
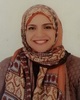
- Open Access
- Authors : Marwa M Rashad
- Paper ID : IJERTV12IS010081
- Volume & Issue : Volume 12, Issue 01 (January 2023)
- Published (First Online): 27-01-2023
- ISSN (Online) : 2278-0181
- Publisher Name : IJERT
- License:
This work is licensed under a Creative Commons Attribution 4.0 International License
Recovery of Rare earth from Abu Tartur Phosphate by Purolite C150 Resin
Marwa M Rashad 1*
1 Nuclear Materials Authority, P.O. Box 530 El Maadi, Cairo, Egypt
Abstract:- Process for REE recovery from Abu Tartur phosphate rocks were studied. Various experiments were carried out using batch technique for the adsorption of RE (III) ion from a standard and obtained leach liquor solution from phosphate ore by applying optimum leaching conditions, the optimum conditions for loading of RE (III) ion onto Purolite C150 were determined in a batch system with a concentration of 100 mg/l. it was found that the adsorption REEs optimum pH value was found to be 6.5 at 120 min contact time, the elution RE (III) loaded on the surface of used resin. Hydrochloric, nitric acid and sodium chloride used as eluting agents, factors that effect on desorption (%) were separately investigated using 0.2 gm loaded resin. The obtained data indicate 1.0 M HCl, 1.4 M HNO3 and 2.0M NaCl were the optimum concentrations, 180 min. contact time and 6 ml volume of eluting agent. Also effect of temperature in desorption was found to be 22 °C.
-
INTRODUCTION
The traditional industries of metallurgy, petroleum, and textiles have all utilized rare earth elements (REE). In high-tech fields today, such as clean energy technologies, superconductor materials, batteries, plasma televisions, optical fibbres, or the military industry, are increasingly becoming important and essential [1].
As a result of their widespread use in technologies like lasers, satellite communications, and radar, they are regarded as strategically significant. Some of them are also essential in petroleum cracking catalysts and vehicle catalytic converters. Two pseudo-lanthanides; Sc and Y, 14 lanthanides, and other elements with a similar electron configuration make up the group of elements known as REE [2] . They have high oxidation (III) states and large ionic radii. Light Rare Earth Elements (LREEs) are those REEs with atomic numbers between 57 (La) and 64 (Gd), whereas Heavy Rare Earth Elements are those with atomic numbers between 65 (Tb) and 71 (Lu) (HREEs). Sc and Y are classified as LREE and HREE, respectively, based on the similarities in their properties [3].
Other phosphorite sources are also considered potential rare earth resources. Egyptian phosphate rocks occur in three main provinces, Western Desert; Abu Tartur plateau, Nile Valley and Red Sea. About 1200 km2 of the major Plateau between Kharga and Dakhla Oases in the Western Desert of Egypt are covered by the Upper Cretaceous Abu-Tartur phosphorite, which is located about 50 km to the west of Kharga town. A little amount of the Ca can isomorphously replace with several elements, including Mg, Mn, Sr, Pb, and Na in addition to uranium and rare earth elements in rock phosphates, which may also contain other intriguing trace elements. PO4 radical can typically be
partially substituted by trace amounts of VO4, AsO4, SiO4, and SO4. The sedimentary phosphorite rocks have a grey to black color due to the reducing environment in which they were formed, but if they were subjected to geochemical weathering, the pyrite mineral would be converted to hematite and anhydrite or gypsum minerals via oxidation [4]. Although REEs are found in more than 200 minerals, practically all of the production has originated from fewer than 10 minerals. The three most economically significant minerals known to contain significant or critical REEs are bastnasite [(Ce La) (CO3) F], monazite [(Ce La Nd Th) PO4], and xenotime (YPO4).
Recovery of REE and possible associated valuable elements are the most important concerns of the Nuclear Materials Authority of Egypt. In recent years, a large number of researchers interested in rare earth elements separation and recovery from their solutions. The most common method for the recovery of REEs from mineral acid leachates has been solvent extraction using organophosphorus reagents, mainly tributyl phosphate; TBP or di-2-ethylhexyl phosphoric acid; D2EHPA [5]
Radhika et al., 2012 [6] studied solid liquid extraction of gadolinium from phosphoric acid medium using commercial amino phosphonic acid resin, Tulsion CH-93. The extraction efficiency decreased with acid concentration increasing, conforming ion exchange mechanism. Tulsion CH-93 resin showed a selective extraction towards heavy rare earths (Lu and Yb) which could be separated from other rare earths at 3 mol/l H3PO4, similar to wet phosphoric acid (3-5 mol/l). On the other hand, Gd (III) and other rare earths were studied with chelating resin Tulsion CH-90. Light rare earths were highly extracted and these could be separated from heavy rare earths and Gd.
