
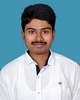
- Open Access
- Authors : Deepak Nelmangala Chandrashekhar , Guntumadugu Girish Raj , Akshay Gowda Nanjunda
- Paper ID : IJERTV10IS050337
- Volume & Issue : Volume 10, Issue 05 (May 2021)
- Published (First Online): 31-05-2021
- ISSN (Online) : 2278-0181
- Publisher Name : IJERT
- License:
This work is licensed under a Creative Commons Attribution 4.0 International License
Properties and Application of Ablative Material
Deepak Nelmangala Chandrashekhar1 Department of Mechanical Engineering RNS Institute of Technology
Bengaluru, India
Guntumadugu Girish Raj2 Department of Mechanical Engineering SJB Institute of Technology Bengaluru, India
Akshay Gowda Nanjunda3
Department of Mechanical Engineering University of Applied Sciences Hochschule Emden Leer
Emden, Germany
AbstractThis In this review paper, we are going to discuss the properties, composites of ablative material, and their application in various departments of engineering (composite names). In the aerospace department, it is used as protecting layer on the surface of the rocket, where it reduces the outcomes of an increase in temperature due to higher heat flux (2000C to 2500C). We have also discussed the stages which it undergoes during the flow of heat, with the understanding of its classification to what type of ablative material is used with the use of other compounds. What would it be like if we would consider an ideal ablative material, with the application and its operation.
Keywords Ablative Material; Aerospace Department; Rockets; Heat Flux; Char Layer; Fiber Reinforcement.
-
INTRODUCTION
This The word ablation is derived from Latin auferre which means Remove, This word describes the absorption, dissipation, and blockage of heat associated with high-speed entry into the atmosphere. [2]
Lets consider the spacecraft re-entry the earth's atmosphere. Re-entry begins at a line known as the Karman line (100 km or 62 miles above from the surface) commonly represents the border between earth atmosphere and outer space where the air Is dense enough to support the aircraft. As the aircraft enters the atmosphere, the speeding spacecraft compresses air in front of it and generates a huge amount of heat which ranges from 2000C to 2500C. These extremely high-temperature conditions may lead to thermal destruction of an exposed vehicle or a component unless suitable protection is provided. Thus ablative, thermal protection materials are used to protect the vehicles from damage during atmospheric re-entry. They are applied to the exterior of a load-bearing structure where it will redirect heat energy into a chemical reaction which causes ablate( Endothermic)and the mechanism is called ablation which helps to dispel the heat and thereby isolating the component or vehicle from the hyperthermal environment.
Ablation is a heat and mass transfer process in which a large amount of heat is dissipated in a very short period with a sacrificial loss of material. Ablation consists of convection, radiation, conduction, and diffusion of chemical species, the need for these materials was first realized during the development of the missile, where the missile failed to reach the target because of the missile skin disintegration caused by
aerodynamic heating. Ablative materials are also used to protect rocket nozzles, Thermal protection systems, and ship hulls from high heat environments.
-
ABLATIVE MECHANISM
Ablative materials are unique where they accommodate virtually high temperature or heat flux conditions and automatically controls the surface temperature by restricting any internal flow of heat and expands energy for each pound of the material. [Figure 1].
Stage 1: Absorption of incident heat Stage 2: Thermal Degradation
Stage 3: Vaporization of organic compounds and leaving residual char layer
Stage 4: Surface Recession
Stage 5: Exposing Fibre Reinforcement.
Figure 1: Stages of Ablative Material [14]
Lets consider the ablative material (Charring material: The charring material are the materials which pyrolyze are the most commonly used material for atmospheric re-entry) most ablative material consist of fibrous composite with organic resins as binders, During the process, ablative material is
subjected to very high heat flux, due to this surface temperature increases rapidly. [7]
When the heat is incident to the surface, it is absorbed and then conducted into the material substrate. The penetration of the takes place at a slower rate due to the lower thermal conductivity of the material. Because of the lower thermal conductivity of the material, surface temperature increases which leads to Thermal degradation (Material changes its property under the influence of high temperature). In Charring ablative material, the heated resin undergoes a decomposition known as pyrolysis which generates gaseous products primarily hydrocarbons. This resin pyrolysis also produces carbonized porous residue called Char. The pyrolysis gases permeate through the char zone remove the additional heat by convection method which moves towards the surface and later injected into the boundary layer, thereby reducing the conduction of the heat underlying the reaction zone. This outgoing gas results in a significant blocking effect on convection heat transfer. Because of pyrolysis, a layer of porous char forms between the outer surface and the pyrolysis zone and it has to withstand high shear stress, which can cause mechanical ablation of the material. Moreover, the chemical reaction between the material of the surface and the chemical species present in the boundary layer may also result in Surface recession. As the layer of the surface erodes the next layer gets exposed and the process continues. [1]
-
CLASSIFICATION OF ABLATIVE MATERIAL Before Ablative materials are classified according to
dominant ablation mechanism. [Figure 2] There are three groups:
-
Subliming and Melting Ablators
-
Charring Ablators
-
Intumescent Ablators.
