
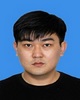
- Open Access
- Authors : Li Xin
- Paper ID : IJERTV11IS030029
- Volume & Issue : Volume 11, Issue 03 (March 2022)
- Published (First Online): 10-03-2022
- ISSN (Online) : 2278-0181
- Publisher Name : IJERT
- License:
This work is licensed under a Creative Commons Attribution 4.0 International License
Research on Bearing Fault Diagnosis Based on Correlation Entropy Time-Frequency Analysis and Deep Learning
Li Xin
School of mechanical engineering,
Tianjin Vocational and Technical Normal University, Tianjin
Abstract- For the research of bearing fault diagnosis based on correlation entropy time-frequency analysis and deep learning, the vibration signal obtained by the sensor is divided according to the training set and test set, the correlation entropy function of the segmented signal is calculated to reduce the noise, then the short-time Fourier transform is carried out to further filter the noise, and the two-dimensional time-frequency map of the segmented signal is obtained. Finally, the two-dimensional time- frequency map is input into the neural network,Automatic fault feature extraction, and draw the accuracy ACC curve, target value loss curve, confusion matrix and other visual graphics to automatically complete the classification of fault types.
Keywords- Graph wavelet; Figure signal; Feature extraction; Sparse; local
-
INTRODUCTION
With the continuous development of modern industry, mechanical equipment is widely used. It is developing towards large-scale, complex, digital, information and intelligence in both industrial production and daily transportation. At the same time, it also increases the uncertainty of the safe operation of mechanical equipment.In case of failure of these equipment, it will degrade the performance of the equipment, affect the processing accuracy of processed products, and cause great damage to the economy, life safety and environment. Therefore, in order to ensure the safe operation of the equipment and improve the service life of the equipment, it is necessary to monitor the operation status of the equipment in real time and detect and diagnose the key components of the equipment,Ensure the safe operation of the equipment.
Bearing is a very important component in rotating machinery. Many industrial products and consumer electronics and other equipment will use bearings. The stability of bearings directly affects the accuracy, reliability and comfort of equipment operation.If the faults and problems of bearings are found in time, the stability of rotating machinery can be greatly improved.Traditional bearing fault diagnosis is based on vibration signal analysis. When the background noise is strong or there are other impact elements, the diagnosis effect is very poor.The performance of simple time-frequency analysis method will degrade or even fail in the face of strong noise environment, and the correlation entropy can be used for noise reduction, which will have an ideal effect on Gaussian noise and non Gaussian noise. Therefore, a research on Bearing
Fault Diagnosis Based on correlation entropy time-frequency analysis and deep learning is proposed,This method makes comprehensive use of the correlation entropy time-frequency analysis, which can effectively extract fault features in the environment of low signal-to-noise ratio, and the method based on deep learning, which can adaptively extract representative features without any manual intervention, and can achieve the advantage of higher accuracy than vibration signal analysis and diagnosis in most tasks when the data set is large enough.
As a key component of rotating machinery, the running state of rolling bearing is not only related to major economic interests, but also has a far-reaching impact on social security.Therefore, the running condition monitoring and fault diagnosis of rolling bearing is very important.With the advent of the era of artificial intelligence, fault diagnosis is also developing towards the trend of intelligence.Therefore, it is of great significance to apply entropy based fault diagnosis in theory and practice.
-
RESEARCH ON BEARING FAULT DIAGNOSIS BASED ON CORRELATION ENTROPY TIME-
FREQUENCY ANALYSIS AND DEEP LEARNING
-
A. research status of bearing fault diagnosis methods at home and abroad
The fault diagnosis technology of bearing is to identify the fault type and degree according to the signal processing method or data-driven fault diagnosis method through the bearing operation state information collected by the sensor.
As the key mechanical equipment of modern industry, bearing has been operating in the complex environment of high temperature, fatigue and heavy load for a long time.In case of failure, it may lead to serious accidents, resulting in huge economic losses and casualties.Therefore, the running condition monitoring and fault diagnosis of rolling bearing is very important.
