
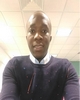
- Open Access
- Authors : Adekanmi Miracle Adeyinka , Mesach O. Olaleke
- Paper ID : IJERTV9IS060885
- Volume & Issue : Volume 09, Issue 06 (June 2020)
- Published (First Online): 03-07-2020
- ISSN (Online) : 2278-0181
- Publisher Name : IJERT
- License:
This work is licensed under a Creative Commons Attribution 4.0 International License
Predictive Model for Thermal Response During Dry Machining of Al 6082-T6 using Fem
Adekanmi Miracle Adeyinkaa* , Mesach O. Olalekeb
Department of Engineering and Mathematics, Sheffield Hallam University, Sheffield, United Kingdom.
Department of Mechanical Engineering, Federal University of Technology Akure, Nigeria.
Abstract:- A significant amount of energy used up during machining is converted into heat due to plastic deformation of the workpiece material and friction generated due to relative motion between the workpiece and tool. This phenomenon tends to induce residual stresses, lower the dimensional accuracy of the job, accelerated wear of the tool and ultimately reduced tool life. This research presents a finite element simulation model to predict the temperature distribution in the cutting zone during orthogonal machining of Al 6082- T6 workpiece using commercially available explicit finite element solver Abaqus. The cutting process was simulated using the Arbitrary Lagrangian-Eulerian (ALE) analysis and adaptive meshing to simulate the plastic flow of material at the tool-tip. The temperature fields in the machining elements, as well as the stress distribution in the chip and workpiece, were determined. The results obtained from the simulation were compared with published results. The results of the study revealed temperature has a significant correlation with the cutting speed and feed rate, thereby validating the proposed FE model.
Keyword: Machining, Finite Element Simulation, Arbitrary Lagrangian-Eulerian, Adaptive meshing.
1.0 INTRODUCTION
Machining is a complex process used for producing spare parts with required geometric properties, surface properties, sub-surface properties and mechanical stability. It is a high strain rate deformation process during which a significant amount of energy consumed is converted into heat due to the plastic deformation of the work material. High temperature experienced at the shear zone is as a result of rubbing action at the tool-chip interface. Research has shown that the heat produced at the primary shear zone is the main factor that influence tool performance and workpiece geometry. This phenomenon tends to induce residual stresses, lower the dimensional accuracy of the job, accelerated wear of the tool and ultimately reduced tool life. This effect is more noticeable when working on materials that are difficult to machine because higher heat is generated. The quest to achieve improved manufacturing quality, better tool performance, cost reduction and optimum cutting conditions have resulted in several pieces of research aimed at better understanding of the machining process. Several experimental methods have been developed to investigate the heat generated during machining, among which the thermocouple method is the most used. Due to the high cost and time constraint associated with experimental optimization approach, there is need to develop cost-effective simulation models desired for process optimisation. Thus, the development and appraisal of a simulation model to predict the heat generated during machining have become important.
Most industrial products and materials used in aerospace and automotive industries are produced through machining process. During machining, high temperatures are generated in the region of the cutting edge, which has a negative influence on the tool life. To prevent the adverse effects of high temperature on workpiece and tool, machinists need to select the cutting conditions carefully. Therefore, the prediction of temperature in the tool and workpiece is important for tool design and the selection of most productive cutting conditions that yields an optimum tool life and minimal residual stresses left on the machined part. Hence, optimum cutting conditions can be obtained through successful finite element simulation for process variables prediction, thereby decreasing the time and cost of experimenting. Analysing investigations from literature revealed that the heat produced at the primary shear zone has not been adequately examined and this fact justifies the research.
This study presents a comprehensive finite element-based simulation for predicting the temperature distribution and material behaviour at the shear zone when machining the Al 6082-T6 workpiece. The research is based on the development of a 2D simulation model representing orthogonal machining of Al 6082-T6 workpiece using tungsten carbide cutting tool. The simulation of the machining process was performed using a commercially available FEA solver Abaqus. This will be accomplished by:
-
developing a two-dimensional finite element simulation model using the thermo-mechanical properties of Al 6082-T6.
-
studying the effect of some process conditions on the interface temperature and stress distribution.