Kim et al., 2011 [7] described leaching REEs from the ore materials using (NH4)2SO4 then, REEs were adsorbed from this leachate by blue green algae; phormidium. When the concentration of ammonium sulfide was 1 %, leaching time was 3 h, and S/L ratio was 0.09, the leaching ratio of Nd was 67.3 %. In the adsorption process, when the dosage of phormidium was 0.2 kg L-1, the contact time was 30 min, and the temperature was 298 K, while pH was being kept at the initial value (i.e., pH 5.6), the adsorption density of Nd was 182 mg kg-1. This study aims to describe the optimum conditions that suitable for recovery of REEs from Abu Tartur phosphate using Purolite C150 resin
-
MATERIALS AND METHODS
Phosphate rock is the major source of phosphorus in nature. It exists mainly in the form of hydroxyapatite
[Ca10(PO4)6(OH)2] and fluoroapatite [Ca10(PO4)6F2] or a mixture of both and is mainly used for the production of fertilizers and elemental phosphorus. Nile Valley, Red Sea coast and New Valley in the Western Desert represents the main regions of phosphate in Egypt. The sedimentary phosphate rock contains 100-200 ppm of uranium, 2-20 ppm thorium and about 0.5 % rare earth elements (REEs). Phosphoric acid produced by the wet process method has many heavy trace elements which lead to environmental calamities. The phosphate samples were collected from the practical mine of Abu Tartur plateau located in Egyptian Western Desert.-
Rinsing of Purolite C150
Purolite C150 is a strong acid cation-exchange resin (Na form), contains crosslinked polystyrenes with sulphonic acid groups which introduced after polymerization by treatment with concentrated sulfuric or chloro-sulfonic acid, all experiments were applied with a high purity resin. If the resin is not purified, the following steps are applied to keep the resin cleaned. Washing a 50 g of a resin with 200 ml of 0.5 M HCl in Teflon beaker, let both of them in contact with each other for 6 hours; then acid removed by filtration. The resin can be poured into a beaker with distillated water. The cleaning resin was done by alternating 6 M HCl; 100 ml and distillated water; 200 ml at least 3 times. Distillated water was used to remove all the excess acid. It was then dried and the dried resin was used for further experimental work.
-
Sample digestion
The dissociation of phosphate samples, which is introduced for analyzing and measuring REEs by different techniques, runs in the following steps; i) weighing 1gm of each powder geological rock samples in 100 ml Teflon beakers and moistened with a few ml of distillated water ii) adding 40 ml of concentrated HF, 10 ml of concentrated HClO4 and 10 ml of concentrated HNO3, the mixture was evaporated on a hotplate at 200°C until dryness. iii) remove any remnant traces of HF by adding 5ml of concentrated HClO4; 70% to each beaker and the solution again evaporated to dryness. iv) the residue was dissolved in 20 ml 1 M HCl acid with gentle heating until a clear solution obtained and then alkali fusion was done.
-
Preparation of total REEs stock synthetic solution
A standard stock solution of 1000 mg/l REEs was prepared by dissolving a mixture of 1.039 g lanthanum nitrate (La (NO3)3.6H2O) and 1.033 g cerium nitrate (Ce (NO3)3.6H2O) besides 1.436 g yttrium nitrate (Y (NO3)3.6H2O) of Sigma-Aldrich in 1000 ml acidified distilled water with 5 ml concentrated hydrochloric acid. This solution was actually used to determine the relevant factors of REEs sorption upon the Purolite C150 resin.
-
Preparation of Some Ions Stock Synthetic Solutions
Several standard stock solutions of 1000 mg/l of possible ions were prepared by dissolving suitable weights
of their salts in 1000 ml distilled water e.g., Si4+ Al3+ Ca2+,
-
Analytical Procedures
-
Chemical Analysis of Phosphate Rock
-
The phosphate sample and its leach liquor were analyzed to determine their constituents then crushing. about 3 kg into pea size, followed by grinding using a blending mill to 60 mesh size, about 50 g was separated by quartering before being ground to -200 mesh size, the pulverized sample was then analyzed using the suitable techniques after complete dissolution. Whereas the major oxides SiO2, Al2O3, TiO2, and P2O5 were analyzed using spectrophotometric methods, the content of Na and K were determined by the flame photometric technique. Total Fe as Fe2O3 was determined by titration with EDTA using sulphosulcylic acid as an indicator from which was subtracted the amount of ferrous which was determined by titration method.
