
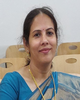
- Open Access
- Authors : Madhavi M , Pratik Tawde , Shilpa Gaikwad
- Paper ID : IJERTV10IS120156
- Volume & Issue : Volume 10, Issue 12 (December 2021)
- Published (First Online): 29-12-2021
- ISSN (Online) : 2278-0181
- Publisher Name : IJERT
- License:
This work is licensed under a Creative Commons Attribution 4.0 International License
Simulation of Switched Reluctance Motor Drive using Asymmetric Bridge Converter
Madhavi M
Lecturer
Department of Electronics and Telecommunication Engineering,
Vidyalankar Polytechnic, Wadala, Mumbai, India
Pratik Tawde
Lecturer
Department of Electronics and Telecommunication Engineering,
Vidyalankar Polytechnic, Wadala, Mumbai, India
Shilpa Gaikwad
Lecturer
Department of Electronics and Telecommunication Engineering, Vidyalankar Polytechnic, Wadala, Mumbai, India
Abstract:- An Electrical machine is a device which can ease the human effort. Electrical machines include DC machine, and AC machine (Synchronous and Induction). Nowadays, Special Machines are used to meet the demand of various applications. Among special machines, Switched Reluctance Motor (SRM) is finding massive application in various fields due to its high performance when combined together with the power electronics.. Increased applications of switched reluctance motor (SRM) leads the potential to improve its drive system. Proper operation of the SRM requires the control of the switching angles and current magnitude in order to achieve the commanded object for different modes of operation .This paper interprets the design and implementation of a SRM with a driver system which could be used for Electric Vehicle Applications.
Keywords: Switched Reluctance Motor, Rmxprt Ansys Maxwell, Asymmetric Bridge Converter.
I.INTRODUCTION
There is an increased requirements on electrical systems today. The system should have better efficiency and reduced electromagnetic. It should be flexible to meet market modification and to reduce development time. Even then, it should be economical satisfying all these constraints. Switched Reluctance Motor is a one which satisfies all the above needs. Switched Reluctance motor is a brushless AC motor. Switched Reluctance Machines (SRMs) applied in adjustable speed drives are receiving considerable attention from industry since they are characterised by rigid construction, high operation reliability, high efficiency, high torque to inertia ratio and finally low manufacturing costs. The successful realization of a SRM drive demands inter alia of the determination of the best motor construction from the point of view of the requirements of considered drive. The hybrid design method for SRM drives with application of new analytical calculation methods, finite element method and simulation models is proposed in this paper.
-
LITERATURE REVIEW
Being offline the turn-off angle of SRM is adjusted via solving a multi objective function consisting of two criteria: the torque ripple factor and copper loss. The turn ON angle adjustment is done in online,the turn on angle is simple and easy to implement since exact knowledge of SRM is not needed. The advantages of switching ON angle improves the performance characteristics of Switched reluctance motor increase in switching ON angle leads to high efficiency, input and output power. To achieve maximum specific output power, ideal non-saturating iron is beneficial. In pre-axis, the machine design should have magnetic circuits of low reluctance in order to have a high ratio of maximum to minimum inductance. Minimizing the size of both the motor and the inverter requires a small air gap and iron very high permeability. Adrian Cheok and Nesimi Ertugrul (1999) presented SRM drives may be used applications due to their simplicity and low cost and these drives require rotor position feedback to operate. The position sensorless scheme is described which uses fuzzy modeling, estimation and prediction. Instead, a fuzzy-logic- based model is constructed from both static and real-time motor data and from this model the rotor position is estimated. The system incorporates fuzzy logic-based methods to provide a high robustness against noise. It also includes a fuzzy predictive filter which combines both fuzzy-logicbased time-series prediction and heuristic knowledge based algorithm to detect and discard feedback signal error. Cheok and Ertugrul (1995) proposed Sensorless rotor position detection techniques in switched reluctance motor drives. The position sensors are commonly employed to obtain rotor position measurements; however, many systems advantages can eliminate the sensors. It includes the elimination of electrical connections to the sensors, reduced size, low maintenance and insusceptibility to environmental factors. Hence, a diverse range of indirect or sensorless position estimation methods is presented. Zhan et al. (1998) proposed a novel position and velocity observer for robust
control of switched reluctance motors. It uses simplified linear motor models and involves complex mathematical computations and requires large numerical lookup tables. It makes the schemes practically difficult to implement due to the fact that the motors normally operate under magnetic saturation and described by a nonlinear model Lyons et al. (1991) proposed flux/current methods for SR motor rotor position information. SR motor position estimation schemes a numerical table of measured static motor is used to describe the motor and measured motor data that provide a numerical model of the static angle versus flux linkage and current characteristics. The size of the table must be large for accurate position estimation and impractical for low-cost or embedded applications. Cheok (1998) proposed a new fuzzy logic based sensorless rotor position estimation algorithm for switched reluctance motor drives. It considers under steady-state speeds, the rotor position and flux linkage trajectories will be regular and periodic functions. However, during transients, the fuzzy predictors do not perform as well, due to the learning period always required with new events. Thus, under steady speeds and conditions, the confidences in predicted values are high, whereas under transient speeds and conditions, confidence might be low.