-
validating the simulation model by comparing with data found in reviewed literature.
-
THEORETICAL BACKGROUND
Due to the advancement in manufacturing technology, extensive research attempts have been made to evaluate machining performance through predictive or simulation modelling. Hendri et al. (2010) opined that the need to improve productivity and maintain good quality for machined parts had encouraged several researches committed to studying the effect of machining parameters using a simulation model. The interfacial temperature during machining is an important parameter for predicting the useful life of the tool and surface integrity of the job. Three deformation zones exist during machining viz:
-
The primary shear zone where a significant amount of the energy is changed to heat and the chip is sheared from the metal.
-
The secondary shear zone where the chip sticks and slides over the rake face of the tool and the friction experienced at the tool-chip interface is the main cause of heat in this zone.
-
The tertiary shear zone where the cutting edge of the tool ploughs the workpiece surface and the friction experienced between the new surface and tool causes heat to be generated.
Fig. 1: Heat zones in machining (Haddag et al., 2015)
Heat is generated in all three zones, which increases the temperature of the work material and tool. High temperature in localized tool-tip weakens the tool and causes accelerated tool wear and chipping of the cutting edge (Liu et al., 2002). It also induces residual stresses on the finished surface, which affects the surface integrity and leads to low fatigue strength of the finished part (Jomaa et al., 2014). The generation and dissipation of heat to tool and workpiece is a dynamic process, and as temperature rises, it reaches a steady state. The highest temperature must not exceed the diffusion limits of the binding material to avoid premature chipping of the tool. The diffusion between tool and workpiece at the tool-chip interface caused by elevated temperature is a primary cause of wear. Tool designers use cobalt as a binder for tungsten-carbide tools but at high temperatures, it diffuses into the workpiece material. Hence, thermal analysis of the machining process is essential to improve tool design and ensure higher productivity in the industry.
-
-
Chip Formation and Nomenclature
Metal cutting operations are associated with the cutting edge placed at a certain angle to the direction of cut. Fig. 2a shows that the cutting edge makes 90o with the cutting velocity, known as orthogonal cutting. Fig. 2b shows that the inclination angle is not right angle, known as oblique cutting.
-
(b)
Figure 2: Cutting Operations (a) Orthogonal Machining (b) Oblique Machining (Rao, 2013)
The nature of chips formed depends on the workpiece and tool material along with process conditions. The continuous chip is produced when cutting materials that are ductile such as Al 6082-T6. This can also be produced when machining at small depth and high cutting speed. The merit is that good surface finish results, and less heat will be produced between the tool and chip.
The continuous chip with built-up edges (BUE) is formed under a high friction condition between the tool and chip. BUE will continue to grow but breaks down when unstable. The merit of continuous chip with BUE is that it protects the cutting edge from getting damaged from friction and high temperature, and hence the tool life is increased but rough surface finish results.
Discontinuous chip is formed when the workpiece material undergoes severe strain, causing fracture to take place in the primary heat region when the chip is partially formed. This type of chip is often formed when machining brittle material or when machining materials that are ductile at low speed and high feed.
-
(b) (c)
Figure 3: Types of Chips produced during Machining (a) Continuous chip (b) Continuous chip with build-up edges (c) Discontinuous chip (Rao, 2013)
-
-
-
Effect of high temperature
During machining, the main part of the heat produced is removed by the chips. Therefore, the experiment should be designed so that a significant amount of heat is removed by the chip leaving behind a trivial amount that will not have negative effect on the workpiece and tool. High temperature damages the cutting tool because:
-
Tool wear is accelerated, which affects the tool life.
-
The cutting edges will plastically deform when the tool materials are not as hard as the work. Also, high temperature is unfavourable to the workpiece because:
-
The dimensional accuracy is reduced because of thermal expansion and contraction that takes place during metal cutting.
-
The properties of the workpiece are affected due to residual stress and micro-cracks induced during machining.
-
-
-
Finite element modelling
Three solution methods are usually applied to finite element simulation of machining process viz: Lagrangian formulation, Eulerian formulation, and Arbitrary Lagrangian-Eulerian (ALE) formulation.