-
REEs Determination
-
Batch leaching experiments
Leaching experiments were carried in under batch technique because of its simplicity, using dried and ground phosphate sample that had an initial REEs concentration of 2117 ppm., these experiments were performed by using the optimum condition [ 8].
-
REEs Adsorption Procedures
A strongly acidic cation exchange resin Purolite C150 Polystyrenic Macroporous, was used for REEs adsorption from standard and leach liquor solutions. Several Batch adsorption experiments were performed to evaluate the performance of Purolite C150 resin in the removal of REEs from aqueous solutions such as pH, contact time, adsorbent dosage, initial REEs concentration and temperature. All the experiments were carried out in duplicate and the mean values were used in all cases. The experiments were carried out by shaking 50 mg of Purolite C150 resin with REEs solution in 100ml conical flask on a magnetic stirrer for 2h at constant agitating speed Most experiments were conducted at room temperature. Moreover, effect of temperature was conducted at different temperature values. The pH was adjusted to desired values by adding 0.2 M NaOH or 0.2 M HCl solutions. At the end of the agitation period, the aqueous phase was separated from solid by filtration. The amount of REEs uptake; adsorbed onto surface of resin was calculated by the difference between the equilibrium and the initial REEs concentration.
-
Desorption Studies
The desorption procedure was performed upon 0.2 g of the RE loaded-resin that is carefully washed with flowing distilled water using 5 ml volume of different Concentrations of the hydrochloric, nitric acids and NaCl ranging from 0.1 up to 3 M at room temperature for 180 min contact time. At the end of the agitation period, the aqueous phase was separated from solid by filtration. The concentration of REEs eluted was spectrophotometrically determined with Arsenazo-III. In this study we investigated
, ,
Fe3+, Ti4+, Th4+, Cl etc. These ions are used as standard solutions during its determination using the suitable technique.
the parameters that effect on REEs desorption such as
concentration of eluent, contact time, and temperature. After treating the resin with the eluent, it is carefully washed with distilled water to become ready for recycle.
-
Precipitation of Total REEs
-
After the desorption procedure, the total rare earth elements were precipitated by adding excess of 20% oxalic acid solution. The latter is often used in industrial operation due to process simplicity and effective recovery. Adjust the pH of the solution to 1-2, then heat to 70 °C for 30 min. The mixture was left for 24 h to cool and complete precipitation then the precipitate was then filtered. The oxalate precipitate was dried and calcined in a muffle furnace at 800-1000 °C for 2 h to obtain mixed rare earth oxides. Dissolve the precipitate in a small amount of hot 1 M HC1 to introduce for spectrophotometer and ICP-OES for analysis.
-
-
RESULTS AND DISCUSSION
The chemical analyses data of major and trace elements as well as individual and total rare earth elements for the examined Abu Tartur phosphate rock are listed in Tables 1 and 2. The rare earth elements leach liquor used for this study is prepared by treating 1 kg of properly ground sample; -200 mesh size of Abu Tartur phosphate sample with 3 liters of 1 M hydrochloric acid solution for 60 min. agitation time at room temperature [8] . The insoluble gangue residue is then filtered and the obtained leach liquor is found to assay 665 mg/L of total rare earth elements using a spectrophotometric technique. On the other hand, the interesting associated ions in the prepared leach liquor are analyzed. From the results in Table 3 and 4 the leach liquor contained a different concentration of associated metal ions therefore it was recommended that the leach liquor required further purification or addition of masking agents to obtain high grade of the rare earth elements.
