
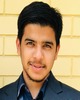
- Open Access
- Authors : Nishkarsha Dawadi , Akkal Bahadur Singh
- Paper ID : IJERTV9IS080277
- Volume & Issue : Volume 09, Issue 08 (August 2020)
- Published (First Online): 29-08-2020
- ISSN (Online) : 2278-0181
- Publisher Name : IJERT
- License:
This work is licensed under a Creative Commons Attribution 4.0 International License
Prediction of Rock Burst, Squeezing and Support Design using Three-Dimensional and Conventional Methods Along Headrace Tunnel in Balephi, Nepal
Nishkarsha Dawadi#1,
#1Student, M.S. in Geotechnical Engineering, Institute of Engineering, Tribhuvan University
Pulchowk, Lalitpur, Nepal
Akkal Bahadur Singh*2
*2Professor, Department of Civil Engineering, Institute of Engineering, Tribhuvan University
Pulchowk, Lalitpur, Nepal
Abstract The prediction of rock burst and squeezing along the headrace tunnel of Upper Balephi A hydropower project is presented in this paper. The rock mass classification along the headrace tunnel at various sections are presented. The assessment of potential rock burst is carried out using methods suggested by various researches and squeezing is predicted using empirical and semi-empirical methods. The support system design of a section in the headrace tunnel and at its junction with an underground vertical surge shaft is also presented. The support system suggested by the empirical RMR and Q- value method is compared with the support system suggested by convergence confinement method and safety factor is checked for the most demanding support system using numerical modeling. Three-dimensional modeling is carried out in sections where the longitudinal homogeneity of stress distribution is disturbed and plain strain condition is not valid. The finite element modeling is done using Phase2 for two-dimensional modeling and GTS NX for three-dimensional modeling at the junction of main tunnel with the surge shaft.
Keywords Tunnel, Rock Mass Classification, Surge Shaft, Tunnel Support, Rock Burst, Squeezing, Empirical Method, Convergence confinement method, Numerical modelling, Three-Dimensional modelling, Phase2, GTS NX, Tunnel Junction
-
INTRODUCTION
Tunnel are underground structure generally used as the shortest mean of conveyance. In Nepal, due to the diverse geography, land form changes within short reach and in case of hydropower, higher head can be achieved in short distances. Thus, tunnel is conveniently used over canal for conveying water to the powerhouse from the intake. While underground excavation itself is a very challenging construction, it also brings along various geological hazards like squeezing and rock burst. So, proper analysis should be made before designing a support system in tunnel. On the other hand, in certain sections in a tunnel like connection with an adit, tunnel bends or underground surge shaft, plain strain condition can no longer be assumed as the longitudinal homogeneity of stress distribution around the tunnel is disturbed and the stress
distribution becomes three-dimensional. Only three- dimensional analysis can suggest accurately, the support system needed in such junctions.
The aim of this paper is to analyse the rock mass properties, to predict rock burst and squeezing along the headrace tunnel of Upper Balephi A hydropower project and to find the required support system at certain sections of major importance. Upper Balephi A is a hydropower project located in Sindhupalchowk district in Nepal, with an installed capacity of 36MW. It has a net head of 197.24m and design discharge of 21.3 m3/s [1].
TABLE I: ROCK MASS PARAMETERS [1]
Chainage (m)
Overburden (m)
RMR
Q-value
0+600
155
70
10
1+400
205
55
3
2+000
590
40
0.8
2+500
345
30
0.066
3+200
145
25
0.003
1+460
(Tunnel Bend)
239
55
3
3+185
(Adit Junction)
170
25
0.003
4+520
(Surge Shaft)
103
45
1
The rock cover, uniaxial compressive strength (UCS), Geological strength index (GSI), Rock Mass Rating (RMR) and Q-value of some sections in the alignment of the Headrace tunnel is given in Table I.
