
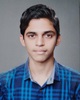
- Open Access
- Authors : Aditya Bodas , Ruben Fernandes , Shreyas Kulkarni
- Paper ID : IJERTV10IS100079
- Volume & Issue : Volume 10, Issue 10 (October 2021)
- DOI : http://dx.doi.org/10.17577/IJERTV10IS100079
- Published (First Online): 20-10-2021
- ISSN (Online) : 2278-0181
- Publisher Name : IJERT
- License:
This work is licensed under a Creative Commons Attribution 4.0 International License
Recent Advances in Stretchable Electronics: Materials, Mechanisms, and Applications
Aditya Bodas
Dept. of Mechanical Engineering Pillai College of Engineering New Mumbai
Shreyas Kulkarni
Ruben Fernandes
Dept. of Mechanical Engineering P.E.Ss Modern College of Engineering Pune
Dept. of Mechanical Engineering
PVGs College of Engineering and Technology Pune
Abstract Recent advances in mechanics and materials, integrated circuits can be developed that have the same electrical properties as conventional, rigid wafer-based technologies but are capable of stretching, compressing, bending, twisting, and deforming to fit any shape. Elastic electronics, or stretchable electronics, are an emerging class of electronic devices that consist of circuits or devices built on stretchable substrates. A wide range of applications can be envisioned, including flesh-like biodevices as well as stretchable, completely conformable, skin sensors for robotic devices. With stretchable electronics, it can be challenging to keep functionality when subjected to external strains. This paper reviews the materials and mechanism of stretchable electronics A wavy design allows one-dimensional stretchability, while the island-bridge design allows flexibility in all directions. A structural design inspired by fractals is an effective way to achieve greater stretchability and large-area properties.
Keywords Stretchable Electronics, Nanowires, Dielectrics, PDMS, Transistors, Display, Flexible Substrates, Healthcare, Sensors, Machine Learning
INTRODUCTION
In the past 70 years, the miniaturization of electronics on traditional electronic materials has enabled modern-day conveniences, safety, and efficiency in our daily lives. However, we are constantly searching for alternative materials and process technologies to lower manufacturing costs while enhancing the capabilities of electronic devices. Having the ability to compress and twist its components, stretchable electronics is a relatively new technology that achieves a great variety of applications. Otherwise, these applications are impossible to address using conventional wafer-based technologies or even those that allow simple bendability. With this physical transition from rigid electronic components to a mechanically compliant, flexible, and stretchable system will discard architectural incompatibilities, enhance existing applications, and enable new ones that aren't possible today. Recent trends in the electronics industry have driven the interest in and development of stretchable electronics due to the growing demand for wearable, intelligent, and integrated systems. This paper summarizes key elements of this emerging area of electronics (1-3).
-
MATERIALS IN STRETCHABLE ELECTRONICS Organic conductive materials have been studied since
1962. In 2000, the Nobel Prize in Chemistry was awarded for the discovery of a large set of polymeric conductive materials that lead to further progress in the field of low-cost large-area thin-film transistors and organic LEDs (4-6). So far, molecular and organic electronics are considered the primary ingredients for flexible electronics, but two key aspects are still unresolved: low electrical conductivity and thermal instability (7-9). In the 1990s, the discovery of fullerenes was followed by advances in carbon nanotubes and a wide variety of nanowires that inspired research into materials for flexible electronics (10-12). As a result of their superior properties (compared to organic materials) and natural compliance, these materials have been used for a variety of flexible devices (13- 15). Scientists have been focusing on two-dimensional materials for the past ten years, which show promise for large area coverage and pristine atomic crystal structure with superior charge transport (11-16). In particular, these materials have been investigated for energy storage, transparent conductive thin films, and sensor technology. Yet, non-uniform growth, the lack of an interfacial layer to improve conduction, as well as the formation of dielectric and conductive interfaces, remain major challenges (22).
The development of new two-dimensional atomically thin materials continues every day despite the reduction in momentum. Since the beginning of flexible electronics, classical crystalline materials have been ignored because of their rigidity, brittleness, and already dominant presence. Yet advances in thin films have opened up a new way to work with nearly identical material properties (those of traditional materials) for flexible electronics. Despite this, flexible single crystal silicon, gallium nitride, and III-V electronics have surged from the late 1990s until the early 2000s (22). These devices can be manufactured using existing complementary metal-oxide-semiconductor (CMOS) technology, which makes them very appealing. They are fast, scalable, and reliable, too. There has also been research exploring the use of paper as a possible host substrate for ultra-low-cost flexible electronics (17-19). Nevertheless, their reliability has been questioned frequently. The recent demonstrations of
recyclable papers as active electronic materials and their biocompatibility have brought them back as an alternative material for flexible electronics (20-21).
