
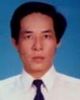
- Open Access
- Authors : Nguyen Van Thinh , Vo Thanh Tung
- Paper ID : IJERTV9IS060467
- Volume & Issue : Volume 09, Issue 06 (June 2020)
- Published (First Online): 22-06-2020
- ISSN (Online) : 2278-0181
- Publisher Name : IJERT
- License:
This work is licensed under a Creative Commons Attribution 4.0 International License
Research on Building Process Technology of Synthetic Piezoelectric Materials System PZT – SZN Doped Mn and Application
Nguyen Van Thinh Nguyen Th Hai Van
University of Technology and Education The University of Danang
Danang, Vietnam
Vo Thanh Tung University of Sciences The University of Hue Hue, Vietnam
AbstractMaterials science is the field of synthesizing, analyzing and applying new materials. Piezoelectric materials on the doped PZT base materials are used to manufacture ultrasonic transmitters and receivers. Regarding technology monopoly, commercial piezoelectric ceramic companies only publish the parameters and applications while the material formulas and technological processes are always kept secret. In this paper, we present the results of research on building technological process of synthesizing hard-doped PZT material system. To evaluate the technological process, a composite of PZT – SZN doped Mn4+ was conducted. As a result, we have successfully fabricated ceramic system (Pb0.95Sr0.05) ((Zn1/3Nb2/3)0.2 (Zr0.53Ti0.47)0.8)O3 + 0,5% Wt MnO2. In
particular, this technological process has lowered the material heating temperature, the 1st burning temperature at 7000C, sintering temperature at 10000C. Dielectric, electric iron and piezoelectric parameters: = 7,8 (g/cm3), kp = 0,58, d33 = 330 (pC/N), Tc = 3420C, Qm = 1000. Results of the study shows that the characteristic parameters clearly show the properties of hard piezoelectric materials, suitable for manufacturing power ultrasound transducer.
Keywords – Piezoelectric ceramic; PZT doped Mn2+; hard piezoelectric ceramic; piezoelectric coefficient d33; Curie temperature TC.
-
INTRODUCTION
From the properties of the forward and backward piezoelectric effect, piezoelectric ceramic is the basis for the manufacture of electrical – mechanical, mechanical – electrical energy conversion elements, in which the typical ultrasound transmitters and transceivers is made from piezoelectric ceramic based on doped PZT, also from here to develop the field of ultrasound, hydrography and applications. Currently, ultrasound technology is rapidly developing and widely used in many fields: science and technology, industry, agriculture, environment, medicine … In military, underwater ultrasound technology is called hydrodynamic, which is applied in Sonar passive and active equipment to actively equip for system of underground hunting of the Navy[1, 2].
Overview of the research and application of piezoelectric materials, in the world there is Morgan – USA producing commercial piezoelectric ceramic and there are many scientific works that have announced different types of piezoelectric ceramics depending on application purpose [1, 2]. However, it exists a situation of monopoly of technology;
commercial piezoelectric ceramic manufacturers and scientific works only announce trade names, typical parameters and application while material formulas, technological processes are always kept secret. Thus, with the goal of proactively manufacturing doped PZT ceramic systems suitable for application requirements, the issues that need to be posed and must be solved are:
Firstly, it is necessary to study and determine the PZT base materials formula, composition and doped concentration in order to create a hard and soft doped PZT ceramic system with high characteristic parameters, especially stable under conditions of high stimulus for a long time. Hard piezoelectric materials are used to make ultrasonic transmitters, soft piezoelectric materials are used to manufacture ultrasonic transducers and ultrasonic sensors [1].
Secondly, it is necessary to study and develop a process of synthesizing piezoelectric materials based on doped PZT.
Thirdly, it is necessary to identify the characteristic parameters according to international standards IRE – 61 and IRE – 87 on piezoelectric materials.
-
THEORETICAL BACKGROUND OF PIEZOELECTRIC MATERIAL
Piezoelectric ceramic is a material of polycrystalline structure, exists many domains in the microcrystalline in different directions, when it is not polarized by electric fields, the total electric dipole moment of the crystal is zero. After polarization by the electric field, the domain structure is rearranged in a fixed direction, the electric dipole moment is non-zero and the material exists piezoelectric nature. When the domain structure is rearranged, the direction of the external electric field is applied to the piezoelectric ceramic plate and the mechanical oscillation direction, whereas the direction of the mechanical stress on the ceramic plate and the generated electric field is determined. This is a decisive factor for the properties of forward,backward piezoelectric effect [4].