Prediction of ground condition, i.e. Rock Burst and Squeezing is made for first five sections shown in Table I along the tunnel alignment. The section at chainage 2+000 has considerably high overburden, so the design of support system at this section is presented in this paper. Also, the design of connection with the Surge Shaft using three- dimensional modelling is presented in this paper.
-
PREDICTION OF ROCK BURST Approaches suggested by various researchers were used to
access potential rock burst [2] [3]. By making detailed studies for the stability analysis in different tunnels in South Africa, Hoek and Brown suggested a method to access rock burst potential, by using the ratio of uniaxial compressive strength (c) and tangential stress () [2]. Grimstad and Barton also
made a relation by using stress measurements and rock mass strength, which supports the finding of Hoek and Brown [3]. They also used the ratio of uniaxial compressive strength (c) and tangential stress () to describe various conditions of rock bursting potential. These criteria are given in Table II. The tangential stresses in above relations are calculated using the relation proposed by Hoek and Brown [2]. For estimation of the tangential stresses for roof (r) and walls (w) in massive rocks, Hoek and Brown gave the following equations according to the excavation shapes.
r = (A × k 1)
(1)
w = (B k)
(2)
where is for tangential stress (r for roof and w for wall), k is the horizontal/vertical stress ratio, z is the vertical stress and A, B are the excavation geometry factors. The value of A
and B in above equations [2] depend on the shape of the cross section of the tunnel which are given in Figure I. The field stresses calculated for various sections are given in Table III. The detail results on prediction of rock burst based on criteria defined by these researchers are given in Table IV and V.
FIGURE I: VALUE OF A AND B FOR VARIOUS SHAPES OF TUNNEL OPENINGS [2]
TABLE II: CRITERIA DEFINED BY DIFFERENT RESEARCHERS FOR ROCK BURST
Hoek and Brown [2]
Grimstad and Barton [3]
Ratio(c/)
Description
Ratio(c/)
Description
c/ >7
Stable
c/ > 100
Low stress, near surface, open joints
c/ =3.5
Minor sidewall spalling
c/ = 3-100
Medium stress, favorable stress conditions
c/ =2
Severe spalling
c/ = 2-3
High stress, usually favorable to stability, maybe unfavorable to wall stability
c/ =1.7
Heavy support required
c/ = 1.5-2
Moderate slabbing after one hour
c/ <1.4
Severe rock burst problem
c/ = 1-1.5
Slabbing and rock burst after minutes in massive rocks
c/ < 1
/td>
Heavy rock burst and immediate rock deformation
TABLE III: CALCULATION OF FIELD STRESS
Chainage
Maximum rock cover
(H) in m
Poisson Ratio
Tectonic stress, MPa
Unit Weight, MN/m3
Vertical Stress, MPa
Horizontal Stress, MPa
K
c
r
w
0+600
155.00
0.10
3.50
0.027
4.19
3.97
0.70
50
5.19
6.70
1+400
205.00
0.10
3.50
0.027
5.54
4.12
0.60
50
5.09
9.41
2+000
590.00
0.10
3.50
0.027
15.93
5.27
0.40
40
4.46
30.27
2+500
345.00
0.10
3.50
0.026
8.97
4.50
0.40
40
2.51
17.04
3+200
145.00
0.10
3.50
0.026
3.77
3.92
0.70
30
4.67
6.03
TABLE IV: RESULTS OF ROCK BURST ASSESSMENT USING HOEK AND BROWN'S APPROACH
Chainage
For Roof
For Wall
c/r
Prediction
c/w
Prediction
0+600
9.64
Stable
7.47
Stable
1+400
9.82
Stable
5.31
Minor Sidewall Spalling
2+000
8.97
Stable
1.32
Heavy support required
2+500
15.93
Stable
2.35
Minor Sidewall Spalling
3+200
6.42
Minor sidewall spalling
4.97
Minor Sidewall Spalling
TABLE V: RESULTS OF ROCK BURST ASSESSMENT USING GRIMSTAD AND BARTONS APPROACH
Chainage
c/r
c/w
0+600
9.64
Medium Stress, favorable stress condition
7.47
Medium Stress, favorable stress condition
1+400
9.82
Medium Stress, favorable stress condition
5.31
