
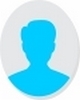
- Open Access
- Authors : Payal Vishnupant Shinde, Prof. D.P.Kharat
- Paper ID : IJERTV13IS030096
- Volume & Issue : Volume 13, Issue 03 (March 2024)
- Published (First Online): 26-03-2024
- ISSN (Online) : 2278-0181
- Publisher Name : IJERT
- License:
This work is licensed under a Creative Commons Attribution 4.0 International License
Review Paper on Effect of Carbon Fiber Reinforcement on Square Aluminum Cross Section for Automotive Applications
Authors Name: Payal Vishnupant Shinde
Mechanical Engineering Department Padmashri Dr.V.B.Kolte college of engineering,
Malkapur City: Malkapur,Maharastra Country: India
Authors Name: Prof. D.P.Kharat
Mechanical Engineering Department Padmashri Dr.V.B.Kolte college of engineering,
Malkapur City: Malkapur,Maharastra Country: India
Abstract- The existing studies on thin-walled structures have focused on structural optimization mainly for enhancing crashworthiness and light weighting, whilst relatively little attention has been paid to analysis of cost efficiency of an optimized structure. How to develop cost-effective products has always been a primary goal pursued by enterprises in different ways. To address this issue, this study aims to elucidate a systematic approach for exploring the effects of various material grades and structural dimension (e.g. wall thickness) on cost efficiency relative to the crashworthiness performance. Crashworthiness of a material is a measure of its ability to absorb energy during a crash. A well-designed crash box is instrumental in protecting the costly vehicle components. A square, hybrid beam of aluminium/CFRP was subjected to dynamic axial load. Composites are efficient, to deal with tensile loads, than metals. Now-a-days, metals are replaced with composites owing to their higher strength to weight ratio and are extensively used in automotive applications. Modeling and analysis of composite crash box was done on CATIA V5R21 & ANSYS workbench. Manufacturing of hybrid crash box will be done using open molding method. Testing of hybrid crash box performed on UTM for bending test.
Keywords – Crash boxes, impact, FEA, Impact Energy
- INTRODUCTIONThe operational cost of either passenger vehicles or fleet is directly proportional to the amount of fuel consumption. The fuel consumption, in turn, is proportional to the gross vehicle weight. Hence any reduction in the weight of the vehicle can bring in operational efficiencies. Hence manufacturers have been trying to use advanced and lightweight material such as CFRP composites to achieve low weight to high strength ratio [1]. Thin-walled CFRP tubes are also used as energy absorbers in both aerospace and ground transport vehicles in place of metals [2]. In the case of automobiles, few parameters are of significance to compare the effectiveness of the tubular designs. The most significant among these is the specific energy absorption capacity (SEA) of the tube which also considers the material with which the absorber is made up of.Fig 1- Crash box used in automobilesA crash box is a vital component located between the side- rails and the bumper protecting passengers as well as the parts that are expensive to repair like fender hood and radiator from serious damage during a frontal crash [1]. They are designed to meet the low speed impact regulations listed by the Research Council for Automotive Repair (RCAR) [2].Aluminum is a lightweight replacement that delivers excellent energy absorption compared to traditional materials like steel. Much research has been done to prove the crashworthiness of Aluminum [3]. Fiber reinforced polymers though expensive are used for light weight vehicles to improve its strength and crashworthiness with minimal increase in weight. Due to the presence of differently oriented fibers composites have better energy absorption characteristics than metals [4]. But metals are ductile while composites are brittle thus composites cannot be used as collapsible crash boxes to absorb energy despite its merits. A hybrid beam is a metal tube coated with a particular polymer composite thus retaining the ductility of metal and energy absorption of composites while increasing the overall strength, stiffness and crashworthiness [5]. Numerous researchers conducted axial
crushing experiments on hybrid beams. Crashworthiness of these was investigated while considering different cross sections, materials and different orientation of the fibers and ply [5-17]. An experimental analysis though necessary is expensive not to mention time consuming with a lot of uncertainty. A modeling and analysis software is a perfect utility to narrow down the total number of cases so that experimental validation can be done for the most important and positive cases.
