
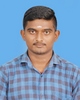
- Open Access
- Authors : Karthikeyan. S , Praveenkumar. P , Mugesh M. A , Thirumurugaveerakumar S
- Paper ID : IJERTV11IS050326
- Volume & Issue : Volume 11, Issue 05 (May 2022)
- Published (First Online): 04-06-2022
- ISSN (Online) : 2278-0181
- Publisher Name : IJERT
- License:
This work is licensed under a Creative Commons Attribution 4.0 International License
Role of Flywheel Batteries in Energy Storage System – A Review
Thirumurugaveerakumar S1, Karthikeyan. S2, Praveenkumar. P3, Mugesh M.A4
1 Associate professor, Department of Mechanical Engineering, Kumaraguru College of Technology, Tamil Nadu,
India.
2 Student, Department of Mechanical Engineering, Kumaraguru College of Technology, Tamil Nadu, India. 3 Student, Department of Mechanical Engineering, Kumaraguru College of Technology, Tamil Nadu, India. 4 Student, Department of Mechanical Engineering, Kumaraguru College of Technology, Tamil Nadu, India.
Abstract:- In flywheel-based energy storage systems, a flywheel stores mechanical energy that interchanges in form of electrical energy by means of an electrical machine with a bidirectional power converter. Flywheel based energy storage systems are suitable whenever numerous charge and discharge cycles (hundreds of thousands) are needed with medium to high power (kW to MW) during short periods (seconds). The materials for the flywheel, the type of electrical machine, the type of bearings and the confinement atmosphere determine the energy efficiency (>;85%) of the flywheel-based energy storage systems. A flywheel stores mechanical energy that is converted to electrical energy by an electrical machine with a reciprocal power converter in flywheel-based energy storage systems. Flywheel-based energy storage systems are ideal for applications that need a large number of charge and discharge cycles (hundreds of thousands) with medium to high power (kW to MW) over a short period of time (seconds).
Key words: Flywheel, energy storage, renewable energy, spacecrafts, microgrids
-
INTRODUCTION:
A flywheel is a mechanical battery that consists of a spinning mass around an axis. It works by spinning a rotor to extremely high speeds and storing the energy in the device as rotational energy. As a result of the theory of energy conservation, the flywheel's rotational speed is decreased when energy is removed from the device. We learned how to construct these systems based on our requirements and what criteria must be considered during the design process. Also, the tests that were needed to ensure the product's safety and efficiency. It focuses on FESS's use of microgrids and renewable energy storage systems such as solar and wind energy. It provides a good picture of how FESS can be used. It explains how FESS can be used in micro grids to stabilize an unbalanced power supply and how it is cost effective as compared to other ESS. How can it be used in combination with lead acid batteries to extend the life of the battery? Finally, these systems can be combined with hydraulic and pneumatic systems for use in other applications.
-
LITERATURE REVIEW:
-
DESIGN AND CONTRUCTION
[1] Xiaojun Li and Alan Palazzolo et al [2021] explains about the features of flywheel batteries as if they have high energy density, renewable energy and mass energy storage capacity. In addition, this journal explains about steel flywheel batteries and composite flywheel batteries. Steelflywheel batteries operate at low speed but it can be recyclable. comparatively, composite flywheel batteries have low reducing stresses in radial direction.it operates at high speed and easily store high energy compare with steel flywheel batteries. This journal explains about their applications like transportation, etc.
[2] Amiryar and Pullen et al [2017] presents that Electrical energy storage systems are primarily used to boost efficiency by balancing the input and output electric power. This paper describes the structure and construction features such as bearing systems, power electronic converters, and so on in detail. These flywheel batteries, unlike chemical batteries, have a long life, a high-power density to weight ratio, and a small footprint. As an energy storage medium, these systems are used with UPS. These are typically used in situations where a large amount of energy is required in a limited amount of time. They've been seen in transportation systems, ships, and particle accelerators. [3] Pullen [2019]. FESS is one of the most ancient types of energy storage systems. These systems are mostly recommended because they are well-suited to high energy density applications and have long life cycles. It has been used in various applications in conjunction with lithium-ion batteries to improve performance and cost effectiveness. It is important to note that it is a renewable energy storage system. It could be a better replacement as we transition to renewable energy in all aspects. These energy systems are low-maintenance and have a 25-year life expectancy. [4] Wang and Xue et al [2021] focus on the source storage load power characteristics, which were investigated using a simulation model created in Mat lab. FESS was chosen because it responds quickly to control strategies and provides the load with the required strength. Following these tests, it was determined that it can meet the load power and energy requirements in the early stages of fast charging, as well as compensate for DC bus voltage drop in DC fast charging stations [5] Egor A. Kuschenko and Ekaterina P. Kurbatova et al [2021] had explained this work is devoted to the development of a contactless magnetic bearing based on high-temperature superconductors for a flywheel energy storage system (FESS). Electromagnetic calculations ofvarious designs of high temperature superconducting (HTS) bearings are presented, their force characteristics are analysed. The construction of the magnetic bearing based on HTS tapes has been developed for use in FESS.