Medium Stress, favorable stress condition
2+000
8.97
Medium Stress, favorable stress condition
1.32
Slabbing and rock burst after minutes in massive rocks
2+500
15.93
Medium Stress, favorable stress condition
2.35
High stress, usually favorable to stability, maybe unfavorable to wall stability
3+200
6.42
Medium Stress, favorable stress condition
4.97
Medium Stress, favorable stress condition
Chainage
c/r
c/w
0+600
9.64
Medium Stress, favorable stress condition
7.47
Medium Stress, favorable stress condition
1+400
9.82
Medium Stress, favorable stress condition
5.31
Medium Stress, favorable stress condition
2+000
8.97
Medium Stress, favorable stress condition
1.32
Slabbing and rock burst after minutes in massive rocks
2+500
15.93
Medium Stress, favorable stress condition
2.35
High stress, usually favorable to stability, maybe unfavorable to wall stability
3+200
6.42
Medium Stress, favorable stress condition
4.97
Medium Stress, favorable stress condition
For Roof
Prediction
Prediction
For Wall
-
PREDICTION OF SQUEEZING Assessment of potential squeezing was made using
tunneling quality index values. Empirical and Semi-empirical methods were used. By using Bartons Q-value and overburden in the tunnel, Singh et al. [4] in 1992 developed an empirical equation to predict squeezing in rocks. Goel et al. [5] also developed an equation based on rock mass number
(Q-value for SRF = 1), overburden and width of the tunnel. The suggested equations and squeezing conditions by various methods are given below in Table VI.
TABLE VI: SQUEEZING CONDITIONS AS PER VARIOUS EMPIRICAL METHODS [4] [5]
Method
Squeezing condition
Non-squeezing condition
Singh et al.
(1992)
H > 350 Q 1/3
meters
H < 350 Q 1/3
meters
Goel et al. (1994)
H > (275 N 0.33) B-0.1 meters
H > (275 N 0.33) B-0.1 meters
A semi-empirical approach suggested by Hoek and Marinos 2000 [6] was also used to check squeezing in tunnel. It is based on the ratio of uniaxial compressive strength and the in-situ stress. They used Sakurai 1983 [7] approach to determine the relationship between cm/po and the percentage strain of the tunnel. Hoek and Marinos [6] also suggested the classifications of squeezing severity based on the strain percentage. There are five classes of squeezing problems from few support problems to extreme squeezing problems i.e.; from A to E. The ranges of these classes are shown in Figure II.
FIGURE II: APPROXIMATE RELATIONSHIP AND THE DEGREE OF DIFFICULTY ASSOCIATED WITH TUNNELING THROUGH SQUEEZING IN ROCK IN CASE OF UNSUPPORTED TUNNEL [6]
TABLE VII: RESULTS OF ASSESSMENT OF SQUEEZING USING EMPIRICAL METHODS
Chainage (m)
Overburden
RMR
Q
Value
N value SRF=1
Singh 1992
Goel 1994
Check
350Q1/3
275N0.33
×B-0.1
Singh
Goel
0+600
155
70
10
700
754.05
511.83
Non-Squeezing
Non-Squeezing
0+1400
205
55
3
165
504.78
344.01
Non-Squeezing
Non-Squeezing
0+2000
590
40
0.8
32
324.91
222.40
Squeezing
Squeezing
0+2500
345
30
0.066
1.98
141.44
97.62
Squeezing
Squeezing
0+3200
145
25
0.003
0.075
50.47
35.20
Squeezing
Squeezing
TABLE VIII: RESULTS OF ASSESSMENT OF SQUEEZING USING SEMI-EMPIRICAL METHOD BY HOEK AND MARINOS (2000)
Chainage
Overburden
UCS
Tunnel Diameter (m)
Tunnel Closure (m)
Strain without support,
Squeezing condition
0+600
155
50
4
0.0008
0.02%
Few Support Problems
0+1400
205
50
4
0.004
0.1%
Few Support Problems
0+2000
590
40
4
0.25
6.25%
Very severe squeezing problems
0+2500
345
40
4
0.23
5.75%
Very severe squeezing problems
0+3200
145
30
4
0.14
3.5%
Severe squeezing problems
The results of assessment of squeezing using methods suggested by Singh et al. (1992) and Goel et al. (1994) are given in Table VII. The results based on semi-empirical method suggested by Hoek and Marinos (2000) is given in Table VIII.
