
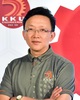
- Open Access
- Authors : Achinee Polsawat , Suwit Kiravittaya , Pirat Khunkitti , Apirat Siritaratiwat
- Paper ID : IJERTV9IS080243
- Volume & Issue : Volume 09, Issue 08 (August 2020)
- Published (First Online): 29-08-2020
- ISSN (Online) : 2278-0181
- Publisher Name : IJERT
- License:
This work is licensed under a Creative Commons Attribution 4.0 International License
Scratch and Surface Roughness Detection on Magnetic Disk by using Red and Blue Light Reflection Approach
Achinee Polsawat1
1Department of Electrical Engineering, Faculty of Engineering,
KhonKaen University, KhonKaen/40002, Thailand
Suwit Kiravittaya2
2Department of Electrical and Computer Engineering, Faculty of Engineering, Naresuan University, Phitsanulok/65000, Thailand)
Pirat Khunkitti3
3Department of Electrical Engineering, Faculty of Engineering,
KhonKaen University, KhonKaen/40002, Thailand
Apirat Siritaratiwat4
4Department of Electrical Engineering, Faculty of Engineering,
KhonKaen University, KhonKaen/40002, Thailand
Abstract:- In hard disk drive (HDD) manufacturing processes, a quality inspection mainly focuses on detecting the scratches on the magnetic disk since it could essentially affect the read/write ability of the HDD. In this research, a non-destructive technique using light reflection technique to detect the scratch on the magnetic disk is proposed. The red and blue laser diodes are performed as a detector to identify the size and position of scratches where an optimistic intensity of laser power is measured. It is clearly indicated that the scratches on the magnetic disk can be experimentally detected by this newly invented instrument. The size and position of scratches can be also examined by using either red or blue laser. It is intriguingly found from the laser power intensity analysis that the detected signal is independent on distance between magnetic disk and laser source. The scratched characteristics are well agreed with those obtained from Scanning Electron Microscope (SEM) and Stereoscopic Microscope (SM). One of its advantages is that it is able to utilize during the fly testing in order to rejection of damaged disk prior to further HDD manufacturing process.
Keywords – Hard disk drive, Light reflection technique, Magnetic disk, Scratches detection.
-
INTRODUCTION
Scratch detection on magnetic disk is an important process of a quality inspection of the hard disk drive (HDD) manufacturing, since the scratches could possibly affect the read/write performance of the HDD [1]. The scratches are mainly caused by the contamination in the HDD assembly processes and the crash between the magnetic recording heads and the magnetic disk [2]. So far, the scratch inspection process in manufacturing processes is required in order to reject the damaged disks before the disks are transported to the assembly process. This inspection process also prevents the waste of production time and cost [3].
The scratch detection techniques are normally categorized into two types which are destructive and non-destructive methods. The destructive method can be done by using many techniques such as Scanning Electron Microscope (SEM) [4], Atomic Force Microscopy (AFM) [5] and etc. However, the non-destructive method is more suitable for HDD manufacturing because it is no need to destroy magnetic disk. This method can be performed using several approaches consisting of stereoscopic microscope (SM), laser scanning [6], laser Doppler heterodyne interference system [7] and infrared camera [8, 9]. Since the scratches on magnetic disk is difficult to detect due to its hair-line type and its glossy surface. Todtong et al. proposed a new inspection approach by using laser beam from CD pick-up head [9, 10]. It showed a good ability to locate the scratch position during the disk-running process but there are still some limitations in classifying the significant details of scratch, such as the scratch characteristic and dimension [11]. The authors demonstrated a shape measurement of scratches by using laser beam of CD pick- up head but, nevertheless a large noise in the detection process was still occurred [12]. Various laser lights have been used to detect scratches on magnetic disk, such as SEM, AFM, laser Doppler, CD and DVD pick up head [13]. Some major limitations of these techniques are the ability to perform in running process of manufacturing and the indistinctness of scratch characteristics. Therefore, this paper will propose a new approach of non-destructive scratch detection to identify the position on magnetic disk by light reflection technique. The red and blue laser diodes are used as a detector to specify the size and position of scratches. The intensity analysis of suitable laser light for scratch detection on magnetic disk is also demonstrated. The shapes of scratches are also examined by the SM and SEM in order to compare with the experimental results.