[6] DÃaz-González and Sumper et al [2013] A rotating disc mechanically coupled to a PMSM, a series of back-to-back power converters, and a two-winding transformer make up the system, which allows power transmission between the servomotor and the external grid. The system's energy capacity was calculated to be 30 KW by reducing the machine's speed from its rated value to 65 rad/s at a constant stator current rated discharge of 9 A. This method has been calculated to have a 73 percent energy efficiency. Furthermore, the system's power capacity has been limited to 3 kW in order to keep the system running within the power converters' safe operating limits. [7] Jiang and Zhang et al [2017] exposed the significance of flywheel shape design and its contribution to improving flywheel energy storage efficiency was highlighted. Form optimization for the interference fit flywheel will boost not only the stored energy density, but also the stress concentration and reduce the structure stress alternation. As a result, fatigue protection has greatly improved. -
ROLE IN MICROGRIDS
[8] onský, J. and Tesa, V., [2019], authors of this paper established a unit with a spinning flywheel for storing energy and thus reducing the supply and demand for electricity. The aim of the development was to reduce the amount of energy extracted from the flywheel while maintaining all five degrees of freedom. They looked at issues like air resistance, stabilization, and bearings, and concluded that the theory could provide an advantage over other storage methods by achieving high specific energy up to 500 kJ/kg. [9] Thomaschewski and Turnbull et al [2017]. The flywheel is connected to a battery source and a power converter via a permanent magnet synchronous motor (PMSM). The PMSM was able to rotate the flywheel to store and extract energy because of the coupling. The power converter converts DC to AC and vice versa to power the PMSM. The flywheel i made of steel and has a rotational speed of 10000 rpm and a storage capacity of 240 KJ. The charging and discharging times are determined by the system's load. [10] Samineni S and Johnson BK et al [2006]. In this case the energy storage system consists is a flywheel coupled to an induction machine. The power electronic interface consists of two voltage sourced converters (VSC) connected through a common DC link. The flywheel stores energy in the form of kinetic energy and the induction machine is used for energy conversion. [11] Abdul Ghani Olabi andTabbi Wilberforce et al [2021], This review presents a detailed summary of the latest technologies used in flywheel energy storage systems(FESS). This paper covers the types of technologies and systems employed within FESS, the range of materials used in the production of FESS, and the reasons for the use of these materials. Furthermore, this paper provides an overview of the types of uses of FESS, covering vehicles and the transport industry, grid levelling and power storage for domestic and industrial electricity providers, their use in motorsport, and applications for space, satellites, and spacecraft. Different types of machines for flywheel energy storage systems are also discussed. This serves to analyse which implementations reduce the cost of permanent magnet synchronous machines.
[12] Arani and Karami et al [2017]. A close examination of previous energy storage systems reveals that FESS was the first widely used method of storing electrical energy. Later, as our experience and research in chemical engineering grew, we discovered a new path for storing energy, which is nothing but chemical batteries, which began to replace other energy storage systems due to their high energy density for long periods of time. Even, the FESS systems have their own comment in a variety of fields where no other device can replace them, such as space projects and military applications, due to their ability to produce high energy in a limited period of time. The only issue with these devices is the rate at which they discharge. While it has a high initial cost, it has the lowest maintenance cost of any other energy storage system. Their work in micro grids was critical in resolving the demand-supply power imbalance that occurs when electrical energy is derived from renewable energy sources that are dependent on nature. Clean energy was desperately needed in our country, and FESS has a better chance of replacing chemical batteries.FIGURE 1: FESS APPLICATION IN UPS STRUCTURE
[13] Tariq Hendricks and Macro Adonis [2020] had presented a paper focusing on selecting the best and most feasible energy storage systems for African micro grids that produce electricity using renewable energy sources such as wind and solar power. The three systems considered were FESS, Supercapacitor storage systems, and they were compared in terms of capital and maintenance costs, annual energy production, annual input and output capacity, carbon emissions, and other factors. As a result, supercapacitor storage systems outperform FESS in terms of overall charge and discharge current, life expectancy, and other parameters, but their cost is too high to be easily accessible, so FESS was chosen because it emits no carbon into the atmosphere and has the lowest maintenance cost among the ESS. [14] Barelli L and Bidini G et al [2020] ran several tests with different AC and DC bus configurations to see which one provided the best energy conversion. These tests were carried out in a HESS system that included a photovoltaic cell and a flywheel battery. Under normal operating conditions, performance tests revealed that current stabilisation in the AC configuration is 30ms faster than in the DC configuration. The AC configuration never reaches0.2 percent in voltage distortion study.