-
Lagrangian Formulation
In the Lagrangian formulation, the elements of the mesh deform with the material because the mesh is attached to the material (Vaz et al., 2007). This formulation is most suited for simulating transient process, crack initiation and discontinuous chip formation. However, the major drawback of this formulation is excessive element distortion at the primary deformation zone. Also, the Lagrangian formulation requires the use of chip separation criterion to remove the undeformed chip from the workpiece. The drawback of the formulation can be eliminated by using an updated Lagrangian formulation with mesh adaptivity and automatic re-meshing capability.
-
Eulerian formulation
In Eulerian formulation, the mesh is spatially fixed, and the material flow through the control volume allowing large strains without causing numerical problem (Vaz et al., 2007). Eulerian formulation is not easily adaptable for modelling the free flow of the material as the chip evolves during the process and therefore, cannot simulate serrated and discontinuous chip formation (Rodriquez et al., 2018). This formulation avoids the problem of mesh distortion and can be used for simulating steady-state continuous chip formation process. Therefore, there is no need for chip separation criteria in Eulerian based models. However, the shape of the chip must be determined before the numerical simulation.
-
ALE formulation
The ALE formulation merges the features of pure Lagrangian formulation in which the mesh follows the material and Eulerian formulation analysis in which the mesh is fixed in space, and the material flows through the mesh. This approach can be used to simulate chip formation from incipient to steady-state and does not require chip separation criterion. An advantage of this
technique is the dynamic freedom in defining the mesh configuration (Zouhar & Piska, 2008). ALE formulation is utilized in simulating machining to avoid frequent re-meshing for chip separation. The major disadvantage of this ALE approach is that the chip shape must be determined beforehand and entered into the FEM model (Ozel & Zeren, 2007).
-
Applications of FEM for modelling temperature during machining
Modelling temperature with FE has been gaining relevance since the early 1970s. The early FE models were not entirely independent of experimental data. The finite element method is an efficient tool applied for solving engineering problems such as solid and structural mechanics. Priyadarshini et al. (2012) outlined the advantages of the application of FEM to machining over analytical method as follows:
-
It can be used to measure useful quantities such as stress, strain, temperature, forces, etc
-
It accommodates non-linear geometric boundaries such as the free surface of the chip.
-
The contact between the tool and chip can be modelled as sticking and sliding conditions.
-
Material properties can be modelled as functions of strain, strain rate, and temperature.
Recent FEM codes have the capability of showing strain and stress graphs suitable to obtain optimum cutting conditions without having to conduct the experiment needed. The objective of numerical simulation is to predict cutting forces, temperature, roughness, and residual stresses accurately (Sadeghina et al., 2007). Temperature prediction is a complex task because it is problematic to measure temperature between two bodies in constant relative motion. However, FE simulation is a powerful tool that can overcome this difficulty and can be used for studying the temperature in the shear zone. Developing an accurate temperature prediction model for machining is quite complex but can simplify the actual manufacturing process.
Several researchers have been studying the application of FEM to machining targeted at modelling the thermo-mechanical process of the formation of chip in metal cutting. Tay et al. (1974) were one of the first who modelled the steady-state temperatures of the tool and workpiece during orthogonal cutting. They later revised this model with mechanistic model inputs to decrease the experimental input dependency. Childs et al. (1988) modelled a 2D FE heat conduction model for steady-state conditions to examine the effect of coolant on interface temperature. A Eulerian finite element model was developed by Strenkowski & Moon (1990) to simulate chip formation and evolution during orthogonal cutting. They introduced the concept of chip separation criteria by simulating the cutting process based on the critical value of effective plastic strain and thermomechanical material properties. Shih (1995) developed a FEM model that uses elastic visco-plastic material behaviour with sticking and sliding friction on the rake face. Marusich & Ortiz (1995) modelled orthogonal cutting based on Lagrangian formulation, which served as the basis of commercial machining finite element code AdvantEdge. A thermomechanical model for orthogonal cutting was developed by Wu et al. (1996) utilizing a sticking-sliding friction model.