Major constituents |
Concentration (%) |
Trace constituents |
Concentration (ppm) |
SiO2 |
5.00 |
Zn |
176 |
Al2O3 |
0.90 |
Zr |
35 |
Fe2O3 |
4.2 |
Th |
5 |
CaO |
43.5 |
U |
21 |
MgO |
1.55 |
V |
182 |
P2O5 |
29.3 |
Pb |
6 |
TiO2 |
0.09 |
Cu |
15 |
Na2O |
1.42 |
Cr |
157 |
K2O |
0.17 |
Cd |
9 |
MnO |
0.09 |
Ba |
209 |
F- |
3.11 |
Ni |
16 |
Cl- |
0.05 |
Sr |
1330 |
*L.O.I |
9.54 |
As |
45 |
Table 1. Chemical analysis of major and trace constituents for Abu Tartur phosphate rock sample
Sm |
90 |
Yb |
22 |
Eu |
15 |
Lu |
30 |
Gd |
140 |
Y |
290 |
Tb |
30 |
Sc |
200 |
* RE E s |
2117 ppm |
*REEs: total rare earth elements
Table 3. Chemical analysis of some major and trace
elements for phosphate leach liquor
Constituents |
Concentration g/L |
Constituents |
Concentration mg/L |
SiO2 |
1.10 |
Zn |
60 |
Al2O3 |
0.23 |
Zr |
<>5 |
Fe2O3 |
2.3 |
Th |
0 |
CaO |
7.4 |
U |
5 |
MgO |
0.43 |
V |
30 |
P2O5 |
4.53 |
Cr |
37 |
TiO2 |
0.08 |
Ba |
55 |
Na2O |
0.18 |
Ni |
4 |
K2O |
0.07 |
Sr |
412 |
MnO |
0.01 |
—— |
——– |
Table 4. Chemical analysis of individual and total REEs for
REEs |
Concentration mg/L |
REEs |
Concentration mg/L |
La |
85.4 |
Dy |
18.6 |
Ce |
141.3 |
Ho |
11.0 |
Pr |
18.5 |
Er |
5.0 |
Nd |
97.5 |
Tm |
31.5 |
Sm |
28.1 |
Yb |
6.3 |
Eu |
4.6 |
Lu |
9.1 |
Gd |
44.9 |
Y |
90.2 |
Tb |
9.4 |
Sc |
63.3 |
REEs |
665 |
—– |
—— |
phosphate leach liquor.
Table 2. Chemical analysis of individual and total REEs for
Constituents |
Concentration, ppm |
Constituents |
Concentration, ppm |
La |
270 |
Dy |
60 |
Ce |
450 |
Ho |
35 |
Pr |
59 |
Er |
16 |
Nd |
310 |
Tm |
100 |
Abu Tartur phosphate rock sample
-
Adsorption Studies of REEs
Various experiments were studied to determine the optimum adsorption parameters such as initial pH, contact time, initial concentration of RE (III) and temperature on the stander solution which assay 100 mg/L.
-
Influence of pH
The effect of pH on the adsorption of REEs by Purolite C150 Polystyrenic Macroporous, Strong Acid Cation Resin was examined. The pH of the aqueous solution is an important parameter that controlled the sorption process. In order to study the influence of pH upon the adsorption behaviors of Purolite C150 resin toward REEs, several batch experiments were performed by shacking 50 mg dry resin with 50 ml volume of standard REEs assaying 100 mg/l in chloride medium at different pH value in the range of 1.5 to 7.5, for 180 min. contact time at room temperature. The pH of the REEs studied solutions were adjusted to desired values by using 0.2 M HCl or 0.2 M NaOH. From the obtained results in Figure 1. It is clearly evident that the rare earth elements uptake on Purolite C150 resin has gradually
increased by increasing the pH till reaching maximum percent at pH 6.5. The reduced uptake on the resin at the acidic medium is due to the excess of hydrogen ions in the solution which have a large ability to compete with the REEs cations on the resin active sites during adsorption processes. The concentration of H+ decreased gradually with increasing pH, thus the adsorption percentage increases, till the maximum adsorption percentage at pH 6.5. Then the percentage of adsorption decreases again at the pH values above 6.5 this might be attribute as some amount of REEs ions were precipitated as hydroxide forms. Hence, the selected pH 6.5 was used for the quantitative extraction of rare earth elements by the studied resin which gave the highest uptake at the given conditions.
Fig. 1. Effect of pH on the adsorption efficiency of RE(III) onto Purolite C150 resin
-
Influence of Contact time
The effect of contact time upon the REEs uptake from their solution by Purolite C150 resin were studied in the range of 5 to 240 min. while the other adsorption parameters were fixed at pH 6.5, 50 mg resin and 50 ml volume of RE ions assaying 100 mg/L at room temperature. The obtained data showed that REEs uptake percent gradually increased with increasing the contact time till reaching the maximum values in 120 min. further increase in contact time has no significant increase in adsorption percent. On the other hand, REEs uptake reached to equilibrium at 120 min. as showed in Figure 2. Thus 120 min. considered the equilibrium contact time for adsorption REEs.