-
ROLE IN RENEWABLE ENERGY STORAGE
[15] Hutchinson, A. and Gladwin, D.T., [2020] said that because of the unpredictable existence of power production, it often reaches or falls short of the site's export limits. Flywheels are suitable for acting as an energy store because of their resistance to high cycle speeds. This paper describes how real-world data are used to model a wind farm with a Flywheel Energy Storage System (FESS) and the efficacy of various storage capacities. [16] De Siqueira, et al [2021] analysed that, wind energy plays an important role in the global energy mix. However, BESS has a broad capacity to compensate for deviations, which raises the capital cost and reduces its suitability. Some studies focused on implementing control systems to optimize BESS and reduce its necessary size to solve this problem. This paper provides a literature review of control strategies for smoothing wind power output using battery energy storage systems, which can be used to direct future practical applications. [17] Killer, M, et al [2020] explained this paper is to provide an outline of how large-scale Li-Ion BESS are currently being implemented in the EMEA area, as well as the main use-cases for large-scale. Li-ion batteries that are being implemented and the key factors that are enabling the deployment of BESS projects in current markets. They concluded that Li-ion BESS are a viable technology for enabling a gradual shift toward decentralized renewable energy generation. Li-ion battery projects are usually not economically feasible. The effect of Li-Ion BESS on the potential evolution of electricity networks to achieve a large share of renewable energy generation is highly significant. [18] Qian, X, et al [2010] explained that, Because of the speed limit of chemical reactions and the slow charge and rapid discharge of batteries, wind and solar power generation is unstable. As a result, the author Xianyi Qian, et al. used statistical and data analysis to examine the merits and drawbacks of flywheel energy storage based on economic and social benefits. As a result, they concluded that storing huge amounts of wind and solar power as mechanical energy would be beneficial.FIGURE 2: FLYWHEEL BATTERY
[19] Mahmoud, M., et al [2020] discussed that in recent years, the mechanical energy storage system has proven to be the most effective energy storage system. The author discussed the parameters that affect the utilisation and performance of flywheel batteries in short-term applications using recent developments in MESS coupled with both wind and solar, and also discussed the parameters that affect the utilisation and performance of flywheel batteries in short- term applications using flywheel batteries. As a result, the writers came to the conclusion that pumped or compressed air was preferable for long-term use. [20] Delille, G., et al [2012] focuses on how to minimize the effect of wind and solar power systems in the event of a power failure. Many other aspects of renewable energy incorporation in independent power systems must also be studied, but it is unclear how this would help. Additional research on these subjects, as well as the evolution toward properly identifying risk levels and drawn definite conclusions, are required.FIGURE 3: DYNAMIC FREQUENCY CONTROL SUPPORT BY ENERGY STORAGE
[21] Berrada, A. and Loudiyi, K., [2016] Renewable energy sources, as we all know, minimize greenhouse gas emissions while also reducing the energy sector's reliance on fossil fuels. The unpredictable nature of these sources raises questions about the electric grid's stability. Energy storage isessential for integrating these sources into the electric grid. The methods for determining the best operation and sizing of a machine are described in detail in this paper. Case studies have been conducted to check the validity of these approaches. The authors suggest an economic study to figure out how much each KWh of stored energy.
