
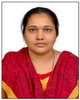
- Open Access
- Authors : P G K Aruna , Banda Sai Kishore
- Paper ID : IJERTV10IS110112
- Volume & Issue : Volume 10, Issue 11 (November 2021)
- Published (First Online): 25-11-2021
- ISSN (Online) : 2278-0181
- Publisher Name : IJERT
- License:
This work is licensed under a Creative Commons Attribution 4.0 International License
Performance of Induction Motor driven by Three Level Neutral Clamped Inverter using Space Vector Modulation as Voltage Control Technique
P G K Aruna1
1Assistant Professor, Department of EEE, Malla Reddy University,
Hyderabad, Telangana, India 500075.
Banda Sai Kishore2
2UG Scholar, Department of EEE, Mahatma Gandhi Institute of Technology, Hyderabad,
Telangana, India 500043.
Abstract – This paper deals with the performance of Induction Motor which is driven by a three-level neutral clamped inverter using space vector modulation technique as voltage control strategy. SVM has increasing applications in power converters and motor control. Compared to other modulation techniques, space vector modulation technique has the advantages like higher modulation index, utilizing DC bus voltage more effectively, generating less THD and thus less harmonics and low ripple content. In this paper, DC voltage is given as input to the three-level neutral clamped Inverter. This inverter has been designed and implemented in MATLAB/SIMULINK software. IGBTs are used as active switches. The triggering pulses to these IGBTs are given by using space vector modulation technique. By selecting proper switching states and by calculating the time-period in particular switching state AC voltage with less THD, low dV/dt is obtained as output. AC output of this inverter is given as input to the Induction Motor. After simulating, the output parameters of induction motor like torque, speed, load current is studied.
Keywords: Induction Motor (IM), Neutral Clamped Inverter (NCI), Space Vector Modulation Technique (SVM), Total Hormonic Distortion (THD).
-
INTRODUCTION
Multilevel inverters are gaining importance in high power and high voltage applications like manufacturing industry, transportation, renewable energy and in reactive power compensation due to their superior performance compared to two-level inverters. If we use two-level inverters in high voltage and high-power applications, the rate of rise of voltage (dV/dt) is significantly high, the switching losses will be more and also there will be constraints of device rating [1]. Hence, Multilevel Inverters are becoming popular which produce high power, high voltages without requiring transformers or higher rating individual devices. Multilevel Inverters produce higher level voltages with low dV/dt, low hormonic content and low ripple content [3]. The only disadvantage of this technique is that by increasing the levels, the number of switches will increase, and the switching combination will become complex and control will become complicated and expensive [9]. Its various applications are in Renewable DC source utilization, Uninterruptible Power Supplies (UPS), Power Transmission through high voltage DC (HVDC), Variable frequency drives and electrical vehicle drives [1]. The multilevel inverters are classified into three types:
-
Neutral clamped multilevel inverter
-
Flying-capacitors multilevel inverter
-
Cascade H-Bridge multilevel inverter.
-
-
NEUTRAL CLAMPED MULTILEVEL
INVERTER
Neutral clamped multilevel inverter is also known as Diode clamped multilevel inverter. Circuit diagram of a three-level neutral clamped inverter is shown in the Fig.1. In m level inverter with one leg consists of (m-1) dc bus capacitors, (m-1) (m-2) clamping diodes and 2(m-1) main switching devices. Thus, a 3-level neutral clamped inverter with one leg consists of 2 dc bus capacitors, 2 clamping diodes and 4 main switching devices. There fore, for a 3- phase, 3-level neutral clamped inverters there are 2 dc bus capacitors, 6 midpoint clamping diodes, 12 main switching devices [1], [4], [5]. Table.I shows the switching states of three-level inverter. Each phase has three output states, P, O, and N, corresponding to positive voltage (+), zero voltage (0), and negative voltage (-). Take phase a as an example, if switch Sa1 and Sa2 are turned on, then phase a is on P state; if switch Sa2 and Sa3 are turned on, then phase a is on O state. Similarly, when switch Sa3 and Sa4 are turned on, then phase a is on N state.