Fig. 2. Effect of contact time on the adsorption efficiency of RE(III) onto Purolite C150 resin
-
Influence of Resin Dose
The effect of the resin amount upon rare earths adsorption was investigated in the range of 10 to 100 mg; the other factors were fixed at 50 mL of synthetic mixed rare earth elements in chloride solution assaying 100 mg/L, pH of 6.5, and 120-min. stirring time at room temperature. The effect of adsorbent dose was expressed in terms of both adsorption efficiency and maximum uptake (qe). The obtained results shown in Figure 3 revealed that REEs adsorption efficiency increased with increasing the resin dosage. As the figure showed, the significant increase in the adsorption efficiency of REEs was observed when the dose was increased from 10 to 60 mg. where, the adsorption percent increased from 19.5 to 94.5 % and further increasing in dose of resin didnt cause significant increasing in adsorption percent. On the other hand, the corresponding maximum uptake decreased from 94.5 to 82.7 at 60 mg resin dose and down to 49.6 mg/g at 100 mg resin dose. The increase in adsorption efficiency can be attributed to the fact that more active sites are available by increasing the surface area resulting from increasing adsorbent dose, whereas some of active sites remain unoccupied by increasing the dose of adsorbent and this leads to decrease in REEs uptake [9,10].
10
9
8
7
6
5
4
3
2
1
0 1 2 3 4 5 6 7 8 9 10
Resin (mg)
Fig. 3. Effect of resin dose on the adsorption efficiency of RE(III) on to Purolite C150 resin
-
Influence of Initial REEs Concentration
Several batch experiments were performed to study the effect of varying the initial RE (III) concentration on the uptake of RE (III) ions from solutions. These experiments were carried out by shaking 50 mL of standard REEs solution in the range of 20 to 300 mg/L at pH 6.5 with 50 mg resin for 120 min. contact time at room temperature. The results plotted in Figure 4 revealed that as the initial REEs concentration increased, the amount of REEs uptake (qe in mg/g) increased. The maximum uptake value was 94.5 mg/g when the initial REEs concentration was 100 mg/L. Further increasing the initial REEs concentration does not affect the REEs uptake. This result confirmed that the maximum REEs loading capacity is 94.5 mg/g of dry resin. Assuming that the total exchange capacity of the working resin equals 2 eq/L in consideration of its Na+ form, thus the calculated REEs saturation capacity would be 81.76 g REEs/L. resin, according to the specification. Moreover, the obtained practical loading capacity compared with the specifications of the working resin, where 10 g of the dry resin is practically wetted in a measuring cylinder to determine the volume of the wet resin which was 14.5 ml. In a manner that 1 g dry resin is equivalent to 1.45 mL wet resin, the obtained practical capacity has however only attained 65.17 g/L. This difference between the theoretical and practical exchange capacities is indeed due o the presence of hydration shell that may cover some active site of the studied resin at the optimum conditions of extraction.
Fig. 4. Effect of initial RE(III) concentration (mg/l) on the adsorption performance of Purolite C150 resin.
-
Influence of Temperature
-
The influence of temperature on the rare earth elements adsorption efficiency using Purolite C150 resin was investigated in the range of 25 to 70ºC, by stirring 50 ml of synthetic mixed obtained results were plotted in Figure 5 indicate that the adsorption efficiency of REEs slightly increased to 97.3 % by increasing the temperature to 70ºC. This effect is Characteristic of the chemical reaction or bond involved in the Sorption process with the increase in temperature increasing the Equilibrium conversion. [11] mentioned that the Increase in sorption with temperature may be either attributed to the increase in the number of active surface sites available for sorption on the adsorbent or owing to the decrease in the boundary layer thickness surrounding the sorbent, so that the mass transfer resistance of adsorbate in the boundary layer was decreased. Accordingly, the RE adsorption efficiency (94.5 %) is equivalent to 94.5 mg rare earth elements per 1 g of dry resin at room Temperature.