[22] Arianna Baldinelli and Linda Barelli et al [2019] had developed an idea by integrating renewable sodium oxide cells and a flywheel, he came up with the concept of hybrid energy storage systems (HES). In comparison to other ESS, the self-consumption efficiency has improved to 58.04 as a result of this. In a year, energy wastage was reduced by up to 88 kWh. This paper also includes information about how these systems operate in various weather environments and how well they perform. From May to April, the flywheel's angular speed and power varied, providing a good indication of its contribution throughout the year.FIGURE 4: MICRO GRID GENERATION AND STORAGE DC BUS
-
ROLE IN HYBRID VEHICLES
[23] Leila Abdullina et al [2021] explains about eco- friendly mechanized rotary parking lots with a flywheel energy storage device. The purpose of this study was to propose a solution to improve the operation of a multi-storey rotary car park, as well as to increase its efficiency and environmental friendliness. First, the choice of execution depends on the cost of the parking space. Recently, hybrid power plants with recovery of braking energy (which reduce energy loss by up to 50% depending on the frequency of the braking process) have become widespread in the world. In practice, engineers usually use various types of electric, pneumatic and flywheel energy batteries. The methodology for calculating the main parameters of the energy storage brake system and determining the parameters of the flywheel accumulator. The use of a flywheel battery allows reducing energy losses and increasing the efficiency of rotary car parks in unsteady operating modes. [24] Dhand A and Pullen K et al [2013] explains about the role of flywheel in hybrid vehicles. The flywheel is coupled to the driveline with a continuous variable transmission (CVT). T1o\he flywheel energy storage system (FESS) is an ideal secondary storage technology for the conventional ICEV since it is able to store the energy in the form that it was recovered i.e., mechanical kinetic energy. By utilizing the FESS, the energy lost in conversion from one form to the other is saved. The FESS can be classified as low speed and high-speed systems or subcritical and supercritical systems depending on their maximum speed. The FESS would becharged at the recharging stations placed along the route using 360 V, 50 Hz AC supply. The bus could run for an average distance of about 1.2 km on one single charge.
[25] Hossam A and Ibrahim Md et al [2020] Adham explains about fast charging with flywheel batteries. The flywheel energy storage has advantages to fast-charging applications. Besides, the target fast-charging system will support transportation electrification infrastructures, reduced operational costs, and CO2 emissions. The design of the system can use flywheel technology to reduce the adverse effects of the high demand in the power grid. Also, the proposed system can reduce the charging demand around 66%. This show that the flywheel can help to control high demand caused by ultra-fast chargers. [26] A. H. Atienza et al [2020], In the Philippines, the motorized tricycle is one of the most common means of public transportation order to store the kinetic energy recovered by the braking system, a mechanical component called flywheel is used. The braking process with the use of KERS will not be able to completely stop the vehicle but rather only slow down the vehicle to a certain amount of reduced speed. Whenever the driver switches on the flywheel KERS, the actuator pulls up the steel lever that engages the flywheel. While the flywheel is engaged, it serves as an engine brake that decelerates the vehicle and harnesses the kinetic energy from the rear wheels and transfers to the flywheel in the form of stored kinetic energy. [27] Nguyen and Hoang et al [2020]. Electricity is one of the most important requirements for industry to function. The world has begun to use renewable energy sources such as wind and solar energy because most non-renewable methods of production pollute the environment. Since the majority of energy is dependent on weather conditions, which induces power output variability, it is not ideal for consumption. As a result, FESS has evolved into the ideal solution for controlling and stabilising power fluctuations in microgrids. In hybrid cars, energy is stored in the flywheel during regenerative braking and returned when acceleration is needed. These are recommended as a replacement for chemical batteries and super capacitors in electric vehicles. [28] Akagi H and Sato H et al [2002] explains that paper proposes a new control strategy for a doubly-fed induction machine intended as a flywheel energy storage system, which is characterized by the combination of vector control and decoupling control. [29] Alan I and Lipo T.A et al [2003]. Flywheel energy storage (FES) system fed from a 20 kHz high frequency (HF) ac link and pulse density modulated (PDM) Converter. The feasibility of FES system is investigated both in software and hardware and is demonstrated successfully in both cases. The investigated system offers a good potential as a temporary energy storage system for various applications from automobile industry to aerospace applications. [30] Richardson, M.B [2002]. The flywheel system can resolve many of the problems encountered in traction supplies due to the 'peaky' nature of the loads caused by trains accelerating and braking. In addition, the UPT system can provide energy savings by improving the system's receptivity to energy from trains with regenerative braking. This paper describes how the system was applied to London Underground's Piccadilly line for a trial application and presents some of the data from these tests. This successful trial has now led to the first commercial application with the New York City Transit Authority. Finally, the paper reviews some of the possible developments which may lead to the application of this technology to higher voltage systems. [31] Hong LI and Jiangwei CHU et al [2021] explains about traditional