
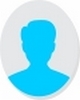
- Open Access
- Authors : Antoni Simanjutak , Latuhorte Wattimury
- Paper ID : IJERTV10IS100092
- Volume & Issue : Volume 10, Issue 10 (October 2021)
- Published (First Online): 22-10-2021
- ISSN (Online) : 2278-0181
- Publisher Name : IJERT
- License:
This work is licensed under a Creative Commons Attribution 4.0 International License
Savonius Turbine Analysis for Ocean Current Power Plant Using a Computational Fluid Dynamics Approach
Antoni Simanjutak
Department of Mechanical Engineering, Universitas Pattimura
Maluku, Indonesia
Latuhorte Wattimury
Department of Marine Engineering, Universitas Pattimura
Maluku, Indonesia
AbstractTechnology for utilizing renewable energy sources has been created in order to minimize the consumption of fossil fuels. It is advantageous to use this renewable energy since it is both ecologically beneficial and readily available at all times. As instance, the utilization of ocean currents as a source of power through the use of a turbine is becoming increasingly popular. In order to enhance turbine performance, several research have been performed, including the usage of Savonius turbines. The goal of this research is to determine the Darrieus-Savonius turbine power using computational fluid dynamics (CFD). CFD simulation it was found that all congurations showed an improvement on the coecient of power, and high rpm (100 rpm) had the highest coecient of power where the maximum Cp was 0.24 at TSR of 0.25.
-
INTRODUCTION
The use of renewable energy for power generation is becoming more popular as a way to minimize the usage of fossil energy. Because the usage of fossil fuels such as oil and coal may harm the environment and create the greenhouse effect, which causes global warming. Furthermore, fossil energy is anticipated to deplete. Renewable energy sources such as wind, sunshine, ocean currents, ocean waves, and geothermal energy are constantly accessible and never run out.
The Indonesian government is also becoming more involved in the development of renewable energy. For example, the building of Indonesia's first wind power plant (PLTB) at Sidenreng Rappang Regency, South Sulawesi, with 30 windmills, each of which drives a 2.5 megawatt turbine, or 75 MW for 30 turbines. The building began in April 2016 with a USD 150 million investment. The largest solar power plant (PLTS) in Indonesia is being built in Kupang, with a total expenditure of US$ 11.2 million. Even during the rainy season, this power plant can generate 5 MWp of electrical power and provide 27 percent of its regular capacity. This project was finished in June of 2016[1].
Another renewable energy that can also be used as a source of electrical energy is ocean currents. Ocean currents are energy that is always available and will never run out. The potential for renewable energy from ocean currents and sea waves has the potential of 61 GW while the installed 0.01 MW [2]. This data shows that the use of renewable energy from ocean currents and waves is very low compared to other
renewable energies. To convert the ocean currents into electrical energy, you must use a turbine, where the turbine converts the kinetic energy of the ocean currents into electrical energy with the help of a generator. Turbine modifications are mostly done to get a turbine that has good performance. One of them is to combine two models of vertical turbine Darrieus and Savonius [3].
The Savonius wind turbine is a simple vertical axis wind machine invented by Sigurd J. Savonius in 1922. In its original design, it was made with two half-cylindrical blades arranged in an S shape. The convex side of one half-cylinder and the concave side of the other face the wind at the same time as shown in Figure 26. As the drag coefficient of the concave surface is more than that of the convex side, in a given wind stream, the drag force experienced by the concave half would be higher than that of the other half. It is this difference in drag force that spins the rotor to develop mechanical power [4].
Figure 1 Operational principle of a Savonius
A small turbine ripple factor value will reduce power fluctuations and vibrations in the turbine. To find this out, a CFD (Computational Fluid Dynamics) analysis was carried out with the help of software. The purpose of this study is to determine the TRF on the blade, where the smallest value of TRF is an indicator of the optimum turbine design.
-
LITERATUR STUDY
A vertical axis turbine is a type of turbine in which the axis of rotation is oriented in the vertical plane. Turbines with vertical axis, such as the Darrieus and Savonius, are employed. When compared to other vertical axis turbines, the Darrieus turbine has a high power coefficient (or efficiency). The Sanovius turbine, on the other hand, is designed for low- speed currents. The efficiency of a turbine may be measured by measuring how much kinetic energy from the water stream is transformed into electrical energy by the turbine. The power coefficient (Cp) and the torque coefficient (Cm) of the turbine are two metrics that may be used to evaluate the overall performance of the turbine.