9
9
9
9
9
2 3 4 5 6 7
Temperature
Fig. 5. Effect of temperature on the adsorption efficiency of RE(III) on Purolite C150 resin
3.2. REEs Adsorption from Leach Liquor
The separation RE(III) from leach liquor which contain 665 mg/l RE(III) ions was carried out also by
purolite C150 by batch adsorption technique to investigate the similarity or the difference between adsorption RE(III) from standard and leach liquor solutions. A lot of parameters that effect on RE(III) adsorption such as pH, contact time, and temperature were studied.
3.2.1. Effect of pH
In order to investigate the effect of pH upon maximum adsorption efficiency of rare earth elements from their leach liquor, some experiments were done by shacking 100 mg Purolite C150 with 15 ml leach liquor assaying 665 mg/L REEs; 15 ml contains 9.97 mg REEs content at different pH values in the rage of 1.5 to 7.0. For 60 min contact at room temperature, the experimental results were plotted in Figure 6, it can be observed from the figure, as the values of pH increase the RE(III) adsorption efficiency increased and the maximum adsorption efficiency was achieved at 6.5. in strong ac medium, the uptake in low percent. This is due to the large excess of H+ ions which compete RE(III) for the binding sides on the surface of the resin. While at the pH greater than 6.5, the adsorption efficiency decreased again owing to the formation of RE(III) precipitation and some impurities such as Ca (II) ions that have ionic radii similar to RE(III) ionic radii which ranged from 0.851.14 Ã… for RE(III) and 0.99 Ã… for Ca (II). These led to precipitate RE(III) ions with Ca (II) ions as hydroxide on the surface of resin. Therefore, the pH 6.5 is the optimum value for further experiments of adsorption REEs.
10
9
8
7
6
5
4
3
10
9
8
7
6
5
0 3 6 9 12 15 18 21 24
Contact time
Fig. 7. Effect of contact time on the adsorption efficiency of RE -leach liquor onto Purolite C150
3.2.3. Effect of Temperature
The effect of temperature on the adsorption efficiency of RE(III) from leach liquor was studied by mixing 15 ml leach liquor with 100 mg Purolite C150 resin at different temperature values in the range of 25 to 70 °C, while the other parameters were kept constant at pH 6.5, 120 min., contact time. The results are plotted in Figure 8. It was observed that the adsorption efficiency of RE(III) ions slightly increases from 93.9 to 97.1 % with increasing the temperature from 25 to 70 °C. The increase in sorption efficiency with increasing the temperature may be either attributed to the increase in the number of active surface sites available for sorption on the resin or due to the decrease in the boundary layer thickness surrounding the sorbent, so that the mass transfer resistance of adsorbate in the boundary layer was decreased. According to the feasibility study, the room temperature is the suitable temperature for the REEs sorption efficiency (93.9 %) which equivalent to 93.7 mg rare earth elements uptake per 1 g of dry resin at room temperature. Therefore, the REEs loading capacity upon the resin was 93.7 mg/g. Studying the adsorption of RE(III) from the phosphate leach liquor using Purolite C150 resin, showed that the optimum conditions of this process were pH 6.5, 120 min contact time at room temperature and the maximum loading capacity of RE(III) from leach liquor reached 93.7 mg/g at the giving conditions.
0 1 2 3p
4 5 6 7
Fig. 6. Effect of pH on the adsorption efficiency of RE- leach liquor onto Purolite C150
3.2.2. Effect of Contact Time
To study the effect of contact time on the adsorption of RE(III) from aqueous chloride leach liquor,15 ml leach liquor solution was shacked with 100 mg Purolite C150 resin for different contact time in the range of 15 to
240 min. Initial pH was adjusted at 6.50 at room temperature. The experimental results are graphically represented in Figure 7, it is observed that the sorption efficiency of RE(III) increased with increasing the contact time until a maximum sorption is achieved at 120 min. Therefore, the equilibrium time was attained for 120 min.
9
9
9
9
9
9
9
2 3 4 5 6 7
TemperaC
Fig. 9. Effect of eluting agents concentration on desorption efficiency of REEs from the loaded-resin
Fig. 8. Effect of temperature on the adsorption efficiency of RE leach liquor onto Purolite C150
-
Rare Earth Desorption Studies
In this study, desorption process to elute RE(III) adsorbed from the leach liquor on the resin was applied using HCl, HNO3 and NaCl as eluting agent in batch technique, at constant agitating speed, At the end of the agitation period the aqueous phase was separated from solid by filtration, the obtained solutions were analyzed to determine the RE(III) content.