-
B. fault diagnosis method based on signal processing
In actual working conditions, most of the fault signals generated by bearing faults are non-stationary and nonlinear signals. Time domain analysis methods and frequency domain analysis methods can only reflect the fault information from a single aspect, and can not reflect the information in time domain and frequency domain at the same time. Therefore, it is difficult to accurately extract the fault characteristics. For
non-stationary and nonlinear gearbox bearing fault signals,Time frequency analysis is a more effective method.In recent years, the research results of time-frequency analysis methods for rolling bearing fault diagnosis include: in literature [1], Guo Yuting and others proposed rolling bearing fault signal analysis based on wavelet transform, which proved that compared with short-time Fourier transform, the rolling bearing fault signal analysis method based on wavelet transform can more clearly reflect the information in time domain and frequency domain.In reference [2], Wang Chaohai and others proposed a rolling bearing fault diagnosis method based on empirical mode decomposition and principal component analysis. This method can accurately identify faults, improve the efficiency of fault feature extraction and shorten the diagnosis time.In reference [3], Yue Xiaofeng and others proposed a time-frequency comprehensive analysis method based on wavelet packet analysis and Hilbert envelope analysis, and proved the effectiveness of this method.In reference [4], Li Xinyi and others proposed a new method for rolling bearing fault diagnosis based on haanning window interpolation fast Fourier transform. This method is based on minimum entropy deconvolution and Teager Energy Operator Demodulation, which can select fewer analysis points and identify the characteristic frequency of bearing fault in most cases.
However, the short-time Fourier transform has the problem of fixed time window width, the wavelet transform has the problem of reasonable selection of basis function [5], and the Wigner Ville distribution has defects such as cross interference term. When processing non-stationary signals, in order to obtain the information in time domain and frequency domain, it is necessary to process the fault signals with special means [6],The periodic time-varying characteristic caused by the physical structure and operation mechanism of the rotating equipment is an inherent attribute, which is internally related to the physical parameters of the system itself. The fault signal is non-stationary and non Gaussian.
-
C. Application of noise reduction mechanism based on correlation entropy in fault diagnosis
Correlation entropy [7-10] proposes a generalized correlation function based on the comprehensive use of reproducing kernel and information theory learning method. It is also an efficient method for analyzing Gaussian noise and non Gaussian noise. In literature [11], Li Hui et al proposed that correlation entropy includes not only the second-order moment of random variable amplitude, but also the higher- order moment of random variable amplitude,Therefore, it can effectively characterize the nonlinear characteristics of the signal and effectively process the nonlinear signal.Correlation entropy can effectively suppress Gaussian and non Gaussian noise. Correlation entropy based on kernel function provides a new robust solution for the treatment of Gaussian and non Gaussian noise.Document [12] proposed that the processing method of cyclostationary signal is combined with correlation entropy theory for signal processing.However, the cyclostationary signal processing method has limitations.That is, the correlation entropy time-frequency analysis method is
proposed, which can effectively reduce the above shortcomings.
-
D. fault diagnosis method based on deep learning
Traditional intelligent diagnosis methods mainly include feature extraction based on signal processing method [13,14] and fault classification based on machine learning method [15]. These methods have made great progress.However, in the face of a large number of structural data, the feature extraction method and mapping ability from signal to condition designed and selected by experts largely depend on previous knowledge, which is time-consuming and requires experience.Therefore, how to diagnose more accurately and efficiently is still a challenging problem.As the latest application technology in the field of machine learning and pattern recognition, deep learning has been widely used in image processing, computer vision [16,17], natural language processing [18-20], electromechanical equipment fault diagnosis and other fields with strong feature modeling and representation ability, and has achieved fruitful results.
In 2006, the concept of deep learning was first introduced into technology through proposal [21].In 2015, a review published in the journal Nature [22] pointed out that deep learning allows computing models composed of multiple processing layers to learn data representation through multiple layers of abstraction.Due to its strong representation learning ability, deep learning is very suitable for data analysis and classification.Therefore, in the field of intelligent diagnosis, many researchers apply technologies based on deep learning, such as multilayer sensing (MLP), self encoder (AE), convolutional neural network (CNN), DBN, recursive neural network (RNN) and so on.However, different researchers often recommend using different inputs (such as time domain input, frequency domain input, time-frequency domain input, etc.) and setting different superparameters (such as learning rate, batch scale, network architecture, etc.). Therefore, fault features in mechanical signals can be effectively mined through deep learning.
