
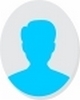
- Open Access
- Authors : Vijay K S , Likhitha R , Dhruti M Jain , Hitesh C, Hemanth Kumar B V
- Paper ID : IJERTV11IS100102
- Volume & Issue : Volume 11, Issue 10 (October 2022)
- Published (First Online): 03-11-2022
- ISSN (Online) : 2278-0181
- Publisher Name : IJERT
- License:
This work is licensed under a Creative Commons Attribution 4.0 International License
Solar Chargeable E – Rikshaw With Smart Systems
Vijay K S (Author) Former Student, Dept. of EEE Global Academy of Technology
Bangalore, India.
Hitesh C (Co-Author) Former Student, Dept. of EEE Global Academy of Technology Bangalore, India.
Likhitha R (Co-Author) Former Student, Dept. of EEE Global Academy of Technology Bangalore, India.
Hemanth Kumar B V (Co-Author) Former Student, Dept. of EEE Global Academy of Technology
Bangalore, India.
Dhruti M Jain (Co-Author) Former Student, Dept. of EEE Global Academy of Technology Bangalore, India.
AbstractAn Electric Vehicle has number of advantages over IC engine vehicles. The main advantage is that an EV has nothing to do with rise in fuel price. Another important advantage is that EVs contribution to the environment pollution is much less. Our vehicle stands different from other EVs by the fact that it can be charged by solar energy. Hence the vehicle is completely using Green energy.
Keywords Motor, Battery, Solar, vehicle, Automatic, Arduin, Brake, Multipurpose.
-
INTRODUCTION
In every Electric vehicle the main problem is, limited range of vehicle and lack of charging infrastructure. India is slowly adapting to the change. The charging stations are being installed in fuel pumps. The key point of this project is that the vehicle can be charged using Solar energy. Solar panels are installed on top of the vehicle, panels are connected to Maximum Power Point Tracker (MPPT) charge controller. The MPPT controller optimizes the match between the solar array and the battery, hence the battery is charged efficiently. The safety of battery is also taken care by MPPT charge controller during charging.
The vehicle is given with the modern touch by installing some of the smart features like Automatic headlights, Automatic Wipers, Reverse parking system, Digital instrument cluster, and Automatic braking. The digital instrument cluster uses a 7- inch TFT touch screen display, which shows all the necessary information for driver. The Automatic Braking system is built using a machine learning approach.
-
HARDWARE COMPONENTS USED
The hardware components can be divided as A. Mechanical hardware B. Electrical hardware C. Electronics Hardware
-
Mechanical Hardwarae
The mechanical Hardware is the chassis and the outer body of the vehicle. The complete vehicle body is made up of Mild steel metal. The chassis way built using 2 inch round MS pipe
and 1 inch square MS pipe. The handle bar arrangement and the front wheel arrangement was derived from Honda Active two wheeler. At the rear the chassis has been attached to electric motor differential of gear ratio 1:10. All the tires are 90/100-10 size standard tire. The Brake Arrangement is Drum Brakes at both front and rear. The rear brake arrangement is drum brake which is activated using brake by wire system. When driver press the brake pedal the brake wire is pulled and hence the drum brakes are activated.
The Body work is completely hand built. At the beginning frame works at the rear part of the vehicle was done using ½ inch square MS pipe and ¾ inch MS flat belt. The framework was covered by 1mm MS Sheet By cutting it into required shape and size. The same work has been carried out in the front part also. The complete outside body of the vehicle is constructed using MS sheet. The inside of the vehicle is covered by Aluminum checker plate to enhance the look of the vehicle. The roof section of the vehicle is built to fit the solar panel on them. And to make the vehicle protect from rain MS sheet has laid from the inside of the vehicle.
-
Electrical Hardware
-
BLDC Motor The vehicle is powered by 1.2kW BLDC electric motor. BLDC motors are best suited for electric vehicle application because of their linear torque delivery, and they can be used in hazardous environment also. The motor used in the vehicle produces around 3.8 N-m of torque at 3000rpm.