Fig.1. Circuit diagram of a three-level neutral clamped inverter
Switches S1x and S3x are complementary and switches S2x and S4x are complimentary. If one of the complementary switch pairs is turned ON, the other of the same pair must be OFF. Two switches are always turned ON at the same time [3], [4], [5].
Table I: Switching states and terminal voltages of a three- level inverter
symbols
Switching States
Output Voltage
S1x
S2x
S3x
S4x
P
ON
ON
OFF
OFF
Vdc/2
O
OFF
ON
ON
OFF
0
N
OFF
OFF
ON
ON
-Vdc/2
-
SPACE VECTOR PULSE WIDTH MODULATION TECHNIQUE
Space Vector Pulse Width Modulation Technique is a voltage control technique used in inverters which is used to regulate voltage of inverters, cope up with variations of DC input voltage and maintain constant voltage and frequency. Voltage is controlled in each sampling period by Space Vector Transformation concept [1] by
-
Properly selecting the switching states for the inverter and
-
Calculation of appropriate time-period for each state [4], [7], [8].
Since three kinds of switching states exist in each phase, three-level inverter has (33=) 27 switching states, out of which 3 are null states, and remaining are active states [3], [7]. But we consider only 19 states to avoid redundancy and memory wastage in MATLAB [10].
From Fig.1. The resultant output load phase voltage of inverter is
Table II. All Switching states with their corresponding voltage vectors: magnitude and angle
VR(t) =
Here,
2(VAN(t)+VBN(t)
3
2
3 +VCN(t)
4
Switching States
Corresponding Voltage Vectors
Va
Vb
Vc
Vector
Magnitude
Angle
P
P
P
V0
0
0
O
O
O
N
N
N
P
O
O
V1
2Vdc 3
0
O
N
N
P
N
N
V2
4Vdc 3
0
P
O
N
V3
2 Vdc
3
6
P
P
O
V4
2Vdc 3
3
O
O
N
P
P
N
V5
4Vdc 3
3
O
P
V6
2 Vdc
3
2
O
P
O
V7
2Vdc 3
2
3
N
O
N
N
P
N
V8
4Vdc 3
2
3
Switching States
Corresponding Voltage Vectors
Va
Vb
Vc
Vector
Magnitude
Angle
N
P
O
V9
2 Vdc
3
5
6
O
P
P
V10
2Vdc 3
N
O
O
N
P
P
V11
4Vdc 3
N
O
P
V12
2 Vdc
3
5
6
O
O
P
V13
2Vdc 3
2
3
N
N
O
N
N
P
V14
4Vdc 3
2
3
O
N
P
V15
2 Vdc
3
2
P
O
P
V16
2Vdc 3
3
O
N
O
P
N
P
V17
4Vdc 3
3
P
N
O
V18
2 Vdc
3
6
Switching States
Corresponding Voltage Vectors
Va
Vb
Vc
Vector
Magnitude
Angle
P
P
P
V0
0
0
O
O
O
N
N
N
P
O
O
V1
2Vdc 3
0
O
N
N
P
N
N
V2
4Vdc 3
0
P
O
N
V3
2 Vdc
3
6
P
P
O
V4
2Vdc 3
3
O
O
N
P
P
N
V5
4Vdc 3
3
O
P
N
V6
2 Vdc
3
2
O
P
O
V7
2Vdc 3
2
3
N
O
N
N
P
N
V8
4Vdc 3
2
3
Switching States
Corresponding Voltage Vectors
Va
Vb
Vc
Vector
Magnitude
Angle
N
P
O
V9
2 Vdc
3
5
6
O
P
P
V10
2Vdc 3
N
O
O
N
P
P
V11
4Vdc 3
N
O
P
V12
2 Vdc
3
5
6
O
O
P
V13
2Vdc 3
2
3
N
N
O
N
N
P
V14
4Vdc 3
2
3
O
N
P
V15
2 Vdc
3
2
P
O
P
V16
2Vdc 3
3
O
N
O
P
N
P
V17
4Vdc 3
3
P
N
O
V18
2 Vdc
3
6
3 (1)
V (t) = 2V
-1V
-1V
(2)
AN 3
AO 3
BO 3 CO
VBN(t) = 2VBO-1VAO-1VCO (3)
3 3 3
VCN(t) = 2VCO-1VBO-1VAO (4)
When all these switching states are represented in space by using space vectors then we get a hexagon with 6 sectors [3],
[6] and with 4 subsectors in each sector as shown in Fig.2.3 3 3
By substituting the values of VAO, VBO, VCO we can find the voltage vector magnitudes and phase angles of all switching states [1], [10] as shown in Table II.