- LITERATURE REVIEWG. Balajiet al. [1]Experimental and numerical evaluation is performed on a square hollow aluminium column, an aluminium honeycomb filled column, an aluminium column filled with combined carbon fibre and an aluminium honeycomb at constant velocity of 3.06 mm/s to analyze the axial crushing phenomenon at low speed axial loads. To validate experimental outputs, numerical simulation is performed using PAMCRASH explicit finite element code. The effects of honeycomb core and carbon fibre reinforced aluminium honeycomb were analysed experimentally and numerically. A decent agreement between experimental and numerical results is observed. The effects of deformation modes and force-displacement curves on these different structural columns were studied. Experimental and numerical results showed the square aluminium column filled with carbon fibre reinforced aluminium honeycomb was the most crashworthy combination, where the maximum increase of energy absorption, specific energy absorption and crush force efficiency were up to 60.6%, 27.8% and 17.4% respectively, compared with bare aluminium hollow column.Gurpinder S. Dhaliwalet al. [2]Hybrid Composite laminates have been widely regarded as a family of highly damage tolerant materials with a high weight-saving potential. The main hindrance to full utilization of Hybrid Composite System in the automotive industry is their structural response as compared to monolithic materials like Steel or Aluminum (AL). The main goal of this research is to investigate the stiffness, weight savings, loadcarrying capacity, failure Modes of Al/carbon fiber reinforced polymer (CRFP) hybrid composite system and validate the experimental results with computational Model.MA Quanjinet al. [3]The study aims to investigate the effect of different infill pattern structures on the energy-absorbing characteristics of single filament wound carbon fiber- reinforced plastic tubes, single polylactic acid and hybrid carbon fiber-reinforced plastic/ polylactic acid tubes under quasi-static axial compression condition, which were fabricated using filament winding and additive manufacturing techniques.The infill pattern structure plays an important role on the energy-absorbing characteristics in the inner single PLA and hybrid CFRP/PLA tubes.Filament wound hybrid CFRP/PLA tubes have potential for improvement of the energy-absorbing characteristics compared to inner single PLA and outer CFRP tubes.
- NasirHussainet al. [4]In case of a crash due to collision of vehicles, effective impact energy absorption by the vehiclesafety structure is significant as it reduces the damage to the vehicle and its occupants. Components made of composite materials have a more complex mode of deformation, unlike metals, which in general deform with buckling or bending modes. The deformation mode of the component made of a composite is of great importance as the energy absorption level depends on it. Deformation mode can be modified by introducing special geometric features known as triggers in the design of the crash box. A trigger can also be useful in achieving required deformation mode and thereby helpful in attaining target energy and force values.The relative merit of crash boxes with different combinations of cross-sections and trigger types for these parameters was assessed. The best performing combinations made from various notch triggers and different cross sections of crash boxes have been identified.Gangadhar Biradar1 et al. [5]in this research it represents execution of crash confine the vehicle crash value applications, likewise its impact on energy engrossing limit by expanding its divider thickness and the conduct of the crash box at different speeds. The Energy at stacking point is around 27,775 N-m. From the above classified qualities, we can see that by expanding the mass of the rectangular cross-area crash box to 4mm energyconsumed can be expanded to 25000 N-m which is exceptionally near energy at stacking point for example toward the beginning of the effect 27775N-m. At different speeds the conduct of the crash box was comprehended, higher the speed higher the energyabsorption and the energyare moved at a quicker rate to different pieces of the vehicle. The most significant finish of this examination is the adjustment in divider thickness for example 4mm is engrossing more energy than 2mm while 4mm divider thickness can be utilized in thevehicle gave it fulfills different factors, for example, the plan and mass of the crash box contemplations.Se-Jung Leeet al.