-
Battery The vehicle uses 2.4kW Li-ion battery. Li-ion batteries are known for their good energy density and efficiency. The battery used is having voltage output of 48V, and Max current of 25A.
-
BLDC Motor Controller The motor controller used here is MOSFET type controller. This controller has a current rating of 50A. and voltage rating of 48V.
-
MPPT Solar Charge Controller The MPPT solar charge controller is used to charge the battery through solar panels. The MPPT controller has 20A rated current at 48V.
-
Solar Panels The key feature of the vehicle is solar charging feature. Hence solar panels are most important. The solar panels used are 80W panels each. Total 4 solar panels are used. The total rated output of solar panel is 320W.
-
-
Electronics Hardware
The vehicle has many electronic smart features, like automatic headlight, Automatic wipers, Reverse parking system, Automatic Braking system, Digital instrument cluster. Most of the systems are built using Arduino and some are built on raspberry pi and Nvidia Jetson Nano.
-
Arduino Uno – Arduino is a open source dev board based on the ATmega328P microcontroller. Which has 16MHz frequency. This board is programmed using Arduino IDE software. It has an operating voltage of 7-12V (Input), output voltage of 5V. Arduino has 14 digital I/O pins and 6 analog pins for the interface. Arduino nano has 2kb of SRAM and 32kb of flash memory. It is used for automatic wiper, automatic headlight and reverse parking sensor.
-
Ultrasonic Sensor An Ultrasonic sensor is a device which is used to measure distance from an object. In this project this device is used to measure the distance between obstacle and the vehicle at the rear.
-
LDR sensor LDR sensor is also known as light dependent resistor, which works on the principle of variable resistance. The resistance of the sensor is varied based on the light intensity.
-
Servo motor A servo motor is used where precise angular moment is necessary. In this project the precise angular motion is required in automatic wipers.
-
5 – 12 V DC – DC converter The Converter is necessary for the automatic headlight feature because the lights are of voltage rating 12V but the controlling Arduino is rated 5V.
-
Raspberry Pi Raspberry pi is a single board computer which is used for IoT and light ML applications. In this project it is used for digital
instrument cluster application with a 7 inch TFT touch screen display.
-
-
-
WORKING
The Solar Chargeable E-Rikshaw as the name denotes the key feature of the vehicle is Solar charging feature. The four solar panels on the roof of the vehicle produces rated 320W. The solar panels are connected in series with MPPT controller. The MPPT controller is further connected to the battery. The main advantage of the vehicle is it can be charged while driving also whenever sufficient amount of sunlight is available. The battery can be charged by two ways, one is by solar panels and other is by conventional electric charging. The Battery is charged in 3-4 hours if we use conventional electric charger. If we can charge the battery by Solar energy it takes around 6-7 hours.
On a full charge the vehicle can travel up to 80-100 km based on road and load conditions. The vehicle can reach a speed of 35 kmph on no load. The Li-ion battery powers the BLDC motor, but the torque output of the motor is just 3.81 N-m. therefore a differential of gear ratio 1:10 is used to maximize the torque. The vhicle can pull around 600kg of load except it's kerb weight.
The vehicle is also having many smart features like automatic headlight, automatic wipers, reverse parking sensor, digital instrument cluster, and automatic braking system.
The Automatic head light is built using Arduino microcontroller, LDR sensor and a relay. The LDR works on the principle of variable resistance. When the light intensity falls below the specified limit The relay is activated and it turns on the light. This feature is very useful when the vehicle is moving in darkness or tunnels.
Automatic Wipers is also Arduino based project. When the rain drops falls on rain sensor it send a signal to Arduino. The Arduino activates the servo motor. The servo motor speed is depends upon the rain intensity.