vehicles with internal combustion engine (ICE) can only add secondary energy storage devices to recovery of part of braking energy. The Rag one diagram shows that flywheel energy storage (FES) has many merits such as higher power density, higher efficiency, fast response, environmental-friendly performance and long cycling using life, which becomes an ideal secondary energy storage technology for traditional ICE vehicles. Despite some progress, there is no systematically review on the recent progress of flywheel energy storage system in the automotive industry. [32] Barbashov NN and Barkov AA [2021] explained for the development of the agricultural industry, the current task is to design mobile robots that can independently perform a wide range of tasks. In this area, it is necessary to achieve both a reduction in the mass of the robot to reduce its impact on the top layer of soil, and an increase in its operating time without recharging from batteries. A promising method for improving the efficiency of agricultural machinery is the use of braking energy recovery, its accumulation and use during further acceleration. [33] Ayodele and Ogunjuyigbe et al [2020] presented the complementary effect of battery and flywheel hybridization on battery ageing for a PV-powered application has been investigated. The battery's age was predicted using a Schiffer weighted Ah-throughput model. When used in a PV-powered mixed fishery and poultry farm, a hybrid of battery and flywheel had a lower capital and lifecycle cost than a battery alone. When used in a hybridised device with a flywheel, the life of a lead acid battery was extended by two years. Higher discharging current may have a negative impact on battery ageing, according to the sensitivity study, while differences in corrosion and deterioration limits have no effect on battery ageing.FIGURE 5: PV BATTERY STANDALONE SYSTEMS
[34] Barbashov and Leonov et al [2018] established a dynamic model for a life-saving appliance, as well as the computation and study of its variables. In the event of a fire on the drilling platforms, thi life-saving device may be used. The energy of descent is converted to the rotational energy of the flywheel by the flywheel energy storage. After the launch, the accumulated energy can be used to rotate the survival capsule's propeller to increase the distance between the fire and the capsule. [35] Cronk and Van de Ven et al [2018] examined the current state of mechanical energy storage devices for hydraulic systems was investigated. Flywheels aren't exactly new, but advances in composite materials, continuously variable transmissions, and magnetic bearings have made them viable options for a variety of energy storage applications. Van de Ven's Hydraulic Flywheel Accumulator is another way of integrating kinetic and pneumatic potential energy storage in one device (2009). The system spins a piston-style accumulator around its axis, storing energy in the pressurised gas as well as kinetically in the accumulator's spinning fluid and structural components. -
ROLE IN SPACE VEHICLES
[36] Aydin, K. and Aydemir, M.T., [2016] described that in recent years flywheel energy storage system is mostly used for space application. In that manner the FESS has been designed for the control system in satellite attitude. To simulate the low orbit operation the machine is run as motor for 60 min and the following 30 mins the stored energy is discharged. To achieve high efficiency the magnetic suspension and integrated motor will be used for future work. [37] Kenny, B.H. et al [2005] reviewed that for space application the charge and discharge modes of flywheel energy storage system is operated by novel control algorithm. By this algorithm the technique which controls the speed limits are signal injection and electromotive force techniques in low and higher speed respectively in motor- controlled portion. And the command feedforward and disturbance decoupling algorithm controls chare and discharge. [38] Christopher, D.A. and Beach, R., [1998] said earlier that FESS plays vital role in aerospace, so that the advanced flywheel development in aerospace application is described in this paper. However, due to this emerging technology NASA is working closely with industries to develop the advanced flywheel system which will useful for both altitude control system and for potential terrestrial applications and also for launch vehicles. [39] Ginter, S., et al [1998] said that due the emergence of FESS in communication and data access in satellite, there is an increasing demand. So that increasing in growth of number of satellite system according to their performance requirements. The emergence of LEO vehicles is heavy, life limited and difficult to handle so FESS make an alternate to that with more benefits. [40] Richie, D.J, et al [2007] explained that the sizing the actuators for practical space mission with required energy storage for small satellites. The cast the design as a constrained programming problem with the help of performance index and solve the problem using gradient based solver code. It results in most efficient, structured approach to develop a combined energy storage and altitude control system -
FUTURE APPLICATIONS
-
-
CONCLUSION:
Both energy storage systems, such as chemical and thermal energy storage systems, currently contain chemical waste and emissions. Because of different forms of emissions, the existing environmental conditions are very grim. As a result, the increase of renewable energy output is booming, and it would be a perfect substitute for energy storage systems or in conjunction with other ESS at this time. Through doing so, we can learn more about its potential applications, such as FESS in spacecraft and the design and optimization of composite flywheels to improve energy storage. Currently, research is being conducted on the hybridization of FESS, which shows promise in terms of improved efficiency and energy storage on both a theoretical and practical level. Which can be predicted to become common in the future.
-
REFERENCES: