
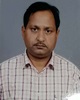
- Open Access
- Authors : Krishna Pal Singh Chauhan
- Paper ID : IJERTV11IS110121
- Volume & Issue : Volume 11, Issue 11 (November 2022)
- Published (First Online): 28-11-2022
- ISSN (Online) : 2278-0181
- Publisher Name : IJERT
- License:
This work is licensed under a Creative Commons Attribution 4.0 International License
Role of Pouring Process Variables in the Improvement of Casting Properties of Aluminum-Silicon Casting Alloys
Krishna Pal Singh Chauhan
Head of the Department Department of Mechanical Engineering,
Future Institute of Engineering and Technology, Bareilly (U.P.)
Abstract:- The gravity die casting is a widely used production method which is most suitable for mass production of component of high surface finish along with good dimensional accuracy. The alloying elements and process variables are main responsible factors which affect the quality of product. Some process variables like pouring temperature and pouring rate of molten materials into mold cavity, affect the melt quality and finally the quality of finished product. The influence of these variables on mechanical properties is investigated in the present work for casting of hyper-eutectic aluminum-silicon alloy. The effect of pouring temperature and pouring rate on tensile strength is investigated in this research paper and the effect of pouring temperature on fluidity of molten metal is also investigated. Influence of various parameters on fluidity is examined for hypoeutectic alloy (having Silicon 12%) and hyper eutectic alloy (having Silicon 24%). The optimum conditions of various process parameters are explored through experimental work.
1. INTRODUCTION-
In the gravity die casting method the molten alloy is poured into the mould cavity under the influence of gravitational force. The dies are made of metal in two identical half sections. When both sections are in closed position they form die cavity. The molten alloy is poured in this die cavity. The cast component is taken out from the die after completion of solidification of the component. Finally the extra material from the cast component, including the gate, runners, riser and flash are removed to get the appropriate shape of casting Excellent dimensional accuracy and flawless cast surfaces are produced by this method. By using this method thinner walls can be cast properly thus enabling the creation of complex shapes. Alloys made of aluminum are frequently utilized in the casting of lightweight components. When silicon is added to cast aluminum alloy, it increases fluidity and lowers the cracking tendency. Al-Si alloy is one of the most often used materials for casting automobile components [1]. Alloys made of aluminum and silicon are classified as either hypoeutectic or hypereutectic depending on the factor that , how much silicon is added as alloying element (by weight)in aluminium. [2] Other elements like nickel and copper are also added to aluminum-silicon alloys to enhance their mechanical properties. [3] Copper addition reduces shrinkage and provides a foundation for age hardening, which after some time further increases the hardness of the cast component. By the addition of nickel the strength at high temperature of the alloy can be increased [3]. The process variables of the casting also affect the quality of cast components. Through a review of the literature, it was concluded that the thermal conductivity of alloy, pouring temperature of melt, and die temperature all influences the metal flow in die castings. [4][5] The specific gravity and thermal conductivity of the liquid melt affect the manner in which an alloy solidifies. The process variables like degasification, pouring temperature, and pouring rate affects the quality of the cast components. J.H. Lee et al. [5] find the relationship between melt turbulence in the holding furnace (before pouring) and the duration of the degasification process. They arrived at the conclusion that the design of degassing rotor had a significant impact on the creation of turbulence in the holding furnace prior to pouring.
Reddy et al[6] concluded that silicon content in aluminum alloy reduces the freezing range and magnesium content widens it.. Ankit Oza et el. [7] proposed the use of ultrasonic degassing methods for removal of the hydrogen gases. M. Hernandez et al. [8] concluded that analysis of casting is very costly if every process is executed physically, therefore various simulation software are used to analyze the casting parameters and the optimum conditions were obtained with help of thse software. Manjunath Patel et al [9]find that squeeze pressure, die temperature and pouring temperature are the input parameters and minimized wear rate is the output parameter for squeeze casting From literature survey it is found that to manufacture components of good quality the casting process variables like rate of pouring ,temperature of melt, relative humidity etc are some variables, which needs to be controlled properly for making defect free casting.
2.1. Testing of Tensile Strength-
2 EXPERIMENTAL SETUP AND TEST PROCEDURE-
To investigate the influence of casting variable on mechanical properties like tensile strength and casting properties like fluidity the test samples are solidified at different pouring temperature and tensile test is conducted on universal testing machine. In this test straining a test piece is done by applying tensile load on the specimen as shown in figure 1.
Figure 1
To perform this test the molten aluminum alloy is solidified in the tensile test bar dies, specially made for this purpose. The bars of stranded dimensions are casted by pouring the molten alloy into the die cavity. After solidification these bars are removed from the dies. The bars of circular cross section are gripped in Tensile Testing machine, in such a manner that the tensile load is applied axially.
2.2 Testing of Fluidity-
For the casting point of view, the fluidity is an important property of molten alloy. The objective of this test is to find the variation of the fluidity with the variation of pouring temperature. A special die is made for the purpose of testing the fluidity. It consists of a hollow spiral coil attached with sprue and having pouring cup as shown in figure 2
Figure 2
The molten alloy is poured at different pouring temperatures in the pouring cup. The length covered by molten alloy in the spiral coil depends upon the pouring temperature. The length of spiral coil filled by the material is the indication of relative value of fluidity of molten alloy.
