have the better vision in hill areas especially during night times. In this, the light illumination from the headlights will not fall in the unnecessary region area since the control of the light is done by the driver itself (since the headlight turns along with the steering).
Alternate Way use of Electrical Controlled Headlight Mechanism: An idea proposed
Now-a-days most of the automobiles uses electrical and electronic technologies for easy and quick operation of any system. For example, wind wiper, electronic power steering etc. So, in this project apart from working mechanically, an electrical system is can also being introduced to turn headlights. The main components used in this system are power window motor, its switch and battery. Cables are used to connect the power window motor with the headlights. Also, electrical wires are used to connect power window motor to the switch which has been placed at the steering column. The switch is also connected to the batterythrough electrical wires. A cam mechanism is mounted on the steering column to operate the switch.
When the steering is rotated towards right, the cam mechanism operates the switch (i.e., it presses the switch) then the circuit is closed and the power is supplied. Due to this the motor operates and simultaneously the headlights operate i.e., they are tilted towards right. When the steering is rotated towards left, the cam mechanism operates the switch (i.e., it lifts the switch) then the circuit is opened and the power is supplied. Due to this the motor operates and simultaneously the headlights operate i.e., they are tilted towards left.
They auto align to the center when the steering wheel is at neutral position. By this we can say that in electrical system the headlights follow the motion of steering wheel but not the motion of front wheels.
The pitch circle diameter for rack is infinite but we have the travel of pinion (i.e. Rack travel) from that value, convert the rack travel length into circular pitch diameter (only for the calculation purpose).
Rack travel = 3.14 *d(t) d(t) = 19
The value of d(t) is determined, so from that, gear ratio of rack and pinion is obtained and from the gear ratio the total number of teeth on rack is obtained.
39/26= 19/tra
tra = 12.66 round off = 13(teeth on rack).
Steering ratio
The steering ratio is defined as the ratio of steering wheel rotation angle to steer angle at the road wheels.
Steering ratio = 90+90/28+48.
Calculations:
The value of rack travel is obtained from the solid work software and on assumption/calculation basis.
For the dimension of rack and pinion we have the following formula
Rack Travel = 3.14*dpi*n n=no of steering wheel turns dpi = diameter of pinion 60=3.14*d*0.5
dpi =39 mm
Now, from the standard values of module (as per convenience).
Let us assume m = 1.5. from this the number of teeth on pinion is easily calculated.
M=d/tpi 1.5=39/tpi
Tpi = 26(teeth on pinion) Tpi = no of teeth on pinion
The module for rack and pinion will be same in order for messing of both the teeth. m =dpi/tpi = dra/tra
LIST OF MATERIALS
S.NO. |
MATERIAL |
SPECIFICATION |
QTY. |
1 |
Bearings (Roller type) |
20mm internal dia |
2 |
2 |
Bolts & Nuts with Washers. |
Size 8, 1 inch |
4 |
Size 10, 1 inch |
4 |
||
Size 13, 1inch |
10 |
||
Size 13, 2inch |
2 |
||
Size 14, 1.5inch |
4 |
||
Size 17, 4inches |
2 |
||
3 |
C-Section Beam (Structure) |
36.6142 inches length |
3 |
4 |
Metallic Strip |
1 inch length |
12 |
COST ANALYSIS
Material Cost:
SR. No |
PARTS |
Qty. |
AMOUNT (in Rs.) |
1 |
Steering system of Maruthi 800 Car |
1 |
1800 |
2 |
Head Lights |
4 |
800 |
3 |
Wheels |
2 |
1200 |
4 |
Material for construction (MS Steel bars) |
50kgs |
2200 |
5 |
Connecting cables |
8 |
900 |
6 |
Power window Motor |
1 |
1500 |
7 |
Electrical Wires |
20Mts |
400 |
Total Cost = Rs. 8800
Labor Cost = Drilling, Welding, Grinding, Power Hacksaw, Gas Cutting = Rs. 200.Overhead Charges = 30% of Manufacturing Cost
Manufacturing Cost = Material Cost + Labor Cost
= Rs.8800 + Rs. 2000
= Rs. 10800.
30% of Manufacturing Cost = 3200
Total cost of the Project = Material Cost + Labor Cost + Overhead Charges
= Rs. 8800 + Rs. 2000 + Rs. 3200
= Rs. 14000.
ADVANTAGES
-
Provides Smooth and safety ride in curved roads especially in ghat roads.
-
Provides mind free ride for the motorist.
-
Provides the nation with accident-free roads.
-
It requires simple maintenance cares.
-
This is the improved safety measure introduced in theautomobile.
-
Easy to operate.
-
Manual power required is less.
-
Repairing is easy.
-
Replacing parts is easy. No need of heavy lubrication
APPLICATION
-
The steering controlled head light mechanism can
be applied in heavy vehicles such as buses, trucks., whichride maximum in the ghat roads.
-
Specially designed for installing in buses riding in ghatroads.
-
This mechanism can also be installed in all types of commercial vehicles such as:
-
Maruthi,
-
Ambassador,
-
Fiat,
-
Mahindra,
-
Tata, etc.,
CONCLUSION
An effective steering controlled headlight mechanism was designed, based on Ackermann Steering mechanism and a live model was developed. Cost analysis was also done and a new mechanism at nominal cost was presented.
Hence the steering angle was calculated and found approx. to be = 20.00o.
REFERENCES
-
AUTOMOBILE ENGINEERING VOL-I by Dr.KIRPAL SINGH. STANDARD PUBLISHERS DISTRIBUTORS.
-
THEORY OF MACHINES by R.S KHURMI & J.KGUPTA
S. CHAND & COMPANY LTD. NEW DELHI.
-
AUTOMOBILE ENGINEERING by R.B GUPTA
-
G.B.S. NARANG, AUTOMOBILE ENGINEERINGKHANNA PUBLISHERS, DELHI. 1991, PP671.
-
AUTOMOBILE ENGINEERING WILLIAMCROUSE.
-
AUTOMOBILE ENGINEERING, K.KRAMALINGAM.
-