-
EXPERIMENT SETUP
-
Light reflection technique for scratch detection
The diagram of the proposed light reflection technique for laser wavelengths of blue and red light, 405 and 650 nm, respectively, is shown in Fig. 1 [14]. A laser beam is propagated onto a surface of magnetic disk and then, reflected to a portion of photodiode detector. The specifications of the red and blue lasers are shown in Table 1.
Fig 1. Principle of laser light reflection [6].
In order to analyze an output signal of photodiode, it is converted by photodiode detector to a current signal and then, amplified by a non-inverting amplifier circuit as shown in Fig. 2 [15]. An output voltage (Vo) can be calculated by equation (1) where R2 is a feedback resistance, R1 is a source resistance and Vi is a 5 V input voltage [16].
V0 = (1+ R2/R1) .Vi (1)
Laser diode
Vi =5V
Photodiode
I-V
1K
+
–
R2
10K
R
R
1K
1
Non-
inverting Amp
Output
Vo Signal
Oscilloscope
Fig. 2 The measurement setup of the proposed method for light reflection and amplifier circuit [13,14,17].
Table 1. Specifications of laser diode [17].
Specification
Blue Laser
Red Laser
Laser diode (LD)
Laser wavelength (nm)
405
650
Maximum threshold current (mA)
300
300
Output Power (mW)
250
250
DC Input Voltage (V)
3.6-4.2
3-5
-
Laser diode technique for scratch characterization
The characteristics of scratches on magnetic disk were experimentally evaluated by using the proposed laser diode technique. The SM and SEM were also performed to characterize scratches in order to confirm the experimental results. They were done in the final process because a magnetic disk must be destroyed.
The 8x-40x magnification of SM were used to scan the visible scratches while the SEM (JEOL JSM-6010LA) with image resolution of 5x-300,000x of magnification at 400-700 nm wavelength was performed to evaluate the size of the scratches. In addition, the laser intensity is also measured by laser power meter, model 843-R of Newport, which is capable for measuring the power level from pico- to thousands of Watts. The setup of laser intensity measurement is shown in Fig. 3.
Laser Power Meter the
Model 843-R of Newport
Laser Power Meter the
Model 843-R of Newport
Magnetic disk
Laser beam
Laser
Detector
-
Scratches detection system
Fig. 3 The Intensity measurement setup.
The light reflection technique and laser diode technique are assembled in the scratch detection system asits block diagram is shown in Fig. 4.
Power supply for laser diode
Photodiode detector
Photodiode detector
650 nm
amplifier circuit
amplifier circuit
405 nm
Stepping Motor
Motor control circuit
Motor control circuit
Oscilloscope Measurement
Oscilloscope Measurement
Stepping Motor
Fig. 4 The block diagram of scratch detection system.
A 2.5-inch magnetic disk is set to rotate at 1,500 rpm by using stepping motor and controlled by microcontroller. The components of proposed system are a laser diode (LD), photodiode circuit, stepping motor, control circuit and amplifier circuit. A maximum threshold current of LD is 300 mA and an operating voltage is 3-5 V where the output power is 250 mW. The assembly of proposed detection system is indicated in Fig. 5.
(a)
Laser Diode and Photodiode
Stepping Motor
Motor Drive
Amplifier Circuit
Motor Control Circuit
(b)
Laser diode Photodiode
Laser Beam
Magnetic disk
Fig. 5 An experimental setup of (a) an overall system and
(b) laser and detector section.
-
-
RESULTS AND DISCUSSION
III.I Positioning comparison of 3 scratch sizes between red and blue lasers with current and distance variation
Three sizes of deliberately marked scratch, i.e. 55, 332 and 94 m, were measured and later scanned by SEM. The red and blue laser diodes perform as detector to specify scratch positions on a disk. A 70-250 mA input current source was varied and set at 190, 220 and 250 mA in order to compare these results for 1 and 2 cm distances for both red and blue lights as shown in Fig. 6 and 7, respectively.
(a)
(b)
Fig. 6 The amplitude of the three scratches on the magnetic disk by using red laser with varied currents of 190, 220 and 250 mA
at (a) 1cm and (b) 2 cm distances.
It is truly seen that when a current is increased, a voltage output is relatively increased and its signal is more visible. However, a voltage output of 1 cm distance is larger than that of 2 cm distance. This can be explained in term of intensity variation effect.