Method
RMR
Q-system
Bolts
End anchored, 20mm diameter, systematic bolts 4- 5 m long, spaced 1-1.5 m in crown and walls with wire mesh.
25mm diameter, 2.5m long grouted rock bolts @ 1.3 x 1.5m spacing.
Shotcrete
100-150 mm in crown and 100 mm in sides.
10 cm thick steel fibre reinforced shotcrete
Steel Sets
Light to medium ribs spaced
1.5 m where required.
None
Method
RMR
Q-system
Bolts
End anchored, 20mm diameter, systematic bolts 4- 5 m long, spaced 1-1.5 m in crown and walls with wire mesh.
25mm diameter, 2.5m long grouted rock bolts @ 1.3 x 1.5m spacing.
Shotcrete
100-150 mm in crown and 100 mm in sides.
10 cm thick steel fibre reinforced shotcrete
Steel Sets
Light to medium ribs spaced
1.5 m where required.
None
TABLE IX: SUPPORT SUGGESTED BY EMPIRICAL METHODS [8] [9]
-
DESIGN OF SUPPORT SYSTEM
-
Support System Design Using Empirical Methods Support system for section at chainage 2+000 was carried out using Q-system [8] and RMR [9] method. RMR system classifies the rock at this section as Poor rock while Q-system classifies it as very poor rock. The support suggested by these two methods are given in table below.
-
Support System Design Using Analytical Method Convergence confinement method was used for analytical design of the support system. Carranza, Torres and Fairhurst put forward three terms in CCM [10].
-
Longitudinal displacement profile
LDP represents the graph of the radial displacement that occurs along the axis of a cylindrical tunnel for sections ahead and behind the excavation face. Vlachopoulos and Diederichs in 2009 proposed a set of best fit relationships [11], and those equations have been used in this study for construction of GRC and LDP.
-
Ground Reaction Curve
GRC is the graphical representation of decreasing internal pressure plotted against increasing radial displacement of tunnel wall. This relationship is obtained from the elasto- plastic solution of deformation of rock around an excavation.
And the stiffness
is given by:
1 = s s [ 4l + ]
Ks c l db Es
(6)
is given by:
1 = s s [ 4l + ]
Ks c l db Es
(6)
Where,
db is the bolt or cable diameter (m),
l is the free length of bolt or cable (m),
Tbf is the ultimate load obtained from a pull-out test (MN),
Q is a deformation load constant for the anchor and head (m/MN),
Es is Youngs modulus of bolt or cable (MPa), Sc is the circumferential bolt spacing (m), and Sl is the longitudinal bolt spacing (m)
-
Steel Sets:
pmax = Asy s scR
K = E
(7)
pmax = Asy s scR
K = E
(7)
The maximum support pressure of the set is:
And the stiffness is:
3. Support Characteristics Curve
SCC is the relationship between stress on the support and the
Where,
SR2
(8)
radial displacement of the support.