(1)
Where: Cm is torque Coefficient, T is Torque (Nm), As swepr area (m2), D is Diamer of turbine (m) and v is velocity (m/s)
The value of torque (T) and power (P) or the numerator in the above equation is the quantity obtained by the turbine when it is operated while the denominator is the total torque or power that can be converted by the turbine. Calculations of Cm and Cp are carried out in the range tip speed ratio () of the turbine. The tip speed ratio is the ratio of the angular speed at the end of the rotor to the current speed so that can be defined as follows:
(2)
Where: is tip speed ratio, is angular velocity (rad/s), D is diameter of turbine (m) and v is velocity (m/s)
The instantaneous power produced by the turbine is equal to the product of the instantaneous torque and the angular velocity. This value is not constant because the torque produced is also not constant. Therefore, one of the quantities used to describe turbine performance is torque ripple. Torque ripple is the value of torque which always changes per unit time. The value of the torque ripple (torque ripple factor) can be defined as the difference between the peak torque Tmax and the minimum torque Tmin with the average torque Tavg, which can be seen in the following formula [4]:
continuity and momentum equations for incompressible flows may be given as in the following two equations [5]. The equations of mass and momentum can be written as follows in Equations (4) and (5):
(4)
(5)
Furthermore, introduced Reynolds Averaged Navier-Stokes (RANS) in which configurated from modification of unsteady Navier-Stokes by involving averaged and fluctuating quantities. The turbulence model based on the RANS equation is known by Anderson [6], as a statistical turbulence model caused by procedure of statistical average used to obtain the equations. Reynolds' average equations are given in Equations (6) and (7):
(6)
(7)
where is the stress tensor molecular consisting of normal and shear stress components
The SST model combines the advantages of the k- model to achieve an optimal model formulation for a wide range of applications. For this, a blending function F1 is introduced which is equal to one near the solid surface and equal to zero for the flow domain away from the wall. It activates the k- wall region and the k- model for the rest of flow. By this approach, the attractive near-wall performance of the k- model can be used without the potential errors resulting from the free stream sensitivity of that model. The modelled equations for the turbulent kinetic energy k and the turbulence frequency are as follows:
(8)
(3)
The value of TRF is one if the torque produced is stable. The significant ripple torque dfference causes the turbine to vibrate during operation. The turbine components will become fatigued as a result of this. The power coefficient can be increased by reducing torque ripple.
-
METHOD
-
GOVERNING EQUATION
The Reynolds-averaged Navier-Stokes (RANS) method is a three-dimensional equation developed and used in the CFD model. One of the equations developed by ANSYS- CFX software is unsteady viscous incompressible flow to solve flow problems in the walls of ships. The averaged
(9)
Its performance has been reported by Menter and Esch [7]. In a recent NASA Technical Memorandum by Bardina et.al. [8] the SST model was rated the most accurate model in its class.
-
TURBINE DESIGN
The Savonius turbine is conducted to computational fluid dynamics (CFD) simulation. The three-dimensional (3D) model used in this research is a full-scale replica. According to the following table 1, the turbine is of the following dimensions:
Parameter
Unit
value
Rotor Diameter (D)
m
1.5
Rotor Heigh (H)
m
2
Number of blade
2
Parameter
Unit
value
Rotor Diameter (D)
m
1.5
Rotor Heigh (H)
m
2
Number of blade
2
TABLE 1 Size of the Savonius turbine
Figure 2 Savonius Turbine
-
BOUNDARY CONDITION AND MESHING
The domain dimensions and boundary conditions are specified in Figure 3. The boundary conditions are specified as follows: the turbine salvonius is a no-slip condition is imposed on the wall surface; opening condition is applied to
the top, side and bottom walls; the flow velocity at inlet is defined as the current speed of waters (4-12m/s); at the outlet, the velocity set as same with inlet section.
Figure 3 Numerical Domain of Turbines
A good mesh is essential for accurate and dependable results. CFD Simulation, formally known as CFX, has a long tradition of innovative meshing technologies including Mesh Enhancement, Automatic Mesh Sizing, and Automatic Refinement. The mesh generation in this study is accomplished using Design Modeler. The calculation domain is discretized using unstructured meshes. Considering the complex geometrical characteristics of the turbine a mesh with triangular elements is generated on the turbine surface and the boundary layer is refined with prism elements created through extending the surface mesh node. The region around the turbine is filled with tetrahedral elements with interface
domain, while in the far field, unstructured mesh with grid generation is generated for reducing the number of elements as shown Figure 4.
The mesh size plays an important role in the calculation procedure, a fine mesh can always bring credible results in ANSYS CFX but at the same time increases the computational cost and time consumption due to the large element number. Therefore, to determine the mesh size with acceptable numerical accuracy and element number, mesh convergence studies are carried out for the Salvonius Turbine. Grid model of turbine according to Chung, [9] the number of used elements about 1,583,256.
Figure 4 Meshing mode
-
-
RESULT AND DISCUSSION
The coefficient of power generated by the turbine can be seen in Table 2 and Figure 5 below.