Moreover, it is clearly seen that output voltages in Fig. 6 measured by a 650-nm-wavelength red light are about 2.5 times larger those of a 405-nm-wavelength blue light as shown in Fig. 7.
(a)
(b)
Fig.7 The amplitude of the three scratches on the magnetic disk by using blue laser with varied currents of 190, 220 and 250 mA
at (a) 1cm and (b) 2 cm distances.
The locations and characteristics of the scratch can be determined from an output signal. The locations are estimated from spike characteristics on the line and dependent on the size of scratch. The location can be observed from the presence of signals and calculated by the relationship between the velocity and the time of occurrence. In Fig. 6(a), for a 190 mA input current, it is estimated that maximum amplitudes of 94, 332 and 55 m scratches are 1.24, 1.3 and 1.18 V where minimum amplitudes are 0.86, 0.74 and 0.88 V. The calculated peak-to-peak voltage of 0.38, 0.56 and 0.3 V indicate the size of the scratches. These results are well agreed with those of a 250 mA input current where their maximum amplitudes are 1.82, 1.78 and 1.64 volt and minimum amplitudes of the scratches are 1.08, 0.9 and 1.1 V. The differences are 0.74, 0.88 and 0.54 V. It is intriguingly noticed that the difference of signal is dependent on the size of scratch.
Three detected scratches show different peaks of amplitude referred to that of smooth surface and this is identifiable of scratches. It is also observed from Fig. 6(a) and (b) that the distance between disk and laser of 1 and 2 cm has no significantly affect to the results as their output amplitudes are almost the same.
In Fig. 7(a) and (b) as a blue laser is studied, it is clearly seen that scratches on a disk of input current of 190 and 250 mA are more visible than that of 220 mA in both 1 cm and 2 cm distances. It is also explicitly seen that three scratch signals represent
their locations relatively to the velocity and times of occurrence. In addition, the peak-to-peak voltages also showed similar tendency to those of red laser. For example in Fig. 7(a), as an input current is 190 mA, the maximum amplitudes of 94, 332 and 55 m scratch are 0.5, 0.52 and 0.46 volts where the minimum amplitudes are 0.3, 0.3 and 0.36 volts, respectively. The peak-to- peak voltages are 0.2, 0.22 and 0.1 volts. That means the peak-to-peak voltage may indicate the sizes of scratches. It is possibly due to the dependence of different power between receiving and transmitting on a scratch size causes relative different voltages between the near end, or a maximum voltage, and the far end, a minimum voltage. It is more understandable to compare cross sectional pictures by SEM in Fig 9(a)-(c).
It also present a similar result for a 250 mA current as the peak-to-peak voltages of 94, 332 and 55 m scratch are 0.2, 0.32 and
0.18 V. It is also noticed that distances between disk and laser of 1 and 2 cm are not effective to the result because output voltages are nearly the same.
Therefore, it is found from the experiment that this technique can identify the scratch position and a peak-to-peak voltage of signal seems to depend on scratch characteristics. The distances of 1 and 2 cm between disk and laser show no influence on the measurement. Finally, the red light provides a larger output voltage or signal amplitude than that of blue light and also, shows more visible signals in all scratch size than those of blue one. However, one interesting result shows that amplitudes of red laser are about 2.5 times larger than those of blue. This is can be explained that the shorter the wavelength, the higher the energy. Although the blue light can carry more photonic energy than the red one, the red light shows less dispersion in the air. In addition, since the blue light is harmful, the power of intensity is set at lower power, as explained in the next topic. This possibly causes high amplitude of red light presented in the results.
(a)
(b)
Fig. 8 Power measurement of laser intensity with varying applied current of 70 to 250 mA to (a) red and (b) blue lasers.
III.II Dependence of laser current and power
It is essential to find proper laser intensities of red and blue lights to detect a scratch on the magnetic disk. The powers of red and blue lasers were then measured. The input current of the laser diode was varied from 70 to 250 mA for both lasers and the distance between the laser and the disk was varied at 1 and 2 cm. As shown in Fig. 8, it is found that the output power of both lasers at a distance of 1 or 2 cm produces similar light intensity. The maximum energies of red and blue lasers were about 155 and 22 mW/cm2, respectively, at a 250 mA applied current. However, the output power of the blue laser was started when the input current of the laser diode was more than 110 mA in order to protect the harmful light to eyes.
(a)
(b)
Fig. 8 Power measurement of laser intensity with varying applied current of 70 to 250 mA to (a) red and (b) blue lasers.