Calculation of support strength:
-
Shotcrete lining:
The maximum support that is provided by shotcrete lining can be calculated by the using the theory of hollow cylinders.
cc (R tc)2 pmax = [1 ] s 2 R2
(3)
The stiffness constant Ks is as follows:
Ec R2 (R tc)2
Ks = (1 )R (1 )R2 + (R t )2
C C c
(4)
Where,
Ec elastic modulus of concrete, c is Poissons ratio,
R is external radius of tunnel (m),
tc is thickness of the concrete or shotcrete, and
cc is unconfined compressive strength of the shotcrete or concrete
-
Rock Bolts:
If the circumferential spacing of the bolts are assumed to be equal, the maximum support provided by rock bolts is given by:
ys is yield strength of steel (MPa),
Es is the Youngs modulus of the steel (MPa), As is the cross-sectional area of the section (m),
Sl is the set spacing along the tunnel axis(m), and R is the radius of the tunnel (m)
4. Combined system:
In this case, the stiffness of the combined system is determined as the sum of the stiffness of the individual components.
K = K1 + K2
(9)
Where, K1= stiffness of the first system, and K2= stiffness of the second system.
The GRC, LDP and SCC were prepared for the section 2+000 and by providing 150mm Shotcrete of UCS 25Mpa, End anchored Rock Bolts 25mm diameter and 2.5m long, a FOS of 2.33 was obtained.
Combined elastic stiffness (Ksb)
1561.63 MPa/m
Maximum displacement (ur)
0.0015 m
Maximum support pressure (Psbmx)
2.311 MPa
Combined elastic stiffness (Ksb)
1561.63 MPa/m
Maximum displacement (ur)
0.0015 m
Maximum support pressure (Psbmx)
2.311 MPa
TABLE X: CHARACTERISTIC PROPERTIES OF SUPPORT SYSTEM
pmax = Tbf s scsl
(5)
Combined SCC GRC LDP
18
16
Internal Pressure, pi (MPa)
Internal Pressure, pi (MPa)
14
12
10
8
6
4
2
0
140.00
120.00
Distance to the face, X (m)
Distance to the face, X (m)
100.00
80.00
60.00
40.00
20.00
0.00
-20.00
0.000 0.00 0.100 0.150 0.200 0.250 0.300
Total Displacement, ur (m)
FIGURE III: GRC, LDP AND SCC FOR SECTION 2+000
-
-
-
Two-dimensional Numerical Modelling using Phase2 Finite Element Method is the most widely employed numerical method for rock mechanics and rock engineering. It does not require detailed programming experience to make efficient use of the finite element approach to problem solving in rock mechanics. However, familiarity with the fundamentals of the technique and with practical guidelines for generating reliable results is essential not only for the preparation of the program input, but also for recognition of faulty output.
The Phase2 [12] is a 2-dimensional FEM based program and is very popular for the analysis of underground/surface excavation in rock mass or soil. In this research, the support system for tunnel section at chainage 2+000 is also carried out using two-dimensional Numerical Modelling.
Rock Mass Property
Values
Rock Type
Schist
Poissons Ratio
0.1
ci (MPa)
40
mi
10
GSI
35
i M
400
mb
0.453
s
0.0001722
0.5159
27
urd
590
Rock Mass Property
Values
Rock Type
Schist
Poissons Ratio
0.1
ci (MPa)
40
mi
10
GSI
35
i M
400
mb
0.453
s
0.0001722
0.5159
27
urd
590
TABLE XI: INPUT PARAMETERS FOR TWO-DIMENSIONAL NUMERICAL MODELLING
D 0.5
E ( Pa) 3 0
a
Unit Weight (KN/m3) Overb en (m)
Hoek and Brown criterion was used to carry out nonlinear
analysis. The Hoek-Brown constant are determined as follows:
mb = mi exp (GSI100
)
2814D
(10)
s = exp (GSI100
)
93D
(11)
a= 1 + 1(eGSI/15- e20/3) 2 6
(12)
The total closure of the tunnel in unsupported condition was found to be 0.216m. The radius of plastic zone was 9.02m. The ratio of distance from tunnel face to tunnel radius (X/Rt) was 2 and plastic zone to tunnel radius (Rt/Rp) was 4.51. Vlachopoulos and Diederichs method was used to determine the ratio of closure to maximum closure which was found to be 0.44. Therefore, the closure equaled 0.096 m. This was about 44% of the total closure of 0.216 m. This meant that 44% of deformation will already have taken place before the support can be installed. An Internal pressure factor of 0.02 yield the tunnel wall displacement computed above for the point of support installation.