[6]in this paper it presents a plan strategy to decide the cross-sectional measurements to improve the energyadaptation ability of the crash box. In the initial step, the cross-sectional measurements for the applied plan are resolved in two different ways. One is a parameter study utilizing discrete plan with a symmetrical cluster. The cross- sectional elements of the crash box are chosen among the accessible cross-segments namely a circle or a polygon. Three new sorts of crash box are recommended, with point by point shapes from the proposed plan technique. When planning the structure of a vehicle, crashworthiness of the frontal structure ought to be considered to limit traveler wounds, to diminish the effect energy moved to the vehicle body and to diminish the fix cost of the vehicle. In a low-speed crash, damage to the vehicle andpassenger wounds ought to be decreased as the crash box ingests the effect energy to the greatest. Calculated structure utilizing topology streamlining with ESLSO gives an altogether new cross-area state of the crash box. The three crash boxes with new cross-sectional measurements are acquired and these have high energy retention capacity and light mass. For crashworthiness enhancement of the crash box,
the parameters of strain energy, greatest clasping load and dislodging are utilized as theresponses.
Liu Yan-jieet al. [7]In the paper it presents car crash box at low-speed impact by utilizing Finite Element Method. The FE model of the cylinder was approved by looking at the exploratory outcomes and FE model outcomes. If there should arise an occurrence of frontal crash mishap, it is required to be fell with retaining crash energy preceding other body parts with the goal that the damage of the primary lodge outline is limited and travelers might be safe. Crash-box normally was made a psychological refined walled tube. Results show that on normal the difference of these was inside 10percent.The acceptable relationship of results acquired show that the numerical examinations are dependable. Crash-box of carbon steel and aluminum compound materials are thought about, it demonstrates that the peakimpact power and greatest energyadaptation have certain impact to energy retaining segment with various materials. The utilization of aluminum compound materials, it demonstrates that materials have certain impact to crashworthiness of energy retaining part.
Pawel Kaczyenskiet al. [8]in this paper it presents the consequences of semi static and dynamic crushingexperimental of tightened energy engrossing components made of AZ31 magnesium combination sheets. Also, few researches concerning the energyabsorption of thinwalled structures made of AZ31B magnesium amalgam and utilization of appropriate geometric shape permits to control the procedure of dynamic crushing and initiates another instrument of energy retention that is dynamic crushing. During the devastating of void crash boxes, there was no impact of the strain rate fair and square of energyconsumed. Strain rate impact was seen during the pounding of the aluminum froth, which was described by 53% more noteworthy crashworthiness during the static tests. Therefore, aluminum filled examples consumed more energy during the semi static tests.Interaction impact between the crash box (magnesium composite), and its filling (aluminum froth) have been watched. The energy consumed by filled crash boxes was 50-70% higher than the whole of energies consumed by aluminum froth and crash box independently.
OmkarGarud et al. [9] In this paper it presents crash box geometry with changing thickness for the energyadaptation and different parameters like width, thickness, tighten which influences on the crash box execution are examined. The plan of such structures for dynamic crush is significant provided that these structures distort at highsmashing powers there is high hazard to bio-mechanical damage to the vehicle tenants. Here, dynamic pound is a method of pivotal crush that starts close to the tip of the crash box and afterward advances towards back. Trial test is performed on UTM machine. Semi static recreation is performed utilizing ABAQUS. Utilization of different situated points show great impact on the energywithholding. Good understanding discovered in the middle of investigative, test and numerical investigation bring about the crash confine there is increment mean crushing load, and assimilated energy when we change cross area from rectangular to round or including a few irregularities like holes
in rectangular cross separated tubes.The crash box profile is improved and can satisfy the necessary goals. Additionally, we arrive at the resolution that conformedenergy increments with increment in thickness.