The laser power was measured according to the experimental setup shown in Fig. 8. The energy of the red and blue lasers was measured in the three configurations which were the directed light of laser to detector, reflected light of laser to non-scratch disk to detector, and reflected light of laser to scratch disk to detector of both lasers. From table 2, it was found that the maximum laser powers of direct measurement of red and blue lasers are 155 and 22 mW/cm2, respectively. The maximum laser power of reflecting light to non-scratched disk of red and blue laser are 133.34 and 20.26 mW/ cm2 which are 86% and 90% comparing to the light intensity from direct measurement, respectively. In addition, the maximum laser power of reflecting light to scratched disk of red and blue laser are 123.61 and 5.5 mW/ c2 which are 79.75% and 25% comparing to the light intensity from direct measurement, respectively.
Table. 2 Results of laser power of direct measurement, reflected light to non-scratched disk and reflected light to scratched disk of red and blue lasers.
Red Laser
Ia
Laser Power (mW/cm2)
Laser direct to detector
Non-scratch disk
Scratch disk
1cm
2cm
1cm
2cm
1cm
2cm
190mA
105.36
109.11
71.79
71.63
66.61
66.03
250mA
155.00
150.93
133.34
132.92
123.61
122.55
Blue Laser
Ia
Laser Power (mW/cm2)
Laser direct to detector
Non-scratch disk
Scratch disk
1cm
2cm
1cm
2cm
1cm
2cm
190mA
12.02
12.00
10.40
10.38
3.10
2.95
250mA
22.00
21.97
20.26
20.21
5.50
5.04
It is seen that the laser power of red light is larger than the blue light because of less dispersion of red light and less power set for the blue light. However, it is interestingly found that the powers of both lasers tested in 3 configurations are well agreed. The scenario of laser direct to detector provides larger laser power than that of non-scratch disk. It is obviously seen that the laser power reflected from a scratch disk shows the least power. This ensures that both light sources at any distances can detect a scratch by applying an input current more than 130 mA because of the linear dependency between current and laser power. The least power shows that the scratch occurs on the disk.
-
Scratches measurement on the magnetic disks by using SEM and SM
In order to confirm the results of the scratches characteristics measured by the proposed technique, three different scratches were also measured by the SEM with a magnification of 300,000x and the SM with a magnification range of 8x to 40x. Fig. 9(a) – 9(c) show the SEM measurement results of scratch characteristic with the scratch width of 55, 94 and 332 m, respectively, while Fig. 9(d) 9(c) illustrated the scratch characteristic measured by SM at the scratch width of 30, 70 and 230 m. It was found that the sizes of small scratch measured by SEM are similar to that of SM. However, a difference of scratch size measured by two equipment becomes higher at larger scratches as seen from Fig. 9(c). The measurement results were different at the large scratches measured by SM due to the unclear boundary of the scratches. Due to the very high magnification of SEM, it is appropriate to identify the scratch characteristic at 10s micrometer scale, while the SM is suitable to analyze the characteristic of larger scratches that was larger than 10s micrometer scale. Remarkably, it is found that the SEM, SM measurement results of scratches characteristic show a good agreement with the experiment results done by the laser diode of CD and DVD pick-up heads.
55 m 94 m 332 m
-
(b) (c)
-
30m
70m
230m
-
(e) (f)
Fig. 9 The scratch characteristic measured by SEM with scratch sizes of (a) 55 m (b) 94 m (c) 332 m and measured by SM with scratch sizes of (d) 30 m
-
70 m (f) 230 m
-
-
CONCLUSIONS
A non-destructive technique to detect the scratch on the magnetic disk by light reflection technique was proposed. The detection system was set up by using the red and blue laser diodes as a scratch detector to detect the size and position of scratches. It was found that the scratches on the magnetic disk can be detected by using the proposed technique. The detection system is also able to identify the size and position of scratches by using either red or blue laser. The laser power intensity analysis shows that the distance between magnetic disk and laser source has no effect on the detected signal. In addition, the characteristics of scratches obtained from SEM and SM measurement indicates a good agreement to that of proposed technique. It is noted that this technique can detect the surface roughness and small scratches at the micrometer scale. The proposed technique has the advantages over the existing techniques since it can be performed to detect the scratches during the manufacturing process as on the fly testing. It also has shorter time consume, materials and requires much lower cost.