The support system used in numerical modelling is given in Table XII.
TABLE XII: SUPPORT ANALYSED USING TWO-DIMENSIONAL NUMERICAL MODELLING
Rock Bolts
Shotcrete
Type
End Anchored
UCS
25Mpa
Length
2.5m
Youngs Modulus
25000 MPa
Diameter
25 mm
Thickness of shotcrete
200mm
Bolt Modulus
2 × 105 MPa
Poissons Ratio
0.2
Out of Plane Spacing
1.5 m
Tensile Strength
3.5 MPa
For factor of safety of 1.0,1.5 and 2.0, safety envelopes of axial force vs moment space and axial force vs shear force space were generated. It can be seen from Figure IV that the values of axial force, moment and shear force in the liners, when compared to the capacity envelope, lie inside the curve of FOS of 2.0. Also, there was no yielding in the rock bolts and lines which can be seen in Figure V.
FIGURE IV: SAFETY ENVELOPE FOR FOS 1, 1.5 AND 2.0
FIGURE V: TOTAL DISPLACEMENT AROUND TUNNEL WITH SUPPORT AND FORCES ON LINER AND BOLTS
-
Three-Dimensional Modelling using GTS-NX
Like any numerical modeling, three-dimensional modeling requires a control volume in which analysis is to be made. But in case of 3D-modeling a control volume with all three dimensions has to be selected. Keeping in mind the solution of a circular hole on a metal plate given by Kirsch, it is known that in case of elastic bodies the stress due to excavation dies out at a distance of 3-5 from the center of excavation. But the rock masses in which the tunnel under consideration is being excavated shows elasto-plastic nature so, plastic zone has to be considered. Hence, geometric model with control volume of dimensions ten to twenty times that of tunnel diameter was created for analysis in this research work.
GTS-NX [13] was used to carry out three-dimensional analysis on selected zones where the longitudinal homogeneity of the tunnel breaks due to presence of additional excavations. One of such three-dimensional design of support system for the headrace tunnel surge shaft junction is presented in this paper.
The geometric model was prepared considering the symmetry plane passing vertically through the axis of the main tunnel. The material model is restricted in translation at the four faces in the sides along the direction perpendicular to those faces and is restricted for translation along all three axes at the bottom face. The upper face of the model is free to move in all three direction.
This analysis is carried out using a non-linear analysis based on Generalized Hoek-Brown criterion. The tolerance is kept at 0.001 for load and 1e-06 for work done. Newton- Raphson method was used to solve the non-linear equations at created nodes. Tunnel closure was found to be 30mm.
Figure VI shows the maximum shear stress imposed on the shotcrete lining. The stress is maximum at the junction of the surge shaft with the main tunnel. This stress has increased from top to bottom of the surge shaft as the vertical in-situ stress goes on increasing. The maximum shear strength of shotcrete of 100mm thickness for a tunnel radius diameter of 4m is 1.219 MPa, obtained by using properties of hollow cylinder. Here, the maximum shear stress induced is 0.511 MPa. This gives a minimum factor of safety of 2.38 at the
junction. Since, the factor of safety is above two, this can be considered safe.