-
SWITCHED RELUCTANCE MOTOR-OVERVIEW
The Switched Reluctance Motor (SRM) is a type of stepper motor, an electric motor that runs by reluctance torque. Unlike common DC motor types, power is delivered to windings in the stator(case) rather than the rotor. This greatly simplifies mechanical design as power does not have to be delivered to a moving part, but it complicates the electrical design as some sort of switching system needs to be used to deliver power to the different windings.
B.ROTOR:
The rotor of SRM is also made up of silicon steel stamping with outward projected poles. The number of rotor poles is also preferably an even number, which is less than the number of stator poles. A position sensor is present in the rotor shaft.
Figure2.Block Diagram of SRM
The turning on and off operation of power semiconductor circuits are influenced by the signals obtained from rotor position sensor.
-
DESIGN OF SRM USING RMxprt
RMxprt is an interactive software package used for designing and analyzing electrical machines. It is a template based electrical machine design tool that provides fast, analytical calculations of machine performance and we can export the same to 2-D and 3-D geometry creation in ANSYS Maxwell. Using RMxprt, we can simulate and analyse various machines. With the help of Maxwell, we will be able to compute static electric fields, static magnetic fields, time varying magnetic fields and transient magnetic fields. Starting with a model in both RMxprt and Maxwell includes a geometric model, its boundary conditions and material assignments, and field solution and post processing information.
A.STATOR:
Figure1.Cross-Sectional view of SRM
-
MACHINE SPECIFICATION
The stator of SRM is made up of silicon steel stamping with inward projected poles. The number of stator poles can either be even or odd. Most of them have even number of poles and they carry field coils. In order that the mmfs are additive, the filed coils of opposite poles are connected in series. Group of these coils form Phase Winding and this is connected to the motor terminals. The terminals are suitable connected to the output terminals of power semiconductor switching circuitry, which has DC input supply.
S.No
Parameter
Range
1
Power Output
3HP
2
Supply Voltage
230V DC
3
Rated Current
10A
4
Speed of the Machine
1880rpm
5
Number of Stator Poles
8
6
Number of Rotor Poles
6
S.No
Parameter
Range
1
Power Output
3HP
2
Supply Voltage
230V DC
3
Rated Current
10A
4
Speed of the Machine
1880rpm
5
Number of Stator Poles
8
6
Number of Rotor Poles
6
-
DESIGN OF SRM USING RMxprt
S.No
Parameter
As per theory calculation
1
Stator Outer Diameter
194 mm
2
Stator Inner Diameter
99 mm
3
Air Gap
0.5 mm
S.No
Parameter
As per theory calculation
1
Stator Outer Diameter
194 mm
2
Stator Inner Diameter
99 mm
3
Air Gap
0.5 mm
-
PARAMETER CALCULATION
4
Rotor Outer Diameter
98 mm
5
Rotor Inner Diameter
36 mm
6
Stator Yoke Thickness
15 mm
7
Rotor Yoke Thickness
15 mm
8
Stack Length Of Stator
110 mm
9
Stack Length Of Rotor
110 mm
10
Parallel Branches
1No
4
Rotor Outer Diameter
98 mm
5
Rotor Inner Diameter
36 mm
6
Stator Yoke Thickness
15 mm
7
Rotor Yoke Thickness
15 mm
8
Stack Length Of Stator
110 mm
9
Stack Length Of Rotor
110 mm
10
Parallel Branches
1No
-
Output power Vs Speed
-
STATOR
Figure3.Cross-Stator Design
-
ROTOR
-
Flux Linkage
Figure7.Speed curve
Figure4.Rotor Design
-
SRM MACHINE
Figure5.Design of SRM
-
-
RESULTS (RMxprt)
(a) Efficiency Vs Speed
Figure6. Efficiency curve
Figure8. Flux Linkage Curve
(d) Airgap Inductance
Figure9. Airgap Inductance curve
-
DESIGN OF ASYMMETRIC BRIDGE CONVERTER
Figure10. Asymmetric Converter circuit diagram
Half-bridge IGBT modules are the popular choice to build asymmetric bridge converters and many other converters in industrial applications, instead of discrete IGBT modules. Because the diodes for freewheeling are necessary even there are build-in diodes in the discrete IGBT modules. It makes the circuit less trustworthy and more complicated phase branch with half-bridge modules for typical SRM converters. It can be seen that each phase branch needs two
half-bridge switch modules. Consequently, a four-phase SRM drive requires eight half-bridge switch modules. Therefore, the use of half-bridge switch modules in asymmetric bridge converter brings low utilization and high count of switch devices. To figure out the problem, a new converter for SRM drives is developed illustrates the proposed converter circuit for four-phase SRM drives. It can be observed that the proposed converter needs four half- bridge IGBT modules and four SCRs, in comparative to eight half-bridge IGBT modules in asymmetric bridge converters. On the other hand, each phase is controlled by different switching devices. It is helpful to reduce the temperature rise and extend the lifetime of IGBT components.