3. Experimental work
For tensile testing various rods casted at different pouring temperatures are tested on universal testing machine and the results of tensile test are recorded in table 1.
Table No.1Tensile Test Results
S.No |
Pouring Temperature (° C) |
Average Tensile Strength (N/mm2) |
||
Pouring Rate (50 gm/sec) |
PouringRate (100 gm/sec) |
PouringRate (150 gm/sec) |
||
1 |
840° C |
148 |
149 |
150 |
2 |
850° C |
150 |
151 |
153.5 |
3 |
860° C |
152 |
153.5 |
157 |
4 |
870° C |
154 |
156 |
160.5 |
5 |
880° C |
156 |
158 |
164 |
To find the variation of fluidity with pouring temperature and silicon content, two samples are taken from hypoeutectic and hypereutectic alloys. the molten alloys are poured in the dies at the difference of 20°C starting from 780°C to 880°C.and the readings are taking and as shown in table 2.
Table No.2 Fluidity Test Resuls
S.NO |
Pouring Temperature (° C) |
Fluidity (mm) |
|
For Hypo Eutectic Alloy (Si 12%) |
For Hyper Eutectic Alloy (Si-24%) |
||
1 |
780° C |
660 |
711 |
2 |
800° C |
787 |
838 |
3 |
820° C |
890 |
965 |
4 |
840° C |
1016 |
1092 |
5 |
860° C |
1080 |
1190 |
6 |
880° C |
1150 |
1295 |
4-RESULTS AND DISCUSSIONS-
The various test values obtained from these tests are plotted in the graph by taking pouring temperature on x axis and tensile strength on y axis(figure no.3) and pouring temperature on x axis and fluidity in mm on y axis(figure no.4)
166
164
Tensile Strength (N/mm2)
162
160
158
156
154
152
150
148
146
830 840 850 860 870 880 890
Pouring Temperature (° C)
Tensile Strength (N/mm2) Pouring Rate-50 gm/sec
Tensile Strength (N/mm2) Pouring Rate-100 gm/sec
Tensile Strength (N/mm2) Pouring Rate-150 gm/sec
Figure 3:
The length of section filled by molten alloy after solidification in cast iron mould is measured and is recorded. To get the results of fluidity at different silicon content two alloys are considered. For this test alloy 124 number (having silicon 12%) and alloy 244 number (having silicon 23%) is considered for the test. The results of fluidity tests are recorded in table no. 2 The variation of tensile strength and fluidity of aluminium alloy increases almost in a linear manner with the increase in pouring temperature in case of hypo eutectic alloy (Si 12%) the fluidity is less than the fluidity of hyper eutectic alloy(Si-24%)it shows that as silicon content increases , the fluidity also increases .
1400
1200
Fluidity (mm)
1000
800
600
400
200
0
750 800 850 900
Pouring Temperature (° C)
Fluidity (mm) For Hypo Eutectic Alloy
Fluidity (mm) For Hyper Eutectic Alloy
Figure 4:
5. CONCLUSIONS-
It is concluded that pouring temperature have a great impact on tensile strength of aluminum alloy. The variation of tensile strength and fluidity of aluminum alloy increases almost in a linear manner, with the increase in pouring temperature. Increasing silicon content in aluminum alloy increases the fluidity of aluminum alloy. The fluidity of hyper eutectic alloy (having Silicon 24%) is more as compared to hypoeutectic alloy (having Silicon 12%). Thus it is concluded that the fluidity of the molten aluminum alloy is influenced by two variables, Silicon content in the molten aluminum alloy and Pouring temperature of melt.
ACKNOWLEDGEMENT
The author of this paper acknowledges Production staff of Foundry Division, and staff of Quality Control Division of Escorts Mahle Ltd Punjab (India) for providing help and support through this research work.
REFERENCES
[1] Dieter, E. George, Mechanical Metallurgy McGraw Hill Book Co. New Delhi [2] Clark, S. Donald, Physical metallurgy Eastweat Process P. Ltd. New Delhi [3] J.R.Davis Aluminum and Aluminum Alloys ASM international p351-416, 2001, www.asminternational.org [4] Hein, R.W., loper, C.R. and Rosenthal P.C., Principles of Metal Casting. McGraw Hill New York [5] JH. Lee (2002). Effect of gap distance on cooling behavior and the microstructure.Materials science and engineering. Volume-2.2002 [6] Chennakesava Reddy, and Ch. Rajanna , Design of Gravity Die Casting Process Parameters of al-si-mg alloys journal of machining and forming technologies Volume 1 Issue ISSN: 1947-4369 2009 [7] Ankit D Oza. Tushar M Patel, Analysis and validation of gravity dies casting process" International journal of applications and innovations in engineering and management.2017 [8] M.Hernandez, Camacho Martinezb, Impeller design assisted by physical modelling und pilot plant trails". Journal of materials processing technology 2018. [9] Manjunath Patel G Ca, Arun Kumar Shettigarb, Mahesh B. Parappagoudare. A systematic approach to model and optimize wear behavior of castings produced by squeeze casting process, 199-212, (2018) [10] EML, Piston Foundry Operation Manual, Escorts Mahla Ltd India