
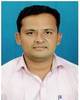
- Open Access
- Authors : S. L. Kadam , R. A. Kadam , M. A. Yewale
- Paper ID : IJERTV9IS020341
- Volume & Issue : Volume 09, Issue 02 (February 2020)
- Published (First Online): 03-03-2020
- ISSN (Online) : 2278-0181
- Publisher Name : IJERT
- License:
This work is licensed under a Creative Commons Attribution 4.0 International License
Preparation and Performance of CuS thin films in Non-Aqueous Medium as Supercapacitor Electrode Materials
S. L. Kadam1, R. A. Kadam2, M. A. Yewale 1, *
1Post Graduation Department of Physics and Research Centre, New Arts, Commerce and Science College, Parner – 414302.
2Department Applied Science, Shri Chhatrapati Shivaji Maharaj College of Engineering Nepti Ahmednagar- 414005
Abstract – In this study, cauliflower microstructure of CuS thin films were prepared by using electrodeposition method for the assembly of supercapacitor application. X -ray diffraction analysis shows their polycrystalline nature and SEM images confirmed their cauliflower microstructure. The investigation of structural, elemental and compositional properties of the CuS thin films were confirmed that the thin films were used as electrode material for supercapacitor applications. As predictable, the synthesized CuS thin films were usefull in different supercapacitor application. The CuS thin films shows specific capacitance (SC) of value102 F g-1 at a scan rate of 10 mV s -1 in a 1 M NaOH electrolyte.
Keywords: Electrodeposition method, nanostructure, supercapacitor, capacitance, contact angle, Electrochemical study.
1. INTRODUCTION
Supercapacitor or electrochemical capacitors are energy storage and passive gadget, which display fast charging rates. The main characteristics of the supercapacitor are maximum power capability, quick charge propagation, charging and discharging response, life cycle, maintenance cost, durability [1]. As compared to the conventional capacitor the supercapacitor have high energy density, due to which equipments have high energy storage capacity and fast charging. Because of these characteristics scientists working in the field of energy storage in supercapacitor have focused on the synthesis of new materials that can be useful to enhance the efficiency of the device. Metal chalcogenide shows crystalline structure and exhibits interest in electronic, optical, electrical and mechanical properties due to these structure. In the previous few decades, diverse materials like carbon nanotubes (CNTs) [2], graphene oxide (GO) [3], metal oxides [4], polymers [5] etc. were tried for supercapacitor application. Also, composites of RGO/MnO2 [6], NiO/CNTs [7], polyaniline/CNTs [8] etc. were ready for more enhancement in the electrochemical supercapacitor performance. The metal sulfides like CoS2 [9], NiS [10], MnS [11], CuS [12], MoS2[13] etc. have expected attention for their exhaustive usage in supercapacitor. Currently copper sulfide (CuS) has been studied for numerous applications like quantum dot solar cell (QDSC) [14], sensors [15], as an electrode for Li-ion battery [16], supercapacitor electrode
-
etc. Copper sulfide have advantages over graphene oxide and metal oxide is their higher conductivity [18] Furthermore, copper based materials shows numerous valence states and ionic chemistry, which marks them a capable candidate for electrochemical applications. CuS is an
associate with chalcogenide material family having different structural properties of attention for the application in supercapacitor [19-20]. Till now, studies on chemical synthesis and supercapacitive properties of CuS film have been infrequent. Present work reports easy-going chemical synthesis of binder free CuS films and its electrochemical supercapacitive performance tested in 1M NaOH electrolyte.
-
EXPERIMENTAL DETAILS
A-Materials:
Copper nitrate Cu(NO3)2, sulfur powder(S), sodium nitrate(NaNO3), dimethyl sulfoxide (CH)SO.
B- Preparation of CuS thin films:
CuS thin films were prepared by using simple three electrode electrodeposition method. For the synthesis of CuS thin film 0.1 M Copper nitrate Cu(NO3)2 were dissolve in dimethyl sulfoxide (CH)SO and 0.1 M of sodium nitrate (NaNO3) and 0.1 M sulfur powder were dissolve in dimethyl sulfoxide (CH)SO. The depositions were performed using above solution and films were deposited for 20 min., the deposition potential was kept 0.9V. Similar process was carried for deposition of CuS thin film for different molar concentration of sulfur. Prepared film were used for further characterization.