-
OPERATION OF ASYMMETRIC BRIDGE CONVERTER
Discharging mode:
Figure13. Discharging mode
-
Block Diagram of SRM Drive
Charging mode:
Figure11. Charging mode
Freewheeling mode:
Figure12. Freewheeling mode
Figure14. Block Diagram of SRM Drive
The block diagram consists of following important units viz. IGBT Intelligent Power Module (IPM), PIC16FXX40 PIN DSP Controller, Switched Reluctance Motor and Hall Sensors.IPM contains Bridge rectifier, Asymmetrical converter, Current sensors and Signal conditioner. The IPM consists of a single phase Bridge rectifier, IGBT Asymmetrical converter, Current sensors, Signal conditioner and protective devices. The IPM is rated for20 A,600V. The Rectifier & Filter block outputs the filtered DC voltage to the converter. The converter excites the SRM phases in the required sequence to rotate the motor. The Hall Effect Current sensors sense the output currents of the converter and gives signals to the signal conditioner block. The heart of the closed loop control scheme is the DSP controller. The inputs to the DSP are provided through connector. The analog inputs to the DSP are conditioned phase current signals and the digital inputs are Hall sensor position signals of the SRM. The DSP controller processes these inputs and gives the corresponding outputs to the Asymmetrical converter .The outputs of the DSP are eight PWM signals. These signals are fed to various IGBTs through high speed opto-isolators. The main function of the opto-isolator is to isolate the PWM signals from the main power circuit of the IGBT converter. The actual switching of the IGBTs is therefore controlled by the DSP controller by means of the PWM signals. The necessarysoftware for operating the DSP controller is stored in PC. A Power
Analyzer is used to measure, capture and analyze the voltage and current waveforms of the motor.
-
SIMULATION MODEL OF SRM DRIVE USING MATLAB
XIII. CONCLUSION AND FUTURESCOPE
A Switched Reluctance motor ,by assigning all the parameters of it, designed using RMxprt and the necessary output were noted. The driver circuit for the SRM drive was also developed using MATLAB and its required outputs were simulated.
-
Speed:
-
Torque:
-
Flux:
Figure14. Simulation Model using MATLAB
-
-
SIMULATION RESULTS
Figure15. Speed curve
Figure16. Torque curve
-
REFERENCES
-
Mahmoud M.Elkholy,Hamid M. Elswey and Afaf F. Abdel- kader, Development Operation Of Switched Reluctance Motor By Advancing The Switching ON Angle, Vol. 6 No. 1 January-
June 2012; pp. 49-64
-
Ali SHAHABI*,Amir RASHII,Milad AFSHOON,SeyyedMortaza SAGHAIAN NEJADDepartment of Electrical and Computer Engineering,Isfahan University of Technology,Isfahan,Iran, Commutation Angles Adjustments In SRM Drives To Reduces Torque Ripple Below The Motor Base Speed,Turk J Elec Eng & Comp Sci (2016) 24: 669-682.
-
JawadFaiz,SeniorMember IEEE, B.Ganji,P.Pillay, Senior, Member IEEE and C.Yicheng,Anlaytical Core Loss Model For The Switched Reluctance Motor With Experimental Verification,
-
TorstenWichert,M.Sc.,DesignAnd Construction Modification Of Switched Reluctance Machines,
-
R. Krishnan, Switched Reluctance Motor Drives: Modeling, Simulation, Analysis,Design, and Applications, Boca Raton, FL: CRC Press, pp.398, 2001.
-
T. J. E. Miller, Electronic Control of Switched Reluctance Machines, Oxford:Newness, pp. 272, 2001.
-
I. Husain, Minimization of torque ripple in SRM drives, IEEE Trans. on
Industrial Electronics, Vol. 49, No. 1, pp. 2839, February 2002.
-
J. Ye,B. Bilginand A. Emadi,An Extended-Speed Low-Ripple Torque Control
of Switched Reluctance Motor Drives, IEEE Trans. on Power Electronics, Vol.
30, No. 3, pp. 1457 -1470, 2015.
-
Praveen Vijayraghavan,Design Of Switched Reluctance Motor And Development Of A Universalcontroller For Switched Reluctance And Permanentmagnet Brushless Dc Motor Drives,November 15, 2001
-
J. Uma and A. Jeevanandham,Performance Of Four Phase Switched Reluctance Motor Drive Using Single Pulse Width Modulation Technique Under Constant Turn Off Angle And Random Turn Off Angle,ISSN 1819-6608VOL. 10, NO. 5, March 2015.
-
T. Dinesh Kumar PG scholar, Department of EEE, PSG College of technology, Coimbatore, India A. Nagarajan PG scholar Department of EEE, PSG College of technology, Coimbatore, India,
-
Design Of Switched Reluctance Motor For Elevator Application,Journal of Asian Scientific Research, 2013, 3(3):258- 267.
Figure17. Flux curve