Each analysis method has its own advantages or disadvantages. Combining several methods can get a more effective method. Therefore, the combination of correlation entropy time-frequency analysis and deep learning can diagnose bearing faults more quickly and efficiently, so as to reduce the economic loss caused by rotating machinery.
-
-
TIME FREQUENCY ANALYSIS METHOD
-
A. Research on Bearing Fault Diagnosis Based on correlation entropy time-frequency analysis and two- dimensional convolution neural network
In view of the pollution of the sensor signal caused by the environmental noise in the running environment of the bearing, the correlation entropy of the training set and the test set is calculated to reduce the signal noise, and then the one- dimensional signal after noise reduction is time-frequency transformed to obtain the two-dimensional characteristic map of the fault signal. Finally, the preprocessed characteristic map is input into the convolutional neural network,In order to solve the accurate identification of vibration signal under the condition of noise.
Time frequency analysis method:
-
Short time Fourier transform
The process of calculating the short-time Fourier transform is to adopt the sliding window mechanism, set the window size and step size on the longer time-domain signal, divide it into small segments of signals with the same length, perform fast Fourier transform on each small segment of signals, and stack the transformed frequency-domain signals to form a complete STFT time-frequency diagram to reflect the change of frequency with time.
-
Wavelet transform
Wavelet transform (WT) is a time-frequency analysis method for analyzing non-stationary signals. It can be used for fault feature extraction and can effectively extract the weak pulse signal of small defects in vibration signals.The wavelet transform basis function adopts finite length and attenuated wavelet basis. By scaling and translating the wavelet basis to a certain point, the amplitude of the frequency corresponding to the wavelet of this size at that point is obtained through the inner product of the signal
-
Wigner Ville distribution
WVD is the Fourier transform of the instantaneous correlation function of the signal, which reflects the instantaneous time-frequency relationship of the signal.For a single component LFM signal, the projection of WVD on the time-frequency plane is a straight line, that is, the linear variation of frequency with time.Because there is no window operation in the calculation, it avoids the mutual restriction between time domain resolution and frequency domain resolution.For single component LFM signal, the time- frequency representation of WVD has the best energy concentration.However, because the window function is not involved, WVD will be disturbed by cross terms when analyzing multi-component signals.
Through the combination of correlation entropy and the above time-frequency analysis methods, the two-dimensional characteristic map is obtained and input into the neural network to complete the classification of bearing faults.
-
-
FLOW CHART
-
RESEARCH CONTENT
This research adopts the method of combining theoretical research, simulation analysis and experimental research to diagnose the fault of bearing.
In view of the wear, pitting, fracture and other faults of rolling bearings, most of them will produce periodic vibration signals during rotation, and some of them can be regarded as cyclostationary signals, but some signals can not be regarded as cyclostationary signals.Therefore, the bearing fault diagnosis can only be carried out through the time-frequency analysis methods (short-time Fourier transform, wavelet transform, Wigner Ville distribution) to solve the non- stationary signal, so as to reveal the characteristic law of the complex and changeable vibration signal of the rolling bearing and effectively improve the reliability of the fault diagnosis of the rolling bearing.
In the case of low signal-to-noise ratio, the fault diagnosis of bearing by time-frequency analysis method may deteriorate or even fail, and Gaussian noise and non Gaussian noise will be generated when bearing fault occurs.Therefore, the method of correlation entropy is proposed to reduce noise and solve the influence of low noise ratio, Gaussian noise and non Gaussian noise on bearing fault diagnosis.
The traditional intelligent diagnosis method is feature extraction based on signal processing method, which largely depends on artificial feature extraction and artificial feature selection, which is time-consuming and requires experience.Therefore, a bearing fault diagnosis based on deep learning is proposed, which extracts the features of the training sample set and the test sample set, so that the extracted information has the fault features to the greatest extent, and then classifies the fault.Reduce the manual fault diagnosis of bearing as much as possible, so as to make its use more concise and convenient, time-saving and labor-saving.
-
CONCLUSION
A bearing fault diagnosis network model based on correlation entropy time-frequency analysis and deep learning is built.The research of bearing fault diagnosis based on correlation entropy and deep learning is completed to make its application more concise and convenient.It can achieve the effect of noise reduction. Using the deep learning framework based on pycharm, it completes the construction of neural network structure, parameter adjustment, data training and testing, and visualization of classification results. Finally, it successfully distinguishes the fault type and degree of bearing.