Commercial finite element codes started finding applications after the late 1990s because of its capability to handle large deformations. They were used to simulate both continuous and interrupted cutting operations. Strenkowski & Carroll (1985) was first to use FEM simulation to analyse the process of the formation of chip using NIKE2D code. A 2D simulation model was set up to study temperature using the updated Lagrangian model utilizing the thermoelastic-plastic properties of the workpiece. Grzesik & Nieslony (2004) developed an analytical model to predict the interface temperature with heat partition using coated and uncoated tool. Akbar et al. (2007) studied the process of formation of chip in metal cutting using FEM and validated the results obtained by the experiment. Abhang & Hameedullah (2010) examined the effect of some cutting conditions on temperature while cutting steel workpiece using thermocouple technique. Advanced FEM was applied by Yogesh & Alan (2003) to simulate machining for estimating tool temperature and cutting forces. Three different materials, 1018CR steel, Al6061-T6 and Ti-6Al- 4V, were tested. They concluded that the friction, chip separation criterion and the extent of thermal contact could play a significant role in defining temperature and deformation fields.
-
-
Johnson-Cook constitutive model
FE modelling of machining involves the application of elastic-plastic and visco-plastic material properties. The JC material model is a frequently used constitutive model for accurately describing material distortion that occurs in the primary and secondary deformation zone. The model is best suited for problems with variable temperature change and strain rates. The JC constitutive model applied in this research is given by equation (1).
= [ + (
(1)
(1)
] [1 + ( )] [1 ( ) ]
)
0
The JC model parameters obtained from the reviewed literature used in this work is given in table 2.
-
JohnsonCook Failure Model
This model will be adopted to initiate the damage to simulate the parting away of the unwanted material from the workpiece. This model is used to define the material failure process for ductile materials based on maximum failure strain which depends on the temperature, strain-rate and stress triaxiality. The J-C failure model contains five failure parameters D, which is used to evaluate the failure strain as given by equation (2). As the value of failure parameter D approaches 1, the element will begin to fail.
= [ + 3] [1 + ( )] [1 +
( )] (2)
1 2
4 0
5
Where = is the stress triaxiality.
The JC failure parameters obtained from the reviewed literature used in this work is given in table 2.
-
Modelling of heat sources in machining processes
The workpiece is plastically deformed under high strain and strain rate conditions during machining. The heat generated at the deformation zones depends on material properties, cutting tool geometry and cutting conditions. The high plastic shear deformation in the primary deformation zone is responsible for the formation of chips. Heat conduction in this deformation zone is neglected during the very first stages of chip formation due to high deformation rates. Hence, the heat generation is assumed to be uniform throughout the shear zone when the chip starts to form. The shearing power is defined as follows:
= (3)
where is the shearing power, is the shearing velocity and is the shear plane area, and is the average shear flow stress. In the primary deformation zone, the average temperature is dependent on work done during metal removal (W), as shown in equation (4).
= +
(4)
Where W is the workdone during metal removal, C is the specific heat capacity, is the mass density of the material and is the ambient temperature.
The secondary deformation zone is characterized by two regions viz: sticking and sliding region. The conversion of frictional energy to heat is greatly responsible for temperature rise in the secondary zone (List et al., 2012). The frictional heat generated in this zone is given by equation (5).
= (1 ) ×
(5)
1 ×
Where is a conversion factor of mechanical energy to heat energy, is the tangential force, is chip velocity, 1 is the contact length and is the fraction of heat moving in the chip.
-
Stress Distribution on the Tool
The ideal stress distribution along the rake face of the tool is shown by an exponential curve in figure 4. Sticking contact occurs near the tool-tip and is influenced by the magnitude of the shear flow stress of the work material which is itself governed by the chip temperature at the tool rake face (Molinari et al., 2011). In the sticking region, a constant shear stress value is assumed. Beyond the sticking zone, the shear stress reduces linearly to zero at the end of the tool-chip contact length. The zone of zero shear stress is called the slipping zone, and Coulombs friction laws are applicable.