TABLE XIII: SUPPORT SYSTEM ANALYSED USING THREE-DIMENSIONAL MODELLING
Rock Bolts
Shotcrete
Type, Model
1D, Embedded Truss
Type, Model
2D, Shell
Length
In Main-Tunnel
2.5m
Poissons Ratio
0.2
In Surge Shaft
4m
Compressive Strength
25MPa
Poissons Ratio
0.25
Tensile Strength
3.5MPa
Spacing (In-plane, Out of plane)
1m, 1.5m
Thickness
0.1m
Section Shape
Slid Round
Youngs Modulus
25000MPa
Diameter
0.025m
Unit Weight
24 KN/m3
Tensile capacity
0.1MN
Bolt Modulus
200000 MPa
FIGURE VI: MAXIMUM SHEAR STRESS IN SHOTCRETE AROUND SURGE SHAFT
FIGURE VII: AXIAL FORCE IN ROCK BOLTS AT THE JUNCTION OF MAIN TUNNEL AND SURGE SHAFT
Figure VII shows the axial force in the rock bolts in the periphery of the surge shaft. Here, it can be seen that the axial force is maximum at the junction of Main Tunnel with the Surge Shaft, near the flat invert of the tunnel.
The maximum tensile capacity of the bolt used is 0.1MN,
i.e. 100 KN. The maximum axial force induced in the Rock Bolt here is 53.3 KN. This gives factor of safety of 1.87 at the junction. Considering the junction is lined using concrete panel, this value of safety factor is safe.
-
-
CONCLUSIONS
In this study, rock mass classification, prediction of rock burst and prediction of squeezing was assessed at five different sections along the 4m diameter D-shaped headrace tunnel of Upper Balephi A hydropower in Sindhupalchowk, Nepal. Support system was designed for a section at chainage 2+000 using empirical, analytical and two-dimensional numerical modeling. Three-dimensional modeling was used to predict the support required at the junction of the tunnel with an underground vertical surge shaft of diameter 8m. Upon comparison with criteria suggested by various researchers, it was found that even though the rock mass at the first two sections were hard rocks types shown by the high RMR value, they were stable against Rock Burst. But the sections at chainage 2+000 and 2+500 were found to possess chances og rock bursting. The Hoek and Brown approach suggested requirement of heavy support at the wall in section 2+000 while minor wall spalling in section 1+400, 2+500 and 3+200. This is mostly due to the D-shape of the tunnel as there will be high stress induced at the corners in the invert level. The Grimstad and Barton method suggested that at section 2+500, the stress is very high which is usually favorable for overall stability but that it can be unfavorable for wall stability. Again, this is due to the high stress induced at the corners of the invert. It also suggested that in the wall of the section 2+000, slabbing and rock burst will occur after minutes in case of massive rocks. The empirical and semi-empirical methods suggested that there will be no squeezing at the first two sections. However, it was found that there is probability of
squeezing in three sections at chainage 0+2000, 2+500 and 3+200m, which were also found to be susceptible to rock burst. But since the rock type is weak at these three sections, squeezing poseses the major threat rather than rock burst. For further analysis, detailed study will be required with subsurface drilling data. So, while providing supports, precautions against squeezing should be taken at the later three sections. Two-dimensional analysis is sufficient for analysis of stress distribution and design of support system in sections where plain strain conditions can be assumed like in section 2+000, but in places where the longitudinal symmetry breaks and stress varies along the longitudinal direction, only three-dimensional approach can give accurate results. Most of the designs today involving tunnel junctions with adit, with surge shaft or in cases of bends in the tunnel are made using empirical methods assuming conservative design with high factor of safety. But this might turn out to be uneconomical and three-dimensional modelling can give the most accurate estimation in such cases as shown in this study.
ACKNOWLEDGMENT
The authors are thankful to Department of Civil Engineering, Institute of Engineering, Tribhuvan University for providing the opportunity to carry out this study. The author wishes to acknowledge M.Sc. Program Co-ordinator Associate Professor Dr. Indra Prasad Acharya for his invaluable suggestions and encouragement during the research. The authors are obliged to all colleagues, family and friends who helped in this study.