TABLE 2 CFD CALCULATION OF POWER COEFFICIENT (CP)
TSR
Revolution per menit (rpm)
60
70
80
90
100
1.25
0.032
0.04
0.052
0.062
0.07
1.5
0.04
0.048
0.065
0.095
0.1
1.75
0.074
0.082
0.095
0.102
0.125
2
0.102
0.12
0.136
0.153
0.17
2.25
0.135
0.145
0.156
0.186
0.2
2.5
0.189
0.21
0.215
0.22
0.23
According to the findings of these research, turbines with high rotational speeds generate greater power coefficients than other types of turbines. These are the results when the tip speed ratio is set to 2.5. When comparing the low rpm of the turbine to the middle and high rpm of the turbine, the whole trend of the turbine curve exhibits the same pattern. If the TSR is raised, the power coefficient of a turbine with a low rotational speed will be greater than the power coefficient of a turbine with a high rotational speed. It may be inferred that the
usage of rpm on the turbine will be more effective or will result in a higher power coefficient if the tip speed ratio is more than 2.5 and is dependent on the velocity of the water flow. This implies that the usage of high rpm will be efficient at high turbine angular velocities because of the increased efficiency. As previously stated, power ripple is a characteristic that affects whether or not a turbine performs well in terms of efficiency.
Figure 5 Coefficient of Power
In the study, free obstacle shield in front of the returning blade for the two-bladed Savonius turbine respectively. The simulation employed the realizable SST model with Finite Volume Method (FVM) for discretization. From the simulation, it was shown that with the obstacle plate, the static torque and the power of coecient for both cases were increased. Fig. 6 shows the optimal orientation of the vektor and contour velocity for the two-bladed Savonius turbine. From the optimization, the coecient of power of the two- bladed Savonius rotor with difference rpm was increased by about 27.3% and 27.5% respectively.
(a)
(b) high rpm
Figure 7 Visualization of contour velocity of fluids with (a) low rpm; (b)
high rpm
A total of five dierent rpm were investigated as shown in Fig. 7. From the CFD simulation it was found that all congurations showed an improvement on the coecient of power, and high rpm (100 rpm) had the highest coecient of power where the maximum Cp was 0.24 at TSR of 0.25. The result was in agreement with the simulation conducted by Mohamed [10] above.
-
CONCLUSSION
All technologies have desired great energy efficiency for ages. Researchers and engineers are always pushed to find methods to utilize a smaller wind turbine to generate more electricity while saving money and simplifying design. The Salvonius turbine has weak self-starting ability, low beginning torque, and a low coefficient of power (CP). This article will offer academics with valuable information and current Salvonius turbine power technologies for future investigations. The review elaborates on and discusses flow estimation methods based on current research. The flow of water current have been shown to improve salvonius turbine performance in terms of self-start and CP value. However, an optimal design reduces current of waters obstruction while increasing positive torque.
(b)
Figure 6 Visualization of vector (a) and contour (b) velocity of fluids
-
low rpm
REFERENCES
-
F. Yusup and i, Sidrap Wind power plant, the first in Indonesias commercial, Warung Sains Teknologi, Jan. 12, 2018. https://warstek.com/srikalahasthi-fired-power-station-wnd-power- indonesia/ (accessed Oct. 05, 2021).
-
M. A. J. R. Quirapas, H. Lin, M. L. S. Abundo, S. Brahim, and D. Santos, Ocean renewable energy in Southeast Asia: A review, Renew. Sustain. Energy Rev., vol. 41, pp. 799817, Jan. 2015, doi: 10.1016/j.rser.2014.08.016.
-
N. R. Maldar, C. Y. Ng, and E. Oguz, A review of the optimization studies for Savonius turbine considering hydrokinetic applications, Energy Convers. Manag., vol. 226, p. 113495, Dec. 2020, doi: 10.1016/j.enconman.2020.113495.
-
A. Kumar and G. Saini, Flow field and performance study of Savonius water turbine, Mater. Today Proc., vol. 46, pp. 52195222, Jan. 2021, doi: 10.1016/j.matpr.2020.08.591.
-
J. H. Ferziger and M. Peric, Computational Methods for Fluid Dynamics. 2002.
-
J. D. Anderson, Computational Fluid Dynamics: The Basics with Applications. New York, USA. pp. 526-532: McGraw-Hill, 1995. [Online]. Available:
https://books.google.co.id/books?id=phG_QgAACAAJ
-
F. R. Menter and T. Esch, Elements of Industrial Heat Transfer Predictions, 16th Braz. Congr. Mech. Eng., 2001.
-
J. E. Bardina, P. G. Huang, and T. J. Coakley, Turbulence Modeling Validation, Testing, and Development, Nasa Tech. Memo., 1997, doi: 10.2514/6.1997-2121.
-
T. J. Chung, Computational Fluid Dynamics. Cambridge: Cambridge University Press, 2010.
-
M. H. Mohamed, G. Janiga, E. Pap, and D. Thévenin, Optimization of Savonius turbines using an obstacle shielding the returning blade, Renew. Energy, vol. 35, no. 11, pp. 26182626, 2010, doi: https://doi.org/10.1016/j.renene.2010.04.007.