The use of new materials opens up new possibilities for stretchable electronics. Typically, electrical interconnections between rigid or bendable active devices are established with elastic conductors. Conductive rubbers made from elastomers with carbon black have been known for decades, but their resistances and strain sensitivity make them unusable. A recently developed approach uses long, single-walled carbon nanotubes (SWNTs) as conductive dopants in a rubber matrix (8-9). Typically, SWNTs are ground in an ionic liquid, then mixed with fluorinated copolymers to yield a black, paste-like material called bucky gel. Individual SWNTs form tangled mats in these gels, which can reconfigure under applied strain so that highly conductive pathways can be maintained. PDMS sheets can be printed with this material to produce elastic conductors with a stretchability of up to 100 percent. Fig -1 shows a sample of this type with a micrograph of the SWNTs associated with it. Alternative, related approaches use SWNTs on thin films made by solution casting or other methods (23- 25).
Fig. 1. Stretchable rubber printed with conductive lines of SWNT gel (left) and SWNTs network (right)[26]
-
MANUFACTURING METHODS AND MECHANISM
In most cases, stretchable systems are formed by engineering flexible shapes and elastic substrates with intrinsic stretchability [27]. These components can be used for a wide variety of applications that require flexibility and longevity. In order to create stretchable systems, various methods have been used. One of these is the use of intrinsically stretchable materials. These include various synthetic rubbers, such as natural rubber, styrene-butadiene rubber, etc. [28]. Due to the nature of this method, it is usually not feasible to make stretchable electronic devices. Other methods such as wavy, island-interconnect and meshing, fractal design, and origami structures were suggested to make the system stretchable [27].
-
Wavy structural configuration
To create the wave structure on an elastomeric substrate, the mechanical buckling method (MBM) is used. The thick- thin film layer can then be stretched and made flexible by the wave structure (Fig -2). With respect to deformation ability and electronic properties of final devices, wavelength () and peak amplitude (A) are crucil [29]. When large strains are used, the and A of a compliant substrate become nonlinear. Therefore, geometrical deformation and a nonlinear constitutive model should be considered. To enhance stretchability, semiconductor materials (such as Si, GaAs, InP,
and lead zirconate titanate) and metals are generally made into wavy shapes using MBM to achieve stretchability [30-32]. The wave structures developed in recent years have been extended from traditional MBM films to arched ones. A highly stretchable LIB with an arched structure, for instance, could accommodate large strains but it only had an area capacity of 0.11 mAh cm -2. It was found that the arched electrode could bear a 400% strain and maintain stable electrochemical properties after 500 cycles, and the stretchable LIBs could handle a 400% strain as well. The stretchability is nearly three times that of the previous wavy methods [33]. The wavy shape is a simple method to fabricate fully stretchable LIBs at the device level, after all the components (cathode, anode, separator, current collector). and packaging is stretched equally for the first time. This stretchable LIB demonstrated stretchability of 50% with an areal capacity of 3.6mA h cm-2 [34]. The concept of wavy structural stretching can be applied to new flexible devices, providing promising new directions for research in the future.
Fig. 2. Schematic illustration of the Composite thin films on a substrate, forming wavy structures with different wavelengths and amplitudes
-
Island-interconnect configuration and mesh structure
An effective method for the manufacturing of stretchable electronics is to develop islands of stiff materials on polymer substrates. These stretchable interconnects can be prepared by utilizing highly malleable electronic materials like low- temperature liquid metals, or by designing the interconnections to attenuate local strains through out-of-plane deformations.
The fracture strength of inorganic semiconductors limits the stretchability of devices based on wavy inorganic nanoribbons and membranes. To overcome this limitation, Kim et al. [35] developed a strategy in which an entire ultrathin circuit system (Fig -3) is fabricated first and then integrated onto a prestrained elastomer to form a wavy interconnected device array.
A thin, flat substrate can be bent into a cylindrical shape having a small radius. When this thin sheet is bent down, the top surface is under tensile force, and the bottom surface is under compressive force. But there is no strain induced on the middle surface so we assume it as a neutral surface. To reduce strains, we can place hard materials on this neutral surface. Hard materials can be placed on the neutral surface by laminating the substrate with another layer of material, to attenuate strains on hard materials
Fig. 3. Optical image of CMOS inverters with coplanar mesh design. [36].