REFERENCES
[1] |
Report on Rock Support Analysis of Underground Excavation, Kathmandu, Nepal, 2017. |
[2] |
Hoek and Brown, Underground Excavation in rock, Institution of Mining and Metallurgy, 1980. |
[3] |
E. Grimstad and N. Barton, Updating the Q-system for NMT, Proceedings of the international symposium on sprayed concrete, Norwegian concrete assosiation, Oslo, Norway, 1993. |
[4] |
B. Singh, J. L. Jethwa and A. K. Dube, Correlation between [10] Carranza, Torres and Fairhust, Application of the convergence- Observed Support Pressure and Rock Mass Quantity, Tunnelling confinement method of tunnel design to rock masses that satisfy the and Underground Space Technology, 1992. Hoek-Brown failure criterion, Tunneling and Underground Space |
[5] |
R. K. Goel, J. L. Jethwa and A. G. Paithankar, Indian Experiences Technology, pp. 187-213, 2000. with Q and RMR Systems, Tunneling and Underground Space [11] N. Vlachopoulos and M. Diederichs, Improved Longitudnal Technology, 1995. Displacement Profiles for Convergence Confinment Analysis of |
[6] |
E. Hoek and P. Marinos, Predicting tunnel squeezing problems in Deep Tunnels, Rock Mechanics and Rock Engineering, 2009. weak heterogeneous rock masses, Tunnels and Tunnelling [12] R. Inc., Phase2 model program reference manual, [Online]. International, 2000. Available: |
[7] |
S. Sakurai, Displacement measurements associated with the design https://www.rocscience.com/downloads/phase2/Phase2_ModelRefer of underground openings, Proc. Int. Symp. Field Measurements in ence.pdf. Geomechanics., 1983. [13] Product Announcement GTS NX 2019 (v2.1), Midas IT Co. Ltd., |
[8] |
N. Barton and E. Grimstad, Forty years with the Q-system in 2019. [Online]. Available: Norway and Abroad, GEOTEKNIKK, 2014. https://www.midasgeotech.com/blog/new_release_of_midas_gtsnx_ |
[9] |
Kaisier et al., Evaluation of rock classification at B.C Rail tumbler ridge tunnels., Rock Mechanics and Rock Engineering, 1986. |
[4] |
B. Singh, J. L. Jethwa and A. K. Dube, Correlation between [10] Carranza, Torres and Fairhust, Application of the convergence- Observed Support Pressure and Rock Mass Quantity, Tunnelling confinement method of tunnel design to rock masses that satisfy the and Underground Space Technology, 1992. Hoek-Brown failure criterion, Tunneling and Underground Space |
[5] |
R. K. Goel, J. L. Jethwa and A. G. Paithankar, Indian Experiences Technology, pp. 187-213, 2000. with Q and RMR Systems, Tunneling and Underground Space [11] N. Vlachopoulos and M. Diederichs, Improved Longitudnal Technology, 1995. Displacement Profiles for Convergence Confinment Analysis of |
[6] |
E. Hoek and P. Marinos, Predicting tunnel squeezing problems in Deep Tunnels, Rock Mechanics and Rock Engineering, 2009. weak heterogeneous rock masses, Tunnels and Tunnelling [12] R. Inc., Phase2 model program reference manual, [Online]. International, 2000. Available: |
[7] |
S. Sakurai, Displacement measurements associated with the design https://www.rocscience.com/downloads/phase2/Phase2_ModelRefer of underground openings, Proc. Int. Symp. Field Measurements in ence.pdf. Geomechanics., 1983. [13] Product Announcement GTSNX 2019 (v2.1), Midas IT Co. Ltd., |
[8] |
N. Barton and E. Grimstad, Forty years with the Q-system in 2019. [Online]. Available: Norway and Abroad, GEOTEKNIKK, 2014. https://www.midasgeotech.com/blog/new_release_of_midas_gtsnx_ |
[9] |
Kaisier et al., Evaluation of rock classification at B.C Rail tumbler ridge tunnels., Rock Mechanics and Rock Engineering, 1986. |
2019v2.1#none.