Fig. 1. Morphotropic Phase Boundary MPB according to the temperature of the PZT piezoelectric ceramic
Figure 1 is a Morphotropic Phase Boundary MPB according to the temperature of the PZT piezoelectric ceramic based on two components having the Perovskite ABO3 structure, PbTiO3 and PbZrO3. This is the basis for selecting the PZT component and determining the Curie temperature Tc of the material [4].
From the diagram, the horizontal axis represents the Zr / Ti component ratio, the right side is rich with Ti, the left side is rich in Zr, the vertical axis represents the temperature dependence according to the Zr/Ti component ratio. The temperature transition diagram is divided into three main areas: PC is the cubic crystal phase region, FT is the quadrilateral crystal phase region and FR is the rhomboidal crystal phase. The dividing line between the cubic and quadrilateral phases, the rhombic surface represents the variation of temperature, the dividing line between the quadrilateral phase and the rhombic phase is called the Morphotropic Phase Boundary (MPB). At room temperature, MPB lies adjacent to the Zr/Ti component ratio: 51/49, 52/48, 53/47. It is worth noting that the MPB has a stable and quite high temperature of 3600C. On the other hand, the adjacent MPB always exists two quadrilateral and rhombus surface so the material has very good piezoelectric properties. When the temperature is higher than the Curie temperature, the material changes to the cube phase so the material loses its piezoelectric properties. Thus, the selection of material system with the proportion Thus, the selection of the material system has the proportion of components adjacent to the morphological phase margin with high piezoelectric and Curie temperature is one of the important issues of piezoelectric ceramic manufacturing technology process [5] .
The morphological phase diagram is the basis for selecting PZT base materials according to Zr / Ti component ratio adjacent to MPB from two solid materials PbTiO3 and PbZrO3. A more important issue of the synthesis of piezoelectric materials based on PZT is that it is doped to have basic parameters suitable for the purpose of application. With piezoelectric materials on the basis of perovskit ABO3 structure, hard and soft doping method is oftend used. The softening effect of soft impurities is the creation of Pb defects (Vacancy Pb) in the network. The result when doping hard or soft into PZT-based piezoelectric material will produce the defect effect of Pb, O atoms in perovskit ABO3 structure network, leading to easier movement of atoms, from which Domain walls will also be easier to deform even under the influence of electric fields or small stresses [6, 8].
-
TECHNOLOGY PROCESS – THEORETICAL BACKGROUND OF PIEZOELECTRIC MATERIAL
Stage 1: Prepare the materials
The material is preparedon the basis of the formula of the selected ceramic system, the initial compositing components are oxides, PZT base materials including PbO, ZrO2, TiO2, SrCO3, ZnO, Nb2O5 and the doped component are MnO2. All ingredients must be above 99% purity, electronically balanced to an accuracy of 10-4 grams.
Stage 2: Grinding, mixing for 1st time
This stage is very important to create the homogeneity of the ceramic, it is necessary to make the particles reach fineness and mix evenly, easily creating solid phase reactions according to the principle of atomic diffusion in the stage of heating, it requires a diameter of particles less than 2µm. Attention should be paid to impurities mixed in the grinding and mixing process. To minimize this effect, the grinding and mixing process was carried out by PM400/2 MA-Type planetary crusher using zirconia balls for 20 hours [7].
After grinding and mixing for the first time, the material needs to analyze DTA-TG differential temperature to determine the material transition temperature. The results of DTA-TG will determine the 1st burning temperature and sintering temperature. According to the DTA-TG diagram, there are 2 peaks absorbing heat and the weight loss at 3700C and 9000C with analytical sample volume is only 50.63 mg. Experiments show that the fabricated samples with large volume need to investigate higher burning temperature. In this technological process, the first burning temperature was selected at 6500C, 7000C and 7500C, selecting sintering temperature at 9500C, 10000C and 10500C. The result chosing the first calcination temperature at 7000C and the sintering temperature at 10000C is the best. This is the basis for selecting the burning temperature for 2nd times in the process of synthesizing hard piezoelectric materials system PZT – SZN doped Mn4+.
Fig. 2. Differential thermal analysis scheme DTA-TG
Stage 3: Press, preheat
The solid material mixture after the first grinding is pressed into a 30 mm diameter disc tablet, 1500 kg/1cm2 compression force. With doped PZT material, the temperature of 7000C is selected, the heating speed is 50C/min, keeping the temperature at 7000C for 2 hours. This stage is the synthesis of compounds by solid phase reaction that occurs when there is the diffusion of atoms between adjacent particles, at a temperature lower than the melting point of each participating material. The mechanism consists
of four physical processes that occur during the preheating stage, which are: Linear expansion of particles in the room temperature range to 4000C; solid phase reactions in the range of 4000C – 6000C; shrinkage of material in the range of 6000C – 7500C and finally the development of particle size at temperatures above 8000C [6]
Stage 4: 2nd crushing
After preheating, we conduct a second crushing with a planetary crusher in a period of 15 hours. The purpose of grinding this time is to create a homogeneous compound and reduce particle size, helping substances participating in solid phase reactions occur completely at the sintering stage. The fineness and uniformity of the particles greatly affect the quality of the ceramic after sintering [7].
