
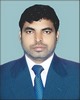
- Open Access
- Authors : Allois Kioko Luvai , John P.O. Obiero , Christian T. Omuto
- Paper ID : IJERTV10IS080168
- Volume & Issue : Volume 10, Issue 08 (August 2021)
- Published (First Online): 26-08-2021
- ISSN (Online) : 2278-0181
- Publisher Name : IJERT
- License:
This work is licensed under a Creative Commons Attribution 4.0 International License
Performance Evaluation CO2 Vapor Compression Heat Pump Considering Refrigerant Filling Pressure
Dr. M G Basavaraju1
1 Senior Scale Lecturer, Department of Mechanical Engineering (MTT),
Government CPC Polytechnic, Mysore, Karnataka, India
Savitha D R2
2 Lecturer,
Department of Mechanical Engineering (MTT), Government CPC Polytechnic, Mysore, Karnataka, India
Abstract:- Carbon dioxide (CO2) is non-toxic, on-flammable, has zero ozone depletion potential and negligible global warming potential as refrigerant. By using CO2 refrigerant, heat pumps are the most promising technologies to reduce global warming emissions and ozone depletion. A carbon dioxide heat pump requires further technological progress and environmental friendly refrigerants with higher Coefficient of Performance. CO2 is one of the few non-toxic and non-flammable working fluids that do not contribute to ozone depletion or global warming, if leaked to the atmosphere. Carbon dioxide (CO2) is non-toxic, non-flammable, has zero ozone depletion potential and negligible global warming potentials refrigerant. The aim of this paper is the evaluation of the energy performances using counter flow heat exchanger at different refrigerant filling pressure to the compressor. The performance of the heat pump evaluated considering the parameters like different refrigerant filling pressure, evaporator fan speed and water outlet temperature at different mass flow rate
Key words: Heat pump, LMTD, COP, Ozone Depletion Potential, Evaporator
Nomenclature:
mw Mass flow rate of water Two Outlet temperature of water
INTRODUCTION:
Due to harmful effects of the chlorine based refrigerants on the environment, CO2 has been used as a potential refrigerant due to the low critical temperature [1]. The use of this water heater in place of the ordinary water heater, which is mainly driven by gas, can lead to a significant reduction in the primary energy consumption. In order to improve the system performance of the CO2 heat pump, it is necessary to develop an optimum design and a control method for the CO2 heat pump water heater [2].
It works on the principle of vapor compression refrigeration system. Presently used refrigerants globally are Tetrafluoroethane (R-134a) and Dichloro Difluoro Methane (R-22). These are made from the components of chlorofluorocarbons and hydro chlorofluorocarbons. Increase in the amount of chlorofluorocarbons in the environment results in problems ODP and GWP. So, these refrigerants should be replaced by those which have no ODP and less GWP [3]. Therefore, naturally available refrigerant like CO2 is used as a refrigerant [4]. It has many advantages like eco friendly, low cost, non flammable, non corrosive, non toxic, stable and suitable for wide range of operating conditions [5]. The heat pump consists of compressor, condenser, evaporator and capillary tube [6] which is best suitable for domestic water heater [7].
In the present study the modification of heat exchanger and experimental performance evaluation of vapor compression prototype heat pump model was carried out. By modifying the heat exchanger, improvement in COP is observed [8]. The variation of speed of compressor and evaporator affect the performance of the heat pump [9].The experiment was conducted to evaluate the water outlet temperature for different mass flow rate, different refrigerant filling pressure and evaporator fan speed.
EXPERIMENTAL SET UP:
Fig 1: Heat pump cycle Fig 2: Line diagram of heat pump model
The figure 1 and 2 shows the heat pump cycle and line diagram of heat pump model. Figures 3 and 4 show the experimental set up of prototype heat pump model. The supporting fabrication is done by using mild steel angles. The prototype heat pump model consists of the components like 2 numbers of condensers, compressor, evaporator, capillary tube and water tank. The compressor is 1 ton capacity reciprocating type 250V, 50Hz which compresses to maximum pressure of 280 PSI and temperature up to 1100C.
Fig 3: Experimental set up Fig 4: Experimental set up
In this model condenser and evaporator are the two heat exchangers used which works on counter flow method. Refrigerant (hot fluid) flows in the tube side and water (cold fluid) flows in the shell side. The specification of evaporator and condenser are as follows.
Heat exchangers |
Condenser 1 |
Condenser 2 |
Evaporator |
Configuration of heat exchangers |
Coaxial, single pass and counter flow |
Coaxial, single pass and counter flow |
Coaxial, single pass, 1/83 HPGW, 1200 rpm |
Inner /outer tube diameters |
8mm/6 inch |
10mm/5inch |
12mm/10inch, 3 rows (cooling coil) |
Total length of tubes |
20 inch |
21 inch |
13 inch |
The capillary tubes of diameter 2mm is used for expansion process. The refrigerant is expanded in 18mm diameter tube.
Experimental procedure:
The experiment was conducted to measure the rate of increase in water outlet temperature in the condenser at different pressures and mass flow rates. Refrigerant is filled to a pressure of 50, 60 and 70 PSI into the heat pump model at different intervals. Initial reading at 50PSI filling pressures both pressures and temperatures in the gauges are noted and inlet water temperature of condenser also noted. The heat pump is started and allowed to run for some time to reach steady state. The water is supplied from water tank to condenser through inlet valve using pump. After reaching the steady state, experiment is started by recording the pressure and temperature at different components of the system using temperature gauges and pressure gauges. The outlet mass flow rate and temperature of water from condenser is recorded. This procedure is repeated for 60 PSI and 70 PSI filling pressures of refrigerant and mass flow rate of water with constant time interval. The refrigeration cycle is as shown in the figure
-
The outlet water temperature recorded for different filling pressure under the variable conditions like different mass flow rate of water and evaporator fan speed at water inlet temperature is 270C.