Figure 2: Shows the physical zones of each
Because of the basic thermal and physical differences, the classes of ablative materials are used in different types of applications.
-
Subliming Or Melting Ablators
Subliming ablators are used as heat sink to protect the vehicles. When the heat flux is incident on this material, the temperature on the surface reaches the melting temperature and this removes the heat from the insulation material. The first subliming ablative materials to be identified was polytetrafluoroethylene Teflon, which offers lightweight, good insulating properties as a result of its decomposition temperature (about 500C), and a high endothermic value for the depolymerization or ablative heat of reaction. Subliming ablators are used for vehicles subject to long term and low altitude exposure.
-
Graphite
Graphite [7782-42-5] sublimes at temperatures as high as 3900 K. monolithic graphite which is used for ablation has a characteristic of high uniform density and small uniform pore size. Pyrolitic graphite offers resistance for laser penetration and has a characteristic of open porosity and very high density.
-
Carbon-Carbon Composites
Carbon-carbon composites are simply described as a carbon fiber reinforcement in one or many directions using a carbon or graphite matrix material. Carbon-carbon composites for rocket nozzles or exit cones are usually made by weaving a 3D preform Composed of radial, axial, and circumferential carbon or graphite fibers to near shape and later densification to high densities. For reusable applications, a silicon carbide- based coating is added to retard oxidation with a boron-based sub-layer to seal any cracks that may form in the coating.
-
Ceramic Ablators
Ceramic ablators have been used or considered for use in dielectric Applications. The material which is designated as – 3DX is a 3Dsilica-fiber-reinforced composite densified with colloidal silica which demonstrates improved mechanical toughness compared to monolithic ceramics. Other dielectric ceramic composites have been used with performance improvements over monolithic ceramics.
-
Charring Ablators
Charring ablators are widely used in a wide range of thermal environments. Compared to subliming or intumescent ablators because of the ability to withstand much higher heat flux. Charring ablators are often used in combination with Subliming and melting ablators. Carbon-phenolic which is known as high-density charring ablators contains high-density reinforcements to improve shear resistance where low-density charring ablators, epoxynovolac resin containing phenolic micro balloons, and silica fiber reinforcement are used only in low shear environments.
-
Cork
Cork is an effective low-cost charring ablator. To reduce moisture absorption and related poor performance, cork particles are often mixed in a silicone or phenolic resin.
-
Wood
Wood is also one of the low-cost charring ablator, where white oak is used as a heat shield for vehicles. It is recommended in place of high-cost material but while considering this safety factor should be very high since there is no easy way to guarantee uniformity.
-
Intumescent Ablators:
-
In this, the material is like foam exposed to heat, due to this the material thickness increases which result in better insulation. When Intumescent Ablators are used the decomposition reaction usually exothermic but inorganic fillers are added to make the reaction endothermic resulting in decreased thermal conductivity and increase specific heat. A typical example of intumescent coating material is CHARTEK 59, a high-performance, lightweight, epoxy-based material from Textron that can be applied by either spray coating or troweling.[3]
-
-
THE IDEAL ABLATIVE MATERIAL
Figure 3: Desired Trends for Ideal Ablative Material [13]
The design spectrum of hyperthermal environments is very large, a single material can't be optimum for all types of environments. Each material exhibits optimum performance characteristics for a specific environment. It thus becomes necessary to develop a wide variety of ablators, which have the collective capability to accommodate the entire design spectrum of hyperthermal environments. [Figure 3]
The ablative material should possess material properties and characteristics which lead to optimum ablative performance and are discussed as follows. [4]
Heat of ablation, the heat of ablation defined as the ability of a material to serve as a heat protection element in a severe thermal environment. The heat of ablation value should be as high as possible to minimize the weight of material required to accommodate the incident flux.
The strength of the ablative material should be high to withstand the mechanical forces of the environment.
Along with it, the ablative material should also have high Enthalpy of phase changes, specific heat, and thermal shock resistance.
A low thermal conductivity is necessary for an ablative material to prevent heat flux from entering the system. The dimensional erosion of the surface should be relatively low, uniform, and predictable. Gaseous species formed by material degradation should be of low molecular weight, and also material should be of lower density.
Surface emittance should approach unity for maximum heat dissipation. Materials that gasify completely exhibit excellent heat blockage; there fore, all of the initial solid material should be converted to gaseous products.
A high ablative temperature is generally desired for conditions involving a very high heating rate. The converse is true for a low heating rate environment.
To summarize, the ablative performance of a material may be altered by many different environmental variables. Careful consideration should therefore be given to each of these factors in determining the performance of a material, and in selecting an ablator for a specific high-temperature environment. [5]
-
ADVANTAGES AND DISADVANTAGES Ablative materials are mainly used as heat protection
systems for outer space vehicles. They are mainly used in aerospace industries due to the unique combination of properties and characteristics offered by the materials. Lets consider the advantages and disadvantages of ablative materials. [6]
-
ADVANTAGES
-
High heat absorption and dissipation
-
Resistance to thermal and mechanical shock
-
Exceptional thermal insulation passive in operation
-
Design, simplicity and flexibility
-
Non strategic materials
-
-
DISADVANTAGES
-
Susceptible to high mechanical forces
-
Service life is time dependent
-
-
-
APPLICATION OF ABLATIVE MATERIALS We have considered two areas where the ablative material is
been considered:
-
Space Craft
-
Passive Fire Protection
-
Space Craft
Ablative material is used in rockets where it is used to withstand huge thermo-mechanical desire because of its high velocity and the friction with the atmosphere. This is also in effect with during the return, the heat fluxes can be very high in the atmosphere, and thus, an adequate thermal protection
system is mandatory to preserve the structure of the vehicle, the payload, and for a manned mission, the crew. [8]
Material chosen are as follows:
-
Carbon Phenolic Ablators
-
Polybenzimidazole (PBI) addition of nano-ZrO2, can overcome Carbon Phenolic Ablators performance
-
Carbon Phenolic Ablators
This is used because of its properties like low densities (from ~0.14 up to ~0.18 g/cm3), low thermal conductivity, the maximum effectiveness in the range of
~1350 to ~2050 W/cm2; and highly effective heat of ablation, both the standard PICA (Phenolic Impregnated Carbon Ablators) and densified PICA offer great weight savings over conventional TPS ablators such as Avcoat 5026, SLA-561, and FRPAs (silica/ or carbon/phenolic composites).
However, due to the limitations of the used arc-jet facility, it was not possible to test PICA at higher stagnation pressures. At a heat flux over 2050 W/cm2, PICA exhibited a surface recession primarily due to the sublimation of carbon-based constituents. [9]
-
Polybenzimidazole
Figure 4: Structure of Polybenzimidazole
-
Properties of Polybenzimidazole and ZrO2
-
Case Study when 10 mg Zirconium dioxide in Polybenzimidazole
-
Thermogravimetric analysis
-
Figure 7: Manufacturing Materials
Figure 7: Manufacturing Materials
Themogravitmetric analysis (TA) or thermal gravimetric analysis (TGA) is a method of thermal analysis in which the mass of a sample is measured over time as the temperature changes. This measurement provides information about physical phenomena, such as phase transitions, absorption, adsorption, and desorption; as well as chemical phenomena including chemisorptions, thermal decomposition, and solid-gas reactions. [figure 6]
Figure 8: TG curves for PBI samples and for PBI + nanoZrO2 samples
Figure 5: Properties of Polybenzimidazole
-
Derivative Thermogravimetry
Derivative Thermogravimetry (DTG) is a type of thermal analysis in which the rate of material weight changes upon heating is plotted against temperature and used to simplify reading the weight versus temperature thermogram peaks that occur close together. [Figure 8]
Zirconium dioxide (ZrO2)
Figure 6: Properties of ZrO2
Figure 9: Rebuilt of the experimental DTG curves with the evaluated activation energies
Figure 10: Activation energy for each steps of reaction for PBI/m-Z
Thermogravimetric analysis on polymer samples was carrie out at different heating rates to observe PBI/m-Z and to appreciate the difference induced by the addition of nanoparticles. Three different peaks were individuated in the DTG curves, thus a three steps reaction was supposed and the three different activation energies. Samples enriched with nanoZrO2 showed higher activation energy for the second and third steps of the reaction, showing that the ceramic nanoparticles can act as thermal degradation stabilizers when added to PBI. [figure 10]
-
-
-
-
Passive Fire Protection
In buildings and construction structures, passive fire protections main purpose is to attempt to contain fires or slow their spread. The fire protection systems usage aims to maintain the temperature of the building component (structural steel element, electrical installation) below the critical temperature during the fire but also is intended to contain a fire in the origin fire compartment for a limited period. The thermal insulation barrier, endothermic building materials including concrete and gypsum, and also novel solution based on alkali- activated binders. Concrete is considered to be fire protective, however, in some specific cases, dense and low permeable concrete (i.e. high-performance concrete) tends to spall explosively under fire. Several fires in structures have caused
cracking of concrete elements that risk the structure stability. Polypropylene fibers (PP) added to the concrete mix act as a passive protection system. Another group of passive fire protection materials, described in this document, are the intumescent and ablative materials for steel structure protection.
The ablative material is made of elastomeric silicone so, if properly designed, they are elastic enough to remain tight on the curved surface as well as are resistant to cracking in the exploitation phase of the structure. According to tests by [11] the 12 mm thickness of ablative coatings can resist fire load for 20 minutes and thus preferred coating thicknesses are approximately applied in the range between 1 mm and 7 mm to provide fire resistance between 30 minutes and 120 minutes. To protect the ablative layer from water and mechanical damage, the non-structural top layer of resin is commonly applied.[10]
Figure 11: Fire scenarios used in laboratory testing done in Germany
In the case of passive protection, there is no need to continue tests longer, if the criteria of insulation are no longer met. Moreover, to determine the effectiveness of passive protection, the test should last as long as it is required for designed purposes. The duration of the test is dependent on considered resistance R, which is defined in the standard [12]: R15, R20, R30, R45, R60, R90, R120, R180, R240, where the number means a minimum period in minutes, which structure should withstand under fire load. The passive protection is considered to be effective if, after a defined time, the structure being protected is not exposed to fire, or the load-bearing properties of the structural component of the testing system are not decreased to an undesirable extent.[Figure 11]
-
-
CONCLUSION
As per the information provided, there is primitive evidence that ablative materials (Charring ablators, Polybenzimidazole with Zirconium dioxide (ZrO2) composite) have been widely used in aerospace industries. This material is considered as the primary material for rocket nozzle and nose tip to protect from the higher heat flux. There is still research conducting on
ablative materials to optimize their properties and to reduce their complexity.
REFERENCES
-
One-Dimensional Thermal Analysis Model for Charring Ablative Materials – Antonio Mazzaracchio
-
Ablation in ECT 2nd ed., Vol. 1, pp. 1121, by I. J. Gruntfest, General Electric Company; Ablative Materials in ECT 3rd ed., Vol. 1, pp. 10 26, by E. R. Stover, P. W. Juneau, Jr., and J. P. Brazel, General Electric Company.
-
Advances in Ablative Composites of Carbon Based Materials: A Review – Colonel Vijay Kumar and Balasubramanian Kandasubramanian.
-
Thermoset Nanocomposites as ablative materials for rocket and military applications – M. Natali, J.M. Kenny, L. Torre.
-
Carbonphenolic ablative materials for re-entry space vehicles: Manufacturing and properties – G. Pulci, J. Tirillò, F. Marra, F. Fossati,
-
Bartuli, T. Valente.
-
-
Low density ablative materials modified by nanoparticles addition: manufacturing and characterization – G. Pulci, L. Paglia, V. Genova, C. Bartuli, T. Valente, F. Marra.
-
Advanced Ablative composites for Aerospace applications – Mohan Kumar.L, Usha. KM, Chakravarthy.PLow density ablative materials modified by nanoparticles addition: manufacturing and characterization
– G. Pulci, L. Paglia, V. Genova, C. Bartuli, T. Valente, F. Marra.
-
Thermochemical characterization of polybenzimidazole with and without nanoZrO2 for ablative materials application – L. Paglia, V. Genova, M. P. Bracciale, C. Bartuli, F. Marra, M. Natali, G. Pulci.
-
Science and technology of polymeric ablative materials for thermal protection systems and propulsion devices: A review by Maurizio Natali, Jose Maria Kenny, LuigiTorre.
-
Material solutions for passive fire protection of buildings and structures and their performances testing – Katarzyna Mróz, Izabela Hager, Kinga Korniejenko.
-
P. Conroy, U. Sorathia, Fireproof barrier system for composite structure, US5270105 A patent, 1993.
-
EN 1363-1:201, Fire resistance tests – Part 1: General Requirements, CEN, 2012.
-
Ablative Material – Copyright _c John Wiley & Sons, Inc.
-
Ablative Material Chairman Mr. H.S Schwartz, Speaker Mr. D.L Schmidt…