Fig.2. Space Vector representation of 3-level Inverter
A. Space Vector Modulation Algorithm:
Steps to execute SVM logic in MATLAB/SIMULINK are as follow:
Step I: Give three-phase sinusoidal input voltage Va, Vb, Vc.
Va = Vm sinwt (5)
Vb = Vm sin(wt-120o) (6)
Vc = Vm sin(wt-240o) (7)
Step II: The coordinate transformation from the abc- axis to the axis.
The transformation from the ab-c axis to the – axis, which is rotating with an angular velocity of , can be obtained by clerk and perk transformations as shown below
Fig.3. Transformation from ab-c axis to the – axis
Step IV: Selection of sector in which Vref is considered
Let n be the sector. As there are 6 sectors, n can be from 1 to 6. n is the function of deta () [9]. The sector in which the command vector Vref is located, is determined as follow:
-
If is between 0° and 60°, then Vref is located in Sector 1, n=1.
-
If is between 60° and 120°, then Vref is located in Sector 2, n=2.
-
If is between 120° and 180°, then Vref is located in Sector 3, n=3.
-
If is between 180° and 240°, then Vref is located in Sector 4, n=4.
-
If is between 240° and 300°, then Vref is located in Sector 5, n=5.
-
If is between 300° and 360°, then Vref is located in Sector 6, n=6.
Step V: Selection of Sector angle
Let be the sector angle. sector angle is the function of deta and n. The value of sector angleis given as follow:
-
If n=1 i.e., in sector 1: =
-
If n=2 i.e., in sector 2: = -60o
-
If n=3 i.e., in sector 3: = -120o
-
If n=4 i.e., in sector 4: = +180o
-
If n=5 i.e., in sector 5: = +120o
-
If n=6 i.e., in sector 6: = + 60o
1 (2) ( )
2
2
[ ] = 2 [ 33 ] []
Step VI: Selection of Subsector
3
3
2 2
0 ( ) ( )
Let y be the subsector. y is the function of Vdc,
3 3
1 1 1
Vref and sector angle (). In each sector there are 4 subsectors, y can be from 1 to 4. Subsector is selected by
[] = 2 [2 2 ] []
using Modulation Index (MI). Modulation Index differs
3 0 3
2
3 2
from modulation to modulation and from inverter to inverter. For space vector modulation technique, the
Which can also be written as
V = 2 ( 1 3 ) (8)
modulation index is given by
M =
2
3
(12)
3 2 2
V = 2 (3 3 ) (9)
3 2 2
Here -axis is direct axis (real axis) and -axis is quadrature axis (imaginary axis).
Step III: Calculate the value of deta () and Reference voltage (Vref)
Which is given by,
deta = = tan-1() (10)
Reference voltage = Vref = 2 + 2 (11)
This Reference voltage is selected as control instruction, which rotates in the space with an angular frequency . When we consider the reference vector in one of the 6 sectors, two active space vectors nearest to Vref is selected along with one of the three null vectors by means of their corresponding operating times [7], [8], [10].
Fig.4. Calculation of M1 and M2
From above figure, by using trigonometric ratios we get
M1 = M 2 sin( ) (13)
3 3
M2= M 2 sin (14)
3
Table III. Conditions for Subsector selection
y =1
M1<0.5, M2<0.5 and (M1+M2) <0.5
y = 2
M1<0.5, M2<0.5 and (M1+M2) >0.5
y = 3
M2>0.5
y = 4
M1>0.5
Step VII: Calculation of Switching Timings
Vref Ts = V1TA+V7 TB+V2 TC (15)
Consider a resultant vector in sector 1. Choose any three vectors nearest to the resultant vector.