RESULT AND DISCUSSION:
Condenser 1 Condenser 2
Outlet t water temperature in 0C
Outlet t water temperature in 0C
47
46 70 PSI
45 60 PSI
44 50 PSI
43
42
41
40
39
38
47 70 PSI
Outlet water temperature in 0C
Outlet water temperature in 0C
46 60 PSI
-
50 PSI
44
43
42
41
40
39
38
0.009 0.01 0.011 0.012
Mass flow rate kg/sec
0.009 0.01 0.011 0.012
Mass flow rate kg/sec
Fig. 5: Two V/s mwo at 800rpm Fig 6: Two V/s mwo at 800rpm
47
Outlet t water temperature in 0C
Outlet t water temperature in 0C
-
70 PSI
45 60 PSI
47 70 PSI
Outlet water temperature in 0C
Outlet water temperature in 0C
46 60 PSI
-
50 PSI
-
50 PSI
43
42
41
40
39
38
0.009 0.01 0.011 0.012
Mass flow rate kg/sec
44
43
42
41
40
39
38
0.009 0.01 0.011 0.012
Mass flow rate kg/sec
Figure 7: Two V/s mwo at 1000 rpm Figure 8: Two V/s mwo at 1000 rpm
Outlt water temperature in 0C
Outlet water temperature in 0C
47 47
Outlet water temperature in 0C
Outlet water temperature in 0C
46 70 PSI 46
45 60 PSI 45
44 50 PSI 44
43 43
42 42
41 41
40 40
39 39
38 38
70 PSI
60 PSI
50 PSI
0.009 0.01 0.011 0.012
Mass flow rate kg/sec
0.009 0.01 0.011 0.012
Mass flow rate kg/sec
Figure 9: Two V/s mwo at 1200 rpm Figure 10: Two V/s mwo at 1200 rpm
The experimental results of outlet water temperature of condenser (Two) versus mass flow rate of water for different pressures (50, 60 and 70 PSI)are shown for condenser 1 and 2 (different evaporator fan speed).The figures 5, 7, 9 show Two versus mass flow rate for condenser 1. The figures 6, 8, 10 show Two of condenser versus mass flow rate for condenser 2. The water is pumped from the water tank. As pressure increases, Two of condenser increases for different pressures. As mass flow rate decreases, Two of condenser increases for different pressures. The increase in Two of condenser is observed more for the pressure70 PSI and less for 50 PSI. The Two of condenser got from the experiment is in the range of 38.80C to 450C. The maximum outlet water temperature (45) is observed in condenser 2 for 1200 rpm evaporator fan speed and 70 PSI pressure. The minimum Two(38.8) is observed in condenser 1 for 800 rpm evaporator fan speed and 50 PSI pressure. The Two of condenser 2 (10 mm diameter tube used)at 1200 rpm and pressure 70 PSI is more compared to condenser 1(8 mm diameter tube used)
because of area of contact for heat transfer is more in condenser 2.Also as the evaporator fan speed increases heat and Two increases because of quick rate heat transfer between air and refrigerant in evaporator.
CONCLUSION:
The experimental performance evaluation of CO2 refrigerant prototype heat pump model to heat the water was performed. The parameters like different refrigerant filling pressure, evaporator fan speed and water outlet temperature at different mass flow rate are evaluated. It is observed that as increase in refrigerant filling pressure water outlet temperature increases. Increase in mass flow rate of water, decreases the outlet temperature of water in the condenser. The maximum outlet water temperature (45) is observed in condenser 2 for 1200 rpm evaporator fan speed and 70PSI pressure. The minimum Two(38.8) is observed in condenser 1 for 800 rpm evaporator fan speed and 50 psi pressure. Condenser 2 shows better performance at 70PSI refrigerant filling pressure.
REFERENCES:
-
Jahar Sarkar-2010 Journal of Advanced Research in Mechanical Engineering (Vol.1-2010/Iss.1) Review on Cycle Modifications of Transcritical CO2 Refrigeration / pp. 22-29.
-
Seiichi Yamaguchi, Daisuke Kato, Kiyoshi Saito, Sunao Kawai-2011 International Journal of Heat and Mass Transfer 54 (2011),page no 1896 1906
-
J.Steven Brown, Yongchan Kim and Piotr A. Domanski 2002 Evaluation CO2 as R-22 substitute for Residential Air conditioning vol 108 page no 1- 10.
-
J M Belman Flores and Vicente Perez-GarcÃa 2014 General aspects of carbon dioxide as a refrigerant vol 25 page no 96-106.
-
Alberto Cavallini Italy- Properties of co2 as a refrigerant.
-
Seiichi Yamaguchi, Daisuke Kato, Kiyoshi Saito and Sunao Kawai 2011- Development and validation of static simulation model for CO2 heat pump
vol 54 page no 1896-1906.
-
E FornasierI, S Girotto and S Minetto -2008 CO2 heat pump for domestic hot water.
-
Jahar Sarkar- 2010 Review on Cycle Modifications of Transcritical CO2 Refrigeration and Heat Pump Systems vol 1-2010/Iss.1 page no 22-29.
-
M. Raisul Islam , K. Sumathy , J. Gong , Samee Ullah Khan-2012 International Conference on Renewable Energies and Power Quality (ICREPQ12) Santiago de Compostela (Spain).
-