-
Effect of Eluent Concentration
Effect of eluting agents concentration on desorption RE(III) ions loaded on the surface of Purolite C150 resin was carried out in batch technique by shaking 5ml of each eluting agents, HCl, HNO3 and NaCl at different concentrations of in the range of 0.1 to 3 M, with
0.2 g loaded resin. The other parameters were kept constant,
120 min. contact time at ambient temperature. The experimental results in (Fig. 9), it is observed that the elution efficiency of RE(III) increased with increasing the concentration of the eluting agents, maximum desorption efficiencies attaining 85, 87 and 80% at 1 M HCl, 1.5 M HNO3, and 2 M NaCl respectively. Therefore, it can be concluded that the three eluting agents can be used quantitative desorption RE(III) from the surface of used resin.
-
Effect of Contact Time
The effect of contact time upon the desorption efficiency of the RE(III) loaded on the surface of the Purolite C150, was studied in the range of 15 to 240 min, by shacking 5ml of each eluting agents, 1 M HCl, 1.5 M HNO3 and 2 M NaCl, with 0.2 g loaded resin at room temperature. the obtained results are plotted in Figure 10, it is clearly that the desorption efficiencies increase as shaking time increase and the maximum rare earths desorption efficiencies 92, 90 and 85% obtained at 180 min. for 1 M HCl, 1.5 M HNO3, and 2 M NaCl respectively. Further increase in contact time has no significant effect on desorption efficiency, this indicates the system attained its equilibrium for the studied eluting agents. From these data, it can be recognized that each 1 ml of 1 M HCl, 1.5 M HNO3, and 2 M NaCl could elute 3.46, 3.38 and
3.19 mg of rare earths from the loaded resin respectively.
Fig. 10. Effect of conact time on the desorption efficiency from the loaded resin.
-
Effect of Eluting Volume
The import factor in this study is investigate the minimum volume of eluting agents could elute high percent
Of rare earths from the loaded-resin. Several experiments were studied by stirring 0.2 g RE(III) loaded-resin with different volumes of each eluting agents, Hydrochloric, nitric acids and sodium chloride solutions in the range of 1 to 10 ml, for 180 min. contact time at room temperature, the obtained results are graphically represented in Figure 11. It was found that number of rare earths ions eluted increased with increasing the volume of eluting agents, the maximum amount of REEs eluted were achieved at 6 ml the three used eluting agents, the RE(III) ions contents almost 18.78 mg. Therefore, 6 ml volumes of the studied eluting agents are enough to the RE(III) ions desorption content from 0.2 g loaded resin at the giving conditions.
HCl HN 3 NaC
1
1
1
9
9
8
8
8
8
8 HC HN3
7
NaC
7
7
2 3 4 5 6 7 8
Temperatu°C
1
1
9
7
5
3
1
-1 1 2 3 4 5 6 7 8 9 1
Volume
Fig. 11. Effect of eluting volume on the desorption content of REEs from the loaded-resin
-
Effect of Temperature
-
The effect of temperature upon the desorption efficiency of RE(III) was investigated by shacking 0.2 g RE- loaded resin with 5 ml eluting volume 1 M HCl, 1.5 M HNO3 and 2 M NaCl at different temperature in the of 25 to 80 °C, for 180 min. contact time. The obtained results were plotted in Figure 12; indicate that the desorption efficiency of REEs slightly increased from 92, 90 and 85% to 93.5, 91.2 and 87% for HCl, HNO3, and NaCl respectively by increasing the temperature to 80 ºC. It is possible to deduce that the effect of temperature on desorption efficiency of RE (III) from the surface of the studied loaded-resin is endothermic and thus the room temperature is the best temperature for desorption efficiency
Fig. 12. Effect of temperature on the desorption efficiency of REEs from the loaded-resin
-
Desorption optimum Conditions
According to the experimental results of REEs desorption from the surface of Purolite C150 using Hydrochloric, Nitric acids and Sodium chloride as eluting agents and 0.2 g RE loaded-resin, 1M HCl, 1.5 M HNO3 or 2 M NaCl, 180 min. contact time ,6 ml the volume of eluting agent and room temperature were found the optimum conditions.