Fig. 4: Stress Distribution Curve on the Rake Face of the Cutting Tool
2.9 Friction model
Friction models are needed for simulating the process of chip formation, and it has a direct influence on the stress distribution, force and temperature. The coefficient of friction is the ratio of the cutting force to the normal force on the rake face. The accuracy of the developed model is dependent on the coefficient of sliding friction selected at the interface between the tool and chip. The friction model used in Abaqus subroutine for modelling the problem is the Coulombs law and given by:
In Sticking region
= { 0 < < 1
(6)
In sliding region:
=
<
{ 1 < < 2
3.0 FEM MODEL FORMULATION
In this study, Abaqus/Explicit with Arbitrary Lagrangian-Eulerian (ALE) analysis was employed to conduct the finite element simulation of turning of Al 6082-T6 using tungsten carbide cutting tools. Adaptive meshing was used to model the plastic flow of material at the tool-tip since metal cutting is a dynamic process with significant geometrical change. The explicit dynamic scheme was used because of its computational efficiency. The assumptions used in FE analysis, as presented by Qasim et al. (2015), are:
-
Plane strain conditions were assumed as the cutting width was much larger than the undeformed chip thickness.
-
The tool edge is assumed to be perfectly sharp to keep the simulation as simplified as possible.
The model was set up using the thermo-mechanical properties of the tool and workpiece, as illustrated in Table 1.
The geometric model of the workpiece and tool was created as a 2D representation of orthogonal machining operation. The length and width of 2.5 mm and 1.0 mm respectively were used for the workpiece. It was partitioned at 0.2mm from the top to represent the undeformed chip region. The tool was model as a rectangle with a height of 1 mm with a clearance angle of 7°. The assumption made by Qasim et al. (2015) that the cutting tool is a perfectly rigid body because of its large youngs modulus when compared to that of the workpiece was used. Consequently, for high plastic deformations of the workpiece, small elastic deformations in the tool were taken as negligible. These specifications were used for model validation by comparing with experimental results.
Table 1: Thermo-mechanical properties of the tool and workpiece
S/N |
Parameter |
Al 6082-T6 |
WC tool |
Units |
1 |
Density |
2700 |
12700 |
kg/m3 |
2 |
Youngs Modulus |
70 |
800 |
GPa |
3 |
Poisson ratio |
0.3 |
0.2 |
|
4 |
Specific heat |
894 |
234 |
J/kg/oC |
5 |
Thermal conductivity |
180 |
33. |
W/moC |
6 |
Inelastic heat fraction |
0.9 |
– |
All units used for the FE Model is built with SI (mm) units. The basic material properties of the Al 6082-T6 are shown in table 1. To simulate the material flow and chip formation process, the Johnson-Cook model was employed. The JC model considers the stress required to sustain plastic deformation as a function of strain, strain rate and temperature (Abukhshim et al., 2005). The JC constants of Al 6082-T6 as adapted from Karpat & Ozel (2006) and Chen et al. (2015) are given in table 2.
Setup dynamic coupled temperature-displacement explicit analysis and create a step time of 0.01. Also, configure the analysis procedure and output requests such as nodal temperature (NT11) and average elemental temperature (TEMP). Here, ALE adaptive mesh domain is assigned to the chip formation zone of the workpiece where the material will deform. The ALE adaptive mesh domain defines the portions of a finite element model where mesh movement is independent of material deformation. This characteristic helps to preserve the properties of each node.
Table 2: Johnson-Cook constitutive model constants for Al 6082-T6
Al 6082-T6 |
Value |
A(MPa) |
250 |
B(MPa) |
243.6 |
n |
0.17 |
c |
0.00747 |
Tm(oC) |
582 |
T(oC) |
25 |
m |
1.31 |
D1 |
0.0164 |
D2 |
2.245 |
D3 |
-2.798 |
D4 |
0.007 |
D5 |
3.65 |
A surface-to-surface contact was used to setup the friction contacts between the workpiece and the tool. Researchers have experimentally found the value of coefficients of friction (COF) to be within the range of 0 to 0.5 (Strenkowski & Moon, 1990; Strenkowski & Carroll, 1985) and hence the coefficients of friction () of 0.35 was selected using the penalty contact method.