Dhananjay Desai et al. [10]In this article it present research on plane crash box geometry for the energy retaining. Different parameters like width, thickness, tighten which influences on the crash box execution are concentrated.Crash instruction smashing conduct is examined by utilizing semi static technique. Exploratory test is performed on UTM machine. By fluctuating the parameters and use of globules various structures are proposed and recreated for the greatest energy assimilation. Application of different situated globules show great effect on the energyabsorption. Trial and numerical recreation by utilizing ANSYS Explicit Dynamic examination is performed on plane crash box. In the crash box there is increment mean smashing load, most reduced pounding load and consumed energy. It is concluded that consumedenergy increments with increment in thickness and with decrease in tighten edge. Likewise increment in number of sides of box influences essentially on the energyabsorption. Plan G1 is assessed as best plan as it has high energy assimilation with low basic holding load.
- NasirHussainet al. [4]In case of a crash due to collision of vehicles, effective impact energy absorption by the vehiclesafety structure is significant as it reduces the damage to the vehicle and its occupants. Components made of composite materials have a more complex mode of deformation, unlike metals, which in general deform with buckling or bending modes. The deformation mode of the component made of a composite is of great importance as the energy absorption level depends on it. Deformation mode can be modified by introducing special geometric features known as triggers in the design of the crash box. A trigger can also be useful in achieving required deformation mode and thereby helpful in attaining target energy and force values.The relative merit of crash boxes with different combinations of cross-sections and trigger types for these parameters was assessed. The best performing combinations made from various notch triggers and different cross sections of crash boxes have been identified.Gangadhar Biradar1 et al. [5]in this research it represents execution of crash confine the vehicle crash value applications, likewise its impact on energy engrossing limit by expanding its divider thickness and the conduct of the crash box at different speeds. The Energy at stacking point is around 27,775 N-m. From the above classified qualities, we can see that by expanding the mass of the rectangular cross-area crash box to 4mm energyconsumed can be expanded to 25000 N-m which is exceptionally near energy at stacking point for example toward the beginning of the effect 27775N-m. At different speeds the conduct of the crash box was comprehended, higher the speed higher the energyabsorption and the energyare moved at a quicker rate to different pieces of the vehicle. The most significant finish of this examination is the adjustment in divider thickness for example 4mm is engrossing more energy than 2mm while 4mm divider thickness can be utilized in thevehicle gave it fulfills different factors, for example, the plan and mass of the crash box contemplations.Se-Jung Leeet al.[6]in this paper it presents a plan strategy to decide the cross-sectional measurements to improve the energyadaptation ability of the crash box. In the initial step, the cross-sectional measurements for the applied plan are resolved in two different ways. One is a parameter study utilizing discrete plan with a symmetrical cluster. The cross- sectional elements of the crash box are chosen among the accessible cross-segments namely a circle or a polygon. Three new sorts of crash box are recommended, with point by point shapes from the proposed plan technique. When planning the structure of a vehicle, crashworthiness of the frontal structure ought to be considered to limit traveler wounds, to diminish the effect energy moved to the vehicle body and to diminish the fix cost of the vehicle. In a low-speed crash, damage to the vehicle andpassenger wounds ought to be decreased as the crash box ingests the effect energy to the greatest. Calculated structure utilizing topology streamlining with ESLSO gives an altogether new cross-area state of the crash box. The three crash boxes with new cross-sectional measurements are acquired and these have high energy retention capacity and light mass. For crashworthiness enhancement of the crash box,
- PROBLEM STATEMENTThe two most common forms of collision in car crashes are frontal and side crash. The crush box and car frontal rails could likely undergo severe axial deformation during a frontal crash scenario, while the B-pillar, sill and roof rail, cross beam of the car pumper, etc., experience lateral bending deformation under side crash. For this reason, both the axial and transverse crash characteristics should be considered in crashworthiness design
- OBJECTIVES
-
- The present research work is to investigate the influence of composite reinforcement, on the bending strength, energy absorption and subsequent failure of hybrid composites crash box.