-
Island-Interconnect Circuit Mesh on Flat Elastomers: This type of circuit consists of isolated device islands that are linked by metal interconnects. Using photolithographic patterns and etching the island interconnect mesh design is obtained on a wafer-like pattern. The design is then deposited on Polydimethylsiloxane also called PDMS slab which allows depositing a thin layer of Cr/SiO2 on inorganic islands.
Fig. 4. The fabrication process of wavy structure [37].
-
IslandInterconnect Circuit Mesh on Curvilinear Elastomers:
The processes are shown in Fig -5 show how to wrap electronic components onto flexible substrates with complex curvilinear shapes. These components can be assembled using an island-interconnect circuit mesh layout or an elastomeric transfer element. A flat drumhead membrane is formed by radially stretching a transfer element from its rim. The tension between the points in the PDMS varies with position. The tension is then relieved to make the membrane and the circuit on it resemble the shape of the substrate. The mesh interfaces are then modified to accommodate the forces required to make the system work seamlessly.
Fig. 5. Representation of islandinterconnect circuit meshed on curvilinear elastomers
-
-
Fractal design of stretchable interconnects
For stretchable electronic applications, a structural design inspired by fractals is an effective way to achieve greater stretchability and large-area properties. Due to this highly complex and diverse microstructure inherent in high-order fractal patterns, this structure often undergoes intricate nonlinear deformations in response to external stress [38,39]. By using simplex cuts in a hierarchy with different motifs, fractal designs can transform inextensible sheets into highly tensile and super-conformable materials with various conceivable shapes and patterns, as seen in Fig -6 [40]. Hierarchical cuts and motifs resulting from a simple transformation would have the effect of changing macroscopic shapes and resulting stretching performances [41]. Thus, the fractal design has the distinct purpose of cutting a flexible substrate into rotating units defined by the cutting patterns and motifs of the unit. Stretchable devices can be manufactured with rigid thin films combined with fractal motifs, enabling unusual mechanics that have a wide range of implications. There are a number of fractal designs that are typically used for fabricating space-filling hard electronics (cables, sensors, actuators), including the piano, Greek cross, and Vicsek designs. The function of different fractal constructs is also determined [42]. Fractal geometries play a significant role in determining the final stretchability performance.
Fig. 6. Representative fractal-inspired layouts for hardsoft materials integration [43]
-
-
APPLICATIONS
-
Soft robotics and stretchable electronics
Through the development of soft-robotics by Whitesides et al, we can observe major innovations as well as their practical usage in robotic arms and other organs [44]. While interacting with humans and handling fragile objects soft robots show advantages over hard counterparts. Stretchable electronic devices are vital for the sensing and actuation of soft robots, transforming the interaction between humans and machines.
-
Wearable
Fitbit introduced the first mainstream electronic health tracker, establishing itself as a major player alongside major electronics giants Apple and Samsung. The same type of products has been developed by hundreds of companies since then, while only slightly varying in the functionalities and the designs. The device uses miniaturized integrated circuits, but in the end, it is not completely flexible. It is still expensive. Overall, there is still a long way to go before truly flexible wearable devices become mainstream [45].
-
Implantable
Similar to how pacemakers transformed the pacemaking industry, implantable electronics would likely transform the medical field. Implantable electronics are viewed negatively by the general public due to long-term reliability and safety concerns, along with genuine acceptance by medical practitioners. Researchers currently focus on brain-machine interfaces and nanomedicine drug delivery (which, by the way, is not an implantable device) [46,47].
-
Healthcare
Stretchable Electronics embedded in garments can be used to interact with the body seamlessly and collect data non- invasively on diseases or patients. Seoul National University and MC10 (a flexible-electronics company) have developed, a patch that can detect glucose levels in sweat and deliver the medicine needed (insulin or metformin) on demand. A graphene patch embedded with gold particles has sensors that can detect temperature, pH level, glucose level, and humidity [48]. Developers can also design soft robots that can perform minimally invasive surgery in hospitals by integrating stretchable electronics. Robots may be better suited to brain surgery, because every millimeter count, and humans my lack a very precise scope of action [49].
CONCLUSION
The purpose of this paper is to describe some of the unique material properties, mechanisms, and applications of flexible electronics. The flexibility, mechanical flexibility, and durability of flexible electronics, as well as the easy and low- cost integration of the devices, make them well suited for a wide range of applications. It is only the tip of the iceberg when it comes to technological advances in flexible and stretchable components, substrates, and applications. New advances in flexible electronics are being made every day. Researchers are developing new materials with unprecedented form factors, as well as ways to fabricate devices in less conventional shapes, cheaper, and easy to access. Future electronics will be able to deliver effective and impactful applications through materials, process technologies, and
affordable integration strategies. From harvesting energy from sunlight through roofs, vehicles, and generating energy using warmth from our bodies and surroundings for consumer electronics, wearables, and implantable bioelectronics, this will place the field at the forefront of new products and applications.