Stage 5: Pressing, sintering
The mixture of solid materials after the 2nd grinding is pressed into many pellets of 1.2mm diameter, 1.4mm thickness, 150kg/1cm2 compression force. With doped PZT material, sintering temperature of 10000C is chosen, heating speed of 50C/min and keeping the temperature at 10000C for 2 hours.
Stage 6: Sample treating
Create a sample size according to the international standard IRE – 61 on piezoelectric materials, in order to prepare for the measurement and survey of subsequent piezoelectric parameters. The surface of the sample is grinded by a sandpaper with increasing fineness of the Labpol Duo8 machine until it reaches the desired thickness, then rinse the sample with ultrasound before creating the electrode. Pay special attention to the surface flatness and the duplex plane between two sample surfaces.
Stage 7: Creating silver electrodes
Requirements of piezoelectric ceramic electrode: good conductivity, high adhesion and not destroyed when polarizing at high temperatures and electric fields. Electrode coating process is carried out as following: The sample is heated to a temperature of 4000C and a silver-oxide emulsion layer is applied to the two surfaces in turn for 20 minutes. At a temperature of 4000C silver oxide in the emulsion layer will be decomposed into Ag metal adhering to the sample.
Stage 8: Polarizing in an electric field
Before polarization, electric iron ceramics do not have piezoelectricity due to the chaotic distribution of electric iron domains. Polarization is the process of orienting and fixing domains in the direction of the electric field. After being processed, the sample has a thickness of 1mm, polarized at 30kV/cm electric field in silicon oil at 1200C, time is 30 minutes.
-
GENERAL RESULTS OF VOLTAGE MATERIALS PZT- SZN + 0,5% 5%wt Mn2+
From the theoretical basis of choosing material formulas, in this study, we choose the system of materials with the formula (Pb0.95Sr0.05) ((Zn1/3Nb2/3)0.2 (Zr0.53Ti0.47)0.8)O3 +
5%Wt MnO2 ( PSZ SZN + Mn2+). In particular, the PZT basis materials are selected according to the component mass ratio of Zr/Ti = 53/47 adjacent to the morphological phase boundary.
The parameters and properties of the material are surveyed according to international standards IRE-61 and
IRE-87. The experiment was conducted according to the established technology process, at the Material Science Laboratory, the Department of Physics – Hue College of Sciences. Dielectric, electric iron and piezoelectric parameters are measured on Hioki 3532 LCR measuring system and automation Impedance HP 4193A equipment, ceramic polarization with adjustable high voltage DC source of 0 – 40 kV. The structure was measured by X-ray diffraction method on D8 ADVANCE – Bruker device, the microstructure was photographed SEM by S4800 NIHE device. The results of parameters and properties are:
-
Piezoelectric properties.
In order to study the piezoelectric properties, we created the sample with shape and size in accordance with the international standard IRE – 61, the samples were made Ag electrode and polarized in appropriate ways in order to obtain the oscillation modes respectively. The selected polarization temperature is 1200C, polarized electric field of 30 kV/cm, 30 minutes. Resonance vibration spectrum measured on the Hioki 3532 LCR measuring system and automation Impedance HP 4193A equipment.
Fig. 3. Resonance spectrum of piezoelectric material PZT- SZN +
5%Wt Mn2+
Figure 3 shows the result of resonant spectroscopy measurements of ceramic samples in radial direction. The characteristic lines represent the phase dependence of the resonant oscillation spectrum, the impedance of the piezoelectric ceramic plate according to the frequency of the excitation signal. From the characteristic lines shows that when the impedance with the smallest value Zmin, resonant oscillation starts to occur, the frequency corresponding to Zmin is called the resonance frequency. When the impedance with the maximum value Zmax, it no longer exists resonant oscillation, the frequency corresponding to Zmax is called the anti-resonant frequency. The characteristics of the resonant oscillation spectrum in the resonant and anti-resonance frequency bands have the type of clear square, showing the piezoelectric properties of the material under the effect of the excitation signal source [4].
-
Structure.
The structure of the material was measured by X-ray diffraction method on D8 – ADVANCE Bruker device.