Fig.5. calculation of switching timings
Table IV. Calculated values of Switching Timings
Step VIII: Subsector Switching
Now time period for each switching device is calculated by using the switching timings calculated in each subsector in the above step and tabulated below.
Table V. Subsector Switching Timings
V1 = 0 V2 =
V7 =
3 3 3 3 3
2
2
Substituting V1, V2 and V7 in (15) we get
3
= 1TA + 3 TC + 1 TC (16)
Ts
2 2 6 2 3
M Ts = 1 TA + 3 TB + 1 TC (17) M Ts
-
To reduce the harmonics, S1c is kept zero
2 2 6 2 3
[cos + jsin ] =1 TA + 3 [cos + jsin ] TB + 1[cosStep IX: All Sector Switching
2 2 6 6 2
+ jsin ] TC (18)
Reference voltage in sector A is given by
3 3
Vref
(A) =
2
2
2
(Va + Vb 3 + Vc
2
3 ) (24)
Equating real and imaginary terms we get,
When V
ref
3
(A) is
rotated in anticlockwise direction at an angle
Mn Ts cos = 1 TA + 3 TB + 1 cos TC (19)
of 60 degree.
2 2 6 2 3
Mn Ts sin = 3sin TB + 1 sin TC (20)
2 6 2 3
Ts = TA + TB + TC (21)
By solving equations (19), (20) and (21) we get
TA = Ts 2 k sin (22) TB = 2 k sin ( + ) – Ts (23)
3
TC = Ts 2 k sin ( ) (24)
3
Similarly, we can calculate the switching timings for all
subsectors. The calculated values are tabulated below
Fig.6. All sector switching
Vref(B) = Vref (A) * 3 (25)
V (B) = 2
(-v
2 2
+ -v ) + (-v )
(26)
ref
3 b C 3 a 3
Similarly, reference voltages are calculated in all sectors. Now, the relationship between phase voltages and the reference voltages in the subsectors is:
Table VI. Relation between phase voltages and the reference voltages in the subsectors
Sector
Phase Voltage A
Phase Voltage B
Phase Voltage C
A
Va
Vb
Vc
B
-Vb
-Vc
-Va
C
Vc
Va
Vb
D
-Va
-Vb
-Vc
E
Vb
Vc
Va
F
-Vc
-Va
-Vb
-
-
SIMULATION
The MATLAB\SIMULINK diagram of 3-phase, 3-level neutral clamped inverter connected to an induction motor is shown in Fig.6. The input given to the inverter is DC voltage and the output voltage of inverter is given to the 3-phase induction motor. The Output voltage of inverter is observed in the scope using voltage measurement blocks. Output parameters of induction motor i.e., torque, speed, and load current are observed in the scope.
Fig.6. Simulation model of 3-phase, 3-level neutral clamped inverter fed Induction Motor
In MATLAB software 3-phase induction motor is available as Asynchronous machine (Implements a three-phase asynchronous machine modelled in a selectable dq reference frame). Stator and rotor windings are connected in wye to an internal neutral point. In SVM block 3-phase sinusoidal voltage is given as input. The output pulses obtained from all sector switching block are compared with the triangular pulses, and the resultant pulses generated by SVM block are given to the IGBTs in the inverter by using GOTO and FROM blocks. These IGBT switches are used to control the output voltage.
Parameters:
-
DC input voltage of inverter = 400V
-
Output frequency = 50Hz
-
Induction motor Rotor type = Squirrel cage
-
Number of poles in the Induction motor = 4
-
Inertia of Induction motor = 0.0131 J(kg.m2)
-
Rated Power of Induction motor = 4KW (5.4 HP)
-
Rated Speed of Induction motor = 1430 rpm
-
Stator Resistance of Induction motor = 1.405
-
Rotor Resistance of Induction motor = 1.395
-
Stator Inductance of Induction motor = 5.839 mH
-
Rotor Inductance of Induction motor = 5.839 mH
-
Mutual Inductance of Induction motor = 0.1722 mH
-
-
SIMULATION RESULTS
The output voltage of three phases of 3-level neutral clamped inverter by using space vector modulation as voltage control strategy is shown in Fig.7.
