
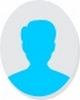
- Open Access
- Authors : Vashisht Patil , M C Paliwal
- Paper ID : IJERTV9IS120121
- Volume & Issue : Volume 09, Issue 12 (December 2020)
- Published (First Online): 23-12-2020
- ISSN (Online) : 2278-0181
- Publisher Name : IJERT
- License:
This work is licensed under a Creative Commons Attribution 4.0 International License
Partial Replacement of Cement with Rice Husk Ash in Cement Concrete
Vashisht Patil1, Prof. M. C. Paliwal2
1P. G. Student, Department of Civil and Environment Engineering, National Institute of Technical Teachers Training and Research, Bhopal, India
2Associate Professor, Department of Civil and Environment Engineering, National Institute of Technical Teachers Training and Research, Bhopal, India
Abstract – Concrete is one of the significant materials of the construction industry. These days because of expansion in a population, the demand of infrastructure is expanding day by day. This prompts the increment in production of cement. In the present scenario the overall cement production is about 4.1 billion metric tons worldwide. This huge amount of production prompts utilization of natural resources and it is very unsafe for environment. Enormous amount of waste by-products are delivered from the manufacturingenterprises, for example, mineral slag, fly ash, silica fumes, rice husk ash and so on. the rice husk ash is an agricultural byproduct which is obtained from the rice mills ,the husk which is obtained from mill is of no use i.e it is not even be used for animals to eat. Hence it is used as a fuel in various big industries the burning temperature is very high hence they are obtained from that .the RHA is very lightweight. The research work here deals with the partial replacement of cement with RHA in concrete at various percentage such as 0%,5%,10%,15%,20% and25% by mass of cement. Various experimental investigations are carried out to find out the compressive strength , split tensilestrength and of concrete samples cured for period of 7 and 28 days . the results obtained from the experiments with satisfactory replacement of cement with rice husk ash are presented in this research paper.
Key Words: Concrete, rice husk ash, compressive strength, split tensile strength, flexural.
1.INTRODUCTION
Concrete is a most broadly utilized construction material. It is, all in all, a mixture of cement (binding material), aggregate (filler materials), admixture and water. It very well may be formed in any necessary shape, simple to deal with and has a wide range of design strength. It is therefore utilized in approximately all benevolent construction work. Cement is the main element of concrete as to act as a binding material. Be that as it may, the production of concrete causes so numerous natural risks, like cement dust, air contamination ,solid waste pollution, noise pollution, ground vibrations and resource depletion because of crude material extraction. The primary components of the gases produced from cement enterprises are CO2, N2, O2, SO2, water vapours and micro components for example CO and NOx. The cement industry is one of the two biggest producers of carbon dioxide (CO2), making up to 8% of overall man-made emanation of this gas, of which half is from chemical process and 40% from consuming fuel. The CO2 produced from structural concrete is assessed at 410 kg/m3. Around 900 kg of CO2 are discharged for the creation of every 1 ton of concrete. The CO2 is major green house gas. In this way cement assembling contributes green house gases both straightforwardly through the decay of calcium carbonate and furthermore through utilization of energy, especially from the combustion of fossil fuel.
Thus we are expected to discover other discretionary material for concrete instead of cement. In the event that we ready to supplant few percent of cement from concrete , it will supportive to lessen CO2 emission. From different exploration works, some mechanical squanders are discovered which can diminish the measure of concrete in cement without bargaining its essential properties (like strength). Granulated blast furnace slag, silica fume, rice husk ash, cenospheres and fly ash are some industrial waste that can be utilized as strengthening cementitious materials. Rich husk ash is an agricultural by product which is obtained fromricemill andthen burned and very high temperature as fuel .which gives some extra advantages when utilized in cement. Before additional conversation about RHA let us quickly examine about concrete.
2 OBJECTIVE OF RESEARCH
-
To examine the gainful use of modern waste as the cement substitution in construction work.
-
To evaluate the optimum proportion of rice husk ash as a beneficial replacement with cement in cement concrete.
-
MATERIAL USED
-
cement
For this research work, PCC cement of Ultratech cement company is used, that is available in our nearest construction material shop. While adding cement in concrete mix, it is ensured that cement is moisture free and no lumps are found in the cement bag.
-
rice husk ash (RHA)
RHA is the result of burning of rice husk. A large portion of the evaporable parts of rice husk are gradually lost during consuming and the essential deposits are the silicates. The attributes of the debris are subject to (1) arrangement of the rice husks, (2) consuming
temperature, and (3) consuming time. Each 100 kg of husks consumed in a heater for instance will yield around 25 kg of RHA. For this experimental work , the rice husk ash is purchased from a reliable source ambika traders situated anand Gujarat.
-
fine aggregates
Fine aggregates are the material going through an IS sieve 4.75 mm and hold on to 150m gauge. Locally accessible sand isutilizedas fine aggregates in this a\experimental investigation.
-
coarse aggregate
The aggregates which may infilterate 75mm IS strainer and held on 4.75mm IS sieve is called coarse aggregate. Size of coarse aggregate may change from 10mm to 40mm. Locally accessible coarse aggregate is utilized for test, that accessible on closer construction material shop.
-
water
Generally water having pH value 6.0 to 8.0 is used , it is potable water i.e not containing any type of alkalinity and salinity.