-
RESULTS AND DISCUSSION
A- X-ray diffraction (XRD) study:
Fig.1 shows the XRD graph of products synthesized by electrochemical method at different molar concentration of sulfur. When the concentration of sulfur changes from 0.1 M molar to the 0.03 M diffraction peaks of 48.6o variations were observed. The intensity of the peak corresponding to these angle peaks decreases with increase in molar concentration of sulfur. The XRD patterns of the as- synthesised CuS thin films deposited for diverse molar concentrations from bath (a, b, c) with deposition time of 20 min are shown in Fig. 1. Numerous concentrations show the development of polycrystalline CuS structure and they are indexed with JCPDS Card Nos.01-074-1234. To conclude the phases of current cauliflower structure, XRD were used. The XRD of the peaks observed for CuS and the orientation of the plane along (100), (104), (105), (106), (110), (204) and
(214) direction. All of the samples display an analogous XRD pattern, which indicates development of the films in a specific way. Diffraction peaks of other phases or impurities were not observed, further it was observed that the precursors have been totally converted into CuS nanostructures. All the
d values are in much agreement with the theoretical value. From Fig. 1 it is observed that with increasing in molar conc. the peak intensity goes on decreasing shows reduced crystallinity. The crystallite size were calculated by using Scherrers formula. The crystal size decreases with the increase in molar concentration of sulfur in the film composition. Greater the concentrations of sulfur lesser are the crystal size. The crystallite size of the film were changes with change molar concentration of sulfur shown in table 1
Fig. 5 XRD graph of CuS thin films for different concentration of Sulfur.
.
TABLE 1- Variation crystallite size with change in sulfur concentration.
Sr.
No.
Deposition time (min)
Molar concentration of Copper
Molar concentration of
Sulfur
Molar ratio of Cu/S Molar
Crystal size (nm
1.
20
0.1
0.1
1:1
19
2.
20
0.1
0.2
1:2
15
3.
20
0.1
0.3
1:3
09
B-. SEM and EDAX analysis
The surface morphology and structure of CuS samples synthesized by electrochemical method is as shown Fig. 2. The as-grown CuS samples showed small cauliflower
-like morphology. SEM micrographs exposes that the flowers are cluster of numerous small granules. The full array of one small cauliflower structure is observed in this micrograph. These micrograph shows that the sample is uniformly covering the substrate and is composed of dense array of small granules like nanostructures with 0.9 micrometer in diameter. The average diameter of the cauliflower is about
0.70 micrometer. Fig. 3 shows the EDS micro images of the CuS thin films deposited at 0.3 M concentration of sulfur. The samples exposed the presence of Cu and S confirming the formation of the CuS thin films. The atomic percentage of Cu is 51.9% and sulfur is 48.1 %.
<2>C- Wettability study
Fig. 4 shows the wettability of CuS thin film. The wettability study explains the interaction between electrolyte and surface of the thin film. When contact angle of the film were small, the more interaction of the electron with electrode and electrolyte. For small contact angle there is the
probability of transfer of electron from electrolyte to electrode which enhance the charge transfer mechanism. The wettability of CuS thin films show the contact angle of the water with CuS thin film is 970. Small contact angle may more useful to study of supercapacitive behavior.
Fig. 2 SEM micrograph of CuS thin films for 0.3 M concentration of Sulfur.
Fig. 3 EDS spectra of CuS thin films for 0.3 M concentration of Sulfur.
Fig. 4 Contact Angle of CuS thin films.
D- Electrochemical supercapacitive properties
Afterwards the structural, surface morphological and compositional study of the CuS films were confirmed, CV measurements were carried out to more examine the electrochemical supercapacitive properties. CV graph of the
s synthesized CuS electrodes were noted at varying scan [16]
ates of 10-50 mV s-1 within a potential of 1.5 to 1.0 V in a 1
H. Lia, L. Sun, Y. Zhao, T. Tan, Y. Zhang, Applied Surface Science, 466 (2019) 309-319.
[17] M NaOH electrolyte.CV graph of the as synthesized CuS
T.Marimuthu, N.Anandhan, R.Panneerselvam, K.P.Ganesan, A. Amali Roselin, Nano-Structures & Nano-Objects, 17 (2019) 138-147.
lectrodes is as shown in Fig. 5. The specific capacitances of [18]
he electrode were calculated from equation 1. The specific
K. Krishnamoorthy, G.K. Veerasubramani, P. Pazhamalaia, S.J. Kim, Electrochim Acta 190 (2016) 305312.
apacitance of the electrode is 102 F g-1 [19]
.
K. V. G. Raghavendra Chandu V.V. M. Gopi, R.Vinodh, L. K. Durgaa, H. J. Kim, Journal of Energy Storage, 27( 2020), 101148.
[20] M.A.Yewale A.K.Sharma D.B.Kamble C.A.Pawar S.S.Potdar S.C.Karle. Journal of Alloys and Compounds, 754 (2018) 56-63.
s synthesized CuS electrodes were noted at varying scan [16]
ates of 10-50 mV s-1 within a potential of 1.5 to 1.0 V in a 1
H. Lia, L. Sun, Y. Zhao, T. Tan, Y. Zhang, Applied Surface Science, 466 (2019) 309-319.
[17] M NaOH electrolyte.CV graph of the as synthesized CuS
T.Marimuthu, N.Anandhan, R.Panneerselvam, K.P.Ganesan, A. Amali Roselin, Nano-Structures & Nano-Objects, 17 (2019) 138-147.
lectrodes is as shown in Fig. 5. The specific capacitances of [18]
he electrode were calculated from equation 1. The specific
K. Krishnamoorthy, G.K. Veerasubramani, P. Pazhamalaia, S.J. Kim, Electrochim Acta 190 (2016) 305312.
apacitance of the electrode is 102 F g-1 [19]
.
K. V. G. Raghavendra Chandu V.V. M. Gopi, R.Vinodh, L. K. Durgaa, H. J. Kim, Journal of Energy Storage, 27( 2020), 101148.
[20] M.A.Yewale A.K.Sharma D.B.Kamble C.A.Pawar S.S.Potdar S.C.Karle. Journal of Alloys and Compounds, 754 (2018) 56-63.
a r
e t c
Fig. 5 Cyclic Voltammetry of CuS thin films in 1 M NaOH electrolyte
-
CONCLUSIONS
-
In conclusion, advanced CuS thin films were successfully produced by the Electrodeposition method at different molar concentration of sulfur. The electrochemical results exposed that the CuS thin films display good capacitive performance. The surface topography and crystal structure exploration established the development of a cubic polycrystalline nature and the development of different small cauliflower nanostructures on conducting stainless steel substrate of the CuS thin films. The maximum specific capacitance value 102 Fg1 were noted at scan rates of 10 mVs1 in 1 M NaOH electrolyte.
REFERENCE
[1] |
S.K.Shinde, S.M.Mohite, A.A.Kadam, H.M.Yadav, G.S.Ghodake , K.Y.Rajpure D.S.Leee, D. Y.Kim, Journal of Electroanalytical Chemistry, 850 2019, 113433. |
[2] |
S.K. Ujjain, P. Ahuja, R. Bhatia, P. Attri, Mater Res Bull 83 (2016) 167-171. |
[3 |
Q. Yang, S.K. Pang, K.C. Yung, J Power Sources 311(2016) 144- 152. |
[4] |
L. Liu, Y. Luo, W. Tan, Y. Zhang, Fan Liu, G. Qiu, J Colloid Interface Sci 482 (2016) 183-192. |
[5] |
Y. Zhao, C.A. Wang, Mater Des 97 (2016) 512-518 |
[6] |
P.Y. Chan, Rusi, S.R. Majid, Solid State Ionics 262 (2014) 226-229. |
[7] |
G.S. Gund, D.P. Dubal, S.S. Shinde, C.D. Lokhande, ACS Appl Mater Interfaces, 6 (2014) 3176-3188. |
[8] |
X. Wu, Q. Wang, W. Zhang, Y. Wang, W. Chen, Electrochim Acta 211 (2016) 1066-1075. |
[9] |
R.B. Pujari, A.C. Lokhande, J.H. Kim, C.D. Lokhande, RSC Adv, 6 (2016) 40593-40601. |
[10] |
L. Yu, B. Yang. Q. Liu, J. Liu, X. Wang, D. Song, J. Wang, X. Jing, J Electroanal Chem739 (2015) 156-163. |
[11] |
R.B. Pujari, A.C. Lokhande, A.A. Yadav, J.H. Kim, C.D. Lokhande, Mater Des 108 (2016) 510517. |
[12] |
K.J. Huang, J.Z. Zhang, K Xing, Electrochim Acta 149 (2014) 28-33. |
[13] |
M. Wang, H. Fei, P. Zhang, L. Yin, Electrochim Acta 209 (2016) 389-398. |
[14] |
S. S. Kalanur, S. Y. Chae, O. S. Joo, Electrochim Acta 103 (2013) 91-95. |
[15] |
F. A.Sabah, N. M. Ahmed, Z. Hassan, H. S.Rasheed, Sensors and Actuators A: Physical, 249 (2016) 68-76. |