- Modelling and dynamic analysis of composite crash box was done on Catia V5R21 & ANSYS workbench.
- To perform experimental bending test on UTM and comparative study of optimized design of Hybrid Composite crash box.
-
- CONCLUSION
Based on previous research, the important findings are:
- In the past, many researchers used FEA method with different software packages to analyze the impact behavior during crash and how the device responded to the energy absorption. Moreover, various types of materials had been used in crash box structures in order to obtain high energy absorption.
- However, so far, none of the previous researchers used uniform carbon fiber reinforced polymer composites as materials with different cross section area of crash box structures.
REFERENCES:
- G. BalajiCrushing response of square aluminium column filled with carbon fibre tubes and aluminium honeycombThin-Walled Structures 132 (2018) 66768
- Dhaliwal GS, Newaz GM, Experimental and numerical investigation of flexural behavior of hat sectioned aluminum/carbon fiber reinforced mixed material composite beam, Composites Part B (2019), doi: https://doi.org/10.1016/j.compositesb.2019.107642.
- MA Quanjin1,2, Idris M Sahat1 , Mohd R Mat RejabThe energy- absorbing characteristics of filament wound hybrid carbon fiberreinforced plastic/polylactic acid tubes with different infill pattern structuresJournal of Reinforced Plastics and Composites 2019
- N. NasirHussain, SrinivasaPrakashRegalla and Y.V. DaseswaraRao, Study on influence of notch triggers on absorption of energy for composite automobile crash box under impact loads, Materials Today: Proceedings, https://doi.org/10.1016/j.matpr.2020.09.715.
- Automotive Crash Box Performance Analysis and Simulation during Frontal Rigid Barrier Crash Gangadhar Biradar1, AnjanBabu V.A, International Journal of Science and Research (IJSR), ISSN (Online): 2319-7064
- Omkar B Garud, Krishna S Pawar, Prashant K Thorat, Amit M Waghmare and Sagar P Chopade, Analysis and Experimental Validation of Crash Box for the Energy Absorption Capacity Journal of Engineering and Technology e-ISSN:2319-9873,18 February 2018
- Se-Jung Lee, Hyun-Ah Lee, Sang-Il Yi, Dae-Seung Kim, Heui Won Yang and Gyung-Jin Park, Design flow for the crash box in a vehicle to maximize energy absorption Proceedings of the Institution of Mechanical Engineers, Part D: Journal of Automobile Engineering 2013 227: 179, 30 july 2012
- Liu Yan-jie, Xia Chun-yan, Ding Lin,Liu Chun-hua,Influence of Material on Automotive Crash-box Crashworthiness Subjected to Low Velocity Impact Advanced Materials Research Vols. 655-657 (2013) pp 169-172 Online: 2013-01-25© (2013) Trans Tech Publications, Switzerland
- A Study of using Different Crash Box Types in Automobile Frontal Collision by Yanjie LIU, Lin DING.
- Pawel Kaczyenski Progressive crushing as a new mechanism of energy absorption. The crushing study of magnesium alloy crash-boxes, Progressive crushing as a new mechanism of energyabsorption. The crushing study of magnesium alloy crash-boxes, International Journal of Impact Engineering (2018)
- Omkar Garud, Krishna S. Pawar, Prashant K. Thorat, Amit M. Waghmare, Sagar P. Chopade, Analysis and Experimentation of Crash Box, International Journal for Research in Applied Science & Engineering Technology (IJRASET)ISSN: 2321-9653; IC Value: 45.98; SJ Impact Factor: 6.887Volume 6 Issue V, May 2018
- Dhananjay D.Desai, Prof.M.A.Kadam, analysis and development ofEnergy absorbing crash box, Vol-2 Issue-3 2016 IJARIIE-ISSN(O)- 2395-4396