-
-
METHODOLOGY
-
proportioning
The standard proportion according to IS:456-2000, for M20 grade concrete is 1:1.5:3. Here extent is embraced 1:1.8011:3.283 which is determined by mix design method. Concrete is supplanted with RHA at different rates for example 0%, 5%, 10%, 15%, 20% and 25%. The measure of every fixing utilized per cubic meter is as follow:-
Concrete = 363.498 kg; Fine total = 683.812 kg; Coarse total = 1329.614 kg
-
casting of samples
Total 108 samples are casted out 36 cubes, 36 cylinders and 36 beams are prepared. Concrete mix is filled in moulds in three layers. Each layer is compacted by tampering rod with 25 number of blow.
-
curing
The sample specimens are set apart inside 2 to 3 hours of casting and are kept in vibration free place, in almost 90% relative damp air and at temperature of 270 ± 20 C for 24 ± ½ hours. After this period, the specimens are put in submerged condition in fresh water in a tank and are kept there only before to test. The duration of curing of sample is according to their schedule of testing.
-
testing of samples
Compressive strength test
The IS code followed for testing IS: 516 1959. The concrete cubes are casted of size 150mm ×150mm × 150mm. These samples are tested in UTM (Universal Testing Machine) of capacity 2000KN. at pace of 140 kg/cm2/min. The compressive strength test is performed at 7 days and 28 days.
Split tensile test
This test is an indirect method for finding tensile strength of concrete. The cylinder of dia 150mm and height 300m is casted and afterward tested at 7 days and 28 days. The loading rate is kept 1.2 MPa.
Flexural strength
The beams of size 100mm × 100mm × 500mm were casted for this test and one point loading method is adopted for testing. Tests are performed per the ASTM C 293. The tests are performed at 7 and 28 days.
-
-
RESULTS AND DISCUSSION
Table-1: average compression test results of cube specimens
Percentage of RHA
7 days compressive strength
28 days compressive strength
0
14.85
27.75
5
16.95
30.86
10
17.26
31.72
15
18.27
32.78
20
19.89
32.00
25
16.10
28.80
Chart Title
Chart Title
35
30
25
20
15
10
5
0
35
30
25
20
15
10
5
0
0%
5%
10%
15%
20%
25%
0%
5%
10%
15%
20%
25%
perrcentage of RHA in concrete mix
perrcentage of RHA in concrete mix
7 days
28 days
7 days
28 days
compressivestrength
compressivestrength
graph 1 : compression test analysis
The compression test results are shown in table-1. From GRAPH-1 it is observed that the maximum result is obtained at 15% rice husk ash in concrete. The 28 days compressive strength for conventional concrete is found 27.75 MPa and that for 15% rice husk ash concrete is32.78 MPa. It shows the 15.34% improvement from conventional concrete. thus optimum use of rice hus k ash is 15%.
Table 2 : average tensile strength of cylindrical specimens
Percentage of RHA
7 days compressive strength
28 days compressive strength
0
1.182
1.526
5
1.249
1.651
10
1.289
1.677
15
1.380
1.697
20
.950
.961
25
.92
.781
GRAPH 2 : split tensile strength analysis
The split tensile strength test results were shown in table no 2, from GRAPH-2 it is observed that the maximum result is obtained at 15% rice husk ash In concrete. The 28 days strength for conventional concrete is found out to be 1.697 MPa and that for 15% rice husk ash in concrete is 1.380 MPa. It shows the 24.41 % improvement from conventional concrete. For other percentage of rice husk ash the strength is getting low , thus optimum percentage for use of RHA is 15%.
-
CONCLUSION
The compressive strength of conventional concrete at 28 days is 27.75MPa and 15% rice husk ash concrete is 32.78 MPa , it show the 15.34 % improvement from conventional concrete.
For other percentages of RHA(rice husk ash) the strength is below 20MPa , thus optimum percentage of RHA is 15%.
The split tensile strength of conventional concrete for 28 days is found to be 1.526MPa and that for 15% rice husk ash concrete is 1.697MPa. it shows the 24.41% improvement from conventional concrete. The optimum use of rice husk ash is 15%.
Finally , from the experimental analysis we have found that 15 % replacement of rice husk ash with cement in cement concrete is beneficial replacement. And we go beyond this for further replacement in percenatage of cement we will see decrease in strength of concrete.
-
ACKNOWLEDGEMENT
I would extremely like to thanks to my mentor Prof. M. C. Paliwal , for his constant support and motivation during the course of my thesis work. I truly appreciate and value his esteemed guidance and encouragement from initiation to the completion of the thesis. His valuable guidance will be remembered lifelong .special thanks to god for everything and family members for always encouraging me to push the limits.
REFERENCES
-
Arvind kumar and amit kumar tomar, Replacement of cement in concrete with rice husk ash, SSRG international journal of civil engineering (SSRG-IJCE)- volume 3 issue 7 july 2016
-
Swami Nathen. A.N., Indian rice husk- improving the mechanical properties of concrete: a review. ISSN : 2248-9622, issue 1,(part-1) January 2017, pp.76-79
-
Alireza Naji Givi, contribution of rice husk ash to theproperties of mortar and concrete: areview, journal of American science ,2010;6(3), NajiGivi, etal, rice husk ash in concrete
-
Dr. A. M. Pande, S.G. Makarande, effect of rice husk ash on concrete, international journal of engineering research and applications (IJERA) ISSN:2248- 9622.