Fig.7: Output voltage of 3-phase, 3-level neutral clamped inverter.
The FFT (Fast Fourier Transform) analysis is used to calculate the total harmonic distortion present in the output voltage and output current of inverter. The FFT analysis of output current of 3-phase, neutral clamped 3-level inverter for Space Vector Modulation is shown in the Fig.8.
Fig.8: FFT analysis of output current of inverter for Space Vector Pulse Width Modulation.
The waveforms of electromagnetic torque (Te), speed (w) and three-phase current (Iabc) of induction motor are shown below in Fig.9. In MATLAB/SIMLINK a step input (magnitude of 10 from 0 sec to 1 sec and magnitude of 20 after one second) is given to the torque terminal of Induction motor. Initially the magnitde of torque is 10 N-m and at 1 second the torque magnitude is increased from10 N-m to 20 N-m as shown in Fig.9. As a result, the magnitude of speed decreases and current increases at 1 second [10].
Fig.9: Waveforms of Speed, Torque and 3-phase output current of Induction Motor
-
CONCLUSION
In this paper, the performance of induction motor which is driven by a three-phase, three-level neutral clamped Inverter using space vector modulation technique as voltage control strategy has been studied. A MATLAB/Simulink model for implementation of SVM is presented. The step- by-step algorithm of SVM is reported. The Speed, Torque
and Output current of the Induction Motor, the output voltage of the inverter have been plotted. From the above results we observe that the THD value of output current of 3-phase, 3-level neutral clamped inverter with space vector pulse width modulation technique is less than 5% i.e., 2.01%.
REFERENCES
-
Muhammad H. Rashid, Narendra Kumar, Ashish R. Kulkarni, Power Electronics Devices, Circuits, and Applications (Fourth Edition).
-
Nam S. Choi, Jung G. Cho and Gyu H. Cho, A General Circuit Topology of Multilevel Inverter, IEEE Transactions on industry applications, 1991
-
Chengzhu Piao, John Y. Hung, A Simplified Space Vector PWM algorithm for Three-level NPC VSI, IEEE Southeast Conference 2015, April 9 – 12, 2015 – Fort Lauderdale, Florida.
-
R.G.Shriwastavaa, M. B. Daigavaneb , P. M. Daigavanec, Simulation Analysis of Three Level Diode Clamped Multilevel Inverter Fed PMSM Drive Using Carrier Based Space Vector Pulse Width Modulation (CB-SVPWM), 7th International Conference on Communication, Computing and Virtualization 2016.
-
M. SajediHir, Y. Hoseynpoor, P. MosadeghArdabili, T. PirzadehAshraf, Modelling and Simulation of Induction Motor Drive with Space Vector Control, Australian Journal of Basic and Applied Sciences, 5(9): 2210-2216, 2011 ISSN 1991-8178.
-
Debanjan Roy, Sanatan Kumar, Madhu Singh, A novel region selection approach of SVPWM for a three-level NPC inverter used
in electric vehicle, International Journal of Power Electronics and Drive System (IJPEDS) Vol. 10, No. 4, December 2019
-
Identification of Optimal SVPWM Technique for Diode Clamped Multilevel Inverter based Induction Motor Drive., IEEE Southeast Conference 2015.
-
] Suresh L., Mahesh K., Janardhna M. and Mahesh M., Simulation of Space Vector Pulse Width Modulation for Voltage Source Inverter using MatLab/Simulink, Journal of Automation & Systems Engineering 8-3 (2014): 133-140.
- [9] Soumya S., Dr. B. V. Sumangala, Application of Space Vector Modulation Technique for Three Level Neutral Point Clamped Inverters., International Journal of Engineering Research & Technology (IJERT) ISSN: 2278-0181, Vol. 2 Issue 6, June 2013.
- [10] Banda Sai Kishore, Kasoju Bharath Kumar, Cheguri Venkatesham and Bandi Pratish, Space Vector Pulse Width Modulation Technique based Diode Clamped Multilevel Inverter for Induction Motor Drive., IJISET – International Journal of Innovative Science, Engineering & Technology, Vol. 8 Issue 7, July 2021.