REFERENCES
-
A. M. Hussain and M. M. Hussain, Adv. Mater., 28, 4219 (2016).
-
J. M. Nassar, J. P. Rojas, A. M. Hussain, and M. M. Hussain, Extrem. Mech. Lett., 9, 245 (2016).S. F. Shaikh, M. T. Ghoneim, G. A. Torres Sevilla, J. M. Nassar, and A. M. Hussain, IEEE Trans. Electron Devices, 64, 1894 (2017).
-
T. Zyung, S. H. Kim, H. Y. Chu, J. H. Lee, S. C. Lim, J.I. Lee, and J. Oh, Proc. IEEE, 93, 1265 (2005).
-
J. Heeger, A. G. MacDiarmid, and H. Shirakawa, 116 (1974) https://www.nobelprize.org/uploads/2018/06/advancedchemistryprize20 00.pdf.
-
C. D. Sheraw, L. Zhou, J. R. Huang, D. J. Gundlach, T. N. Jackson, M.
G. Kane, I. G. Hill, M. S. Hammond, J. Campi, B. K. Greening, J. Francl, and J. West, Appl. Phys. Lett., 80, 1088 (2002).
-
T. Sekitani and T. Someya, Adv. Mater., 22, 2228 (2010).
-
T. Sekitani, H. Nakajima, H. Maeda, T. Fukushima, T. Aida, K. Hata, and T. Someya, Nat. Mater., 8, 494 (2009).
-
T. Sekitani, T. Yokota, U. Zschieschang, H. Klauk, S. Bauer, K. Takeuchi, M. Takamiya, T. Sakurai, and T. Someya, Science, 326, 1516 (2009).
-
M.-Y. Wu, J. Zhao, N. J. Curley, T.-H. Chang, Z. Ma, and M.S. Arnold, J. Appl. Phys., 122, 124901 (2017).
-
N. O. Weiss, H. Zhou, L. Liao, Y. Liu, S. Jiang, Y. Huang, and X. Duan, Adv. Mater., 24, 5782 (2012).
-
-
C. Wang, D. Hwang, Z. Yu, K. Takei, J. Park, T. Chen, B. Ma, and A. Javey., Nat. Mater., 12, 899 (2013).
-
K. Takei, T. Takahashi, J. C. Ho, H. Ko, A. G. Gillies, P. W. Leu, R. S. Fearing, and A. Javey, Nat. Mater., 9, 821 (2010).
-
Y. H. Jung, T. H. Chang, H. Zhang, C. Yao, Q. Zheng, V. W. Yang, H. Mi, M. Kim, S. J. Cho, D. W. Park, H. Jiang, J. Lee, Y. Qiu, W. Zhou,
Z. Cai, S. Gong, and Z. Ma, Nat. Commun., 6, 7170 (2015).
-
Y. Yuan, G. Giri, A. L. Ayzner, A. P. Zoombelt, S. C. Mannsfeld, J. Chen, D. Nordlund, M. F. Toney, J. Huang, and Z. Bao, Nat. Commun., 5, 3005 (2014).
-
A. C. Siegel, S. T. Phillips, B. J. Wiley, and G. M. Whitesides, Lab Chip, 9, 2775 (2009)
-
L. Wang, W. Chen, D. Xu, B. S. Shim, Y. Zhu, F. Sun, L. Liu, C. Peng,
Z. Jin, C. Xu, and N. A. Kotov., Nano Lett., 9, 4147 (2009).
-
J. Lessing, A. C. Glavan, S. B. Walker, C. Keplinger, J. A. Lewis, and
G.M. Whitesides, Adv. Mater., 26, 4677 (2014).
-
J. M. Nassar, K. Mishra, K. Lau, A. A. Aguirre-Pablo, and M. M. Hussain, Adv. Mater. Technol., 2, 1 (2017).
-
J. M. Nassar, M. D. Cordero, A. T. Kutbee, M. A. Karimi, G. A. Torres Sevilla, A. M. Hussain, A. Shamim, and M. M. Hussain, Adv. Mater. Technol., 1, 1600004 (2016)
-
Muhammad M. Hussain, Zhenqiang (Jack) Ma, and Sohail F. Shaikh, ResearchGate, 65 (Winter 2018).