Figure 4 is the diffraction spectrum of the PZT-SZN sample material without doping, Figure 5 is the diffraction spectrum of the sample material with Mn2+ phase, the diffraction spectra of the two samples show the structure of the material with a single phase characteristic, no strange phase apears. Diffraction lines of PZT – SZN materials coincide with typical diffraction lines of material Pb(Zr0.53Ti0.47)O3 with network parameters a = b = 4.0550 A0, c = 4.1100A0, = = = 900. That shows the material with a typical quadrilateral structure, with double lines appearing at positions corresponding to angles 2 equal to 320, 44.50 500, and single lines at 38.20. With such crystal structure, it is concluded that the synthesized material sample has the main component located adjacent to the morphological phase edge completely in accordance with the selected material formula.
Fig. 4. X-ray diffraction spectra of unadulterated sample PZT- SZN
Fig. 5. X-ray diffraction spectra of sample PZT- SZN + 5%Wt Mn2+
-
Structure.
Microstructures were surveyed by SEM imaging method on S4800 – NIHE device.
Fig. 6. SEM photos taken in different magnification modes
Figure 7 shows a SEM image of a material sample taken at high magnifications. Samples of material without any chemical treatment, just randomly broken and washed with ultrasound before taking pictures. Noticeability from the microstructure shows that on each particle, there has been the formation of a stacked domain wall structure, the domain wall width is about 150nm, with a plate-type domain wall structure completely suitable for the doped PZT piezoelectric material. This is also the expected result because the material
has piezoelectric properties when the material exists the domain wall structure because the domain wall will deform easily under the action of electric fields or generate charges when there is mechanical stress. [6]
Fig 7. SEM photos taken in high magnification modes
-
Typical parameters of a piezoelectric material system PZT-SZN + Mn2+.
Electro-mechanical linking coefficient: kP = 0,58 Piezoelectric coefficient: d33 = 330 (pC/N) Quality coefficient: Qm = 1000
Curie temperature: TC = 3420 C Density: = 7,8 (g/cm3)
From the typical parameters, it shows that the PZT- SZN
+ Mn2+ piezoelectric system has the properties of hard piezoelectric materials. Theory and experiment show that, four parameters kP, d33 and Qm, TC never increase or decrease at the same time. Depending on the application purpose, hard or soft doping is selected to have the appropriate parameters. With this material, it is possible to fabricate high power ultrasound and application. [4].
-
-
CONCLUSIONS
A technological process for synthesizing piezoelectric materials has been developed with each stage explaining the mechanism clearly.
From the technological process, we successfully synthesized piezoelectric ceramic material system Pb0.95Sr0.05) ((Zn1/3Nb2/3)0.2 (Zr0.53Ti0.47)0.8) O3 + 5%Wt MnO2 (PSZ SZN
+ Mn2+). The characteristics of the material are investigated on modern solid analyzers such as Hioki 3532 piezoelectric measuring system and Impedance HP 4193A, XRD, SEM. The results showed that they are consistent with the theory, the typical parameters of the material system (PSZ – SZN + Mn2+) clearly show the properties of hard piezoelectric materials. Accordingly, it is confirmed that the material formula of the chosen hard piezoelectric ceramic system and the established technology process are perfect.
REFERENCES
-
Dong Chen, Sanjay K. Sharma, Ackmez Mudhoo (2012), Handbook on Applications of Ultrasound, Taylor & Francis Group, LLC.
-
Juan A. Gallego-Juarez and Karl F. Graff (2015), Power Ultrasonics Applications of High-intensity Ultrasound, Woodhead Publishing.
-
Walter Heywang, Karl Lubitz, WolframWersing (2008), Piezoelectricity Evolution and Future of a Technology, Springer- Verlag Berlin Heidelberg.
-
Kenji Uchino (2009), Advanced piezoelectric materials, Woodhead Publishing Limited.
-
T. Asada1 and Y. Koyama (2007), Ferroelectric domain structures around the morphotropic phase boundary of the piezoelectric material PbZr1xTixO3, Physical Rewiew B 75, 214111.
-
N. Iwaji, C. Sakaki, N. Wada, H. Takagi and Sh. Mori (2011), Ferroelectric domain structures and piezoelectric properties of Pb(ZrTi)O3 ceramics, Engineering aterials Vol. 485, pp 3-6, 10.4028/www.scientific.net/KEM.485.3.
-
J. S. Lee, M. S. Choi, Nguyen Viet Hung, Y. S. Kim, I. W. Kim, E. C. Park, S. J. Jeong, J. S. Song, Effects of high energy ball-milling on the sintering behavior and piezoelectric properties of PZT-based ceramics. Ceramics International 33, 1283 1286 (2007).
-
I. Kozielski, M. Adamczyk, J. Erhart Amplication Testing of Sr doping effect of PZT cemarÃc on the piezoelectric tranfomer gain and efficiency proposed for MEMS actuators driving. J electroceram (2012) 29: 133-138, DOI 10.1007/s10832-012-9746z