Table 3: Cutting conditions
Cutting conditions |
Parameter |
Unit |
||
Feed rate |
0.1 |
0.2 |
0.3 |
mm/rev |
Cutting speed |
54 |
80 |
120 |
m/min |
The cutting speed and constrained boundary conditions will be made in agreement with the experiment. The FE simulation will be conducted for the various combinations of the machining parameters used in the experiment. The workpiece was restrained as the tool moves inwards to perform cutting operation, thereby separating the chip from the workpiece (Qasim et al., 2015). The workpiece is made static by restricting motion in all directions. The motion of the tool is constrained in some linear and angular
direction but allowed to travel only in the x-direction. The cutting process is achieved by setting the cutting conditions as presented in table 3, and the direction of motion is shown in figure 6.
Fig. 6: Load & Boundary Conditions applied to the Finite Element Model
An initial temperature of 20oC was assumed as a boundary condition for both the workpiece and the tool. The default value of h for free-air convection is 20W/m2 oC and is assumed to be 20oC as the surrounding temperature is taken as room temperature. The CPE4RT element type, which is a four-node bilinear coupled temperature-displacement element with reduced integration, was applied with element deletion option to allow material separation. Due to high element deformation, the hourglass control was used. A total of 25000 elements were generated for the workpiece and 112 elements for the tool. The schematic diagram for the simulation model is shown in figure 7. The element size in this model was varied between 0.001 to 0.05 because of its influence on the predicted temperature.
4.1 Temperature Distribution
Fig. 7: Schematic diagram of the FE Model
4.0 SIMULATION RESULTS
Heat transfer in metal cutting occurs at the deformation zones due to the plastic deformation of the work material and interfacial friction. The main part of the heat produced is removed by the chips through conduction while some heat is lost to the surrounding through convection. Fig. 8 shows the temperature band when cutting at a speed of 120m/min and feed of 0.3mm/rev. It is evident that the major portion of the heat is carried away by the chip produced. The simulation results at different cutting speeds reveals that an increase in cutting speed will result in a corresponding increase in the temperature, as shown in Fig. 9. This is because an increase in cutting speed will give rise to increased friction, thereby generating more heat at the chip-tool interface.
Fig 8: Temperature effect obtained at step time of 5 × 104 seconds at 120m/min
4.2 Stress Distribution
Figure 10 shows the Von Mises stress distribution at a cutting speed of 120m/min. The primary deformation zone, as indicated by the marked area, is the region with the highest stress concentration. The region is constantly changing as cutting proceeds to imitate the transient nature of the process. There are residual stresses on the machined surface while the stress values decrease around the uncut surface and the deformed chip.
Fig. 9: Graphical representation of the gradual change in temperature with increasing time at 120m/min.
Fig. 10: Stress effect obtained at step time of 5 × 104 seconds at 120m/min
The stress concentration experienced at the primary deformation zone per unit simulation time is shown graphically in Figure
11. The maximum stress of 1.6 kN was attained at 0.00045 step time.
Fig. 11: Stress against simulation time for element set selected in the primary deformation zone at 120m/min
The finite element simulation model that represents the system was developed using the cutting conditions and material properties given in table 1 – 3. Figure 8 shows the simulation result for Al6082-T6 workpiece material at cutting speed of 80 m/min and feed rate of 0.1mm. Under this condition, the feed rate plays a dominant role, possibly due to an increase in the cutting area and removed material volume. Figure 12 shows the graph of temperature values obtained from this study and reviewed literature for the cutting speed range considered. The predicted temperatures obtained from this study were smaller than the literature values; however, the predicted temperatures were in good agreement with the result form literature.
Validation
Validation
400
350
300
250
200
150
100
50
0
400
350
300
250
200
150
100
50
0
54
80
CUTTING SPEED (M/MIN)
120
54
80
CUTTING SPEED (M/MIN)
120
Literature Value Simulation Result
Literature Value Simulation Result
TEMPERATURE (OC)
TEMPERATURE (OC)
Fig. 12: Temperature values obtained from this study and predicted values obtained by Ning & Liang (2018).