ACKNOWLEDGEMENTS
Authors would like to thank Mr. Pimai Sawangpol from Department of Electronic computer, Dr. Kesinee Chantharasophon from Department of Microbiology, UbonRatchathani Rajabhat University, Ms. Pairor Sangwang from College of Medicine and Public Health and Dr. Worakarn Wongsaichua from Department of Electrical and Electronic Engineering, UbonRatchathani University for the instrumental support. Many thanks to Seagate Technology (Thailand) Co. Ltd., for most materials, measurements and discussion.
REFERENCES
-
P. F. Odgaard, J. Stoustrup and P. Andersen, (2007). Detection of surface defects on compact discs. Joburg Centre for Software Engineering. 1-9.
-
M. Furukawa, J. Xu, Y. Shimizu and Y. Kato, (2008). Scratch-induced demagnetization of perpendicular magnetic disk. IEEE Transactions on Magnetics, 44(11), 36333366.
-
H.Y. Zhang, Z. H. Wang and H.Y. Fu, (2019). Automatic scratch detector for optical surface. OPTICS EXPRESS, 27(1), 15- 22.
-
P. Russell and D. Batchelor, (2001). SEM and AFM: Complementary techniques for surface investigations. Microscope and analysis. 9-12.
-
C. M. Mate, B.K. Yen, D. C. Miller, M. F. Toney, M. Scarpulla and L.E. Frommer, (2001). New methodologies for measuring film thickness coverage and topography. IEEE Transactions on Magnetics, 36(1), 110-114.
-
H.L. Huang, C. H. Liu, W.Y. Jywe, et al. (2009). Development of a DVD pickup-based four-degrees-of-freedom motion error measuring system for a single-axis linear moving platform. Proceedings of the Institution of Mechanical Engineers Part B Journal of Engineering Manufacture, 224, 37-50.
-
S. Zhu, W. Zhou and Y. Song, (2012). Detecting oscillation amplitude and defects of hard disk rotating in high speed by laser Doppler technique.
Measurement, 45(1), 74-78.
-
Y. Kwee, W. Kee and S. Liu, (2011). Heat source analysis of hard disk drives with different wall conditions using infrared system. Engineering, 3(1), 22- 31.
-
Y. Todtong, A. Kaewrawang, R. Sivaratana, A. Kruesubthaworn, S.M. Thompson and R. Sivaratana, (2013). Thermal image refinement approach for scratches on a magnetic disk evaluated at various angles. Instrumentation Science & Technology, 41(4), 365-381.
-
E.T. Hwu, S.K. Hung, C.W. Yang, K.Y. Huang and I.S. Hwang, (2008). Real-time detection of linear and angular displacements with a modified DVD optical head. Nanotechnology, 19(11), 1-7.
-
B.K. Nayak and M.C. Gupta, (2010). Ultra fast laser-induced self-organized conical micro/nano surface structures and their origin. Optics and Lasers in Engineering, 48(10), 966-973.
-
A. Polsawat, N. Suwannata, A. Siritaratiwat and A. Kruesubthaworn, (2015). Signal analysis of scratch-detection onmagnetic disc by using light reflection approach. Applied Mechanics and Materials, 781, 203-206.
-
C.L. Chu1, C.H. Lin1 and K.C. Fan, (2007). Two-dimensional optical accelerometer based on commercial DVD pick-up head. Measurement Science and Technology, 18(1), 265274.
-
H.C. Kim, D.K. Jeong and W. Kim, (2006). A Partially Switched-Opamp Technique for High-Speed Low-Power Pipelined Analog-to-Digital Converters. IEEE Transactions on Circuits and Systems I: Regular Papers, 53(4), 795-801.
-
S. K. Hung, C.H. Cheng, M.L. Chiang and J.W. Chieh, (2014). Transforming an Optical Pick-up-Head into an Accelerometer With Ultrahigh Sensitivity.
IEEE Transactions on Industry Applications. Technology, 63(3), 687-693.
-
S. K. Kuo, C.C. Hung, C.C. Lin and W.H. Yang, (2007). Development of a nano-displacement measurement system. Measurement, 40(3), 255-263.
-
H.F. Shih and B.W. Li, (2007). Diffraction Grating With Dual Modes for Two-Wavelength Rewritable Optical Pickup Heads. IEEE Transactions on Magnetics, 43(2), 900-902.