Reverse parking system in the vehicle is used to detect obstacle at the rear of the vehicle. An ultrasonic sensor is used to detect the distance between vehicle and obstacle. The system also has a buzzer which makes a beep sound based upon the distance. The sound intensity increases when the distance between obstacle and vehicle decreases.
Digital Instrument cluster is a 7 inch TFT touch screen display which displays speed, rpm, battery information and range. The vehicle speed is obtained using a hall effect sensor and displayed on the screen. The screen layout is designed using PyQt5 software.
-
GRAPHS AND TABLES
MPPT controller Readings
Battery current v/s battery Voltage
Battery Voltage v/s time
-
BLOCK DIAGRAM AND PICTURES
-
Automatic Headlight
-
Automatic Wipers
-
Reverse parking system
-
Automatic Braking system
-
Solar Charging
-
-
ADVANTAGES
-
The vehicle is complete Green-Energy vehicle because it does not require any electricity.
-
Vehicle can be used in a multipurpose way, as it can be used for passengers transport as well as goods transportation
-
The vehicle is very cost effective and affordable and can be used in both urban and rural areas.
-
The Running cost of the vehicle zero since it sis chargeable through solar.
-
-
FUTURE SCOPE
-
The vehicle charging time can be reduced by using fast chargers.
-
By using more efficient solar panels power generation can be increased.
-
The excess amount of solar energy which is available can be used to power home appliances by adding an inverter.
-
Solar panel cleaners can be installed in order to overcome the dust accumulation.
-
The drum brakes can be replaced with the disc brakes with ABS system for more enhanced safety.
-
The motor can be swapped with more powerful one for more power consuming applications
-
-
CONCLUSION
The Solar Chargeable E-Rikshaw is very cost effective and useful vehicle. The solar chargeable E -rikshaw only requires the investment. The operational cost of the vehicle is zero since the vehicle is chargeable through solar power. The vehicle cost effectiveness makes it affordable for middle class people. This vehicle is multipurpose vehicle which can be use for both Goods as well as passenger purpose. Hence this vehicle is can be used by delivery agents.
-
ABBRIVATION USED
-
EV Electric Vehicle.
-
MPPT Maximum Power Point Tracker.
-
TFT Thin Film Transistor.
-
MS Mild Steel.
-
N-m Newton meter.
-
Rpm Rotations per minute.
-
IDE Integrated Development environment.
-
SRAM static random-access memory.
-
LDR light dependent sensor.
-
DC Direct current.
-
IoT Internet of Things.
-
ML Machine Learning.
REFERENCES
[1] The research of an intelligent braking control system Guiqiu Song, Ming Jiang, Guangyao zhao Published in: 2006 7th International Conference on Computer-Aided Industrial Design and Conceptual Design [2] The software design of car Low-speed intelligent braking system – Bao Fanbiao , Huang Baoshan ,Li Bing, Jiao Yonghe Published in: 2015 IEEE 2nd International Conference on Cyber Security and Cloud Computing [3] Vehicle Recognition Based on Radar and Vision Sensor Fusion for Automatic Emergency Braking – Heong-tae Kiml and Bongsob Song Published in: 2013 13th International Conference on Control, Automation and Systems (ICCAS 2013) [4] Regenerative braking system using BLDC motor with brake fail detection for Electric Auto rikshaw Anand V Shivashimpi, Sandesh Chavan, Akshay Shivaji Kokate, Dnyanshewar S Rathod Published in:Journal of Advance in Electrical Devices Volume 6 Issue 1
[5] Optimization of solar-wind energy system power for battery charging using MPPT – Ligade Gitanjali Vasant;V. R. Pawar Published in: 2017 International Conference on Energy, Communication, Data Analytics and Soft Computing (ICECDS) [6] An Implementation of Solar PV Array Based Multifunctional EV Charger – Anjeet Verma;Bhim Singh;A. Chandra;Kamal Al-Haddad Published in: 2018 IEEE Transportation Electrification Conference and Expo (ITEC)