5.0 CONCLUSION
A FE simulation model that represents the system was developed using ALE formulation with adaptive meshing capability on Abaqus to predict the effect of cutting conditions on interface temperature. The Johnson-Cook constitutive was employed to simulate material flow around the tool, and Johnson-Cook failure model was used for damage initiation to simulate the parting away of the unwanted material from the workpiece. The simulation result was validated with results from reviewed literature. The simulation results show reaonable agreement with the data from reviewed literature, reflecting the suitability of the ALE formulation for such simulations.
NOMENCLATURE
t uncut chip thickness /depth of cut (m) V cutting speed (m/min)
cross-sectional area (m2)
r chip thickness ratio
shear stress (N/m2)
coefficient of friction
normal stress (N/m2)
f feed rate (mm/rev)
d depth of cut (mm)
thermal conductivity (W/m oC)
h convective heat-transfer coefficient of the workpiece material (W/m2 oC)
mass density of material (kg/m3)
E Youngs modulus of the material (GPa) C specific heat of the material (J/kg/oC)
effective plastic strain rate (1)
0
effective plastic strain reference strain rate (1)
melting temperature (oC)
ambient temperature (oC)
reference temperature (oC)
1 initial failure strain
2 exponential factor
3 triaxiality factor
4 strain rate factor
5 temperature factor
W workdone during metal removal (J)
conversion factor of mechanical energy to heat energy
1 tool-chip sticking zone length (m)
2 tool-chip slipping zone length (m)
fraction of heat moving in the chip
A equivalent plastic strain in Johnson-Cook constitutive model (MPa) B strain related constant in Johnson-Cook constitutive model (MPa)
c strain rate sensitivity constant in Johnson-Cook constitutive model n strain hardening exponent in the Johnson-Cook constitutive model m thermal softening coefficient
REFERENCES
-
Abhang, L., & Hameedullah, M. (2010). Chip-Tool Interface Temperature Prediction Model for Turning Process. Inter. J. Eng. Sci. & Tech., 382-393.
-
Abukhshim, N., Mativenga, P., & Sheikh, M. (2005). Investigation of heat partition in high speed turning of high strength alloy steel. Int. J. Mach. Tools. Manufac., 1687-1695.
-
Akbar, F., Mativenga, P., & Sheikh, M. (2007). An Investigation of the tool-chip interface temperature and heat partition in high-speed machining of AISI/SAE 4140 Steel with TiN-coated tool. Proceedings of the 35th International MATADOR Conference, 215-218.
-
Chen, Y., Li, H., & Wang, J. (2015). Further Development of Oxley's Predictive Force Model for Orthogonal Cutting. Machining Science and Technology, 86-110.
-
Childs, T. C., Maekawa, K., & Maulik, P. (1988). Effect of coolant on temperature dstribution in metal machining. Materials Science and Technology, 1006-1019.
-
Grzesik, W., & Nieslony, P. (2004). Physics based modelling of interface temperatures in machining with multilayer coated tools at moderate cutting speeds. Int. Jou. of Mac Tools & Manufac.
-
Haddag, B., Atlati, S., Nouari, M., & Zenasni, M. (2015). Analysis of the heat transfer at the toolworkpiece interface in machining: determination of heat generation and heat transfer coefficients. In Springer, Heat and Mass transfer (pp. pp 13551370). Springer Berlin Heidelberg.
-
Hendri, Y., Jaharah, G. A., & Che, H. H. (2010). Effect of Rake angle on Stress, Strain and Temperature on the edge of carbide cutting tool in orthogonal cutting using FEM Simulation. ITB J. Eng. Sci., 179-194.
-
Johnson, G. R., & Cook, W. H. (1983). A constitutive model and data for metals subjected to large strains, high strain rates and high temperature. Int. Symp. Ballistics, 541-547.
-
Johnson, G. R., & Cook, W. H. (1985). Fracture characteristics of three metals subjected to various strains, strain rates, temperatures and pressures.
Engineering Fracture Mechanics, 31-48.
-
Jomaa, W., Songmene, V., & Bocher, P. (2014). Surface finish and Residual stresses induced by orthogonal dry machining of AA7075-T651. Materials, 1603-1624.
-
Karpat, Y., & Ozel, T. (2006). Modeling of Orthogonal Cutting Process-Part I: Predictions of Tool Forces, Stresses, and Temperature Distribution.