-
REEs Precipitation Studies
-
The experimental precipitation of RE as oxalate is performed by evaporating the desorption volume until 100 ml volume assaying 19.95 g/L concentration of REE which is stirred for 120 min. with 100 mL volume of 20 % oxalic acid at pH 1 and then allow to stand for 24 h to reach the equilibrium between the solid and liquid phases and the resulted two phases were separated by filtration. Then, the precipitate roasted in furnace at 8001000 °C for 2 hours to convert RE oxalates to RE oxides concentrate. The photographic picture of the obtained precipitate in Figure 13, Finally, the precipitate was analyzed to determine some cations such as uranium, iron, calcium, sodium, vanadium, strontium, phosphorous and zinc which were found to assay 1, 400, 500, 30, 100, 200, 3000 and 30 mg/L respectively using ICP-AES technique. The concentration of the total rare earth is 75.3 % from the rare earths concentrate by a spectrophotometric technique.
Fig. 13 Photographic picture of RE precipitate
CONCLUSION
The optimum conditions for loading RE (III) ion onto Purolite C150 were established in a batch system with a concentration of 100 mg/l after various experiments were conducted using batch technique for the adsorption of RE
(III) ion from a standard and obtained leach liquor solution from phosphate ore by applying optimal leaching conditions. At 120 minutes of contact time, the REEs' ideal pH value for adsorption was discovered to be 6.5; the elution RE (III) loaded on the surface of utilized resin. Using 0.2 gm of loaded resin, factors that affect desorption (%) were individually examined using hydrochloric, nitric, and sodium chloride as eluting agents. It is important to extract these metals from ore for our beneficial, the extraction these metals have a health and economical importance, in fact this method of extraction this element is simple, low cost and produce 75.3 % REEs as oxide, a novel resin, further treatments may improve this percent, so we recommend using this method in large scale in our country.
REFERENCES
[1] Zhang, J., Zhao, B., Schreiner, B. 2016. Separation hydrometallurgy of rare earth elements. XVI, 259. https://doi.org/10.1007/978-3-319-28235-0. [2] Canadian Chamber of Commerce, Canadas Rare Earth Deposits Can Offer. A Substantial Competitive Advantage, in: Economic Policy Series, 2012. https://www.prnewswire.com/news- releases/rare-earth elements-a-rare-opportunity-for-canada- 149050095.html. [3] Xie, F., Zhang, T.A., Dreisinger, D., Doyle, F. 2014. A critical review on solvent extraction of rare earths from aqueous solutions, Miner. Eng. 56, 10-28. [4] Zidan, I. H. 2014. Evaluation of phosphorite and uranium in Lower Member, Duwi Formation at Kummer Area South Esna, West Nile Valley, Egypt, Sedimentology of Egypt. 2, 55-67. [5] Cánovas, C.R., Pérez-López, R., MacÃas, F., Chapron, S., Nieto, J.M., Pellet-Rostaing, S., 2017. Exploration of fertilizer industry wastes as potential source of critical raw materials. J. Clean. Prod. 143, 497505. https://doi.org/10.1016/j.jclepro.2016.12.083. [6] Radhika, S. Nagaraju, V., Kumar, B. N., Kantam M. L., Reddy, B.R. 2012. Solid-liquid extraction of Gd(III) and separation possibilities of rare earths from phosphoric acid solutions using
Tulsion CH-93 and Tulsion CH-90 resins. Journal of Rare Earths, 30, 1270-1275.
[7] Kim, J. Ah., Dodbiba, G., Tanimura, Y., Mitsuhashi, K., Fukuda N., Okaya, K., Matsuo, S., Fujita, T. 2011. Leaching of Rare-Earth Elements and Their Adsorption by Using Blue-Green Algae, MATERIALS TRANSACTIONS. 52, 9, 1799-1806. [8] Abdel-Aal E.S.A. 2000. Recovery of phosphoric acid from Egyptian Nile Valley phosphate tailings. Minerals Engineering, 13, 223-226. [9] Rafati, L., Mahvi, A.H., Asgari, A.R., Hosseini, S.S. 2010. Removal of chromium (VI) from aqueous solutions using Lewatit FO36 Nano ion exchange resin. Int. J. Environ. Sci. Tech., 7, 147 [10] Mohammed, A. A., Mahmood, H. S. 2013. Removal of Cu+2, Pb+2 and Ni+2 ions from simulated waste water by ion exchange method on Zeolite and Purolite C105 resin. Journal of Engineering, 19, 1327. [11] Meena, A.K., Mishra, G.K., Rai, P.K., Rajgopal, C., Nagar, P.N. 2005. Removal of heavy metal ions from aqueous solutions using carbon aerogel as an adsorbent. Journal of Hazardous Materials, 122, 161.