REFERENCE
-
Guo Yuting, Xiao Shuyan Fault signal analysis of rolling bearing based on wavelet transform [J] China test, 2017,43 (S1): 142-147
-
Wang Chaohai, Cai Jinhui, Zeng jiusun Research on rolling bearing fault diagnosis based on empirical mode decomposition and principal component analysis [J / OL] Journal of metrology, 2019 (06): 1077- 1082
-
Yue Xiaofeng, Shao Haihe A time-frequency comprehensive analysis method for bearing fault diagnosis [J] Manufacturing technology and machine tools, 2015 (08): 51-54
-
Li Xinyi, Xie Zhijiang, Luo Jiufei Application of windowed interpolation fast Fourier transform in rolling bearing fault diagnosis [J]
China Mechanical Engineering, 2018,29 (10): 1166-1172
-
Chen Di Research on equipment fault feature extraction method based on time-frequency analysis [J] China Equipment Engineering, 2021 (19): 11-13
-
Ren Shengjie, Guo Weichao, Shu Dingzhen, Tang aofei, Gao Xinqin, Li Yan Rolling bearing fault diagnosis based on time-frequency analysis and deep learning [J / OL] Mechanical science and technology: 1-11 [2021-11-03]
-
LIU W FPOKHAEL P PPINCIPE J CCorrentropy: a localized
similarity measureC The 2006 IEEE International Joint Conference on Neural Network ProceedingsVancouver: IEEE2006
-
SANTAMAIA IPOKHAEL P PPINCIPE J CGeneralized correlation function: definitionpropertiesand application to blind
equalizationJ IEEE Transactions on Signal Processing2006 54( 6) : 2187 2197
-
LIU W FPOKHAEL P PPINCIPE J CCorrentropy: properties and applications in non gaussian signal processingJ IEEE Transactions on Signal Processing200755( 11) : 5286 5298
-
GUNDUZ APINCIPE J C Correntropy as a novel measure for nonlinearity testsJSignal Processing200889( 1) : 14 23
-
Li Hui Noise reduction mechanism of correlation entropy and its application in bearing fault diagnosis [J] Bearing, 2021 (03): 36-44
-
Li Hui Research on efficient algorithm of cyclic correlation entropy spectral density estimation [J] Journal of electronics and information, 2021,43 (02): 310-318
-
Z. Zhao, S. Wu, B. Qiao, S. Wang, X. Chen, Enhanced sparse period- group lasso for bearing fault diagnosis, IEEE Transactions on Industrial Electronics 66 (2018) 21432153.
-
S. Wang, X. Chen, C. Tong, Z. Zhao, Matching synchrosqueezing wavelet transform and application to aeroengine vibration monitoring, IEEE Transactions on Instrumentation and Measurement 66 (2016) 360372.
-
C. Sun, M. Ma, Z. Zhao, X. Chen, Sparse deep stacking network for fault diagnosis of motor, IEEE Transactions on Industrial Informatics 14 (2018) 32613270.
-
Krizhevsky, I. Sutskever, G. E. Hinton, Imagenet classification with deep convolutional neural networks, in: Advances in neural information processing systems, pp. 10971105.
-
CFarabet, C. Couprie, L. Najman, Y. LeCun, Learning hierarchical
features for scene labeling, IEEE transactions on pattern analysis and machine intelligence 35 (2012) 19151929.
-
J. Hirschberg, C. D. Manning, Advances in natural language processing, Science 349 (2015) 261266.
-
S. Sun, C. Luo, J. Chen, A review of natural language processing techniques for opinion mining systems, Information fusion 36 (2017) 1025.
-
T. Young, D. Hazarika, S. Poria, E. Cambria, Recent trends in deep learning based natural language processing, ieee Computational intelligenCe magazine 13 (2018) 5575.
-
MITTechnologyReview,10BreakthroughTechnologies2013,https://ww w.technologyreview.com/lists/technologies/2013/, accessed on August 2019.
-
Y. LeCun, Y. Bengio, G. Hinton, Deep learning, nature 521 (2015) 436.