Transactions of the ASME, 435-444. doi:10.1115/1.2162590
-
List, G., Sutter, G., & Bouthiche, A. (2012). Cutting Temperature Prediction in High Speed Machining by Numerical Modelling of Chip Formation and its dependence with Crater Wear. International Journal of Machine Tools & Manufacture, 1-9.
-
Liu, Z. Q., Ai, X., Zhang, H., Wang, Z. T., & Wan , Y. (2002). Wear patterns and mechanisms of cutting tools in high-speed face milling. Journal of Materials Processing Technology, 222-226.
-
Marusich, T., & Ortiz, M. (1995). Modelling and Simulation of high-speed machining. International Journal of Numerical Methods in Engineering, 3675-3694.
-
Molinari, A., Cheriguene, R., & Miguelez, H. (2011). Numerical and Analytical Modeling of Orthogonal cutting: The link between local variables and global contact characteristics. International Journal of Mechanical Sciences, 183-206.
-
Ning, J., & Liang, S. Y. (2018). Prediction of Temperature Distribution in Orthogonal Machining Based on the Mechanics of the Cutting Process Using a Constitutive Model. Jour. of Manufac. and Mat. Pro., 1-15.
-
Ozel, T., & Zeren, E. (2007). Finite element modeling the influence of edge roundness on the stress and temperature fields induced by high-speed machining. Int. J. Adv. Manuf. Techn., 255-267.
-
Priyadarshini, A., Pal, S. K., & Samantaray, A. K. (2012). Finite Element Modeling of Chip Formation in Orthogonal Machining. Statistical and Computation Techniques in Manufacturing. doi:https://doi.org/10.1007/978-3-642-25859-6_3
-
Qasim, A., Nisar, S., Shah, A., Khalid, M. S., & Sheikh, M. A. (2015). Optimization of process parameters for machining of AISI-1045 steel using Taguchi design and ANOVA. Simulation Modelling Practice and Theory, 36-51.
-
Rao, P. N. (2013). Manufacturing Technology, Metal Cutting and Machine tools.
-
Rodriquez, J. M., Carbonell, J. M., & Jonsen, P. (2018). Numerical Methods for the Modelling of Chip Formation. Arch. Computat. Methods Eng.
-
Sadeghina, H., Razfar, M. R., & Takabi, J. (2007). 2D finite element modeling of face milling with damage effects. 3rd WSEAS International Conference on Applied and Theoretical Mechanics. SPain.
-
Shih, A. J. (1995). Finite Element Simulation of Orthogonal Metal Cutting. Journal of Engineering for Industry, 84-93.
-
Strenkowski, J. S., & Carroll, J. T. (1985). A finite element model of orthogonal metal cutting. ASME Journal of Engineering for Industry, pp. 349-354.
-
Strenkowski, J. S., & Moon, K. J. (1990). Finite Element Prediction of Chip Geometry and Tool/Workpiece Temperature Distributions in Orthogonal Metal Cutting. Journal of Engineering for Industry, 313-318.
-
Tay, A. O., Stevenson, M. G., & Davis, G. D. (1974). Using the finite element method to determine temperature distribution in orthogonal machining.
ARCHIVE: Proceedings of the Institution of Mechanical Engineers, 188, pp. 627-638.
-
Trent, E. M., & Wright, P. K. (2000). Metal Cutting. Boston: Butterworth-Heinemann.
-
Vaz, M., Owen, D. R., Kalhori, V., Lundblad, M., & Lindgren, L. (2007). Modelling and simulation of machining processes. Arch Computer Methods Eng., 173-204.
-
Wu, J. S., Dillion, O. W., & Lu, W. Y. (1996). Thermo-Viscoplastic Modelling of Machining Process Using a Mixed Finite Element Method. Journal of Manufacturing Science and Engineering, 470-482.
-
Yogesh, K., & Alan , T. (2003). Measurments and simulations of temperature and deformation fields in transient metal cutting. J. Manufac. Sci. & Eng., 645-655.
-
Zouhar, J., & Piska, M. (2008). Modelling the orthogonal machining process using cutting tools with different geometry. M. M. Science Journal, 49-52.