-
L. Xiao et al., Nano Lett. 8, 4539 (2008)
-
L. B. Hu, W. Yuan, P. Brochu, G. Gruner, Q. B. Pei, Appl. Phys. Lett. 94, 161108 (2009).
-
John a. Rogers, Takao Someya and Yonggang Huang, 26 mar 2010, vol 327, issue 5973, DOI: 10.1126/science.1182383
-
Wei Wu (2019) Stretchable electronics: functional materials, fabrication strategies and applications, Science and Technology of Advanced Materials, 20:1, 187-224, DOI: 10.1080/14686996.2018.1549460
-
Noh J-S. Conductive elastomers for stretchable electronics, sensors, and energy harvesters. Polymers. 2016;8:123.
-
Song J, Jiang H, Liu ZJ, et al. Buckling of a stiff thin film on a compliant substrate in large deformation. Int J Solids Struct. 2008;45:3107
-
Sun Y, Choi WM, Jiang H, et al. Controlled buckling of semiconductor nanoribbons for stretchable electronics. Nat Nano. 2006; 1:201.
-
Wang C, Zheng W, Yue Z, et al. Anatomy of a nanoscale conduction channel reveals the mechanism of a high-performance memristor. Adv Mater. 2011;23:3580.
-
Qi Y, Kim J, Nguyen TD, et al. Hot-spot engineering in polygonal nanofinger assemblies for surface-enhanced Raman spectroscopy. Nano Lett. 2011;11:1331.
-
Weng W, Sun Q, Zhang Y, et al. A gum-like lithium-ion battery based on a novel arched structure. Adv Mater. 2015;27:1363.
-
Liu W, Chen J, Chen Z, et al. Stretchable lithium-ion batteries enabled by device-scaled wavy structure and elastic-sticky separator. Adv Energy Mater. 2017;7:1701076.
-
Kim DH, et al. Complementary metal oxide silicon integrated circuits incorporating monolithically integrated stretchable wavy interconnects. Appl Phys Lett. 2008;93(4) Art. ID 044102.
-
Choi WM, Song J, Khang DY, Jiang H, Huang YY, Rogers JA. Biaxially stretchable wavy silicon nanomembranes. Nano Lett. 2007 Jun;7(6):16551663.
-
Jones J Lacour S P Wagner S Suo Z G 2004 J. Vac. Sci. Technol. 22 1723.
-
Su Y, Wang S, Huang Y, et al. Elasticity of fractal inspired interconnects. Small. 2015;11:367.
-
Ma Q, Zhang Y. Mechanics of fractal-inspired horseshoe microstructures for applications in stretchable electronics. J Appl Mech. 2016;83:111008.
-
Yang S, Choi I-S, Kamien RD. Design of super-conformable, foldable materials via fractal cuts and lattice kirigami. MRS Bull. 2016;41:130.
-
Cho Y, Shin J-H, Costa A, et al. Engineering the shape and structure of materials by fractal cut. Proc Nat Acad Sci. 2014;111:17390.
-
Fan JA, Yeo W-H, Su Y, et al. Fractal design concepts for stretchable electronics. Nature Commun. 2014;5:3266.
-
Kim DH, et al. Materials and noncoplanar mesh designs for integrated circuits with linear elastic responses to extreme mechanical deformations. Proc Nat Acad Sci USA. 2008 Dec;105(48):18675 18680.
-
M. T. Tolley, R. F. Shepherd, B. Mosadegh, K. C. Galloway, M. Wehner, M. Karpelson, R. J. Wood, and G. M. Whitesides, Soft Robot., 1, 213 (2014)
-
Hussain, Muhammad & Ma, Jack & Shaikh, Sohail. (2018). Flexible and Stretchable Electronics Progress, Challenges, and Prospects. The Electrochemical Society Interface. 27. 65-69. 10.1149/2.F08184if.
-
S. P. Lacour, G. Courtine, and J. Guck, Nat. Rev. Mater., 1, 16063 (2016).
-
S. M. Khan, A. Gumus, J. M. Nassar, and M. M. Hussain, Adv. Mater., 30, 1705759 (2018).
-
Talbot, David. "A skin patch prototype could someday end reliance on constant finger pricks for people with diabetes". MIT Technology Review. Retrieved 2017-11-08.
-
Wikipedia contributors. (2021, January 24). Stretchable electronics. In Wikipedia, The Free Encyclopedia. Retrieved 14:33, September 28, 2021, from
https://en.wikipedia.org/w/index.php?title=Stetchable_electronics&oldi d=1002457704 For papers published in translation journals, please give the English citation first, followed by the original foreign-language citation[6]